Health & Safety in Construction PDF
Document Details
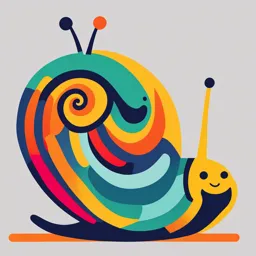
Uploaded by IntuitiveCurl
2006
Stephen Williams
Tags
Summary
This document is a guide to health and safety in construction published by the Health and Safety Executive (HSE). It covers planning, site setup, construction-phase health and safety, and management. It focuses on common causes of accidents and ill health in construction, such as falls, mobile plant, and electrical accidents.
Full Transcript
Health and Safety Executive Health and safety in construction This is a free-to-download, web-friendly version of HSG150 (Third edition, published 2006). This version has been adapted for online...
Health and Safety Executive Health and safety in construction This is a free-to-download, web-friendly version of HSG150 (Third edition, published 2006). This version has been adapted for online use from HSE’s current printed version. You can buy the book at www.hsebooks.co.uk and most good bookshops. ISBN 978 0 7176 6182 2 Price £10.95 This is the third edition of Health and safety in construction. It has been updated and expanded in the light of new legislation, in particular the Work at Height Regulations 2005. It also features new information on recent advances and examples of good practice in the construction industry. This book is aimed at the small contractor but also applies to everyone involved in construction. It provides help and assistance on how to work safely on most tasks you will encounter. It will also help to identify the main causes of accidents and ill health and explains how to eliminate hazards and control risks. The guidance is simple but comprehensive. The solutions are straightforward and easy to adopt. The first two editions sold over 250 000 copies, making it one of the most popular guides to construction health and safety. HSE Books Page 1 of 141 Health and Safety Executive © Crown copyright 2006 First published 1996 ISBN 978 0 7176 6182 2 All rights reserved. No part of this publication may be reproduced, stored in a retrieval system, or transmitted in any form or by any means (electronic, mechanical, photocopying, recording or otherwise) without the prior written permission of the copyright owner. Applications for reproduction should be made in writing to: The Office of Public Sector Information, Information Policy Team, Kew, Richmond, Surrey TW9 4DU or e-mail: [email protected] This guidance is issued by the Health and Safety Executive. Following the guidance is not compulsory and you are free to take other action. But if you do follow the guidance you will normally be doing enough to comply with the law. Health and safety inspectors seek to secure compliance with the law and may refer to this guidance as illustrating good practice. Page 2 of 141 Health and Safety Executive Contents Foreword 4 Introduction 5 1: Preparing for work 7 Planning the work 8 Organising the work 9 Notifying the site to HSE 9 2: Setting up the site 11 Site access 11 Site boundaries 11 Welfare facilities 11 Good order, storage areas and waste materials 14 Lighting 15 Emergency procedures 16 Fire 17 First aid 19 Reporting injuries, diseases and dangerous occurrences 20 Site rules 20 3: Construction-phase health and safety 20 Site management and supervision 21 Working at height 22 Site traffic and mobile plant 54 Moving goods safely 62 Groundwork 70 Demolition, dismantling and structural alteration 78 Occupational health risks 81 Electricity 94 Slips and trips 98 Working in confined spaces 99 Prevention of drowning 102 Protective equipment 103 Work affecting the public 106 Monitoring and reviewing 110 4: Health and safety management and the law 110 Appendices 129 1: Inspection recording form with timing and frequency chart 129 2: Construction health and safety checklist 131 References and further information 137 Health and safety in construction Page 3 of 141 Health and Safety Executive Foreword Every year many construction site workers are killed or injured as a result of their work; others suffer ill health, such as musculoskeletal disorders, dermatitis or asbestosis. The hazards are not, however, restricted to those working on sites. Children and other members of the public are also killed or injured because construction activities have not been adequately controlled. The construction industry’s performance has shown a steady long-term improvement, which I welcome. However there is no room for complacency. We can so easily believe that accidents will always happen to other people and will never touch us. But unless we all recognise our own vulnerability – and just how vulnerable others can be – then, as a result of the decisions we make, construction workers and their families will continue to witness the unnecessary injuries, pain and suffering that so tragically afflict the industry. In addition, accidents and ill health have a financial cost. The business case for improving performance is absolutely clear. This publication is aimed at the small contractor but is also applicable to all those involved in construction. It provides help and assistance on how to work safely on most tasks you are likely to encounter. It also helps you identify the main causes of accidents and ill health, and explains how to eliminate hazards and control risks. The guidance is simple but comprehensive. The solutions provided are straightforward and easy to adopt. Please read this publication and turn the advice into action. Doing so may well prevent you and other people from becoming victims of accidents or suffering ill health. Stephen Williams HM Chief Inspector of Construction Chair of the Health and Safety Commission’s Construction Industry Advisory Committee Health and safety in construction Page 4 of 141 Health and Safety Executive Introduction What is this book about? 1 This book explains the essential tasks for achieving healthy and safe construction sites. It will help you to identify hazards and control risks and it explains how to plan, organise, control, monitor and review health and safety throughout the life of a project. Who should read this book? 2 The book is aimed at everybody involved in construction work, including clients, designers, contractors and individual workers. It will appeal most to: directors and partners running construction businesses; site managers and supervisors running sites; managers and supervisors who work on sites run by other companies; and those doing the construction work, including employees and the self-employed. 3 Clients, designers and others who specify construction work may also find the book useful. Clients can use the book to identify the skills and competences contractors need to work safely and without risks to health. Designers, specifiers and planning supervisors can use it to identify the most common risks that contractors have to manage on site. They can then take account of how to design out or reduce these risks when they prepare their designs, specifications and plans. What sort of construction work does this book cover? 4 It provides guidance for people who work on all kinds of construction sites, including: general building and construction work; refurbishment work; maintenance and repair work; engineering construction work; and civil engineering work. How is the book structured? 5 The book is divided into four sections: Section 1: Preparing for work 6 This section covers planning and organising the job to ensure health and safety is taken into account from the very beginning. Section 2: Setting up the site 7 This section deals with setting up the site before work starts to ensure the fundamental health and safety issues have been addressed. Health and safety in construction Page 5 of 141 Health and Safety Executive Section 3: Construction-phase health and safety 8 This section summarises the main requirements for controlling and supervising site activities to ensure safe systems of work are followed. It helps the reader to identify health and safety hazards found on many sites and advises on how to control the risks that can arise. It then outlines the requirements for monitoring and reviewing to ensure site health and safety is maintained through to completion of the job. 9 The book cannot address every hazard, but it does focus on those matters that are the common causes of death, injury and ill health. It provides guidance on how to eliminate the hazards, or where this cannot be done, reduce the risk. Advice is given on protecting those who are directly employed to do the work, others working on the site, visitors to the site and members of the public who could be affected. Accidents 10 The most frequent causes of accidental death and injury are: Falls: People fall because access to and from the workplace is not adequate, or the workplace itself is not safe. The importance of providing good access to a safe working position (eg a platform with toe boards and guard rails) cannot be over-emphasised. Mobile plant: Construction plant can be heavy. It often operates on ground which is muddy and uneven, and where driver visibility is poor. People walking on site are injured or killed by moving vehicles, especially reversing ones. Others, particularly drivers and operators, are killed or injured by overturning vehicles and plant. Falling material and collapses: People are struck by material falling from loads being lifted and material that rolls or is kicked off work platforms; others are struck or buried by falling materials when excavations, buildings or structures collapse. Structural collapses can range from walls, which fall because their foundations are undermined by nearby excavations, to buildings, which collapse during alteration works because the structure was weakened and/or overloaded. Structures can also collapse unexpectedly during demolition if action is not taken to prevent instability. Scaffolds collapse because ties are either forgotten or removed too early during striking, or the scaffold is overloaded. Structures under construction may also collapse, eg steel frames that have not been adequately braced, or formwork that is prematurely loaded. Electrical accidents: People suffer electric shock and burns when they use unsafe equipment and when they contact overhead power lines and buried cables. Trips: Trips are the most common cause of reported injuries on construction sites, with over 1000 major injuries each year. Most of these can be easily avoided by effective management of access routes such as corridors, stairwells and footpaths. Health and safety in construction Page 6 of 141 Health and Safety Executive Ill health 11 The construction industry has a poor health record. Construction workers are likely to suffer ill health as a result of their work in the industry after exposure to both harsh working conditions and hazardous substances. Ill health can result from: Asbestos: Exposure to asbestos can cause serious respiratory diseases such as asbestosis and cancer. Manual handling: Lifting heavy and awkward loads causes back and other injuries. Some injuries can result from a single lift, but more commonly, long- term injury develops as a result of repeated minor injury due to repetitive lifting. Noise and vibration: High levels of noise can cause hearing loss and repeated use of vibrating tools can cause hand-arm vibration syndrome (damage to nerves and blood vessels – most commonly in the hands and fingers). Chemicals: Exposure to materials such as cement and solvents can cause skin problems such as dermatitis. Section 4: Health and safety management and the law 12 The law requires health and safety issues to be managed and controlled. This section sets out the most important parts of the law that apply to construction. It explains what needs to be done to ensure health and safety is dealt with effectively. References and further information 13 Sources of further information about site health and safety, which you may find useful, are listed at the back of this book. Regularly updated advice and guidance on many of the issues covered in this publication is also available on the Health and Safety Executive’s (HSE’s) website at www.hse.gov.uk/construction. Why has this book been revised? 