Maintenance Manual for BG Coaches of ICF Design PDF
Document Details
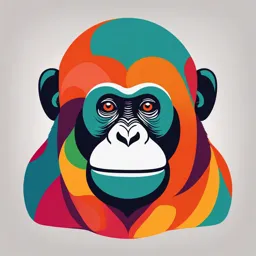
Uploaded by ImaginativePeachTree
STC/JHS
Tags
Related
- Maintenance Manual for BG Coaches of ICF Design (PDF)
- Maintenance Manual for BG Coaches of ICF Design PDF
- Maintenance Manual for BG Coaches of ICF Design PDF
- Train Lighting and Maintenance Schedules of Non AC Coaches PDF
- Maintenance Manual for BG Coaches of ICF Design PDF
- Maintenance Manual for BG Coaches of ICF Design PDF
Summary
This document is a maintenance manual for BG coaches of ICF design. It details various aspects of maintenance procedures, including repair procedures, inspection, and maintenance of various parts of the coach. The document lists different parts of the coach and provides details on how to conduct the necessary checks, repairs and maintenance. It provides detailed technical instructions for railway coaches.
Full Transcript
Maintenance Manual for BG coaches of ICF design Appendix APPENDIX D LIST OF RDSO TECHNICAL PAMPHLETS S.No. RDSO No. Descri...
Maintenance Manual for BG coaches of ICF design Appendix APPENDIX D LIST OF RDSO TECHNICAL PAMPHLETS S.No. RDSO No. Description 01 C-6803 Maintenance and repair procedure for hydraulic shock absorbers used on coaching stock. 02 C-6904 Instructions for repair of corroded ICF coaches BG 03 C-7103 Instructions for examina tion and maintenance of bogies and undergear of coach nominated to run at sanctioned speed of 110 kmph (BG). 04 C-7301 Direct admission valve for passenger coaches maintenance instructions. 05 C-7511 Instructions for adjustment of buffer height of ICF built BG coaches in workshops and depots. 06 C-7512 Hindi version of C-7511, adjustment of buffer height of ICF BG coaches. 07 C-7601 Description of water raising apparatus and instructions for filling water in coaches fitted with under slung water tanks. 08 C-7602 Instructions for corrosion repairs ICF built BG coaches. 09 C-7607 Instructions for inspection, repair and manufacturing procedure for helical springs of ICF & BEML built coaches. 10 C-7703 Instructions for inspection and maintenance of roller bearing axle boxes of BG/ICF bogies.. 11 C-7717 Instructions for maintenance of axle box guide arrangement for mainline ICF built coaches (BG/MG) 12 C-7807 Instruction for maintenance of bogie and under gear of Rajdhani express coaches (BG) (for shops and maintenance depots) 13 C-7808 Hindi version of C-7807, maintenance of bogie and undergear of Rajdhani coaches. 14 C-7809 Instruction for inspection, repair and manufacturing procedure for helical springs of ICF & Jessop's EMU stock. 15 C-7817 Instructions for inspection and maintenance of direct mounted roller bearing axle boxes of BG/ICF bogies. 16 C-7901 Maintenance and repair procedure of Gabriel vertical hydraulic shock absorber. 17 C-7902 Hindi version of C-7901, maintenance and repair procedure Gabriel shock absorber. 18 C-7907 Wheel and axle manual 19 C-8105 Schedule of requirements for asbestos sheets roof ceiling of railway passenger coaches. 20 C-8107 Schedule of requirements for nylon bush for brake gear for mainline coach. 21 C-8108 Hindi version of C-8107, nylon bushes for coaches 22 C-8207 Schedule of requirement for FRP Battery Box. Maintenance Manual for BG coaches of ICF design Appendix S.No. RDSO No. Description 23 C-8211 Schedule of requirements for rubberised coir cushion 24 C-8215 Schedule of requirements for plastic guide bush for axle box guide of ICF/BG bogie (tentative) 25 C-8217 Schedule and requirements for aluminum chequered sheets for use as flooring material on coaching stock. 26 C-8219 Fibre glass reinforced plastic in railway coaches 27 C-8303 Technical specification for hot coiled helical springs used Rev. I on main line coaches and EMU stock. 28 C-8305 Anti-pilferage measures for compartment, lavatory and other coaching stock fittings. 29 C-8409 Tentative schedule of requirements for sheet moulding compound to be used for manufacture of FRP products for passenger coaches. 30 C-8415 Tentative schedule of requirements for FRP seat cum back tests of Indian railway coaches. 31 C-8419 Technical specification for hot coiled helical springs used Rev. I on maintenance coaches & EMU stock. 32 C-8421 Tentative schedule of requirements for FRP wall protector for bath room of coaching stock of IR (Sk. -83114) 33 C-8515 Schedule of requirements for flexible PVC flooring for passenger coaches (tentative) 34 C-8517 Schedule of requirements for anaerobic adhesive for use on coaching stock (tentative). 35 C-8518 Hindi version of C-8517, anaerobic adhesive for use in coaches. 36 C-8519 STR for air brake equipment for coaching stock. 37 C-8527 Roller bearing specification 38 C-8531 Particular specification for BG (1676 mm) all metal integral light weight self -generating Ist class air conditioned coaches. 39 C-8533 Particular specification for BG all metal light weight coaches. 40 C-8605 STR for nylon guide roller/wearing piece for retractable footplate 41 C-8606 Hindi version of C-8605, nylon guide roller/wear piece for retractable foot plate. 42 C-8623 STR for decorative thermosetting synthetic resin bonded laminated sheets. 43 C-8625 Note on cleaning media for us e in bearing cleaning plants. 44 C-8626 Procedure for manual ARC welding of wear plates (IRS: R-65-78) 45 C-8629 Report of committee on reduction of weight of coaches. 46 C-8703 Specification for shock absorber. 