Maintenance Manual AC DC EMU (Siemens) PDF
Document Details
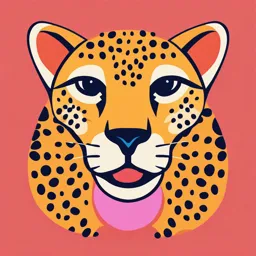
Uploaded by SolicitousOklahomaCity
null
Tags
Related
- Aterramiento de Trenes Alstom – 6 Coches PDF
- Aterramiento de Trenes Alstom – 6 Coches (UNNA-L1ML-MTO-INS-0101) PDF
- Mantenimiento Preventivo R1 Bajo Bastidor - Tren Alstom Ver00 PDF
- Maintenance Manual AC DC EMU (Siemens) PDF
- CH 17 Section 3 PDF - Train Detection Track Circuits
- Chapter 17 Train Detection Track Circuits & Axle Counters PDF
Summary
This document provides a comprehensive maintenance manual for an AC/DC EMU train using Siemens equipment. It details the various components, abbreviations, and procedures for the upkeep of the train. The document includes diagrams, charts, and diagrams of systems within the train.
Full Transcript
CAMTECH/E/13-14/MM AC-DC EMU/1.0 1 CHAPTER 1 GENERAL DESCRIPTION 1.0 INTRODUCTION The AC-DC EMU (Electrical Multiple Unit) is a newly designed t...
CAMTECH/E/13-14/MM AC-DC EMU/1.0 1 CHAPTER 1 GENERAL DESCRIPTION 1.0 INTRODUCTION The AC-DC EMU (Electrical Multiple Unit) is a newly designed train equipped with state-of-art IGBT control technology. These trains are especially designed for running over DC as well as AC territory in Mumbai sub-urban area to cater growing demand of passenger traffic. These vehicles are equipped with a driver’s friendly diagnostic display (MMI) unit. This Maintenance Manual for AC-DC EMU (Siemens Rake) is prepared for the use and reference for maintenance staff of EMU Car Sheds and Workshops. Maintenance and overhauling procedures of various electrical, mechanical equipment and all other accessories of Siemens Rake are briefly described in this manual. 1.1 ABBREVIATIONS ACU - Auxiliary Control Unit ADC/COS - AC/DC Changeover Switch AFB - Automatic Traction/ Brake Control (Cruise Control AM - Shut Off Valve (Parking Brake Circuit) AWS - Auxiliary Warning System BCU - Brake Control Unit BW - Braking Resister CCU - Central Control Unit DCS - Driver’s control switch (Master key) DM - Diagnostic Message DTC Driving Trailer Coach EBU - End Basic Unit EBL - Emergency Brake Loop ES - Electronic Cabinet FML - Traction Motor Fan GTO - Gate Turn Off Thyristor HB - Main Air Compressor HBL - Main MR Pipe HL - Main Brake Pipe HSCB - High Speed Circuit Breaker HTC - High Tension Compartment IGBT - Insulated Gate Bi-Polar Transistor MBU - Middle Basic Unit MMI - Man Machine Interface MPS - Motor protective switch MS - Main Switch Maintenance Manual for AC-DC EMU (Siemens) Chapter 1 2 CAMTECH/E/13-14/MM AC-DC EMU/1.0 MVB - Multi Vehicle Bus NDTC - Non Driving Trailer Coach PBC - Power brake controller PIS - Passenger Information System PT - Potential Transformer PTS - Position of Train System RDM - Rescue Drive Mode SB - Signal Bell SC - Shunting Cab SIBAS - Siemens Bahn Automatisierungs System SKS - SIBAS KLIP Station. SW - Software TCC - Traction converter cabinet TCU - Traction Control Unit VCB - Vacuum Circuit Breaker VSD - Voltage Sensing Device VVVF - Variable Voltage Variable Frequency 1.2 THREE-PHASE TECHNOLOGY The vehicle is equipped with a state-of-the-art three-phase drive with asynchronous motor. The advantages over direct current drives are as follows: Smooth (Step-less) acceleration. Reduced weight Wear-resistant drives hence less maintenance and high level of reliability as no wearable part like carbon brushes and commutator. Good starting properties High tractive force over the whole speed range Wear-free regenerative brake for reduced maintenance, increased wheel and other mechanical component life and energy conservation as well Easy starting even on gradients The stator winding of the asynchronous motor consists of coils, which are electrically offset by 120°. If these are connected to a three-phase network, they generate a rotating magnetic field, also known as rotating field. The rotor consists of one winding which is designed with rods whose ends are short-circuited by means of rings. This kind of rotor is therefore called short-circuit rotor. A rotating magnetic field induces an electromagnetic force into the rotor winding. The electric circuit of the short-circuit rotor is always closed, thus creating a current flow which generates another magnetic field (rotor magnetic field). The rotor magnetic field attempts to catch up with the rotating field in the process. If the rotor rotates faster than the