Maintenance Manual for BG Coaches of ICF Design PDF
Document Details
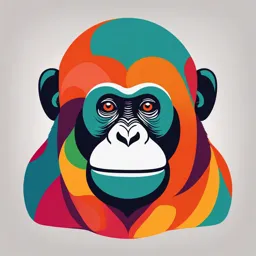
Uploaded by ImaginativePeachTree
STC/JHS
Tags
Summary
This document is a maintenance manual for BG coaches of ICF design, focusing on the vacuum brake system. It details general descriptions, maintenance procedures, and testing methods for the various components of the system.
Full Transcript
Maintenance Manual for BG coaches of ICF design Vacuum Brake System CHAPTER 5 VACUUM BRAKE SYSTEM 501 GENERAL DESCRIPTION respective rep...
Maintenance Manual for BG coaches of ICF design Vacuum Brake System CHAPTER 5 VACUUM BRAKE SYSTEM 501 GENERAL DESCRIPTION respective repair/ maintenance sections for thorough cleaning in the washing plant and 501a Vacuum brake system has been improved overhaul. gradually over the years by increasing the brake rigging ratio, effecting modifications Slack adjuster to the vacuum brake cylinders, hose pipe D.A.Valve cages and adopting direct admission valves Vacuum cylinder with release valve and slack adjusters (See figure 5.1 ). Vacuum reservoir Alarm chain apparatus 502 MAINTENANCE AT WORKSHOP Guard van valve 502a During POH all components of the brake 503b Train pipe gear system shall be examined, repaired and replaced as necessary. The pins and bushes i) Check the train pipe with compressed shall be examined for wear and replaced if air of 2 kg/cm2 for leakage specially at the radial clearance exceeds 0.75 mm. threaded joints, bends and portions where clamps are fitted, tee joints, 502b Following items should receive particular swan neck, etc. with one end dummy. attention during POH: ii) Check and replace corroded, dented, bent more than 10 mm, or thin walled portions of the train pipes. Spiked i) Safety brackets provided for brake gear hammer should be used to check thin components should be in accordance wall, corrosion, etc. While renewing with the approved drawings and shall the pipe, it should be ensured that be examined for proper condition and bending do not decrease the cross secured according to the prescribed sectional area of pipe passage at the method. bends. New brake pipe should be given a coat of anti-corrosive paint before ii) Vacuum cylinders and their trunnion fitting. brackets, vacuum reservoirs and train pipes, rubber hose & syphon pipes, iii) Renew the damaged/ missing brackets alarm chain apparatus including the or clamps used for clamping the train chain, disc and locking arrangement, pipe. brake beams, hangers, and brake iv) All the pipe threads must be cleaned blocks shall be secured as prescribed. and applied with white lead before All brake gear pins (should be couplings are fitted. Clean the grooves chromium plated) shall be secured on swan neck. with washers and split cotters. v) After attending to all the repairs, test iii) Vacuum gauges shall be properly the train pipe for sound joints and tested and adjusted using master bends with compressed air at 2 kg/cm2 gauges before being fitted. pressure. There should not be any leakage of air over the entire length of the train pipe. 503 LIFTING SHOP vi) After repairs and testing, the train pipe 503a After lifting the coach body and placing it should be given a coat of anti- on trestles, dismantle the following parts of corrosive paint. the vacuum brake system and send to the Chapter 5, Page 1 of 14 Maintenance Manual for BG coaches of ICF design Vacuum Brake System BRAKE CYLINDER 24" TYPE F D.A. VALVE HOSE PIPE RAIL LEVEL D.A. VALVE SLACK ADJUSTER VACUUM RESERVOIR TRAIN PIPE SLACK ADJUSTER LINE DIAGRAM OF VACUUM BRAKE FIGURE 5.1 Chapter 5, Page 2 of 14 Maintenance Manual for BG coaches of ICF design Vacuum Brake System 503c Rubber hose pipe and syphon pipe surfaces and cages fitted before the couplings are inserted into the hoses. i) Renew the hose pipe and syphon pipes They should be clipped firmly. if they had cracked or lost the bond between the various layers/ 503d Vacuum Reservoir Straps components. ii) Reusable hose/ syphon pipes should be Vacuum reservoir straps should be tested for vacuum retention. For this examined for slackness, corrosion and test, the hose should be connected by thinning, and damaged or worn out threads means of a cylindrical nozzle of size at their ends. and entire straps or threaded corresponding to the vacuum/ syphon ends, as required, should be replaced. If the hose bore to a chamber of 1640 cu. securing holes in the under frame are worn cm. volume and the free end of hose more than 3 mm, build up by welding and closed with a cylindrical plug. 510 mm redrill the holes. The reservoir straps should Hg of vacuum should be created in the be double secured with spring washer and chamber and hose system. On isolation check nuts. After all