Sheet Metal Forming Processes PDF
Document Details
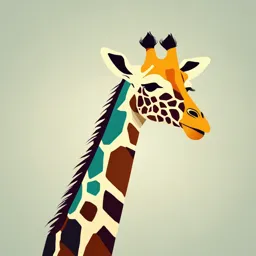
Uploaded by WellBehavedCaricature
2024
Tags
Related
Summary
This document provides an overview of sheet metal forming processes, covering shearing, bending, and other operations. It explains concepts like punch and die operations, burr formation, and different bending methods such as air bending and bottom bending. The document also explores material characteristics, such as elongation and anisotropy, relevant for sheet metal processing. Lastly, an overview of various processes like fine blanking, punching, and blanking is presented.
Full Transcript
PROD1334 - Sheet Metal Monday, November 11, 2024 2:50 PM Sheet metal (usually steel, often aluminum) is used in a lot of applications - Auto parts - Aerospace parts - Appliances - Furniture - Food containers - Tubes - Machine parts Sheet Metal advantages...
PROD1334 - Sheet Metal Monday, November 11, 2024 2:50 PM Sheet metal (usually steel, often aluminum) is used in a lot of applications - Auto parts - Aerospace parts - Appliances - Furniture - Food containers - Tubes - Machine parts Sheet Metal advantages - Light & strong - Extremely formable into a wide variety of shapes - Suited to high production rates - Wide variety of well-established, well understood production processes available Shearing Basic process of cutting sheet metal using shear forces, typically with a punch & die or a pair of shear blades - Unlike other cutting processes, shearing produces no chips. No melting or burning of material - Shearing action is similar to cutting paper with scissors or thin metal with tin snips - Shearing is done using dies or blades - When blades are straight, the process is simply called shearing. Shearing with curved blades has special process names (Punching, blanking) - Conventionally sheared edges are not straight & smooth - Deformation occurs as the punch presses into the sheet metal. - This is followed by fracture of the material due to shear stresses exceeding the material shear strength - The resulting edges are somewhat rough & ragged - Sharp tool edges & proper clearances tend to produce edges that are acceptable for many purposes. - The resulting edges are not only somewhat rough & ragged but also strain hardened by the shearing deformation - This strain hardening may reduce formability of a punched part for further forming processes. Shearing with a Punch & Die - Quality of the sheared edge depends largely on the clearance between the punch & die - Larger clearances cause the metal to be pulled into the gap, resulting in heavy deformation & a large burr - Secondary deburring operations may be necessary to improve the resulting edges Burrs - Burrs are raised edges or ridges along a sheared edge - They are worsened by ○ Soft ductile materials ○ Dull tooling ○ Large clearances - Burrs may interfere with subsequent forming operations & present a safety hazard when handling parts Shearing Clearance - Clearance is usually 2% - 8% of metal thickness - It can be as tight as 1% for precision operations - Clearance is usually higher for softer metals than for hard metals Fine Blanking - Produces much smoother & better edges than conventional blanking - Clearance is very tight, less than 1% of metal thickness - Higher forces are req'd - Workpiece must be clamped firmly before blanking dies are applied - Material stresses are compressive & shear, with essentially no bending stress - Complex shapes may be produced with very clean, square edges Punching & Blanking Two very common shearing operations that use closed-curved dies (round or otherwise) are punching & blanking: - Punching (or piercing) removes an unwanted slug from the surrounding workpiece - Slug is typically scrap - Blanking cuts a workpiece for further processing from a sheet - Rest of the sheet is typically scrap Other Shearing Operations - Parting to separate lengths of sheet metal - Perforating to make numerous small pierced holes in workpiece - Notching to remove pieces of material from existing edges - Lancing to form a tab without material removal - Slitting to shear metal using circular rolling blades - Nibbling to cut a contour using short overlapping slits or notches - Shaving to trim away a small amount of material from a sheared edge to improve it’s quality - Steel Rule cutting uses thin steel blades to cut soft metal, rubber, leather & other soft materials Slitting with Rotary Knives - Slitting cuts sheet metal, usually continuously along the length, using rotary rolling blades, much like a can opener Nibbling - Can be done using pneumatic or other hand tools, or by production machines - Because only small amount of metal are removed at a time, forces correspondingly lower Parts made by Perforating - Used for light weight, to allow flow for filter elements, to enhance friction for tread plates & decorative applications Compound Dies - Several shearing operations can be performed in close succession