14 This guidance replaces the 2001 revision of Health and safety in construction (Second edition, ISBN 0 7176 2106 5) and takes into account new legislation, in particular the Work at Height Regulations 2005.1 It builds on previous editions by incorporating recent advances and examples of good practice identified within the construction industry. 1: Preparing for work 15 The key to achieving healthy and safe working conditions is to ensure that health and safety issues are planned, organised, controlled, monitored and reviewed. 16 Everyone controlling site work has health and safety responsibilities. Checking that working conditions are healthy and safe before work begins and ensuring that the proposed work is not going to put others at risk requires planning and organisation. 17 This applies equally to a firm running and managing a small job, or to a subcontractor working at a large site controlled by someone else. Planning has to consider changes to the site as it develops – from welfare arrangements at the set up, through to snagging work and the dismantling of site huts and hoardings at the end of the contract. The basic requirements apply to all jobs. Health and safety in construction Page 7 of 141 Health and Safety Executive 18 The principal contractor, who is appointed under the Construction (Design and Management) Regulations 19942 (CDM), has more formal responsibilities for securing health and safety on site. These are set out in Section 4. The legal requirements of CDM do not apply to every job (see Section 4 Figure 54). Whether or not CDM applies, the principles of successful health and safety management are the same. Planning the work 19 Gathering as much health and safety information about the project and the proposed site before work begins is important. Information available at tendering should be used so that allowance is made for the time and resources required to deal with particular problems. Sources of information include: the client; the design team; contract documents; the main contractors on the site; specialist contractors and consultants; trade and contractor organisations; equipment and material suppliers; and HSE guidance and British or European Standards. 20 Find out about the history of the site and its surroundings. See if there are any unusual features which might affect the work, or how the work will affect others. Pay particular attention to: asbestos or other contaminants; overhead power lines and underground services; unusual ground conditions; public rights of way across the site; nearby schools, footpaths, roads or railways; and other activities going on at the site. 21 Where CDM applies, much of this information should be found in the pre- construction-stage health and safety plan. Make sure its contents have been taken into account before tenders are submitted. Where CDM does not apply, gathering information is still important. 22 When estimating costs and preparing the programme, consider any particular health and safety hazards associated with the work. Make sure suitable allowances have been made in the price. The job will run more smoothly, efficiently and profitably if hazards have been predicted, planned for and controlled from the outset. Having to stop or reschedule work to deal with emergencies wastes time and money. 23 When materials are bought, or equipment is hired, the supplier has a duty to provide certain health and safety information. Make sure this is obtained and read. It may be necessary to: consider using a specialist who is familiar with the necessary precautions; carry out an assessment of the health risks arising from substances or equipment; and act on your findings, eg by eliminating harmful substances where possible, or by using a less hazardous method of work or providing training on the safe use of the material or equipment. Health and safety in construction Page 8 of 141 Health and Safety Executive 24 When programmes are prepared, consider whether there are any operations that will affect the health or safety of others working at the site. For example: think about access to the workplace – which trades will need to go where and when? Arrange the programme to make sure everyone who needs to use a scaffold or other means of access has time to do so. Plan to make sure the access will be safe and suitable for their use; timber treatment or site radiography usually has to be done when no one else is on site. The site may have to be left vacant for a few days. Where a specialist contractor is used, check the requirements with them and programme the work well in advance. 25 Discuss proposed working methods with subcontractors before letting contracts. Find out how they are going to work, what equipment and facilities they are expecting to be provided and the equipment they will bring to the site. Identify any health or safety risks that their operations may create for others working at the site and agree control measures. Obtaining health and safety risk assessments and method statements will help (see paragraphs 580-597). 26 Decide what plant will be required and check that it will be suitable. 27 Plan material deliveries and consider storage needs. 28 Plan your emergency and rescue procedures. Decide what equipment will be required and who is trained to operate it. Organising the work 29 Decide who will supervise the work – check that they are adequately trained and experienced. 30 When taking on workers, ask about the training they have received and ask to see certificates of training achievement. Get them to demonstrate their knowledge or to show examples of safe working practice before setting them to work. 31 Make sure that firms coming onto site provide adequate supervision for their workers. Agree what training they will have received or will be provided at the site. 32 See that work methods and safety precautions agreed before work is started are put into practice. Make sure everyone understands how work is to be done and is aware of relevant method statements before work starts. 33 Find out if any of the work will be further subcontracted. Make sure that people working for subcontractors also get the information they require and provide training, supervision etc as needed. Notifying the site to HSE 34 HSE should be notified in writing before construction starts (see Figure 1) if the work is expected to either: last longer than 30 days; or involve more than 500 person days of construction work. Health and safety in construction Page 9 of 141 Health and Safety Executive 35 The notification should be sent to the HSE office nearest to the proposed site. You can obtain this information from HSE’s Infoline Tel: 0845 345 0055. 36 A form (Form 10 rev) can be used for notification. Forms are available from HSE offices. It is not essential that this form is used for notification, but the information required on Form 10 must be provided in writing to HSE. A copy of the notification details should be displayed at a place on site where it can be easily read. 37 Where CDM applies to the work, notification of the project will be the responsibility of the planning supervisor (see paragraphs 630-631). The planning supervisor should update the information as it becomes available (eg when the principal contractor is appointed). Where CDM does not apply, it will be the responsibility of the contractors to notify the site to HSE. A flow diagram illustrating when CDM applies to a project is given in Section 4 Figure 54. How to decide if your project has to be notified to HSE Will the construction phase involve more than 30 days’ Yes work? Written notification No to HSE required Will the construction phase involve more than 500 person days of construction Yes work? No Notification not required Figure 1 F10 notification requirements Health and safety in construction Page 10 of 141 Health and Safety Executive 2: Setting up the site Site access 38 There should be safe access onto and around the site for people and vehicles. Plan how vehicles will be kept clear of pedestrians, especially at site entrances where it may be necessary to provide doors or gates to achieve this segregation. Doors that open onto traffic routes may need viewing panels or windows. 39 Your plan should include how vehicles can be kept clear of pedestrians at vehicle loading/unloading areas, parking and manoeuvring places and areas where drivers’ vision may be obstructed. For further information, see Safe use of vehicles on construction sites.3 Site boundaries 40 Construction work should be fenced off and suitably signed. This will protect people (especially children) from site dangers and the site from vandalism and theft. For some jobs the workplace will have to be shared. Perhaps the work will be done in an operating factory or office. Agree who has to control each area. Agree what fences, barriers, means of separation or permits to work are required to keep both construction workers away from hazards created by others and other people away from hazards created by the construction work; site rules might be needed (see paragraphs 100-101). Make sure there is a system to ensure necessary precautions are kept in place during working hours and that night-time and weekend protection is put in place as required before the site closes. For further information, see Protecting the public: Your next move.4 Welfare facilities 41 Everyone who works on any site must have access to adequate toilet and washing facilities, a place for preparing and consuming refreshments and somewhere for storing and drying clothing and personal protective equipment. 42 Principal contractors and others who have control over construction sites are responsible for providing or making available site welfare facilities. Employers are also responsible for ensuring that welfare facilities are adequate for their employees. 