repairs, the reservoir from the source of vacuum, the drop of straps should be given a coat of anti- vacuum should not be more than 75 corrosive paint. FRP tissue should be placed mm Hg in one hour on the chamber in between reservoir and safety straps. APD gauge. The pipe should not be clipped should be done. or otherwise bound to t he chamber 503e Vacuum cylinder trunnion bracket nozzle or plug for this test. The hose should also be bent around a mandrel Where bushes are provided in the brackets, of 228 mm diameter till the ends of the they should be renewed and a light coat of hose are parallel. This should not result graphite grease applied before fitting a in any displacement or distortion of cylinder. Trunnions of the cylinder must wire. neither be too loose nor too tight in their iii) Cracks, porosity, tears, etc., of the hose brackets. Lateral clearances on the trunnions should be detected by giving it a (on each side) should not exceed 3 mm. It stretch test. For this purpose, hose pipe should be adjusted by renewing the bushes. should be secured to a special jig and If there are no bushes, the trunnions should should be stretched to 20% over its be bored and bushes of correct size fitted to original length and released 100 times. get the required clearance. Thereafter, in the stretched position, its surface should be examined to detect 503f Brake shaft the defects, if any. Cracked, torn, porous, or collapsed hose pipes or hose Brake shaft should be examined for pipes with coiled wire loose or straightness, bending and wear on its missing, or length reduced below 50 bearing surfaces. The shaft bearing worn cms. should be rejected. beyond 3 mm should be built up by welding and machined to its original size. Before the iv) Serviceable hose pipe should be shaft is fitted into its brackets its bearing secured on swan neck (after applying surfaces should be smeared lightly with rubber solution on swan neck) with grease. The fork arm should also be clip and tighten with spanner. examined for bending, distortion and wear v) Renew the corroded or damaged hose on its forked ends and restored to its original pipe clips. shape and size as required. The brake shaft vi) Broken, damaged, or distorted cages mounted in its brackets under a coach should be replaced with modified should be parallel to the trunnions on which cages to drg.No.VB 409/M. the cylinder swings to avoid setting up of side or crosses stresses and hence damage to vii) Universal coupling should be the arm. The brake shaft should not have a examined for broken, cracked and side play in its bracket bushes in excess of 2 distorted lugs and renewed on mm after POH. condition basis. Rubber solution should be applied on the mating Chapter 5, Page 3 of 14 Maintenance Manual for BG coaches of ICF design Vacuum Brake System 503g Brake shaft brackets the vertical pipe should be blown clear with compressed air and the pipe Brake shaft bracket bolts and nuts should be threads should be checked before the examined for rusting, looseness, thinning assembly is connected to train pipe. and worn out or damaged threads and v) All moving parts including spring replaced, if required. Good bolts and nuts should be greased and checked for should otherwise be reused after greasing proper movement. their threads. The brackets should be checked for cracks, corrosion and thinning vi) The clappet operating chain and the or damage and repaired/ replaced as pipe through which the chain passes required. The brake shaft bracket bushes should be dismantled, examined and should invariably be changed. renewed with standard chain or 6 mm wire. If in normal position of the 503h Slack adjuster support bracket on coach clappet valve, the chain hangs loose in any of the compartment openings, its The support brackets should be stripped and length should be adjusted by cutting it examined for missing or worn out rollers out to the extent necessary. Wooden and bent, defective or missing springs. The handles provided in the compartment defective or missing roller and springs openings for pulling the chain should should be replaced. Defective spring should also be checked and replaced where be repaired by restoring them to their found broken or cracked. original shape and size and hardened and tempered to give correct tension. The vii) After the clappet valve assembly is securing brackets and nuts as well as pins overhauled and refitted, its chains, etc., should also be checked and replaced or are checked and replaced, the alarm repaired as required. chain apparatus should be tested at the outgoing pit for its operation in 503i Alarm chain apparatus accordance with the following procedure. i) During POH, alarm chain apparatus should be opened, cleaned and 503j Alarm