Production & Operations Management Slides PDF
Document Details
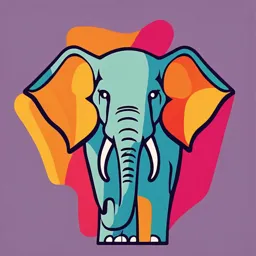
Uploaded by KidFriendlySerpent
United States International University-Africa
2024
Jane N. Were
Tags
Summary
These are slides covering different aspects of production and operations management. The document introduces various concepts and principles related to the topic.
Full Transcript
PRODUCTION & OPERATIONS MANAGEMENT WEEK 8 1 PREPARED BY DR. JANE N. WERE 9/5/2024 INTRODUCTION From an economic standpoint, organizations are only feasible and practical if they can satisfy their cust...
PRODUCTION & OPERATIONS MANAGEMENT WEEK 8 1 PREPARED BY DR. JANE N. WERE 9/5/2024 INTRODUCTION From an economic standpoint, organizations are only feasible and practical if they can satisfy their customers‟ wants through product, service or systems they produce or provide. Production and operation functions are concerned with providing these goods, services or systems. However, the concern of production operations management is the effective management of organizational resources used to provide these goods, services or systems. Consequently, any successful organization must have an efficient and effective production/operations management. 2 PREPARED BY DR. JANE N. WERE 9/5/2024 Definition Production can be defined as the activity of transforming raw materials or components into finished products. Production management is the process of the effective planning and control of the operations of that section of an enterprise devoted to transforming materials into finished products. Industries vary a great deal and even within an industry companies vary in organization and methods of work. Terminology also has not been standardized to a large extent, but there are basic principles which can be used and adapted to the varying types of 3 production. PREPARED BY DR. JANE N. WERE 9/5/2024 THE CONCEPT OF PRODUCTION MANAGEMENT Production function is that part of an organization, which is concerned with the transformation of a range of inputs into the required outputs (products) having the requisite quality level. Production is defined as “the step-by-step conversion of one form of material into another form through chemical or mechanical process to create or enhance the utility of the product to the user.” Thus, production is a value addition process. At each stage of processing, there will be value addition. 4 PREPARED BY DR. JANE N. WERE 9/5/2024 Input Output: Transformation Process: Men Products Product design Materials Services Machines Process planning Information Product control capital maintenance Continuous Inventory Quality Cost 5 PREPARED BY DR. JANE N. WERE 9/5/2024 PRODUCTION MANAGEMENT Production management is a process of planning, organizing, directing and controlling the activities of the production function. It combines and transforms various resources used in the production subsystem of the organization into value added product in a controlled manner as per the policies of the organization. It may be defined as: (i) It is the process of effectively planning, coordinating and controlling the production that is the operations of that part of an enterprise, it means to say that production and operations management is responsible for the actual transformation of raw materials into finished products. (ii) Production management is a function of Management, related to planning, coordinating and controlling the resources required for production to produce specified product by specified methods, by optimal utilization of resources. 6 PREPARED BY DR. JANE N. WERE 9/5/2024 Objectives of Production Management The objectives of the production management are to produce goods services of right quality and quantity at the right time and right manufacturing cost. 1. RIGHT QUALITY The quality of product is established based upon the customers needs. The right quality is not necessarily best quality. It is determined by the cost of the product and the technical characteristics as suited to the specific requirements. 2. RIGHT QUANTITY The manufacturing organization should produce the products in right number. If they are produced in excess of demand the capital will block up in the form of inventory and if the quantity is produced in short of demand, leads to shortage of products. 7 PREPARED BY DR. JANE N. WERE 9/5/2024 3. RIGHT TIME Timeliness of delivery is one of the important parameter to judge the effectiveness of production department. So, the production department has to make the optimal utilization of input resources to achieve its objective. 4. RIGHT MANUFACTURING COST Manufacturing costs are established before the product is actually manufactured. Hence, all attempts should be made to produce the products at pre-established cost, so as to reduce the variation between actual and the standard (pre-established) cost. 8 PREPARED BY DR. JANE N. WERE 9/5/2024 OPERATING SYSTEM Operating system converts inputs in order to provide outputs which are required by a customer. It converts physical resources into outputs, the function of which is to satisfy customer wants i.e., to provide some utility for the customer. In some of the organizations the product is a physical good (hotels) while in others it is a service (hospitals). Bus and taxi services, tailors, hospital and builders are the examples of an operating system. 