rotating magnetic field, the engine automatically switches into braking mode. This means that by changing the voltage and the frequency, the output (torque) and the speed (number of revolutions per minute) can be altered. The frequencies and the voltages are Chapter 1 Maintenance Manual for AC DC EMU (Siemens) CAMTECH/E/13-14/MM AC-DC EMU/1.0 3 generated in the current converter. The main components are the four-quadrant converter, the intermediate circuit and the pulse width modulation inverter. In DC mode, the voltage is fed into the intermediate circuit via a line filter. The transformer and the four-quadrant converter are therefore not required. After an automatic commutation from AC to DC, the transformer cooling is automatically switched off. In braking mode, the vehicle can feed the generated energy back into the contact line network. This is only possible if the network is able to receive the generated energy. If the network is not able to do this, the pneumatic brake is activated. 1.3 CONTROL TECHNOLOGY There are two Central Control Units called CCU. These are located in the driver's cab. Apart from the control of the entire train, the CCU also controls the display. The vehicles of one unit and the units themselves are connected to each other via an MVB bus. The MVB is designed redundantly with line A and line B. If the MVB bus is not available despite of this fallback, the vehicle can be operated in degraded operation via the rescue drive mode. This function is only used for clearing the track. In this operating mode, the display is switched off and the auxiliary tell-tale lamps are switched on. All switches, buttons and devices which are controlled via the control technology are connected to a KLIP station. 1.4 DISPLAY SUPPORT The MMI (Man-Machine Interface) is installed in the driver's cab in the DTC and informs the driver of the current state of all important functions in the train. The states of functions are indicated to the driver by means of coloured icons. The driver can detect faults at a glance. The display assists the driver during the subsequent error detection. For information on further actions, the driver can call up the corresponding remedy for the error message. Automatic vigilance device has been implemented via the master controller. If the driver releases the vigilance monitoring button during the journey, the brakes are applied automatically and the power of the train is switched off. This only happens during the journey. If the speed is below 5 km/h, this function is disabled. In rescue drive mode, the automatic application of the brakes is immediately initiated even if the vigilance monitoring switch is not actuated and if the speed is below 5 km/h. 1.5 AUXILIARY EQUIPMENT The three-phase auxiliary equipment are supplied by an auxiliary inverter. The inverter for auxiliary equipment generates the following voltages: 415 Volt AC for fans / main air compressor and pumps 110 Volt AC for passenger compartment fans and lighting 110 Volt DC for the auxiliary air compressor, plugs, battery bus bar, instrument and emergency lighting. The inverter for auxiliary equipment supplies the three-phase components with a fixed frequency (50Hz) and voltage. The auxiliary equipment is connected by means of contactors. Maintenance Manual for AC-DC EMU (Siemens) Chapter 1 4 CAMTECH/E/13-14/MM AC-DC EMU/1.0 1.6 UNIT & RAKE FORMATION OF EMU There are two types of basic units o End basic unit o Middle basic unit. 1.6.1 End Basic Unit It consists of three coaches viz. Motor Coach (MC) Driving Trailer coach (DTC) Trailer Coach (TC) Figure 1 : End Basic Unit Motor-Coach This is the coach responsible for the movement of the EMU as desired by the driver command. This consists of propulsion equipment viz. transformer, traction motor, traction converters, (Four quadrant chopper), PWM inverters, brake chopper etc. Driving Trailer Coach This is non-powered coach with facilities for driving. These coaches are equipped with Master/ Brake Controller, Drivers Desk, Passenger Information System, Light & Fans etc. Trailer Coach This is also non-powered coach but without Drivers desk. Passenger Information System and Light & Fans are provided in this coach. 