Maintenance Manual for BG Coaches of ICF Design-73-108 PDF
Document Details
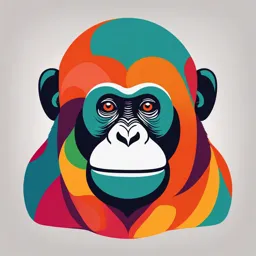
Uploaded by ImaginativePeachTree
STC/JHS
Tags
Related
- Maintenance Manual for BG Coaches of ICF Design (PDF)
- Maintenance Manual for BG Coaches of ICF Design PDF
- Maintenance Manual for BG Coaches of ICF Design PDF
- Draw & Buffing Gear Maintenance Manual PDF
- Maintenance Manual for BG Coaches of ICF Design PDF
- Maintenance Manual for BG Coaches of ICF Design PDF
Summary
This document is a maintenance manual for BG coaches of ICF design, specifically focusing on the bogie components. It describes the construction and design features of the bogies, including axle loads, wheelbase, suspension systems, and shock absorbers. The document also includes details on wear limits for different parts.
Full Transcript
Maintenance Manual for BG Coaches of ICF design Bogie CHAPTER 3 BOGIES 301 GENERAL 302b Deflection due to the tare w...
Maintenance Manual for BG Coaches of ICF design Bogie CHAPTER 3 BOGIES 301 GENERAL 302b Deflection due to the tare weight is almost equally divided between axle The main constructional and design and bolster springs. Weight of coach features of the ICF/RCF all-coil body is transferred to its bogie by side bogies, used on mainline BG coaches bearers pitched 1600 mm apart. Side- are briefly described in the following bearers consist of lubricated metal paragraphs. Leading Parameters of slides immersed in oil baths. No ICF bogie are as under: vertical weight transfer is effected through bogie pivot and the pivot acts Table 3.1 merely as a centre of rotation and serves to transmit tractive/braking S. Description Parameters forces only. No. 1. Maximum Axle 16.25t, 13t load bearing 303 BOGIE ASSEMBLY capacity (see figure 3.1) 2. Wheel base 2896mm 3. Wheel diameter 915mm (New) The bogie frame and components are 4. Axle guidance Telescopic axle guide of all-welded light construction with a with oil damping wheel base of 2.896 metre. The wheel 5. Primary Coil spring sets are provided with self-aligning suspension spherical roller bearings mounted in 6. Secondary Coil spring cast steel axle box housings. Helical suspension coil springs are used in both primary 7. Shock absorbers i) Vertical dashpot in and secondary suspension. The primary suspension. weight of the coach is transferred ii) Hydraulic double through side bearers on the bogie acting vertical bolsters. The ends of the bogie shock absorber in secondary bolsters rest on the bolster helical suspension. springs placed over the lower spring 8. Transfer of Through bogie side beam suspended from the bogie frame coach body bearer pitched at by the inclined swing links at an angle weight 1600mm. 70. Hydraulic shock absorbers and dash pots are provided in the 302 ALL-COIL ICF BOGIE secondary and primary suspensions respectively to damp vertical 302a The bogies being currently oscillations. manufactured by ICF/RCF which have been accepted as standards of 304 AXLE BOX GUIDE WITH DASH the Indian Railways and are of an all POT ARRANGEMENT welded light weight construction. (see fig. 3.2a & 3.2b) Axles are located on the bogie by telescopic dash pot and axle guide Axle box guides are of cylindrical assemblies. Helical coil springs are type welded to the bottom flanges of used in both the primary and the the bogie side frame with close secondary stages. The axle guide dimensional accuracy. These guides device provides viscous damping together with lower spring seats across primary springs while located over the axle box wings, hydraulic dampers are provided house the axle box springs and also across the secondary stage. Dampers serve as shock absorbers. These are protected against misalignment by guides are fitted with guide caps resilient fittings. Isolation of vibration having nine holes of diameter 5 mm is effected by rubber pads in primary equidistant through which oil in and secondary suspension. the lower spring seat passes under Chapter 3, Page 1 of 36 Maintenance Manual for BG Coaches of ICF design Bogie VERTICAL SHOCK ABSORBER SECONDARY SUSPENSION PRIMARY SUSPENSION SAFETY STRAP BOLSTER SUSPENSIONPHANGER AXLE BOX SPRING LOWER SPRING BEAM 2896 WHEEL BASE BRAKE BEAM BRAKE BLOCK CENTRE PIVOT BOGIE FRAME ANCHOR LINK 2364 3950 EQUALISING STAY WHEEL AXLE BOGIE BOLSTER SIDE BEARER I.C.F. BOGIE FIGURE 3.1 Chapter 3, Page 2 of 36 Maintenance Manual for BG Coaches of ICF design Bogie pressure during dynamic oscillation bogies. It does not transmit any of coach and provide necessary vertical load. It is equipped with damping to primary suspension to rubber silent block bushes which tend enhance better riding quality of to centralise the bogies with respect to coach. This type of rigid axle box the body and, to some extent, control guide arrangement eliminates any and damp the angular oscillations of longitudinal or transverse relative the bogies. (see figure 3.3) movement between the axles and the bogie frame. 