9 PREPARED BY DR. JANE N. WERE 9/5/2024 SCOPE OF PRODUCTION & OPERATIONS MANAGEMENT Production and operations management is concerned with the conversion of inputs into outputs, using physical resources, so as to provide the desired utilities to the customer while meeting the other organizational objectives of efficiency, effectiveness and adoptability. It distinguishes itself from other functions such as personnel, marketing, finance, etc., by its primary concern for „conversion by using physical resources. The following are the activities which are listed under production and operations management functions: 10 PREPARED BY DR. JANE N. WERE 9/5/2024 LOCATION OF FACILITIES Location of facilities for operations is a long-term capacity decision which involves a long term commitment about the geographically static factors that affect a business organization. It is an important strategic level decision-making for an organization. It deals with the questions such as „where should our main operations be based?‟ The selection of location is a key-decision as large investment is made in building plant and machinery. An improper location of plant may lead to waste of all the investments made in plant and machinery equipments. Hence, location of plant should be based on the company‟s expansion plan and policy, diversification plan for the products, changing sources of raw materials and many other factors. 11 PREPARED BY DR. JANE N. WERE 9/5/2024 PLANT LAYOUT AND MATERIAL HANDLING Plant layout refers to the physical arrangement of facilities. It is the configuration of departments‟ work centers and equipment in the conversion process. The overall objective of the plant layout is to design a physical arrangement that meets the required output quality and quantity most economically. “Plant layout is a plan of an optimum arrangement of facilities including personnel, operating equipment, storage space, material handling equipments and all other supporting services along with the design of best structure to contain all these facilities”. „Material Handling‟ refers to the „moving of materials from the store room to the machine and from one machine to the next during the process of manufacture‟. 12 PREPARED BY DR. JANE N. WERE 9/5/2024 PRODUCT DESIGN Product design deals with conversion of ideas into reality. Every business organization has to design, develop and introduce new products as a survival and growth strategy. Developing the new products and launching them in the market is the biggest challenge faced by the organizations. The entire process of need identification to physical manufactures of product involves three functions: marketing, product development, and manufacturing. Product development translates the needs of customers given by marketing into technical specifications and designing the various features into the product to these specifications. Manufacturing has the responsibility of selecting the processes by which the product can be manufactured. 13 PREPARED BY DR. JANE N. WERE 9/5/2024 PROCESS DESIGN Process design is a macroscopic decision-making of an overall process route for converting the raw material into finished goods. These decisions encompass the selection of a process, choice of technology, process flow analysis and layout of the facilities. Hence, the important decisions in process design are to analyse the workflow for converting raw material into finished product and to select the workstation for each included in the workflow. 14 PREPARED BY DR. JANE N. WERE 9/5/2024 PRODUCTION PLANNING AND CONTROL Production planning and control is defined as the process of planning the production in advance, setting the exact route of each item, fixing the starting and finishing dates for each item, to give production orders to shops and to follow up the progress of products according to orders. The principle of production planning and control lies in the statement „First Plan Your Work and then Work on Your Plan‟. Main functions of production planning and control includes planning, routing, scheduling, dispatching and follow-up. 15 PREPARED BY DR. JANE N. WERE 9/5/2024 Main Functions of Production Planning & Control Planning is deciding in advance what to do, how to do it, when to do it and who is to do it. Planning bridges the gap from where we are, to where we want to go. It makes it possible for things to occur which would not otherwise happen. Routing may be defined as the selection of path which each part of the product will follow, which being transformed from raw material to finished products. Routing determines the most advantageous path to be followed from department to department and machine to machine till raw material gets its final shape. Scheduling determines the programme for the operations. Scheduling may be defined as „the fixation of time and date for each operation‟ as well as it determines the sequence of operations to be followed. 16 PREPARED BY DR. JANE N. WERE 9/5/2024 Dispatching is concerned with the starting the processes. It gives necessary authority so as to start a particular work, which has already been planned under „Routing‟ and „Scheduling‟. Therefore, dispatching is „release of orders and instruction for the starting of production for any item in acceptance with the route sheet and schedule charts‟. The function of follow-up is to report daily the progress of work in each shop in a prescribed proforma and to investigate the causes of deviations from the planned performance. 