1.6.2 Middle Basic Unit It consists of three coaches viz. Motor Coach (MC) Non Driving Trailer coach (NDTC) Trailer Coach (TC) Figure 2 : Middle Basic Unit Non Driving Trailer Coach This is non-powered coach without facilities for driving. These coaches are equipped with Light & Fans etc. Chapter 1 Maintenance Manual for AC DC EMU (Siemens) CAMTECH/E/13-14/MM AC-DC EMU/1.0 5 1.6.3 Train Formation For the EMU, following train formations are possible: (i) Nine Car Rake : It comprises of 3 basic units Figure 3: Nine Car Rake (ii) Twelve Car Rake : It comprises of 4 basic units Figure 4: Twelve Car Rake (iii) Fifteen Car Rake : It comprises of 5 basic units (Only in WR) Figure 5: Fifteen Car Rake 1.7 MAJOR EQUIPMENT OF DTC 1.7.1 Driving Cab Figure 6: Driving cab 1 Side panel left + RDM signal lights 7 Speedometer 2 Signal lights 8 Radio /PIS panel 3 Display, MMI 9 Side panel right 4 Pressure panel 10 Pneumatic control valve (master brake controller) 5 Key switch and master controller 11 Wiper valve 6 Power brake controller 12 Horn valve Maintenance Manual for AC-DC EMU (Siemens) Chapter 1 6 CAMTECH/E/13-14/MM AC-DC EMU/1.0 1.7.1.1 Driving Desk a. Brake controller b. Master controller c. Left hand side panel for push buttons, rotary switches and indications. d. MMI e. Different gauges f. PIS g. TMS (Train management system) h. Foot operated valve for hooter i. AWS indication panel j. Analog speedometer k. ESMON l. SIBAS KLIP Station (12 & 13) m. Cocks for AWS 1.7.1.2 Guard’s Desk a. Brake pipe pressure gauge b. Panel for push buttons 1.7.1.3 Electronic Cabinet a. CCU b. Push buttons c. Rotary switches d. MCBs (1st layer & 2nd layer) 1.7.1.4 Driving Cab Front View a. Head Light b. Flasher Light c. Tail light d. Blinker e. Marker light f. Electronic head code g. Look out glass h. Cattle guard i. Buffer & couplers Figure 7 : Driving Cab Front View 1.7.1.5 Panel in Passenger Area of DTC a. SIBAS KLIP Station (11) b. Different rotary switches MCBs, MPS for MCP, Ventilation fans, light & fans for passengers. Chapter 1 Maintenance Manual for AC DC EMU (Siemens) CAMTECH/E/13-14/MM AC-DC EMU/1.0 7 1.7.1.6 Roof Equipment: a. Ventilation fans 1.7.1.7 Under-frame Equipment a. Main compressor b. Battery box c. Different reservoirs d. Combined brake unit e. Parking brake equipment f. Air suspension equipment g. Mechanical weight transfer equipment 1.7.2 Indication Panels 1.7.2.1 Control Elements in the Driver's Desk on the Left-Hand Side Figure 8: Control Elements in the Driver's Desk on the Left-Hand Side 1. Mounting Plate 11. SB I (Signal Bell) 2. Flasher Push Button 12. Emergency Brake 3. Head Light Main / Auxiliary. 13. Emergency Off 4. Head Light On / Off 14. RDM Active 5. Audio visual push button 15. Fire Alarm 6. SB II Alarm bell (HW) 16. Spare 7. Head Light Bright / Dim 17. Minimum 1 Brake applied 8. Fire Alarm (Buzzer 18. Minimum 1 Panto up 9. Audio Visual (Buzzer) 19. Minimum 1 CB On 10. AWS vigilance 20. Lamp Test Driver A. All switches/push buttons on this panel have metallic border B. All indications on this panel have black border Maintenance Manual for AC-DC EMU (Siemens) Chapter 1 8 CAMTECH/E/13-14/MM AC-DC EMU/1.0 1.7.2.2 Auxiliary Tell-Tale Lamps Figure 9: Auxiliary Tell-Tale Lamps A1 Not all Pantos up B1 Emergency brake A2 Not all main switches on B2 Emergency OFF A3 Spare B3 Spare A4 Min. 1 brake applied B4 Fire Alarm A5 Spare B5 Spare A6 Spare B6 Spare A7 Spare B7 Spare 1.7.2.3 Pressure Panel Figure 10: Pressure Panel 1. Brake Cylinder Gauge 2. MR/BP/Duplex Gauge 3. Panto Up / Down 4. Main Circuit Breaker On / Off 5. Cruise Control 6. Neutral Section Push Button Chapter 1 Maintenance Manual for AC DC EMU (Siemens) CAMTECH/E/13-14/MM AC-DC EMU/1.0 9 1.7.2.4 Man Machine Interface (General View) Figure 11: Man Machine Interface (General View) 1 Display ON / OFF 2 Not Connected 3 Legends of Symbols (Meaning) 4 Event Overview 5 Trouble Shooting Guidelines for Motorman 6 Not Connected 7 Brightness Control Dialog 8 Not Connected 9 Not Connected 10 Clear 11 Cursor Up 12 Cursor Down 13 Curser Left 14 Curser Right 15 Enter 16 to 25 Soft keys 0 to 9 Maintenance Manual for AC-DC EMU (Siemens) Chapter 1 10 CAMTECH/E/13-14/MM AC-DC EMU/1.0 1.7.2.5 Train Radio and Passenger Information System Figure 12: Train Radio and Passenger Information System 1.7.2.6 Control elements in the driver's desk on the right-hand side Figure 12: Control elements in the driver's desk on the right-hand side 1 Mounting plate 2 Cab tube light for driver 3 Cab spot light for driver 4 Cab emergency light for driver 5 Cab fan for driver 6 Parking brake