Logistics Final Review PDF
Document Details
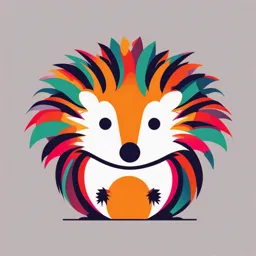
Uploaded by FamedBlueTourmaline8646
Tags
Summary
This document provides a detailed overview of logistics and material handling, covering external and internal logistics, transportation, and handling equipment. It also discusses material handling considerations, including safety, effectiveness, and cost efficiency.
Full Transcript
ELECTIVES FINAL REVIEWER 3. Unitizing equipment - refers to: a) Containers to hold materials, and Logistics - which is concerned with the acquisition,...
ELECTIVES FINAL REVIEWER 3. Unitizing equipment - refers to: a) Containers to hold materials, and Logistics - which is concerned with the acquisition, b) equipment used to load and package the movement, storage, and distribution of materials and products, as containers. 4. Identification and tracking systems – to well as the planning and control of these operations identify and keep track of the materials being in order to satisfy customer demand. moved and stored. 2 CATEGORIES OF LOGISTICS External logistics is concerned with Unit Load Principle (unitizing) transportation and related activities that occur In general, the unit load should be as large outside of a facility. In general, these activities as practical for the material handling system that involve the movement of materials will move and store it. between different geographical locations. The five traditional modes of transportation are rail, truck, A Unit Load is the mass that is to be moved or air, ship, and pipeline. otherwise handled at one time. Internal logistics - more popularly known as material handling, involves the movement and storage of materials inside a given facility. The interest in this book is on internal logistics. MATERIAL HANDLING Defined “The movement, storage, protection (a) Wooden Pallet ( b) Pallet Box ( c) Tote Box and control of materials throughout the manufacturing and distribution process The second category of unitizing equipment includes: including their consumption and disposal” (The - palletizers, which are designed to Material Handling Industry of America) automatically load cartons onto pallets and shrink-wrap plastic film around them for MATERIAL HANDLING shipping - Handling od materials must be performed - depalletizers, which are designed to unload cartons from pallets. Safety Design Considerations in Material Handling Effectively 1. Material characteristics At low cost 2. Flow rate, routing, and scheduling In a timely manner 3. Plant layout 4. Unit load principle Accurately Material characteristics And without damage to materials Material characteristics affect type of transport and storage equipment required: Categories of Material Handling Equipment Solid, liquid or gas 1. Material transport equipment – to move Size materials inside a factory, warehouse, or Weight other facility Shape - long, flat, bulky 2. Positioning Equipment - category consists Condition - hot, cold, wet, dirty of equipment used to handle parts and Risk of damage - fragile, brittle, sturdy other materials at a single location. Safety risk - explosive, flammable, toxic, corrosive Material Transport Equipment Five categories: 1. Industrial trucks 2. Automated guided vehicles 3. Monorails and other rail guided vehicles. 4. Conveyors 5. Cranes and hoists Industrial Trucks Flow rate, routing, and scheduling Two basic categories: a) Flow Rate - amount of material moved i. Non-powered per unit time. - human workers push or pull loads. o Examples: pieces/hr, pallet loads/hr, tons/hr o Whether the material must be moved in individual units, as batches, or continuously (pipeline) b) Routing - pick-up and drop-off locations, move distances, routing variations, conditions along the route (surface, traffic, elevation) c) Scheduling - timing of each delivery b) Powered Prompt delivery when required. ii. self-propelled, guided or driven by Use of buffer stocks to mitigate human. against late deliveries. iii. common example: forklift truck PLANT LAYOUT Walkie Truck a) Material handling equipment considerations must be included in the plant layout design problem. b) Correlation between layout type and material handling equipment Wheeled forks insert into pallet openings. No provision for riding; truck is steered by worker using control handle at front of vehicle. Forklift Truck Widely used in factories and warehouses because pallet loads are so common. Capacities from 450 kg (1000 lb) up to 4500 kg (10,000 lb) Power sources include on-board batteries and internal combustion motors. TOWING TRACTOR AGV PALLET TRUCK Designed to pull one or more trailing carts in