chain apparatus test overhauled. i) Create 460 mm to 510 mm of vacuum, ii) The chain must be of the prescribed pull the chain, using a spring balance, specification and each link must be at both sides of the coach from the end physically examined for crack/ wear/ where the chain is anchored, ie., from elongation. Proper fitment/ anchoring the end which is farthest away from of all the components should be the clappet valve. checked and ensured to avoid their ii) The alarm chain should not operate the failure/ non-operation/ mal-functioning clappet valve if the pull applied during service. vertically down wards is less than 6.4 iii) The clappet valve should be removed kgs. It should also not require a pull of from the coach for overhauling. more than 10 kgs. for its operation. Replace the rubber washer. The iii) When the chain is pulled, the brakes clappet valve cover should be checked should apply on the coach and the drop and repaired or replaced as necessary. of vacuum in the train pipe should be The clappet valve operating rods, between 180 mm and 200 mm if one levers, indicating discs and other coach is being tested, or between 130 moving parts should be cleaned and mm and 180 mm when a rake as a checked and straightened if bent, or whole is being tested. If the drop in replaced if broken or deficient. The vacuum is less than 130 mm and still pins if worn should be renewed, if not the brakes are applied, it shows an they should be cleaned before reuse. obstruction in the vertical pipe, in iv) The vertical pipe connecting the which case it is necessary to locate and clappet valve with train pipe should be clear the obstruction in vacuum examined to ensure that it is neither vertical pipe. leaking nor blocked. The air passage in Chapter 5, Page 4 of 14 Maintenance Manual for BG coaches of ICF design Vacuum Brake System iv) On resetting the clappet valve, it 504b Guard Van Valve should automatically come to lap position. After restoration of 460 mm i) During overhaul of guard van valve, its to 510 mm of vacuum, the exhauster rubber diaphragm and rubber washer should be isolated and the drop in should be invariably changed. Passage vacuum noted. The drop in vacuum through the valve connecting its train should not be more than 25 mm in one pipe side to its chamber should be minute. This check should be carried cleaned. If the passage hole diameter out twice. exceeds 6 mm, the valve should be replaced. 504 OVERHAUL OF COMPONENTS ii) The chamber space of the guard van 504a Vacuum reservoir valve should be checked for leakage, cracks and damage and repaired or i) The vacuum reservoir should be replaced as necessary. The valve itself examined for corrosion, damages, should be checked for easy and correct distortion, cracks, etc. If the extent of lift. The valve cover holes should be corrosion, etc., are only about 5% of cleaned, blocked holes opened and total area, it should be cut off and bent/deficient lever replaced. The replaced with another plate by vacuum gauge nipple provided on the welding. Otherwise the whole barrel guard van valve chamber should be should be replaced. Open the drain checked for damaged or worn out plug and blow compressed air into the threads. The loose nipple should be reservoir to remove dusts, dirt and secured firmly on the chamber. water particles, accumulated inside the reservoir. iii) All studs and nuts with worn or damaged threads should be placed. The ii) After thorough cleaning, refit the drain threads in the body of the chamber plug smeared with small quantity of should also be good enough to ensure graphite grease on the threads and no leakage past them. The guard van tighten it firmly. Clean the pipe threads valve body threads on which train pipe with a brass wire brush in both the dish is secured should also be checked for ends to fit the syphon nipples. Replace damage and wear and the body the missing or damaged syphon in the replaced if the threads are bad. dish ends of the reservoir. iii) After attending the defects and before iv) After overhaul, the entire guard van painting the reservoir, a pneumatic valve assembly should be tested for pressure of 2.0 kg/cm2 by gauge satisfactory functioning, as given should be applied in it for the purpose below: of ensuring sound fabrication and finish. With the pressure applied, the ♦ Vacuum retaining capacity test: welded seams all over the body should Guard van valve connected to a be thoroughly checked for leakage chamber of 1640 cu. cm. volume with soap and water solution. throughout the assembly, should not, on isolation from the source of iv) Vacuum reservoir should be tested for vacuum, record a drop of more than vacuum retaining capacity with 510 25 mm in 1 minute on the chamber mm of vacuum throughout the gauge. assembly. It should not, on isolation from the source of vacuum, record a ♦ Operation test drop of more than 13 mm in 30 minutes on test gauge. 