309 SIDE BEARERS Figure 3.2a & 3.2b show modified The side bearer arrangement consists and unmodified guide arrangement of a machined steel wearing plate respectively. The quantity of oil immersed in an oil bath and a floating required to achieve 40 mm oil level bronze-wearing piece with a spherical above the guide cap in modified top surface kept in it, on both sides of arrangement is approximately 1.6 the bogie bolster. The coach body liters and in unmodified arrangement rests on the top spherical surface of is approximately 1.4 liters. As it is these bronze-wearing pieces through not possible in open line to the corresponding attachments on the distinguish between modified and bottom of the body-bolster. The unmodified arrangements, 40 mm whole arrangement is provided with a oil level is standardised for both. cover to prevent entry of dust in the oil sump. (see figure 3.4 ) 305 AIR VENT SCREWS Table 3.2 On the bogie side frames, directly above the dash-pots, tapped holes are Wear limit for wearing plate provided for replenishing oil in the dash pots. Special screws with New Shop renewal Condemning copper asbestos washers are screwed size size size on the tapped hole to make it air tight. 10 mm 9 mm 8.5 mm 306 BOGIE BOLSTER SUSPENSION Wear limit for wearing piece The bolster rests on the bolster coil springs - two at each end, located on New Shop renewal Condemning size size size the lower spring beam which is 45 mm 43.5 mm 42 mm suspended from the bogie side frame by means of bolster-spring- 310 ANCHOR LINKS suspension (BSS) hangers on either side. The two anchor links diagonally The floating bogie bolster which positioned are provided with silent supports the coach body is held in block bushes. The links prevent any position longitudinally by the anchor relative movement between the bogie links which are pinned to the bolster frame and coach body. sides and the bogie Transoms. One 307 SPRINGS anchor link is provided on each side of the bolster diagonally across. The In ICF bogie, helical springs are used links can swivel universally to permit in both primary and secondary the bolster to rise and fall and sway suspension. The springs are side wards. They are designed to take manufactured from peeled and the tractive and braking forces. The centreless ground bar of chrome anchor links are fitted with silent vanadium/chrome molybdenum steel block bushes (see figure 3.5) conforming to STR No. WD-01-HLS- 94 (Rev.1) 311 SILENT BLOCK 308 CENTRE PIVOT This is a synthetic rubber bush fitted ARRANGEMENT in anchor link and center pivot of ICF The centre pivot pin joins the body bogies to transmit force without shock with the bogie and transmits the and reduce noise. tractive and braking forces on the Chapter 3, Page 3 of 36 Maintenance Manual for BG Coaches of ICF design Bogie 1 2 1. SPECIAL SEREW WITH 3 SEALING WASHER 4 2. GUIDE 3. PROTECTIVE TUBE COMPLETE 5 4. UPPER RUBBER WASHER 6 5. TOP SPRING SEAT 6. DUST SHIELD SPRING 7 7. DUST SHIELD 8. HELICAL SPRING 8 9. GUIDE RING OIL LEVEL UNDER TARE 10. RUBBER PACKING RING 9 40 11. GUIDE BUSH OIL LEVEL BEFORE ASSEMBLING 12. CIRCLIP 10 X TO RAIL LEVEL 13. COMPENSATING RING 142.5 14. LOWER RUBBER WASHER 92.5 104 11 15. SAFETY STRAP 16. LOWER SPRING SEAT 12 13 X TO RAIL LEVEL- 14 686 FOR ALL AC & NON-AC COACHES EXCEPT POWER CARS POWER CAR- 15 670 FOR BOGIE ON LUGGAGE SIDE 16 672 FOR BOGIE ON GENERATOR SIDE MODIFIED AXLE BOX GUIDE ARRANGEMENT Figure 3.2a Chapter 3, Page 4 of 36 Maintenance Manual for BG Coaches of ICF design Bogie 1 2 1. SPECIAL SEREW WITH 3 SEALING WASHER 4 2. GUIDE 3. PROTECTIVE TUBE COMPLETE 5 4. UPPER RUBBER WASHER 6 5. TOP SPRING SEAT 6. DUST SHIELD SPRING 7 7. DUST SHIELD 8. HELICAL SPRING 8 9. GUIDE RING 