IMCA Safety Flash 11/24 - June 2024 PDF
Document Details
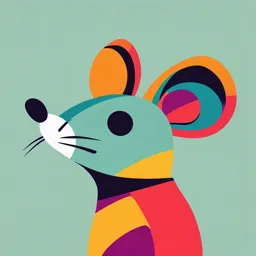
Uploaded by IntelligibleBeige
null
2024
Tags
Related
- MEC232 Human & Equipment Safety - Topic 1 - PDF
- Unsafe/Unhealthy Acts and Conditions in the Workplace PDF
- Chapter 1: The Concept of Safety PDF
- General Engineering All Concepts PDF
- Safety Refresher Training Manual PDF (Southern Petrochemical Industries Corporation Ltd)
- Proposed CBCS Course Syllabus Industrial Safety PDF
Summary
This document is an IMCA safety flash from June 2024, detailing various safety incidents and lessons learned relating to lifting operations, vessel collisions, diver incidents, and stored energy.
Full Transcript
Safety Flash 11/2...
Safety Flash 11/24 – June 2024 IMCA Safety Flashes summarise key safety matters and incidents, allowing lessons to be more easily learnt for the benefit of all. The effectiveness of the IMCA Safety Flash system depends on members sharing information and so avoiding repeat incidents. Please consider adding [email protected] to your internal distribution list for safety alerts or manually submitting information on incidents you consider may be relevant. All information is anonymised or sanitised, as appropriate. 1 Dropped lifting beam due to parted soft strop What happened? Applicable During lifting operations a lifting beam weighing 4 Te was dropped from 50cm. Life Saving The incident occurred when the lifting beam was being prepared for relocation Rule(s) Safe for sea fastening prior to transit. A 1 Te strop was doubled through the main Line of Fire Mechanical Lifting lifting pad eye on the lifting beam for the relocation. When the crane started lifting the beam, the soft strop parted, and the beam fell 50cm to deck. The deck crew kept a safe distance from the lift; no-one was injured. What went wrong The weight of the lifting beam was not checked before the relocation; An unidentified sharp edge on the pad eye in combination with an 1 Te soft strop (lifting a beam weighing 4 Te) caused the soft strop to part. Our member considered that owing to the nature of the unidentified sharp edge on the pad eye, it is likely that even a higher rated soft strop would have also been severed in this operation. What was the cause Our member identified as the cause, a failure to properly assess and identify risk. Actions taken Never use soft strops against straight / sharp edges; Any straight or sharp edges or corners identified should be protected or covered or alternate lifting arrangements identified; IMCA store terms and conditions (https://www.imca-int.com/legal-notices/terms/) apply to all downloads from IMCA’s website, including this document. IMCA makes every effort to ensure the accuracy and reliability of the data contained in the documents it publishes, but IMCA shall not be liable for any guidance and/or recommendation and/or statement herein contained. The information contained in this document does not fulfil or replace any individual’s or Member's legal, regulatory or other duties or obligations in respect of their operations. Individuals and Members remain solely responsible for the safe, lawful and proper conduct of their operations. © 2022 Page 1 of 7 Verify the weight of objects before the lift. Always verify that lifting equipment has the capacity to lift the load in hand; Be ready to STOP THE JOB if you are unsure about the safest method to be used. Members may wish to refer to: Failure of webbing strop during lifting operations Failure of slings during loading operations Failure of lifting equipment: Dropped ROV High potential near-miss – Lifting equipment failure IMCA LR009 - Guidance on the selection, safe use and inspection of high performance fibre slings used for engineered lifts 2 Vessel collided with platform What happened? Applicable A vessel was waiting on weather when it collided with an unmanned and unlit platform. Life Saving The vessel had been holding on DP at a fairly constant distance from the platform for about Rule(s) Bypassing four hours from midnight, but thereafter, started to move towards the platform. The Safety vessel was being driven using “joystick auto heading mode”. The vessel started moving Controls forward and collided with the platform. The vessel was pulled out to a safe location and then moved out of the field and into port for investigation and assessment. Nobody was injured and the vessel only sustained minor damage to the helideck netting supports. The platform suffered no significant damage. What went right There were no failures to the vessel equipment or systems; There was no failure of the management system; the Masters’ night orders, standing orders and the safety management system itself all clearly emphasised watchkeeping duties; Vessel track and the 2 circles plotted on the survey screen. IMCA Safety Flash 01-24 had been received by the vessel just 10 days before this incident, Item 5 dealt with a similar incident at a wind farm. All the bridge personnel had signed off on a toolbox talk discussing the very issue; The vessel operates strictly according to Safe Manning Levels for 24-hour operations, and MLC STCW Rest Hours. What went wrong The second officer was carrying out non-essential paperwork, in contradiction of the night orders, the standing orders, and the safety management system itself; ̶ Investigation with the crew afterwards suggested that it is considered normal practice even when it is stated as not being permitted - because “somebody has to do it”; IMCA Safety Flash 11/24 Page 2 of 7 The Chief Mate was new to the company and the vessel (a little over a month) but had extensive experience as a Senior DPO, a Chief