release 7 Parking brake apply 8 PIS release button for microphone 9 PIS Microphone Chapter 1 Maintenance Manual for AC DC EMU (Siemens) CAMTECH/E/13-14/MM AC-DC EMU/1.0 11 1.7.2.7 Guard Panel Right-Hand Side Figure 13: Guard Panel Right-Hand Side 1 Mounting Plate 2 Ventilation Release Off 3 Fan Release Off 4 Spare 5 Train Light 100 % Off 10 Flasher Light On / Off (Guard) 11 Tail Light On / Off 12 SB I Signal Bell (Guard) SW 13 SB II Alarm Bell (Guard) HW 18 Spare 19 Spare 20 Spare 21 Train Light 50 % Off 26 Cab Spot Light (Guard) 27 Cab Tube Light (Guard) 28 Cab Fan (Guard) 29 Lamp Test Maintenance Manual for AC-DC EMU (Siemens) Chapter 1 12 CAMTECH/E/13-14/MM AC-DC EMU/1.0 1.7.3 Electronics Cabinet DTC 1.7.3.1 Level 1 Figure 14: Electronics Cabinet DTC level 1 Chapter 1 Maintenance Manual for AC DC EMU (Siemens) CAMTECH/E/13-14/MM AC-DC EMU/1.0 13 1.7.3.2 Level 2 Figure 15: Electronics Cabinet DTC level 2 Maintenance Manual for AC-DC EMU (Siemens) Chapter 1 14 CAMTECH/E/13-14/MM AC-DC EMU/1.0 1.8 MAJOR EQUIPMENT OF MOTOR COACH 1.8.1 Shunting Cab 1.8.1.1 Shunting Desk a. Brake controller b. Master controller c. Shunting desk, rotary switches and indications. d. Different gauges e. Foot operated valve for hooter f. SIBAS KLIP Station (21) g. Shunting desk control panel Figure 16: Shunting Desk 1 Mounting Plate 11 Lamp Test 2 Panto is Up 12 Parking Brake Released 3 MC is On 13 Panto Up / Down 4 OHE is available 14 Main Switch On / Off 5 Emergency Brake 15 HTC Tube 6 Min. 1 Brake Applied 16 HTC Fan 7 Summary Fault 17 Battery Volt Meter 8 Cab Tube Light 18 Test battery Voltage 9 Cab Emergency Light 19 Parking Brake Applied 10 Cab Fan 20 Start Extinguish Fire 1.8.1.2 Electronic Cabinet a. DC earthing switch b. Push buttons c. Rotary switches d. MCBs Chapter 1 Maintenance Manual for AC DC EMU (Siemens) CAMTECH/E/13-14/MM AC-DC EMU/1.0 15 1.8.2 HT Compartment a. TCC i. AC-DC converter (4Quadrant Chopper) ii. DC-AC converter (Pulse width modulated inverter) iii. Traction Control Unit iv. Converter cooling blowers v. Various contactors and relays vi. Voltage & current sensors b. Electronic Cabinet: Brake Electronics Control Unit (BECU) Electronics cabinet MC (top) Figure 17: Electronics cabinet MC (top) Maintenance Manual for AC-DC EMU (Siemens) Chapter 1 16 CAMTECH/E/13-14/MM AC-DC EMU/1.0 Electronics cabinet MC (bottom) Figure 18: Electronics cabinet MC (bottom) c. Aux. converter unit d. Aux. compressor e. HSCB f. VSD Chapter 1 Maintenance Manual for AC DC EMU (Siemens) CAMTECH/E/13-14/MM AC-DC EMU/1.0 17 1.8.3 Roof Equipment a. Pantograph b. Surge Arrestor c. AC-DC change over switch d. Brake resister e. PT f. HVCB g. CT h. Ventilation fans 1.8.4 Under Frame Equipment a. Traction Motors b. Traction Transformer c. Different reservoirs d. Combined brake unit e. Air suspension equipment f. Mechanical weight transfer equipment 1.8.5 Panel in Passenger Area of Motor Coach a. SIBAS KLIP Station (21) b. Different rotary switches, MCBs, MPS for, Ventilation fans, light & fans for passengers. 1.9 ELECTRICAL EQUIPMENT IN MOTOR COACH 1.9.1 Pre-Charging AC Contactor This is AC contactor working under AC OHE supply. The traction transformer has two secondary windings. This contactor is connected in one of the circuit. One resistor is connected across the HT contact of the pre-charging AC contactor. Initially this contactor remains open, keeping pre-charging resistor in power circuit of four quadrant chopper module. As a result, initial inrush of charging current for DC link is reduced considerably which ensures the safety of semiconductor devices of the four quadrant chopper module. 1.9.2 Pre-Charging DC Contactor This is DC contactor working under DC OHE supply. Its function is to connect the equipment to power supply under DC condition. One resistor is connected across the HT contact of the pre-charging DC contactor. Initially this contactor remains open, keeping pre-charging resistor in power circuit of DC link. As a result, initial inrush of charging current for DC link is reduced considerably which ensures the safety of semiconductor devices in the HT circuit. Maintenance Manual for AC-DC EMU (Siemens) Chapter 1 18 CAMTECH/E/13-14/MM AC-DC EMU/1.0 1.9.3 Traction Converter Cubical The traction converter cubicle is a completely assembled unit installed in the HT compartment of the motor coach. The traction control unit (TCU) is situated inside the cabinet. It consists following modules: i. Four Quadrant Chopper Module (4 QC) ii. Pulse Width Modulated Inverter iii. Brake Chopper 1.9.4 Earth Fault Detector It is connected across the circuit of 4-QC module for protection of 4-QC module against the Earth Fault in AC side i.e. Transformer side of the HT circuit. 