Gestione della Sicurezza PDF
Document Details
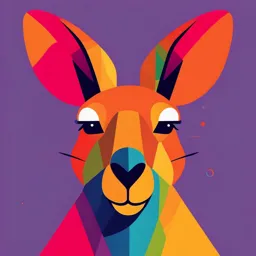
Uploaded by CelebratedMatrix768
Tags
Summary
Questo documento tratta la gestione della sicurezza negli ambienti di lavoro italiani. Analizza l'evoluzione storica delle normative e dei rischi professionali. Il testo include una lista di norme e regolamenti, oltre a un'analisi dei diversi tipi di rischi, dall'incendio al rumore, con le relative misure per la prevenzione.
Full Transcript
GESTIONE DELLA SICUREZZA 1. EVOLUZIONE STORICA 2. NORMATIVE: DPR 547/55, DPR 302/56, DPR 303/56, DPR 626/94, D. lgs 242/96, DPR 459/96 (D.M.), D.M 2006/42/CE, D. lgs 81/08, D. lgs 106/09 3. CIFRA DI RISCHIO, CURVA ISORISCHIO, CURVA COSTI EFFICACIA, PROGETTAZIONE FABBRICATI INDUSTIALI, SEGNA...
GESTIONE DELLA SICUREZZA 1. EVOLUZIONE STORICA 2. NORMATIVE: DPR 547/55, DPR 302/56, DPR 303/56, DPR 626/94, D. lgs 242/96, DPR 459/96 (D.M.), D.M 2006/42/CE, D. lgs 81/08, D. lgs 106/09 3. CIFRA DI RISCHIO, CURVA ISORISCHIO, CURVA COSTI EFFICACIA, PROGETTAZIONE FABBRICATI INDUSTIALI, SEGNALETICA 4. RISCHIO INCENDIO: curva T, progettazione: PASSIVA (REIm, CARICO INCENDIO), ATTIVA, classificazione incendi 5. RISCHIO ELETTRICO: Auto produzione vs. Fornitura esterna, effetti sull’uomo, limiti di pericolosità, sistemi di protezione, incidente per tensioni di contatto 6. ERGONOMIA: adattamento del lavoro all’uomo, fisiologia del lavoro, rapporto uomo-macchina, carico di lavoro 7. MICROCLIMA: meccanismi termoregolazione, equazione bilancio termico, variabili da considerare, ambienti da analizzare e valutazioni 8. RISCHIO ESPLOSIONE: aree atmosfere esplosive, classificazione apparecchi 9. RISCHIO CHIMICO: classificazione in base al pericolo, indici di valutazione 10. RISCHIO POLVERI: metodo MOVARISCH, metodologia EMILIA-ROMAGNA (rischio inalatorio, cutaneo e cumulato), classificazione agenti chimici 11. RISCHIO BIOLOGICO: classificazione agenti, pericolosità agenti biologici, HACCP, PRINCIPI e PASSI 12. RISCHIO RUMORE: rumorosità globale (rumore di fondo e ambiente), apparato uditivo, FONOMETRO, livello sonoro equivalente e livelli di esposizione, misure protezione e prevenzione 13. RISCHIO VIBRAZIONI 14. RISCHIO MECCANICO: norme tecniche ARMONIZZATE europee (tipologia), IMMISSIONE sul mercato vs. MESSA IN SERVIZIO, MARCATURE CE, valutazione dei rischi 15. GESTIONE DELLA QUALITÀ: concetto, ISO 9000-9001-9004, a. 7 METODI: fogli raccolta dati, analisi Pareto, diagramma causa/effetto, istogrammi, diagramma di correlazione, analisi di regressione, carte di controllo (esercizi xr, esercizi pn). b. COLLAUDO (tipi piani campionamento, progettazione piano campionamento, esercizi), curve operative OC 16. GESTIONE DELLA MANUTENZIONE: c. POLITICHE: - correttiva (o a guasto) - preventiva: statistica (time based / used based), condizionale (predditiva / sotto condizione). - produttiva - migliorativa d. (opportunistica, ispettiva, per sostituzione) e. PARAMETRI MANUTENTIVI: MDT tempo medio di guasto; MTBF tempo medio tra due guasti; MTTF tempo medio al guasto per sistemi non riparabili; MTBM tempo medio tra eventi di manutenzione; MTTR tempo medio di riparazione f. DISPONIBILITA’ e TIPOLOGIE g. MODELLI: - preventivo ad età costante (esercizio) - preventivo a data costante (esercizio) - politica ispettiva elementare (macchina singola) (esercizio) - minimizzazione del costo atteso UDT - massimizzazione del profitto (B.I) h. GESTIONE DEI RICAMBI: Caratteristiche e Categorie, Metodi Previsione i. CRITERIO COSTO GLOBALE MINIMO j. CRITERIO LIVELLO DI SCORTA k. SIM, FRAMEWORK CONCETTUALE SIM, CMMS l. MANUTENZIONE REMOTA 17. SVILUPPO SOSTENIBILE: concetto, 3 dimensioni, Agenda2030, 5P, 17 goals: (12, 13), LCA, SIMAPRO, FASI SICUREZZA DEGLI IMPIANTI INDUSTRIALI La sicurezza è una parte delle attività industriali che riguarda l’interazione tra: 1. UOMO-MACCHINA-AMBIENTE (come nel caso dell’ERGONOMIA à che è la disciplina scientifica che si occupa dei problemi relativi al lavoro umano in rapporto alla progettazione delle macchine e agli ambienti di lavoro, al fine di individuare le soluzioni più idonee alle esigenze psicofisiche dei lavoratori e al contempo a quelle della produzione). 2. UOMO-UOMO: in generale di problematiche lavorative legate alla non corretta interazione tra uomo e uomo sul luogo di lavoro. 3. UOMO-AMBIENTE (ecologia): non solo l’impatto che l’uomo ha sull’ambiente ma anche il legame tra ambiente e uomo in cui quest’ultimo si presta a svolgere l’attività lavorativa. ATTIVITÀ PRODUTTIVA-AMBIENTE (impatto ambientale). Quando si parla di sicurezza sul lavoro non s’intende solo il RISPETTO DI NORMATIVE, ma è fondamentale L’ETICA nel rapporto professionale, cioè comportarsi secondo principi etici durante lo svolgimento del lavoro. Molto importante è anche l’aspetto ERGONOMICO poiché l’uomo deve muoversi all’interno di un contesto che dal punto di vista delle situazioni lavorative e del rapporto UOMO-MACCHINA- AMBIENTE si presti bene allo svolgimento delle attività, quindi dev’essere posizionato in un’ambiente con macchine e attrezzature che siano idonee allo svolgimento corretto della propria attività. Questi tre ambiti: sicurezza, ergonomia ed etica vanno a essere inter-correlati e soprattutto rivisti nell’ottica delle nuove tecnologie, quindi quelle norme valide dieci anni fa devo essere riscritte poiché sono obsolete dal momento che la tecnologia è avanzata sempre di più. (esempio: nell’ambito dei robot collaborativi che durate l’attività manufatturiera può aiutare il lavoratore come nel montaggio di alcuni componenti all’interno di una scheda elettronica e in questi casi l’operatore svolge le operazioni più difficile per poi lasciare alla macchina le operazioni di routine per poi nuovamente subentrate l’operatore per controllare oppure apportare modifiche. Con le norme precedenti ciò non era ammesso, ma con l’avanzamento della tecnologia questa interazione tra uomo-robot è stata rivista) La sicurezza sul lavoro ha tanti diversi temi poiché deve affrontare diversi aspetti che possono essere legati: § ALL’IGIENE DEL LAVORO che vede al suo interno tutto quello che è una valutazione dei rischi riguardo l’ambiente in cui si lavora, ovvero viene valutato l’ambiente de è soggetto ad agenti chimici, radiazioni, rumore e così via. § l’ERGONOMIA cioè l’adattamento del lavoro all’uomo al fine di individuare le soluzioni più idonee alle esigenze psicofisiche dei lavoratori. § RISCHI SPECIFICI cioè temi che portano all’infortunio (evento traumatico conseguente ad un incidente), cioè ad una manifestazione immediata del danno attraverso a causa di un incidente (un incendio, un’esplosione e così via) § ANTINFORTUNISTICA cioè l’utilizzo di sistemi di protezione, la segnaletica, misure organizzative che permettono di organizzare il lavoro e tutto ciò permette di prevenire determinati rischi. Negli anni inoltre è entrato a far parte la MEDICINA DEL LAVORO cioè uno studio più approfondito del lavoratore tramite il medico competente per evidenziare l’insorgenza di tecnopatie (malattie professionali che sono tabulate e monitorate da INAIL e inoltre il datore di lavoro è obbligato ad assicurare dal 1934) o prevenire determinati rischi specifici. EVOLUZIONE STORICA DELLA SICUREZZA Il tema sulla sicurezza è stato affrontato molto bene dall’Europa e ancora oggi ha una sensibilità molto alta su ciò rispetto ad altri paesi. Tale sicurezza sul lavoro è nata in Europa fin da quando è nata l’attività industriale, nella metà dell’800 nei paesi anglosassoni in cui vi sono state le prime leggi quadro e normative applicative sulla sicurezza. In Italia invece con la creazione di un gruppo di industriali milanesi verso la fine dell’800 (1894) prendendo spunto dai paesi anglosassoni emergono i primi interessi legati alla sicurezza sul lavoro. Da qui nasce un’Associazione Prevenzioni Infortuni API per occuparsi di valutare a livello nazionale infortuni e soprattutto su come prevenirli. Poco dopo (17 marzo 1898, n.80) il parlamento italiano emana la prima legge specifica in materia di sicurezza in particolare riguardo la valutazione dell’assicurazione sul lavoro e di norme specifiche per le principali attività imprenditoriali. Nel 1920 l’API prese una connotazione più nazionale divenendo ANPI Associazione Nazionale Prevenzioni Infortuni in cui parte anche un compito di vigilanza tecnica, normativa e antinfortunistica. Nel 1927 (14 aprile) è stato emanato un Regolamento D’igiene Sul Lavoro che fissava una serie di regole sulla prevenzione igienica del lavoro, la cui prima norma sancisce la necessità di un ambiente di lavoro sano. Nel 1932 vi fu la soppressione dell’ANPI per generare l’Ispettorato dell’industria e del lavoro (con funzione di controllo del lavoro, cioè di quello che era l’applicazione delle leggi sul lavoro e di previdenza sociale. Inoltre, trasmettere al ministero dell’economia notizie e informazioni relative alle condizioni e allo svolgimento della produzione nazionale) e l’ENPI (ente nazionale prevenzione infortuni con una funzione di ricerca normativa). Nel 1948 con la costituzione della repubblica italiana che sancisce il diritto alla salute à Art. 32. “La Repubblica tutela la salute come fondamentale diritto dell'individuo e interesse della collettività, e garantisce cure gratuite agli indigenti”. Nel 1955 vi fu l’abolizione dell’ENPI e i compiti vengono affidati ai comuni, alle regioni e agli organi centrali dello stato (Art. 72). A livello nazionale si ha un parlamento che da inizio ad emanare una serie di norme più specifiche e dettagliate legate al mondo del lavoro come il DPR 547/55 riguardante le norme per la prevenzione degli infortuni sul lavoro. Nel 1978 vi è l’attuazione della riforma sanitaria in cui ENPI E ANCC vengono soppressi e confluiscono in USL/ASL (L.833/78) con ruolo di controllo (à Legge 23 dicembre 1978, n. 833 Art. 1 la repubblica tutelando il diritto alla salute come fondamentale diritto dell’individuo mediante il servizio sanitario nazionale che crea una struttura di monitoraggio di attività produttive. Art. 10 le unità sanitarie locali si occuperanno della gestione e della tutela della salute) e nel 1980 in ISPESL Istituto superiore per la prevenzione e la sicurezza del lavoro (D.P.R. 619/80) che era un organo tecnico-scientifico con ruolo di ricerca e proposta normativa che ad oggi è stato abolito ed è sotto INAIL (Istituto Nazionale Assicurazione Infortuni sul Lavoro) à svolge un’importante funzione di valutazione del fenomeno infortunistico poiché ha come prerogativa iniziale l’assicurazione contro gli infortuni sul lavoro. Riceve tutte quelle che sono le denunce per infortuni superiori ai 3 giorni legati all’indennizzo per salario perduto oppure di una rendita (morte). Le statistiche che INAIL svolge ci informano sull’infortuni sul territorio nazionale ci mostrano l’evoluzione sulle varie tipologie dei rischi in base ai cambiamenti dell’evoluzione del tipo di lavoro. Dall’INAIL vengono forniti anche degli indici di frequenza in base alle tipologie di lavoro per verificare anche l’evoluzione negli anni. Altro aspetto importante è legato agli avvenimenti “in itinere” riguardo infortuni che si verificano durante il percorso tra abitazione del lavoratore e il luogo del lavoro si ha una copertura assicurativa che viene prescritta dal datore di lavoro. Fondamentale passaggio a livello normativo fu il D.Lgs.626/94 poiché fu la prima norma gestionale in ambito sicurezza che definisce l’SPP Servizio Prevenzione e Protezione come “l’insieme delle persone, sistemi e mezzi esterni o interni all’azienda, finalizzati all’attività di prevenzione e protezione dai rischi professionali nell’azienda”, quindi una funzione di ‘’staff ‘’ con prevalente consulenza alle funzioni aziendali (identificare fonti di rischio, effettuarne la valutazione, individuare le misure di sicurezza, elaborare misure preventive/protettive, proporre programmi di informazione/formazione). BASI LEGISLATIVE E NORMATIVA ITALIANA SULLA SICUREZZA Molte norme che riguardano la sicurezza sul lavoro sono presenti nel codice civile (CC), nel codice penale (CP), nella costituzione oltre che in normative specifiche che vedremo nel dettaglio più avanti. Partiamo dal CODICE PENALE con l’art. 347 evidenzia che “chiunque omette di collocare impianti, apparecchi o segnali destinati a prevenire disastri o infortuni sul lavoro, li rimuove o li danneggia è punito con reclusione fino a 5 anni”. Altri aspetti del CODICE PENALE come l’art. 451 evidenzia che “chiunque per colpa omette di collocare, rimuove o rende inservibili apparecchi o altri mezzi destinati all’estinzione di un incendio [...] è punito con la reclusione fino ad un anno”. Altri aspetti della COSTITUZIONE con gli articoli 32 e 35 sono incentrati sulla tutela del lavoro e il diritto alla salute. NORMATIVE DI INTERESSE: Queste prime tre sono norme introdotte a distanza di un anno, dopo la Seconda Guerra Mondiale, nel momento della ripartenza dell’Italia a livello industriale. Sono state delle norme di base poiché sono state quelle a cui ci si è affidati nel realizzare le industrie. 