Draw & Buffing Gear Maintenance Manual PDF
Document Details
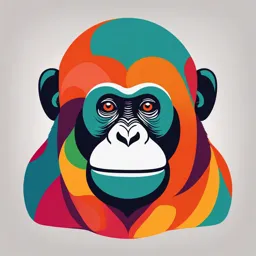
Uploaded by ImaginativePeachTree
STC/JHS
Tags
Summary
This document provides guidelines and instructions for the maintenance of draw gear and screw couplings in BG (Broad Gauge) coaches of ICF (Integral Coach Factory) design. It details the enhanced design components, relevant specifications, and maintenance procedures for various components. It also includes inspection and repair guidelines.
Full Transcript
Maintenance Manual for BG coaches of ICF design Draw & Buffing Gear CHAPTER 9 DRAW & BUFFING GEAR 901 ENHANCED DRAW GEAR & SCREW coupling and draw gear...
Maintenance Manual for BG coaches of ICF design Draw & Buffing Gear CHAPTER 9 DRAW & BUFFING GEAR 901 ENHANCED DRAW GEAR & SCREW coupling and draw gear is 35 Mn6Mo3 to COUPLINGS IS 5517-1993. The material is required to be in hardened and tempered condition to 901a Description & Guidelines achieve high tensile and yield strength. i) Description Stress relieving during maintenance acts as tempering treatment and there will be Enhanced draw gear and screw coupling adverse effect on tensile properties every components were earlier manufactured time stress relieving is done. For screw from Stc. 60.61 VSM10661 steel. The couplings and draw gear manufactured draw gear & screw couplings are designed from steel to IS 5517 the practice of stress for a proof load of 60t (both) and a relieving in workshops should be breaking load of 108t & 112t dispensed with. respectively. Due to poor weldability of these steels as well as inadequate infrastructure in In 1998, the material for the draw gear Railway workshops for pre- & post-weld and screw coupling components has been heat treatment, reclamation of these upgraded to IS:5517 -93 Grade 35 components (except draft yoke) by hot Mn6M03 to enhance the proof load to 75t working / welding is prohibited. (both) and a breaking load of 130 t (both). Specifications C -9509 and C -9505 apply The proof load testing machines should to these draw gear and screw coupling have a capacity of applying loads upto a respectively. The dimensions of these maximum of 100t - 150t. The load should draw gear & screw couplings are the same be increased on the component gradually. as earlier. When the prescribed load is achieved, Relevant drawings are given below: hold it for 2 minutes before gradually releasing the load and checking for VSM10661 IS:5517-93 permanent set. Stc.60 -61 Gr.35Mn6M03 General SK-79061 SK-99003 M easure permanent set by checking the Arrangement distance across 2 marks on the Draw Hook SK-79062 SK-99004 component, as far as possible, before and after application of load. It is preferable to Draft Yoke SK-79146 SK-99005 have direct indication of permanent set, Draft Key SK-79064 SK-99006 for higher productivity. Draw bar and SK-79063 SK-99007 castle nut 901b Inspection & Maintenance i n POH Rubber buffer SK-96002 Spec. C-9501(Rev.2) spring Screw SK-79067 SK-99001 Periodicity : Every POH. coupling assly. Record-keeping: Inspection records Details of SK-79068 SK-99002 should be kept for each inspection stage, screw relating them to the coach from which coupling stripped & also the coach on which fitted after maintenance. Reasons for rejection ii) Guidelines & repairs should be clearly mentioned. The components, except draft yoke, are Load testing and crack detection should specially heat treated to achieve the load be carried out even on newly procured bearing capacity. Hence these components draw gear components before fitting them should not be heated above 550oC. The on the coaches. latest specified material for screw Chapter 9, Page 1 of 8 Maintenance Manual for BG coaches of ICF design Draw & Buffing Gear i) Draw Gear Maintenance