1) On release of operating handle, v) Aft er all repairs and tests, the reservoir the valve should, with should be given a coat of anti- atmospheric pressure corrosive paint and FRP tissue pasted throughout the assembly, re-set at the areas where suspension straps itself by its own weight. are located. Chapter 5, Page 5 of 14 Maintenance Manual for BG coaches of ICF design Vacuum Brake System 2) With 460 t o 510 mm of vacuum 504f Gland box (Stuffing box) throughout the assembly, and the source of vacuum isolated, Table 5.1 gradual admission of air to the train pipe should show a Guide Bush corresponding drop in vacuum Inside diameter 44.52 +0/-0.03 mm on the van valve gauge. Outside diameter 54 +0/-0.1 mm 3) With vacuum throughout the Renew all the rubber items like the neck assembly, the guard van valve ring and gland box joint washer invariably. should automatically lift on a Renew the worn/ loose guide bush. Replace rapid destruction in the train the worn, damaged, or broken studs. Secure pipe of approximately 225 mm the gland box on the cylinder cover with of vacuum, and on the operating spring washers and nuts. handle of the test apparatus being placed in the "running" 504g Piston rod position, the guard van valve Dismantle the piston rod from the piston. should re-set itself within 3 to Renew the bent, damaged, dented, worn, 5 seconds. corroded, or pitted piston rods. If the threads of the piston rod are damaged, the rod Note:- Above tests 2 & 3 apply only to should be replaced. automatic type of guard van valves having a diaphragm and dome above 504h Piston the atmospheric valve. The cracked piston should be replaced. The 504c Vacuum gauge piston skirt serrations should be cleaned free of dust, rust and sediments. Visually check Vacuum gauge which is permanently fitted the piston for worn or cracks. Replace the in guard's van should be removed and piston if found damaged beyond salvage. calibrated with master gauge before Measure the out side diameter with refitting. If defective, it should be repaired micrometer of range 575-600 mm & record and again calibrated with master gauge and the dimensions. While assembling the refitted. The vacuum gauge guard must be Piston and Vacuum cylinder the diametrical invariably provided to protect the gauge difference between the two should be 20.3 from damage or theft. mm. The blind holes for the piston rod cover bolts should be tapped and eased. 504d Vacuum brake cylinder 504i Ball valve cage Strip the vacuum cylinder completely. Thoroughly clean and dry the components The ball valve should be opened, thoroughly and check for defects like cracks, damages cleaned free of dust, dirt and sediments and and wear. lightly lapped. Four holes in the cage which should be of 6 mm diameter should be 504e Pan (Cylinder cover) cleaned thoroughly. The ball valve cage cover should be checked for good threads. Replace the cracked/ broken cover or if the The ball should be replaced even when welded lugs are more than 50% of the total slightly worn. Ball valve should be changed lugs. Broken/ cracked lugs should be when its seating is worn out or pitted and replaced with new lugs by welding and the surface is not smooth to provide good grinding. After attending to the defects, the seating for the ball. the ball and the ball seat pan should be painted with one coat of anti- should otherwise be cleaned with emery corrosive paint. paper and lapped together before assembly. The cage cover should be replaced if its threads are damaged. Chapter 5, Page 6 of 14 Maintenance Manual for BG coaches of ICF design Vacuum Brake System 504j Piston assembly and horizontal, when the ring is in its piston groove. Select the serviceable/ new piston assembly ii) In order to test the ring for twist, it components and assemble the piston should be hung on a stretched finger assembly as per drawing No.VBA - 16 / M. and examined. A good ring should The piston should then be painted all over hang straight and should not make a except over the working surface ie., serrated figure of 8 and show a twist. The portion. The date of overhauling and the rolling ring should also be stretched by code of the shop of overhauling should then hand and examined. If any cracks be stenciled on the cover end of the piston appear, it should be considered as disc. perished and replaced. 