47 C-8805 Instructions for inspection/maintenance of air brake equipment on passenger coaches. Maintenance Manual for BG coaches of ICF design Appendix S.No. RDSO No. Description 48 C-8812 Schedule of requirements for UIC type elastomer flange connections for intercommunication between passenger coaches. 49 C-8903 Schedule of requirement for hot cases operated by liquefied petroleum gas for installation in Rly. pantry cars. 50 C-8906 Schedule of technical requirements for vestibule canvas cloth to be used in passenger coaches. 51 C-8910 Schedule of technical requirements for direct admission valve. 52 C-8914 Schedule of requirements for flexible load bearing polyurethane foam to be used in berth and seats of passenger coaches. 53 C-9001 Procedure for laying PVC flooring in passenger coaches. 54 C-9005 Water raising system and instruction for filling water for air braked coaches 55 C-9009 Description of water raising system to SK-86209 and instructions for filling water for air braked coaches. 56 C-9011 Quality assurance specification for 'L' type Ferrodo quality 89/24 composition brake blocks for passenger trains. 57 C-9019 Schedule of technical requirement for water purifier. 58 C-9101 Specification for electric train set. 59 C-9103 Schedule of technical requirements for plastic sheets (filled PVC) for use in interior roof ceiling of passenger coaches. 60 C-9105 Schedule of technical requirements for FRP axle box front covers for all coil ICF type bogies for passenger coaches (BG) 61 C-9121 Schedule of requirements for push cock (tentative) 62 C-9123 Schedule of requirements for plast ic lavatory chute (tentative). 63 C-9125 Schedule of requirements for plastic packing ring (tentative). 64 C-9202 Technical specification for fabricated bogie frame/bolster for coaching stock. 65 C-9203 Schedule of requirements for plastic brake gear bushes for passenger coaches (ACETAL) 66 C-9206 Instructions for operation of air brake main line passenger trains (BG) 67 C-9210 Specification for pipes and joints for Air braked coaches 68 C-9212 Guide for approval of manufacturers for supply of bolster suspension hangers for main line coaches and EMU stock. 69 C-9213 Guide for approval of manufactures for supply of screw couplings for main line coaches and wagon stock. 70 C-9303 Schedule of technical requirements for air brake system for loco hauled main line passenger stock for operational speed of 160 kmph (tentative). Maintenance Manual for BG coaches of ICF design Appendix S.No. RDSO No. Description 71 C-9307 Schedule of technical requirements of axle end locking screw used in roller bearing axle box arrangement of ICF coaches. 72 C-9309-U Specification for sliding plug doors for mainline coaching stock. 73 C-9313-U Specification for side-buffer. 74 C-9314-U Plywood specification for new Ac chair car 75 C-9318-U Specification for test scheme for stress investigation in prototype new design of BG AC coach shell. 76 C-9319 Schedule of technical requirements for development of interior roof ceiling sheet for passenger coaches. 77 C-9321 Schedule of technical requirements for development of light weight transverse upper sleeping berth to be used in AC coaches. 78 C-9322 Schedule of technical requirements for development of light weight partition walls to be used in AC coaches. 79 C-9403 Schedule of technical requirements for fibre glass reinforced (SMC) glass window frames, lavatory banzo frames and louvre sheets for use in coaches. 80 C-9406 Schedule of technical requirements for silent block for anchor link. 81 C-9407 Schedule of technical requirements for compreg laminate. 82 C-9408 Instructions for operation of air braked main line passenger trains (BG) Dec,94. 83 C-9501 Rubber buffer spring of 1030 kg. m. capacity for side buffers of BG coaches. 84 C-9502 Schedule of technical requirements for fibre glass reinforced (SMC) window guides and sills for use in coaches. 85 C-9503 Schedule of requirements for upholstery cloth for coaching stock. 86 C-9505 STR for high tensile steel screw coupling. 87 C-9509 STR for alloy steel draw hook on Railway coaches. 88 C-9511 Schedule of technical requirements for Natural Fibre Thermo-Set Composite (NFTC) sheets for roof ceiling of passenger coaches (tentative) 89 C-9601 Tentative specification for Natural Fibre composite board for use in flooring in passenger. Maintenance Manual for BG coaches of ICF design Appendix S.No. RDSO No. Description 90 C-9602 Schedule of technical requirements for decorative thermo setting synthetic resin bonded laminated sheets for use in coaching stock. 91 C-9702 Instructions for maintenance of brake system of air braked coaches fitted with bogie mounted brake cylinders and 'K' type composition blocks. 92 C-9703 Schedule of technical requirements of packing ring for axle box guide arrangement. 93 C-9704 Schedule of technical requirements for polymerised floor topping compound for flooring of coaches. 94 C-9705 Schedule of technical requirements for Ultra High Molecula r Weight Polyethylene (UHMWPE) for use in Railway coaches. 95 C-9802 Overhauling and testing of hose coupling of air brake system. 96 C-9803 Schedule of technical requirements for rubber items used in air brake components for coaching stock. 97 C-9805 Specification for flasher light for SLR (Brakes, luggage- cum-2nd class). 98 C-9807 STR for friction snubber for primary suspension of Broad Gauge mainline ICF all coil bogie for operation at max. speed of 105 kmph. 99 C-9808 Schedule of technical requirements for manufacture of brake block hanger. 