1. DPR 547/55 “Norme per la prevenzione degli infortuni sul lavoro”: norma più tecnica che tratta temi legati alla prevenzione degli infortuni sul lavoro (norme generali di protezione delle macchine, mezzi di sollevamento, di trasporto, immagazzinamento, impianti e apparecchi vari e elettrici, materie e prodotti pericolosi o nocivi, mezzi di protezione personali, manutenzione e riparazione). CAMPO DI APPLICAZIONE: le norme del decreto riguardano tutte le attività alle quali siano addetti lavoratori subordinati a meno di alcune specifiche attività che non si applicano in quanto gestiti da appositi provvedimenti (come i servizi e gli impianti gestiti dalle Ferrovie dello Stato, dal Ministero delle poste). La 547/55 stabilisce gli obblighi per: DATORE DI LAVORO, DIRIGENTI E PREPOSTI LAVORATORI 1. Attuare le misure di sicurezza previste nel 1. Osservare le misure disposte dal datore di decreto lavoro 2. Rendere edotti i lavoratori riguardo i rischi a cui 2. Usare con cura i dispositivi di sicurezza sono esposti 3. Segnalare problemi dei dispositivi e dei mezzi di 3. Esigere che i lavoratori osservino le norme di sicurezza e protezione sicurezza e usino i mezzi di protezione a 4. Non rimuovere o modificare i dispositivi disposizione. 5. Non compiere manovre o operazioni che non sono di propria competenza. 2. DPR 302/56 “Norme per la prevenzione degli infortuni sul lavoro, integrative a quelle del DPR 547/55”: l’anno dopo è seguita un’integrazione in cui si sono integrati aspetti che precedentemente erano risultati carenti in dettaglio o mal interpretabili. Stesso CAMPO DI APPLICAZIONE della 547/55 (introducendo il settore esplosivi, collaudi e mole abrasive). 3. DPR 303/56 “Norme generali per l’igiene del lavoro”: sempre nello stesso anno fu emanato un’ulteriore DPR per evidenziare tutte quelle tipologie di rischio che caratterizzavano l’igiene del lavoro. Il CAMPO DI APPLICAZIONE riguarda tutte le attività alle quali sono addetti lavoratori subordinati, dunque non solo attività industriali, ma anche attività di servizio. Inoltre, con l’art. 6 vengono fissati i limiti minimi per altezza, cubatura e superficie dei locali chiusi destinati o da destinatari al lavoro nelle aziende che occupano più di 5 lavoratori. Questo ci fa capire come già ci fossero dei limiti legati alla occupazione degli spazi. L'osservanza dei limiti stabiliti dal presente articolo è estesa anche alle aziende industriali che occupano meno di 5 lavoratori quando le lavorazioni che in esse si svolgono siano ritenute, a giudizio dell'Ispettorato del lavoro, pregiudizievoli alla salute dei lavoratori occupati. Sulla base di ciò si è creata l’industria e i diversi controlli dal 56 in avanti. 4. D.Lgs. 626/94: A livello di attività è una norma che ha introdotto in particolare una nuova struttura a livello di organizzazione aziendale, dunque la parte di principale interesse è legata alle disposizioni generali ai luoghi di lavoro. Tutto il resto è stato preso da altre norme precedenti ed inserite. CAMPO DI APPLICAZIONE: tale decreto è esteso in tutti i settori di attività privati o pubblici e l’applicazione vale per tutto il territorio nazionale essendo un recepimento europeo. Inoltre, si sono riprese delle definizioni presenti già all’interno della 547 e della 303 ma con qualche differenza legate sia al (persona che presta il proprio lavoro alle dipendenze del datore di lavoro) al (soggetto titolare del rapporto di lavoro con titolare dei poteri decisionali e di spesa). Viene definito anche (ELEMENTO INNOVATIVO) servizio di prevenzione e protezione dai rischi definito come insieme delle persone, sistemi e mezzi esterni o interni all'azienda finalizzati all'attività di prevenzione e protezione dai rischi professionali nell'azienda. Per macro-aziende ci si avvale di un SPP INTERNO (a volte anche più di uno) mentre per micro-aziende è possibile anche di un servizio di SPP ESTERNO che fa da consulente per una o più aziende. A capo del servizio prevenzione e protezione dai rischi abbiamo responsabile del servizio prevenzione e protezione cioè persona designata dal datore di lavoro per assisterlo nella valutazione dei rischi. Il suo ruolo è quello consulenziale nei confronti del datore di lavoro, cioè esperto in tema prevenzione e protezione dei rischi che affianca il datore di lavoro nello svolgimento delle sue attività. Si occupa in ambito tecnico di tutta la sicurezza e all’interno di una riunione collegiale può o meno approvare il documento di valutazione dei rischi e definire le azioni per aumentare la sicurezza in azienda. Le fasi importanti per ridurre le situazioni di pericolo e i rischi connessi alle attività lavorative sono: la PREVENZIONE, infatti viene chiarito il concetto di prevenzione ovvero evitare o diminuire rischi professionali all’interno dell’attività produttiva o alla popolazione attigua all’ambiente di lavoro. Per questo viene definito agente come agente chimico, fisico, biologico potenzialmente dannoso per la salute. Inoltre, fissa altre definizioni come quella di unità produttiva: stabilimento o struttura finalizzata alla produzione di beni o servizi, dotata di autonomia finanziaria e tecnico-funzionale. Inoltre, la 626 nell’art 3 ha introdotto misure generali per la protezione della salute e per la sicurezza sul lavoro come: i. Mappatura e valutazione dei rischi secondo una certa importante da parte del DL e RSPP; ii. Eliminare i rischi o ridurli al minimo oppure ridurli alla fonte; iii. Agire in prevenzione e priorità a misure di protezione collettiva rispetto a quella individuale; iv. Limitare al minimo il numero dei lavoratori esposti a rischio; v. Eseguire un controllo sanitario sui lavoratori così di monitorare; vi. Prima di introdurre il lavoratore ad un determinato settore è importante RENDERE EDOTTI I LAVORATORI attraverso informazione e formazione. Due concetti fondamentali DI GRANDE INNOVAZIONE: Informazione: complesso delle attività dirette a fornire conoscenze utili alla identificazione, alla riduzione e alla gestione dei rischi nell’ambiente di lavoro, le misure di protezione e prevenzione, i pericoli correlati all’uso di sostanze e preparati, a chi riferirsi in caso di segnalazioni (si tratta di una forma passiva). Importante associare all’informazione è la Formazione: processo educativo attraverso il quale trasferire ai lavoratori ed agli altri soggetti del sistema di prevenzione e protezione conoscenze e procedure utili alla acquisizione di competenze per lo svolgimento in sicurezza dei rispettivi compiti in azienda. Essa deve avvenire nel momento dell’assunzione, del trasferimento o cambiamento di mansioni, all’introduzione di nuove attrezzature di lavoro o nuove tecnologie. Inoltre, deve essere periodicamente ripetuta in relazione all’evoluzione dei rischi. Per questo l’RLS ha una formazione particolare, ha bisogno di una maggiore formazione perché non è solo un semplice lavoratore ma ha un ruolo di rappresentanza. vii. È stata introdotta la figura del con ruolo di sorveglianza sanitaria (ELEMENTO INNOVATIVO) che si chiama tale poiché è sicuramente un medico dotato di una laurea in medicina ma competente sul tema sicurezza sul lavoro quindi in possesso di alcuni titoli: § specializzazione in medicina del lavoro o in medicina preventiva dei lavoratori e psicotecnica o in tossicologia industriale o in igiene industriale [...]; § docenza o libera docenza in medicina del lavoro o in medicina preventiva dei lavoratori e psicotecnica o in tossicologia industriale o in igiene industriale o in fisiologia ed igiene del lavoro. viii. Infine, vi è anche il rappresentante dei lavoratori per la sicurezza (ELEMENTO INNOVATIVO) cioè persona eletta o designata a rappresentare i lavoratori riguardo la sicurezza e la salute sul lavoro cioè raccogliere indicazioni dagli altri lavoratori che rappresenta ma che non è responsabile e riportarle alle altre figure citate prima. Ha una libertà di accesso ai locali aziendali, cioè può controllare se vi sono pericoli per i lavoratori o avere informazioni sui rischi, infortuni e malattie tipiche. OBBLIGHI: DATORE DI LAVORO (coadiuvato dal RSPP e LAVORATORI MEDICO COMPETENTE) 1. valutazione di tutti i rischi e adozione di misure Nel tempo si è riconosciuto che parte della per sicurezza e salute responsabilità è data anche ai lavoratori che: 2. Elaborazione di un documento valutazione 1. devono prendersi cura della propria sicurezza e rischi (ELEMENTO INNOVATIVO) che salute. contiene indicazione dei criteri impiegati per 2. Non devono essere passivi e non devono ad la valutazione, misure di prevenzione e di esempio trascurare la presenza di un guasto protezione necessari, eventuali misure per solo perché non è compito loro aggiustarlo ma garantire il miglioramento. Viene fatto devono riportarlo segnalarlo agli organi dall’RSPP e dal MEDICO COMPETENTE ma poi preposti. siglato dal DATORE DI LAVORO poiché Il vero 3. Osservare le disposizioni e istruzioni da parte responsabile della sicurezza è il datore di lavoro del datore di lavoro e non l’RSPP poiché lui è responsabile del 4. Utilizzare correttamente macchinari servizio protezione e prevenzione. apparecchiature e dispositivi di sicurezza 3. designazione del RSPP (Responsabile del 5. Sottoporsi a controlli sanitari previsti Servizio Prevenzione e Protezione), degli addetti alla sicurezza e del medico competente Altro ELEMENTO INNOVATIVO riguarda il concetto di “LAVORARE IN SICUREZZA” perché sono possibili due livelli. Un primo livello che riguarda la parte tecnica di “progettare in sicurezza” cioè seguire regole normative indicazioni atte a ridurre la probabilità che si verifiche un rischio riguardo l’edificio in cui si lavora, le macchine utilizzate, la struttura generale degli impianti. Ovviamente un secondo livello riguarda “progettare la sicurezza” cioè è importante che le persone siamo organizzate, gestite, monitorate e sorvegliate in modo corretto, che siano organizzati i mezzi, le procedure e così via. 5. D.Lgs. 242/96: Anch’essa ha avuto un aggiornamento con il D.Lgs. 242/96 e proprio sulla base di queste due norme si è costruito ed ancora oggi è valida la struttura aziendale nel rispetto della sicurezza sui luoghi di lavoro. 