1.9.5 Line Filter This is an inductor connected in series with DC link capacitor. This is LC (resonance) circuit to suppress the harmonics or ripples of DC supply to obtain pure DC supply across the DC link. 1.9.6 Auxiliary Converter Unit Auxiliary converter unit basically consists of two PWM inverter modules with two primary windings. Input supply for inverter modules is obtained from DC bus-link. There are three different secondary windings for different purposes. i. Three Phase AC 415V 50Hz Output One secondary of auxiliary converter having 3 Ø AC, 415V, 50 Hz (121A/ 87kVA) supply is used for Main compressor & other auxiliaries. ii. Single Phase 110V AC 50 Hz Output One secondary of auxiliary converter having 1Ø AC, 110V (20 kVA) supply is used for light & fans in the passenger compartment. One tapping is taken out for redundancy lines of supply for adjacent units. iii. DC 110 V Output One secondary of auxiliary converter having 3 Ø AC supply for battery charging equipment is used. Battery having 110 V DC supply is connected across this battery charging equipment to charge continuously. This 110 V DC supply is used for control supply as well as for emergency light supply when normal light & fan supply of 110 V AC is failed due to any reason. 1.9.7 Pantograph (Type Am-1882) It is provided to collect H.T. Supply from OHE contact wire. The OHE supply may be 1500 VDC or 25 KV AC, 50Hz. This is fitted on foot insulator on the top of the roof of the motor coach. 1.9.8 Surge Arrestor It is provided on the top of the roof of the motor coach to protect the coach from lightening. Chapter 1 Maintenance Manual for AC DC EMU (Siemens) CAMTECH/E/13-14/MM AC-DC EMU/1.0 19 1.9.9 Line Voltage Transformer It is provided on the roof of the motor coach. It is a step down transformer for voltage sensing (AC or DC) 1.9.10 Line Current Transformer It is provided on the roof of the motor coach. It senses the current through primary winding of traction transformer. It provides over current protection by opening VCB. 1.9.11 Voltage Sensing Device The voltage sensing device is provided to sense whether the OHE supply is AC or DC. 1.9.12 Change Over Switch AC/DC It is provided on the roof of the motor coach. It is an air operated switch with two positions i.e. AC and DC. Default position of the switch is AC. It changes its position to either AC or DC depending upon the OHE voltage. 1.9.13 Braking Resister Rs 25.10 1.9.14 High Voltage AC Circuit Breaker (HVCB) This is an air operated single pole AC circuit breaker. It is used as a line circuit breaker to open/ close the power circuit and also to break the circuit under overload and short circuit conditions. It is provided on the roof of the motor coach. 1.9.15 High Speed Dc Circuit Breaker This circuit breaker works under DC catenaries. 1.9.16 AC Earthing Switch It is provided across the VCB. During off position of VCB it is connected to Earth primary side of the traction transformer while opening H.T. compartment. 1.9.17 DC Earthing Switch It is provided across the HSCB. During off position of HSCB it is connected to Earth DC link while opening H.T. compartment. 1.9.18 Surge Arrestor AC These are two in numbers. It is provided on the roof of the motor coach to arrest AC surges during AC operation. 1.9.19 Surge Arrestor DC It is provided on the roof of the motor coach to arrest DC surges during DC operation. Maintenance Manual for AC-DC EMU (Siemens) Chapter 1 20 CAMTECH/E/13-14/MM AC-DC EMU/1.0 1.9.20 Traction Motors Four number of traction motors are provided in one motor coach. Two pairs of traction motors are connected across two different PWM inverters. 1.9.21 Traction Transformer The transformer is designed for a nominal rating of 1250 kVA. It consists of a primary winding and 2 secondary windings. Therefore, 625 kVA is available at each secondary. This corresponds to a secondary side nominal current of 731 A at a secondary voltage of 855 Volt (22.5 kV mains voltage). 1.10 TRAILER COACH 1.10.1 Panel in Passenger Area of TC a. SIBAS KLIP Station (31) b. Different rotary switches, MCBs, MPS for Ventilation fans, light & fans for passengers. 