Train Lighting and Maintenance Schedules of Non AC Coaches PDF
Document Details
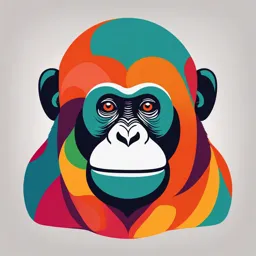
Uploaded by ImaginativePeachTree
STC/JHS
Tags
Summary
This document details the train lighting and maintenance schedules for non-AC coaches of Indian Railway BG coaching stock. It covers different types of train lighting systems, including End On Generation (EOG), Self Generation (SG), and Mid On Generation (MOG), and provides a general description of major equipment, such as brushless alternators and rectifier-cum-regulator units.
Full Transcript
Maintenance Manual for BG coaches of ICF design Train Lighting (Non - AC coaches) CHAPTER 7 TRAIN LIGHTING AND MAINTENANCE SCHEDULES OF NON AC COACHES 701 INTRODUCTION...
Maintenance Manual for BG coaches of ICF design Train Lighting (Non - AC coaches) CHAPTER 7 TRAIN LIGHTING AND MAINTENANCE SCHEDULES OF NON AC COACHES 701 INTRODUCTION Depending upon the train lighting The following systems of Train Lighting systems, the coaches are of following are in use on Indian Railways BG types. coaching stock: In this chapter the train lighting system 1. End On Generation (EOG) of Non AC and AC SG coaches will be discussed. 2. Self Generation (SG) 3. Mid On Generation (MOG) BG COACHES Self Generating Mid On Generation End On Generation (SG) Coaches (MOG) Coaches (EOG) AC Coaches Split type Roof Mounted AC Non- AC Under Package Unit Coaches Coaches slung (RMPU) Split type RMPU with 25 Under Slung KVA inv erter Chapter 7, Page 1 of 21 Maintenance Manual for BG coaches of ICF design Train Lighting (Non - AC) coaches 702 GENERAL DESCRIPTION OF during journey from minimum speed MAJOR EQUIPMENT for full output (MFO) to maximum speed. The alternator is used for: 702a BRUSH LESS ALTERNATORS i. Charging the coach batteries. Brushless alternators are axle driven, with ‘V’ belt drive, mounted on the ii. To meet electrical load i.e. fans, lights, bogies of the AC & TL coaches. These air conditioning, water-raising alternators are of various ratings and apparatus (WRA) etc. in the coach. make as per requirement for different type of coaches. They are being 4.5 kW brush-less alternator procured as per following RDSO’s are driven by 4 Nos. of C122 matched specifications: - sets of ‘V’belt coupled between the axle and the alternator pulley. The axle Specification No. Ratings pulley is of 572.6 mm PCD (pitch circle dia.) and alternator pulley is of EL/TL/47 Rev 'C' 4.5 kW, 37.5A, 120 V 200 mm PCD. Belts are kept under with amdt no.1,2,3 DC tension by a spring-loaded belt- used on non AC tensioning device. coaches. EL/TL/54 Rev 'A' 18 kW, 138.5A, 130 V 18kW/ 22.75kW/ 25kW DC alternators are fitted with 12 Nos. of with amdt no.1,2,3 deep V-grooved pulleys of 200 mm used on SG AC PCD with six grooves on each side of coaches. the shaft, which is driven by V-belt in (Split type underslung) conjunction with an axle pulley. ELPS/SPEC/TL/01, Optimized 22.75 Dec. 1993 kW/25kW, 702b RECTIFIER-CUM-REGULATOR UNIT (RRU) with amdt no. 1 & 2 175A/ 193A, 130V DC, used on AC The rectifier cum regulator unit has coaches of SG type mainly following functions: 4.5 kW Brush less alternators are used i To rectify the 3 phase AC output of on Non AC BG Coaches. It consists of the alternator through DC full a three-phase hetropolar inductor type wave bridge rectifier. Alternator and a static Rectifier-Cum- ii Regulating the voltage generated by Regulator Unit (RRU). the alternator at the set value. Earlier AC coaches provided iii Regulating the output current. with under slung split type AC units were fitted with two nos. of 18 kW Recently electronic rectifier cum brush less alternators. After the regulator (ERRU) confirming to development of roof mounted AC units RDSO specification (RMPU) and 25 KVA inverters, 22.75 No.RDSO/PE/SPEC/D/AC/0013 kW (Optimized) brush less alternator (Rev.0), developed, which has was developed within the same frame been fitted on a very few coaches size of 18 kW alternator. Subsequently on trial. 25 KW alternator with new design was developed for 2 tier and 3 tier AC 702c BATTERIES sleeper coaches with RMPU and 25 kVA inverters and for AC 1s t class one The following types of batteries are 25 kW alternator with 25 kVA inverter provided on under -frame of AC & non provided. AC Self Generating type and End On Generation type coaches. The brushless Alternator with the help of static rectifier cum regulator i. 6V/120 Ah flooded type (Mono unit is capable of developing voltage at block cells) on Non AC BG SG the set value to meet the coach load coaches. Chapter 7, Page 2 of 21 Maintenance Manual for BG coaches of ICF design Train Lighting (Non - AC) coaches ii. 2V/120 Ah , VRLA cells on Non battery box is painted with anti- AC BG SG (Self Generating) corrosive paint. coaches. iii. 2V,1100 Ah 56 cells VRLA 110 V While mounting the battery SG AC coaches fitted with RMPUs box in underframe of the coaches, and 25 kVA Inverter special care is taken to provide locking nuts and split pins to avoid iv. 2 V, 800 Ah flooded type cells on any accidental falling of batteries under -slung mounted split type AC while running. equipment. v. 90/120 Ah, 24V on EOG (End- Recently both the Production On-Generation) type AC coaches Units have been instructed to provide (Emergency batteries for lighting ) battery boxes as per RDSO drg. No. RDSO/SK/K/0037, which is suitable The 2V,120 Ah TL batteries are for both makes of VRLA batteries i.e. used in conjunction with brushless M/S Exide and M/S Amar Raja. The alternator with suitable Rectifier-cum battery box is having improved safety Regulator of 4.5 kW capacity for train factor coup led with flexibility to lighting system of TL BG SG type accommodate both makes of VRLA coaches. The 2V, 56 cells 800 Ah / 2V, batteries. 56 cells 1100 Ah VRLA batteries are used in conjunction with brushless 702e BCT (Battery Charging Terminals) alternator with Rectifier -cum Regulator unit of 18/22.75/25 kW capacity for AC BCT is provided at the both coaches. 1100 Ah batteries are used on sides of the coaches for external AC coaches equipped with the Roof charging of the batteries at stations of Mounted Package type AC plants. 1100 maintenance lines. Ah capacity battary are of the valve regulated lead acid (VRLA) type which 702f RJB (Rotary Junction Box) has its inherent advantages like : Rotary Junction Box is provided inside the coach. It is used to Topping up with water is not arrange and control the power supply to required. various circuit of the coach (e.g. light, Periodical checking of specific fan) with the help of rotary switches gravity is not required. and HRC fuses. Regular maintenance to avoid sulphation of terminals and 702g EFT (Emergency Feed Terminals) connections not required. It is provided at the both ends of the coach to feed the additional The VRLA batteries are also known as supply to the adjacent coach in case of Sealed Maintenance Free (SMF) emergency. Supply from the healthy batteries. coach may be extended to him/dark coach by connecting supply to the 702d BATTERY BOX positive and negative terminals of the EFT. ICF type design battery box for AC coaches is a fabricated 702h TL Lamps framework made of mild steel confirming to drg. No. WGFAC-7-1- 25 and 40 Watt lamps are 026. Whereas RCF design is of closed provided in the non AC coaches. The type confirming to drg. No. CC71448 power supply is at 110 Volt DC. 25 (PP side) & CC71451 (NPP side), It is Watt lamps are used in corridor, light suspended on coach in the under lamp, wash-basin, toilet. 