43 The welfare facilities should be sufficient for everybody who is working on the site. If facilities such as toilets and canteens provided by someone else are to be used, check that they are suitable and properly maintained. They should be kept clean, warm and properly ventilated and lit. 44 Welfare facilities should be easily available to people working on the site. Toilets need to be easily accessible from where the work is being done. Washing facilities should be as close as possible to the toilets. Washing facilities also need to be close to canteens and rest rooms so that people can wash before eating. 45 In almost all cases, these facilities will be provided on site. Where the work is of short duration, arrangements still need to be made for welfare facilities. 46 If mobile gangs are employed to work at a number of locations over a few days (eg road repair and cable-laying gangs), facilities can be provided at a central location. This is on condition that they are available to workers within reasonable Health and safety in construction Page 11 of 141 Health and Safety Executive walking distance or within a reasonable time, taking into account the available transport. Workers should not be left to make their own arrangements on an ‘as and when required’ basis. Sanitary conveniences 47 The numbers of toilets required will depend on the number of people working on the site. 48 Wherever possible toilets should be flushed by water and connected to a mains drainage system. If this is not possible, toilets with a built-in water supply and drainage tank may be provided. If neither option is possible, chemical toilets may be provided. Figure 2 shows a self-contained water-flushing toilet block with built-in tank. 49 Men and women may use the same toilet, provided it is in a separate room with a door that can be locked from the inside. 50 A washbasin with water, soap and towels or dryers should be located close to the toilets. Washing facilities 51 On all sites, provide basins large enough to allow people to wash their faces, hands and forearms (see Figure 3). All basins should have a supply of clean hot and cold, or warm, running water. If mains water is not available, water supplied from a tank may be used. Figure 2 A self-contained water-flushing toilet block with built-in tank Figure 3 Washbasin large enough for people to wash their forearms 52 Soap and towels (either roller-type cloth or paper) or dryers should also be provided. It is good practice to provide skincare products. 53 Where the work is particularly dirty or workers are exposed to toxic or corrosive substances (eg during demolition or work in contaminated ground), showers should be provided. 54 Men and women can share basins used for washing their faces, hands and arms. Health and safety in construction Page 12 of 141 Health and Safety Executive 55 A shower may be used by both men and women provided that it is in a separate room with a lock on the inside of the door. Rest facilities 56 Facilities should be available for taking breaks and meal breaks (see Figure 4). The facilities should provide shelter from the wind and rain and be heated as necessary. 57 The rest facilities should have: tables and chairs; a kettle or urn for boiling water; a means of heating food (eg a gas or electrical heating ring, or microwave oven). Figure 4 A welfare unit with a rest area and drying room 58 It should be possible for non-smokers to use the facilities without suffering discomfort from tobacco smoke. This can be achieved by providing separate facilities for smokers and non-smokers, or by prohibiting smoking in the rest facilities. 59 For small sites, rest facilities can often be provided within the site office or site hut, especially where this is one of the common portable units. 60 Remember, open-flued gas heaters and gas cooking rings can produce carbon monoxide if there is inadequate ventilation. When poorly maintained, they also give rise to leaks of methane which can ignite or explode without warning. Gas appliances should not be used in site huts, containers or other enclosed areas unless there are vents or louvres that give a permanent supply of fresh air that cannot be closed off (a window that can be opened is not adequate as it is likely to be closed in cold weather). LPG cylinders must be stored in the open air, if necessary locked cages may be used to secure them. Health and safety in construction Page 13 of 141 Health and Safety Executive Storing and drying clothing and personal protective equipment 61 Make sure there are proper arrangements for storing: clothing not worn on site (eg hats and coats); protective clothing needed for site work (eg Wellington boots, overalls, gloves etc); personally issued equipment (eg ear defenders, goggles, harnesses etc). 62 Separate lockers might be needed, although on smaller sites the site office may be a suitable storage area, provided it is kept secure. Where there is a risk of protective site clothing contaminating everyday clothing, store items separately. 63 Where necessary for propriety, men and women should be able to change separately. 64 A drying area should be provided to dry wet site clothing. This area should be separated from the eating area (see Figure 4). 65 If electrical heaters are used, ensure that they are either fitted with a high- temperature cut-out device or are properly ventilated. Many fires have been caused by placing clothing on electrical heaters to dry, making the appliance overheat. Drinking water 66 Make sure there is a supply of drinking water. It is best if a tap direct from the mains is available, otherwise bottles or tanks of water may be used for storage. If water is stored, it should be protected from possible contamination and changed often enough to prevent it from becoming stale or contaminated. 67 The tap should be clearly marked if it is possible to confuse the drinking water supply with other water supplies or other liquids such as: those not fit for consumption (eg water from storage tanks used for wheel washers); or certain toxic materials (eg from taps to pipelines in factories). 68 Cups or other drinking vessels should be available at the water tap, unless the water is supplied as an upward jet that can be drunk from easily (eg a drinking fountain). Good order, storage areas and waste materials 69 Plan how the site will be kept tidy and how housekeeping will be actively managed: keep walkways and stairways free of tripping hazards such as trailing cables, building materials and waste. This is especially important for emergency routes. Make sure that all flammable waste materials (such as packaging and timber offcuts) are cleared away regularly to reduce fire risks; keep inside floor areas clean and dry; outdoor footpaths should be level and firm and should not be used for storing materials. Health and safety in construction Page 14 of 141 Health and Safety Executive 70 Designate storage areas for plant, materials, waste, flammable substances (eg foam plastics, flammable liquids and gases such as propane) and hazardous substances (eg pesticides and timber treatment chemicals). Flammable materials will usually need to be stored away from other materials and protected from accidental ignition. Do not store materials where they obstruct access routes or where they could interfere with emergency escape, eg do not store flammable materials under staircases or near to doors or fire exits (see Figure 5). Figure 5 A designated timber storage area 71 If materials are stored at height (eg on top of a container or on a scaffold gantry), make sure necessary guard rails are in place if people could fall when stacking or collecting materials or equipment. 72 Keep all storage areas tidy, whether in the main compound or on the site itself. Try to plan deliveries to keep the amount of materials on site to a minimum. 73 Decide how the waste stream will be managed to ensure it is timely and effective. You might want to consider whether you will require the contractors to be responsible for collecting their own waste or whether you will provide someone to do this for the site. Don’t forget that waste materials also need storing safely before their removal from the site and make sure that you allow sufficient space for waste skips and bins. If you are collecting waste in skips you will need to decide where the skips can be positioned and how often they will need to be collected (see Figure 6). Consider waste generated inside and whether you need to provide wheeled bins to enable it to be brought out of the building safely. Lighting 74 Every part of the site that is in use should, as far as possible, be arranged so that natural light is available for people to see to do their work and move about the site safely. Where natural light is inadequate or not available, artificial lighting should be provided. 75 Where work will continue outside daylight hours or the building or structure is enclosed, artificial lighting will be required. Make sure that any artificial lighting does not change the apparent colour or visibility of any safety signs or other safety- related items such as fire extinguishers. Health and safety in construction Page 15 of 141 Health and Safety Executive 76 With both daylight and artificial light, shadows can obscure hazards both at the workplace (eg making it difficult to see the blade of a cutting disc or a drill bit) and on the site generally (eg at stairwells). If necessary, provide extra lighting to illuminate shadow areas. 77 Where failure of the primary artificial lighting would be a risk to the health or safety of anyone (eg someone working on a tower scaffold in a basement may fall while trying to descend in the dark), provide emergency lighting. Where it is not possible to have lighting that comes on automatically when the primary lighting fails, torches or other similar lights may provide suitable lighting. 78 In addition, emergency routes (the corridors, passageways etc that people must follow in an emergency to escape from danger) should be kept well lit while there are workers on the site. Where daylight provides adequate lighting, no further action is required. Where emergency routes need artificial light, provide emergency lighting that comes on if the primary lighting fails (eg battery or emergency generator-powered lighting). See also Emergency procedures (paragraphs 79-82). Emergency lighting does not have to provide the same level of lighting as under normal circumstances; merely enough to enable escape. Figure 6 A designated waste collection area Emergency procedures 79 At most sites, the most obvious emergency is fire. The general principles for dealing with fire risks are considered in greater detail in paragraphs 83-93. These general principles can be applied to planning for other emergencies, such as flooding in excavations, tunnels, work near the sea or rivers, waterworks etc, or a risk from asphyxiation or toxic gases. Plan emergency procedures before work begins and put general precautions in place from the start of work. 80 Some emergencies may require evacuation of the site or part of the site, while others might involve the rescue of an injured person. For example, it may be necessary to plan how someone injured in a fall within a confined space or within a restricted plant room can be attended to by first aiders and the emergency services before being taken to a place of safety. Health and safety in construction Page 16 of 141 Health and Safety Executive Planning for an emergency 81 When planning emergency procedures, routes and exits, take into account: the type of work being done on site (eg extra precautions may be required to maintain routes down stairs during demolition); the characteristics and size of the site and the number and location of workplaces on the site. A large site with people working at many locations will probably need bells or sirens at a number of places to raise the alarm. On small sites with only two or three people working, an air horn may be adequate; the plant and equipment being used (eg consider tower crane drivers, people working on suspended access equipment or where the exit may be obstructed by equipment); the number of people likely to be present on the site at any one time. On sites where many people work, escape routes need to be wide enough to allow everyone to get through doorways or down stairs easily without them becoming overcrowded; and the physical and chemical properties of substances or materials on or likely to be on the site (eg work at petrochemical installations or at sites where flammable paints or glues are in use may require an increased standard of ventilation). 