1.10.2 Roof Equipment Ventilation fans 1.10.3 Under Frame Equipment a. Different reservoirs b. Combined brake unit c. Air suspension equipment d. Mechanical weight transfer equipment 1.11 NON DRIVING TRAILER COACH 1.11.1 Panel in Passenger Area of NDTC a. SIBAS KLIP Station (41) b. Different rotary switches, MCBs, MPS for MCP, Ventilation fans, light & fans for passengers. 1.11.2 Roof Equipment Ventilation fans 1.11.3 Under Frame Equipment a. Main compressor b. Battery box c. Different reservoirs d. Combined brake unit e. Parking brake equipment f. Air suspension equipment g. Mechanical weight transfer equipment Chapter 1 Maintenance Manual for AC DC EMU (Siemens) CAMTECH/E/13-14/MM AC-DC EMU/1.0 21 1.12 TRANSDUCERS AND SENSORS Transducers are the equipment which are utilised for converting the electrical or mechanical quantities into suitable electrical signals so that these signals can be processed by the control electronics for efficient control of the system. Following transducers and sensors are used in Siemens AC-DC EMU: a. Voltage transducer b. current transducer c. pressure transducer d. speed sensor e. oil flow sensor f. oil level sensor 1.13 BRIEF DESCRIPTION OF HT POWER CIRCUIT The pantograph receives the supply voltage of either 25 kV catenary or 1500 V DC catenary. The detection of AC or DC voltage is achieved through voltage sensing device which includes PT (potential transformer) for AC voltage detection & in series resistors for DC voltage detection. In case of AC voltage detection or no voltage detection, changeover switch AC/DC remains in the AC position thus connecting VCB (Vacuum circuit breaker) to the pantograph. This is a failsafe method of protecting the DC equipment against high voltage AC. For DC catenary, changeover switch AC/DC moves to DC position connecting HSCB (High speed circuit breaker) to pantograph. A spark gap lightening arrestor is mounted directly on the pantograph to protect the complete circuit from extreme over voltages. The VCB is the main circuit breaker in case of AC catenary & the HSCB acts as the same for DC catenary. Each motor coach is equipped with a main transformer. The main transformer converts the 25 KV overhead line voltages to lower operating voltages. There are two secondary windings each of 950V (corresponding to 25 kV), 625 kVA. The transformer is oil cooled. For AC catenary, as the VCB closes, the main transformer steps down the voltage & feed the 4-QC (Four Quadrant Chopper Module) through two secondary winding of 950 V each (corresponding to a ratio of 25 kV/ 950 V). The initial charging of the 4-QC is done through a pre-charging resistor (AC) which is in series with secondary winding-1 of the main transformer. Once the voltage at the 4-QC output is build up to certain voltage level of DC using rectification process, the contactor across the pre-charging resistor are closed & the 4-QC builds up a fixed voltage of 1800 V DC to feed the PWM inverter & the auxiliary converter through DC link capacitor. Main functions of 4-QC’s are to maintain a fixed DC voltage at its output irrespective of the catenary voltage variations & to maintain a near unity power factor for the current consumed from or fed back to the AC catenary. It achieves these functions through two pairs of IGBT based modules. An LC filter circuit is provided at the output of the 4-QC, to filter out the second harmonic components from the rectified voltage & smoothen the DC link voltage. Maintenance Manual for AC-DC EMU (Siemens) Chapter 1 22 CAMTECH/E/13-14/MM AC-DC EMU/1.0 Figure 19: Overview of AC/DC electric circuit Chapter 1 Maintenance Manual for AC DC EMU (Siemens) CAMTECH/E/13-14/MM AC-DC EMU/1.0 23 The AC circuit is protected against surge voltages through gapless surge arrestors (AC). Similarly DC circuit is protected through gapless surge arrestors (DC). For DC catenary, Changeover switch AC/DC is in DC position. As the HSCB closes the DC link capacitor is charged through pre-charging resistor (DC) to avoid heavy inrush current. After some time delay Line Contactor is closed to bypass the pre-charging resistor & the full catenary voltage is applied across the DC link. Fig. 20: Current converter (AC operation) Fig. 21: Current converter (DC operation) Maintenance Manual for AC-DC EMU (Siemens) Chapter 1 24 CAMTECH/E/13-14/MM AC-DC EMU/1.0 Figure 22: Power