504k Barrel (Cylinder body) iii) New rolling rings should be tested for compression and stretching. A 50-mm Cracked barrel including the one with long test piece cut from the ring should cracked trunnions should be replaced. Lugs be compressed to half of its sectional cracked or broken should be replaced with diameter and kept in the compressed new lugs by welding and grinding. The condition for 3 hours. On release, if its barrel should be replaced if the number of diameter does not come back within original lugs (ie., those which have not been 2% of its original diameter within an repaired at all) goes down below 50%. hour, it should be rejected as defective. Thoroughly clean the serrations and check Similarly, the ring should be stretched for wear. Measure the inside diameter with to 300% of its original length and kept micrometer of range 600-625 mm. Replace in the stretched condition for 3 hours. the barrel if serrations are found worn or If on release, the ring does not come damaged. Dry the barrel with hot air after back to within 5 % of its original wiping out all the traces of water particles. length within an hour, it should be Clean the release valve seat and the holes rejected as defective. for proper seating and free passage of air respectively. After attending to the defects and cleaning, inside of the barrel should be 504n Release valve painted with one coat of anti-corrosive paint i) Open the release valve and renew all except the serrated surface, which should be left unpainted. the rubber items like diaphragm, seating washer, etc., invariably during 504 Joint rings overhaul. Dry the release valve after wiping out all the traces of water. Every time a vacuum cylinder is opened, the Check the release valve operating lever joint ring should invariably be replaced. and renew if found cracked. The After fitting the joint ring in the correct release valve studs should be cleaned position between flange of cylinder and and replaced if found damaged or cover, it can be retained in the correct worn. While assembling the valve, alignment while fitting the cylinder cover to nuts should be smeared with graphite the cylinder by suitably designed clips. grease. It should also be ensured that all the sharp edges on the seat of the 504m Rolling ring spindle washer are rounded off. After i) Twisted, cut, worn out or perished assembly, the release valve should be rolling rings should be replaced. While tested as given below: fitting a rolling ring on a piston A) Vacuum retaining capacity test surface, it should be ensured that it is of the correct size, i.e. diameter is ♦ Release valve, connected either 13.1mm or 13.5 mm depending through the cylinder port to upon the wear on the serrated surfaces chamber of 1640 cu. cm. of the piston and the cylinder and, that volume with 510 mm of the ring does not get twisted. The seam vacuum throughout the line of the rolling ring should be even assembly, shall not, on isolation from the source of Chapter 5, Page 7 of 14 Maintenance Manual for BG coaches of ICF design Vacuum Brake System vacuum, record a drop of more vacuum exhauster and train pipe. This than 20 mm in one minute on valve will automatically control the the chamber gauge. vacuum to a maximum of 460 mm ♦ Release valve, connected with lever in horizontal position and a through the chamber port to a minimum of 356 mm with the lever in chamber of 1640 cu. cm. vertical position with, exhauster volume with 510 mm of working. vacuum throughout the ii) Create 460 mm of vacuum (lever of assembly, shall not, on control valve horizontal). destruction of the vacuum, iii) Destroy the vacuum. record a drop of more than 20 iv) 20 minutes after destruction, create the mm in 1 minute on the balancing vacuum of 356 mm (lever of chamber gauge. control valve vertical). The piston of B) Operation test: cylinder in good condition should partly descend but not completely. ♦ Release valve, connected That which completely descends is through the chamber port to a faulty and should be dismantled and reservoir with vacuum repaired again. throughout the assembly shall, v) Increase vacuum to 460 mm (lever of when the vacuum is destroyed control valve in horizontal) when in the train pipe by pulling on piston should completely descend. the operating lever wire thus That which does not descend operating the valve, remain in completely is faulty and should be the open position till there is dismantled and repaired again. pull on the lever wire. It After successful BVT testing, supply the should re-set immediately on brake cylinder to lifting shop for fitting on removal of the pull. coach. ♦ On re-creation of not more than 205 mm of vacuum, the 506 D.A.VALVE (ESCORT- KNORR D.A. valve shall re-set itself. VALVE) 505 ASSEMBLING AND TESTING OF 506a Open the two halves of DA valve by VACUUM CYLINDER removing the four M8 hexagonal nuts. Clean all the components and sub 505a After attending to the defects of vacuum assemblies like lower locking screw cylinder