40 W lamps frame and is provided with front are used for lights in the coach. opening doors for paying attention to batteries. FRP trays are provided to prevent corrosion. The interior of the Chapter 7, Page 3 of 21 Maintenance Manual for BG coaches of ICF design Train Lighting (Non - AC) coaches 702i FTL (Fluorescent Tube Light) as per platform report. Proceed as follows:- It is a 2 feet long, 20 watt fluorescent tube light provided in the n Check field fuse, replace if found coach for the light. It works at 110 V blown, with approved makes i.e., DC supply. It gives better illumination S&S or English Electric make. and is being provided in the coaches in place of TL lamps. n Check the continuity of field and phase winding with the help of test 702j Carriage Fans lamp/ multi-meter to ensure that windings are not open circuited. On non AC BG coaches 400 mm sweep carriage fans are used where n Check for loss of residual system voltage is 110 DC. These fans magnetism with the help of are fixed type and confirm to IS : 6680- voltmeter across the field 92 with latest annexure 'H' for deviation terminals. In case of loss of to IS 6680-92. magnetism, give 12 V DC flashing to the field terminals for few 703 TRIP SCHEDULE seconds to regain lost residual (PRIMARY & SECONDARY magnetism. MAINTENANCE) n Check that the regulator feedback 703a ATTENTION ON MAINTENANCE loop is O.K. LINES n Check connections for tightness in As soon as the rake is berthed alternator and rectifier regulator. If in the maintenance lines and before this is all right, remove belt from commencing the work, a caution board alternator. shall be clamped to the rail on either side of the rake by TXR or his n Use testing machine for testing representative. Rail locks shall be used alternator in situation. Couple the on either side of the rake for the safety portable motor drive with of maintenance staff attending under Alternator. gear equipment. TXR should ensure clearance from electrical n Check the DC output voltage at the Chargemen/staff incharge for the rectifier and regulator terminals. maintenance of rack before removing Identify the defects if any and the caution board and rail locks. rectify them. The battery should be isolated while doing this test. To avoid any malfunctioning of the above system, print ed forms for n Provide new split pin for pulley permit to work on pit lines issued by castle nut after completion of work. the traffic department and after completion of the work, completed / n Check up the condition of safety men withdrawn form can be used. chain and availability of split pins in safety chain bolts. Check the plate-form attention report and concentrate first on n Check up alternator suspension attending the defects in these coaches bracket and tension gear for any by adapting systematic trouble shooting damage and replace, if necessary. procedures. Proceed as follows in respect of other equipment. n Check up and tighten loose bolts in terminals box covers. 703b ALTERNATOR n Check availability of split pin for First attend alternators in alternator castle nut. coaches for generation, which have arrived "cold" and coach dark condition n Check the belt tension after every round trip of the coach. Chapter 7, Page 4 of 21 Maintenance Manual for BG coaches of ICF design Train Lighting (Non - AC) coaches n For new V-belt fitted, the belt meter as per recommendations of should be re-tightened after V belt manufacturers. completing the first trip. n Check that all the sets of belts n Check the tension indicator pin at provided should be of same make suspension point after every round & grade. trip for flat belt drive alternator. 703e RECTIFIER CUM REGULATOR n Never energize field from battery in case of failure of field circuit n Clean regulator externally. Open diode in regulator. Apart from non regulator terminal cover and check regulation, this may cause for signs of overheating in all the permanent damage to field terminals/bus bars/etc. Check up windings. for loose connections and tighten the same. If the terminal board is n If there is no generation, ensure found affected due to heat, replace that there is no breakage in the terminal board with new one. cable termination. n Check for any damage to the phase and field wires /cables inter 703c AXLE PULLEY connecting regulator and alternator and its anchoring arrangement. n Examine the indicating white mark n Check and secure properly the on the pulley axle and ensure that terminal cover and regulator cover. the pulley has not slipped. If pulley has slipped, take necessary n If the generator is normal, check corrective action. the cable termination of the regulator visually for any n Tap the pulley with hammer and abnormality. judge the tightness or crack by n If the alternator arrived without sound. If it gives clean metallic generation, open the regulator and sound the pulley is tight. Dull sound indicates that it is loose. Bolt check for any abnormality and ensure the fuses are intact. should be tightened with torque wrench to 30 kgm. n Check the cable for any abnormality from the alternator to n Check the lock nuts and split pins the regulator by using test lamp, if for availability and tightness. found open/short attend the same. 703d BELTS n Ensure the residual magnetism is available in the alternator. n Check condition of belt for fraying n If needed change the regulator and of edges, etc., ensure the generator by running the alternator with a portable motor. n Check the belts for overturn and correct it, if necessary. NOTE : Components : Components of RRU such as MA, ET, CT, OVR etc., and n Check the number of belts which electronic components such as power should be 4 nos. for 4.5 kW diode, field diodes, zener diodes, alternator. auxiliary diaode etc., shall be procured only from OEM. n Tension should be felt by hand by striking it slightly. Belt in correct Maintenance of alternator/RRU has tension will respond `alive' and to be done in line with SMIs issued `spring-back'. If required by RDSO as well as Manufacturer's retensioning, the same shall be recommendations. retensioned to the recommended values as applicable. This can also be checked using a suitable tension Chapter 7, Page 5 of 21 Maintenance Manual for BG coaches of ICF design Train Lighting (Non - AC) coaches 703f BATTERIES/BATTERY BOX n Coaches with discharged batteries which shows less than 100 V on i. Conventional Lead Acid load should be put on charge at Batteries double the normal rate of charge and the charging reduced to half n To know the condition of cells the rate of charge as soon as the during `Trip Examination' some gassing starts and continued till cells in a battery are treated as the specific gravity rises to the `pilot' cells. On arrival of train in fully charged value which should the maintenance line, disconnect be between 1210 and 1220. Use all inter vehicle connections. the battery charging terminals Record the specific gravity of provided in coaches for charging `pilot' cells in each battery. purpose. Check up correct polarity Different cells should be identified and connect the charging cables. as pilot cells every month. The idea Use a clip on D.C. ammeter of 0- of identifying different cells as 25 A range to check up the battery pilot cells every month is to ensure charging current. Note down the that true condition of the battery is rate of charging and the number of reflected. hours of charge. In case of conventional coaches n Check specific gravity of pilot cells working on 110 V D.C. system and the total voltage of battery on there are two crates with 9 mono load at the end of charge and block batteries in each battery box. record. Marking of these cells to indicate pilot cells shall be done as follows. n Keep micro porous vent plug tight. Ensure that washer is available in Table 7.1 micro porous vent plugs. 