grinding/filing. Take care so that (Ref. Drawing : RDSO Sk. 79061 alt no grinding cracks or sharp edges 4 & SK. 99003) are generated which could act as stress raisers. Use dye-penetrant Pre -inspection test for checking surface cracks in case of doubts. § Inspect all components visually for § Inspect the draw hook for dimensional distortion and surface deformations & cracks. The defects such as crack, dent marks, neck, its pin hole, and the slot are pitting etc. Mark components failing vulnerable locations. Draw hooks in this check for rejection. worn beyond the maximum § Special attention should be paid to permissible wear laid down in the the condition of the yoke & draw table below should be scrapped : - gear pins for signs of creep motion, Table 9.2 loose or bent /cracked pins. Elongated or worn out yoke holes Location of Wear Suggested should be marked for repairs. Any wear limit no go gauge welding cracks or distortion in the Root of hook 13 mm Profile yoke should also be checked near point of gauge with visually. contract with 15 mm Dismantling bent link adjustable projection § Take out the draft key from the draw 62 mm dia pin 3 mm 65 mm flat bars and the draw hook after hole straightening & pulling out the draft key cotters. Bottom side of 15 mm 41 mm snap shank 56 mm § Remove the draw hook along with height the screw coupling. § Detach the screw coupling assembly Draft key 13 mm 173 mm flat from the draw hook by cutting off slot(159 mm) the snap head rivet and removing the 38 mm width 2 mm 40 mm flat pin from the collar. Hook opening 5 mm 46 mm go § Remove the split pins and the castle 48 mm 53 mm no nuts from the draw bar rear ends. go plug § Remove the spring end plates, draft pads and parting plates and pull out § Stress relieve the draw hooks both the draw bars. manufactured from steel to Stc. § Dismantle the draw hook beam by 60-61. Stress relieving should not un-bolting it from the underframe. be done for draw hooks § Remove the draft yoke, if required in manufactured from steel to pre-inspection, by pulling out the IS:5517. draw gear pins, using a puller. § Load Test draw hooks (Stc. 60 - § Clean the components by any 61) at 60 t and those of IS:5517 suitable method (Bosch tanks, hot Gr. 35Mn6Mo3 at 75 t water jets etc) before inspecting respectively. There should be no them for cracks, distortions, permanent set after release of corrosion or wear. The detailed load. instructions for inspection & repair of individual components are given Draw Bar below :- Ref. Drawings :RDSO Sk. 79063 alt.4 & Sk. 99007 Draw Hook (Ref. drg. RDSO Sketch - 79062 alt.5 § Check the draw bar for & 99004) dimensional distortions and damaged threads. Also check for § Remove the scale, rust, work wear on the following locations :- hardened layers and surface cracks, if any, by light Chapter 9, Page 2 of 8 Maintenance Manual for BG coaches of ICF design Draw & Buffing Gear Table 9.3 § Renew worn, mis shaped draft keys. In acceptable draft keys, round off the contact area with the draw bars & Wear Suggested no Location of wear limit go gauge draw hook to remove ridges, pitting, etc. if any. 155mm draft key 9 mm 164 mm snap § Stress relieve draft key manufactured slot from steel to Stc. 60-61. Stress 39 mm shank 3 mm 36 mm snap relieving should not be done for draft body key manufactured from steel to IS:5517. Slot width 38 mm 2 mm 40 mm flat Threads M39x3 1 mm Thread profile Rubber draft pads (Ref.drg. RDSO Sk.96002 alt.3 & spec.C- 9501 (Rev.2)) § Reject draw bars failing these standards. In acceptable draw bars, § The rubber pads should invariably be clean the threads and ease them. changed as a set every alternate Round off the roots of threads at the POH. The sets should not be formed slot. from supplies from different § Check the castle nuts