parts, assemble the Parts as per subassembly of the lower housing, housing IRS drawing No.VBA - 16 / M. alt 6. Care upper subassembly, diaphragm sub should be taken to invariably replace all assembly, valve seat subassembly, etc. All the rubber items like rolling ring, joint the rubber items should be replaced ring, release valve joint washer, piston cap invariably and other parts should be washer, etc. While assembling the Piston changed on condition basis. and Vacuum cylinder the diametrical difference between the two should be 20.3 List of Rubber Items which should be mm. After complete assembly, the changed vacuum cylinder should be tested on the Table 5.2 test bed and stencil the date of overhaul, the date of testing and shop code on the Part Name Drawing Number vacuum cylinder body. Diaphragm 4A 38266 Seal 48174 505b Testing of Brake cylinder (Balanced Nylon guide bush KB 408 Vacuum Test ) Sealing ring A 35 x 41 Dln 7603 i) Attach the overhauled brake cylinder Sealing ring A 30 x 36 Dln 7603 to test stand train pipe and test K Ring N 891 / 20.2 reservoir. The balanced vacuum Joint ring KB 115 control valve is connected in between Chapter 5, Page 8 of 14 Maintenance Manual for BG coaches of ICF design Vacuum Brake System 506b The filter element of (Escort-Knorr 506d Testing of DA valve: After the DA valve is D.A.Valve) should be thoroughly washed in overhauled and assembled, it should be kerosen and blow with compressed air to tested on the test bench as indictated in remove the entire collected dirt. Before figure 5.2 for its functional performance fitting back, the filter element should be and leakage. immersed in light machine oil and the oil allowed to be drained. i) Retention test : Mount the DA valve on the test stand and create vacuum till The filter element of (Greysham 530 mm Hg is indicated on both D.A.Valve) should be thoroughly washed in gauges A and B of the test stand. Close parafin to remove the entire collected dirt. stop cock "Y" and then stop cock "X". Record the drop of vacuum in both the List of Items to be Changed in Escort gauges A & B, which should not be type DA valve on Condition Basis more than 12.5 mm in 10 minutes. ii) Operation test : The stop cock "X" is Table 5.3 opened till the gauges A & B again record 530 mm of vacuum. Then stop Part Name Drawing Number cock "X" is closed and "Y" is opened. Pin and screw assembly 4KB 613 Record the drop in gauge B (brake cylinder) from 530 mm to 25 mm Diaphragm seat 4A 50314 which should be within 3 seconds. Valve seat 4A 50807 iii) Proportionality test : Open stop cock Locking screw 4A 55757 "X". Vary vacuum in gauge A by Valve seat 4A 54952 opening and closing cock "Y". It will be observed the gauge B follows gauge Locking screw 4A 69805 A very closely both during creation of Hex. nut M8, DIN 934 vacuum and brake application. Spring washer B8, DIN 127 Hexagonal bolt M8x35 DIN 931 507 SLACK ADJUSTER (SAB DRV2-450) Self tapping screw 4x5/16" Refer to write-up on Slack adjuster in para 413 of Air Brake Chapter. Filter assembly KB 137 Cup plate KB 409 507a End piece for slack adjuster pull rod Hex. nut M10 x 1.5 DIN 439 Prepare end piece for pull rod as per the Washer DIN 433 RDSO SK - 96102 alt. 3 to be used in Compression spring 4A 30485 / 8 modified vacuum brake system to provide horizontal movement to slack adjuster: 506c The DA valves should be closely examined Type of coaches Length of end and seats ground lightly to avoid leaks. piece While assembling care should be taken for fitting the diaphragm on to the lower WFSCN, SL, SCNLR 265 mm housing groove properly. The end corners must be pressed inside the groove. Free All other vacuum 155 mm movement of the diaphragm subassembly braked coaches should be checked by hand. During the final assembly of upper and lower housing, tightening of hexagonal nuts should start from the O-ring end and the 4 nuts must be tightened evenly. Chapter 5, Page 9 of 14 Maintenance Manual for BG coaches of ICF design Vacuum Brake System GAUGE ‘B’ GAUGE ‘A’ (BRAKE CYLINDER) (TRAIN PIPE) COCK - X FILTER 1/2” 1/2" TP TO VACUUM PUMP DA VALVE UNDER LC TEST RESERVOIR 3/4" 34 LITER 1.2 Cu. ft. COCK - Y RESERVOIR 1/2" 34 LITER 1.2 Cu. ft. TESTING OF DA VALVE Figure 5.2 508 ASSEMBLING BRAKE SYSTEM ON should be tested with 255 mm vacuum COACH to detect and attend porous or leaky hose pipe and or joints. After receiving the overhauled brake system ii) The balanced vacuum control valve is components, these should be fitted on the connected in between vacuum coach in proper order and in their respective exhauster and train pipe. This valve locations. Then lower the coach on will automatically control the vacuum overhauled bogies and connect the pull rod to a maximum of 460 mm with lever end of slack adjuster to vertical levers of the in horizontal position and a minimum bogie brake rigging. of 356 mm with the lever in vertical position with exhauster working. 