1 2 3 4 5 6 7 8 9 n Check all the battery box members 10 11 12 13 14 15 16 17 18 for any cracks in the fabricated battery box/cradle and take Table 7.2 corrective action. Month Pilot Cells n Check for proper fit ment of mono 1st Month 1, 12, 13 block in the battery box ensuring 2nd Month 2, 11, 14 wooden packing pieces. 3rd Month 3, 10, 15 4th Month 4, 9, 16 n The person in charge of battery 5th Month 5, 8, 17 maintenance should record all the 6th Month 6, 7, 18 readings mentioned above in his diary and this information should Repeat cycle further. be transferred to the register maintained for various trains. Check the floats of each cell and check for correct electrolyte level n Check anti-theft rods and provision as indicated in the float stem. Replace of nuts both inside and outside the missing/defective floats. In case of battery box on either side. Provide low level, replenish with distill water. If if found missing. Secure battery any cell needs too much water for box cover finally after all works replenishing, watch for crack in the are completed. cells and also check the voltage on load n Ensure that the fitment of the which should not be less than 1.80 V. battery box is in order with all the In case of any defect, remove the cell bolts, nuts, lock nuts, split pins etc. and replace by a spare one preferably are in order. of the same make and lug date or a lug date as close to the one already in the n Ensure the weldings are proper coach. and the bottom plate of the box is well secured. Chapter 7, Page 6 of 21 Maintenance Manual for BG coaches of ICF design Train Lighting (Non - AC) coaches n Ensure the cells are properly 703h FANS cleaned. Following scheme is prescribed for all n Ensure the water level in all the trains during primary or secondary cells/mono block is upto the mark maintenance at a depot:- and top up the cells with distilled water wherever required. n Switch on each fan individually. n Ensure all micro porous vent plugs Check starting of fan when and sealed floats guide are properly switched on. In upper class closed. coaches, check fan for starting in the lowest position of regulator and n Check the sp. Gravity of the cells if also for variation of speed in the it is less than 1200, the battery other regulator positions. If the fan shall be connected on charge. does not start, short the switch n Measure the load voltage of the terminals with a small piece of cells/mono block if it less than 100 wire temporarily. If the fan starts V, identify the low voltage cell and this will indicate that the replace if needed. controlling tumbler switch/regulator is defective. n Check the terminations in the fuse Replace defective switch/regulator. and the condition of the fuse. n Check the termination of cable in n If the fan does not start when the the under frame link box, for toggle switch terminals are proper condition and attend if shorted, proceed as follows: needed. ♦ Test for supply at the 2-way ii. VRLA Batteries : connector terminals near the fan with the tumbler switch SMI no.RDSO/PE/TL/SMI/0001 - on. If there is no supply, the 98 (Rev.0) dt. 01.06.98 to be wiring is defective and has to followed. be attended. 703g EARTH CHECKING ♦ Open dome cover in case of swiveling fans and remove fan Before checking the earth in body fixing screws in case of the coach, it should ensure that coach is fixed fans. not connected to the adjacent coach through EFT (Emergency Feed ♦ Remove carbon brushes. Terminal). After isolating the coach the Check brushes for condemning earth shall be tested by using a double size, proper bedding, correct test lamp as explained in the RDSO spring tension and correct code of practice of 110 V coaches. If grade of brush. any earth is noticed the required corrective measures should be taken to ♦ Check for free movement of remove the earth before inducting the brush in the brush holder. coach in the service. No coach shall be Replace defective brushes/ allowed for service with +ve earth. springs. However incase of –ve earth this can be allowed for maximum one trip that too with properly marking as –ve earthed. ♦ If the commutator is dirty, clean the surface with sand Record all the attention given paper of 0/0 size. in the under frame and roof, the Specific Gravity, the condition of ♦ If the commutator surface is generation, lamps, fans and fuses, grooved or the segments are availability of belts etc. with coach and found pitted in one or more other details. locations, replace the fan by an overhauled fan. The defective fan can thereafter be rectified by replacing the defective Chapter 7, Page 7 of 21 Maintenance Manual for BG coaches of ICF design Train Lighting (Non - AC) coaches armature by a good one. If repeated large scale deficiencies of spare armature is not available foreign Railway's coaches. The send defective fan to shop for Depot/Railway entrusted with attention. primary maintenance shall be advised by message whenever the ♦ If the fan is noisy, check for deficiency is made good or when loose blades/fan guards and large scale deficiencies are noted tighten them. If the noise is on arrival. due to bearings, replace the 703i LIGHTING fan and send defective fan to shop for replacing. n Switch on each lamp/tube light. If the lamp/tube light does not glow, n Check the fuse for fans and ensure check lamp/tube light and that it is of correct size (35 SWG) replace, if fused. If the lamp is all tinned copper. right, check control fuse and replace, if found blown. n Clean fan body and its guard. n If the fuse is all right, check control n In swiveling and bracket fans switch and replace, if necessary. ensure that the fan dust cover is If the switch is all right, check up promptly replaced after attention lamp holder for stuck up plunger and also that the nylon cord or loose connection and rectify provided to prevent loss of fan defect. If there is no defect in the dust cover, is available in position. lamp holder, check up for supply at the holder terminals and if the n The MCB/fuse controlling the fan wiring is found defective, mark the circuit shall be checked for correct coach "Sick" and arrange for rating (16A for non AC SG attention in maintenance lines. coaches and 