6. DPR 459/96 DIRETTIVA MACCHINE: DPR 459/96 nata come recepimento di una direttiva europea ed è stata la prima direttiva macchine recepita in Italia che ha imposto delle regole ben precise sulla messa in commercio di macchine nella comunità europea. Si ha un recepimento molto frequente di normative europee, quindi lo stato italiano può recepire in modo leggermente diverso una normativa rispetto ad un altro stato ma la parte fondamentale di essa deve rimanere immutata, questo perché bisogna garantire normative che permettono lo scambio di macchine. La direttiva macchine serve per avere macchine sul territorio europeo che siano in linea con quanto definito. CAMPO DI APPLICAZIONE: decisamente molto vasto là dove venga specificato o ci si riferisce a macchine e componenti sia già immessi sul mercato (prima messa a disposizione sul mercato dell’UE) sia a quelli messi in servizio (prima utilizzazione sul territorio dell’UE) dopo il decreto. Tale obbligo è tenuto ad essere rispettato da chiunque costruisce, rivende e utilizza macchine su suolo europeo. Un prodotto per il suolo europeo deve rispettare i RES (Requisiti Essenziali per la Sicurezza) che sono specifici per tipologia di prodotto. Per stabilire se una macchina risponda ai RES bisogna rifarsi alle norme tecniche EN che evidenziano quali siano i requisiti di sicurezza per quella macchina e il loro rispetto dà presunzione di assolvimento ai res ed è possibile certificare la macchina come sicura ai sensi della direttiva macchina. Esistono dei casi in cui non si riescono a trovare norme tecniche e bisogna trovare soluzione alternative (RACCOLTE ISPESL) cioè cercare altre linee guida specificando che la macchina sia sicura poiché risponde a diversi punti di diverse norme presenti a livello europeo. Una volta seguite le norme tecniche o ISO TC (si tratta sempre di norme tecniche su temi specifici. La differenza con le EN è il campo di emanazione. Queste vengono fatte dal comitato europeo di normazione che valgono a livello europeo, mentre le ISO TC valgono a livello mondiale) viene messa una marcatura CE sulla macchina e viene fatta una DICHIARAZIONE DI CONFORMITÀ. Sulla base di ciò bisogna fidarsi che la macchina sia sicura, ma i calcoli vengono eseguiti su un DOCUMENTO RISERVATO (che è un documento tecnico, che non viene consegnato al cliente, ma a lui viene rilasciato solo un manuale uso e manutenzione con la dichiarazione di conformità) che l’azienda mantiene a livello aziendale (quindi presso il produttore della macchina) e può darlo solo se lo chiede un’autorità giudiziaria o un organo competente. Non viene rilasciato poiché contiene aspetti di catetere intellettuale in cui spiega com’è costruita la macchina. Le macchine vengono classificate in due gruppi: i. più pericolose e sono soggette all’intervento di un organismo notificato e il nome di tale organo deve comparire sulla macchina insieme alla marcatura CE. ii. meno pericolose caratterizzate da un fascicolo tecnico in cui il costruttore dichiara come ha soddisfatto ai RES. Il concetto complessivo è quello di una direttiva armonizzata tra i vari paesi in cui ⁃ i prodotti che rispondono ai RES possono essere messi sul mercato e circolare in Europa, ⁃ inoltre, gli enti di normazione (CEN, CENELEC) devono farsi carico di elaborare le specifiche tecniche per fabbricare i prodotti rispondenti ai RES. ⁃ Le specifiche tecniche hanno carattere di norma volontaria, cioè non si è obbligati a seguire le EN. A livello mondiale, europeo e italiano abbiamo diversi enti che trattano l’aspetto normativo. L’Italia aveva UNI (per la parta generale) e CEI (per la parte elettrotecnica, Centro Elettrotecnico Italiano) e questa ha prodotto norme tecniche per rispondere ai RES, ora entrambe quando emanano norme hanno di solito il compito di tradurre in italiano una norma europea. Le norme EN prodotte a livello europeo da CEN E CENELEC vengono fatte appositamente in lingua inglese e poi vengono mandate ai vari enti nazionali che si occupano di tradurle. La traduzione non è immediata, dunque i produttori si basano direttamente sulle EN EUROPEE. Quindi, lo SCOPO è quello di mantenere e migliorare il livello di sicurezza nell’ambito macchine e impianti industriali. I CONTENUTI PRINCIPALI riguardano la responsabilità del produttore (colui che fabbrica un prodotto finito o chiunque si presenti come tale) in merito al danno causato dal difetto (cioè non offre la sicurezza) di un suo prodotto. Altri contenuti sono la certificazione e marchio CE, progettazione in sicurezza e di sicurezza, protezione individuale e manuali e istruzioni di uso. 7. Direttive CEE 8. Direttiva Macchine 2006/42/CE: Questa ha sostituito la precedente direttiva macchina che è attualmente in vigore, ed ha abrogato la precedente. Gli stati membri hanno avuto alcuni anni per adattarsi alle nuove disposizioni entrate in vigore dal 2010. Tale direttiva non ha stravolto i concetti della 459/96 ha solo chiarito una serie di punti che sono stati mal interpretati nel tempo. Ha introdotto il concetto di “quasi-macchina” che è un insieme di componenti che costituiscono quasi una macchina poiché da soli non sono in grado di garantire un’applicazione ben determinata. Esse sono destinate ad essere incorporate nelle macchine o in altre quasi macchine. Il fabbricante delle quasi macchine deve accompagnarle da una DICHIARAZIONE D’INCORPORAZIONE che deve contenere il preciso elenco dei RES così da sottolineare che sono state rispettate norme ben precise e dalle ISTRUZIONI PER L’ASSEMBLAGGIO per installarlo correttamente. Dunque, la nuova direttiva prevede solo 2 tipi di dichiarazione: i. Dichiarazione CE di conformità (se si tratta di una macchina); ii. Dichiarazione d’incorporazione per le quasi-macchine (se si tratta di una quasi macchina). Inoltre, ciò che varia è l’esposizione della marcatura CE che dev’essere apposta nelle immediate vicinanze del nome del fabbricante e nel caso anche dal numero di identificazione dell’organismo notificato usando la stessa tecnica. 9. D.Lgs. 81/08 “TESTO UNICO SULLA SALUTE E SICUREZZA SUL LAVORO”: Alla luce della complessità che si era generata in Italia dal dopoguerra con una serie di norme tecniche e specifiche, si è deciso di semplificare tutte le normative di maggiore interesse accorpandole all’interno di un unico testo di riferimento per ogni azienda, in modo da avere un’unica fonte normativa da cui trarre spunto che rimandi poi ad eventuali approfondimenti. Il testo unico, infatti, non si identifica come una nuova norma ma come una norma che raccoglie in sè norme esistenti che sono state poi abrogate con questo Testo unico. Ha un CAMPO DI APPLICAZIONE a tutto quello che è il mondo del lavoro italiano, quindi, anche l’inclusione di lavoratori autonomi o temporanei che lavorano con appalti, da qui l’obbligo della redazione del DUVRI -documento unico di valutazione dei rischi per le interferenze- per valutare le interferenze che possono esserci tra un lavoro occasionale e quello continuativo. Si tratta di un documento a firma congiunta in cui vengono chiariti i costi relativi alla sicurezza, pena nullità del contratto. Il RLS deve poter accedere al DUVRI. Tenendo conto dei cambiamenti nel mondo del lavoro i PRINCIPALI CAMBIAMENTI sono stati: i. Una tutela estesa ad ogni tipo di collaboratore; ii. È stato introdotto il concetto di salute come stato di completo benessere fisico, materiale e sociale; iii. Rafforzamento delle rappresentanze dei lavoratori; iv. Revisione e inasprimento delle sanzioni; v. Semplificati obblighi formali. È stato introdotto un coordinamento delle attività e delle politiche in tale materia su tutto il territorio nazionale coinvolgendo diverse parti sociali. Gli art. 15-17-25-28-29 sono dedicati a misure generali di tutela e valutazione dei rischi in cui si conferma: i. l’importanza del datore di lavoro con l’RSPP, il medico competente e l’RLP che si occupino della redazione del DVR (documento valutazione rischi) in cui tra i rischi viene inserito quello da stress da lavoro. ii. l’importanza di individuare procedure per l’attuazione delle misure da adottare e mansioni a rischio specifico che richiedono competenze e addestramento particolare e l’esplicitazione dei nominativi di RSPP, RLS e Medico Competente. iii. Il medico competente ha l’obbligo di custodire la cartella sanitaria e di rischio. iv. L’obbligo di eleggere un Rappresentante dei Lavoratori per la Sicurezza (RLS), o in alternativa un Rappresentante dei Lavoratori per la Sicurezza Territoriale (RLST). v. Requisiti professionali per il Responsabile del Servizio di Prevenzione e Protezione (RSPP): Frequenza a specifici corsi di formazione in materia di prevenzione e protezione rischi, anche di natura ergonomica e psicosociale, di organizzazione e gestione delle attività tecnico- amministrative e di tecniche di comunicazione in azienda e di relazioni sindacali. 10. D.Lgs 106/09 Disposizioni integrative e correttive del decreto 81/08: Quest’ultima fatta come integrazione della precedente riguardo il testo unico. Per quanto concerne il CAMPO DI APPLICAZIONE, oltre alle imprese di tutti i settori, vengono ricompresi anche i volontari della Croce Rossa, le forze armate e di polizia ed i vigili del fuoco. Le principali novità riguardano: i. Snellimento di alcune procedure burocratiche per la valutazione della sicurezza nei luoghi di lavoro; ii. Maggior spazio alla prevenzione; iii. Rivisitazione delle sanzioni. Viene introdotto il principio per il quale la sottoscrizione del Documento di Valutazione dei Rischi (DVR) da parte del datore di lavoro del responsabile del servizio di prevenzione e protezione, del rappresentante dei lavoratori per la sicurezza e del medico competente, è sufficiente per conferire al documento tutti gli effetti di legge. Gli obblighi dei preposti sono trasversali rispetto agli obblighi dei datori di lavoro e dei dirigenti, poiché si esplicano sempre, a fronte di qualunque tipo di rischio, nelle attività di: i. Vigilanza sul comportamento dei lavoratori; ii. Segnalazione delle non conformità ai datori di lavoro o dirigenti; - iii. Frequenza di appositi corsi di formazione. Analoghe considerazioni possono essere fatte con riferimento agli obblighi dei lavoratori riguardo: i. Osservanza delle disposizioni di legge e delle disposizioni aziendali di sicurezza; ii. Utilizzo corretto delle attrezzature di lavoro e dei Dispositivi di Protezione Individuali (D.P.I); iii. Segnalazione immediata ai superiori di eventuali situazioni di pericolo; iv. Evitare operazioni o manovre che non rientrano nella loro competenza; v. Partecipazione ai programmi aziendali di formazione ed addestramento; vi. Sottoposizione ai controlli sanitari. FONDAMENTI TEORICI DELLA SICUREZZA DEGLI IMPIANTI INDUSTRIALI Indispensabile per il datore di lavoro, l’RSPP e il medico competente, è una valutazione del rischio che si deve concretizzare in quello che è l’elaborazione del DVR cioè il documento valutazione dei rischi. Anche se la normativa italiana non riporta un metodo preciso di valutazione, ma suggerisce alcune metodologie, proprio per questo in ambito industriale è possibile trovare diverse metodologie di analisi del rischio. Una semplice analisi del rischio può essere identificata tramite la CIFRA DI RISCHIO ‘R’ cioè il prodotto tra la frequenza prevista per un evento F (la probabilità di accadimento di un determinato evento di rischio) e la magnitudo delle conseguenze M (ovvero se accade l’evento quale può essere la conseguenza dell’accadimento). Le FASI DI ANALISI DEL RISCHIO sono: 1. Una pre-analisi riguardo la determinazione degli eventi potenzialmente pericolosi. 2. Si ricorre ad un’analisi dell’affidabilità del sistema e conseguente probabilità di verificarsi dell’evento di danno. Bisogna fare una valutazione più specifica di tutti i componenti presenti o di tutte le attrezzature per capire tra tutte le possibili rotture, non solo in ambito meccanico, ma anche errori umani, se ne esistono alcune che possono avere ripercussione in ambito sicurezza. 