509 ADJUSTMENT OF BRAKES Although the vacuum reading at the valve applies to the front of the coach, 509a A vacuum cylinder as fitted shall have a it will control the necessary drop of minimum clearance of 13 mm between the 102 mm for balancing throughout the piston cotter and fork end arm of the brake train during test. shaft when both are in their lowest positions. iii) After the vacuum is created up to the The brake gear adjustment should be such end of the coach completely destroy that the piston stroke is within limits the vacuum. specified for different types of stock. With iv) 20 minutes after destroying, create the the piston in fully lifted up position, there balancing vacuum of 356 mm (lever of must be a minimum clearance of 25 mm control valve vertical). The pistons of between the top of the fork end arm and the cylinders in good condition should cylinder stuffing box. partly descend but not completely. That which completely descends is 509b Testing of vacuum brake system (Balance faulty and should be replaced and vacuum test) checked again. v) Increase vacuum to 460 mm (lever of i) Adjust brake gear to ensure that the control valve in horizontal) when piston stroke is within prescribed piston should completely descend. limits i.e,. 203 –3 mm (This is That which does not descend important as the balancing vacuum is completely is faulty and should be based on the correct piston stroke). replaced and checked again. While this is being done, the train pipe Chapter 5, Page 10 of 14 Maintenance Manual for BG coaches of ICF design Vacuum Brake System 510 ADJUSTMENTS OF SLACK dimension `A' again with brake fully ADJUSTER released and correct if necessary. vi) Lock the control rod head firmly with 510a Control dimension `A' Slack adjuster: After nut and tooth lock washer. Secure pin the Brake Regulator has been installed or with split pin. when checking an existing installation, carry out the following: 510b Dimension `e' i) Make sure that the hand brake and the The dimension `e' which is 375 ± 25 mm vacuum brake are fully released and represents the capacity available for the whole rigging is in proper order. adjustment and will decrease as wear takes ii) Make three or four brake applications place at brake shoes, wheel and pin joints. at correct vacuum to ease the rigging. iii) Once again ensure that the whole brake The maximum value of dimension `e' rigging is in the fully release position. should be within the permissible limits for The installation can not be correctly each value when: adjusted or checked if the brake rigging is only partly released. i) All brake shoes are new. iv) Now set the dimension `A' between the ii) All pin joints have new pins and control rod head and the barrel head bushes. which is 16 +4/-0 mm and 22 +4/-0 iii) All wheels are new. mm for ICF coaches with 13t and 16.25t bogies respectively and rotate to If it is not within permissible limits, after suit refitting control rod and pin when ensuring that all other relevant parts in the the dimension `A' is correct. rigging are correct to the drawing, the v. Make a few more brake applications at length of one of the pull rods may be the correct vacuum, this time checking adjusted and the piston stroke checked piston strokes which should be within again. the limits specified. Also recheck 511 LIST OF TOOLS AND PLANT Table 5.4 Lifting shop Vacuum brake shop Slack adjuster shop Ball peen hammer Ball peen hammer Ball peen hammer Chisel Chisel Chisel Spanner set Spanner set Steel measuring type Gas cutting plant Single girder electric hoist Pipe vice Welding plant Box spanner set Spanner set Jack for brake cylinder fitting Vacuum exhauster Jacking tool BVT test equipment BVT valve Screw driver Pallets D.A. Valve test rig soaking tank Platform truck Compressed air supply Inspection guages Guard van valve test rig Box spanner set Clapet valve test rig Spring testing rig Vacuum gauge test bench Gas cutting plant Train pipe test rig Welding plant Vacuum test rig D.A. Filter cleaning plant Fork lift Plat form truck Cleaning plant Hot water jet system Waste water treatment plant Chapter 5, Page 11 of 14 Maintenance Manual for BG coaches of ICF design Vacuum Brake System 512 TROUBLE SHOOTING ON VACUUM BRAKE Table 5.5 Sr. Defects Probable cause Method of Testing Remedies No. i) Coaches not provided with Slack Adjuster Brake Power Weak a) Brake Blocks slack & Check the piston Adjust brake gear. If even not braking wheels travel. Brake shaft then the brake power is arm will be touching weak, change the brake the cylinder when blocks. brakes are