Maintenance Manual for BG Coaches of ICF Design PDF
Document Details
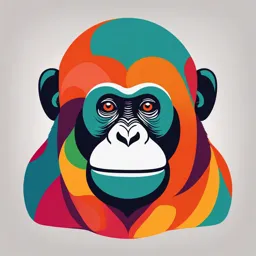
Uploaded by ImaginativePeachTree
STC/JHS
Tags
Related
- Maintenance Manual for BG Coaches of ICF Design (PDF)
- Maintenance Manual for BG Coaches of ICF Design-73-108 PDF
- Maintenance Manual for BG Coaches of ICF Design PDF
- Draw & Buffing Gear Maintenance Manual PDF
- Maintenance Manual for BG Coaches of ICF Design PDF
- Maintenance Manual for BG Coaches of ICF Design PDF
Summary
This document is a maintenance manual for BG coaches of ICF design. It covers various aspects of the coach shell, including its construction, dimensions, and body repairs. It also details aspects of corrosion, and provides procedures for inspection and repair of various coach components.
Full Transcript
Maintenance Manual for BG coaches of ICF design Shell CHAPTER 2 SHELL 201 DESCRIPTION...
Maintenance Manual for BG coaches of ICF design Shell CHAPTER 2 SHELL 201 DESCRIPTION form part of the tubular construction as well as to absorb a large portion of the The concept of the lightweight integral buffing forces. Anti-t elescopic structure design originated in the recognition of the has been provided in the end -walls to properties of hollow girders from the avoid telescoping of the adjacent coaches point of view of strength and utilization of and to absorb the major part of collision material. The reduction in tare weight of energy in case the ends collide during these coaches could be achieved by heavy collisions. utilising "stressed skin" concept and by use of low alloy fittings. Corrugated Leading dimensions of ICF, BEML and sheets are utilised for the trough floor to IRS are (see figure 2.1): Table 2.1 Coaches Over Buffers Over Body Over all width Height from (mm) (mm) (mm) Rail level (mm) ICF/RCF 22297 21337 3245 4025 BEML 22296 21336 3250 3991 IRS 21996 21030 3251 3886 HEIGHT FROM OVER BODY RAIL LEVEL OVERALL WIDTH OVER BUFFERS COACH SHELL Figure 2.1 the length between the head stocks of 201a The integral shell is made of a framework underframe. The whole forms a tubular of series of hoops, consisting of floor shell of integral construction in which the crossbeams, body side pillars and roof sides and roof panels also share the load. carlines located transversely at regular The corrugated trough floor with its intervals, to suit door and window corrugations running longitudinally from openings (see figure 2.2). These hoops one head stock to the other takes up the are connected together by sole bars, waist buffing loads. Below lavatory the tubular rails, light rails, cant rails and carlines constructions are provided in place of longitudinally. This frame work is trough floor to avoid corrosion due to sheathed all over by 2 mm thick corten seepage of water (See figure 2.2). In steel (IRS-M -41) on the side walls and coaches with stainless steel trough floor, 1.6 mm thick corten steel on the roof. no tubular structure is used. At the bottom 2-mm thick corten steel corrugated trough floor is provided between the sole-bars and running over Chapter 2, Page 1 of 9 Maintenance Manual for BG coaches of ICF design Shell CAR LINE CANT RAIL BODY PILLAR LIGHT RAIL WAIST RAIL SOLE BAR SIDE WALLSHEET THROUGH FLOOR SHELL FOR ICF COACHES (CROSS SECTIONAL VIEW) Figure 2.2 201b End wall consists of four vertical pillars 202b All furnishing and other components from of box section connected transversely by coach shell, which are stripped, are to be `Z' sections and are welded to the head sent to the respective sections for stock at the bottom and to the roof at the maintenance. See figure 1.1 (In chapter top. (See figure 2.3) ‘Coach’) for normal repair chart for sequential POH repairs and fitment of 201c The head stock of BG integral coaches overhauled equipment consists of outer and inner head stocks connected by two rigid center buffer 202c Inspection of Underframe stiffeners, which transmits all the buffing forces to the under frame structure. i) The underframe members should be thoroughly inspected for locating 201d Under -frame acts as support for mounting cracked/bent/corroded members. equipment like air or vacuum brake Corrosion is indicated by flaking