100 C-9809 Specification for non-asbestos based 'K' type high friction composition brake blocks for bogie mounted mainline coaches (both AC & Non-AC coaches) 101 C-9810 Specification for asbestos based 'K' type high friction composition brake blocks for bogie mounted mainline coaches (both AC & non-AC) 102 C-9901 STR for upholstery for Ist class AC coaches and executive class chair car of Satabdi express 103 C-9903 Inspection and test scheme for primary suspe nsion of BG (1676 mm) main line ICF all coil bogie (13 t axle) for operation of maximum speed of 150 kmph. 104 C-9904 STR for insecticide paint for coach interiors (tentative) 105 C-9905 STR for specially Treated Brake Pins (Alternative to Electroplating) Maintenance Manual for BG coaches of ICF design Appendix S.No. RDSO No. Description 106 C-9906 STR for controlled Discharge Toilets for Indian Railway coaches (BG) 107 C-9907 Specification for L-type composition Brake block for main line coaches. 108 C-9908 STR for Biological Toilets in Indian Railway coaches. 109 C-9911 STR for fire retardant curtain fabric 110 C-9912 Tentative specification Natural Fibre Reinforced Panels (NFRP) for use in Railway coaches. 111 C-K013 Specification for Bogie mounted brake cylinder with inbuilt Slack adjuster for EMU and mainline passenger coaches. 112 CMI 9801 Maintenance instructions for IRY coaches fitted with IR- 20 bogies. 113 CMI 9901 Maintenance Instructions for enhanced draw gear & screw coupling (BG) of mainline coaches. 114 CMI-K003 Guidelines for interpretation of wheel defects in solid/tyred coaching/EMU wheels in open line and workshops. 115 G-92 Maintenance manual for IRSA-600 slack adjuster. 116 G-97, Amnd. Maintenance manual of Air brake System for freight stock. Slip 2, July, 2001 117 M&C/PCN/ Specification for cleaning solution. 101/2001 118 02-ABR-94 Specification for Air Brake for freight & passenger stock of Indian Railways. 119 R-64/98 STR for upper and lower rubber washers for mail line (Revised) coaches. 120 R-19/93 Wheels 121 IRS – M-41 Corrosion resistant high tensile strength steel (corton) Maintenance Manual for BG coaches of ICF design Appendix APPENDIX E STANDARD INTEGRATED MODULAR PITLINE FOR UNIFIED MAINTENANCE This has been separately issued as CAMTECH’s document no. CAMTECH/M/99/INFRA-WASHING LINE/1.1 (Please refer latest version) Maintenance manual for BG ICF coaches Appendix APPENDIX F MAINTENANCE SCHEDULES Sr. No. Schedule Particulars Primary / ‘A’ ‘B’ ‘C’ Secondary examination Primary / 1 month + 3 3 months + 7 6 months + Freq uency of Examina tion Secondary days days 15 days Maintenance Maintenance to be done at: On rake On rake at On rake at Sick line at nominated nominated nominated primary depot primary depot primary depot 1.0 Coach 1.1 Coach should be washed both from out side & inside. 1.2 Disinfect and spray insecticide at corner and crevices of - coaches after washing all coaches 1.3 Intensive cleaning of coach - 2.0 Shell 2.1 Visually check body panels/end walls for damages 2.2 Visually inspect destination boards brackets. 2.3 Visually inspect window bars for damage/missing 2.4 Examine body side doors for working/ damages 2.5 Inspect door handles for damages/missing 2.6 Inspect vestibule and its Rubber fittings for damages/missing, repair if necessary Maintenance manual for BG ICF coaches Appendix Sr. No. Schedule Particulars Primary / ‘A’ ‘B’ ‘C’ Secondary examination Primary / 1 month + 3 3 months + 7 6 months + Freq uency of Examina tion Secondary days days 15 days Maintenance Maintenance to be done at: On rake On rake at On rake at Sick line at nominated nominated nominated primary depot primary depot primary depot 2.7 Visually check vestibule fall plate, mounting brackets, pins and lock lever for ease of operation, damages/ deficiency 2.8 Thoroughly clean and remove dust, rust accumulated at - - - pillars through turn under holes with coir brush and compress air 2.9 Examine for corrosion of sole bar and other under frame - - - members with torch light or inspection lamp 2.10 Touch up damaged paint both inside & outside - - - 2.11 Check roof ventilator for damages - - - 3.0 Under frame 3.1 Visually examine centre pivot mounting bolts and attend if needed 3.2 Check condition of head stock/sole bar 3.3 Examine trough floor, turn under and other under frame - - members from underneath for corrosion 3.4 Visually inspect centre pivot cover Maintenance manual for BG ICF coaches Appendix Sr. No. Schedule Particulars Primary / ‘A’ ‘B’ ‘C’ Secondary examination Primary / 1 month + 3 3 months + 7 6 months + Freq uency of Examina tion Secondary days days 15 days Maintenance Maintenance to be done at: On rake On rake at On rake at Sick line at nominated nominated nominated primary depot primary depot primary depot 4.0 Bogie 4.1 Bogie frame 4.1.1 Examine visually the condition of bogie side frame, transom, longitudinals and all welded locations 4.1.2 Examine rubber stopper/stop screw of axle box crown for damage/missing/loose 4.1.3 Inspect axle box safety straps/loops for damage/broken/missing 4.1.4 Bolster safety straps/loops for damage/broken/missing 4.1.5 Brake hanger brackets for damages 4.1.6 Inspect safety brackets for brake hanger pins 4.1.7 Examine oil level in side bearer oil-bath and oil filling - cap, replenish oil if needed 4.1.8 Check visually BSS hanger brackets 4.1.9 Examine visually anchor link brackets 4.1.10 Examine condition