for damaged suppliers. Furthermore, the pads threads, worn nut faces and threads should be checked every POH for visually. Replace castle nuts if so. bulging, perishing or having got set to a length below 186 mm. Replace § Stress relieve the draw hooks the pads (as a set) if found defective. manufactured from steel to St. 60-61. Stress relieving should not be done for draw hooks manufactured from Draft Yoke (Ref. Drawing : RDSO Sk.79146 alt.2 & steel to IS:5517. Sk.99005) § Test all draw bars by magna-glow equipment for surface cracks. § Carry out detailed inspection, after § Load test draw bar (Stc. 60.61) at removal and cleaning, for welding 39.5 t and those of (IS 5517 Gr. cracks, distortions and wear as 35Mn6Mo3) at 60t. There should not given in the table below : be any permanent deformation. Table 9.5 Draft Key (Ref. Drawing : RDSO SK. 79064 alt.2 & Comp- Wear Wear Suggested Sk.99006) onent location limit no go gauges § Check draft key for bending and for wear as given below :- Draft 45 mm dia 3mm 48 mm flat yoke hole Table 9.4 Bush 32mm dia 1mm 33 mm flat Location of Wear Suggested no go hole wear limit gauge Draw bar 4 mm Profile gauge with seating 139 5 mm adjustable § Rebuild the 45mm dia hole by mm projection welding and drilling to the nominal size, if required. Ensure that the Draw hook 4 mm Profile gauge with minimum distance between the seating 139 5 mm adjustable inner edges of the 2 holes is mm projection 171+0.5-0 mm. Thickness 4 mm 32 mm snap 36 mm § Replace corroded, cracked or worn bushes. Cotter hole 2 mm 16 mm plug 14 mm dia Chapter 9, Page 3 of 8 Maintenance Manual for BG coaches of ICF design Draw & Buffing Gear Draw gear pin Compo- Wear Wear Suggested (Ref. Drawing : ICF/Sk.-2-1-016) nent location limit no go gauge Bent link 47 mm 2 mm 49 mm flat § Replace pins, found damaged, bent dia hole or worn more than 1 mm anywhere Bent link 78 mm 3 mm 77 mm to go on the nominal diameter (31 mm). ‘U’ gap on each 85 mm no arm go gauge Draw hook beam Pin on 60 mm 2mm 58 mm flat (Ref ICF drg. no. T -2-1-602 and draw dia Sk.99034) hook Screw 55 x 6.35 1 mm K thread § Check the following locations for mm profile wear :- k/thread gauge Trunnion Thread 1 mm K thread Table 9.6 LH/RH 55.635x6 profile Wear location Wear Suggested no Knuckle.35 gauge limit go gauge K/thread Wearing piece 6 mm snap gauge 12 -do- 76 mm 4 mm 72 mm snap mm thick thickness Locating pins 6 mm 19 mm snap -do- 46 mm 2 mm 44 mm snap 25 mm dia dia pin § The wearing piece on the draw § Replace the worn out components. hook beam should be replaced if Replace both the trunnions if worn or cracked. required. Remove ridges, rust, § The locating pins provided to notches etc. by grinding. restrict side-ways movement of the § Stress relieve the screw coupling draw hook, should be replaced if manufactured from steel to Stc. 60- deficient , cracked or worn. 61. Stress relieving should not be done for draw hooks manufactured Screw Coupling Maintenance from steel to IS:5517. (Ref. Drawings : 79067 alt. 7 & Sk. § Assemble the screw coupling as 99001 (Assembly),79068 alt.8 & SK shown in SK 79067 & 99001. 99002 (Details)) § Load test the screw coupling assembly under proof load of 60t § Cut off rivets at both ends of screw (Stc. 60-61) and 75t (IS:5517) and also rivets on trunnion for respectively. There should not be straight links and remove screw any permanent set. and straight links. § Inspect the components for Re-fitment of Draw Gear on coach distortion, cracks or wear exceeding the limits below. In case (Ref Drawing : RDSO Sk. 79061 alt. 4 of doubt, dye-penetrate tests may & Sk.99003) be used for confirming the presence/absence of cracks. § Lubricate the wearing surfaces in the screw couplings, draw hooks Table 9.7 and draw bars with graphite grease or used