of system (brake cylinders, DV, BP & FP paint, flaking of metal, pitting and pipes, auxiliary reservoirs, control scale formation. Components like reservoirs, etc.), air -conditioning system sole bar and trough floor which are (Compressor unit, Battery, Control not visible from both sides should be rectifier, etc.), train lighting battery boxes, examined by tapping with a spiked under slung water tank, etc. hammer. Proper illumination will be required to carryout the check. A 202 BODY REPAIRS component will require repair/ replacement, if it has lost more than 202a Inspection and repair of body members 20% of it’s thickness. are done after the coach body is lifted off the bogies and placed on trestles. Chapter 2, Page 2 of 9 Maintenance Manual for BG coaches of ICF design Shell 110 25 5.0 2.0 252.5 110 25 END STANCHION STIFFENER 406 3107 406 406 406 283 110 482 110 635 635 110 482 110 283 3240 END CONSTRUCTION OF BROAD GAUGE ALL METAL LIGHT WEIGHT COACH ICF Figure 2.3 Chapter 2, Page 3 of 9 Maintenance Manual for BG coaches of ICF design Shell ii) Particular attention should be paid to sufficient length and all the the more vulnerable members and exposed parts, after scraping locations listed below:- and cleaning, should be examined to determine the § Sole bar, body pillars, turn extent of corrosion. under and tubular frame/ trough floor below lavatories in all ii) Sole bar, turn under and pillars types of coaches and the above the lifting pads luggage compartments of all SLRs and parcel vans. § Examine the above members in § Sole bars, body pillars, turn the same manner as described unders and pillars above lifting para 202d (i ) pads § Sole bars and pillars behind the § If signs of corrosion are sliding door pockets of SLRs noticed, the side wall sheet and parcel vans. above the lifting pads should be § Sole bars, pillars and turn cut to a height of 500 mm. unders at the door corners. above the turn under and to a § Head stock. length of half metre, on either § Sole bars, pillars and turn under side of lifting pads. Scrape the near coach body bolster. structural members, clean and examine minutely to ascertain 202d Procedure for inspection of underframe the extent of corrosion. members for corrosion attention in case of vulnerable and not so -vulnerable locations iii) Sole bar and pillars at door should be followed as given in RDSO corners technical pamphlet No. 7602 (Rev.1) § Examine the above locations i) Sole bar, body pillar and turn visually. If corrosion is noticed, under at lavatory area cut the turn under to a width of half metre from the door § Examine visually supplemented corner. Remove accumulated by tapping with a spiked dust. Structural members hammer sole bars, body pillars should be thoroughly scraped, and turn under in the bays cleaned and examined to assess under and adjoining lavatories the extent of corrosion. from below the coach and through the elongated holes in iv) Sole bar, turn under and body the turn under after removing pillars at locations other than the accumulated dirt and those described above cleaning the surface through the holes. If corrosion is suspected § Examine visible portion of sole at places in the coaches without bar through the elongated holes elongated holes in the turn of turn under and from bottom under, a 100 mm diameter of the underframe. hole should be cut in the bottom of the turn under § Remove the accumulated dust without damaging the pillars in the turn under through for examining the inside. elongated holes and scrape structural members to the § If incidence of corrosion is extent possible. If corrosion is noticed in the bottom half of noticed, side wall sheet in the the sole bar, the trough floor area of corrosion should be cut should be cut to a width of 300 to a height of 450 mm. from mm and requisite length for the bottom of turn under examination of inside top half. covering sufficient length for § If heavy corrosion is noticed, thorough examination. the side wall should be cut to a height of 500 mm. from the bottom of turn under covering Chapter 2, Page 4 of 9 Maintenance Manual for BG coaches of ICF design Shell v) Head stock 202e Corrosion repairs to Underframe Members § Examine visually inner head stock, outer head stock, i) Corrosion repairs should be stiffening immediately behind carried out as per instructions the buffers and the junction of laid down in RDSO Technical the sole bar at the head stock Pamphlet nos. C-7602 (rev.1) for for incidence of corrosion. ICF coaches. § Examine carefully the base of It is essential to use corrosion buffer assembly as corrosion resistant steel sheets for has been primarily noticed at corrosion repairs of coaches. this location. Welding electrodes and paints should be of the prescribed § Examine carefully the buffer quality conforming to the base of head stock by chalk test relevant IS/ IRS specifications. or sound test for cracks and dents. Buffer fixing holes § Corrosion resistant steel should not be elongated and no sheet for trough floor, minor cracks to be allowed. pillars, side-wall and roof Replace head stock if the wear to IRS M.41 - 97. is more than 4 mm i.e. when § Electrode: IRS Class B2 the thickness is below 4 mm. of approved brands. § Paints: Red oxide zinc vi) Trough floor chromate primer - IS § Examine the trough floor in the 2074-62. Bituminous anti- bays adjoining the lavatories corrosive solution to IRS and under the luggage P30-96, solution type, compartments of SLRs and brushing quality. parcel vans from below for signs of corrosion, ii) Where the corrosion noticed is of supplemented by tapping with a a very minor nature and has just spiked hammer. started, there is no need to renew § If signs of corrosion are noticed the parts. In those areas, the paint in the above examination, the and the rust should be thoroughly part should be thoroughly cleaned to reach the bare metal cleaned by scraping and an and the surface treated with two intensive inspection should be coats of red oxide zinc chromate carried out to detect the extent primer. In addition, underframe of corrosion in the trough floor. members should be given two § Magnesium oxychloride or coats of bituminous solution. plywood/compreg with PVC overlay flooring in the Where the corrosion repairs are lavatories and bays adjacent to carried out on the underframe or lavatories of all coaches over its paint coat is damaged, the six years old should be broken underframe should be painted and trough floor thoroughly with two coats of red oxide zinc examined for incidence of chromate primer followed by the corrosion. four coat system of anti-corrosive bituminous paint. vii) Tubular frame below lavatories For carrying out corrosion repairs § Examine visually the tubes and to underframe members, the joints for incidence of coach body should be lifted off corrosion. the bogies and kept on trestles. For repairs to side wall and end § Corroded tubes shall be replaced. wall, no lifting is required. If corrosion is extreme, entire tubular frame should be replaced. Chapter 2, Page 5 of 9 Maintenance Manual for BG coaches of ICF design Shell iii) The parts of a coach requiring done as shown in RDSO's sketch nos. corrosion repairs most commonly are: 78102, 78103 & 78096. 1. Head stock (refer figure 2.4) 2.2 Corrosion repair of sole bar For replacement of head stock, the Repairs to sole bar for replacement of following parts need be stripped first: corroded portions at the locations mentioned below should be carried out § Side buffers. as per the respective RDSO sketches § Plywood/compreg and PVC indicated: flooring. § end partition and electrical § At locations other than lifting wiring pads and body bolster - RDSO § draw gear assembly. sketch no. 76018. § end portion of BP/FP in case § At body bolster and lifting pad of air brake coaches. locations - RDSO sketch no.76019. Before the corroded portion is cut off, the auxiliary head stock and the two 3. Side wall members sole bar ends should be firmly supported to rail lines. The corroded For repairs to side and end wall sheets, head-stock is then replaced as per the interior fittings, laminate paneling annexure-v of RDSO Technical and window frames should be stripped pamphlet no. C-7602 (Rev.1). Only 8 first. Corrosion repair of side/ end wall mm thick corrosion resistant steel sheets, body pillars and turn unders sheets should be used for head stock should be done as per RDSO sketch repairs. no. 76 020. 