3. valutazione delle conseguenze dell’evento di danno. Calcolando numericamente la cifra di rischio si ha una CURVA ISORISCHIO. È un ramo di iperbole equilatera e rappresenta graficamente la relazione che determina la cifra di rischio, vale a dire il prodotto costante fra frequenza prevista dell’evento e la magnitudo delle sue conseguenze: 𝑅 = 𝐹×𝑀. Per diminuire il rischio, ovvero per saltare da una curva ad un’altra a rischio più accettabile, si può agire in due modi: i. tramite la prevenzione, riducendo la frequenza; ii. tramite la protezione, riducendo la magnitudo. In alcuni casi una riduzione di prevenzione o protezione non sempre è facile, quindi, spesso si ricorre ad un mix di soluzioni di riduzione da rischio elevato a rischio accettabile, agendo a livello di combinazione tra protezione e prevenzione abbassando sia la frequenza che la magnitudo. Questo approccio è universale e può essere applicato in qualsiasi contesto lavorativo ma i limiti riguardano quello di avere situazioni opposte, cioè situazioni in cui si hanno valutazioni in cui la frequenza è molto elevata e la magnitudo bassa o viceversa. Per EVENTI DI RISCHIO s’intende il possibile risultato di un comportamento soggettivo (ATTO INCAUTO) in una condizione oggettiva di non sicurezza (SITUAZIONE PERICOLOSA). Vi è una classificazione generica di eventi di rischio, al di là dell’estensione del danno che può essere DANNOSO e NON DANNOSO vi è la manifestazione temporanea che può essere IMMEDIATA, PROGRESSIVA e IMPROVVISA A DISTANZA DI TEMPO. 1. a1A - INFORTUNIO le cui caratteristiche sono: la vittima ha contribuito all’infortunio stesso producendo un atto incauto. Può essere causato da un singolo atto ed ha minimi riflessi sull’ambiente. Le misure riguardano azioni di prevenzione, addestramento, norme comportamentali 2. a1B - ESPOSIZIONE A RADIAZIONI le cui caratteristiche sono: avere una responsabilità di ambiente e organizzazione, l’entità del danno dipende dal modo di operare del lavoratore, inoltre diffusa coscienza del rischio. Le misure sono istruzioni, addestramento e miglioramento di igiene ambientale 3. a1C - MALATTIE PROFESSIONALI le cui caratteristiche sono simili a quelli precedenti così anche per le misure. 4. a2A - INCENDIO, ESPLOSIONE, CEDIMENTO STRUTTURALE le cui caratteristiche riguardano il fatto che le vittime non sono responsabili dell’evento poiché generato da una serie di cause, mancato intervento delle misure di protezione e possibili conseguenze all’ambiente. Le misure riguardano provvedimenti su legislazione e regolamenti e disponibilità di risorse da applicare per protezione e prevenzione. 5. a2B, a2C - EMISSIONI DI SOSTANZE TOSSICHE le cui caratteristiche e le misure sono come le precedenti 6. a3A - FRANE, TERREMOTI E INCIDENTI RILEVANTI le cui caratteristiche sono: imprevedibilità, errori di progetto e gestione, estraneità di gran parte delle vittime. Le misure riguardano una progettazione più scrupolosa. 7. a3B, a3C - EVENTI INQUINANTI le cui caratteristiche riguardano alterazioni profonde dell’ambiente indotti dall’attività umana o subirli da aziende limitrofe e le misure riguardano la formazione/informazione sul rischio e il rispetto della legislazione, e tecnologie avanzate e più innovative. Altra classificazione riguarda eventi di rischio per impianti produttivi poiché l’attività produttiva può avere una presenza di rischi dettata da EVENTI ESTERNI o da EVENTI INTERNI che si producono. L’insieme di eventi esterni ed interni dà luogo a valutazione di un SISTEMA DI SICUREZZA che può essere interna (su cui si può agire in maniera preventiva cercando di ridurre eventi di rischio prodotti dall’azienda stessa) o esterna (su cui si può agire in maniera protettiva, riducendo eventuali danni). Inoltre, altra classificazione riguarda eventi di rischio per impianti produttivi è dettata da FATTORI OPERATIVI (comportamento umano, quindi non averlo formato correttamente oppure nel tempo ha perso conoscenza di procedure più complicate, non corretta gestione di sistemi automatici che possono presentare delle imperfezioni o dei guasti, oppure non perfetta esecuzione di attività manuali) o FATTORI TECNOLOGICI (cioè utilizzare alcune tecnologie per svolgere delle funzioni). A livello tecnologico è importante che se le macchine nel tempo perdono la propria precisione di dosaggio e vanno ad alterare il loro funzionamento è fondamentale monitorare i parametri di processo cambiandoli o valutando una sostituzione. In generale gli EFFETTI prodotti sui lavoratori sono traumi, contatto con sostanze nocive, intossicazioni, incendi, malattie professionali. MAPPATURA DEI RISCHI A livello aziendale tutto ha inizio con una MAPPATURA DEI RISCHI, ovvero una valutazione di tutte le attività e dei rischi associati ad esse. Il PROCEDIMENTO di analisi è quello di evidenziare per ogni attività tutti quelli che possono essere fattori di pericolo, le cause di pericolo e quelle che sono le condizioni scatenanti. Sulla base di questo si va a fare una valutazione riguardo la perdita di funzionalità e il livello di pericolosità legato a quel determinato evento di rischio e a seguito di ciò si fa una valutazione non solo circostanziato alla presenza umana sul posto di lavoro ma anche legato all’ambiente in cui si svolge l’attività aziendale. Sulla base di questa valutazione preliminare circa la pericolosità si va a proporre nel DVR una serie di interventi, delle soluzioni migliorative che riducono la cifra di rischio connessa all’evento. Questi interventi possono avvenire a: 1. livello 1: A livello di eliminazione del fattore di rischio e in questo caso il tutto viene affrontato eliminando direttamente il fattore di pericolo. 2. livello 2: Agendo sulla causa di pericolo o sulla condizione scatenante riducendone la probabilità di accadimento. Nei primi due livelli si agisce a livello di prevenzione. 3. livello 3: limitando i danni nel caso in cui si va a proteggere persone e ambiente e in tal caso si agisce a livello di protezione. CURVA COSTI EFFICACIA DELLA PROGETTAZIONE Si ricava sperimentalmente ed è la rappresentazione grafica dell’efficacia (in ordinata) degli interventi progettuali in funzione dei costi (in ascissa) sostenuti per effettuarli. Si può progettare in sicurezza (fase I), cioè seguire norme, regole, indicazioni per ridurre la probabilità che si verifichi un evento di rischio e progettare la sicurezza (fase II) cioè organizzare uomini, mezzi e procedure affinché le conseguenze degli eventi siano meno dannose. (Graficamente si parte dall’origine e si tende ad andare ad un asintoto orizzontale E1. Inizialmente si hanno una serie di investimenti che portano ad un determinato vantaggio in termini di efficacia, poi attuando una serie di interventi “in sicurezza” ovviamente si perde efficacia e aumentano di più i costi. Si parte dal punto finale della fase uno e si cerca di arrivare verso un asintoto verticale. L’andamento è simile al precedente, inizialmente si attuano una serie di investimenti legati a progettare “la sicurezza” che portano a dei vantaggi per poi arrivare ad una diminuzione di efficacia che vanno a definire un valore E2.) Fondamentale è il punto di flesso che sancisce la fine della curva della fase I e l’inizio della curva della fase II e da alcune valutazioni si è visto come l’efficacia delle operazioni di sicurezza dipendono dalla posizione del punto F cioè da quanto è buona la base in sicurezza che si è creata, poiché si ritiene che partire con una buona organizzazione di uomini su una base strutturale carente non porta gli stessi benefici rispetto ad avere una base strutturale già in sicurezza. Questo, graficamente, lo si vede nel caso in cui si prende una curva costificata che invece di partire dal punto F per la seconda fase di sicurezza parta da un punto F’ con costi inferiori per quel che riguarda la sicurezza in termini progettuali da cui non sarà possibile arrivare agli stessi livelli di efficacia raggiunta rispetto al caso precedente. La scelta del punto di flesso F dipende dal livello di efficacia che si vuole raggiungere: in base alla scelta di F si può raggiungere un’efficacia maggiore a parità di costi sostenuti. Da un punto di vista analitico la curva ha equazione: 𝑦 = arctg (𝑎𝑥) + arctg (𝑏𝑥 − 𝑐𝐶𝑓) + 𝑑𝐸𝑓, dove a, b sono i coefficienti angolari dei tratti di curva, c e d sono i coefficienti correttivi e Cf ed Ef sono le coordinate del punto di flesso F; pertanto, la curva costi- efficacia è la somma di due curve. SICUREZZA DEI FABBRICATI E DEGLI AMBIENTI DI LAVORO A livello della progettazione della sicurezza si va a valutare quello che è il sistema industriale, produttivo al cui interno si ha sempre un determinato input (le materi prime di lavorazione) e un determinato valore di output (di prodotti finiti che si va a produrre). All’interno del sistema si hanno tanti sottosistemi e infatti il ciclo produttivo si compone di una serie di attività manifatturiere in linea, in cui il prodotto subisce più trasformazioni. Dunque, una volta che viene fatta la mappatura delle attività di un sistema di sicurezza aziendale si passa ad una valutazione di due aspetti: 1. SECURITY: cioè legata alla sicurezza dei beni aziendali tramite l’utilizzo di dispositivi aziendali, regolamentazione degli accessi, per evitare furti, effrazioni, sabotaggio. 2. SAFETY: cioè legata alla sicurezza delle persone che lavorano per l’azienda. Tutto ciò che circonda il lavoratore e agisce su di lui, quindi l’igiene del lavoro, l’ambiente di lavoro (fattori ambientali di rischio interni ed esterni), la parte legata alla sicurezza del fabbricato industriale (edifici destinati ad accogliere le attività produttive e di servizio o supporto). Ciò che può generare un evento di rischio all’interno e all’esterno che possono danneggiare il fabbricato di lavoro sono diversi come: ⁃ Sostanze e materie prime utilizzate nei cicli tecnologici; ⁃ Inquinanti; ⁃ Condizioni fisiche e ambientali; ⁃ Fabbricati industriali: fondazioni, strutture fuori terra, elementi di divisione, tamponature, coperture, pavimentazioni idonee alle attività che si svolgono all’interno CARATTERISTICHE DEI FABBRICATI INDUSTRIALI IN BASE ALLE ATTIVITA’ DI LAVORAZIONI § Livello luminoso § Temperatura e grado igrometrico (umidità relativa) § Livello di rumore § Inquinanti (polveri, fumi) Ovviamente un fabbricato industriale dev’essere in linea con alcune NORMATIVE DI RIFERIMENTO: DPR 547/55, DPR 303/56. Diversi punti di queste norme evidenziano diversi spunti per la progettazione di spazi idonei per lo svolgimento di attività lavorative: D.Lgs 626/94, D.Lgs 242/96. Hanno definito il modo in cui organizzare le persone all’interno degli spazi predefiniti: D.Lgs 493/96 segnaletica di sicurezza. Inoltre, per assecondare le attività e identificare gli spazi idonei per alcune attività rispetto ad altre sono norme che riguardano la segnaletica di sicurezza FASI DI PROGETTAZIONE DEI FABBRICATI INDUSTRIALI La progettazione degli edifici industriali consta di 5 fasi: 1. POSIZIONE GEOGRAFICA, nella quale si stabiliscono UBICAZIONE cioè la definizione di una macro-area generale, LOCALIZZAZIONE cioè la definizione di un’area più specifica e SEDIME cioè la scelta del terreno dello stabile in cui bisogna tenere conto di diverse valutazioni come quella della salubrità dell’industria per rientrare nella I categoria (cioè collocare lo stabilimento lontano dalle zone abitate perché magari produttrice di rifiuti tossici o emissioni inquinanti) oppure nella II categoria (cioè collocare lo stabilimento nei pressi dei centri abitati poiché presentano emissioni che rientrano nei limiti imposti dalle normative vigenti). Inoltre, è importante anche di informazioni relative al profilo climatico: temperatura, piogge, fulminazioni, venti principali (informazione importante per eventuali incendi), illuminazione, la valutazione dell’omogeneità del terreno, cioè il fatto di avere un terreno che sia in tutte le sue parti dotato delle stesse caratteristiche in termini ad esempio di portanza o drenabilità, per valutare l’eventualità di avere o avviare fondazioni di tipo più o meno complesso per stabilizzare la struttura. Inoltre, la valutazione sismica, cioè del livello di sismicità della zona, poiché il fabbricato che si dovrà costruire dovrà rispondere a determinati requisiti previsti dalle normative. Altra valutazione riguarda la compresenza in zone limitrofe di attività analoghe o pericolose. 