factories and warehouses, as well as for airport baggage handling. Powered by on-board batteries or IC Used to move palletized loads along engines. predetermined routes. Automated Guided Vehicles Vehicle is backed into loaded pallet by worker; An Automated Guided Vehicle System pallet is then elevated from floor. (AGVS) is a material handling system that uses Worker drives pallet truck to AGV guide path and independently operated, self-propelled vehicles programs destination. guided along defined pathways in the facility floor. UNIT LOAD CARRIER Types of AGV: Driverless trains Pallet trucks Unit load AGVs (5-150 MM FROM THE GUIDE PATH) DRIVELESS AUTOMATED GUIDED TRAIN Used to move unit loads from station to station. Often equipped for automatic loading/unloading of pallets and tote pans using roller conveyors, moving belts, or mechanized lift platforms. VECHILE SAFETY Travel velocity of AGV is slower than typical walking speed of human worker. Automatic stopping of vehicle if it strays from guide path. o Acquisition distance First type of AGVS to be introduced around Obstacle detection system in forward direction 1954. o Use of ultrasonic sensors common Common application is moving heavy Emergency bumper - brakes vehicle payloads over long distances in warehouses when contact is made with forward object. and factories without intermediate stops Warning lights (blinking or rotating red lights) along the route. Warning sounds of approaching vehicles RAIL -GUIDED VECHILES Roller conveyor Self-propelled vehicles that ride on a fixed rail system Vehicles operate independently and are driven by electric motors that pick-up power from an electrified rail. Fixed rail system o Overhead monorail - suspended overhead from the ceiling Pathway consists of a series of rollers o On-floor - parallel fixed rails, tracks that are perpendicular to direction of travel. generally protrude up from the floor. Loads must possess a flat bottom to span OVERHEAD MONORAIL several rollers. Powered rollers rotate to drive the loads forward. Un-powered roller conveyors also available Skate-Wheel Conveyor Conveyor Systems Large family of material transport equipment designed to move materials over fixed path, usually in large quantities or volumes Similar in operation to roller conveyor but use skate wheels instead of rollers. 1. Non- powered Lighter weight and unpowered a. Materials moved by human workers or Belt Conveyor by trolly 2. Powered a. Power mechanism for transporting materials is contained in the fixed path, using chains, belts, rollers, or other mechanical devices. Continuous loop with forward path to Conveyor Types move loads. Belt is made of reinforced elastomer. Roller Support slider or rollers used to support Skate-wheel forward loop. Belt In-floor towline Overhead trolley conveyor In-floor Tow-line Conveyor can be suspended. Four-wheel carts powered by moving chains Trolleys are connected and moved by a or chain or cable that forms a complete loop. Often used to move parts and assemblies between major production areas. Powered Conveyor Operations and Features Types of motions 1. Continuous - conveyor moves at constant velocity 2. Asynchronous - conveyor moves with stop- and-go motion - They stop at stations, move between stations cables in trenches in the floor. Another classification of conveyors: Carts use steel pins (or grippers) to project 1. Single direction - are used to transport loads one below floor level and engage the chain (or way from origination point to destination point, pulley) for towing. This allows the carts to be disengaged from 2. Continuous loop - are used when loads are towline for loading and unloading. moved in carriers (e.g., hooks, baskets) between load and unload stations and the carriers are affixed to the conveyor loop. Overhead Trolley Conveyor Cranes and Hoists Handling devices for lifting, lowering and transporting materials, often as heavy loads. Cranes A trolley is a wheeled carriage running - used for horizontal movement of on an overhead track from which loads materials. Hoists - used for vertical lifting of materials. Cranes usually include hoists so that the crane- and-hoist combination provides. Horizontal transport Vertical lifting and lowering - Cranes include a variety of STORAGE SYSTEM material handling equipment designed for lifting and moving Storage System Performance heavy loads using one or more Performance measures for storage systems: overhead beams for support. - A hoist is a mechanical device Storage capacity - can be defined and used to raise and lower loads. As measured in two ways: (1) as the total seen in Figure 10.11,a hoist volumetric