10. RUBBER PACKING RING 9 OIL LEVEL 11. GUIDE BUSH UNDER TARE OIL LEVEL BEFORE 12. SPRING CLIP 40 10 ASSEMBLING X TO RAIL LEVEL 13. COMPENSATING RING 14. LOWER RUBBER WASHER 119.5 66.5 11 88 15. SAFETY STRAP 16. LOWER SPRING SEAT 12 17. GUIDE CAP 13 17 14 X TO RAIL LEVEL- 686 FOR ALL AC & NON-AC COACHES EXCEPT POWER CARS 15 POWER CAR- 16 670 FOR BOGIE ON LUGGAGE SIDE 672 FOR BOGIE ON GENERATOR SIDE AXLE BOX GUIDE ARRANGEMENT Figure 3.2b Chapter 3, Page 5 of 36 Maintenance Manual for BG Coaches of ICF design Bogie FIXING ARRGT. OF PBOTTOM COVERPWITH BOLSTER SECTION A-A TO BE TACK WELDEDPAFTER ASSEMBLY CENTRE PIVOT PIN SEALING CAP A BOGIE BOLSTER SILENT BLOCK SLEEVE HEX. HEAD SCREWP& SPRING WASHER BOTTOM COVER PCOMPLETE COTTER SPLIT PIN A CENTRE PIVOT ARRANGEMENT FIGURE 3.3 Chapter 3, Page 6 of 36 Maintenance Manual for BG Coaches of ICF design Bogie 10 % % ° R1 c 9.5 0 45 3 WEARING PIECE FOR SIDE BEARER 5 REF. DRG. NO. T-O-5-649 5 13 % % c 6 SURFACE SHOULD BE SMOOTH FELT OIL LEVEL CHECK FOR POROUS WELDING WEARING PIECE Note:-P1. Bronze Wearing Piece should be renewed when the wear on the mating surface reaches 3mm that is, height is less than 42 mm or damages occur to the oil grooves.P2. The hard ground plate should be renewed when the wear exceeds 1.5mm that is, thickness is less than 8.5 mm or ridges are observed on the plate. SIDE BEARER ARRANGEMENT FIGURE 3.4 Chapter 3, Page 7 of 36 Maintenance Manual for BG Coaches of ICF design Bogie ANCHOR LINK WITH SILENT BLOCK Figure 3.5 312a Coach Under Frame Mounted 312 BRAKE RIGGING Brake Rigging Brake rigging is provided to control The brake rigging is as per figure 3.6. the speed of the coach by transferring In 16.25 t axle load bogie the four the braking force from the brake lever used in bogie brake rigging are cylinder to the wheel tread. Brake each with lever ratio of 1:1.376 and rigging can be divided into two hence the total Mechanical advantage groups i.e. Bogie mounted brake in a bogie is 5.504. rigging and coach under frame The components details of 16 t bogie mounted brake rigging. are given in table 3.3 (Refer ICF drawing No. WTAC3-3-2-305). COACH UNDERFRAME BRAKE RIGGING Figure 3.6 Chapter 3, Page 8 of 36 Maintenance Manual for BG Coaches of ICF design Bogie Table 3.3 Sr.No. Description Ref. Drg. NO (ICF) Quantity 1 Brake Head & block complete (L.H. Assembly) T-3-1-919 8 2 Brake Head & block complete (R.H. Assembly ) T-3-1-619 8 3 Short lever WLRRM 3-2-002 12 4 Long lever WLRRM-3-2-002 8 5 Brake Block Hanger T-3-2-645 16 6 Adjusting link WT AC3-3-2-302 2 7 Lever Hanger HIG AC 3-3-2-302 16 8 Pull rod WLRRM3-2-002 4 9 Pull rod T-3-2-616 2 10 Pin T3-2-048 50 11 Washer ICF/STD 3-2-003 50 12 Split Cotter T-3-2-632 50 13 Pin T-3-2-648 8 14 Washer ICF/STD 3-2-103 24 15 Split Cotter T-3-2-632 8 16 Pin for lever Hanger ICF/SK-3-2-179 16 17 Pin for safety wire rope WT AC3/3-2-307 32 18 Plain washer M20 IS: 2016-67 T.2type A 32 19 Split cotter EMU-3-2-048 32 20 Brake beam T-3-2-804 8 21 Safety wire rope T-3-2-651 16 22 Safety straps fixing Arrangement WT AC-3-2-304 8 In 13 t axle load bogie the four lever used in bogie brake rigging are each with lever ratio of 1:1 and hence the total Mechanical advantage in a bogie is 4. The components details of 13 t bogie are given in table 3.4 (Refer ICF drawing No. T-3-2- 601). Table 3.4 Sr.No. Description Ref. Drg. NO (ICF) Quantity 1 Brake Head & block complete T-3-1-601 16 2 Brake Beam T-3-1-602 8 3 Long lever T-3-2-605 8 4 Short lever T-3-2-604 8 5 Pull rod T-3-2-607 4 6 Pull rod T3-2-616 2 7 Adjusting Link T-3-2-609 2 8 Lever Hanger T-3-2-611 16 9 Safety Strap T3-2-612 4 10 Safety Strap T-3-2-621 4 11 Pin T3-2-048 8 12 Pin T3-2-048 50 13 Hex head screw ½" BSWx 38 BS :3083 –64 64 14 Spring Washer M-12 IS: 3063-72 64 15 Hex. Nut ½” BSW BS:1083-65 64 16 Washer DL-0-5-034 50 17 Washer DL-0-5-034 24 18 Pin for lever Hanger ICF/SK-3-2-179 16 19 Split cotter T-3-2-632 50 Chapter 3, Page 9 of 36 Maintenance Manual for BG Coaches of ICF design Bogie i) CONVENTIONAL AIR BRAKE COACH POWER CAR (refer figure 3.7) TYPE OF COACH BUILDER TARE WEIGHT IN % OF BRAKING TONNES POWER CAR TO ICF 53.7 118 WLRRM6-9-0-601 HIGH CAPACITY ICF 60 105.6 POWER CAR ii) CONVENTIONAL AIR BRAKE COACH SELF GENERATING AC COACHES (refer figure 3.8) TYPE OF COACH BUILDER TARE WEIGHT IN TONNES % OF BRAKING WGACCW ICF 50.0 114.8 RCF 49.1 120.9 WGACCN RCF 50.1 118.6 WGSCZAC ICF 49.3 123.7 WGFAC ICF 49.7 119.5 WGFSCZAC ICF 50.0 118.8 Levers for Power car & self generating AC coaches Sr. No. Size Shape/Drg. Types of coaches fitted Drawing no. 1. 