2. DISPOSIZIONE E DIMENSIONI DEL FABBRICATO. È necessario un’analisi sull’estensione per possibili e future espansioni e di dimensioni che riguardano gli edifici. La scelta ottimale dal punto di vista della sicurezza è una forma rettangolare con asse maggiore perpendicolare ai venti dominanti e angoli rivolti verso i punti cardinali, con locali pericolosi opposti ai venti dominanti. 3. TIPOLOGIE EDILIZIE, nella quale si sceglie se si tratti di una fabbrica compatta (unico edificio) o estesa (più edifici), ovviamente vi sono benefici o meno per entrambe le tipologie. Dunque, se si hanno operazioni o stoccaggio di materiali pericolosi a rischio esplosione o incendio è preferibile una struttura estesa con edifici dedicati per quel tipo di attività, mentre per le attività produttive non a rischio è preferibile edifici compatti così da avere una migliore movimentazione. Altra scelta è tra edifici intensivi cioè multipiano o estensivi cioè ad un solo piano. Ovviamente tali scelte sono dettate dal tipo di attività che poi si andrà a svolgere, dunque per le attività amministrative o da ufficio si cerca di privilegiare edifici intensivi, mentre per attività produttive si privilegia edifici estensivi anche per una migliore illuminazione che può provenire dall’alto. 4. MATERIALI DA COSTRUZIONE, le cui caratteristiche e tipologie vanno scelte in base alle esigenze. Esse sono importanti poiché definiscono diverse caratteristiche del fabbricato dal punto di vista della sicurezza. Definiscono la resistenza meccanica del fabbricato in quanto materiali differenti tra loro possono garantire un diverso comportamento in condizioni di carico. In alcuni casi, alcuni materiali consentono delle navate, cioè le distanze tra pilastri importanti, poiché questi grandi spazi consentono l’inserimento di grandi impianti produttivi. Altro aspetto è legato al costo del materiale. Importante è l’isolamento acustico e termico, poiché il fatto di avere impianti che producono un certo rumore, la quale struttura riesce ad attenuare, può aiutare nella gestione della produzione al fine di non arrivare a sommare un valore di rumorosità molto elevato. Infine, l’aspetto illuminazione, soprattutto quella naturale è molto importante in un luogo di lavoro sia per la sicurezza che per un determinato clima lavorativo. Le tipologie utilizzare possono essere: i. Calcestruzzo armato e precompresso: si tratta di un materiale prodotto nel luogo in cui viene realizzata la struttura perciò definito anche “in opera”. Tuttavia, le tecnologie disponibili che consentono questi prefabbricati permettono di avere una maggiore compattazione del materiale e quindi un aspetto a livello di navata maggiore rispetto al calcestruzzo armato. Proprio per questo che i fabbricati sono più utilizzati perché permettono spazi più ampi e anche più leggeri e a livello di costi sono più convenienti poiché non ci sono cantieri in opera ma un montaggio che avviene nelle fasi successive alle fondazioni. ii. Profili in acciaio: ormai non più utilizzate. Si prevede l’utilizzo di materiali metallici che di conseguenza si connotano per forte conducibilità termica ed elettrica che, se da una parte garantiscono una grande navata, dall’altra l’aspetto legato alla conduzione ha fatto sì che queste strutture anche molto costose venissero abbandonate per utilizzare strutture diverse. iii. Laterizio armato: cioè la costruzione in mattone è poco utilizzata per edifici industriali, molto più comune per edifici civili perché il laterizio non permette di avere grandi navate quindi si è vincolato da aree molto più ridotte. Hanno un buon isolamento acustico e termico quindi ottimo per strutture amministrative. Ottima resistenza al fuoco quindi ottime per strutture intensive anche se presentano il vincolo dell’illuminazione che sarà maggiormente artificiale. iv. Legno lamellare tipico di strutture ricreative (tipo sportive) e civili molto vantaggiose sia per luminosità, leggerezza della copertura, buon isolamento acustico e termico con ampie navate disponibili hanno reso questa tipologia di materiale ottima anche per soluzioni industriali, dove inizialmente si è avuto qualche dubbio per eventuali rischi incendi poiché si tratta di base di un materiale combustibile ma con ottime coperture si ha un’ottima protezione. 5. COMPONENTI STRUTTURALI, che comprendono le fondazioni che possono essere di tipo superficiale o profonde, ciò dipende dal profilo geologico del terreno, poiché se pensiamo a strutture realizzate in terreni collinari o di montagna, la probabilità di avere un cedimento del terreno può essere elevata quindi importante la scelta del tipo di fondazione. Nel caso di fondazioni superficiali esistono tre differenze. Se si ha un terreno coerente cioè una caratteristica a livello di portanza omogenea su tutta la superficie, può essere sufficiente una costruzione di fondazione a plinti (1) (I plinti sono strutture che vanno a creare la fondazione del pilastro portante solamente nell’intorno della base di appoggio del pilastro, cioè ogni singolo pilastro è appoggiato su un plinto ed è molto importante che il terreno abbia coerenza). Ciò ha anche un costo più basso rispetto a fondazioni più estese come per quella a cordoli (2), che sono un insieme di plinti connessi tra loro con lo scopo di formare una striscia. Si preferisce scegliere questo tipo di struttura quando si ritiene che ci sia una differenza di portanza tra il terreno e quindi si cerca di omogenizzare con una fondazione superficiale a cordolo. Ultima tipologia è quella della platea (3) cioè l’insieme complessivo di materiale di fondazione che ricopre tutta la superficie. Ovviamente vi sono casi particolari regolati da normative nel caso di fondazioni in zona sismica e fondazioni in presenza di vibrazioni. Inoltre, si parla di coperture e pareti. A livello di pareti si parla di tamponature cioè elementi che collegano tra loro due strutture portanti. È importante tenere in considerazione in questi casi aspetti come: i. Illuminazione: fondamentale per il regolare svolgimento delle funzioni lavorative. È importante che non ci sia solo un’illuminazione laterale ma anche zenitale. Ovviamente un buon livello di luminosità e illuminamento è funzione delle dimensioni e caratteristiche del fabbricato, del tipo di lavoro da svolgere (poiché hanno un numero di lux o lumen richiesti elevati perciò necessario avere sia un’illuminazione artificiale che direzionato verso la postazione di lavoro, per quanto è già presente un’illuminazione naturale) e della distanza lavoratore-piano di lavoro. Una scarsa illuminazione ricade poi sull’eventuale difettosità del prodotto che si realizza e per l’uomo potrebbe esserci un affaticamento mentale. Ovviamente ci sono aspetti tecnici per regolare la luminosità attraverso rapporti tra illuminamento interno ed esterno considerando i vari periodi dell’anno. Dal punto di vista delle coperture bisogna evitare il fenomeno dell’abbagliamento cioè il fenomeno dell’ingresso di luce che colpisce il lavoratore e può distrarlo dalla sua attività. La luce sappiamo può provenire dall’alto (solitamente aperture dal soffitto e per edifici mono-piano. Vi sono diverse tipologie di coperture come quelle a shed o a denti di sega fatti da una zona in cui vi è la copertura vetrata che è disposta lateralmente così che i raggi solari entrano laterali e non dall’alto per evitare abbagliamento. Altra tipologia è quella a pozzo o a lucernari in cui l’ingresso della luce avviene sempre dalle pareti laterali) oppure lateralmente (solitamente da finestre e soprattutto per edifici pluripiano. Può essere monolaterale, bilaterale, multilaterale). ii. Protezione dal rumore: attraverso pannelli fonoassorbenti, materiale isolante cioè strutture che vanno a coprire il fabbricato e proteggono gli operatori a livello di protezione collettiva invece di dotarsi di protezioni individuali. iii. Pavimentazione: possono essere degli elementi importanti per la riduzione di rischi a livello di infortuni, in quanto devono garantire resistenza ad urti e vibrazioni, ridotto costo in quanto la pavimentazione occupa una grande area, ottimo isolamento termico e acustico e deve essere impermeabile, antiscivolo, ma anche di limitata polverosità. iv. Scale, ascensori e montacarichi: da isolare rispetto al resto dell’edificio con idonee porte tagliafuoco, costruiti con materiali incombustibili e dimensionati per sopportare momentanei sovraccarichi. SEGNALETICA DI SICUREZZA La segnaletica di sicurezza è un sistema di segni il cui contenuto percettivo rinvia ad un messaggio avente lo scopo di realizzare una maggiore condizione di sicurezza per garantire la salute e l’integrità dei lavoratori e la salvaguardia dei beni aziendali. Lo scopo è di attrarre l’attenzione su oggetti o situazioni che possono determinare pericoli e trasmettere messaggi che richiedono una risposta immediata. A livello normativo la più importante è il D.Lgs. 493/96 che va ad identificare la diversa tipologia di segnali da mettere in atto per segnalare situazioni a livello lavorativo. Inoltre, fornisce definizioni precise e suggerimenti anche su come impostare la segnaletica a livello di posizionamento per gli ambienti industriali. Vengono diversificate le diverse tipologie di segnali in base al messaggio che si vuole dare: divietò, avvertimento, prescrizione, salvataggio/soccorso, informazione. Il D.Lgs. 493/96 fornisce una serie di indicazioni riportate in allegati che valgono per le diverse tipologie di applicazione: (Allegato I: Prescrizioni generali per la segnaletica di sicurezza; Allegato II: Prescrizioni generali per i cartelli segnaletici; Allegato III: Prescrizioni per la segnaletica dei contenitori e delle tubazioni; Allegato IV: Prescrizioni per la segnaletica destinata ad identificare e ad indicare l'ubicazione delle attrezzature antincendio; Allegato V: Prescrizioni per la segnalazione di ostacoli di punti di pericolo e per la segnalazione delle vie di circolazione; Allegato VI: Prescrizioni per i segnali luminosi; Allegato VII: Prescrizioni per i segnali acustici; Allegato VIII: Prescrizioni per la comunicazione verbale; Allegato IX: Prescrizioni per i segnali gestuali. CARATTERISTICHE DELLA SEGNALETICA DI SICUREZZA 1. COMUNICAZIONE che può essere: i. Strumentale (finalizzata ad una determinata azione del lavoratore); ii. Di regolazione (al fine di identificare il corretto posizionamento di alcuni indicatori per lavorare al meglio); iii. Informativa (di informazione su una particolare situazione). 2. SPECIFICI PER LA PROBLEMATICA DA SEGNALARE dunque non generica o abbinare più tipologie di messaggi 3. TENDENZA ALLA STANDARDIZZAZIONE cioè una segnaletica di sicurezza che sia uguale per tutti e non varia da un’azienda all’altra. Gli elementi di maggior COMPRENSIONE DEL SEGNALE (CARATTERISTICHE INTRINSECHE) sono: 1. FORMA e COLORE DEI CARTELLI SEGNALETICI da impiegare sono definiti in funzione del loro oggetto specifico (cartelli di divieto, di avvertimento, di prescrizione, di salvataggio e per le attrezzature antincendio). I pittogrammi, cioè le figure poste all’interno, sono esempi di immagini schematiche che devono essere semplici, con omissione di particolari difficili da comprendere. Possono differire leggermente dalle figure riportate e presentare anche maggiori particolari l’importante che il significato non sia reso equivoco dalle modifiche apportate. 