6 A for SG AC coaches and proper functioning and n Note down the coach number, total replace if found defective. number of lights in each coach and the number of defective/missing n Note down the total number of fans lights on arrival. in each coach and the number of fans found defective. Defective n Provide switch covers and fuse fans shall include fans, which covers promptly, if they are required push start. The aim is to missing. achieve cent percent working of fans. The records mentioned above n If any dome cover is open or not will help in working out the extent secured properly, rectify defect, if of the problem in any particular any and secure. service to take quick remedial action. n Replace broken glass domes/acrylic covers of tubelights. n The fans shall be available as per lay out for the coaches. In case it is n In case of berth lights in first class necessary to remove any fan for and AC coaches, check up for free attending to major defects and no movement of shutters. Replace, if spare fan is available a ‘Deficiency found defective. Label’ shall be affixed near the fan point. In case no deficiency Label n Clean side lamp glasses and red is available. Theft Memo shall be shield inside the lamp in SLRs. issued to the security branch. Check up for free movement of operating handle and drop same n Deficiency of fans shall be lubricating oil, if necessary. Clean promptly made good when noted tail lamp glass and the reflecting by any depot irrespective of surface inside. whether the train is primarily maintained or not except in case of Chapter 7, Page 8 of 21 Maintenance Manual for BG coaches of ICF design Train Lighting (Non - AC) coaches n In case of fluorescent light check n The chipping of insulation is a holders, switches, electronic ballast dangerous practice this leaves and wiring and rectify permanent scratch on the cable. defect/replace component. The taped conductor will not be quite satisfactory and so chipping n Check MCBs/fuses for light should never be done. Testing circuits in junction box for proper shall be done only at cable operation and replace defective terminations. MCBs. Watch for loose connections between MCB and bus n Poor chipping of cable, poor bars and rectify. Ensure that crimping of cable lugs and loose MCBs/fuses are intact for connections in terminals will protection of each circuits. result in excessive heating and discoloration of lugs, tapes and n Check tightness of terminal cables. Watch for this during connections of HRC fuse for inspection and take prompt action negative circuit in junction box and to locate and rectify the defects. rectify defect, if any. Replace overheated tape and re- tape the overheated portion of n Use fuses/fuse wires of cable insulation at terminals using recommended sizes in junction PVC tape after ensuring proper box as a stop gap measure in place cable connection and cause of of MCBs and HRC fuses. Ensure overheating. that fuse wire provided in junction box as a temporary measures n Replace blown fuses, incorrect size enroute should be rep laced with fuses and discolored fuses by MCBs & HRC fuses of the correct fuses of proper rating. Replace sizes at the primary maintenance blown or incorrect size of HRC depot. fuses by correct rating. Check all fuses and ensure that they are n Remember that fuses & MCBs are secured tightly to their terminals. safety switch gears provided for Replace defective MCBs/fuses in isolating the supply in case of junction box by MCBs/fuses of faults. Never by-pass or use correct rating. incorrect fuses as this may result in serious failures. n Never replace a blown fuse by a higher gauge fuse. Remember that 703j WIRING AND ACCESSORIES fuses are provided for protecting circuits in case of faults. Try to n Earthing of wiring in the coach find out the cause of fault. shall be checked both on the positive and negative wire n Loose and exposed/hanging wires separately in each coach by the should be secured and properly earth testing device. A coach with covered. In case wiring is found negative earth fault in case of 110 mechanically damaged or tampered V DC system, which could not be with or needs replacement , the attended in time, can be given in coach should be marked service in case of emergency. The electrically sick. If the work is of coach shall be taken for attention a minor nature, this may be done in by the primary maintenance maintenance lines. station during the next trip. n If the repairs are heavy the coach n Cable insulation on coaches get may be booked to Shops for damaged in various ways resulting attention. Coaches which are in earthing. Damaged insulation suspected to have wiring defect whenever noticed shall be either in the underframe or roof promptly taped with PVC tape. shall be subjected to insulation test with 500 V megger. Chapter 7, Page 9 of 21 Maintenance Manual for BG coaches of ICF design Train Lighting (Non - AC) coaches 704 FORTNIGHTLY SCHEDULE n Check the "make of cells and the lug date. Different "makes" of cells 704a BATTERY mono block if found mixed together should be replaced by a In addition to the instructions single "make " of cells. If it is not contained under "Trip examination" the possible to do this during one following works shall be carried out. Fortnightly Examination this should be noted down and attempts n Clean the interior of battery box. made to replace the same during the next Fortnightly Examination. n Clean the cell tops and deposit of sulphate, if any, in inter cell and n Check whether cell/ mono block end cell connections. packing is tight and provide additional packing, if necessary. n Remove sulphated inter cell Use only hard wood coated with connections, clean the connecting acid resistant paint for cell surface with a piece of cloth. Use packing. Never use untreated wood fresh fasteners. Sulphated internal or plywood for packing of cells/ connections and fasteners should mono block. If any cell/ mono be soaked in kerosene oil, cleaned block is found cracked, replace it with warm water and kept ready promptly. for use. Inter cell connections should be provided with both small n Check for provision of anti-theft and large strips and four fasteners rods and provision of nuts, both each with one hexagonal nut, one inside and outside the battery box spring washer to IS:3063 and two on either side. Replace deficient steel punched washers to IS:2016. rod and nuts. n Remove end cell connectors, clean n Apply petroleum jelly on inter cell the connecting surface both in cell connection and end cell and connector thoroughly and connections. Do not use grease. provide back. Check for proper crimping of terminal. In case n Check battery fuses and replace strands of connecting cable are overheated/incorrect size fuses by found cut at the crimping end, cut correct size. wire at the crimping end and re- crimp with a new inter cell n Check battery box fixing nuts for connector. End cell connector tightness. confirming to IS:6848 should only be provided. Tinned copper n VRLA Batteries : SMI.No. crimping sockets with a single RDSO/PE/TL/SMI/0001-98 IRev hole, if any, provided as a stop 0) dtd. 01.06.98 to be followed. gap measure should be replaced by standard end cell connector. 