space available or (2) as the total consists of one or more fixed number of storage compartments in the system available to hold items or loads. pulleys, one or more moving Storage density - is defined as the pulleys, and a rope, cable, or volumetric space available for actual storage chain strung between the pulleys. relative to the total volumetric space in the Analysis of Material Transport storage facility. Systems Accessibility - refers to the capability to The from-to chart is a table access any desired item or load stored in the that can be used to indicate material flow system. data and/or distances between multiple System throughput - is defined as the locations. hourly rate at which the storage system (1) receives and puts loads into storage and/or Network diagrams can also be (2) retrieves and delivers loads to the output used to indicate the same type of information. station. A network diagram consists of nodes and Utilization and availability (reliability) arrows, and the arrows indicate relationships Utilization is defined as the proportion of among the nodes. time that the system is actually being used In material handling, the nodes for performing S/R operations compared represent locations (e.g., load and unload with stations), and the arrows represent material the time it is available. flows and/or distances between the stations. Availability is a measure of system reliability, defined as the proportion of time that the system is capable of operating (not broken down) compared with the normally scheduled shift hours Availability A is a reliability factor (Section Storage Location Strategies 3.1.1) defined as the proportion of total shift time that the vehicle is operational and not 1. Randomized storage – pwedeng ilang broken down or being repaired. lagay yung mga part kahit saan location To deal with the time losses due to traffic basta available yung space. congestion, the traffic factor Ft is defined 2. Dedicated storage – may specific na bin per item. as a parameter for estimating the effect of these losses on system performance. Worker efficiency is defined as the Conventional Storage Methods actual work rate of the human operator relative to the work rate expected under standard Bulk Storage or normal performance. Rack Systems Shelving and Bins Drawer Storage Bulk Storage - is the storage of stock in an open Shelves and Bins floor area. The stock is generally contained in unit loads on pallets or similar containers, and unit loads are stacked on top of each other to increase storage density. Rack Systems. provide a method of stacking unit loads vertically without the need for the loads themselves to provide support. Shelving and Bins. Shelves represent one of the most common storage equipment types. A shelf is a horizontal platform, supported by a wall or frame, Drawer Storage on which materials are stored. Drawer Storage. Finding items in shelving can Contents easily visible sometimes be difficult, especially Good accessibility if the shelf is either far above or far below eye level Relatively high cost for the storage attendant. Small items (tools, repair parts, etc.) Bulk Storage Bulk storage arrangements: (a) high-density bulk storage provides low accessibility, (b) bulk storage with loads forming rows and blocks for improved accessibility. Automated Storage Systems Mechanized and automated storage equipment to reduce the human resources Pallet Rack System required to operate a storage facility. Significant investment Level of automation varies: Pallet loads placed on racks in multi- rack structure. In mechanized systems, an operator participates in each storage/retrieval (a) Low cost transaction. (b) Good storage density In highly automated systems, loads are (c) Good accessibility entered or retrieved under computer control. Types of Automated Storage System 1. Automated Storage/Retrieval System 2. Carousel Storage System Carousel Storage System Vertical lift storage modules (VLSM) - uses a vertical aisle rather AS/AR than a horizontal aisle as in other AS/RS types. Unit load on pallet AS/RS with one aisle. Carousel Storage Systems Horizontal – series of bins and basket suspend to an overhead. Vertical – pull advantage of overhead and also save floor space. AS/AR Types Unit load AS/RS – large automated system for pallet loads Deep-lane AS/RS - uses flow- through racks and fewer access aisles. Miniload AS/RS - handles small loads contained in bins or drawers to perform order picking. Man-on-board AS/RS - human operator rides on the carriage to pick individual items from storage. Automated item retrieval System - picks individual items 1. Optical. Most