17 PREPARED BY DR. JANE N. WERE 9/5/2024 Quality Control Quality control ensures that customers receive products of adequate and satisfactory quality. The quality of a product is also important concern to an organization as the cost quality calamities can be very high. Quality control concerns itself with those features and characteristics of a product that it maintains its ability to satisfy a given need. It is an ongoing process directed towards future production rather than past production. The main objectives of quality control are: To improve the companies income by making the production more acceptable to the customers i.e., by providing long life, greater usefulness, maintainability. To reduce companies cost through reduction of losses due to defects. To achieve interchangeability of manufacture in large scale production. To produce optimal quality at reduced price. To ensure satisfaction of customers with productions or services or high quality level, to build customer goodwill, confidence and reputation of manufacturer. To make inspection prompt to ensure quality control. 18 PREPARED BY DR. JANE N. WERE 9/5/2024 Scope of production and operations management Location & Facilities Plant layout Maintenance & Management Material Handling Production Material Product /Operation Management Design Management Quality Process Control Design Production Planning & Control 19 PREPARED BY DR. JANE N. WERE 9/5/2024 The Four P‟S of Production management Product A product is anything that can be offered in a market for attention, acquisition, use or consumption and is capable of satisfying a want or need. It includes physical objects, services, activity, persons, places, organization or ideal. One finds, therefore, that the Production Manager‟s duty is multifaced. He must be concerned with design, quality, quantity, reliability, selection, forecast, selling, price and delivery of the production to the target market. He must design and develop a product that fits his firm‟s production process. All these means that not every product will have a ready market, as for some a market must be created. To add do this requires a lot of planning and control, quality control, inventory control and material handling. Production planning and control determines limits or levels of production processes in some future period of time. The aim is to ensure that the customers receive a product or service according to the organization‟s predetermined schedules. 20 PREPARED BY DR. JANE N. WERE 9/5/2024 Plant This is an establishment of an organization for producing goods and services. The following factors have to be taken into account when establishing a suitable: Location of the plant Capacity of the plant Manufacturing method Flow of materials Handling methods 21 PREPARED BY DR. JANE N. WERE 9/5/2024 Location Location of a plant may determine its success or failure as it will influence its operations and costs. Management has to rigorously evaluate several factors in order to choose the most attractive site. These factors are both quantitative and qualitative. Cost is the major quantitative factor. Qualitative factors like social infrastructure are also important. However, after evaluating both quantitative and qualitative factors, final choice of the site should be based on either: The quantitative factors which showed a superior cost rating or A qualitative factor which appeared most attractive or A combination of both giving minimum location cost. 22 PREPARED BY DR. JANE N. WERE 9/5/2024 Capacity The capacity of the plant determines the amount of equipment needed by an organization. In determining the capacity level, an organization has to consider both external balance and internal balance criteria. While external balance criterion aims at matching plant capacity and forecasted sales demand, it is important to note that demand is generally uncertain. The objective, therefore, becomes difficult to achieve. It is still possible for an organization to achieve this balance by either: Producing to meet peak demand. This is the problem of having idle capacity during low seasons, but it does guarantee satisfaction of demand, or Producing to satisfying normal demand by having even production. This guarantees a stable work force and full utilisation of facilities, however, there may be during slack period, accumulation and maintenance of unnecessary inventory, or Designing physical capacity that ensures that labour and equipment utilisation is at the highest peak but excess demand goes to competitors. 23 PREPARED BY DR. JANE N. WERE 9/5/2024 Layout Appropriate layout requires proper coordination of production system and the productive facilities in order to achieve an optimal productive system that meets a firm‟s capacity and quality requirements. The productive facilities include machines, equipment, materials, work place and people. In order to facilitate the physical coordination of facilities and functions of the present time and the future, it is important that the layout be flexible to accommodate any future changes. 