2. POSIZIONE che dev’essere rappresentativa della zona in cui si vuole segnalare il problema. Il cartello va rimosso quando non sussiste più la situazione che ne giustificava la presenza. 3. FATTORI FISICI DELL’AMBIENTE, cioè il cartello dev’essere protetto dai fattori fisici dell’ambiente. I cartelli devono essere costituiti di materiale il più possibile resistente agli urti, alle intemperie ed alle aggressioni dei fattori ambientali. 4. COLLOCAZIONE cioè collocato in modo stabile, corretto così da poter essere visualizzato. I cartelli vanno sistemati tenendo conto di eventuali ostacoli, ad un'altezza e in una posizione appropriata rispetto all'angolo di visuale, all'ingresso alla zona interessata in caso di rischio generico, ovvero nelle immediate adiacenze di un rischio specifico o dell'oggetto che s'intende segnalare e in un posto bene illuminato e facilmente accessibile e visibile (In caso di cattiva illuminazione naturale sarà opportuno utilizzare colori fosforescenti, materiali riflettenti o illuminazione artificiale secondo il decreto legislativo 626/1994). I TIPI DI SEGNALI sono: 1. CARTELLI che possono essere di: ⁃ AVVERTIMENTO con una forma triangolare, scritta nera su fondo giallo e bordo nero ⁃ PRESCRIZIONE con una forma rotonda, scritta bianca su fondo azzurro ⁃ SALVATAGGIO con forma quadrata o rettangolare, scritta bianca su fondo verde ⁃ PER MATERIALI ANTICENDIO con forma quadrata o rettangolare, scritta bianca su fondo rosso ⁃ DIVIETO con forma rotonda, scritta o disegni neri su fondo bianco, barra inclinata a 45° da sinistra a destra con bordo e barra di colore rosso. I cartelli si connotano per la relazione distanza–superficie: 𝐴 > 𝑳𝟐 /2000 [m] con A = area del cartello e L = distanza in metri operatore-cartello. Ovviamente poi tale formula varia in base alla forma di cartello. Dal punto di vista del materiale vi è l’utilizzo di: i. Lastra PVC (1mm) per la sua resistenza in luoghi interni ed esterni in atmosfera normale o aggressiva, ma non in zone con elevate escursioni termiche. ii. Lamierato di Al (1mm) per la sua resistenza in zone ad elevate escursioni termiche. iii. Pellicola vinile per la sua resistenza in zone di atmosfera aggressiva. Dal punto di vista della disposizione nel luogo di lavoro, è importante evitare un numero eccessivo di cartelli nello stesso luogo poiché si crea una sovrapposizione di messaggi e quindi una difficile comprensione. Dunque, porre solo cartelli strettamente necessari, assicurare buona visibilità, eseguire adeguata manutenzione in modo che se sono rovinati o obsoleti possono essere sostituiti. 1. MANIFESTI: sono segnali usati per rendere più chiaro e comprensibile un messaggio trasmesso da un cartello. Hanno funzione di supporto, la cui efficacia dipende dalla significatività dell’immagine rappresentata, capacità di sintesi del testo, riferimento a situazioni reali, concetti positivi. A livello di colori troviamo il bianco (per concetti di divieto, atteggiamento pericoloso, in cui il comportamento da adottare sarà quello di fermarsi), giallo (per avvertimento che invita a fare attenzione e ad avere cautela), azzurro (per concetti di prescrizione in cui è necessario un comportamento specifico con determinati obblighi), verde (per salvataggio o soccorso, per indicare ad esempio porte o uscite di sicurezza) e rosso (per antincendio). 2. CONTRASSEGNI: per tubi, recipienti, cavi elettrici ecc. 3. PANNELLI: usati per i veicoli per trasporto stradale e ferroviario per identificare merci pericolose e hanno una forma rettangolare di colore arancione e dimensioni almeno 30x40 cm con 2 numeri identificativi di pericolo e sostanza trasportata. 4. ETICHETTE: usate per tubazioni e recipienti contenenti sostanze pericolose che deve contenere il nome della sostanza, la provenienza, simbolo di pericolo e indicazioni specifiche per il trattamento della sostanza. Rientrano nella segnaletica anche i SEGNALI GESTUALI (generali, verticali, orizzontali e di pericolo) e la COMUNICAZIONE VERBALE attraverso l’utilizzo di alcuni termini che hanno un determinato significato. Non dimentichiamo i SEGNALI ACUSTICI e i SEGNALI VISIVI. Per quanto riguarda le macchine, spesso vi è un pannello di controllo su cui ci sono determinate impostazioni ed eventuali allarmi preliminari prima della partenza. Una volta risolto e la macchina è in movimento, in casi di problemi o superamento di parametri di soglia è possibile l’arresto la cui segnalazione può essere visiva che avviene tramite l’accensione di una luce al di sopra del quadro (che può essere gialla a cui non corrisponde un allarme acustico poiché indica allerta o rossa con allarme acustico per attirare l’attenzione degli operatori). Dunque, il tema della segnaletica non è un tema da trascurare anche a livello di formazione dell’operatore poiché essa dev’essere fornita e rispettata. La PROGETTAZIONE DI UN PROGRAMMA DI SEGNALETICA avviene secondo le seguenti fasi: 1. CONTATTO: visionare lo spazio di intervento per sceglierne la modalità; 2. ABBINAMENTO DI INFORMAZIONI: esatta descrizione della struttura dello spazio segnaletico e delle relative esigenze; 3. ORGANIZZAZIONE: pianificazione dell’intervento in base alle conoscenze acquisite à individuazione zone critiche (= dove segnaletica è fondamentale); 4. REALIZZAZIONE: attuazione del programma delineato; 5. CONTROLLO: verifica dei risultati ottenuti manutenzione. RISCHIO INCENDIO L’INCENDIO è una combustione, cioè una reazione esotermica di ossido-riduzione che coinvolge una sostanza riducente/ossidata (combustibile) e una ossidante (comburente), caratterizzata da sviluppo di energia in forma di luce e calore, oltre ad altri prodotti (fumi e gas). Il comburente di norma può essere ossigeno presente nell’aria (circa 20% in volume), ma anche altri gas ad es. l’idrogeno può bruciare in ambiente di cloro. Le CONDIZIONI NECESSARIE affinché avvenga una combustione sono: i. Il contatto tra combustibile e comburente (in alcuni casi l’ossigeno è già presente a livello molecolare nel combustibile) ii. I reagenti necessari in determinate quantità Þ quindi le concentrazioni di combustibile/comburente comprese in un dato intervallo che portano ad intervalli di infiammabilità e definizioni di concentrazioni di infiammabilità. iii. L’energia di reagenti superiore ad un valore di soglia temperatura del sistema superiore ad un valore minimo, detto di accensione o di autoaccensione. La DIFFERENZA TRA TEMPERATURA DI ACCENSIONE E AUTOACCENSIONE è che esse sono legate alle diverse caratteristiche della sostanza. Per un gas, ad esempio, è la temperatura alla quale, in presenza delle altre condizioni, il combustibile inizia spontaneamente a bruciare senza necessità di ulteriore energia per l’innesco. Per un liquido, ad esempio, temperatura minima alla quale il combustibile produce vapori in quantità tale da incendiarsi in assenza di innesco. A seguito della combustione si avrà una fiamma che sarà funzione della temperatura, più la temperatura è elevata più il colore della fiamma sarà chiaro. A livello di PRODOTTI DELLA COMBUSTIONE si ha: i. Il calore cioè energia termica ed è la principale causa della propagazione della combustione ma che spesso non è la prima fonte di pericolo per incendio per i lavoratori. ii. I gas cioè prodotti della reazione chimica, in stato gassoso. Dipendono dal combustibile e dalla temperatura raggiunta in fase di combustione. Sono la prima e principale fonte di pericolo e di rischio di morte. Alcuni sempre presenti come l’anidride carbonica che maggiore del 5% rende l’aria irrespirabile. iii. I fumi cioè sospensione di particelle solide incombuste di combustibile o di prodotti della combustione; queste ultime sono presenti in particolare se la combustione avviene in carenza di comburente. Essi rendono molto difficile l’evacuazione poiché tendono a diminuire la visibilità se non in alcuni casi annullarla completamente; sono tossici perché si tratterebbe di inalare particelle solide e inoltre tendono al trasporto di notevoli quantità di calore. Si distinguono in fumi neri (composti da piccolissime particelle solide costituite da sostanze incombuste) e fumi bianchi (nebbie ed aerosol originati dalla condensazione del vapore acqueo, al di sotto dei 100°C). Altro aspetto è legato al calore di combustione, funzione delle quantità di calore prodotte dalla combustione e dalla tipologia di sostanza. Legato spesso al potere calorifico della sostanza stessa. Questo potere calorifico può essere identificato come superiore (o inferiore) a seconda che non consideri (o consideri) il calore necessario ad evaporare l’acqua contenuta nella sostanza. A seguito della combustione di una sostanza, si ha un processo determinato da una curva su cui si possono identificare le massime temperature raggiungibili che sono definite temperature di combustione e sono legate alla tipologia di sostanza che entra in combustione. Se si tratta di una combustione incontrollata, involontaria e in un ambiente non predisposto o non ideato per accoglierla si può parlare di incendio (differenza tra combustione e incendio). COMBUSTIBILI: 1. SOLIDI. I più comuni sono composti organici costituiti da cellulosa, gruppo alcoolici, aromatici, resine, sostanze minerali e acqua (es. legno). Queste sostanze hanno la necessità di avere in superficie a contatto con l’aria dei vapori in una concentrazione tali per cui risultano nel campo di infiammabilità e possono entrare in combustione tramite un innesco. Tali vapori riescono ad uscire dalla sostanza solida tramite sublimazione (mentre nei liquidi si parlerà di evaporazione). i. Temperatura di infiammabilità: t alla quale il combustibile è in grado di produrre vapori che formano a contatto con l’atmosfera, una miscela interna al campo di infiammabilità. ii. Temperatura di autoaccensione: temperatura alla quale il combustibile brucia senza innesco, autosostentamento della combustione. A livello normativo ci sono stati diversi decreti ministeriali che assegnano ai combustibili solidi una classe di reazione al fuoco con valore da 0 (incombustibili) a 5 (completa partecipazione all’incendio). 