Mate and as a Master on DP2 vessels. On this occasion he allowed himself to become distracted and complacent, it is felt that he might have become a little too relaxed because the vessel was waiting on weather; The vessel heading was not intended to be directly towards the platform, but the wind direction and the shape of the holding area meant it was pointing in that direction at the time; The Radar and ECDIS alarms were not set, it was not mandatory to use them in any document or Risk Assessment, but the advice given in SF 01-24 was to “Use all available sensors and instruments.” ̶ This has now been made mandatory across the fleet. There was no risk assessment of the holding area as such - it was not considered to be unsafe. What were the causes of the incident? Our member considered the following to be Root Causes: Failure to properly monitor the position and speed of the vessel; Lack of situational awareness; the vessel was being held approximately 750m from an offshore installation. It was in a blow off position but because of the wind direction, was pointing directly at the platform; The Master’s standing orders, night orders and safety management system were not fully followed; The second officer, who was officer of the watch (OOW) was engaged in non-watchkeeping duties and had not requested a seaman to assist with the watch keeping. A contributory factor was that neither radar proximity nor ECDIS alarms were set. Lessons learned In the safety management system, clear reference has been included stating the requirement to carry out/maintain DP checklists, even when vessel is set on joystick auto heading mode; A watchkeeping Job Safety Analysis was introduced identifying different modes of navigation and detailing the recommended positioning and mode for the vessel, especially when waiting on weather; There should be no distractions on the bridge, including those caused by reading, electronic devices or irrelevant discussions with non-essential personnel; While it is important to keep administrative tasks up to date, someone suitably trained for the task should keep watch or be posted as a lookout if admin tasks are being carried out, maintaining proper and effective watchkeeping; Use all available navigation aids, sensors and equipment to establish accurate navigational warnings. Actions Updated and reviewed the safety management system to identify ambiguities in wording; A daily toolbox talk to be held for watchkeepers with a discussion of the DP mode being used; Prevented non-essential personnel from being on the bridge unless necessary; Enforced an absolute ban on non-watchkeeping duties unless proper watchkeeping cover is available. Members may wish to refer to: MAIB: Workboat collision with wind turbine platform Windfarm Support Vessel Njord Forseti hit wind turbine tower – Jersey Maritime Administration Vessel Near Miss with wellhead IMCA Safety Flash 11/24 Page 3 of 7 3 Diver’s umbilical trapped during a pipeline flooding operation What happened? A saturation diver lost his breathing gas supply and had to go onto his emergency cylinder. The incident occurred on a moored 8-point construction barge during flooding operations near the pulling head of a newly laid pipeline. Water depth at the platform was 53 msw. The pulling head of the newly laid line was in close proximity to another pipeline approximately 1.5m off seabed. Local arrangements consisted of a quarter turn valve and diffuser at the pulling head. Shortly after initiating the flooding, Diver 1 reported ”All Stop” as the pipeline shifted horizontally by approximately 1.5m. Diver 1 umbilical became trapped between two pipelines resulting in a lost video signal, a restriction of breathing gas and only 1 m of umbilical available for manoeuvring. As Diver 2 approached to help, Diver 1 lost gas and went on his emergency gas cylinder. Diver 2 then provided pneumo gas to Diver 1 who turned off his “Bail-Out” to conserve emergency gas. Both divers worked in tandem to reconnect the pipe, lift it, and clear the umbilical. Once freed, breathing gas was restored to Diver 1 with 210 bar remaining in his “Bail Out Bottle”. Both divers were able to return to the bell. Damaged umbilical Visibility was 1 to 2m with a significant but not excessive tidal current of 0.75 -1 kt. What went right? What went wrong? Everyone in the team followed emergency It was not recognised that there was potential for procedures, communicated, and performed in an movement of the pipeline during the flooding efficient and controlled manner; phase in combination with the relatively unstable All evidence from the event was retained configuration being used; including the Black Box which was sent to shore Despite numerous / continued reminders and for review; confirmations that the umbilicals were clear, the Witness statements received from the OCS, trapping still occurred. assistant dive supervisor, dive supervisor and the bell team were clear and well written. What was the cause The “as left” condition of the pipeline off the seabed and resting on top of other pipelines. The tidal current was pushing umbilicals against an elevated pipeline. Movement of the pipeline was due to a shift in weight as a consequence of flooding. When flooding started, the centre of gravity changed causing the pipeline to shift towards the diver; The divers’ umbilicals were routed over and parallel to the pipes allowing portions to dip into a pinch point area. Lessons Flooding a pipeline is a dynamic undertaking which may have unexpected consequences; “As found” or “as left” conditions should be inspected and assessed for potential hazards before starting work; Umbilical management