282 x 205 POWER CAR TO WLRRM6-9-0- SK-93373 601, HIGH CAPACITY POWER & SK-93371 CAR, WGACCW, WGACCN, WGSCZAC, WGFAC, WGFSCZAC 2. 245 X 178 -DO- -DO- iii) CONVENTIONAL AIR BRAKE COACH NON AC COACHES (refer figure 3.9) Levers Sr. No. Size Shape/Drg. Types of coaches fitted Drawing no. 1. 230 X 230 GS,FC,SLEEPER, SLR, Second SK-93372 day coach, SCNLR, PANTRY CAR 2. 200 X 200 -DO- -DO- TYPE OF COACH BUILDER TARE WEIGHT IN TONNES % OF BRAKING GENERAL SECOND ICF 36 120 CLASS RCF 37.4 115.5 SECOND DAY COACH ICF 37 116.7 RCF 37.3 115.8 SLEEPER ICF 39.5 109.3 RCF 39.45 109.5 FIRST CLASS ICF 41.8 103.3 SLR ICF 40.6 106.4 RCF 40.0 108.0 SCNLR ICF 41.0 105.3 PANTRY CAR ICF 41.3 104.6 Chapter 3, Page 10 of 36 Maintenance Manual for BG Coaches of ICF design Bogie 282 245 245 245 178 178 205 178 2,896±1 CONVENTIONAL AIR BRAKE COACH (POWER CAR) RDSO DRAWING NO. SK-93373 FIGURE 3.7 282 245 245 245 178 178 205 178 2,896±1 CONVENTIONAL AIR BRAKE COACH SELF GENERATING AC COACHES RDSO DRAWING NO. SK-93371 FIGURE 3.8 Chapter 3, Page 11 of 36 Maintenance Manual for BG Coaches of ICF design Bogie 312b Bogie Mounted Brake Rigging Bogie brake rigging has been modified to incorporate a total mechanical advantage of 7.644 per bogie for non-ac coaches and 8.40 per bogie for ac coaches. The components of bogie mounted air brake (16 t bogie) to ICF drawing no. WTAC4-3-3-401 is given in table 3.5. Table 3.5 Sr.No. Description Ref. Drg. No. (ICF) Quantity 1 Brake Head & block complete (LH) T-3-1-801 8 2 Brake Head & Block complete (RH) T-3-1-801 8 3 Brake beam T-3-2-650 8 4 Safety wire rope T-3-2-651 16 5 Lever WTAC4 -3-2-402 8 6 Lever WTAC4 -3-2-402 8 7 Lever Hanger WTAC4 -3-2-402 8 8 Pull rod WTAC4 -3-2-402 8 9 Brake block Hanger T3-2-645 16 10 Pin T-3-2-648 44 11 Plain Washer ICF/ISD 3-2-003 64 12 Split cotter T-3-2-632 52 13 Pin T3-2-648 4 14 Plain Washer ICF/STD 3-2-003 4 15 Pin T-3-2648 4 16 Pin for lever Hanger T-3-2-801 16 17 Pin for Safety wire rope WT AC3 –3-2-307 32 18 Pin Washer M 20 IS: W 16-67 32 19 Split cotter EMU-3-2-048 32 The components of bogie mounted air brake (13 t bogie) to ICF drawing no. T-3-2-801 is given in table 3.6 Table 3.6 Sr. No. Description Ref. Drg. NO ICF) Quantity 1 Brake Head & block complete (L.H. Assembly) T-3-1-801 4 2 Brake Head & block complete (R.H. Assembly ) T-3-1-801 4 3 Brake beam T-3-1-804 4 4 lever T-3-1-802 4 5 lever T-3-1-802 4 6 lever Hanger T-3-1-802 4 7 Pull rod T-3-2-802 2 8 Brake block Hanger T-3-1-645 8 9 Pin T3-2-648 22 10 Plain Washer ICF/STD-3-2-103 32 11 Split Cotter T-3-2-632 26 12 Pin T-3-2-648 2 13 Plain Washer ICF/STD 3-2-103 2 14 Pin T-3-2-648 2 15 Pin for lever Hanger T-3-2-802 8 16 Pin for safety wire rope WFT AC3/3-2-307 16 17 Plain washer M20 IS: 2016-67 16 18 Split cotter EMU-3-2-048 16 19 Safety wire rope T-3-2-651 8 Chapter 3, Page 12 of 36 Maintenance Manual for BG Coaches of ICF design Bogie i) AC COACHES WITH BOGIE MOUNTED AIR BRAKE CYLINDER (refer figure 3.10) Levers Sr. Size Shape/Drg. Types of coaches fitted Drawing no. No. 1. 366 x 174 WGSCZAC, WGSCWAC, SK-98032 WGFAC, WGFSCZ, WSCZAC, WSCWAC, WFAC, WCBAC 2. 311 X 148 -DO- -DO- 3. 412 -DO- -DO- TYPE OF COACH TARE WEIGHT IN TONNES % OF BRAKING WGSCZAC 50.95 40.56 WGSCWAC 52.10 39.66 WGFAC 49.90 41.41 WGFSCZ 50.00 41.33 WSCZAC 48.90 42.26 WSCWAC 49.40 41.83 WFAC 46.20 44.73 WCBAC 47.90 43.14 ii) NON - AC COACHES WITH BOGIE MOUNTED AIR BRAKE CYLINDER (refer figure 3.11) Levers Sr. Size Shape/Drg. Types of coaches fitted Drawing no. No. 1. 302 X 158 GS,SCN,SDC,WCB, SLR, WFC SK-98027 2. 256 X 134 -DO- -DO- 3. 