of these technologies use Automatic Identification and Data high-contrast graphical symbols that can Capture be interpreted by an optical scanner. - Automatic identification and data 2. Electromagnetic. The important AIDC capture (AIDC) refers to technologies technology in this group is radio that provide direct entry of data into a frequency identification (RFID), which computer or other microprocessor- uses a small electronic tag capable of controlled system without using a holding more data than a bar code keyboard 3. Magnetic. These technologies encode - A family of technologies that provide data magnetically, similar to recording direct entry of data into a computer or tape. other microprocessor controlled system a. (a) magnetic stripe, widely used without using a keyboard in plastic credit cards and bank access cards, and AIDC Applications b. (b) magnetic ink character ▪ Retail sales and inventory control recognition, widely used in the banking industry for check ▪ Material handling processing. ▪ Factory operations 4. Smart card. This term refers to small plastic cards (the size of a credit card) ▪ Othe imbedded with microchips capable of Components of AIDC containing large amounts of information. 5. Touch techniques. These include 1. Encoded Data - alphanumeric characters touch screens and button memory. are translated to machine-readable form 6. Biometric. These technologies are 2. Machine reader or scanner - scanner utilized to identify humans or to reads the encoded data and converts it to interpret vocal commands of humans. alternative form, usually an electrical signal Measures of AIDC Reading Accuracy 3. Decoder - electrical signal is transformed 1. First read rate (FRR). This is the into digital data and finally back into original probability of a successful (correct) alphanumeric characters reading by the scanner in its initial AIDC Technologies attempt. - Optical - number of bar codes read over the - Electromagnetic number alternative over 100 percent - Magnetic 2. Substitution error rate (SER). This is - Smart Card the probability or frequency with which the - Touch Techniques scanner incorrectly reads the encoded - Biometric character as some other character. Bar Code Technology Bar codes are of two basic types: 1. Linear (a) - in which the encoded data are read using a linear sweep of the scanner - see to customer goods - name, price, weight 2. Two-dimensional (b) - in which the encoded data must be read in both directions. Two-Dimensional Bar Codes Two forms of linear bar codes: ▪ First 2-D bar code introduced in 1987 1. Width-modulated ▪ Two basic types of 2-D bar code symbols ▪ Symbol consists of bars and spaces of 1. Stacked bar codes varying width ▪ Consists of multiple rows of conventional bar ▪ Most widely used (e.g., Universal Product codes stacked on top of each other Code) 2. Height-modulated ▪ Symbol consists of bars and spaces of varying height ▪ Used only by U.S. Postal Service for ZIP code identification. Bar code readers interpret the code by scanning and decoding the sequence of bars. The reader consists of the scanner and 2.. Matrix symbologies decoder. ▪ Consists of 2-D patterns of data cells that are Linear Bar Code Readers usually square and are colored dark or white Usually classified as: ▪ Advantage over stacked bar codes is 1. Contact capability to contain more data. - Contact bar code readers are handheld wands or light pens operated by moving the tip of the wand quickly past the bar code on the object or document. 2. Noncontact - Noncontact bar code readers focus a light beam on the bar code, and a photodetector reads the reflected signal to interpret the code. Radio Frequency Identification ▪ Much more data can be contained in the identification tag than with most AIDC RFID uses an identification tag containing technologies electronically coded data that is attached to the subject item. ▪ Data in read/write tags can be altered for historical usage purposes or to reuse the ▪ The tag consists of a memory microchip and tag an antenna, usually encased in a plastic container Disadvantages ▪ The tag is a transponder ▪ More expensive than most other AIDC technologies. Tag containing electronically coded data. Types of RFID Tags 1. Passive tags - Passive tags have no internal power source - smaller, less expensive, longer lasting, and have a shorter radio communication range. 