2. Sole bar 4. Trough floor For carrying out repairs to sole bar, it For replacement of trough floor, first is necessary to strip first the interior decolite/ plywood flooring needs to be fittings, laminate paneling and window stripped. Corrosion repairs to trough frames. Before cutting off the corroded floor at the locations mentioned below portion of sole bar, both the adjacent should be done as per the respective ends should be supported to the rail RDSO sketches indicated: lines. The new sole bar piece should be welded from outside and inside. To § At end lavatories of two-doors facilitate welding from inside, the and three-doors aside coaches coach body should be lifted and kept - RDSO sketch no. 76021. on trestles. § At end lavatories of four-doors aside coaches - RDSO sketch no. 2.1 Stiffening of sole bar at 76022. doorways § At middle lavatories of four - doors aside coaches - RDSO As incidence of corrosion in sole bar is sketch no. 76023. predominant in the lavatory areas and adjoining doorways, the sole bar was 203 ROOF strengthened in all coaches manufactured since 1974 by 203a Roof repairs providing a box section as shown in RDSO sketch nos. 76011 & 76012. i) In ICF coaches, roof should be The doorways of luggage checked for corrosion. Special compartments in SLRs were attention should be paid at location strengthened as shown in RDSO where gutter mouldings are welded sketch no. 76013. These modifications and ventilators bolted. Corroded roof should be carried out in all coaches should be repaired according to the instructions given in annexure VII of during POH, if not already done. On RDSO Technical pamp hlet no. C- coaches which have not been 7602 (Rev.1) for corrosion repairs of manufactured or so far modified in ICF coaches. accordance with above, this can be Chapter 2, Page 6 of 9 Maintenance Manual for BG coaches of ICF design Shell 255 50 50 VESTIBULE DOOR 2.5 SILL TOP ICF DRG. NO. END WALL SHEET TO BE CUT 7.1.0802 3 2.5 3 A 28 0 3 5 00 2.5 2.5 2.5 A 746 1200 746 2692 140 SECTION A-A 8 324 11 11 8R C C 100 50 100 11 50 11 3 REFERENCE B B ICF B.G. COACHES CORROSION REPAIR OF 3 HEAD STOCK 15 15 25 R.D.S.O 25 SKETCH 76026 (C) 8 20 20 255 45 255 45 SECTION C-C SECTION B-B FIGURE 2.4 Chapter 2, Page 7 of 9 Maintenance Manual for BG coaches of ICF design Shell 203b TRA type Roof Ventilators repairs 207 REPAIRS TO DRAW AND BUFFING GEAR SUPPORT STRUCTURE i) Examine the roof ventilator for damage or corrosion or leakage. Examine the draw gear support structure If no corrosion is observed then for corrosion, breakage, etc. If the seal the joints and crevices with corrosion is light, scrap off the rust to bare water proof s ealing agent. metal, clean well and re-paint. If the Ventilators found beyond repairs corrosion is heavy, replace the corroded should be replaced as per RDSO angle or gusset plate with new support technical pamphlet No.C-7602 angle. (rev.1) annexure-VII. The Similarly examine the buffing gear securing bolts should be replaced support structure for corrosion, breakage, whenever a ventilator is etc. If the corrosion is light, scrap off the removed. Otherwise, they should rust to bare metal, clean well and re-paint. be checked for tightness. Loose If the corrosion is heavy, replace the and corroded bolts should be corroded angle or stiffeners. replaced. 208 REPAIRS TO BODY BOLSTER ii) After repairs and refitting, ventilators should be tested for Examine the body bolster for corrosion, water leakage at their base joints breakage, wear, etc. If the corrosion is at the time of roof testing. light, scrap off the rust to bare metal, clean well and re-paint. If the corrosion, 203c Roof testing breakage or wear are beyond repair, replace the body bolster. Check the area All coaches after POH repairs should be surrounding centre pivot pin mounting tested under water spray for roof leakage holes for cracks. before they are finally turned out from the workshop. For this purpose, a fixture 209 REPAIRS TO CENTRE PIVOTS designed to simulate monsoon conditions Clean and examine the centre pivot for should be provided in the workshop. bent, wear, cracks. Cracks shall be detected by doing chalk testing or 204 REPAIRS TO DOOR HANDLES magnaflux dye penetrant test. If the centre pivot is found cracked or worn beyond Examine the door handle for breakage, repair, it should be replace. Check the damages. If the fixing bolts are loose or mounting bolts for loose or missing. missing, tighten the bolts. Replace the Tighten and lock the bolts with locking door handles which are found beyond plate. repairs. 