applied. b) Brake blocks slack Check whether the Adjust the brake gear or but braking wheels piston travel is more change the brake blocks. without requisite than 125 mm or not. force. c) Brake gear bushes Shake brake hangers Adjust the brake gear or worn out. with hand to see Change all bushes and pins whether bushes come as necessary. out along with the hangers or pins rattle in bushes. d) Brake rigginng stiff Brake shaft arm Ease the brake shaft & and brake release remains up even after replace the strong release spring too strong. release of brake, spring with that having though the piston proper tension. comes down. ii) Coaches provided with Slack Adjuster Brake Power weak e) Excessive free lift Measure free lift. Adjust free lift to 14 mm. (f) Defective cylinder See whether the Repair or replace vacuum piston goes up cylinder. when vacuum is destroyed. (g) Excess 'A' dimension Measure 'A' Adjust as specified for the dimension type of coach. h) Defective brake Check that all brake Change brake gear compo- rigging rigging components nents, pins and bushes as are as per drawing necessary. and the clearance between brake gear pins & bushes are within the permissible limit. (i) Manual adjustment Measure wheel Adjust 'e' dimension in in respect of wear of diameter and respect of wear of wheels wheel has not been check "e" dimension. made Chapter 5, Page 12 of 14 Maintenance Manual for BG coaches of ICF design Vacuum Brake System Sr. Defects Probable cause Method of Testing Remedies No. j) SAB Slack Adjuster On application & Replace slack adjuster. pin defective. release of brake see whether the Slack adjuster barrel rotates. 2) Brake on a coach (a) Brake rigging pin & Move or shake by Ease the jammed compo- do not release. brake shaft jammed. hand and feet. nents. (b) External leak in the Test by a flame Rectify the leak or change train space of vac. which will be drawn the neck ring or the piston cylinder commonly in at places of rod as required. due to worn out neck leakage or close the ring or scored piston valve connecting the rod source of vacuum, after creation of vacuum and check the train needle in the vacuum gauge which will come down. (c) Engine not creating Visual examination Release train vacuum the same amount of cylinders. vacuum as was prior to an application of brakes 3) Fall in vacuum on (a) Clappet valve spring a) Drop of vacuum by Adjust the clappet valve or run by 125 to 175 defective. 125 to 175 mm. blank it. If can not be mm reported by (b) Syphon pipe getting b) Drop of vacuum adjusted, adjust and secure Driver. disconnected. by 125 to 175 mm. the syphon pipe. 4) Vacuum cannot be a) Leakage at joints of Starting with the last coach, created on the train. train pipe, train pipe check all joints and rectify nipple, hose pipe, all leaks with a sealing Syphon pipe. compound, or/and replace (b)Rubber washers defective hose pipe clips in hose pipe joints Check vacuum in the and rubber washer, as missing or brake van and the necessary. after checking all twisted. engine. Listen for coaches upto the engine and hissing sound to rectifying defects as noticed, (c)Rearmost hose detect leaks. if vacuum still cannot be pipe of the train created, then devide the train not secured into two equal parts and test on its dummy. each part separately. Again (d)Leakage in vacuum subdivide the part found chamber. defective and test each sub- (e)Guard' s van part. This is continued till valve leakage. the defective vehicle is located. (f) D.A. Valve Check for leakage. Replace or by -pass D.A. leaking. Valve. Chapter 5, Page 13 of 14 Maintenance Manual for BG coaches of ICF design Vacuum Brake System Sr. Defects Probable cause Method of Testing Remedies No. 5. Abnormal variation a) Partial obstruction of Create the vacuum 460 to in the amount of hose pipes of the train 510 mm and destroy it. Now vacuum between pipe observe closely the extent of engine gauge and piston travels of all coaches. brake van gauge. The travel of the piston would be greater on coaches between the locked portion and the engine, than that of the coaches in the portion beyond the blockage i.e. between the blocked coach and the rear brake van. In case there is a complete blockage, the piston travel would indicate where the vacuum brake has not functioned, at all. b) Vacuum gauge of Replace the defective Guard Van valve vacuum gauge. defective. 6) Piston applies a) Leak at neck. Destroy vacuum and Change the neck ring or brakes when the see if the piston blank off the vacuum vacuum is created comes down. cylinder and advise the next train examining station to change the neck-ring. b) Wrong connection of Ditto Correct the syphon pipe syphon pipe on the triple connection. way release valve ***** Chapter 5, Page 14 of 14