2. Active tags - include their own battery power packs. - generally possess a larger memory capacity and a longer communication FLEXIBLE MANUFACTURING range (typically 10 m and more) SYSTEM Industrial Applications of RFID Manufacturing system – arrangement or logical arrangement and collection of equipment and ▪ Inventory management human worker. ▪ Supply chain management Flexible – it can accommodate different ▪ Tracking systems product. ▪ Warehouse control Product Variety ▪ Location identification - soft product variety – common process - hard product variety – no common ▪ Work-in-progress process A flexible manufacturing system (FMS) is RFID Advantages and Disadvantages a highly automated Group Technology (GT) Advantages machine cell, consisting of one or more processing stations (usually CNC machine ▪ Identification does not depend on physical tools), interconnected by an automated contact or direct line of sight material handling and storage system and 4. New Part Test. Can it accommodate controlled by a distributed computer system. introduction of new part designs? Group Technology – to identify and to group Types of FMS together the similar parts and processes. ▪ The ▪ Kinds of operations FMS relies on the principles of GT ▪ Processing vs. assembly ▪ No manufacturing system can produce an ▪ Type of processing unlimited range of products ▪ If machining, rotational vs. non-rotational ▪ An FMS is capable of producing a single part family or a limited range of part families ▪ Number of machines (workstations): Where to Apply FMS Technology 1. Single machine cell (n = 1) - consists of one CNC machining center ▪ The plant presently either: combined with a parts storage system ▪ Produces parts in batches or for unattended operation. - The cell can be designed to operate in ▪ Uses manned GT cells and a batch mode, a flexible mode, or a management wants to automate the cells combination of the two. ▪ It must be possible to group a portion of the parts made in the plant into part families ▪ The part similarities allow them to be processed on the FMS workstations ▪ Parts and products are in the mid-volume, mid-variety production range 5000 – 75000 per parts. 2. Flexible manufacturing cell (n = 2 Flexibility Tests in an Automated or 3) Manufacturing System -The cell can be designed to operate in To qualify as being flexible, a manufacturing a batch mode, a flexible mode, or a system should satisfy the following criteria combination of the two. (“yes” answer for each question): - The parts-handling system is connected to a load/unload station. 1. Part-variety test. Can it process different part styles in a non-batch mode? 2. Schedule-change test. Can it accept changes in production schedule? 3. Error-recovery test. Can it respond gracefully to equipment malfunctions and breakdowns? 3. Flexible manufacturing system (n = 4 or more). Workstations - has four or more processing stations connected mechanically by a common - The processing or assembly equipment parts-handling system and electronically used in an FMC or FMS depends on the by a distributed computer system. type of work accomplished by the system. - Loading and Unloading work station - Machine Station and Assembly stations ▪ Load and unload station(s) ▪ Factory interface with FMS ▪ Manual or automated ▪ Includes communication interface with worker to specify parts to load, fixtures FMS Types Level of Flexibility needed, etc. 1. Dedicated FMS Material handling and storage system ▪ Designed to produce a limited variety of part styles - This section covers the functions of the ▪ The complete universe of parts to be handling system, types of handling made on the system is known in equipment used in an FMS, and types of advance FMS layout. ▪ Part family likely based on product ▪ Functions: commonality rather than geometric similarity. ▪ Random, independent movement of parts 2. Random-order FMS between stations ▪ Appropriate for large part families ▪ Capability to handle a variety of part styles ▪ New part designs will be introduced ▪ Production schedule is subject to daily ▪ Standard pallet fixture base changes ▪ Workholding fixture can be adapted ▪ Temporary storage FMS Components ▪ Convenient access for loading and unloading 1. Workstation ▪ Compatibility with computer control 2. Materials handling and storage system ▪ Primary handling system establishes basic 3. Computer control system FMS layout; Function: 4. Human Labor Responsible for moving part to station to station ▪ Secondary handling system - functions: ▪ Transfers work from primary handling system to workstations ▪ Position and locate part with sufficient accuracy and repeatability for the operation ▪ Reorient part to present correct surface for processing 2. FMS Loop Layout ▪ Buffer storage to maximize machine utilization Five Types of FMS Layouts ▪ The layout of the FMS is established by the material handling system ▪ Five basic types