should take into consideration numerous changing variables; IMCA Safety Flash 11/24 Page 4 of 7 Members may wish to refer to: Umbilical management – near miss Near miss: diver’s umbilical trapped Near miss: divers umbilical drawn beneath a load 4 Stored energy - dislodged pin causes injury What happened? Applicable During disconnection of a structure, a securing pin became stuck and could not Life Saving be removed by hand. A hydraulic jack was employed to eject the pin which Rule(s) Bypassing resulted in the pin being released under load directly into someone’s face. A Safety Line of Fire Controls team of four persons were removing a structure. This involved the removal of four securing pins, each weighing around 10kg. The task has been done numerous times and was usually accomplished with a hammer and drift. On this occasion, one of the pins became stuck and could not be removed. The work team decided to use a hydraulic jack to force the pin out. Initially this did not work; one of the workers moved directly into the line of fire to obtain better sight of the restriction. The worker tapped on the adjacent plate with a hammer and the pin came loose and ejected with force, hitting the worker in the face. The pin hit the bridge of the person’s safety glasses causing a laceration to the forehead. They were treated onshore and returned to work soon after the incident. Position of person hit by pin (yellow dot) Size and weight of pin What went wrong The task risk assessment (TRA) for this task did not consider the use of a hydraulic jack for removal of the pin, nor did the toolbox talk (TBT) before starting work; A change was then made during the task (introduction of the jack), but the new risks were not thought through at all. Nobody in the work team thought to intervene and stop the job due to the change in method and equipment; During the operation of the jack, one person decided to switch positions to get a better view and to try and release the pin. That person got directly into the line of fire. There was significant stored energy now pushing behind the pin and that risk was not recognised. Actions and lessons learned Our member noted that lessons were not being learned from previous incidents involving getting in the line of fire. A fresh review on the line of fire risks was initiated, considering all the potential energy forms, including release of stored energy; If something changes during a task - stop the job, and reassess; IMCA Safety Flash 11/24 Page 5 of 7 Stop and think – take the time to think things through; An engineering solution was proposed to remove the line of fire risk while removing these pins. A proposed design of cages or catchers on each pin was put forward, such that the pins can be controllably released into an area without potential for people to be harmed. Members may wish to refer to: LTI: fractured finger during anchor handling Lacerated chin caused by flying wedge Leg injury when struck by rebounding hammer Finger injury while using a crowbar to try to shift a large shackle High potential stored energy incident: inner buoyancy module clamp failure during removal 5 MAIB: Leg injury while mooring The UK Marine Accident Investigation Branch has published Safety Digest 1/2024, consisting of lessons from recent Marine Accident Reports. IMCA has reviewed the report and passes on to members, as of interest, some of the incidents in the MAIB report. This is one of them. What happened During unmooring operations, a crew person got caught in the bight of a messenger line mooring rope and was injured. The incident occurred when a vessel was being prepared for departure. The worker was on the mooring deck, using a messenger line around the mooring rope to guide it onto a winch drum. Another worker was operating the winch remotely, with limited visibility of the first worker’s position near the drum. The messenger line suddenly snagged under the mooring rope and became wound onto the winch drum itself. Realising what had happened the injured person let go of the messenger line, but was unaware that it had formed a bight around their right leg. As the bight tightened, the injured person was pulled towards the winch drum and then dragged over it. The winch operator promptly stopped the winch. The injured person was disentangled from the messenger line and immediately taken ashore for medical treatment for a broken shin bone and other leg injuries. Winch drum Injured person IMCA Safety Flash 11/24 Page 6 of 7 What went wrong The long messenger line used to guide the mooring rope was able to reach the deck and wrap itself around the worker's leg, leading to the incident; The winch drum operator did not have clear “line of sight” to where the injured person was working. Lessons The MAIB noted: Exercise caution around moving machinery – maintain a safe distance; Avoid getting too close to rotating equipment and ensure that loose clothing or any objects that can become caught in it are kept clear; When operating equipment remotely, it is crucial to have clear visibility of the people and surroundings involved. Whilst remote control allows operators to move around the deck while operating machinery from a safe distance, such as outside snapback zones and clear of suspended loads, it is important to maintain a line of sight to monitor the working area effectively and to be able to communicate with colleagues to prevent incidents and respond promptly to any potential issues. Members may wish to refer to: Lost time injury (LTI): Crewman injured foot during offshore renewables mooring operation LTI: foot injury after standing on rotating winch drum IMCA Safety Flash 11/24 Page 7 of 7