Roller Bearing grease. Compo- Wear Wear Suggested § Place the draft yoke and secure it nent location limit no go gauge with draw gear pins. Place lock Straight 61 mm 2 mm 63 mm flat pins and splits pins in the bracket link dia hole and secure lock pin with split pin. Do not re-use split pins. Straight 47 mm 2 mm 49 mm flat link dia hole § Position the draw hook beam on Bent link 42 mm 3mm 39 mm snap head stock and secure it with bolts dia stem and nuts as shown in ICF/SK T-2- 1-602. Chapter 9, Page 4 of 8 Maintenance Manual for BG coaches of ICF design Draw & Buffing Gear § Assemble the screw coupling with Table 9.8 draw hook by inserting pin and rivet the pin. Components Drawings § Position the draw bars in the draft Buffer Assembly SK 92090(existing) & yoke and insert draw hook. Insert Sk 98145(new) the draft key in draw bars and draw Buffer casing W/BD –392 & Sk hook. Fit cotters in the draft key (cast steel) 94043 (with enlarged and bend them. Do not re-use base) cotters. (Forged) W/BD-393 & Sk 94044 § Place a rubber draft pad pack to (with enlarged base) STR No.C- 9501 (Rev.2), parting Buffer plunger- W/BD-359 & Sk 94255 plates and spring end plate on each cast steel (with flat face) draw bar. The free height of rubber (Forged) W/BD-355 & S~ springs & parting plates should be 94256(with flat face) 208 mm. Rubber buffer SK 96002 and STR. § Tighten the castle nuts with 9.15 pads no. C- 9501 (Rev. 2) kg-m torque so as to achieve a Buffer spindle W/BD- 353 pre-compression of 196 mm length Destruction tube ICF drg. No. T-2-2-602 of pack. Recoil spring W/BD-2252 § Insert the split pins through the Recoil spring W/BD-2253 castle nuts and draw bars and open parting plate the split pins to 90 degrees. Use Recoil spring W/BD-350 new split pins always. Washer § Ensure that the projection of the Buffing spring W/BD-2261 shoulder on the draw hook from parting plate the head stock is within 92 mm – Face plate for Sk 94254 120 mm. buffer plunger § Check for proper condition of the M.24 Hex Head ICF drawing No. T-2- draw gear and screw couplings, bolt 2-503 after cleaning the accumulated dirt. Pay special attention to displaced Earlier buffer had a plunger with curved draft key & it’s cotters, draw bars face. During reclamation a wear plate and condition of draft pads. with centre hole as per SK-81142 is fitted § Lubricate the screw portion of the and plug is welded at centre to prevent coupling and the area around the rotation of buffer spindle. To avoid draw hook pin with graphite grease welding of centre plug, an integral face or used roller bearing grease. plate is to be provided and the new buffer assembly should be to SK 98145 § Always replace unused screw coupling on the suspension hook. Rubber buffer pads are to be procured and used as a pack from RDSO approved 902 ICF TYPE BUFFER OF BG sources. MAINLINE COACHES Buffer casing of earlier design are to IRS drawing no W/BD 392 & 393. In order to 902a Description an d guidelines reduce the stress level on fixing bolts and prevent cracks in underframe headstock, i) Description the size of base of casing and location of fixing holes were increased and design of Presently enhanced capacity (1030 kg.m) casing to RDSO SK 94043 and SK 94044 buffer conforming to specification No. has been advised to PU’s and Railways in IRS-M 10 are fitted in all BG mainline 1994. Railways mau use both existing and coaches. revised design of casings depending on the location of holes available in the Relevant assembly and main component underframe head stock. drawings are given in table 9.8. Chapter 9, Page 5 of 8 Maintenance Manual for BG coaches of ICF design Draw & Buffing Gear 902b Inspection and Maintenance in Table 9.9 workshops Wear Wear Suggeste d i) Periodicity – Every POH location limit gauge ii) Record