of FMS layouts ▪ One direction flow, but variations in 1. In-line processing sequence possible for different part types 2. Loop ▪ Secondary handling system at each 3. Ladder workstation 4. Open field 5. Robot-centered cell 3. FMS Rectangular Layout 1. FMS In-Line Layout ▪ Straight line flow, well-defined processing sequence similar for all work units ▪ Work flow is from left to right through the ▪ Rectangular layout allows recirculation of same workstations pallets back to the first station in the sequence after unloading at the final station ▪ No secondary handling system ▪ Linear transfer system with secondary parts handling system at each workstation to facilitate flow in two directions 4. FMS Ladder Layout FMS Benefits ▪ Loop with ▪ Greater responsiveness to change rungs to ▪ Reduced inventory requirements allow greater ▪ Different parts produced continuously variation in rather than in batches processing ▪ Lower manufacturing lead times sequence. ▪ Reduced labor requirements ▪ Higher productivity ▪ Opportunity for unattended production ▪ Machines run overnight ("lights out operation") 5. FMS Open Field MANUAL ASSEMBLY LINE Layout A production line consisting of a sequence ▪ Multiple loops and of workstations where assembly tasks are ladders, suitable for performed by human workers as the large part families product moves along the line ▪ Organized to produce a single product or a limited range of products ▪ Each product consists of multiple components joined together by various assembly work elements 6. Robot- ▪ Total work content - the sum of all work Centered elements required to assemble one product unit on the line Cell ▪ Factors favoring the use of assembly ▪ Suited to the lines: handling of rotational parts and turning ▪ High or medium demand for operations. product ▪ Identical or similar products ▪ Total work content can be divided into work elements ▪ It is technologically impossible tasks on each work unit within a certain or economically infeasible to automate cycle time, which paces the line to the assembly operations maintain a specified production rate. ▪ Most consumer products are Manual Assembly Line assembled on manual assembly lines - is a production line that consists of a sequence of workstations where assembly tasks are performed by human workers, as depicted - Configuration of a manual assembly line with n manually operated workstations Why Assembly Lines are so Assembly Workstation Productive - A designated location along the work ▪ Specialization of labor flow path at which one or more work - Called “division of labor” by Adam Smith elements are performed by one or more (Historical Note 15.1), this principle workers asserts that when a large job is divided into small tasks and each task is assigned to one worker ▪ Interchangeable parts - In which each component is manufactured to sufficiently close tolerances that any part of a certain type can be selected for assembly with Work Transport Systems its mating component. ▪ Workflow principle ▪ Two basic categories: - which involves moving the work to the ▪ Manual worker rather than vice versa. Each work unit flows smoothly through the ▪ Mechanized production line, traveling the minimum distance between stations. ▪ Line pacing Manual Work Transport Systems - Workers on an assembly line are usually required to complete their assigned ▪ Work units are moved between stations by the workers without the aid of a powered conveyor Types of Mechanized Work Transport ▪ Types: ▪ Continuous transport ▪ Work units moved in batches ▪ Conveyor moves at constant ▪ Work units moved one at a time speed ▪ Problems: ▪ Synchronous transport ▪ Starving of stations - is the ▪ Work units are moved situation in which the assembly operator simultaneously with stop-andgo has completed the assigned task on the (intermittent) motion to next stations current work unit, but the next unit has not yet arrived at the station ▪ Asynchronous transport ▪ Blocking of stations - means that ▪ Work units are moved the operator has completed the independently between workstations assigned task on the current work unit ▪ Queues of work units can form in but cannot pass the unit to the front of each station downstream station because that worker is not yet ready to receive it. Mechanized Work Transport Line Pacing Systems ▪ A manual assembly line operates at a certain cycle time - On average, each ▪ Work units are moved by powered worker must complete his/her assigned conveyor or other mechanized task within this cycle time apparatus ▪ Pacing provides a discipline for the ▪ Categories: assembly line workers that more or less ▪ Work units attached