by using compound dies, which contains one set of dies nested within another - Can be used for making washers among many other parts Progressive Dies - Parts require multiple stamping operations to form them can be done sequentially along a strip of metal using different progressive dies at each stage. Last stage separates the finished discrete part from the strip - Aersol can tops are formed this way Tailor-Welded Blanks Sheet Metal Characteristics - Processes involve shearing, bending & stretching metal - The characteristics of the metal have significance in these operations - Important characteristics that influence formability include: ○ Elongation ○ Anisotropy Elongation is the amount that metal can stretch without necking & failure Anisotropy refers to difference in strength & ductility in different directions - Wood is anisotropic because of its grain direction - Rolled sheet metal is anisotropic for similar reasons Elongation Formability & Cupping Test - Cupping test is used to measure a metals formability - Strips of different widths are stretched over a bowl-shaped punch - For narrow strips, the elongation is nearly uni-directional (drawing) - For wide pieces, the elongation is equal & biaxial (stretching) Deformation & Tearing as a result of the cupping test - For all strips the major strain (lengthwise) is always positive, circular always gets taller - Minor strain is negative (circle gets narrower) for the narrow strip Sheet Metal Forming Bending is one of the most common sheet metal forming processes - Usually defined as plastic deformation of sheet metal along a straight line - Producing bends that follow curves instead of straight lines are properly called forming operations - Used to produce corners, hems, flanges, seams, etc Bending Terminology - Bend allowance is length of the curved neutral axis - Bend radius is the radius of the curved inside surface - Bend angle is the inside angle of the end - Length of bend refers to the distance along the bent edge, not around the bend Bending Stresses - Results in compressive stresses on the surface inside the bend & tensile stresses on the surface outside the bend - In between there is a neutral axis, where there is ZERO stress - Tensile stresses can cause cracking if they are large enough to exceed a materials tensile strength Effect of Elongated Inclusions Minimum Bend Radius - There is some minimum bend radius for sheet metal, its usually safe for 1.5T - Depends on material thickness, strength & ductility - Soft thin metals have small bend radii - Thick stronger materials require larger radii to avoid volume defects such as cracking at the outer surface Springback in Bending - Sheet metal bending requires plastic deformation - Before plastic deformation occurs, a certain amount of elastic deformation occurs, causing the material to partly recover its shape when the bending stress is removed Reducing Springback - Three techniques can be used to reduce or eliminate springback ○ Overbending (for air bending or bottom bending) ○ Coining by bottoming the punch (bottom bending only) ○ Stretch Bending Bending Operations - Air bending is done with a wide bend allowance, relatively large bend radius & low bending force - Bottom bending is more like forging, with the dies in closer contact with the workpiece. Smaller radii & more precise bends can be made, but with higher forces - Bending in a 4-slide machine can produce tube from sheet metal Air Bending vs Bottom Bending Roll Bending - Roll bending passes narrow sheet metal or bar stock through rollers to impart a controlled curve - Straight flat bar can be rolled into hoops & wheels Common Die-Bending Operations - Die bending uses a press-brake typically uses a right-angle V die or a wiping die to produce small radius, sharp straight bends Bead Forming - Beads can be formed on sheet metal edges to provide reinforcement & protection from the sharp edge Common Press Brake Bending Operations - Number of bending processes can be carried out on a press brake - Include bends, for edge reinforcement, making joints & shapes Flanging Operations - Flanges are sheet metal edges bent to 90 - Shrink flanges are curved inward & may cause the edges to wrinkle - Stretch Flanges are curved outward & can cause tearing in the metal Flanging & Flaring Operations - Flanges can be made around holes using a punch & die - Flanges can also be done on tube ends to mate with fittings - When the flange angle is lesss than 90 it is called a flared tube Tube Flaring Methods of Bending Tubes - Tubes are bent around forming dies for small radius - Thin-walled, low ductility tubing tends to collapse when bending. This can be addressed by using bendable, removable mandrels inside the tube to support the walls from the inside Sheet Metal Definitions Blanking - sheet metal shearing operation where a sheared slug is the part to be used while the rest of the part is scrap Burr - thin edge or ridge that occurs during a shearing operation