2. LIQUIDI. Non bruciano in questa forma perché la zona di contatto con l’aria è ridotta. La combustione avviene in forma gassosa, tramite evaporazione cioè grazie alla produzione di una quantità di vapori tali da costituire, con l’aria, una miscela interna al campo di infiammabilità (T di infiammabilità = T minima). I combustibili liquidi sono più pericolosi di quelli solidi, perché: la T infiammabilità è bassa; il limite inferiore del campo di infiammabilità è basso e spesso sono più densi dell’aria e hanno una tendenza all’accumulo. A livello normativo in base alla T di infiammabilità si sono distinte le diverse pericolosità dei combustibili in: i. Categoria A (molto infiammabili, che possono dare luogo a scoppio): T ASSENZA DI RISCHIO § se 0,75 < I.E < 4 —> RISCHIO POSSIBILE § se I.E > 4 —> RISCHIO ELEVATO (La Pirelli ha elaborato una proposta per quantificare il carico energetico tramite l’INDICE DI SFORZO, ovvero il periodo di tempo nel quale il lavoro supera il costo cardiaco (uguale alla differenza fra frequenza di lavoro e frequenza basale) di 33 battiti/min. Inoltre, il costo cardiaco permette di distinguere fra lavoro leggero, moderato, medio, elevato e molto elevato). Altro indice è l’INDICE NIOSH per la rilevazione del rischio da sollevamento carichi che è pari al rapporto tra il peso sollevato e il peso limite raccomandato. Quest’ultimo non è altro che il prodotto fra la costante di peso e 6 fattori dipendenti dalle geometrie e dall’organizzazione di lavoro: (CP = COSTANTE DI PESO, A = ALTEZZA DA TERRA DELLE MANI ALL'INIZIO DEL SOLLEVAMENTO, B = DISLOCAZIONE VERTICALE DEL PESO FRA INIZIO E FINE DEL SOLLEVAMENTO, C = DISTANZA ORIZZONTALE TRA LE MANI E IL PUNTO DI MEZZO DELLE CAVIGLIE – (DISTANZA DEL PESO DAL CORPO - DISTANZA MASSIMA RAGGIUNTA DURANTE IL SOLLEVAMENTO), D = ANGOLO DI ASIMMETRIA DEL PESO, E = GIUDIZIO SULLA PRESA DEL CARICO, F = FREQUENZA DEI GESTI IN RELAZIONE ALLA DURATA). Una volta calcolato l’indice di NIOSH: § se < 0,75 à ATTIVITÀ BASSO RISCHIO RESIDUO; § se = 1 à PRESENZA DI RISCHIO DEBOLE DA TENERE SOTTO CONTROLLO; § se > 1 à RISCHIO RICHIEDENTE INTERVENTO. MICROCLIMA Contrariamente al clima generale che riguarda aerea geografica, il MICROCLIMA è la combinazione di fattori ambientali, quali temperatura dell’aria, umidità relativa, velocità dell’aria, calore radiante, che interessano un luogo di più ristrette dimensioni. In base alle valutazioni fatte all’interno di questo ambiente possono sussistere condizioni di benessere, che definiscono un ambiente di tipo moderato, invece condizioni di caldo/freddo che definiscono ambienti di tipo severi. Aspetto fondamentale riguarda il tipo di abbigliamento e di lavoro svolto, quindi coloro che hanno attività che non implica attività fisica saranno soggetti ad un minore attività metabolica e minore riscaldamento dovuto all’attività lavorativa. Tutto ciò bisogna tenerlo in considerazione per settare le temperature minime degli ambienti di lavoro tenendo in conto la differenza tra ambienti produzione e zona uffici. A livello normativo nasce tutto a livello di igiene degli ambienti di lavoro e le normative a livello internazionale, come ad esempio l’OMS, fissa le temperature raccomandate per i diversi ambienti di lavoro. In Italia avendo descritto la 303 come norma di riferimento sull’igiene del lavoro, il microclima è stato introdotto definendo oltre gli spazi adeguati allo svolgimento dell’attività lavorativa anche temperatura dell’aria, umidità relativa, velocità dell’aria, temperatura medio radiante. Tali aspetti sono stati anche riportati all’interno del Testo Unico che ha evidenziato la temperatura nei locali di lavoro adeguata all’organismo umano che deve essere giudicata considerando umidità e movimento d’aria e che la temperatura dei locali di riposo, dei locali per il personale di sorveglianza, dei servizi igienici, delle mense e dei locali di pronto soccorso deve essere conforme alla destinazione specifica di questi locali. Come funziona la TERMOREGOLAZIONE DEL CORPO UMANO? Negli esseri umani la temperatura corporea (tb) è la media pesata fra la temperatura interna (tcr), degli organi vitali (quella misurata internamente al corpo umano che corrisponde all’incirca su 37°C nei soggetti sani), e la temperatura esterna (tsk), relativa alla pelle dei tessuti sottocutanei. Il corpo umano mette in pratica due MECCANISMI AUTOMATICI DI TERMOREGOLAZIONE, disciplinati dall’ipotalamo: 1. Vasomotorio, per il quale i capillari periferici si aprono (vasodilatazioneà aumento scambio termico) e chiudono (vasocostrizioneà diminuzione scambio termico) per modificare lo scambio termico; 2. Comportamentale, che entra in funzione se il vasomotorio non è efficace, per il quale si generano brividi (produzione di energia) contro il freddo e sudore (evaporazione di liquidi con abbassamento locale della temperatura) contro il caldo. Sia brivido che sudore hanno un limite che porta a condizioni di insofferenza da parte delle persone. Funzione importante della termoregolazione la svolge l’ipotalamo, che è l’organo addetto ad attivare dei meccanismi sia comportamentali che vasodilatatori o vaso-costruttori per gestire la temperatura corporea. (MECCANISMO CON CUI PERCEPIAMO LE CONDIZIONI à (ad esempio, svolgendo un’attività intensa come la corsa, bruciando energia si ha un accumulo di calore, che determina la nascita di calore interno, i vasi sanguigni si dilatano per garantire maggiore afflusso di sangue in prossimità delle parti capillari del corpo umano garantendo maggiore espulsione del calore, ma altrettanto importante è quello che è il sistema comportamentale. Quest’ultimo si caratterizza da sudore e brivido. Se ho attività intensa le ghiandole sudorifere producono sudore che viene espulso a livello superficiale producendo raffreddamento del corpo, che avviene sia per abbassamento della temperatura interna che per calore latente, cioè evaporazione del sudore sulla pelle. È un po' la situazione che si ha nel momento in cui anche se parzialmente sudati siamo in ambiente con ventilazione che elimina sudore generando una sensazione di benessere anche in situazioni calde. La situazione opposta a livello di percezione del freddo, il corpo a seconda della situazione, esiste un confronto tra ambiente e temperatura corporea, se l’ipotalamo ha impostato il sistema e si inizia a sentire freddo, il confronto tra temperatura corporea e il valore di riferimento porta l’ipotalamo a innescare un sistema vasocostrittore, in cui si innesca la costrizione dei vasi sanguigni, cioè cala il flusso verso i capillari esterni e in questo modo si limita lo scambio verso esterno. A livello comportamentale se non è sufficiente la vasocostrizione si può attivare un meccanismo comportamentale legato al brivido: contrazione muscolare che produce energia al fine di riscaldare anche localmente il corpo umano, che è un movimento automatico e gestito dall’ipotalamo. La condizioni comportamentali non sono durature ma devono scatenarsi come aspetto comportamentale con piccole tempistiche. Il sistema dovrebbe complessivamente essere gestito a livello di corpo umano da un sistema vasomotorio senza intervento di brivido o sudorazione. Quando ci si accorge della necessità della parte di intervento comportamentale si ha a che fare con ambienti che presentano caratteristiche non di confort quindi o severi caldi o severi freddi) EQUAZIONE DI BILANCIO TERMICO: nell’equazione abbiamo che complessivamente il sistema deve essere possibile con variazione di energia interna del corpo umano nel tempo pari a zero: S = M – W - Ed - Esw - Ere - Cre - C - K - R con S: variazione di energia interna del corpo umano nel tempo [W] e M: metabolismo energetico [W] energia derivante dai cibi ingeriti (kca). Nell’espressione notiamo che abbiamo un solo termine positivo (metabolismo energetico) mentre gli altri termini sono negativi, quindi il nostro metabolismo energetico che è energia derivante dai cibi ingeriti deve essere abbastanza da bilanciare per coprire le spese energetiche date dai vari fattori: – W: potenza meccanica, energia scambiata sotto forma di lavoro, spesso trascurabile per lavori statici di cui si considera solo il 20% di energia dispersa in attività lavorativa. Il restante 80% è dovuto alla respirazione e alla fuoriuscita di calore tramite alcuni meccanismi a livello di conduzione, convezione e irraggiamento: – Ed, Esw, Ere: potenze termiche disperse per diffusione (pelle), sudorazione, respirazione. È funzione di diversi parametri umani (tsk, Iclo) e ambientali (T aria, v aria, umidità relativa/grado igrometrico, t radiante) – Cre: calore sensibile disperso nella respirazione, riguarda solo le differenze temp tra ingresso e uscita. – C, K, R: potenza termica dispersa per convezione, conduzione, irraggiamento. Spesso riferito alla superficie corporea caratterizzata da un indice Ab [W/mq], dove Ab = 0,202 m^0,245 h^0,275 che definisce in modo empirico quella che può essere l’area del corpo umano in funzione del peso e dell’altezza. Questo dice fondamentalmente che persone dotate di una massa maggiore e maggiore altezza, perdono più energia legata all’ampiezza dello scambio termico che si ha sulla superficie. Maggiore è ampio lo scambio termico avuto, maggiore dovrà essere il metabolismo per ripristinare questo bilancio. Tutto questo è legato ad azione stazionaria. Qualora qualcuno mangiasse di più tale variazione non sarà pari a zero ma diventerà positiva e si accumula peso in termini di energie non sfruttate durante l’attività giornaliera. Dall’equazione di bilancio a seconda della temperatura per la quale si verifica S=0 si ha: 1. ambiente moderato S=0; 2. ambiente termicamente severo caldo S=0 ma legato ad elevata sudorazione; 3. ambiente termicamente severo freddo S=0 ma con consumo energetico legato alla potenza meccanica consumata per necessità di riscaldamento tramite attività fisica o brivido; VARIABILI DA CONSIDERARE PER LA VALUTAZIONE MICROCLIMATICA DI UN AMBIENTE. Per la valutazione dell’ambiente di lavoro bisogna considerare le seguenti variabili: i. temperatura aria è la temperatura misurata con un termometro a bulbo secco ii. velocita dell’aria è la velocità che ha l’aria nell’ambiente stesso misurata con dinamometri. iii. grado igrometrico è il grado di umidità relativa posseduto da un ambiente interno. iv. temperatura media radiante è la temperatura uniforme di un ambiente fittizio che causerebbe lo stesso scambio termico con il corpo umano. A livello di calcolo, si calcola sommando la temperatura sulle superfici presenti che vengono valutate in base all’ esposizione che hanno. Bisogna inoltre tenere conto di variabili relative alla persona: v. metabolismo energetico M che è l’energia derivante dai cibi ingeriti vi. resistenza termica dei vestiti ICLO MISURA DELLE VARIABILI 1. Metabolismo: che viene valutato in funzione degli organi vitali. Viene misurata quella che è a livello medio il consumo a livello di riposo fisico e mentale e la necessità di reintegro delle energie spese. In un soggetto a riposo ho un consumo medio di 43 W/mq, più è elevata l’attività svolta dal lavoratore più sarà il suo consumo e quindi l’energia riportata all’esterno sotto forma di energia meccanica. Viene valutata facendo valutazioni sul campo oppure valutata a livello di tabelle in funzione dell’attività fisica svolta studiata negli anni da parte della società ergonomica italiana. 2. Resistenza termica dell’abbigliamento: che ha come unità di riferimento il Iclo cioè un grado di resistenza di abbigliamento che garantisce 0,55 K mq / W. 3. T aria: si usa un termometro a bulbo secco senza indicazione di come questa sia influenzata da umidità e dalla velocità dell’area stessa, oppure sensore posizionato in posizione protetta. 4. Velocità dell’aria: uso di diversi strumenti come anemometri che misurano la velocità dell’aria in base allo scambio termico, sono strumenti a filo caldo. Ad esempio, anemometri digitali possono presentare struttura a palette, tipo sistema eolico, sono meno precisi perché quelli a filo caldo sono di dimensioni più piccoli e prendono meglio la velocità dell’aria in punti più ristretti. Il sistema ad elica valuta la velocità mediamente in un’area coinvolta da flusso di aree. 5. Grado igrometrico: corrisponde alla pressione parziale del vapore d’acqua ad una data T/pressione in condizioni di saturazione. Vengono valutati i gradi igrometrici con termometro bulbo bagnato che misurano in condizioni di umidità quanto è la temperatura rilevata in quell’ambiente considerando l’evaporazione legata al bulbo bagnato, quindi considerando la condizione esterna di umidità che limitano questo aspetto di evaporazioni. Altri strumenti sono igrometri a capello (è un sistema che misura elongazione di un capello a seguito di umidità nell’ambiente. A seguito umidità il capello si allunga ed ha maggiore elasticità) e a condensazione. Gli strumenti di esposizione sono diversi e molte volte vengono abbinati alla temperatura. 