705 MONTHLY SCHEDULE Provide end cell connectors with both the fasteners each with one In addition to the works mentioned in spring washer to IS: 3063 and one Trip & Fortnightly Examination, carry punched steel washer to IS:2016. out the following: n Tap sealed float guides and check for free movement. Look for elongated holes in sealed float guides and replace such guides. Replace deficient floats promptly. n Check whether vent plugs are of the anti-splash type and replace if required. Chapter 7, Page 10 of 21 Maintenance Manual for BG coaches of ICF design Train Lighting (Non - AC) coaches 705a ALTERNATORS, RECTIFIER AND case pilot cells show no REGULATORS appreciable improvement, check specific gravity of adjacent cells. If i) Check for tightness of terminal the specific gravity does not connections of alternators and improve in spite of charging, rectifier regulators. replace the battery by another set and send the defective battery to ii) Thoroughly clean externally the Depot/Shop for treatment at the alternator and regulator. earliest. Cells should be handled with due care while unloading and iii) Open inspection cover of regulator. in transit to avoid breakage. Blow dust with a portable blower. Adequate facilities should be Secure covers tightly after created in Depot for treatment of inspection. cells which do not pick up charge. Sulphation will be the main cause iv) Check locking of current setting of for this and Sulphated cells regulator, if disturbed it should be should be treated for their recovery reset/locked as prescribed. as specified. v) Check the alternator pulley for n On completion of charging, record proper fixture and the availability the specific gravity of individual of castle nut and split pin. cells. If there is any wide variation in the specific gravity/ voltage of 705b AXLE PULLEY cells, disconnect and replace those cells showing low specific n Watch for shifting of axle pulley gravity/voltage by spare ones. In by observing the white band on case there are more than 1/3 of either side of pulley. Reset the total cells with low specific correct position of pulley, if found gravit y, the entire set should be shifted and tighten the loose nuts replaced. Cells showing reverse with torque wrench with voltage, zero volts should be recommended torque.. withdrawn and replaced by charged cells immediately. n Check tightness of nuts and also availability of chuck nuts and split n Record individual voltage of cells pins in all fixing bolts. and the total voltage on full load of the coach. 705c BATTERIES n Change the marking of the pilot i. Conventional Lead Acid Batteries cell as given in table 7.2. n Record specific gravity of ii. VRLA Batteries individual cells/mono block. "Switch on" full load of the coach SMI no. IRCAMTECH/PE /TL/ SMI/ and record individual voltage of 0001-98- (Rev.0) dtd. 01.06.98 & cells and total voltage. "Switch RDSO/PE/TL/SMI/ 0002-98 (Rev.0) dt. off" load. If the specific gravity is 09.12.98 less than that painted on the battery box, charge the cells as 705d JUNCTION BOX specified under "Trip Examination" after topping up with n Open front door. Check all DM water, if required. connections in MCB-cum-fuse panel for tightness any for heating n Use battery charging terminals sign, fuses etc. Check availability provided on coaches for charging of terminal lugs for all cables in purposes. Charging should be junction box and replace if continued till the specific gravity necessary by terminal lugs of rises to the value of mentioned in correct size. battery box, on "Pilot" cells. In Chapter 7, Page 11 of 21 Maintenance Manual for BG coaches of ICF design Train Lighting (Non - AC) coaches n Check Rotary Switch / MCBs n Studs used for fixing the fan to provided for lights, fans circuits for coach body, shall be checked and correct condition and Rotary tightened, wherever necessary. Switch and EFTs for proper Availability of all the three fixing operation. Replace/ repair studs should be ensured. defective MCBs. If MCBs are not n All the switches controlling the readily available provide fans shall be checked for its rewirable fuses of appropriate smooth operation and correct ratings, purely as a stop gap working and replaced, where measure. Check up negative fuse necessary. and replace if necessary by different ratings of HRC fuse for n Fan regulators in Upper class AC and non AC coaches. If rotary coaches shall be checked for switches are provided instead of smooth operation from one MCBs, Check for proper operation. position to the other. In case the Check up HRC fuses provided with regulators are not regulating the rotary switches for correct rating fan speed, the resistance box shall and replace, if necessary. be checked and replaced, where n Close front door and secure necessary. properly by the locking key. If n Fan blades shall be replaced if found defective, the same may be attended/replaced. found bent, or if there is no proper air discharge. 705e WIRING AND ACCESSORIES In addition to the items listed under trip 705g CARRIAGE LIGHTING inspection, the following items shall In addition to the items listed out under be inspected: "Trip Examination" proceed as follows. Superstructure wiring and underframe wiring shall be tested separately for n Open each fitting with the dome which the main negative fuse in shall be key and remove the dust of the opened and controlling MCBs for all fitting both from inside and circuits kept off. All other fuses shall outside. Ensure free operation of remain in circuit. Insulation resistance locking mechanism and er place shall be measured with all fittings and defective fitting. Clean glass equipment connected both on domes first with wet cloth and then underframe and superstructure. The with a clean dry cloth. underframe wiring shall be tested with battery fuse open. The IR value n Replace rusted fittings and fittings should be minimum 2 Mega-Ohm in with damaged surface. fair weather condition and min. 1 Mega-Ohm under adverse weather n Check up wattage of lamps and condition. Availability of inspection replace with that of correct cover of DFBs should ensured. wattage. 