Lesson 4: Production Planning and Control PDF
Document Details
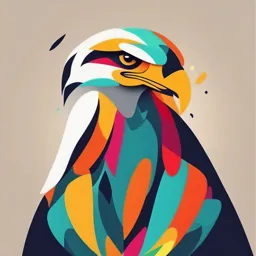
Uploaded by AmazingJudgment1963
Roselyn O. Ragas
Tags
Summary
This document provides an overview of production planning and control, covering topics such as objectives, types of planning (e.g., master production schedule, materials requirement planning), and the importance of workflow planning and capacity planning. It also explains the function and objectives of production control, and includes detailed guidance on different types of production and quality control.
Full Transcript
Lesson 4: PRODUCTION PLANNING AND CONTROL Prepared by: Roselyn O. Ragas Subject In-charge PRODUCTION PLANNING Production Planning involves management decisions on the resources that the firm will require for its manufacturing operations and the s...
Lesson 4: PRODUCTION PLANNING AND CONTROL Prepared by: Roselyn O. Ragas Subject In-charge PRODUCTION PLANNING Production Planning involves management decisions on the resources that the firm will require for its manufacturing operations and the selection of these resources to produce the desired goods at the appropriate time and at the least possible cost. OBJECTIVES OF PRODUCTION PLANNING 1. To determine the workforce, material and equipment requirements. 2. To arrange production schedules based on marketing demand. 3. To arrange various inputs at a right time and in right quantity. 4. Making most economical use of various inputs. 5. To achieve coordination among various departments relating to production. 6. To make all arrangements to remove possible obstacles in the way of smooth production. OBJECTIVES OF PRODUCTION PLANNING 7. To achieve economy in production cost and time. 8. To operate plant at planned level of efficiency. 9. Making efforts to achieve production targets in time. 10. Providing for adequate stocks for meeting contingencies Types of Production Planning 1. Master Production Schedule It is a plan that tells when the production will begin for what products, at what time, and in what quantities. The purpose of which is to create a realistic plan to ensure on-time delivery of goods while minimizing overstock. 2. Materials Requirement Planning Material requirement planning ensures availability of raw materials, maintains the lowest possible stock level, promotes inventory control, and helps plan purchasing activities. Types of Production Planning 3. Capacity Planning Capacity planning is the process of determining the production capacity needed by the organization to meet customers’ orders and changing demand for the product. It aims to strike a balance between expenses and resources as well as demand and supply. 4. Workflow Planning Workflow planning is planning a sequence of operations performed during the production process. It allows you to track each item’s work and see who is responsible for the task and its completion - workflow planning helps check the status of the task. PRODUCTION CONTROL ✓Production control guides and directs flow of production so that products are manufactured in a best way and conform to a planned schedule and are of the right quality. ✓"Production control refers to ensuring that all which occurs is in accordance with the rules established and instructions issued.“ -HENRY FAYOL OBJECTIVES OF PRODUCTION CONTROL 1. To implement production plans by issuing orders to those who are supposed to implement them. 2. To ensure that all inputs are available in the required quantity and quality. 3. Making efforts to adhere to the production schedules. 4. To ensure that goods are produced according to the prescribed standards and quality norms. 5. To undertake the best and most economic production policies. 6. To introduce a proper system of quality control. 7. To ensure rapid turnover of production and minimizing of inventories of raw materials and finished products PRODUCTION PLANNING AND CONTROL "Production Planning and Control is the coordination of series of functions according to a plan which will economically utilize the plant facilities and regulate the orderly movement of goods through the entire manufacturing cycle from the procurement of all materials to the shipping of finished goods at a predetermined rate." -CHARLES A. KOEPKE The main goal of production planning and control is to maximize the materials, workforce, productivity time, and other resources used in the process of manufacturing. CHARACTERISTICS OF PRODUCTION PLANNING AND CONTROL 1. It is the planning and control of manufacturing process in an enterprise. 2. Questions like-what is to be manufactured? when it is to be manufactured? And the like 3. All types of inputs are efficiently used for maintaining efficiency of manufacturing process. 4. Various factors of production are integrated to use them efficiently and economically. 5. The manufacturing process is organized in such a way that none of the work centers is either overworked or under worked. 6. The work is regulated from the first stage of procuring raw materials to the stage of finished goods. Benefits of Production Planning and Control 1. Enhance Material Procurement – Proper production planning and control leads to accurate sourcing and allocation of materials. 2. Improve Production Time – Proactively identify possible challenges, bottlenecks, or causes of production delays ahead of time to ensure production schedules and demands are met. 3. Reduce Production Costs – A well-planned and constantly- monitored production, results to the efficient and effective use of resources. Benefits of Production Planning and Control 4. Minimize resource waste – Maintain inventory at optimal levels. Discrepancies between material supply and material demand avoided to minimize/avoid waste of resources. 5. Streamline production process –Following a standardized approach in the production process facilitates spotting of inefficiencies, prevent production delays, and identify further opportunities for growth. Limitations of Production Planning and Control 1. Based on Assumptions: Production planning and control is based on certain assumptions. In case the assumptions are proven correct then the planning and control will go smoothly, otherwise it may not. 2. Rigidity: Under production planning and control the things are pre-decided and fixed. There is rigidity in the behavior of employees and it may not help in smoothening the flow of work. 3. Difficult for Small Firms: This process is time consuming and costly for small firms. Limitations of Production Planning and Control 4. Costly: It is a costly device as its implementation requires separate persons to perform the functions of planning, dispatching, expediting etc. Small firms cannot use the services of specialists due to cost factor. 5. Dependence on External Factors: - The external factors (natural calamities, change in technology, change in fashion, breakdown of power, government controls etc. ) reduces the effectiveness of production planning and control. Eight Steps in Production Planning and Control 1. Planning As the first step of the process, planning states all the materials, manpower, manufacturing techniques, resources, and other initial details needed to complete the production. This helps strengthen the production approach from the beginning to avoid misuse of resources or miscommunication in manufacturing schedules. Eight Steps in Production Planning and Control 2. Routing Routing determines the path of goods starting from raw materials up to finished products. It specifies the most efficient sequence of the operations and also identifies the machines to be used in each step of production. Routing ensures that the process is continuous by indicating whether a machine is unavailable, or if there are other bottlenecks in the production. Eight Steps in Production Planning and Control 3. Scheduling As the time element of production planning and control — scheduling states all the production elements that are related to timing or schedules. It assist in arranging the manufacturing steps in order of priority and ideally include the start and end times of each production task. Eight Steps in Production Planning and Control 4. Loading Loading is the process of determining the ideal allocation of workload to employees and to machines used, in accordance with their capacity. Eight Steps in Production Planning and Control 5. Dispatching Dispatching is the implementation of all the plans stated in the previously mentioned steps, into actual production. It can be classified as either Centralized — where orders are provided by a specific authority; or Decentralized — where instructions are issued by all involved business units. Eight Steps in Production Planning and Control 6. Expediting Also known as follow-up, expediting is designed to evaluate the effectiveness of the whole production process. The main goal of expediting is to compare the initial plans against the actual result of productions. Eight Steps in Production Planning and Control 7. Inspection Similar to expediting or follow-up, inspection is an extra step performed to ensure that all the planning and controlling approaches identified by the management are consistently implemented and adhered to. Regular or random inspections also help strengthen the reputation of businesses by guaranteeing the quality of goods and services produced by the company. Eight Steps in Production Planning and Control 8. Correction Once the above-mentioned steps are performed and there are issues or areas for improvement that were identified, this is the step where they can be modified. Correction enables businesses to further enhance their production process and implement planning and control techniques in a more efficient manner.