Circuit Chapter 1 Maintenance Manual for AC DC EMU (Siemens) CAMTECH/E/13-14/MM AC-DC EMU/1.0 25 The function of the PWM inverter is to convert the DC link voltage into a variable 3 ØAC voltage of variable frequency in order to feed the traction motors. This is achieved through IGBT based modules. The voltage & the frequency of the 3 Ø output is determined by the control electronics named SIBAS-32 (Siemens Bahn Automatisierungs System with 32 bit microprocessor) based on the demand. The traction motors are ASM (Asynchronous Motor) or squirrel cage induction motors. Inductor is used for smoothing & makes along with capacitor, a low impedance power source under DC catenary for the inverter & auxiliary converter. Protection resistors are externally connected to the brake chopper for protection. When any serious fault is detected by SIBAS, it turns off all IGBT modules and fires chopper. During this, entire DC link gets discharged through protection resistors. This is only for over voltage protection of the DC link & no full duty braking resistor. There are two Auxiliary Converter modules connected in series. These IGBT based modules convert 1500V/ 1800V DC to 3 Ø, 415 V AC supply. This supply is connected to two independent primary windings of isolation transformer. There are three secondary windings out of which, two are 3Ø, 415 V & one is 1Ø, 110 V AC. One 3 Ø, 415 V AC supply is extended to auxiliary machines which includes main compressor. Another supply of similar voltage is given to battery charging equipment. One battery of 110 V DC supply along with battery charging equipment are provided to extend control supply & emergency light supply. 1Ø, 110V AC supply is extended for normal lights & fans in passenger compartment. The same supply is also extended for redundancy lines to adjacent units. Key data Catenary voltage 25 kV AC 50 Hz and 1.5 kV DC Maximum speed 100 km/h Nominal rating (basic unit) 1100 kW Wheel arrangement 2´ 2´ + Bo´Bo´ + 2´ 2´ Starting effort max. 135 kN (basic unit) Vehicle weight 113.6 t (basic unit) 31.55t – 51.2t – 30.88t Length (basic unit) 63 metres Drive Integrated nose-suspended drive Brake Compressed-air brake / electronic brake unit Stop brake (basic unit) Spring-loaded brake 4 cylinder Dynamic brake Catenary voltage-dependent network and dynamic brake Electric brake force max. (basic unit) 125 kN Brake force max. (basic unit) 185 kN Maintenance Manual for AC-DC EMU (Siemens) Chapter 1 26 CAMTECH/E/13-14/MM AC-DC EMU/1.0 1.14 PANTOGRAPH CONTROL Compressed-air release The compressed air for raising the pantograph is released via the key valve on the rear panel of the shunting cab. If the key valve is closed, the pantograph cannot be raised because the air supply to the lifting cylinders of the pantograph is blocked, irrespective of whether the solenoid valve is activated. If the pantograph is raised and the valve is closed, the air supply line to the lifting cylinders of the pantograph is bled and the pantograph is lowered automatically. Control for raising the pantographs The pantograph can be raised and lowered via a rotary switch in the driver's cab. The pre-requisite for this is a sufficient supply of compressed air in the compressed-air reservoir. If no sufficient compressed air is available, it is generated by the auxiliary air compressor. It is supplied by the battery. The following conditions must be met to raise the pantograph: * MCB switched ON * Control voltage 110 V DC available * Emergency stop switch not activated * A shunting desk or driver's desk occupied / active * Release via TCU * Key valve open * Release via push switch in the auxiliary air circuit Figure 23: Pantograph valve Change of driver's cab In the case of a change of driver's cab, the pantograph may remain raised. The change of driver's cab does not affect the pantograph control. Lowering the pantograph Normally, the pantograph is lowered by means of the "Panto down" rotary switch. In the case of a fault, the pantograph can be lowered via the control unit in order to protect the drive unit. Chapter 1 Maintenance Manual for AC DC EMU (Siemens) CAMTECH/E/13-14/MM AC-DC EMU/1.0 27 MCB Rotary switch approx. 