82 Take precautions to ensure: the likelihood of emergencies arising is as low as possible; everyone on site can be alerted in an emergency; everyone working on site (including contractors who may only be at the site for a few hours) knows what signal will be given if there is an emergency and knows what to do; someone who has been trained in what to do is on site while work is in progress and will take responsibility for co-ordinating procedures; emergency routes are available, kept clear, signed and adequately lit. When the site is not adequately lit by daylight for all periods when people are at work, provide lighting that will come on automatically in an emergency; there are arrangements for calling the emergency services. It is good practice to let the Fire Brigade know about any work in tunnels, confined spaces or above 18 m (above this height they may require specialist access equipment) and anywhere else where specialised rescue equipment may be needed; there is adequate access to the site for the emergency services and that access does not become blocked by plant or material building up; arrangements for treating and recovering injured people are available; if an emergency does arise, someone is posted at the site entrance, or in another prominent position, so that they can direct the emergency services. Fire 83 Many solids, liquids and gases can catch fire and burn. It only takes a source of ignition, which may be a small flame or an electrical spark, together with air. Any outbreak of fire threatens the health and safety of those on site and will be costly in damage and delay. It can also be a hazard to people in surrounding properties. Fire can be a particular hazard in refurbishment work when there is a lot of dry timber and at the later stages of building jobs where flammable materials such as adhesives, insulating materials and soft furnishings are present. 84 Many fires can be avoided by careful planning and control of work activities. Good housekeeping and site tidiness are important not only to prevent fire, but also to ensure that emergency routes do not become obstructed. Making site rules can help. Health and safety in construction Page 17 of 141 Health and Safety Executive Precautions to prevent fires 85 The following precautions should be taken to prevent fires: use less-easily ignited and fewer flammable materials, eg use water-based or low-solvent adhesives and paint; keep the quantity of flammables at the workplace to a minimum; always keep and carry flammable liquids in suitable closed containers; if work involving the use of flammable materials is being carried out, stop people smoking and don’t allow other work activities involving potential ignition sources to take place nearby. For example, if floor coverings are being laid using solvent-based adhesives, don’t allow soldering of pipes at the same time; ensure that pipes, barrels, tanks etc which may have contained flammable gases or liquids are purged or otherwise made safe before using hot cutting equipment, such as a cutting torch or angle grinder. A pipe or container may appear to be empty, but can contain enough material on its sides, or within rust or other sediments, to produce a flammable or explosive atmosphere within it when heated or disturbed. Specialist advice may be required; to minimise the risk of gas leaks and fires involving gas-fired plant: –– close valves on gas cylinders when not in use; –– regularly check hoses for wear and leaks; –– prevent oil or grease coming into contact with oxygen cylinder valves; –– do not leave bitumen boilers unattended when alight; store flammable solids, liquids and gases safely. Separate them from each other and from oxygen cylinders or oxidising materials. Keep them in ventilated secure stores or an outdoor storage area. Do not store them in or under occupied work areas or where they could obstruct or endanger escape routes; have an extinguisher to hand when doing hot work such as welding or using a disc cutter that produces sparks; check the site at lunch time and at the end of the day to see that all plant and equipment that could cause a fire is turned off. Stop hot working an hour before people go home, as this will allow more time for smouldering fires to be identified; and provide closed metal containers to collect rubbish and remove them from the site regularly. Collect highly flammable waste such as solvent-soaked rags separately in closed fire-resisting containers. Precautions in case of fire 86 If a fire should break out, people must be able to escape from it. To achieve this consider the points in paragraphs 87-93. Means of giving warning 87 Set up a system to alert people on site; this could be a temporary or permanent mains operated fire alarm (which should be tested regularly, eg weekly), a klaxon, an air horn or a whistle, depending on the size and complexity of the site. Any warning needs to be distinctive, audible above other noise and recognisable by everyone. Means of escape 88 Plan escape routes and ensure they remain available and unobstructed. For work areas above or below ground, provide well separated alternative ways to ground level where possible. Protect routes by installing the permanent fire separation and fire doors as soon as possible. It is important that escape routes give access to a safe place where people can assemble and be accounted for. In a large chemical plant this may be a safety refuge, while on a small site the pavement outside may be adequate. Signs will be needed if people are not familiar with the escape routes (see Figure 7). Make sure that adequate lighting is provided for enclosed escape routes – emergency lighting may be required (see paragraph 78); Health and safety in construction Page 18 of 141 Health and Safety Executive Figure 7 An example of an emergency exit sign Means of fighting fire 89 As well as providing fire extinguishers for hot work, fire extinguishers should be located at identified fire points around the site. The extinguishers should be appropriate to the nature of the potential fire: wood, paper and cloth – water extinguisher; flammable liquids – dry powder or foam extinguisher; electrical – carbon dioxide (CO2) extinguisher. 90 Nominated people should be trained in how to use extinguishers. 91 If the building being worked in is occupied (eg an office, hotel or hospital), make sure the work does not interfere with the escape route from the building, or any fire separation, alarms, dry risers, or sprinkler systems. Check this with the building occupier or the Fire Brigade. 92 Fire doors should never be locked, left open or removed. Keep existing wet and dry risers ready for use and install any new ones as soon as possible. 93 For more information, read Fire safety in construction work.5 First aid 94 First aid can save lives, reduce pain and help an injured person make a quicker recovery. The Health and Safety (First Aid) Regulations 19816 require you to provide adequate and appropriate equipment, facilities and personnel to enable first aid to be given to your employees if they are injured or become ill at work. The minimum provision for all sites is: a first aid box with enough equipment to cope with the number of workers on site; an appointed person to take charge of first-aid arrangements; information telling workers the name of the appointed person or first aider and where to find them. A notice in the site hut is a good way of doing this. 95 An appointed person is someone you choose to take charge when someone is injured or falls ill and who will telephone for an ambulance if one is required. An appointed person should not attempt to give first aid for which they have not been trained. Health and safety in construction Page 19 of 141 Health and Safety Executive 96 A first aider is someone who has undergone a training course in administering first aid at work and holds a current first aid at work certificate. A first aider can undertake the duties of an appointed person. The number of qualified first aiders needed depends on the risk of injury and ill health on site. As a guide: Numbers employed at any location Number of first aid personnel Fewer than five At least one appointed person 5 to 50 At least one first aider More than 50 One additional first aider for every 50 employed 97 The first-aid arrangements should cover shift working, night and weekend working where this is carried out. This may mean appointing or training several people to ensure adequate cover. Reporting injuries, diseases and dangerous occurrences 98 Employers have a duty under the law (Reporting of Injuries, Diseases and Dangerous Occurrences Regulations 1995)7 to report to HSE certain types of accidents that happen to their employees. Whoever is in control of the site also has a legal obligation to report certain accidents which involve a self-employed worker or member of the public and certain dangerous occurrences. 99 Generally, you have to report deaths, serious injuries and dangerous occurrences immediately and less serious injuries within ten days. Certain occupational ill-health issues and diseases also have to be reported. Further details of when you must report an accident, disease or dangerous occurrence are given in paragraphs 668-673. Site rules 100 Clients may insist on certain safety precautions, especially where their business continues at the premises while construction work is in progress. It may assist everyone if site rules are applied. Site rules might cover, for example, the use of personal protective equipment, traffic management systems, pedestrian routes, site tidiness, fire prevention, emergency procedures or permit-to-work systems. 