where the height of the burr increases with increasing clearance & ductility of the sheet metal. Dull tool edges contribute greatly to large burr formation Compound Dies - type of die that allows for several operations to be performed in one stroke on the same sheet at one station Fine Blanking - Square edges with very smooth sheared surfaces can be produced by fine blanking Punching - sheet metal shearing operation where a sheared slug is scrapped & the rest of the part is used Transfer Dies - the sheet metal undergoes different operations at different stations of the machine, dies are usually arranged in a straight line or as a circular path Bend Allowance - length of the neutral axis in the bend, used to determine the length of the blank for the part to be bent Deep Drawing - After a cup is deep drawn, it invariably will spring back slightly towards its original shape. Vertical walls may be difficult to draw and require relief angles of a minimum of 3 degrees Flanging - Process of bending the edges of sheet metals usually to 90 degrees. Hemming - forming operation in which the edges of the sheet are folded or folded over another part in order to achieve a tight fit. Nesting - efficient arrangement of the shapes on the sheet to be cut Press Brake - machine that performs the bends by compressing the sheet or plate between the movable punch and the stationary die. Ironworker - class of machine that can shear, notch, and punch holes in steel plate and profiles by generating force using mechanical advantage or hydraulic systems. Spring Back - All materials have a finite modulus of elasticity, plastic deformation is always followed by some elastic recovery when the load is removed. Tailor-welded blank - method of producing automotive structural components by seam welding two or more pieces of sheet metal together to form a composite blank Sheet Metal Review Questions 16.2 What causes burrs? How can they be reduced or eliminated? Burrs are caused by soft ductile materials, dull tooling & large clearances. Burrs can be reduced or eliminated by ensuring the use of sharp tooling (skimming the face of the die), reducing the clearance if possible & forming material that is harder & less ductile. 16.4 Describe the difference between compound, progressive & transfer dies. Progressive dies are used for high-volume production, creating parts in several stages. Compound dies combine multiple operations into a single stroke, making them efficient for simpler parts. Transfer dies are versatile and suitable for larger, more complex components 16.5 Describe the characteristics of sheet metals that are important in sheet-metal forming operations. Explain why they're important. Elongation - Determines the capability of the sheet metal to be stretched without necking & failure Yield Point Elongation - Observed with mild steel sheets, results in shallow depressions on the sheet surface Anisotropy (plane) - Exhibits different behavior in different planar directions; present in cold rolled sheets, causes earing in deep drawing can be reduced or eliminated by annealing. Anisotropy (normal) - determines thinning behavior of sheet metals during stretching; important in deep drawing Grain Size - Determines surface roughness on stretched sheet metal; coarser grains exhibit rougher appearance Residual Stresses - Caused by nonuniform deformation during forming, results in part distortion when sectioned Springback - due to elastic recovery from plastically deformed sheet after load is removed, causes dimensional inaccuracy & part distortion Wrinkling - caused by compressive stress in the plane of the sheet, can be useful for imparting stiffness to parts by increasing their section modulus 16.10 Define normal anisotropy & explain why it is important in determining the deep drawability of a material. Normal anisotropy is the tendency of a metal to become thinner as it is stretched and is related to grain orientation and Poisson's ratio. In deep drawing, material that is thinner tends to tear. 16.13 Explain the difference between deep drawing & redrawing Deep drawing is a sheet metal forming process in which a sheet metal blank is radially drawn into a forming die by the mechanical action of a punch. Redrawing is the process of drawing a piece that was too difficult to draw in one operation. 16.20 What is springback? What is negative springback? Springback is the tendency of a material to recover elastically from deformation to its shape when a load is removed. The bend radius becomes larger. Negative springback is when the final bend angle becomes smaller than the original angle. 16.33 What recommendations would you make in order to eliminate the cracking of a bent piece shown in Figure 16.17c? Explain your reasons. Cracks also like to appear in the drawing direction of the cup. Stress relieving the material before the operation, producing the cracks, and reducing the material's compression are standard practices to prevent this defect.