705f FANS n Check up whether toggle switches In addition to the items listed under " are marked to indicate lighting trip examination ", the following control "L", night light control works shall be carried out : `NL', side lamps in guards compartment as `SL', tail lamps as n The fan body, guards and blade `TL-Rear', `TL-Front', luggage shall be thoroughly cleaned with room as `LRL'. If not, stencil cloth. legends with fluorescent paint. n All fans shall be opened and n Check up all lighting circuit fuses condition of commutator, brushes in each coach for correct sizes and and brush gear shall be thoroughly replace if necessary. Stencil the checked. Action should be taken size of fuses near the locations, if where necessary as given under not already done. "Trip Attention". Chapter 7, Page 12 of 21 Maintenance Manual for BG coaches of ICF design Train Lighting (Non - AC) coaches n Terminate charging when 3 n Mark inspection covers of successive readings are constant. Distribution fuse boards as `DFB' Record specific gravity and no if not done already. load voltage of each cell 10 minutes after terminating charge. n Thoroughly clean metal guards fo r Specific gravity should be between roof light fittings in luggage rooms 1.210 and 1.220 for cells upto 120 and paint, if necessary. Ah capacity. The voltage should not be less than 2.1 V. 705h TUMBLER / TOGGLE SWITCHES n If there is a wide variation in the Check each toggle switch of lights specific gravity and voltage and fans for proper fixing and readings, such cells should be operation. Replace defective toggle replaced and sent to shops for switches. Toggle switches should treatment. be provided in the locations intended for them and provided n Check the cell voltage on full load. with covers with their knobs Cells showing reverse and low exposed for operation by voltage are to be replaced with passengers. hwalthy cells of the same make/type. 705i DISTRIBUTION FUSE BOARDS AND FUSE CUT OUTS ii. VRLA Batteries : Check distribution fuse boards and SMI no.RDSO/PE/TL/SMI-0001- fuse cut outs of light and fan circuits, 98 (Rev.0) dt.01.06.98 & for tightness of connections and RDSO/PE/TL/SMI/0002-98 provisions of correct size of fuses in (Rev.0) dt. 09.12.98 to be the fuse terminals. Replace missing followed. distribution fuse board covers. 707 HALF YEARLY SCHEDULE 705j EMERGENCY FEED TERMINALS (EFTs) Measure insulation values as follows: n Check up supply and marking of 707a SUPER STRUCTURE polarity of EFTs. Short all the outgoing positive n Replace missing EFTs and those terminals from MCB cum fuse panel. without wiring nuts. Measure and record the following 706 QUARTERLY SCHEDULES insulation values: 706a BATTERIES n Between the bunched outgoing terminals and earth. In addition to the instructions contained under "Monthly n Between the bunched outgoing Examination" following activities positive terminal and main should be done: negative outgoing terminal. i. Conventional Lead Acid n Between the main negative Batteries outgoing terminals and earth. n `Switch off’ load. Charge the cells 707b UNDERFRAME at 50% of normal rate of charge, i.e., at 1/10th of the rated capacity Short the incoming terminals PM and of cells. Record hourly cell L+ in MCB cum fuse panel. Measure voltage and specific gravity and record the following insulation reading of every cell. values: Chapter 7, Page 13 of 21 Maintenance Manual for BG coaches of ICF design Train Lighting (Non - AC) coaches n Between the bunched terminals PM n Check voltage drop between & L+ and earth. battery and the farthest light or fan point with full coach load “on”. n Between the bunched terminals PM The voltage drop should not & L+ and main negative exceed 3.0 V. incoming terminal. n Between the main incoming n Provide deficient switch and fuse negative terminal and earth. covers promptly. Note: Insulation resistance under fair n Coach wiring should be terminated weather conditions shall be minimum 2 in two way connectors which mega ohm. However under adverse shall be of tough non-ignitable (highly humid/wet) weather conditions, moulding materials of rigid PVC the minimum insulation resistance upto from which connection to the 1 M.ohm will be acceptable. fitting shall be provided by In case the insulation resistance is flexible single core cables for the found less than the values mentioned following : above, individual sub-circuits at junction box for super structure wiring Fans and different feeders for underframe Reading light fittings wiring shall be meggered separately. Side light fittings The sub-circuit having an insulation Tail light fittings value lower than that prescribed above Step light fittings. shall be taken up for rewiring. If the nature of repairs is heavy, the coach n Provide missing connectors. shall be booked to shops for attention. Do not resort to patchwork in wiring n All cable ends shall be properly with temporary joints. socketed. Provide crimping type sockets wherever this is not in Proceed further as follows: existence. Use sockets of appropriate size. Corrosion n Strands of alluminium wire cannot inhibiting conducting grease shall serve as tinned copper fuses to be applied to the conductor as well protect circuits. Never resort to as inside the socket before this habit. crimping. Soldered joints should ordinarily be avoided, where this is n Use crimped socket of appropriate absolutely necessary, only size in all cable ends to avoid approved grade of solder and flux loose connections and shall be used. consequent overheating. n Electrical connections provided n Use corrosion inhibiting with bolts and nuts shall be conducting grease while crimping checked and provided with a set cables or while connecting wires of mild steel plain washer and to prevent oxidation. spring washers, protected against corrosion by Zinc or Cadmium n Stencil the correct size of fuses plating and passivation. Use near the locations, if not already correct tools for tightening cable done. connections. n Check all fuses and MCBs for n Surface of aluminum sockets and correct rating and MCBs for proper bus bars, whenever removed for functioning. Replace if necessary. attention shall be cleaned to remove the oxide film from the n Provide spare fuse wires of correct jointing surface before making a rating for use in branch circuits on bolted joint and shall be coated the bobbins located on distribution with corrosion inhibiting fuse boards. conducting grease to prevent re- formation of oxide film. Chapter 7, Page 14 of 21 Maintenance Manual for BG coaches of ICF design Train Lighting (Non - AC) coaches Field terminals and stator n V-Belt : The existing V-Belts shall terminals be replaced with the new V-belt. 4 nos. having same make/grade. The (Note : Minimum insulation resistance old V-belts removed from service should not be less than 1 Mega ohms to be destroyed. for 4.5 kW under worst weather conditions and 20 mega ohm for 708 POH SCHEDULE 18/22.75 kW respectively) 708a BRUSHLESS iii. OVERHAULING ALTERNATOR n The machine received for The procedure to be followed shall be overhauling should be externally as per guide lines given below. cleaned with wire brush and wiped before dismantling. i. VISUAL INSPECTION n Clean and re-grease the bearing Carry out visual inspection of the after removing the bearing from machine and record the following:- the bearing housing. Only Servo Gem (RR-3) grease shall be used. n Serial number and name plate particulars of the machine. n Clean the mating surface of the end shield. n Check that rotor rotates freely. n Check the suspension bushes. n While removing and placing the rotor, care should be taken that the n Check insulation resistance rotor does not rub over the field n Check continuity of the field coils. and stator n If any grease has crept into the n Check alternator tension rod stator surface, clean it before n Check the bearing noise with assembling. shockpulse meter n If stator and rotor parts are found rusty, clean. Apply the insulating ii. ELECTRICAL CHECKS varnish (air drying) of recommended grade. Impregnation Carry out the following electrical of the varnish shall be done in an checks and record the following: - air circulated oven. n Open the cover of the