of wearing piece and wearing plate - - - Maintenance manual for BG ICF coaches Appendix Sr. No. Schedule Particulars Primary / ‘A’ ‘B’ ‘C’ Secondary examination Primary / 1 month + 3 3 months + 7 6 months + Freq uency of Examina tion Secondary days days 15 days Maintenance Maintenance to be done at: On rake On rake at On rake at Sick line at nominated nominated nominated primary depot primary depot primary depot 4.2 Primary suspension 4.2.1 Visually examine axle box springs for breakage 4.2.2 Visually examine dash pot oil filling special screw for deficiency 4.2.3a Check oil leakages in dash pot through defective seals/vent screws 4.2.3b Add specified grade of oil in dash pot - 4.2.4 Visually examine axle box clearance 4.2.5 Check and attend axle guide assembly if necessary - - - 4.2.6 Check axle box clearance with gauge - - - 4.3 Secondary suspension 4.3.1 Visually examine bolster springs breakages/damages 4.3.2 Visually examine Bolster lower spring beam 4.3.3 Visually examine BSS hangers, hanger blocks, BSS pins 4.3.4 Check bolster clearance 4.3.5 Visually examine equalising stay rods and pins (small and big) 4.3.6 Visually check anchor lin ks Maintenance manual for BG ICF coaches Appendix Sr. No. Schedule Particulars Primary / ‘A’ ‘B’ ‘C’ Secondary examination Primary / 1 month + 3 3 months + 7 6 months + Freq uency of Examina tion Secondary days days 15 days Maintenance Maintenance to be done at: On rake On rake at On rake at Sick line at nominated nominated nominated primary depot primary depot primary depot 4.3.7 Examine visually the anchor link securing bolts and attend if needed 4.3.8 Visually examine Equalising stay brackets 4.3.9 Examine and attend safety loops of bolster 4.3.10 Check and attend safety loops of Equalising stay rod 4.3.11 Examine vertical shock absorbers for damages 4.4 Brake rigging 4.4.1 Check brake gear and adjust so that the piston stroke is within the limit. 4.4.2 Examine brake beams breakages/damages 4.4.3 Check and attend brake beam safety wire ropes/safety straps 4.4.4 Check and attend brake shoe head and key & replace if necessary 4.4.5 Check and replace worn brake blocks 4.4.6 Visually inspect brake hangers, brake gear pins and cotters/split pins and replace if necessary Maintenance manual for BG ICF coaches Appendix Sr. No. Schedule Particulars Primary / ‘A’ ‘B’ ‘C’ Secondary examination Primary / 1 month + 3 3 months + 7 6 months + Freq uency of Examina tion Secondary days days 15 days Maintenance Maintenance to be done at: On rake On rake at On rake at Sick line at nominated nominated nominated primary depot primary depot primary depot 4.4.7 Visually inspected damaged/missing brake gear bushes and replace if necessary 4.4.8 Check and attend brake block adjuster - 4.4.9 Examine and attend brake levers - 4.4.10 Examine and attend floating lever suspension brackets - 4.4.11 Examine lever hanger pins. 4.5 Bogie to be run out if found n ecessary during IOH and following should be done: 4.5.1 Examine and replace all the brake gear components - - - found deficient / worn out 4.5.2 Examine and replace primary and secondary suspension - - - components as required 4.5.3 Examine wheel profile and thickness and gauge if in case - - - they appear to be near condemning limit 5.0 Brake System 5.1 Air brake system 5.1.1 Conduct brake test as per rake test and attend leakages and defective components if any. Maintenance manual for BG ICF coaches Appendix Sr. No. Schedule Particulars Primary / ‘A’ ‘B’ ‘C’ Secondary examination Primary / 1 month + 3 3 months + 7 6 months + Freq uency of Examina tion Secondary days days 15 days Maintenance Maintenance to be done at: On rake On rake at On rake at Sick line at nominated nominated nominated primary depot primary depot primary depot 5.1.2 Visually inspect for damage on brake pipe, feed pipe and hose coupling. 5.1.3 Visually inspect suspension bracket for air brake equipement and anti pilferage device for any defect and rectify 5.1.4 Check passenger alarm by pulling the chain with spring Minimum 3 balance with 6.4 kg to 10 kg force coaches 5.1.5 Carry out manual brake release test to ensure proper function of release lever 5.1.6 Check and adjust brake gear to achieve correct piston stroke 5.1.7 Service application, release test of every coach of the rake to ensure full brake power 5.1.8 Carry out guard van valve test to ensure proper functioning of guard van valve. 5.1.9 Examine slack adjuster for damage and mal functioning and subsequent replacement Maintenance manual for BG ICF coaches Appendix Sr. No. Schedule Particulars Primary / ‘A’ ‘B’ ‘C’ Secondary examination Primary / 1 month + 3 3 months + 7 6 months + Freq uency of Examina tion Secondary days days 15 days Maintenance Maintenance to be done at: On rake On rake at On rake at Sick line at nominated nominated nominated primary depot primary depot primary depot 5.2 Vacuum brake System 5.2.1 Clean, grease and test alarm chain apparatus under full minimum 3 vacuum with spring balance and cleaning/checking of coaches clappet valve for leakage 5.2.2 Test entire vacuum bake system including slack adjuster and DA valve in a prescribed manner for leakage and proper functioning to ensure full brake power. 