405 -DO- -DO- TYPE OF COACH TARE WEIGHT IN TONNES % OF BRAKING GS 36.00 52.23 SCN 37.55 50.08 SDC 36.50 51.52 WCB 40.40 46.54 SLR 40.60 46.32 WFC 41.80 44.99 Chapter 3, Page 13 of 36 Maintenance Manual for BG Coaches of ICF design Bogie 31 1 36 6 31 1 412 36 6 412 148 174 14 8 174 2896±1 AC COACHES WITH BOGIE MOUNTED AIR BRAKE CYLINDER P (FITTED WITH K TYPE COMPOSITION BLOCK) RDSO DRAWING NO. SK-98032) FIGURE 3.10 256 302 405 256 405 30 2 13 4 158 13 4 158 (FITTED WITH K TYPE COMPOSITION BLOCK) RDSO DRAWING NO. SK-98027 2,896±1 NON - AC COACHES WITH BOGIE MOUNTED AIR BRAKE CYLINDER P FIGURE 3.11 Chapter 3, Page 14 of 36 Maintenance Manual for BG Coaches of ICF design Bogie 313 EQUALISING STAYS 316a Washing Plant This device has been provided on i) Remove all the oil from the side bogies between the lower spring bearer oil bath. plank and the bolster to prevent ii) Wash the bogie with high lateral thrust on the bolster springs pressure hot water jet to remove which have not been designed to take all dust, mud, scales, grease and the lateral forces. These links have other muck without damaging pin connections at both ends and, the base primer coating. therefore, can swivel freely. (see figure 3.13) After washing and drying, roll the bogies to dismantling line. 314 BOLSTER SPRING SUSPENSION HANGERS (BSS HANGERS) 316b Dismantling In the secondary suspension, the i) Make sure that the vent screws bolster is supported on helical coil are opened. Lift the bogie frame springs which are placed on the lower along with the bolster using spring plank. The lower spring plank overhead crane till all the eight is suspended from the bogie side axle guides disengage from the frame through BSS hangers on lower spring seats. hanger blocks. (see figure 3.14) ii) Lower the bogie frame and bolster on to the shop floor. 315 SHOCK ABSORBERS iii) Remove and collect the axle box guide components and helical Hydraulic shock absorbers with springs in respective bins/ pallets capacity of ± 600 kg at a speed of 10 and send to washing plant for cm/sec. are fitted to work in parallel thorough cleaning. with the bolster springs to provide iv) Wheel sets must be first cleaned damping for vertical oscillations. thoroughly in the washing plant and then sent to wheel shop. 316 WORKSHOP MAINTENANCE- v) Remove vertical shock absorber BOGIE SHOP and send to shock absorber maintenance section. MAINTENANCE OF BOGIES vi) Disconnect anchor links. (Flow Diagram) Dismantle bolster suspension hangers by placing a dead LIFTING WASHING BOGIE SERVICE PLANT SHOPS weight on the bogie frame and SHOP SHOP by using a jack. 1 2 (Fitting shop 3 5 & vii) Disconnect equalising stays. Lift 9 4 Smith shop) the bolster off the bolster springs 7 8 and remove the bolster springs. 10 6 viii) Collect anchor links, equalising stays, bolster spring suspension 1. Coach lifting (BSS) hanger pins, BSS hanger 2. Bogie cleaning blocks (stones), BSS hangers, 3. Bogie dismantling pins of equalising stays, brake 4. Component cleaning rigging components and bolster 5. Attention to components springs into respective bins/ 6. Repair of components pallets and send to washing plant 7. Bogie assembly for thorough cleaning. 8. Load testing and adjustment ix) Send the bogie frame, bolsters, 9. Lowering of coach and lower spring planks to 10. Final adjustment washing plant for thorough cleaning and drying. Figure 3.12 Transport the cleaned and dried bogie After lifting the coach body (refer frame, bolster and spring planks to para 105 of chapter ‘Coach’), roll out inspection and repair stands. Place the the bogies and send them to bogie bogie frame on repair stands in the washing plant in bogie shop. inverted position. Chapter 3, Page 15 of 36 Maintenance Manual for BG Coaches of ICF design Bogie Bracket on Lower Spring Beam 3 6 3 2 3 3 1 5 Bracket on Bogie Bolster 4 3 134 526 67 200 7 263 3 3 3 3 5 7 6 5 672 No. off per ITEM Description & assembly dimensions 7 RIB 120x30x5 2 EQUALISING STAY FOR LOWER SPRING BEAM 6 2 RIB 200x225x5 (16.25 t Axle Load Bogie) (RDSO Sketch 88105) 5 BUSH%%c 42/32 x32L 8 4 BODY %%c 60x134 1 3 BOSS %%c 60/40 x32L 2 2 1 TUBE %%c 50 BOREx462 FIGURE 3.13 1 TUBE %%c 50 BOREx640 1 ) Chapter 3, Page 16 of 36 Maintenance Manual for BG Coaches of ICF design Bogie COMPONENTS SIZE-NEW CONDEMNING WEAR IN mm SHOP ISSUE SIZE 9.5 8 1.5 8.50 HANGER BLOCKPTOP & BOTTOM PIN 37 35.5 1.5 36.00 HANGER 38.4 36.5 1.5 37.00 26 R1 9.5 - 0.25P- HANGER AND HANGER BLOCKS 450.5 FIGURE 3.14 Chapter 3, Page 17 of 36 Maintenance Manual for BG Coaches of ICF design Bogie 316c Attention to Bogie Frame i) Check the bogie thoroughly for for axle guide and 0.5 mm for any possible cracks. Check the BSS bracket bush), damaged or BSS brackets, axle guides, area cracked, they should be surrounding the BSS bracket and replaced. axle guide and all the welding iii) Bent or damaged suspension joints of bogie frame. If cracks straps