terminal box n Change the alternator suspension and check whether the internal nylon bushes 100% and change the termination and terminal board are suspension pin on condition basis. intact. n Tighten all the connections on the n Apply the insulating varnish (air terminal board. drying) of recommended grade. n Using a multimeter, check Impregnation of the varnish shall continuity between be done in an air circulated oven. Field terminal F+&F- Stator terminals U&V, V to W n After complete fitment and and W to U greasing, the bearing noise shall be recorded using shock pulse meter. n Check the insulation resistance by 500 V megger between n Only bearing of SKF/FAG shall be provided as per recommendation of Stator terminals and frame of RDSO. machine Field terminals and frame Chapter 7, Page 15 of 21 Maintenance Manual for BG coaches of ICF design Train Lighting (Non - AC) coaches iv. TESTING OF ALTERNATORS speed from 600 rpm to 2400 rpm. Setting shall be done at INSULATION RESISTANCE TEST 1500 rpm and half load 19A before starting the test. Check the insulation resistance Alternator The voltage should not exceed ± 5 % of the set Place of Check Required Value for voltage at a speed from 600 Conventional Coaches rpm to 2400 rpm. The set voltage can be 120 V, 122 V, Between stator. Above 1 M Ω 124 V at 19 Amp. 1500 rpm. winding and earth Check the MFO (minimum speed for full output) i.e. 37.5 Amp. for 4.5 kW alternator, it Between field Above 1 M Ω should not be more than 600 winding and earth. rpm. Between field Above 1 M Ω vii. TEMPERATURE RISE TEST winding and stator. For 4.5 kW Alternator Regulator Run the alternator at 600 rpm Place of Check Required Value and apply the load. The alternator Conventional Coaches should be capable of giving 37.5 Amps at 120 Volts. Run the Short all terminal alternator at 2500 rpm with full (live parts) together Above 1 M Ω load for five hours with a fan and check the insulation cooling the body. Check the resistance between the temperature at different part of the live parts and earth. alternator and should be as follows:- Note: The insulation resistance of all the above should be measured a) Power diode - Should not exceed by 500 V megger. 100 0C at ambient of 500 C. v. NO LOAD TEST b) Alternator terminal - Should Connect the alternator not exceed 100 0 C and regulator with a at ambient of 500 C. resistance/battery load. Run the Alternator at base load (1 c) Bearing temperature - Should not A) at various speed from 357 exceed 85 0 C at rpm to 2500 rpm. ambient of 50 0 C. This voltage should d) Stator and Field - Should not not exceed ± 5% of set the exceed 900 C at voltage. The cut in speed win ding load of should also be checked. It 37.5 Amps. should not be more than 357 rpm at 108 volts at zero load. 708b RECTIFIER REGULATOR UNIT vi. LOAD TEST The procedure to be followed shall be as per guidelines given below. Connect the alternator and regulator with n Check the terminals and inside resistance/battery load. Run wires for heating signs and the alternator at half load i.e. looseness. Blow out the dust. 19 Amp. and full load 37.5 Amp. respectively at various Chapter 7, Page 16 of 21 Maintenance Manual for BG coaches of ICF design Train Lighting (Non - AC) coaches n Replace the damaged n Record voltage and specific gravity wiring/terminals. The wiring of the of each cell. regulator shall be done n Clean exterior of the cell/ mono systematically, block thoroughly. Wash top of the battery with a 10% solution of soda n Check the PCB circuit with PCB and a wire brush. During such testing kit or multimeter to identify cleaning, it is necessary to ensure defective components. Replace the that the micro porous vent plugs defective components. are mounted on the cells so that the water does not enter into the cells. n Check field transformer for correct voltage. Replace, if found n Battery boxes shall be defective. cleaned/repaired and repainted with anti corrosive epoxy based paint 708c V- BELTS/ TENSIONING GEAR after removing the bat tery. Check the opening of welds and cracks n The existing V belts shall be thoroughly specially on load replaced with the new V belts 4 bearing members, vicinity of Nos. having same grade/make. The mounting bolts etc. Detection of old V belts removed from service minor hair line crack shall be done to be destroyed. with ultrasonic testers. n Top up cells wherever necessary n Tensioning gear shall be removed with distilled water. The level and its spring shall be checked fo r proper functioning. If required should be corrected as indicated on the float. moving parts of tensioning device including spring shall be replaced. n If there is corrosion/sulphation on the inter-cell- connectors etc., clean 708d ‘V’ GROOVED AXLE PULLEY them thoroughly and protect from further corrosion by applying The procedure to be followed shall petroleum jelly or Vaseline. Cell be as per guidelines given below: connectors and fasteners should be changed on condition basis. n Check the axle pulley for slippage, n Replace defective sealed float tightness and physical damage to guide and micro porous vent plugs, grooves. Ensure availability of if any. locking nuts and split pins in position. Check the alignment of n Clean micro porous vent plugs and axle pulley with the alternator sealed float guides and ensure that pulley and adjust. Change the vent holes are in order. rubber packing. n Record lug date to determine the n Replace the pulley if any groove is life of the battery. damaged/broken/worn-out. n Charge the battery fully till 3 constant half hourly readings of n The pulley shall be replaced after voltage and specific gravity are four years period or earlier on obtained. This will indicate that condition basis. battery is fully charged. 708e BATTERY AND BATTERY BOX n Discharge the battery at 10 hrs discharge rate. While discharging, The procedure to be followed shall be record the voltage and specific as per guidelines given below. gravity. n Record the capacity of the battery n Remove the cells from the battery during discharge. It should not be boxes on arrival of the coach in less than 80% of the rated capacity. workshop and bring them in the battery shops for maintenance. Chapter 7, Page 17 of 21 Maintenance Manual for BG coaches of ICF design Train Lighting (Non - AC) coaches n In case while discharging, any of ii. Cable termination joint the cells fall below 1.8 volts, disconnect the cell from the circuit n All cable joints shall be for treatment with one or two checked for its loosness or cycles of slow charge and heating signs. Loose joints and discharge. cables having damaged insulation shall be n After two cycles of charge and replaced/repaired. All cable discharge, recharge the cells fully. ends shall be properly socketed with crimping type n Battery box vertical/horizontal sockets. member shall be checked for any n Surface of crimping sockets minor/hair line cracks, its and bus-bars shall be cleaned mounting arrangement ensuring to remove the oxide film from proper securing through nut the jointing surface before bolts/washers etc. making a bolted joint and shall be coated with corrosion n In case of VRLA Batteries, SMI resistant conducting