5.2.3 Conduct balance vacuum test for whole rake. - 5.2.4 Inspect train pipe and hose pipe including their cages, vacuum cylinders, siphon pipes for leakage 5.2.5 Attention to DA valve - 5.2.6 a) Testing of alarm chain apparatus b) Overhauling of alarm chain apparatus - - 5.2.7 Overhaul release valve, replace its diaphragm and sealing - - washer if necessary 5.2.8 Examine neck ring and replace if necessary - - 5.2.9 Test vacuum gauges with master gauges - - - Maintenance manual for BG ICF coaches Appendix Sr. No. Schedule Particulars Primary / ‘A’ ‘B’ ‘C’ Secondary examination Primary / 1 month + 3 3 months + 7 6 months + Freq uency of Examina tion Secondary days days 15 days Maintenance Maintenance to be done at: On rake On rake at On rake at Sick line at nominated nominated nominated primary depot primary depot primary depot 5.2.10 Testing of cylinder and train pipe joints with exhauster - under 510 mm of vacuum 6.0 Draw gear 6.1 Check and replace damage/missing split pins/cotters/rivets 6.2 Examine draw hook, draw bars, rubber pads for damages 6.3 Check condition of the screw coupling and its components and replace if required. 6.4 Ensure that wear on screw coupling shackle pins, trunion - - - pins, shackle/link holes and draw hook holes should not exceed 3mm. 6.5 Ensure that wear at any section on draw hook should not - - - exceed 10 mm. 6.6 Check condition of draw beam and locating pins on it 6.7 Examine visually draft key locking pins 7.0 Buffing gear 7.1a Visually examine buffer plungers for damage/drooping/stroke length. Maintenance manual for BG ICF coaches Appendix Sr. No. Schedule Particulars Primary / ‘A’ ‘B’ ‘C’ Secondary examination Primary / 1 month + 3 3 months + 7 6 months + Freq uency of Examina tion Secondary days days 15 days Maintenance Maintenance to be done at: On rake On rake at On rake at Sick line at nominated nominated nominated primary depot primary depot primary depot 7.1b Ensure the length is within 584-635 mm - - - 7.2 Inspect buffer plunger false plate for wear and profile - - - 7.3 Examine buffer mounting bolts and attend if necessary 7.4 Examine visually buffer casing for cracks/damages 8.0 Running gear 8.1 Examine visually axle box for grease oozing out, warm box if any 8.2 Visually examine wheel tyre profile and thickness of tyre and check with tyre profile gauge if they appear to be near condemning limit 8.3 Visually inspect axle box covers. 8.4 Check with wheel distance gauge for loose or tight wheel - - - (IOH) 8.5 Inspect wheel tread for shattered rim, spread rim, shelled tread, thermal cracks, heat checks 8.6 Examine axle pulleys on the wheels - - - Maintenance manual for BG ICF coaches Appendix Sr. No. Schedule Particulars Primary / ‘A’ ‘B’ ‘C’ Secondary examination Primary / 1 month + 3 3 months + 7 6 months + Freq uency of Examina tion Secondary days days 15 days Maintenance Maintenance to be done at: On rake On rake at On rake at Sick line at nominated nominated nominated primary depot primary depot primary depot 9.0 Seats and berths 9.1 Examine middle and upper berth chains 9.2 Examine the holding/securing brackets for seats and berths and attend if necessary 9.3 Examine snack tables for damages and rectify if necessary 9.4 Examine and repair damaged upholstery cushions and curtains 9.5 Examine reclining mechanism on chair cars for proper - functioning and attend if necessary 9.6a Wooden seats and frames should be cleaned 9.6b Disinfect the seats and frames. - 9.7 Cushion should be cleaned with duster. Oil or head sta in and dirty spots if any should be cleaned with mild soap solutions and wipe dry 10.0 Doors 10.1 Examine doors for proper functioning and securing with hinge pivots. Doors should not graze with floor or door sill plates Maintenance manual for BG ICF coaches Appendix Sr. No. Schedule Particulars Primary / ‘A’ ‘B’ ‘C’ Secondary examination Primary / 1 month + 3 3 months + 7 6 months + Freq uency of Examina tion Secondary days days 15 days Maintenance Maintenance to be done at: On rake On rake at On rake at Sick line at nominated nominated nominated primary depot primary depot primary depot 10.2 Examine door locks, latches firmly secured with correct sized screws and properly/smoothly engaging in their slot. The tongue of gravity type latch should be in proper alignment with its slot plate. 10.3 Visually examine window shutters for smooth working and proper locking 10.4 Examine visually rolling shutters/sliding doors of vestibule for smooth working 10.5 Examine compartment sliding doors in AC first and ordinary first class coaches for smooth function 10.6 Thorough inspection and repair sliding doors in SLR coaches for easy and smooth operation. 11.0 Windows 11.1 Examine window shutters of non AC coaches for smooth movement in railing to prevent rattling and disengaging of catches on run 11.2 Window frame on non AC coaches should not be broken and its glass, gauze wire and venetian louver should be in proper condition Maintenance manual for BG ICF coaches Appendix Sr. No. Schedule Particulars Primary / ‘A’ ‘B’ ‘C’ Secondary examination Primary / 1 month + 3 3 months + 7 6 months + Freq uency of Examina tion Secondary days days 15 days Maintenance Maintenance to be done at: On rake On rake at On rake at Sick line at nominated nominated nominated primary depot primary depot primary depot 11.3 Check window balancing mechanism on non AC coaches for proper function 11.4 Examine window safety catches for proper engagement in their slots 11.5 Check lavatory banjo shutters for damage/missing 11.6 Examine window frame and rubber profile of sealed windows in AC coaches for damages and attend if needed 11.7 Window bars should be provided and fixed in prescribed manner and replaced if damaged 11.8 Examine sealed windows of AC coaches, replace broken/damaged glasses 11.9 Check the availability of emergency exits in AC and Non AC coaches. Examine and attend if necessary. 