24 PREPARED BY DR. JANE N. WERE 9/5/2024 Production Process Production process is the transformation method used by an organization to convert its inputs into required goods or services. The conversion must be done according to set specifications like physical dimensions, tolerance, standard and quality requirements. Such transformation is done to achieve 25 the best possible output PREPARED BY DR. JANE N. WERE 9/5/2024 Five Types of Production Processes Project: Project system does not produce standardized products. The Plant, Machinery, Men and Materials are often brought to project site and the project is completed. The project is of big size and remains in the site itself after completion. As the costs can be calculated and allocated to the project with considerable accuracy, productivity can be measured. Once the project is completed, all the resources are removed from site. Jobbing process involves works which are of small sizes and the product or services are completed in-house and then transported to consumers. Job Production Shop: Tailors shop; cycle and vehicles repair shops, Job typing shops, and small workshops. 26 PREPARED BY DR. JANE N. WERE 9/5/2024 Batch process requires large and standardized output. A facility once used to produce a given job is then adjusted to take another group of items. Eventually the process returns to the initial work. The process makes each processing stage to be used and re-used to cater for several types of requirements. For examples of batch Production Shop: tyre Production Shops, readymade dress companies, Cosmetic manufacturing companies Line Process is repetitive and each product must pass through the same sequence of operations. The machines and the process produce a single or limited number of products. 27 PREPARED BY DR. JANE N. WERE 9/5/2024 Continuous Production system is the specialized manufacture of identical products on which the machinery and equipment is fully engaged. The continuous production is normally associated with large quantities and with high rate of demand. Hence the advantage of automatic production is taken. Mass Production: Here same type of product is produced to meet the demand of an assembly line or the market. This system needs good planning for material, process, maintenance of machines and instruction to operators. Purchases of materials in bulk quantities are advisable. 28 PREPARED BY DR. JANE N. WERE 9/5/2024 People The success or failure of an organization depends on the quality of its manpower. The production manager must be actively involved in planning and control of employees engaged in production department. This requires active participation in recruitment and selection of production personnel, their training and development, performance appraisal, compensation, motivation, supervision and in the development of their general welfare and safety programme. 29 PREPARED BY DR. JANE N. WERE 9/5/2024 Services Service systems present more uncertainty with respect to capacity and costs. Services are produced and consumed in the presence of the customer. We cannot store the service physically. Because of this, the service organizations, such as hotels, cinemas, hospitals, transport organizations and many other service organizations the capacity must be sufficiently or consciously managed to accommodate a highly variable demand. Sometimes services like legal practice and medical practice involve professional or intellectual judgments, which cannot be easily standardized. Because of this, the calculation of cost and productivity is difficult. Unique characteristics of Service are that: Services are intangible Service capacity is time perishable. Production and consumption of services occur simultaneous Service operations are labour intensive. A service customer is a participant in the service process 30 PREPARED BY DR. JANE N. WERE 9/5/2024 Customer dictates where the service is to be provided. JUST-IN –TIME [JIT] The Japanese are credited with developing zero inventory or just-in-time concept. The concept was conceived to ensure that the inventory has only what is needed and when it is needed. The underlying philosophy of JIT is to devise a production system that encourages staff to strive consistently for improvements. This enhances performance. The aim is to identify problems at the outset and it is the responsibility of the staff to prevent them from recurring. JIT is defined as total quality control that it is a cost effective system for integrating the continuous efforts of people at all levels in an organization to deliver products and services which ensure customer satisfaction. JIT is often called a philosophy as it goes beyond inventory control to include quality planning, control and production scheduling. The system was developed for repetitive production , e.g. in a motor-car production line. Repetitive (or mass) production implies large volume production of batches of small numbers of similar products. 31 PREPARED BY DR. JANE N. WERE 9/5/2024 OBJECTIVES OF JIT A JIT production system aims to: Produce finished goods just-in-time to be sold. Assemble sub-assemblies into finished goods just-in-time; Buy fabricated goods just-in-time to go into sub-assemblies; Transform purchased materials into fabricated parts just-in-time. 32 PREPARED BY DR. JANE N. WERE 9/5/2024 BENEFITS OF JIT Greater productivity, smaller inventory; Better quality/less waste; Better motivated employees; Better customer service, less administration; Fewer stock, less materials handling; Less production control staff and inventory accounts. 33 PREPARED BY DR. JANE N. WERE 9/5/2024