should be attended to as are detected, hold the bogie required. frame in bogie manipulator. iv) Safety wire rope arrangement After proper gouging, weld the and safety straps should be used cracks and finish by grinding. for brake beams as per revised ii) If the BSS brackets or axle RDSO instructions. guides are worn (limits: 1 mm Table 3.7 Suggested BSS bracket and axle 13t bogies 16.25t bogies guide alignment gauges Longitudinal gauge for BSS 1400±± 1.0 mm (700± ± 0.5 mm 1500±± 1.0 mm (750± ±0.5 mm brackets from longitudinal center-line) from longitudinal center-line) Transverse gauge for BSS brackets 2159 ±1.0 mm 2159 ± 1.0 mm Diagonal gauge for BSS brackets 2573 ±1.0 mm 2629 ± 1.0 mm Longitudinal gauge for axle guide ± 1.0 mm (equidistant from 570± 570 ± 1.0 mm (equidistant from center-line of axle) center-line of axle) Transverse gauge for axle guide 2159±± 1.0 mm 2159±± 1.0 mm Diagonal gauge for axle guide 3612±± 1.0 mm 3612±± 1.0 mm Distance between BSS bracket and ± 1.0 mm 463± ±1.0 mm 413± adjacent axle guide Longitudinal gauge for suspension ± 1.0 mm (equidistant 870± ±1.0mm (equidistant from 870± strap from center-line of axle) center-line of the axle) v) Check the squareness and vii) The relevant axle guides should alignment of BSS brackets and be cut using special gouging axle guides with the help of nozzles (PO 18 or 19) to prevent transverse, longitudinal, undercutting of bogie frame. diagonal gauges and straight Axle guides found bent/cracked edge. Axle guide alignment should also be cut out and should be checked with replaced. reference to the BSS brackets viii) Weld the new axle guides with and recorded in RDSO the help of axle guide welding dimensional check report. A fixture, if the axle guides are coordinate measuring machine, damaged or worn. Check the preferably CNC type, can do alignment of new axle guides these checks accurately. with respect to other axle guides vi) If the BSS brackets do not lie using master gauges and straight within the tolerances, relocate edge. Any slight discrepancy in one or more BSS brackets with location can be rectified by correct alignment. After suitable local heating of the ensuring correct alignment of the frame. After complete BSS brackets, measure the rectification, record important location of the axle guide from dimensions in RDSO the BSS brackets and record in dimensional check report. (See RDSO dimensional check report. fig. 3.15 a&b, fig. 3.16 a&b) If the measurements deviate from the standard measurements, ix) Replace the BSS bracket bushes relocate mis- aligned pair of axle and pins if they were damaged guides. or worn. Chapter 3, Page 18 of 36 Maintenance Manual for BG Coaches of ICF design Bogie a DIMENSIONAL CHECK REPORT b FOR AC & POWER CAR BOGIE FRAME C D 35 z + 413 - 1 F E 876 g 1 g2 2 61 g3 K 3 g4 N 2159 T Q + 0.5 - 0.5 26 29 - + + 1 1752 1752 - + 1 - + 1 - 1 - 35 P + M S J + 1 - 876 - 0.5 - 0.5 C.L. OF AXLE C.L.OF AXLE + + 876 R O L 750 570 I G 1500 H d c g 8 g 7 + - 0.5 g 6 + 1 - g 5 2896 z + 1 - + - 1 570 + 1 - A B 1. BOGIE SIDE FRAME & HEAD STOCK CENTRES ON EITHER SIDE OF THE BOGIE FRAME AS SHOWN THUS WILL BE PERMANENTLY PUNCH MARKED IN CONSPICUOUS MANNER.TO ENSURE THIS 2mmTHICK X 25mmWIDE STRIP SHOULD BE WELDED AT THE LONGITUDINAL AND TRANSVERSE CENTRES OF THE BOGIE FRAME.PUNCH MARK SHOULD BE PUNCHED ON THIS STRIP ACCORDINGLY. 2. g TO 1 g REPRESENT 8 LOCATIONS OF BOGIE GUIDES. 3. E,F,G & H REPRESENT LOCATIONS OF SUSPENSION BRACKETS FOR BOLSTER SUSPENSION ARRGT. 4. BOLSTER SUSPENSION BRACKET PIN HOLES E,F,G,H SHALL BE LOCATED AT 750 + 0.5mm FROM THE TRANSVERSE CENTRE LINE PUNCH MARKS ON BOGIE - SIDE FRAME & CHECK IT AS PER FIG.-3.15b. 5. WELDING JOINT SHALL NOT COME UNDER THE BOGIE GUIDE. 