101 Make it clear where your site rules apply and where the client premises rules apply. Make sure everybody knows and follows the rules relevant to them. 3: Construction-phase health and safety 102 In construction work, many of the hazards (a hazard is something with the potential to cause harm) are obvious. Most of them can be found on almost every site. The causes of accidents are well known and often repeated. Too often hazards are just seen as an inevitable part of the job, so no action is taken to control the risks they create. Consequently, the rate of accidents and ill health remains high. Action is needed to change this. Health and safety in construction Page 20 of 141 Health and Safety Executive 103 This section identifies the most common causes of death, injury and ill health and sets out straightforward precautions. Applying this advice will make work safer and, in most cases, improve efficiency. 104 Some activities (eg roof work and steel erection) are considered in detail, but in general most operations will present a number of hazards, which are dealt with on a number of pages. For example: Painting may include: –– a risk of falls; –– paints and solvents, which may be health hazards. Fitting out in an office being refurbished may involve: –– a risk of falls; –– a risk of tripping over trailing cables or waste materials; –– electrical risks from portable equipment; and –– a risk of exposure to asbestos. 105 The information in this section will help those carrying out risk assessments (see paragraphs 580-591) by explaining how to identify hazards and select control measures. In finalising an appropriate safe system of work for any construction job, it will be necessary to consider the particular nature of the site and the detail of the operations to be carried out. Where the Construction (Design and Management) Regulations 19942 (CDM) apply, the health and safety plan (see paragraphs 612- 615) may provide additional useful information. Site management and supervision 106 Effective management of work activities and competent site supervision are essential in maintaining healthy and safe conditions. It should be made clear to supervisors exactly what it is they are expected to do and how they are expected to do it. The greater the risk, the greater the degree of control and supervision required. 107 Ensure the level of site supervision provided is adequate. Site managers and supervisors should be trained to help them discharge their health and safety responsibilities. On larger sites, site managers may require the support of assistant site managers. On smaller sites, if the supervisor or manager is sometimes not present, they (or a deputy) should be contactable by phone and a responsible person should be left in charge of the site. 108 Before work starts: consider if there are any hazards you can avoid altogether (eg the need to paint at height can be eliminated if materials are brought to site ready-finished); decide which risks need to be controlled; consider the best ways of controlling them; and then having decided what needs to be done, make sure it happens. Health and safety in construction Page 21 of 141 Health and Safety Executive 109 Check that: everyone is properly trained and competent; they have the equipment they need; and agreed work methods are put into practice. 110 When people (either employees, other contractors or visitors) first come to site, it is important that they receive information about the site hazards and the steps that have been taken to control the risks. Make sure that the person running the site can be easily identified; if there is a site office, sign it clearly. A site plan showing the office location, placed at the site entrance together with an instruction that all visitors report to the site office, can be helpful. The principal contractor has a duty to take reasonable steps to ensure that only authorised people are allowed where construction work is being done. 111 People who are going to work on the site for the first time should be briefed about risks, welfare facilities and site rules. One way of doing this is by making sure the site supervisor speaks to them before they start work. They might also be given an information sheet or relevant information might be displayed on a notice board prominently placed near the site entrance. Remember, many people are killed and seriously injured during the first few days that they work at a site. 112 Ask people working at the site for their views and ideas about health and safety and how working conditions or systems can be improved. This can be done during formal meetings or on an informal basis either face to face or using a suggestion box. 113 Health and safety checks can be incorporated into normal progress and quality checks carried out by supervisors and managers. Specific additional checks on higher-risk work may also be needed. 114 Included at the back of the book is a health and safety checklist, which may be photocopied. This list covers issues which need to be addressed on almost every site. It can be used by those planning work to help them decide if they have addressed the most significant risks before work starts and also as a tool for site supervisors and others who may need to monitor site conditions. The checklist is a guide; there may be additional matters at some sites which are vital to address. 115 Carrying out routine checks from time to time reminds everyone that health and safety matters! Working at height 116 Work at height means work in any place, including a place at or below ground level, where if measures required by the Work at Height Regulations 20051 are not taken, a person could fall a distance liable to cause personal injury. Work at height also includes obtaining access to or egress from a place of work at height. The hierarchy of control measures 117 Falls are the largest cause of accidental death in the construction industry. They account for 50% of all fatalities. There is no distinction between low and high falls. This means that for any work at height, precautions are required to prevent or minimise the risk of injury from a fall. Health and safety in construction Page 22 of 141 Health and Safety Executive 118 To prevent or minimise risk when planning for work at height, consider the work to be done and take a sensible risk-based approach to identify suitable precautions. There is a hierarchy of control measures for determining how to work at height safely. The hierarchy has to be followed systematically and only when one level is not reasonably practicable may the next level be considered. Where it is reasonably practicable to prevent a fall, precautions should be taken to do so. It is not acceptable to select work equipment from lower down the hierarchy (eg personal fall arrest systems such as harnesses and lanyards) in the first instance. 119 Those in control of the work must: avoid work at height where they can (see Figure 8); use work equipment to prevent falls where work at height cannot be avoided; where the risk of a fall cannot be eliminated, use work equipment to minimise the distance and consequences of a fall should one occur; always consider measures that protect all those at risk, ie collective protection measures (scaffolds, nets, soft landing systems) before measures that only protect the individual, ie personal protection measures (a harness); ensure work is carried out only when weather conditions do not jeopardise the health and safety of the workers. 120 The hierarchy of control measures with practical examples: Avoid working at height unless it is essential (eg erect guard rails on steelwork at ground level and then crane the steel and the guard rails into position; provide cast in mesh across riser ducts at the position of services; fix nets using extending poles). Prevent falls by using an existing safe place of work that does not require the use or addition of work equipment to prevent a fall (eg a flat roof with permanent edge protection). Prevent falls by using work equipment that protects all those at risk (eg access equipment fitted with guard rails, such as independent scaffolds, tower scaffolds, mobile elevating work platforms (MEWPs) and mast climbing work platforms (MCWPs)). Prevent falls by using work equipment that protects the individual (eg a harness with a short lanyard which makes it impossible for a person to get to a fall position (this is called work restraint) or use a podium). Mitigate falls by using work equipment to minimise the distance and consequences of a fall and protect all those at risk (eg nets or soft landing systems positioned close under the work surface). Mitigate falls by using work equipment to minimise the distance and consequences of a fall and protect the individual (eg a personal fall arrest system with the anchorage point sited above the head, or a rope access system). Mitigate falls by using work equipment that minimises the consequences of a fall (eg nets rigged at a lower level, or inflatable injury protection). Mitigate falls through training, instruction or other means (eg ensure ladders are inspected regularly and are used by competent people, demarcate areas to provide a warning, provide adequate lighting, apply sensible housekeeping measures, provide suitable footwear etc). Health and safety in construction Page 23 of 141 Health and Safety Executive Selecting the right means of access and work equipment 121 When planning for working at height that is unavoidable, the first choice will be to use any existing safe place of work that allows safe access and provides a safe working place. Where it is not reasonably practicable to work safely from the existing place of work, an alternative means of access will be needed. This will involve the use of work equipment. 122 Traditionally, much work has been done from scaffolding. However, other means of access (such as MEWPs and tower scaffolds) will ensure collective fall prevention because they are equipped with guard rails. Personal measures, such as podium steps, can also be used to prevent falls. If fall prevention is not reasonably practicable, other work equipment can be used to minimise the distance and consequences of a fall using, for example, personal suspension equipment such as rope access techniques and boatswain’s chairs. 