grease of no.RDSO/PE/TL/SMI/0001 -98 approved make to prevent (Rev.0) dt. 01.06.98 and reformation of oxide film. RDSO/PE/TL/SMI/0002-98 (Rev.0) dt. to be followed. n Fire retarding PVC grommets to IS:1767 or grade 6 of 708f WIRING (After 2 years for new coaches IS:5831 shall be provided at and 1 year for old coaches) all cable entry points in metallic members. The wiring shall be completely n The under -frame wiring if inspected for damage by opening side running loose shall be panels, end wall near EFT's and also provided in flexible steel near fittings after stripping. The re- conduit. wiring shall be done on condition basis or planned on the basis of life of 20 n All inspection covers shall be years for cables. opened to check the distribution boards and The cables used for re-wiring condition of wiring. shall be as per IS:694-1990 (Third Revision) The cables taken up for re- iii. General Precautions wiring shall be done through PVC conduits in super structure conforming n Do not peel insulation for to IS:2509. Bushes/Grommets used testing. If wires are found shall be of Hard PVC as per BS:1767 - with peeled insulation replace 1951 or to grade 6 of IS-5831 latest. them with fresh wires. If Flexible conduits used, if any, under peeling is of short length water tank shall be as per IS:6946. apply proper PVC adhesive tape. i. Coach insulation n Do not use twisted joints of Insulation resistance of the coach aluminum cables to avoid shall be measured with 500 V oxidation and improper megger. IR value should be contacts and over minimum 2 Mega ohms but it heating/earth fault due to should not be less than 1 Mega loose strands. ohm under highly humid/wet weather. n Remove earth fault by isolation method instead of hit and trials and short cir cuiting of opposite polarity of earth. Chapter 7, Page 18 of 21 Maintenance Manual for BG coaches of ICF design Train Lighting (Non - AC) coaches n Use proper rating of fuses both in branch circuits, rotary 708h FANS panels and regulator boxes for field and main fuse. n Dismantle the lower guard, upper guard, blade and fan motor. n Use HRC fuse to the extent possible except for branch n Check the guard assembly, which may be done with re- repair/replace if necessary. wirable tinned copper fuse. In the absence of HRC fuse use n Check the blade angle with a correct size equivalent re- measuring gauge. Correct the wirable fuse. Do not use same, if necessary. under rated or over rated rewirable fuse to avoid faulty n Check the insulation resistance of tripping of defective circuits. the fan motor. The IR value should not be less than 2 Mega ohms as n Use connectors for lights & specified in IS: 6680-1992. fans. n Check the fan leads and change it n Ensure extra length of cables if necessary. near termination’s for future maintenance and replacement, n Check the armature winding and if found inadequate at the field coil, repair/replace, if earliest opportunity. necessary. n Check for earth fault on every n Check the commutator for maintenance and rectify those grooving, pitting marks, ovality, detected. blackness etc. Polish the commutator if required. n Do not tamper with regulator potentiometer setting unless n Check the carbon brush and brush tested in a proper alternator spring. Replace by correct grade of drive having variable speeds. carbon brush as recommended by RDSO. The fan spring should 708g SWITCHES, LIGHT FITTINGS, meet the requirements given in ETC. IS:6680. Replace the same if necessary. i. Light fittings n Apply air drying insulating varnish The light fittings, reflectors, clear if IR value of the armature and acrylic sheet cover, glass globe, field coils is low, give holders, etc., shall be checked and impregnation treatment in an air cleaned. Any defective part shall be circulated oven. replaced. Ant i- theft arrangement for fluorescent light fittings shall be n Clean the ball bearing, check for checked as per ICF Drg. No. noise, replace if necessary or ICF/SK-7-6-079. grease it with recommended grade grease. ii. Rotary Switch Cum Junction Box Testing Strip the housing from the coach and clean thoroughly and remove i) Check the load current at oxidation from terminal points and rated voltage. The wattage check the function of rotary of the fan should not exceed switches. Fit back the same and do the value specified in IS: the connections using corrosion 6680. inhibiting compound for better conductivity and to avoid oxidation of all contacts. Chapter 7, Page 19 of 21 Maintenance Manual for BG coaches of ICF design Train Lighting (Non - AC) coaches ii) Check the air delivery of one or two fans from a batch n Do keep the terminal box to ascertain the correctness tightly closed. of the blade angle. The value of the air delivery n Do open the terminal box shall not be less than that once in a week and clean the specified in IS:6680. accumulated dust, if any. NOTE : n Do check tightness of the connection regularly, at least n SKF/FAG (imported) make once in a week. bearings for alternator procured directly from manufacturers as n Do use the cable grommets specified in the RDSO or cable gland of correct size specification shall be used. Use of for reducing the vibration of other makes of bearing is not terminal connections. It is permitted. preferable to anchor the cables externally to avoid n Shock pulse meter shall be shocks and vibrations on the procured by Railways and terminals. workshops to monitor condition of the bearing regularly during ii. DON’TS maintenance service and after replacement of defective bearings. n Don’t use improper tools to handle the alternator, it may n Induction heater/oil bath shall be damage parts of the alternator. used for heating the bearing to the required recommended n Don’t re-grease the bearing temperature. frequently. Re-greasing should be done after n The pulley condition such as wear thoroughly cleaning the on V group, pulley key way, shaft bearing with white spirit. It way, groove angle etc. shall be is preferable to re-grease the monitored during POH. Proper bearing only during POH. gauges shall be used for checking "V" groove of the pulley. n Don’t over-grease the bearing. 709 DO’S AND DON’TS FOR MAJOR EQUIPMENT n Don’t keep the belts in over tension as this may reduce 709a ALTERNATOR life of the belt. i. DO’S 709b REGULATOR n Do ensure the correct i. DO’S polarity of field winding i.e. positive connected to F + n Do check the regulator while measuring the terminal box once in a continuity of the field month for loose connections winding, otherwise the and for cleaning the dust. alternator will not self excite. n Do short all seven terminals of the terminal box before n Do check the proper measuring the insulation compression force on the resistance. tensioning spring with indicator plate by tightening the special nut. Chapter 7, Page 20 of 21 Maintenance Manual for BG coaches of ICF design Train Lighting (Non - AC) coaches n Do ensure that DC ‘+’ and upto the split pin for the 18 DC ‘-’ are connected to kW, 22.75 kW, 25 kW battery positive and battery Alternators and 55 mm for negative respectively. 4.5 kW alternators. Wrong connection will damage main diodes. n Maintain proper alignment between