6. Temperatura media radiante: il globo termometro è una palla nera con all’interno indicazione di temperatura, in cui viene misurata temperatura esterna dell’aria, e se palla nera è all’ombra ha temperatura radiante simile a quella aria. Se al sole ha temperatura interna molto + alta rispetto a quella dell’aria. Anche il corpo umano subisce questo effetto dell’irraggiamento. In questo caso il fatto di avere la palla nera disposta in ambiente con velocità dell’aria si ha un minore scaldamento all’interno del globo, perché si ha velocità media dell’aria che influisce. QUALI SONO GLI AMBIENTI DA ANALIZZARE E COME VENGONO VALUTATI TERMICAMENTE MODERATI: ambiente moderato si ha se NON intervengono fenomeni comportamentali come attivazione di brivido e di sudorazione, ovviamente funzione del grado di attività svolta dall’operatore e del suo abbigliamento per la stagione considerata. Anche a livello normativo la temperatura da mantenere in periodi invernali ed estive è diversa proprio perché si considera anche la persona terminata l’attività lavorativa esca dal lavoro. Nei periodi estivi si tende ad una temperatura max 24°, nei periodi invernali temperatura minima di 18°. Il tutto cambia nelle parti produttive perché possiamo avere temperatura 2400 W/mq ® rischio grave di congelamento Si chiama così perché considera l’importanza del vento, cioè di quanto oltre alla temperatura l’aria riesce a rimuovere a livello di scambio termico da questo cilindro verticale con t esterna di 33°C in funzione anche della velocità dell’aria, la presenza del vento distrae dal calore del corpo umano. A livello di protezione è possibile utilizzare un abbigliamento soprattutto nei periodi invernali, ma possono esistere anche sistemi per ambienti severi caldi. Parlando di abbigliamento si parla di una protezione passiva, data da abbigliamento costituito da 1 o + elementi in serie con funzioni di protezione. Per lavori in zone particolarmente calde possono esistere sistemi attivi, costituiti da parti in movimento e collegate con una fonte di energia. A tal riguardo un sistema attivo può essere un sistema in cui si ha una tuta completa in cui nella parete esterna si ha lo scorrimento di un fluido refrigerante. Altri aspetti riguardano la posizione e l’acclimatamento cioè posizionare in modo corretto le persone a livello lavorativo per evitare come nel caso dei forni un’esposizione troppo elevata a livello di temperatura e di tempo. RISCHIO ESPLOSIONE Il RISCHIO ESPLOSIONE è normato in Italia tramite direttive europee, in particolare: a. la DIRETTIVA 99/92/CE che riguarda gli obblighi del datore di lavoro riguardo ambienti con rischio esplosione relativa al miglioramento della salute e sicurezza dei lavoratori esposti al rischio di atmosfere esplosive. Si rivolge, dunque, agli utilizzatori di impianti e attrezzature certificate. b. la DIRETTIVA 2014/34/UE maggiormente tecnica si rivolge ai costruttori di apparecchiature utilizzate in zone a rischio esplosione e definisce i RES (Requisiti Essenziali di Sicurezza) di tali prodotti, per i quali è previsto l'obbligo di opportuna certificazione. La Direttiva 99/92 riguarda le prescrizioni minime per il miglioramento della sicurezza e della salute dei lavoratori, che possono essere esposti al rischio di atmosfere esplosive. Tale direttiva definisce cosa si intende per atmosfera esplosiva: una miscela di aria, in condizioni atmosferiche, con sostanze infiammabili allo stato di gas, vapori, nebbie o polveri in cui, dopo ignizione, la combustione si propaga all'insieme della miscela incombusta. Sulla base di quanto definito già in precedenza, l’applicazione di questa direttiva costituisce un contributo concreto alla realizzazione della dimensione sociale del mercato interno e la protezione contro esplosioni, che è di particolare importanza per la sicurezza; poiché le esplosioni mettono in pericolo la vita e la salute dei lavoratori per l'effetto incontrollabile delle fiamme e della presenza di prodotti di reazione nocivi e del consumo dell'ossigeno presente nell'atmosfera. Tale rischio è da considerarsi diverso dal rischio incendio perché non si ha anche fare con una combustione, ma con esplosione che può avvenire grazie alla presenza di sostanze che hanno una certa propensione ad infiammabilità o che producono gas legati a meccanismi interni e fermentativi come possono essere delle polveri che possono entrar in contatto con l’ossigeno e poi esplodere. Il Datore di Lavoro ha obblighi definiti nel valutare e gestire il rischio esplosione presente in azienda, attraverso l’identificazione delle aree di lavoro associate a tali rischi e ai fini della prevenzione e della protezione contro le esplosioni, il datore di lavoro adotta le misure tecniche e/o organizzative adeguate al tipo di azienda in linea con principi fondamentali: Prevenire la formazione di atmosfere esplosive, oppure, se la natura dell'attività non lo consente, Evitare l'ignizione di atmosfere esplosive, e attenuare i danni di un'esplosione in modo da garantire la salute e la sicurezza dei lavoratori Dal punto di vista degli obblighi il datore di lavoro prende i provvedimenti necessari affinché: Dove possono svilupparsi atmosfere esplosive in quantità tale da mettere in pericolo la sicurezza e la salute dei lavoratori o di altri, gli ambienti di lavoro siano strutturati in modo da permettere di svolgere il lavoro in condizioni di sicurezza; Negli ambienti di lavoro in cui possono svilupparsi atmosfere esplosive in quantità, tale da mettere in pericolo la sicurezza e la salute dei lavoratori, sia garantito un adeguato controllo durante la presenza dei lavoratori, in funzione della valutazione del rischio, mediante l'utilizzo di mezzi tecnici adeguati. Inoltre, è stabilito che il datore di lavoro debba provvedere a elaborare (e aggiornare costantemente) un “documento sulla protezione contro le esplosioni". Tra le informazioni principali contenute in questo documento vi sono: i. Individuazione e valutazione dei rischi di esplosione; ii. Adozione delle misure adeguate al raggiungimento degli obiettivi; iii. Identificazione dei luoghi a rischio e di quelli in cui si applicano le prescrizioni minime; iv. Corretto impiego e manutenzione di luoghi, attrezzature e dispositivi di allarme; v. Adozione di accorgimenti per l'impiego sicuro delle attrezzature di lavoro. Dal punto di vista della valutazione del rischio esplosione, essa avviene secondo una procedura diversa dal rischio generico, ma segue le indicazioni principali. Vengono valutate: i. probabilità e durata della presenza di atmosfere esplosive, cioè per quanto tempo ho quella condizione particolare; ii. probabilità della presenza, dell'attivazione e dell'efficacia di fonti di ignizione, comprese scariche elettrostatiche; iii. caratteristiche dell'impianto, sostanze utilizzate, processo e loro possibili interazioni, iv. entità degli effetti prevedibili. Nella valutazione dei rischi di esplosione vanno presi in considerazione i luoghi che sono o possono essere in collegamento tramite aperture con quelli in cui possono formarsi atmosfere esplosive. RIPARTIZIONE DELLE AREE IN CUI POSSONO FORMARSI ATMOSFERE ESPLOSIVE. Nella classificazione delle aree vengono fatte due importanti distinzioni, tra luoghi in cui il rischio esplosione è dovuto alla presenza di gas (1) rispetto a quelli in cui è legato alle polveri combustibili (2). Nella classificazione delle zone con pericolo esplosione per la presenza di gas, nebbie o vapori infiammabili, vengono individuate: 1. Zona 0: l’atmosfera esplosiva è presente continuamente o per lunghi periodi; 2. Zona 1: durante le normali attività, è probabile la formazione di atmosfera esplosiva; 3. Zona 2: durante le normali attività, non è probabile la formazione di atmosfera esplosiva. Come avviene per i gas, anche nella classificazione delle zone con polveri combustibili vengono individuate tre aree: 1. Zona 20: area in cui è presente un'atmosfera esplosiva, sotto forma di nube di polvere combustibile nell'aria, in continuazione, per lunghi periodi o frequentemente; 2. Zona 21: area in cui la formazione di un'atmosfera esplosiva, sotto forma di nube di polvere combustibile nell'aria, è probabile avvenga occasionalmente; 3. Zona 22: area in cui la formazione di un'atmosfera esplosiva, sotto forma di nube di polvere combustibile, non è probabile oppure avviene solo per brevi periodi. Infine, cosa importantissima ai fini installativi, la direttiva 99/92/CE fornisce i criteri per la SCELTA DEGLI APPARECCHI IN RELAZIONE ALLE ZONE DI INSTALLAZIONE Zona 0 – Zona 20 à Apparecchi di categoria 1 Zona 1 – Zona 21 à Apparecchi di categoria 1 o di categoria 2 Zona 2 – Zona 22 à Apparecchi di categoria 1 o di categoria 2 o di categoria 3 La Direttiva 2014/34 sulla base della direttiva precedente 94/9, ha lo scopo primario di assicurare che i prodotti su cui essa si applica, commercializzati in ambito Comunitario, siano sicuri; inoltre, la direttiva vuole assicurare la loro libera circolazione all’interno dei territori della UE. I prodotti che rientrano nel campo di applicazione della Direttiva sono in particolare: Apparecchi e sistemi di protezione destinati a essere utilizzati in atmosfera potenzialmente esplosiva; Dispositivi di sicurezza, di controllo e di regolazione destinati a essere utilizzati al di fuori di atmosfere potenzialmente esplosive ma necessari o utili per il funzionamento sicuro degli apparecchi e sistemi di protezione, rispetto ai rischi di esplosione; Componenti destinati ad essere inseriti negli apparecchi e sistemi di protezione. CRITERI PER LA CLASSIFICAZIONE DEI GRUPPI DI APPARECCHI IN CATEGORIE GRUPPO DI APPARECCHI I: destinati ai lavori in sotterraneo nelle miniere 1. CATEGORIA M1 i. Livello di protezione: Molto elevato. ii. Apparecchiature che possono funzionare anche in presenza di atmosfera esplosiva. 2. CATEGORIA M2 i. Livello di protezione: Elevato. ii. Apparecchiature che devono essere messe fuori tensione in presenza di atmosfera esplosiva. GRUPPO DI APPARECCHI II: 1. CATEGORIA 1 i. Livello di protezione: Molto elevato ii. Presenza di atmosfera esplosiva: sempre, spesso e per lunghi periodi 2. CATEGORIA 2 i. Livello di protezione: Elevato ii. Presenza di atmosfera esplosiva: probabile 3. CATEGORIA 3 i. Livello di protezione: Normale ii. Presenza di atmosfera esplosiva: scarsa possibilità e per breve tempo APPROFONDIMENTI-MARCATURA CE. La marcatura CE è in pratica una dichiarazione del fabbricante in cui si afferma che il prodotto in questione è stato fabbricato in conformità di tutte le disposizioni e a tutti i requisiti applicabili della direttiva ATEX e che il prodotto è stato sottoposto alle procedure di valutazione della conformità. La marcatura CE è obbligatoria e deve essere apposta prima dell’immissione sul mercato o della messa in servizio di qualunque apparecchio o sistema di protezione. In generale, la marcatura CE deve essere apposta sul prodotto o sulla targhetta di identificazione. RISCHIO CHIMICO È un rischio al quanto diffuso che riguarda molte aziende, poiché diffuso in diverse tipologie di lavorazione, non necessariamente solo in aziende chimiche. Il rischio chimico tratta agenti di titolo cioè inquinanti atmosferici che producono effetti dannosi all’interno e all’esterno dell’ambiente di lavoro, sull’organismo umano, relativo al malfunzionamento di macchine (polveri) e di situazioni di pericolo sopra certe percentuali di concentrazioni (sostanze esplosive, infiammabili). A livello di campo dimensionale l’agente di titolo va da dimensioni molto piccole di 0,001 μm di diametro per le molecole gassose, rispetto a dimensioni anche visibili ad occhio nudo di 1000 μm (polveri o terra calcarea). DEFINIZIONE secondo il Testo Unico i. Agenti chimici: tutti gli