123 Ladders are at the bottom of the hierarchy because they do not prevent or mitigate a fall. However, if they are used by competent people and are regularly inspected and well maintained, then their use may be justified providing it is not reasonably practicable to use other work equipment which will prevent or mitigate a fall. 124 It is also essential to consider what risks there may be in erecting and removing the access equipment as well as using it. 125 When deciding upon the safest means of access and selecting the most suitable work equipment, you will need to consider: the distance and consequences of a potential fall; how long the work will last and how often it will be undertaken; how many people will be working at height and require protection; the space available on the site. Each type of platform requires a minimum amount of space, eg MEWPs need outriggers – check you can fit them in; the type of work to be carried out, eg some work may require heavy loads on the platform; what risks there will be during the erection and removal of the platform; can the equipment be stabilised, eg check that the scaffold can be tied; what will happen in adverse weather conditions; whether part of the structure can be provided early in the work so that there is a permanent working platform; and what emergency and rescue procedures are required. Health and safety in construction Page 24 of 141 Health and Safety Executive Figure 8 Using a long pole to avoid working at height 126 Most accidents involving falls could have been prevented if the right equipment had been provided and properly used. 127 Summary of steps to take before working at height: Ask yourself whether any of the work can be carried out without working at height. Start at the top of the hierarchy to decide what equipment will provide the safest method of getting to the work area and carrying out the job. Check that the selected equipment is suitable for the conditions on site. Make sure that the equipment needed is delivered to site in good time and that the site has been prepared for it. Check that the equipment is in good condition and make sure that whoever puts the equipment together is competent and knows what they are doing. Make sure those who use the equipment are supervised so that they use it properly. The more specialised the equipment (eg boatswain’s chairs and rope access equipment), the greater the degree of training and supervision required to ensure safety. Check any equipment provided by another company is safe before using it. Find out who to tell if any defects need to be remedied or modifications need to be made and keep them informed. Ensure you have procedures for rescuing an injured person and handling an emergency situation. 128 When selecting a means of access, remember: only when it is not practicable to provide a work platform that prevents falls (eg scaffolds, MEWPs) should measures which mitigate falls (eg nets, soft landing systems, personal fall arrest systems etc) be used; whenever harnesses are used, a method must be available to enable people to be rescued should they fall and be left suspended in their harness. Rescue kits and training can often be provided by the harness suppliers; Health and safety in construction Page 25 of 141 Health and Safety Executive it may be necessary to put measures in place to protect those installing guard rails or other fall protection measures; ladders should always be prevented from slipping and be positioned to ensure stability. They should be primarily used for access and only be used as workplaces for light work of short duration, and then only if it is safe to do so (see paragraphs 218-219). It is generally safer to use a tower scaffold or MEWP even for short-term work; heavy work activity (such as drilling or carrying heavy or awkward loads) should never be carried out from a ladder. When climbing a ladder with a load, a safe handhold must always be maintained. When working from a ladder, a secure handhold must be available; when selecting a safe system of work at height, all the risks have to be considered before one method is selected. For example, if nets are selected (see paragraphs 194-198), is there adequate clearance under the nets to prevent injury to those who may fall into them? If harnesses are used (see paragraphs 204-217), is there sufficient clearance from the ground to allow the shock-absorbing lanyard or inertia reel to deploy? Make sure that no one will be put at risk while the equipment is being removed; before any work at height, check that there is adequate clearance for equipment, eg overhead power lines can be a risk when erecting scaffolds or using MEWPs, or there can be a risk of crushing against nearby structures when mobile access platforms are manoeuvred. Safe working platforms 129 A working platform is virtually any surface from which work is carried out, such as a roof, scaffold, MEWP, tower scaffold, trestle etc. It becomes a safe working platform when you can’t fall off it or through it or when measures have been taken to mitigate a fall from it. 130 Make sure the working platform is: capable of supporting the weight of the workers using it and any materials and equipment they are likely to use or store on it; stable and will not overturn. For example, scaffolds usually need to be tied to a supporting structure and MEWPs should not be operated on sloping or uneven ground; wide enough to allow people to pass back and forth safely and use any equipment or material necessary for their work at that place; kept clear of loose materials and constructed to prevent materials from falling. As well as toe boards or similar protection at the edge of the platform, the platform itself should be constructed to prevent any object that may be used on the platform from falling through gaps or holes, causing injury to people working below. For scaffolds, a close-boarded platform would suffice, although for work over public areas, a double-boarded platform sandwiching a polythene sheet, fans or protected walkways may also be needed. If MEWPs or cradles are used and they have meshed platform floors, the mesh should be fine enough to prevent materials, especially nails and bolts, from slipping through; free of openings and traps through which people’s feet could pass, causing them to trip, fall or be injured in any other way; and kept free of tripping and slipping hazards. Keep platforms clean and tidy and do not allow materials or waste to build up on them. Health and safety in construction Page 26 of 141 Health and Safety Executive Inspections and reports 131 All working platforms must be inspected by a competent person: after installation or assembly in any position; after any event likely to have affected its stability, eg following strong winds or substantial alteration; and at regular intervals if the working platform is below 2 m or at intervals not exceeding seven days if the working platform is at 2 m or above. 132 The person in control must have the inspections carried out by a competent person. This is someone with the appropriate training (eg attendance at a scaffolding inspection course) and experience to enable them to identify any risks that are present and decide upon the measures required to control the risks. 133 Whoever controls the activities of others who use a scaffold also needs to ensure it is safe before they use it for the first time. 134 If the competent person is not satisfied that work can be carried out safely, they should advise the person the inspection was carried out for (eg a senior manager of the principal contractor) as soon as possible. Stop work if the inspection shows it is not safe to continue. 135 The result of an inspection should be recorded and kept until the next inspection is recorded. 136 However, if the working platform is 2 m or above in height and the inspection is carried out after installation or assembly or to comply with the seven-day inspection regime, the competent person must: complete the inspection report before the end of the working period; provide a copy of the report to the person the inspection was carried out for within 24 hours. 137 The person receiving the report must: keep it at the site where the inspection was carried out until construction work is completed; thereafter, keep it at an office for three months. 138 The report should contain the following information: name and address of the person the inspection was carried out for; location of the place of work or work equipment inspected; description of the place of work or work equipment inspected; date and time of the inspection; details of any matter identified that could give rise to a risk to the health or safety of any person; details of any action taken as a result of any matter identified in the point above; details of any further action considered necessary; name and position of the person making the report. 139 Appendix 1 contains an inspection timing and frequency chart and a suggested format that may be reproduced or copied for recording this information. The suggested form does not have to be used – any form containing the required information is acceptable. The reverse of the form summarises the requirements for timing and frequency of inspections. Health and safety in construction Page 27 of 141 Health and Safety Executive General access scaffolds 140 Suitable precautions must be taken to prevent falls. General access scaffolds provide a means of working at height while preventing falls and should be provided whenever practicable. 141 Scaffolds should be designed, erected, altered and dismantled only by competent people and the work should always be carried out under the direction of a competent supervisor. Scaffolders should always adopt methods of work to prevent falls during the erection of scaffolding. This can be achieved by using an advanced guard rail system. Where this is not practicable, harnesses should be worn to provide a means of fall arrest. For further information on erecting scaffolding, see the National Access and Scaffolding Confederation’s guidance note Preventing falls in scaffolding and falsework.8 142 Scaffolds should never be erected or dismantled over people or busy pavements. If the work presents a danger to the public, you should apply for a road closure to eliminate the risk of a member of the public being injured. If this is not granted, erection and dismantling should be done inside a segregated area and during the times when there are fewer members of the public in the vicinity. 143 Ensure the scaffold is based on a firm, level foundation. The ground or foundation should be capable of supporting the weight of the scaffold and any loads likely to be placed on it. Watch out for voids such as basements or drains, or patches of soft ground, which could collapse when loaded. Provide extra support as necessary. 144 Ensure it is braced and tied into a permanent structure or otherwise stabilised. Rakers only provide stability when they are braced and footed adequately; single- tube rakers alone do not usually provide this and need to be braced to prevent buckling. Put ties in place as the scaffold is erected and only remove them in stages as it is struck. If a tie is removed to allow work to proceed, an equivalent tie should be provided nearby to maintain stability. Ties must be used within their safe working load limit. Proprietary system scaffolds should be erected and tied according to the manufacturers’ instructions. Figure 9 An independent scaffold Health and safety in construction Page 28 of 141 Health and Safety Executive 145 Scaffolds must be capable of supporting loads likely to be placed on them. Scaffolds are not usually designed to support heavy loads on their working platforms. If you are intending to load out platforms, inform whoever is providing the scaffold – a special design is likely be required. The duty rating of your scaffold should be appropriate to the work you are doing. Scaffolds should be assumed to be ‘general purpose’ (2 kN/m2) unless informed otherwise by your scaffold provider. Those specifying scaffolds need to be clear about the duty rating required, eg an ‘inspection and very light duty’ scaffold should be 0.75 kN/m2 whereas a ‘heavy duty’ scaffold should be 3.0 kN/m2. 