4.2 kg/cm² "Panto" up/down TCU 40 l MCB “Panto/MC) switched on Control voltage 110 V DC available Emergency stop switch not activated A driver's desk occupied / active Release via control technology Key valve open Release via push switch Pushbutton "Panto up" is actuated Lifting time exceeding Emergency stop is operated MCB “Panto/MC)” off Pantograph key valve is closed Panto down via control technology Drop of pressure, pressure below 3.4 kg/cm² Power system not recognised Figure 24: Lowering the pantograph 1.15 MAIN CIRCUIT-BREAKER CONTROL The AC main circuit-breaker, which is operated with compressed air, is located on the roof of the MC, the DC main circuit-breaker in the HTC. Next to the AC main circuit-breaker, there is also the earthing switch. Every unit has a separate AC and DC main circuit-breaker. Control for switching ON the main circuit-breaker The power system on the OHE is detected by the power detection system. Before the main circuit-breaker can be switched ON via the TCU, a test run takes place in the TCU. This check determines whether all requirements for switching ON the main circuit- breaker are met. If all of the requirements for switching ON a main circuit-breaker are fulfilled, this is indicated by a white field and an MC symbol on the display. As a next step, the driver can switch on the correct main circuit-breaker for the detected power system via the "MCB ON" command. In the process, the system selection switch is switched to the AC or DC position by the detected power system. Depending on the position of the system selector switch, the corresponding main circuit-breaker is released for connection and switched ON. In the case of malfunctions as a result of system detection or the system selection switch, the main current components are protected against dangerous overvoltage by means of lightning arresters. Maintenance Manual for AC-DC EMU (Siemens) Chapter 1 28 CAMTECH/E/13-14/MM AC-DC EMU/1.0 Change of driver's cab In the case of a change of driver's cab, the main circuit-breaker may remain switched ON. The change of driver's cab does not affect the main circuit-breaker control. Opening the main circuit-breaker In the event of an emergency, the main circuit-breaker is opened via the rotary switch "MC OFF". In the case of a fault, the main circuit-breaker can be opened via the control unit in order to protect the drive unit. MCB Rotary switch TCU MC on/off Requirements for switching on the main circuit-breaker MCB “Panto/MC” switched on Control voltage 110 V DC available A driver's desk occupied / active Emergency stop switch not activated Release via control technology (ACU / TCU) Correct position of the COS (AC / DC) The main circuit-breaker of the other power system is switched off Requirements for switching off the main circuit-breaker Pushbutton "MC off" is actuated Emergency stop is operated MCB “Panto/MC” off Pushbutton "Panto down" is actuated Main circuit-breaker off via control technology (TCU / ACU) Drop of pressure, pressure below 3.4 kg/cm² Catenary voltage < 16 kV & > 30 kV (AC) / < 0.75 kV & 2.0 kV (DC) Overhead current > 200A (AC) / 1200 A (DC) Figure 25: Requirements for switching on the main circuit-breaker 1.16 EARTHING SWITCH It has to be ensured that the earthing switch is only actuated after the main circuit- breaker has been switched OFF and the pantograph has been lowered. The earthing switch short-circuits the main circuit-breaker directly with the chassis of the vehicle. Chapter 1 Maintenance Manual for AC DC EMU (Siemens) CAMTECH/E/13-14/MM AC-DC EMU/1.0 29 1.17 EARTHING Key concept for connecting the basic units to earth: Prior to opening the HTC, the basic units have to be connected to earth. For personal protection, always follow the procedure described below: Opening the door to the HTC with the green key Secure vehicles against un-intentional movement Switch OFF the main circuit-breaker Lower pantograph Remove the key for the pantograph (blue) Visual check ensuring that the pantograph of the unit to be connected to earth has been Figure 26: Lock to HTC lowered Use the blue key to connect the AC main circuit-breaker to earth and remove the yellow key Use the yellow key to connect the current converter and the DC main circuit- breaker and remove the green key Use the green key to open the door to the HTC Please take good care of the keys as these are the only one which fit here. To disconnect the basic units from earth, proceed in reverse order. Figure 27: Earthing switch, AC Figure 28: Earthing switch, DC main circuit-breaker main circuit-breaker Maintenance Manual for AC-DC EMU (Siemens) Chapter 1