12.0 Flooring 12.1 Inspect and attend torn/damaged/cracked PVC flooring - - - 12.2 Examine and attend opened PVC joints - - - Maintenance manual for BG ICF coaches Appendix Sr. No. Schedule Particulars Primary / ‘A’ ‘B’ ‘C’ Secondary examination Primary / 1 month + 3 3 months + 7 6 months + Freq uency of Examina tion Secondary days days 15 days Maintenance Maintenance to be done at: On rake On rake at On rake at Sick line at nominated nominated nominated primary depot primary depot primary depot 12.3 Examine Drain holes in trough floor for accumulation of - - - water due to clogging if noticed, inspect affected area for corrosion. 13.0 Interior fittings 13.1 Examine laminated panels and mouldings for damage /cracks. 13.2 Visually inspect passenger amenity fittings, replace if found damaged/deficient 13.3 Examine door closer in AC coaches for proper function 13.4 Examine tower bolts of back rests in sleeper coaches for proper working 13.5 Examine visually curtain clothes in AC coaches attend if necessary 13.6 Examine ventilation grills for damages 13.7 Examine luggage racks/bunks for breakage Maintenance manual for BG ICF coaches Appendix Sr. No. Schedule Particulars Primary / ‘A’ ‘B’ ‘C’ Secondary examination Primary / 1 month + 3 3 months + 7 6 months + Freq uency of Examina tion Secondary days days 15 days Maintenance Maintenance to be done at: On rake On rake at On rake at Sick line at nominated nominated nominated primary depot primary depot primary depot 14.0 Lavatory and lavatory fittings 14.1 Check lavatory hinge door for proper function 14.2 Examine lavatory door latches/ tower bolts for proper function 14.3 Examine push cock, flush valve for proper functioning. 14.4 Check and attend leakage in pipes, fittings and shower roses in lavatory 14.5 Clean drain grills and drain holes in bath room and wash basin if found choked. 14.6 Check and replace damaged/ missing mirrors/shelves/ soap dishes 14.7 Examine squatting pans and foot rest for damages 14.8 Intensive cleaning of lavatory pans and commode with - cleaning agent. 14.9 Thorough flushing of water tanks - - Maintenance Manual for BG coaches of ICF design Appendix Appendix G IOH FORMAT COACH NUMBER BASE STATION TYPE SERVICE YEAR BUILT MANUFACTURED BY LAST POH SCHEDULE-A RETURN DATE SCHEDULE-B BOGIE DETAILS ICV end NICV end Bogie No: Year Built: Manufactured By: DATE OF IOH DATE OF RELEASE SSE/IOH SE/ JE/ IOH Maintenance Manual for BG coaches of ICF design Appendix BOGIE DETAILS DESCRIPTION ICV END NICV END REMARKS Bogie frame condition Cracked/ Worn out/ good Cracked/ worn out / good Bolster Cracked/ bent/ good/ renewed Cracked/ bent/ good/ renewed Bolster suspension bracket Cracked/corroded/good/renewed Cracked/ corroded/good/renewed Lower spring seat Cracked/ worn out/good/renewed Cracked/ worn out/good/renewed Axle guide Worn/misalign/good Worn/misalign/good Axle guide cap/ Dropped /good/replaced/modified Dropped/good/replaced/modified modified/unmodified Axle guide assembly Worn out/damaged/good/renewed Worn out/damaged/good/renewed Guide bush Worn out/good/renewed Worn out/ good/renewed Packing rings rubber Damaged/good/renewed Damaged/good/renewed Protective tubes Cracked/good/renewed Cracked/good/renewed Equalizing stay Bent/corooded/good/renewed/13/16 Bent/corooded/good/renewed/13/16 tonnes tonnes Anchor links Damaged/good/renewed Damaged/good/renewed Bolster suspension hanger block Gauged/good/renewed Gauged/good/renewed Bolster suspension hanger pin Gauged/good/renewed Gauged/good/renewed Center pivot Bolt loose/worn/good/renewed Bolt loose/worn/good/renewed Center pivot silent block Silent block damaged/renewed/good Silent block damaged/renewed/good Side bearer Damaged/good Damaged/good Side wearing piece Gauged/good/worn out/renewed Gauged/good/worn out/renewed Side wearing plate Gauged/good/worn out/renewed Gauged/good/worn out/renewed Side bearer oil cup Leaking/good/oil topped up Leaking/good/oil topped up Vertical shock absorber Damaged/good/renewed Damaged/good/renewed Axle box safety strap Missing/good/renewed Missing /good/renewed Bolster safety strap Missing /good/renewed Missing /good/renewed Brake beam safety slings/wire Missing/worn out/good/renewed Missing worn out/good/renewed ropes Equalising stay safety bracket Missing/bent/good/renewed Missing/bent/good/ renewed Maintenance Manual for BG coaches of ICF design Appendix BOGIE ASSEMBLY-BRAKE GEAR DESCRIPTION ICV END BOGIE NICV END BOGIE REMARKS Brake beam Damaged / bent / good / renewed / 13 tonnes Damaged / bent / good / renewed / / 16 tonnes 13 tonnes / 16 tonnes Brake head Damaged / good / renewed Damaged / good / renewed Brake hanger Damaged / good / renewed Damaged / good / renewed Brake blocks Good / Renewed / Ordinary / composite Good / Renewed / Ordinary / composite Equalizing lever long Good / Damaged / worn out / renewed Good / Damaged / worn out / renewed Equalizing lever short Good / Damaged / worn out / renewed Good / Damaged / worn out / renewed Equalizing leve r hanger Good / Damaged / worn out / renewed Good / Damaged / worn out / renewed Connecting rod Good / Damaged / worn out / renewed Good / Damaged / worn out / renewed Actuating rod Good / Damaged / worn out / renewed Good / Damaged / worn out / renewed Adjusting link Good / Damaged / worn out / renewed Good / Damaged / worn out / renewed Hanger bracket bushes Good / Damaged / worn out / renewed Good / Damaged / worn out / renewed Hanger bush Good / Damaged / worn out / renewed Good / Damaged / worn out / renewed Brake head bushes Good / Damaged / worn out / renewed Good / Damaged / worn out / renewed Collar bushes Good / Damaged / worn out / renewed Good / Damaged / worn out / renewed Sleeve bushes Good / Damaged / worn out / renewed Good / Damaged / worn out / renewed Equalizing lever bushes Good / Damaged / worn out / renewed Good / Damaged / worn out / renewed Pin No: 1 Good / Damaged / worn out / renewed Good / Damaged / worn out / renewed Pin No: 2 Good / Damaged / worn out / renewed Good / Damaged / worn out / renewed Pin No: 3 Good / Damaged / worn out / renewed Good / Damaged / worn out / renewed Hand brake Good / Jammed / Eased Good / Jammed / Eased Maintenance Manual for BG coaches of ICF design Appendix VACUUM BRAKE VACUUM CYLINDER Position Barrel Piston head Piston rod Piston rod Rolling ring Neck ring Joint ring Balance vac. serrations serrations guide bush Brake test ICV Good/worn Good/worn Good/bent/ Good/worn Damaged/Good Damaged/Good Damaged/Good Done/ Not end out/renewed out/renewed renewed out/renewed /renewed /renewed /renewed done NICV Good/worn Good/worn Good/bent/ Good/worn Damaged/Good Damaged/Good Damaged/Good Done / Not end out/renewed out/renewed renewed out/renewed /renewed /renewed /renewed done DA VALVES Position O.Ring K.Ring Diaphragm Air admission Non return Filter Body Bench testing valve valve ICV end Good / Good / Good / Renewed Good / Renewed Good / Cleaned / Damaged / Done / Not Renewed Renewed Renewed Renewed Renewed done NICV end Good / Good / Good / Renewed Good / Renewed Good / Cleaned / Damaged / Done / Not Renewed Renewed Renewed Renewed Renewed done RELEASE VALVE Position R/Valve Seating washer Release valve body Release valve lever Triangular washer Vacuum testing diaphragm & pin ICV end Good / Reused / Good / Reused / Good / Reused / Good / Reused / Good / Reused / Done / Not done Renewed Renewed Renewed Renewed Renewed NICV end Good / Reused / Good / Reused / Good / Reused / Good / Reused / Good / Reused / Done / Not done Renewed Renewed Renewed Renewed Renewed Maintenance Manual for BG coaches of ICF design Appendix IC VALVE Spring Broken / Weak / Good / Renewed Lid Missing / Good / Renewed Washer Damaged/ Good / Renewed Step screw Bent/ Weak / Good / Renewed Bronze bush Good / Renewed BRAKE FITTINGS ICV END NICV END SAB Defective / good / Renewed / tested Defective / good / Renewed / tested Hose pipes & clips Defective / good / Renewed / tested Defective / good / Renewed / tested Siphon Pipes & clips Defective / good / Renewed / tested Defective / good / Renewed / tested Vacuum reservoir Defective / good / Renewed / tested Defective / good / Renewed / tested Train pipes Defective / good / Renewed / tested Defective / good / Renewed / tested Van Valves Defective / good / Renewed / tested Defective / good / Renewed / tested SAB antivibration bracket Missing / good / defect ive / renewed Missing / good / defective / renewed AIR BRAKE FITTINGS : END ICV END NICV END Angle cocks Defective / good / Renewed / tested Defective / good / Renewed / tested Isolating cocks Defective / good / Renewed / tested Defective / good / Renewed / tested Dirt collectors Defective / good / Renewed / tested Defective / good / Renewed / tested P.E.A.V. Defective / good / Renewed / tested Defective / good / Renewed / tested P.E.A.S.D. Defective / good / Renewed / tested Defective / good / Renewed / tested Guard emergency valve Defective / good / Renewed / tested Defective / good / Renewed / tested Drain cocks Defective / good / Renewed / tested Defective / good / Renewed / tested Brake cylinders Defective / good / Renewed / tested Defective / good / Renewed / tested Bogie mounted brake cylinder Defective / good / Renewed / tested Defective / good / Renewed / tested Flexible hoses of BMBC Defective / good / Renewed / tested Defective / good / Renewed / tested Air reservoir Defective / good / Renewed / tested Defective / good / Renewed / tested Distributor valves Defective / good / Renewed / tested Defective / good / Renewed / tested Hose B.P. with palm end Defective / good / Renewed / tested Defective / good / Renewed / tested Hose F.P. with palm end Defective / good / Renewed / tested Defective / good / Renewed / tested Train pipes – B.P. & F.P. Defective / good / Renewed / tested Defective / good / Renewed / tested Maintenance Manual for BG coaches of ICF design Appendix BUFFING GEAR / DRAW GEAR Description ICV END NICV END Buffer assembly Examined / good / renewed Examined / good / renewed Buffer bolts Examined / good / renewed Examined / good / renewed Buffer plunger Examined / good / renewed Examined / good / renewed Buffer casing Examined / good / renewed Examined / good / renewed Buffer spindle plug Missing / good / renewed Missing / good / renewed Destruction tube Damaged / corroded / good Damaged / good Draw bar assembly Examined / good / renewed Examined / good / renewed Screw coupling Damaged / missing / good / renewed Damaged / missing / good / renewed Screw coupling suspension hook Examined / good / renewed Examined / good / renewed Draw bar guide Worn out / good / renewed Worn out / good / renewed UNDER FRAME Head stock Corroded / cracked / good Corroded / cracked / good Trough floor Corroded / good Corroded / good Sole bar Corroded / good Corroded / good Cross members Corroded / good Corroded / good Diagonals Corroded / good Corroded / good Main transom Corroded / good Corroded / good Inner headstock Corroded / good Corroded / good Train pipe and joints Corroded / good Corroded / good Dummy carrier & dummy plug Missing / good / Renewed Missing / good / renewed Maintenance Manual for BG coaches of ICF design Appendix CONDITION OF WHEEL & AXLE – ON ARRIVAL Location Diameter Wheel distance Axle number Tyre profile Condition of flange & thickness L-1/R-1 L-2/R-2 L-3/R-3 L-4/R-4 CONDITION OF WHEEL & AXLE ON DESPATCH Location Tyre turned / Wheel dia Wheel Axle UST number Axle pulley If shop wheel, SL not turned distance number condition number L-1/R-1 L-2/R-2 L-3/R-3 L-4/R-4 ROLLER BEARING PARTICULARS Axle box Nos. L1 R1 L2 R2 L3 R3 L4 R4 Make Shop code / etching Cage open / closed Number of rollers Condition of locking plate Condition of grease Axle Box sealing ring Torque value applied Type of grease topped up Quantity of grease used Maintenance Manual for BG coaches of ICF design Appendix DIMENSION – ON ARRIVAL Description L-1 R-1 L-2 R-2 Buffer height “A” dimension ‘B” dimension Table height DIMENSION - AFTER IOH Description L-1 R-1 L-2 R-2 Buffer height “A” dimension “B” dimension Table height CONDITION OF AXLE SPRINGS – ARRIVAL Axle springs 1 2 3 4 5 6 7 8 Left Broken / good Broken / good Broken / good Broken / good Broken / good Broken / good Broken / good Broken / good Right Broken / good Broken / good Broken / good Broken / good Broken / good Broken / good Broken / good Broken / good CONDITION OF AXLE SPRINGS – AFTER IOH Axle spring 1 2 3 4 5 6 7 8 height Left Right Maintenance Manual for BG coaches of ICF design Appendix CONDITION OF BOLSTER SPRINGS - ARRIVAL Bolster springs 1 2 3 4 Left Broken / good Broken / good Broken / good Broken / good Right Broken / good Broken / good Broken / good Broken / good CONDITION OF BOLSTER SPRINGS – AFTER IOH Bolster spring height 1 2 3 4 Left Right Maintenance Manual for BG coaches of ICF design Appendix AMENITY FITTINGS Items Remarks Mirrors Missing / damaged / good / renewed Mirror shelves Missing / damaged / good / renewed Commodes Missing / damaged / good / renewed Squatting pans Missing / damaged / good / renewed Commode seat & lid Missing / damaged / good / renewed Commode chute Missing / damaged / good / renewed Push cocks Missing / damaged / good / renewed Flushing valves Missing / damaged / good / renewed Turn over latches Missing / damaged / good / renewed Tower bolts Missing / damaged / good / renewed Shower rose Missing / damaged / good / renewed Coat hooks Missing / damaged / good / renewed Glass shutters Missing / damaged / good / renewed Louver shutters Missing / damaged / good / renewed Banjo shutter Missing / damaged / good / renewed Safety latches Missing / damaged / good / renewed Window bars Missing / damaged / good / renewed Main door handles & latches Missing / damaged / good / renewed Berths / back rest / seats Missing / damaged / good / renewed Cushions Missing / damaged / good / renewed Rexene Missing / damaged / good / renewed Vestibules-UIC / conventional Missing / damaged / good / renewed Vestibule fall plates Missing / damaged / good / renewed Vestibule Door locking / latches Missing / damaged / good / renewed Condition of exterior paint Good / Shabby / Washed / Repainted Condition of interior painting Good / Shabby / Washed / Repainted End body & roof painting Good / Shabby / Washed / Repainted Emergency exit window Not available/Available/Good Maintenance Manual for BG coaches of ICF design Appendix PROFORMA FOR SINGLE CAR TEST COACH NO. TYPE OF DV AND SL.NO: BP PRESSURE: FP PRESSURE: S.No. Check Specified Actual 1. Leakage rate a) Brake pipe 0.2 Kg/cm2 per minute (max.) b) Feed pipe 0.2 Kg/cm2 per minute (max.) 2. a) Brake cylinder filling time (from 0 to 3.6 kg/cm2 ) 3 to 5 seconds b) Maximum Brake cylinder pressure 3.8 + 0.1 Kg/cm2 3. Brake cylinder release time (3.8 to 0.4 Kg/cm2 ) 15 to 20 seconds 4. Sensitivity & Insensitivity a) Brake application when brake pressure is reduced at the rate of 0.6 Brake should apply Kg/cm2 in 6 seconds b) Brake application when brake pressure is reduced at the rate of 0.3 Brake should not apply Kg/cm2 in 60 seconds 5. Emergency brake application and release a) Maximum brake cylinder pressure 3.8 + 0.1Kg/cm2 b) Manual release of brake cylinder after emergency application Brake cylinder should get fully released 6. Graduated application and release a) Application Brake pipe pressure decreases in steps and Brake cylinder pressure builds up in steps b) Leakage in Brake cylinder pressure in 5 minutes after emergency 0.1 Kg/cm2 within 5 minutes application c) Release Brake pipe pressure increases in steps and Brake cylinder pressure reduces in steps 7. Piston stroke 90+10mm Maintenance Manual for BG coaches of ICF design Appendix S.No. Check Specified Actual 8. Passenger alarm system a) Pull handle (1) Air to exhaust from PEAV. (2) Brake should apply (3) Coach indication light should glow b) Reset PEASD Exhaust of air should stop and indication light should extinguish 9. Guard’s emergency valve test a) Pull valve handle (1) Brake pipe air to exhaust. (2) Brake should apply b) Normalise the handle Air exhaust to stop c) Testing of Brake pipe and Feed pipe in guard’s compartment Gauges should register variation in Brake pipe and Feed pipe. 10. Dirt collector Cleaned / Renewed