Operations Management Final Exam Review PDF
Document Details
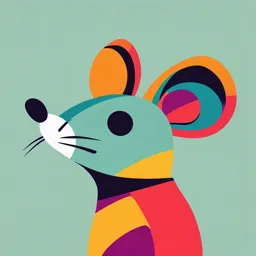
Uploaded by TopBoston9774
Tags
Related
- Introduction to Operations Management Part 1 PDF
- Production and Operations Management PDF
- Production and Operations Management PDF
- Far Eastern University Institute of Architecture and Fine Arts Module 3 PDF
- Production and Operations Management Past Paper PDF
- Production & Operations Management Slides PDF
Summary
This document provides an overview of operations management, including process design, quality management, location strategy, and supply chain management. It also explores strategies for managing a company and production/manufacturing via various methods and metrics.
Full Transcript
Week 1 - Chapter 1 - Introduction to Operations Management Operations Management: Design, Operation, and Improvement of Productive Systems Deals with all aspects of “running the business” such as: 1. Process Design 2. Managing Quality 3. Location and Layout Strategy 4. Human Resources and Job Des...
Week 1 - Chapter 1 - Introduction to Operations Management Operations Management: Design, Operation, and Improvement of Productive Systems Deals with all aspects of “running the business” such as: 1. Process Design 2. Managing Quality 3. Location and Layout Strategy 4. Human Resources and Job Design 5. Supply Chain Management 6. Inventory Management 7. Scheduling Operations is the technical core or hub of the organisation, interacting with other functional areas and suppliers to produce goods and services. Strategy and Operations Strategy is how the mission of a company is accomplished, provides consistency and ensures company is heading in the right direction. 1. Defining a Primary Task of the Company 2. Assessing Core Competencies 3. Positioning the firm a. Cost: Waste Elimination, Examination of cost structure (reduction potential), and lean production (low costs through disciplined operations) b. Speed: Service Organisation (competed on speed), Manufacturers (time-based - build-to-order production and efficient supply chains), Fashion Industry ( lead time) c. Quality: Minimising Defect Rates or conforming to design specs, employees empowerment, high performance work teams d. Flexibility: Ability to adjust to changes in product mix, production volume or design, mass customisation (mass production of customised parts) Overview of Production and Manufacturing Manufacturing: Application of physical and chemical processes to alter geometry, properties and/or appearance of a starting material to make parts or products (includes assembly, sequence of operations) Elements like machinery, Tooling, Power and Labor are used to bring the starting material to the processed part. There are Process Industries, within which there are Discrete products. Fixed-Position Layout: for when product is large and heavy and stays in the fixed position, worked and equipment are brought to product Process Layout: Equipment arranged according to function/type, different parts, each requiring a different operations sequence are routed through departments in order, highly flexible, can accommodate multiple operation sequences for different part configurations. Disadvantages: Machinery/Methods to produce part not designed for high efficiency, lots of material handling move parts between departments, high WIP. Product Variety: different types produced in plant, soft (small differences ) and hard (substantial differences) Production Quantity: Annual production quantities can be classified into three ranges: Production range Annual Quantity Q Low production 1 to 100 units Medium production 100 to 10,000 units High production 10,000 to millions of units Different production facilities are required for each of the 3 ranges & product variety 1. Low Production Quantities: Job Shop, makes low quantities of specialised and customised parts, typically complex products. The equipment is general purpose, Labor force is highly skilled, desgined for maximum flexibility. Fixed Position Layout if product is large or Process Layout if product is smaller. 2. Medium Production Quantities: Batch production, A batch of product is produced, and then facility is changed over to produce another product. Changeover takes time, set up time between batches. Usually uses a Process Layout, when there is Hard Product Variety. Cellular manufacturing and Group Technology: A mix of products is made without significant changes over time between products. Soft Product Variety and determined by principles of Group Terchnology. Group Technology: manufacturing philosophy in which similar parts are identified and group together to take advantage of their similarities in design and production. Processing steps are familiar for each part family. Machines are grouped into cells, each cell specialising in the production of a part family, cellular manufacturing. 3. High Production Quantities: Mass production or flow production, manufacturing system dedicated to production of that product, use of production lines. Product Process Matrix: tool for analysing the relationship between the product life cycle and the technological life cycle. The X-axis is the process life cycle and y-axis is product life cycle. Limitations and Capabilities of a Manufacturing Plant Companies don’t produce everything in one factory. Manufacturing capability refers to the technical and physical limitations of a plant 3 dimensions of manufacturing capability 1. Technological processing capability - the available set of manufacturing processes. 2. Physical size/weight of product plant can produce 3. Production capacity (plant capacity) - quantity that can be made in a given time Production and Manufacturing Metrics Help Company track performance, compare alternative production methods. 1. Production Performance Measures, production rate, cycle time, capacity, lead time, productivity 2. Manufacturing costs, labor material overhead, cost to produce Production Rates (Rp, parts assembled or processed per hour), Cycle Time (Tc, time between one work unit completing and next unit completing in minutes), Manufacture lead time (total time required to process a given part or product through the plant. Components of MTL: processing operations, assembly operations, material handling, lost time due to delays, time spent in storage, inspections) Production Capacity: maximum rate of output that a production line or department is able to produce. Calculated with machines x shifts/week x hours/shift x production rate To increase production capacity, consider running more shifts/week and more hours per shift for the short term. In the long term, try increasing number of machines and increased production rates (process improvements). Utilization: Amount of output of a production facility relative to its capacity. Productivity: output for a firm/division/line divided by inputs used, tells you how competitive a firm is. Single Factor: Output/(Labour/Materials/Capital Spend) Multi Factor: Output/(Labour + Materials + OH Spend)/(Labour/Energy/ Capital) Total Factor Productivity: Output/(All inputs used)