146 Ensure you never sheet or attach debris netting to a scaffold without informing the supplier you are going to do so, as they will need to ensure the scaffold is designed for it. 147 Before using any scaffold, make sure that it is safe and suitable for the intended job: ensure platforms are fully boarded and wide enough for the work and for access (usually at least 600 mm wide); check that scaffold boards are properly supported and not overhanging excessively (eg no more than four times the thickness of the board); ensure there is safe access onto the work platforms, preferably from a staircase or ladder tower; check that loading bays are fitted with fall protection, preferably gates, which can be safely moved in and out of position to place materials on the platform; and make sure the scaffold is suitable for the task before it is used and checked whenever it is substantially altered or adversely affected, eg high winds. Guard rails, toe boards and brick guards 148 Guard rails, toe boards and other similar barriers should be provided to prevent falls whenever practicable (see Figure 10). 149 They should: be strong and rigid enough to prevent people from falling and be able to withstand other loads likely to be placed on them. For example, guard rails fitted with brick guards need to be capable of supporting the weight of stacks of bricks which could fall against them; be fixed to a structure or part of a structure capable of supporting them; include: –– a main guard rail at least 950 mm above any edge from which people are liable to fall; –– a toe board and brick guards where there is a risk of objects rolling or being kicked off the edge of the platform; and –– a sufficient number of intermediate guard rails or suitable alternatives positioned so that the unprotected gap does not exceed 470 mm. 150 Barriers other than guard rails and toe boards can be used, so long as they are at least 950 mm high, secure and provide an equivalent standard of protection against falls and materials rolling or being kicked from any edges. 151 Brick guards are designed to prevent falls of material between the gaps in the guard rails and are not intended to protect against people falling. Therefore brick guards should always be used in addition to the required fall protection consisting of guard rails and toe boards or other similar barriers. Health and safety in construction Page 29 of 141 Health and Safety Executive 152 If the risk comes from falling through openings or fragile surfaces (eg roof roof lights or asbestos roof sheets), an alternative to guard rails or a barrier is to cover the opening or material. Any covering should be: strong enough to support any loads likely to be placed on it (including the weight of a person); and fixed in position to prevent accidental dislodgement. To prevent people removing coverings, mark them with a warning (eg ‘Hole below – do not remove’). 153 If possible, discourage passage across covers by directing people around them, eg using a high-visibility tape barrier. Tower scaffolds 154 Tower scaffolds (also known as mobile access scaffolds) are widely used and can provide an effective and safe means of gaining access to work at height while preventing falls. However inappropriate erection and misuse of tower scaffolds are the cause of numerous accidents each year. Aluminium towers are light and can easily overturn if used incorrectly. Towers rely on all parts being in place to ensure adequate strength. They can collapse if sections are left out. Guard rail Not more than 470 mm Not more than 470 mm Frame Slab At least 950 mm Toe board Bolt down Figure 10 Guard rails and toe boards 155 Before selecting or specifying a tower you must be satisfied that it is the most suitable item of equipment for the job. Tower scaffolds are more likely be suitable for work either at single locations or at the same height at a series of locations, eg work to first floor windows. Tower scaffolds are more difficult to use safely for work that has to be done at varying height, eg underneath a sloping factory roof. 156 The manufacturer or supplier has a duty to provide an instruction manual that explains the erection sequence, including any bracing requirements and the height to which the tower can be erected safely. If the tower has been hired, the hirer has a duty to provide this information. This information must be passed on to the person erecting the tower. Health and safety in construction Page 30 of 141 Health and Safety Executive 157 Towers should be erected by trained and competent people who are following a safe method of work. There are two approved methods recommended by the Prefabricated Access Suppliers’ and Manufacturers’ Association (PASMA), which have been developed in co-operation with HSE. 158 The first method, an advanced guard rail system, makes use of specially designed temporary guard rail units, which are locked in place from the level below and moved up to the platform level. The temporary guard rail units provide collective fall prevention and are in place before the operator accesses the platform to fit the permanent guard rails. The progressive erection of guard rails from a protected area at a lower level ensures the operator is never exposed to the risk of falling from an unguarded platform (see Figure 11). 159 The second is the ‘through-the-trap’ (3T) method of erection. This method allows the person erecting the tower to position themselves at minimum risk during the installation of guard rail components to the next level. It involves the operator taking up a working position in the trap door of the platform, from where they can add or remove the components which act as the guard rails on the level above the platform. It is designed to ensure that the operator does not stand on an unguarded platform, but installs the components to a particular level while positioned within the trap door of that same level. The 3T method makes use of standard tower components (see Figure 12a-b). 160 If a tower scaffold is used: make sure it is resting on firm level ground with the locked castors or base plates properly supported – never use bricks or building blocks to take the weight of any part of the tower; install stabilisers or outriggers when advised to do so in the instruction manual; provide a safe way to get to and from the work platform, eg using an appropriately designed internal ladder; provide edge protection (guard rails and toe boards) on all working platforms and platforms used for storing materials. Figure 11 Advanced guard rails Health and safety in construction Page 31 of 141 Health and Safety Executive 161 The stability of any tower is easily affected. Unless the tower has been specifically designed for such use, activities such as those listed below should never be carried out: sheeting or exposure to strong winds; carrying out grit blasting or water jetting; or using the tower to hoist materials or support rubbish chutes. Figure 12a and b Through the trap 162 If ties are needed, check that they are put in place as required when the scaffold is erected and that necessary ties are kept in place when the scaffold is dismantled. 163 When erecting tower scaffolds: do not exceed the safe height-to-base ratio in the instruction manual. Towers should never be erected to a height not recommended by the manufacturer; do not use the working platform as a support for ladders, trestles or other access equipment; do not overload the working platform; do not fix ties to the centres of thin-walled aluminium tubes; do not climb up the rungs on the end frames of the tower to reach the platform unless the rungs have been specifically designed for the purpose of getting to and from the working platform – these have rung spacings of between 230 and 300 mm and an anti-slip surface. 164 When moving a mobile tower: reduce the height to a maximum of 4 m; check that there are no power lines or overhead obstructions in the way; check that the ground is firm, level and free from potholes; never move it while there are people or materials on the tower. 165 When towers are used in public places, extra precautions are required: erect barriers at ground level to prevent people from walking into the tower or work area; minimise the storage of materials and equipment on the working platform; remove or board over access ladders to prevent unauthorised access if they are to remain in position unattended. 166 To prevent the use of incorrectly erected or damaged tower scaffolds, they must be inspected regularly by a competent person. A new inspection and report is not required every time a tower scaffold is moved to a new location. However, if Health and safety in construction Page 32 of 141 Health and Safety Executive guard rails or other components have to be removed to enable the tower scaffold to be moved past an obstruction, then a pre-use check should be undertaken by a trained and competent user to make sure the tower has been reinstated correctly. In this situation, the use of a visible tag system (which can be updated each time a check is carried out) to supplement inspection records is one way of recording that the pre-use check has been undertaken. 167 For details of the inspection and recording requirements, see paragraphs 131- 139 and the reverse of the inspection form at Appendix 1. Mobile access equipment 168 Where it is not possible to avoid work at height or work from an existing structure, mobile access equipment, including mobile elevating work platforms (MEWPs) and mast climbing work platforms (MCWPs), can be used to prevent falls. Mobile elevating work platforms (MEWPs) 169 MEWPs can provide excellent safe access to high-level work that can be easily moved from one location to another. 170 The three basic types of MEWP are: scissor lift (which gives a vertical lift only); telescopic boom (which gives vertical lift and outreach and is generally known as a ‘cherry picker’); articulating and telescopic boom (which are usually vehicle mounted and used for specialist activities such as bridge repair). 171 Before a MEWP is used you must assess the risks of people falling from or being thrown from the carrier, or the MEWP overturning, and take precautions to eliminate or control those risks. 