keeping Buffer casing 5.5 mm in Inside body wall wall micrometer Record should be maintained related to thickness 11.5 thickness the coach from which buffers are mm removed, the defects, repairs attended and the coach on which fitted after attention. Fixing hole in 2 mm on 28mm flat iii) Dismantling the base 26 dia mm dia § Take out split pin and unscrew nuts holding buffer casing with Buffer plunger (Ref. drg, W/BD- 355 & underframe head stock and remove 359 and SK 94255 & SK 94256) buffer assembly from the coach. § Examine the plunger for wear, § Remove split cotter and nut from cracks & deformation. The plunger buffer spindle and separate buffer worn more than the wear limit on plunger from casing and take out all body and cracked should be components for inspection. discarded. Worn out face plates shall be replaced. iv) Inspections and Repair § The wear limits are as follows : § Clean the components by any suitable method (Bosch tanks, hot Table 9.10 water jet etc.) thoroughly before inspection and check for cracks, Wear Wear Suggested distortions, wear, corrosion & location limit gauge pitting. Buffer plunger 4mm Micrometer § The instructions for inspection and tub e wall repair of individual components are thickness 9 mm given below: Plunger 11mm 1905 mm Buffer casing (Ref. drawing W/BD- face/face plate curvature 392/393 AND Sk 94043 & 94044) 19 mm gauge with depth § Examine the buffer casing for measurement. cracks, damage, deformation & wear. The casing worn more than § Place buffer spindle in the plunger the wear limit and found cracked and rivet cast steel face plate to Sk should be discarded. The elongated 94254 with 6 Nos. of 16 mm dia holes can he filled with weld metal flat CSK rivets on buffer plunger and re drilled to 26 mm dia. The from face plate side. No gap should location of 4 holes are 60.3 +/- 0.2 exist. Circumferential welding of mm from centre of casing along face plate with plunger is prohibited width & 174.5 ± 0.2 mm along length in buffer casing to IRS W/BD Rubber buffer pads – 3 9 2 / 3 9 3. The respective (Ref. Drg. RDSO SK 96002 alt.3 & STR dimensions in casing to SK No. C- 9501(Rev.2) 94043/94044 are 85 ± 0.2 mm & § Rubber buffer pads should invariably 174.5 ± 0.2 mm. These dimensions be changed as a set at every should be checked and restored ,if alternate POH. The set should not found different. be formed from different supplies. Further more, the pads should be § The wear limits are given in table checked every POH for perishing 9.9. or permanent set to a length below 424 mm. Chapter 9, Page 6 of 8 Maintenance Manual for BG coaches of ICF design Draw & Buffing Gear Buffer spindle (Ref. drg. W/BD-353) vi) Mounting of Buffer on Coach § Inspect the spindle for straightness, Before placing the buffer on the wear on body and threads. Straighten underframe head stock, check the the spindle, if required. condition of head stock for corrosion and damage and 4 nos. of 27 mm dia holes The Wear permissible on body is : for cracks and elongation. The corroded / damaged head stock behind buffer location should be replaced with new Table 9.11 part head stock pressing for a length of 746 mm as per RDSO Sk 76026 alt. 1 Annexure V of corrosion Manual C- 7602 Wear location Wear Suggested (Rev.