6. NO INACCURACY IN LOCATION OF HANGER BRACKET AND THE ALIGNMENT OF HOLES IN THE BRACKETS WILL BE PERMITTED. ICF DRG. WTAC - 0-3-301 FIGURE-3.15a 3 SHEET 1 OF 2 Maintenance Manual for BG Coaches of ICF design Bogie DIMENSIONAL CHECK REPORT FOR BOGIE FRAME (AC TYPE) No. …………………. ICF DRG. NO. WTAC3 0-3-301 Measuring Nominal Size Actual Size Variation Measuring Nominal Size Actual Size Variation Point (mm) (mm) (mm) Point (mm) (mm) (mm) E -F 1500 ± 1.0 I-J 876 ± 0.5 G -H 1500 ± 1.0 J-K 876 ± 0.5 E -G 2159 ± 1.0 L-M 876 ± 0.5 F -H 2159 ± 1.0 M-N 876 ± 0.5 E -H 2629 ± 1.0 O-P 876 ± 0.5 F -G 2629 ± 1.0 P- Q 876 ± 0.5 a 413 ± 1.0 R-S 876 ± 0.5 b 413 ± 1.0 S-T 876 ± 0.5 c 413 ± 1.0 I-K 1752 ± 1.0 d 413 ± 1.0 L-N 1752 ± 1.0 g1 - g2 570 ± 1.0 O-Q 1752 ± 1.0 g3 - g4 570 ± 1.0 R-T 1752 ± 1.0 Figure - 3.15b SHEET 2 OF 2 g5 - g6 570 ± 1.0 g1 - g6 3612 ± 1.0 g7 - g8 570 ± 1.0 g2 - g5 3612 ± 1.0 z -F 750 ± 0.5 g3 - g8 3612 ± 1.0 z -H 750 ± 0.5 g4 - g7 3612 ± 1.0 Maintenance Manual for BG Coaches of ICF design Bogie DIMENSIONAL a CHECK REPORT b FOR NON AC BOGIE FRAME C D 35 z + 1 463 - F E 876 g 1 g2 12 g 3 K 36 g4 N 2159 T Q - 0.5 + 0.5 + - + 1 1752 1752 - + 1 - - 1 25 - 1 + 35 P + 73 M S J + 1 - 876 - 0.5 - 0.5 C.L. OF AXLE C.L. OF AXLE + + 876 R O L 570 I G H d c g 8 g 7 + 0.5 - g6 + - 1 g 5 2896 700 z + 1 + - - 1 570 1400 + - 1 A B 1. BOGIE SIDE FRAME & HEAD STOCK CENTRES ON EITHER SIDE OF THE BOGIE FRAME AS SHOWN THUS WILL BE PERMANENTLY PUNCH MARKED IN CONSPICUOUS MANNER.TO ENSURE THIS 2mmTHICK X 25mmWIDE STRIP SHOULD BE WELDED AT THE LONGITUDINAL AND TRANSVERSE CENTRES OF THE BOGIE FRAME.PUNCH MARK SHOULD BE PUNCHED ON THIS STRIP ACCORDINGLY. 2. g TO 1 g REPRESENT 8 LOCATIONS OF BOGIE GUIDES. 3. E,F,G & H REPRESENT LOCATIONS OF SUSPENSION BRACKETS FOR BOLSTER SUSPENSION ARRGT. 4. BOLSTER SUSPENSION BRACKET PIN HOLES E,F,G,H SHALL BE LOCATED AT + 700 0.5mm - FROM THE TRANSVERSE CENTRE LINE PUNCH MARKS ON BOGIE SIDE FRAME & CHECK IT AS PER FIG.-3.16b. 5. WELDING JOINT SHALL NOT COME UNDER THE BOGIE GUIDE. 6. NO INACCURACY IN LOCATION OF HANGER BRACKET AND THE ALIGNMENT OF HOLES IN THE BRACKETS WILL BE PERMITTED. R.D.S.O./CARR./SK93280 FIGURE-3.16a SHEET 1 OF 2 Maintenance Manual for BG Coaches of ICF design Bogie DIMENSIONAL CHECK REPORT FOR BOGIE FRAME (AC TYPE) No. …………………. RDSO/SK/93280 Measuring Nominal Size Actual Size Variation Measuring Nominal Size Actual Size Variation Point (mm) (mm) (mm) Point (mm) (mm) (mm) E -F 1400 ± 1.0 I-J 876 ± 0.5 G -H 1400 ± 1.0 J-K 876 ± 0.5 E -G 2159 ± 1.0 L-M 876 ± 0.5 F -H 2159 ± 1.0 M-N 876 ± 0.5 E -H 2573 ± 1.0 O-P 876 ± 0.5 F -G 2573 ± 1.0 P- Q 876 ± 0.5 a 463 ± 1.0 R-S 876 ± 0.5 b 463 ± 1.0 S-T 876 ± 0.5 c 463 ± 1.0 I-K 1752 ± 1.0 d 463 ± 1.0 L-N 1752 ± 1..0 g1 - g2 570 ± 1.0 O-Q 1752 ± 1.0 g3 - g4 570 ± 1.0 R-T 1752 ± 1.0 Figure - 3.16b SHEET 2 OF 2 g5 - g6 570 ± 1.0 g1 - g6 3612 ± 1.0 g7 - g8 570 ± 1.0 g2 - g5 3612 ± 1.0 z -F 700 ± 0.5 g3 - g8 3612 ± 1.0 z -H 700 ± 0.5 g4 - g7 3612 ± 1.0 Maintenance Manual for BG Coaches of ICF design Bogie x) Replace the anchor link brackets if hanger bracket for renewal. Replace the bushes they are worn or damaged. The M12 in the brake hanger brackets at every POH. threaded hole should be cleaned and xii) Replace the brake lever hanger checked and attended to, as required. brackets if the holes are xi) Bent, damaged, or worn brake hanger oblong/worn or damaged. brackets should be replaced. If the holes are xiii) Replace all the axle box housing not aligned/located as per drawing, replace the crown bolt and screwing piece brackets. Use single piece design of brake by rubber stoppers. Table 3.8 WEAR LOCATIONS (Dimensions in mm) Part name Wear location Drg. Nos. Brake hanger bracket bush 32 H7 Hole +0.025/-0.00 T-0-3-669 & WTAC3-0-3-316 Brake hanger bracket 35 gap T-0-3-675 Brake hanger bracket C.D.1752 +1.0 T-0-3-675 Axle guide 115g6 -0.034/+0.00 diameter T-0-3-670 alt. 2/f Axle guide 120 diameter T-0-3-670 alt. 2/f BSS bracket bush 38 dia. Hole T-0-3-626 alt. 9/h Pin for BSS 37 diameter T-0-5-637 alt. m/12 Bracket for anchor link 25+0.021/-0.0 slot T-0-3-635 alt. j/16 Brake lever hanger bracket 32 dia hole T-0-3-631 & T-0-3-632 xiv) The locations where the repairs 316d Attention to Bogie Bolster have been carried out should be Arrangement cleaned to bare metal and (Refer drg. no.WTAC3-0-5-301 & painted with two coats of primer WLRRM-0-4-001 for 16.25t bogie and to IS:2074 to a minimum Dry T-0-5-601 & T-0-4-601 for 13t bogie) Film Thickness (DFT) of 50 i) Check the bolster for twist, microns followed by one coat crack, corrosion, etc. Repair or of anti-corrosive Black Japan replace the bolster as required, Type-B to IS:341 to a DFT of and attend to the lug as required. 