210 WATER TANK SUPPORT 205 REPAIRS TO DOOR PIVOTS STRUCTURE Examine the door pivots for corrosion, Examine the water tank support structure breakage or wear by cutting the bottom for corrosion, breakage, wear, etc. If the portion of outer panel. Cut the corroded corrosion is light, scrap off the rust to bare portion of the door pillar (Z molding) and metal, clean well and re-paint. If the weld new piece joining the door pivot pin. corrosion, breakage are beyond repair, If the female socket is worn or damaged replace the corroded angle with new angle beyond repairs then replace it. Replace the of suitable size as per the requirement. bush provided in the socket. Replace the rubber/wooden packing if perished or damaged. 206 REPAIRS TO PARTITION WALL, SEAT PILLAR / MOUNTING PLATE 211 REPAIRS TO FLOOR CHANNEL Examine the floor channel for corrosion, Examine seat pillar/mounting plate for breakage, wear, etc. by cutting opening corrosion or breakage, etc. at bottom ends. the PVC and plywood flooring where the If found corroded, repair the same as per corrosion suspected. If the corrosion is RDSO technical pamphlet no. C-7602 light, scrap off the rust to bare metal, (Rev.1). clean well and re-paint. If the corrosion, Chapter 2, Page 8 of 9 Maintenance Manual for BG coaches of ICF design Shell breakage are beyond repair, replace the 214 EXAMINATION AND REPAIR corroded channels with new channel of PRACTICE IN CARRIAGE suitable size as per the requirement. MAINTENANCE DEPOT 212 GENERAL 214a Primary/ Secondary/ Schedule 'A' § All repairs of cracks should be schedule carried out by gouging and welding Check visually the following for any by suitable electrodes. damages/defects/deficiencies: § CAUTION : No electric welding on § Destination board brackets. the coach should be carried out § Body panels. without proper earthing from near the portion being welded on such § End walls that the return current has a distinct § Windows walls path (earth) which should not be allowed through the bogies and rails. § Body side doors In the absence of such earthing, the § Condition of head stock, sole bar and return current passes through axle other underframe members. roller bearings causing pitting of rollers and bearing failure in service. 214b Schedule 'B' § Distorted and bent parts should be § In addition to para 214a do the heated and straightened. following. § The parts used for repairs should be § Examine trough floor, turn under and given proper surface treatment and other under frames from und erneath applied with protective paint. for corrosion. Relatively thick sections such as sole 214c Schedule 'C' and IOH bars, cross bearers, etc. should preferably be grit blasted and § In addition to para 214b do the immediately thereafter given a following. protective coat of red oxide zinc § Thoroughly clean and remove dust, chromate primer paint. rust accumulated at pillars through turn under holes with coil brush and § Welders' Qualification: Welders compressed air. deputed to carry out welding work on coaches and coach components § Examine for corrosion of sole bar should be only those tested and and other under frame members with certified as adequately skilled for torch light and inspection lamp. welding work on coaches and coach components. ***** 213 LIST OF TOOLS AND PLANT Lifting shop Corrosion Repair Shop 1. EOT cranes 1. EOT cranes 2. Trestles for coach 2. Trestles for coach body body 3. Inspection torches 3. Gas cutting plants 4. Spiked hammers 4. Multi-operator 5. Ball peen hammers welding plants 6. Goggles for 5. CO2 Welding plant inspection staff 6. Electrical angle 7. Measuring tape grinders 8. Measuring scale 7. Pneumatic hand grinders 8. Component painting equipment 9. Phosphating plant Chapter 2, Page 9 of 9