-1) Deposit weld metal in elongated permitted no go holes and re drill if needed. The distance gauge of holes from centre of buffer is 60.3 +/- Buffer spindle 5 mm 35 mm 0.2 mm vertically & 174.5 +/- 0.2 mm body 40 mm dia snap horizontally in earlier design of head Threads M 39 0.5 mm thread stocks and this is suitable for fixing buffer profile casing to IRS drg No W/BD/392 &393. gauge These dimensions should be checked and rectified if required for correct fitment of Destruction Tube buffers.In the current design of headstock (Ref. ICF drg. No. T-2-2-602.) the distance is 85.5 ± 0.2 mm vertically & 174 ± 0.2 mm horizontally and is suitable § Check the destruction tube for for fixing buffer casing to RDSO bulging, corrosion. Replace the SK94043 & 94044. damaged/corroded destruction tube. Place 4 nos. of Hex. Head bolts to ICF v) Assembly of Buffer drg. No. T-2-2-503 through holes in head stock and buffer base and fully tight slotted nuts. Insert split pins through the § Measure the free height of a set of slot in the slotted nut and hole in the bolts rubber buffer pad pack(consisting and split open to 90 degree. Ensure the of 16 pads) to STR No.9501 (Rev.2) buffers remains horizontal. and add parting plates, as required, to achieve a free height of 484 +/- 2 vii) Maintenance in Depots mm. Check for tightness of buffer fixing bolts, § Place washer (ICF Drg. No. T-2-2- drooping of buffers and slackness in 602), measured rubber pad pack buffer plunger to ensure destruction tubes with parting plates, destruction tube are not damaged. in the buffer plunger and insert the plunger inside the buffer casing. Buffer face should be scrubbed with a scrapper to remove dirt and muck and § Assemble recoil springs (W/BD - wiped clean using cleaning fluids After 2252) parting plate (W/BD-2253) cleaning, the buffer face should be and washer (W/BD -2261) on buffer checked for the condition of CSK rivets spindle. Place the M39 nut over holding face plate. Apply graphite grease spindle and tighten the nut as to on face plate after checking for cracks achieve a length of buffer of 635 + and wear. /- 2 mm. The pre- compression of rubber pack with parting plate will be 439 +/- 2 mm. viii) Pre -compression § Insert the split cotter in the spindle The projection of buffer from head should and split open to 90 degrees. Use be within 600 mm to 635 mm. always new cotters. Use washer if needed, to eliminate gap between nut and split cotter. Chapter 9, Page 7 of 8 Maintenance Manual for BG coaches of ICF design Draw & Buffing Gear 903 EXAMINATION AND REPAIR § Buffers should not be dead i.e. they PRACTICE IN CARRIAGE should have sufficient buffing MAINTENANCE DEPOT capacity. 903a Draw Gear § The buffer spindle should be in proper condition with the bolts and i) Primary & Secondary Maintenance cotter intact. § Check and replace damage/missing ii) Schedule C split pins/cotters/rivets. § Follow the items given in (i) above. § Examine draw hook, draw bars and rubber pads for damages. § Buffer projection should be not less than 600 mm and not more than 635 § Check condition of the screw mm. coupling and its components and replace if required. § Destruction tube should be examined and coaches with collapsed ii) Schedule A & Schedule B destruction tube should be attended. § Examine as per (i) above. § Inspect buffer plunger false plate for § Check condition of draw beam and wear and profile. locating pins on it. § Examine visually draft key locking pins. iii) Schedule C § Follow the items given in (ii) above. § Ensure that wear on screw coupling shackle pins, trunion pins shackle/link holes and draw hook holes should not exceed 3 mm. § Ensure that wear at any section on draw hook should not exceed 10 mm. 903b Buffing gear i) Primary & Secondary Maintenance, Schedule A and Schedule B § Buffing gear assembly should be externally examined for drooping, cracked and worn parts for proper securing. § Buffer casing should be properly secured in t he prescribed manner. § Buffer face rivets when provided should be counter sunk and intact i.e. not missing. § Destruction tube should be examined and coaches with collapsed destruction tube should be withdrawn from service at the first opportunity for sick line attention. § Buffer alignment with head-stock should be true. ***** Chapter 9, Page 8 of 8