35 microns, after which entire ii) Repair or replace the equalising bogie frame is to be given one stay bracket if found bent, coat of Black Japan Type-B to damaged, or corroded. IS:341 to a minimum DFT of 35 microns. Table 3.9 Part name Wear location (all dimensions in mm) Drg. Nos. Side bearer wearing plate 10 mm thick top wearing surface T-0-5-648 alt 10/L Side bearer wearing piece 45 mm thick bottom wearing surface T-0-5-649 alt 17/h Bolster Centre Pivot sleeve Hole 155 H7 (+0.040/-0.0) c9(-0.2/-0.3) T-0-6-606 Centre-Pivot silent block Hole 140 H7 (+0.040/-0.0) T-0-6-606 sleeve Centre Pivot silent block Hole dia. 90 +0.15/+0.30 T-0-6-611 alt. 16/p Centre Pivot silent block Hole dia. 75 +0.1/+0.2 -do- Centre Pivot silent block Out side dia 140 U6 (+0.195/+0.170) -do- Centre Pivot pin Out side dia. 90 c9(-017/-0.267) & 75 c9 T-0-6-602 alt.s (-0.150/-0.257) (w) Maintenance Manual for BG Coaches of ICF design Bogie iii) Replace the anchor link bracket xiii) The locations where the repairs by holding in bolster repair have been carried out or found fixture, if found worn or corroded should be cleaned to damaged. bare metal and painted with two iv) Replace the bushes in the stay coats of primer to IS:2074 to a rod brackets, if found worn or minimum Dry Film Thickness damaged. (DFT) of 50 microns followed v) Replace the centre pivot silent by one coat of anti-corrosive block if found worn, damaged or Black Japan Type-B to IS:341 rubber has perished. to a DFT of 35 microns, after vi) Replace the centre pivot sleeve if which entire bogie bolster is to worn or damaged or corroded. be given one coat of Black vii) Replace the bolster centre pivot Japan Type-B to IS:341 to a sleeve if worn or cracked. minimum DFT of 35 microns. viii) Replace the rubber sealing cap 316e Anchor Link of centre pivot silent block, if torn or damaged or perished. (Ref: Drawing No. T – 0 – 7 – 603 ix) Replace the centre pivot pin if and T – 0 – 7 –607) worn or cracked. Chalk test the centre pivot pin ‘in position’ or i) Replace the anchor link, if worn ‘off position’ to detect cracks. or corroded. Repair the anchor x) Force fit between silent block link, if found cracked (normally and sleeve and tolerance on at weld joints) under magna flux pivot pin, i.e., c9 (-0.18/-0.27) testing, by re welding after should be maintained in every gouging. Refit new silent block POH/IOH. in every POH. xi) Ensure that there is no leakage of oil from the side bearer oil- ii) Replace the silent block, if the bath welding portion. Replace rubber is perished (indicated by the hard ground plate in side fretting) or loose in the anchor bearer, if worn more than 1.0mm link housing, or the silent block (ref. table 3.2) in thickness or pin is worn thin or loose in ridges formed on the plate. silent block rubber. The silent Replace the bronze wearing block should be force fit in the piece for side bearer, if worn anchor link and the silent block more than 1.5 mm in thickness. pin should be slide fit in the Sharp edges on wearing piece anchor link bracket. should be rounded off before re- use. Ensure that the dust seal iii) The locations where the repairs cover sits effectively all around have been carried out should be without any gap on the oil-bath cleaned to bare metal and and the sleeves slide freely on painted with two coats of primer the guide to ward off dust and to IS: 2074 to a minimum Dry moisture coming in contact with Film Thickness (DFT) of 50 the oil. Clean refilling passages microns followed by one coat and deficient or damaged oil of anti-corrosive Black Japan refilling cups with caps and Type-B to IS:341 to a DFT of pipes should be replaced. The oil 35 microns, after which entire filling plugs should be well anchor link is to be given one secured by chain to prevent it coat of Black Japan Type-B to from dropping. IS:341 to a minimum DFT of 35 xii) Repair or replace the bent or microns. damaged or broken equalising stay rod safety loops. Table 3.10 (all dimensions in mm) Part name Wear location Drg. No. Anchor link silent block pin 25 mm -0.012/-0.052, thick ends RDSO-Sketch-94101 alt.1 Anchor link silent block Outer dia. 90.5 +0.05/+0.025 RDSO-Sketch-94101 alt.1 Anchor link housing Hole dia 90.5 +0.015/ -0.03 T-0-7-605 Maintenance Manual for BG Coaches of ICF design Bogie 316f Equalising Stay Rod and Pins iii) Replace the following parts: (Small & Big) § bushes of BSS brackets if (Ref: Drawing No. RDSO Sk-88105 worn beyond permissible Alt.2 for 16.25t bogie and Sk-88018 limits Alt.6 for 13t bogie) § equalising stay bracket bushes i) Hot dip galvanised equalising