172 Before work starts make sure that: the work is properly planned; the operator is fully trained and is familiar with the performance and controls of the specific type of MEWP they are going to use; there is a current report of thorough examination for the equipment; the machine is fitted with an emergency stop at ground level which can be deployed if the carrier becomes trapped against a fixed structure; the work platform is provided with guard rails and toe boards or other suitable barriers; it is used on firm and level ground, which may have to be prepared in advance and any temporary covers are strong enough to withstand the applied pressure; the daily inspection has been completed; any outriggers are extended and chocked as necessary before raising the platform; areas of the site where people may be struck by the platform or falling materials have been barriered off; other vehicles, such as delivery vehicles and dumpers etc, are segregated from the work area; the equipment is protected from adverse weather. High winds can tilt platforms and make them unstable. Establish a maximum safe wind speed for operation. Storms and snow falls can also damage platforms, so they should be inspected before use after severe weather; and everyone knows what to do if the machine fails with the platform in the raised position. Health and safety in construction Page 33 of 141 Health and Safety Executive Figure 13 A mobile elevating work platform 173 When using MEWPs: do not operate MEWPs close to overhead cables or other dangerous machinery; do not allow people to climb out of the carrier to reach their work position; do not allow a knuckle, or elbow, of the arm to protrude into a traffic route when working near vehicles; do not move the equipment with the platform in the raised position unless the equipment is designed to allow this to be done safely (check the manufacturer’s instructions). 174 At the end of each day check that: the platform is cleared of tools and equipment; all power has been switched off and the keys have been removed from the machine; the equipment is secured where it will not be accessible to vandals or trespassers; and the machine log has no record of any faults, malfunctions, repairs or maintenance requirements. 175 Some MEWPs are described as suitable for ‘rough terrain’. This usually means that they are safe to use on some uneven or undulating ground, but check their limitations in the manufacturer’s handbook before taking them onto unprepared or sloping ground. Health and safety in construction Page 34 of 141 Health and Safety Executive 176 If there is still a residual risk of impact or people falling after you have assessed the risks and put control measures in place, then the use of fall protection equipment should be considered, eg: when working next to or in a live highway (eg street lighting work) where there is a risk of a vehicle hitting the MEWP; when traveling with the carrier in a raised position where it may strike fixed objects in its path (eg branches, steel work); when traveling with the carrier in a raised position over uneven ground; during steel erection where the carrier has to move in and around the steelwork. 177 In practice, wearing a harness with a short work-restraint lanyard provides the most suitable form of personal fall protection as it stops the wearer from getting into a position where they could fall from the carrier in the first place (unless it is a MEWP overturn). In this system, the harness does not normally have shock- absorbing capability and must be fixed to a suitable anchor point inside the basket. Figure 14 A mast climbing work platform 178 MEWPs are versatile machines that can be used throughout the life of a project. When undertaking refurbishment work or when you have reached the fit- out stage of a project, you may consider using a MEWP to provide safe access to height. MEWPs that can fit through a normal-width doorway and can be moved from floor to floor using the lift installed in a building are available for indoor use. Always check the safe working load of the lift against the weight of the MEWP (including people and equipment) before transporting it in this way. Mast climbing work platform (MCWPs) 179 This equipment is often used when carrying out repairs to (or refurbishment of) high-rise buildings. MCWPs are designed to provide access to working positions – they are not designed to act as material hoists. 180 Only specialists should erect, alter or dismantle mast platforms. It is particularly important that the correct sequence is followed. Serious accidents have occurred when ties have been removed or outriggers have not been properly extended during alterations. Health and safety in construction Page 35 of 141 Health and Safety Executive 181 A great advantage of using MCWPs is that those using them can be protected from adverse weather as many types can be provided with screens and a roof to the platform. However, enclosures to platforms can increase wind loads so the supplier must always be consulted before fixing them. High winds can make platforms unstable so consult the supplier to establish a maximum safe wind speed for operation. Storms and snowfalls can also damage platforms, so they should be inspected before use after severe weather. 182 When MCWPs are used, make sure: a handover certificate is provided by the installer. The certificate should cover how to deal with emergencies, operate, check and maintain the equipment, and should state its safe working load; there is a current report of thorough examination for the equipment; masts are rigidly connected to the structures against which they are operating and outriggers are used when necessary; working platforms are provided with suitable guard rails and toe boards; the controls only operate from the working platform; and the area below the platform is barriered off to prevent people from being struck by the platform or by objects that may fall from the platform. 183 At the end of each day check that: the platform is cleared of tools and equipment; all power has been switched off and, where appropriate, power cables have been secured and made dead; and the machine log has no record of any faults, malfunctions, repairs or maintenance requirements. Suspended access equipment 184 Where it is not possible to use mobile access equipment, suspended access equipment can be used. This enables the worker place themselves in the position required to carry out the work and includes suspended access cradles and boatswain’s chairs. Suspended access cradles 185 Accidents happen during installation, use and dismantling of temporary cradles. Most accidents happen because of: unsafe access to and from the cradle; insufficient or poorly secured counterweights and holding-down systems; failure of the cradle platform or components such as drop-nose pins and bolts; failure of winches, climbing devices, safety gear and ropes, usually as a result of poor maintenance; and failure to follow the manufacturer’s instructions on erection and dismantling. 186 Equipment should be selected, installed, thoroughly examined and tested to ensure that it is suitable for its intended purpose. Cradles should only be used by suitably trained and competent workers. Health and safety in construction Page 36 of 141 Health and Safety Executive 187 When using cradles check that: the cradle has adequate guard rails and toe boards and material cannot fall from or through the cradle’s base; the equipment is capable of fitting closely to the building and where buffers or rollers are fitted, they will run against suitable features on the building; the building is capable of carrying the loads placed upon it, particularly under the counterweights and under the fulcrum (or pivot point) of the outrigger. The advice of a structural engineer may be needed; jib spacing matches the cradle length and, when the cradle can move, adequate stops are provided to prevent the cradle running off the end of the track; jib length and counterweights are specified to give a factor of safety against overturning of no less than three; a secondary safety rope fitted with a fall arrest device is provided and used; adequate operating instructions and technical support are available. If the equipment is hired, the supplier should be able to advise; the cradle is not overloaded and loads are placed on the platform as uniformly as possible; there is safe access into the cradle. Access at ground level is safest. If access is from the roof, the cradle should be secured to prevent it swinging away from the building. Access must be possible without the need to climb up or down the suspension ropes. If access is from the roof, or other raised platform, suitable means to prevent falls from roof edges will be required (eg guard rails and toe boards); and there is a plan for rescuing the operator if there is a cradle fault while at a high level. 188 Even where these precautions have been taken, accidents are still possible. For example, if the motor on a powered cradle fails, it can make the cradle tip, or people may overbalance and fall while reaching out of the cradle. Safety harnesses can save lives in these circumstances. Harnesses should be attached to specially designed anchorage points which have been installed in the cradle by the manufacturer. The harness lanyards should be kept as short as possible, while allowing operators to reach their place of work. For further advice on the use of harnesses, see paragraphs 204-217. 189 It is important that a thorough visual pre-use check for obvious faults is carried out before each use. In addition, a weekly inspection should be carried out by a competent person and a record made of that inspection. Before taking a temporary scaffold access platform into use, the following should be checked daily: the platform should be structurally sound – lift it off the ground, say 1 m, and inspect for excessive deflections; while it is off the ground, carry out a tactile inspection of critical connectors; make sure that it runs freely up and down – try it out; and check that lines of communication work properly. 190 At the end of each day, check that: the platform is cleared of tools and equipment; all power has been switched off and, where appropriate, power cables secured and made dead; the equipment is secured where it will not be accessible to vandals or trespassers; the shift report has no entries reporting any malfunction etc. Health and safety in construction Page 37 of 141 Health and Safety Executive Boatswain’s chairs 191 Boatswain’s (or bosun’s) chairs should only be used for light, short-duration work. They should only be used where the provision of a working platform or other mobile access equipment is not practicable. In general, use a chair that consists of a seat with a back, a central suspension point and a carrying point for tools. 192 Whether a chair or seat is used, the user should be attached to the suspension system by a harness and lanyard to protect against falls. Always ensure that the rope grab is compatible with the rope type, rope diameter and/or energy- absorbing lanyard in use. 193 A person in a boatswain’s chair is suspended high above the ground and would be hard to reach if they required assistance. The risk assessment should include your arrangements in case of an emergency. Safety nets and soft landing systems 194 Safety nets and soft landing systems (eg fire-retarded polystyrene-filled bags, air bags etc) can be used as leading edge protection to mitigate the consequences and distance should a fall occur. They are not a substitute for the use of fall prevention measures but can be used in conjunction with them if the risk of a fall cannot be eliminated (see Figure 15). Figure 15 Soft landing system 195 Nets are a complex energy-absorbing system, which should only be installed by trained and competent people. Before gaining access to height you must decide whether nets can be installed at ground level. It is often feasible to incorporate this into the steelwork design, and only if this is no