to conveyor guarantees a certain production rate for ▪ Work units are removable from the line conveyor ▪ Several levels of pacing: ▪ Problems 1. Rigid pacing ▪ Starving of stations 2. Pacing with margin ▪ Incomplete units 3. No pacing Rigid Pacing ▪ Allow worker to move beyond station boundaries ▪ Each worker is allowed only a certain fixed time each cycle to complete the No Pacing assigned task ▪ No time limit within which task must be ▪ Allowed time is set equal to the completed cycle time less repositioning time ▪ Each assembly worker works at his/her own pace ▪ Synchronous work transport system provides rigid pacing ▪ No pacing can occur when: ▪ Manual transport of work units is used ▪ Undesirable aspects of rigid pacing: ▪ Work units can be removed from the ▪ Incompatible with inherent conveyor to perform the task human variability ▪ An asynchronous conveyor is used ▪ Emotionally and physically Coping with Product Variety stressful to worker ▪ Single model assembly line ▪ Incomplete work units if task not (SMAL) - produces only one product in large completed quantities. Every work unit is identical, so the task performed at each station is the same for all products. Pacing with Margin ▪ Batch model assembly line ▪ Worker is allowed to complete the task (BMAL) - are designed to produce two or within a specified time range, the upper more products or models, but different limit of which is greater than the cycle approaches are used to cope with the model variations. time ▪ Mixed model assembly line (MMAL) - ▪ On average, the worker’s average task are designed to produce two or more products time must balance with the cycle time of or models, but different approaches are used the line to cope with the model variation ▪ How to achieve pacing with margin: ▪ Allow queues of work units between stations ▪ Provide for tolerance time to be longer than cycle time Automated Production Automated Production Line Lines Fixed-routing manufacturing system that consists of multiple workstations linked together by a material handling system to transfer parts from one station to the next ▪ Slowest workstation sets the pace of the line ▪ Workpart transfer: A pallet fixture is a work-holding device that is designed to (1) fixture the part in a precise ▪ Palletized transfer line location relative to its base and (2) be moved, ▪ Uses pallet fixtures to hold and located, and accurately clamped in position at move workparts between stations successive workstations by the transfer system. ▪ Free transfer line System Configurations ▪ Part geometry allows transfer without pallet fixtures ▪ In-line - straight line arrangement of workstations Where to Use Automated Production Lines ▪ Segmented in-line – two or more straight line segments, usually perpendicular to each other ▪ High product demand ▪ Rotary indexing machine (e.g., dial indexing ▪ Requires large production quantities machine) ▪ Stable product design ▪ Difficult to change the sequence and content of processing operations once the line is built ▪ Multiple operations required on product ▪ The different operations are assigned to different workstations in the line Benefits of Automated Production Lines ▪ Low direct labor content ▪ Low product cost ▪ High production rates ▪ Production lead time and work-in-process are minimized Control Functions in an Automated Production Line Sequence control To coordinate the sequence of actions of the transfer system and workstations Safety monitoring To avoid hazardous operation for workers and equipment Quality control To detect and possibly reject defective work units produced on the Storage Buffers in Production Lines line. A location in the sequence of workstations where parts can be collected and temporarily stored before proceeding Automated Assembly Systems to subsequent downstream stations The term automated assembly refers to Reasons for using storage buffers: mechanized and automated devices that perform various assembly tasks in an assembly To reduce effect of station breakdowns line or cell. To provide a bank of parts to supply The use of mechanized and automated the line devices to perform the various assembly tasks To provide a place to put the output of in an assembly line or cell the line ▪ Fixed automation usually To allow curing time or other required ▪ Most automated assembly systems are delay designed to perform a fixed sequence of To store parts between stages with assembly steps on a specific product that is different production rates\ produced in very large quantities Automated Assembly - Application Characteristics ▪ Where is automated assembly appropriate: ▪ High product demand ▪ Stable product design ▪ The assembly consists of no more than a limited number of components it indexes from station to station Carousel Assembly System A hybrid between circular work flow of dial indexing machine and straight work flow of in- line system System Configurations Single-Station Assembly Cell 1. In-line assembly machine Assembly operations are performed on a 2. Dial indexing machine base part at a single location 3. Carousel assembly system ▪ A robot is sometimes used as the assembly machine 4. Single-station assembly cell In-Line Assembly Machine A series of automatic workstations located along and in-line transfer system Either synchronous or asynchronous work transfer used Parts Delivery at Workstations ▪ Typical parts delivery system at a workstation consists of the following hardware components: Dial Indexing Machine 1. Hopper - container for parts Base parts are loaded onto fixtures or 2. Parts feeder - removes parts from hopper nests attached to a circular dial table, and 3. Selector and/or orientor - to assure part components are added at workstations is in proper orientation for assembly at located around the periphery of the dial as workhead 4. Feed track - moves parts to assembly Feed Track workhead ▪ Moves parts from hopper to assembly 5. Escapement and placement device - workhead removes parts from feed track and places ▪ Categories: them at station 1. Gravity - hopper and feeder are located at Parts Delivery System at Station higher elevation than workhead 2. Powered - uses air or vibration to move parts toward workhead Escapement and Placement Device Escapement device Removes parts from feed track at time intervals that are consistent with the cycle time of the assembly workhead Placement device Physically places the parts in the correct Selector and/or Orientor location at the assembly workstation Purpose - to establish the proper Escapement and placement devices are orientation of the components for the sometimes the same device, sometimes assembly workhead different devices ▪ Selector ▪ Acts as a filter ▪ Only parts in proper orientation are allowed to pass through to feed track ▪ Orientor ▪ Allows properly oriented parts to pass ▪ Reorients parts that are not properly oriented Parts Selection and Orientation INSPECTION TECHNOLOGIES Inspection Metrology Measurement - a procedure in which an unknown quantity is compared to a known standard, using an accepted and Analog vs Digital Instrument consistent system of units Analog measuring instrument – output The means by which inspection by signal varies continuously with the variable variables is accomplished being measured Metrology – the science of Output signal can take on any of an infinite measurement number of possible values over its operating Concerned with seven basic quantities: range length, mass, electric current, Digital measuring instrument – can temperature, luminous intensity, time, assume any of a discrete number of and matter incremental values corresponding to the From these basic quantities, other variable being measured physical quantities are derived Number of possible output values is finite Characteristics of Measuring Advantages: o Ease of reading the Instruments instrument o Ease of interfacing to a ▪ Accuracy – how closely the measured compute value agrees with the true value Two Basic Types of Inspection ▪ Precision – a measure of the Techniques repeatability of the measurement process 1. Contact inspection Makes contact ▪ Resolution – the smallest variation of with object being inspected the variable that can be detected 2. Noncontact inspection Does not ▪ Speed of response – how long the make contact with object being inspected instrument takes to measure the variable Contact Inspection Techniques ▪ Others: operating range, reliability, cost Uses a mechanical probe that makes contact with the object being measured or gaged Principal techniques: Conventional measuring and gaging instruments, manual and automated Coordinate measuring machines Stylus type surface texture Coordinate Metrology measuring machines Concerned with the measurement of the Noncontact Inspection Techniques actual shape and dimensions of an object and comparing these with the desired shape and Uses a sensor or probe located a certain dimensions specified on a part drawing distance away from the object being measured or gaged Coordinate measuring machine (CMM) – an electromechanical system designed to Two categories: perform coordinate metrology Optical – uses light to accomplish A CMM consists of a contact probe that can the inspection be positioned in 3-D space relative to workpart Nonoptical - uses energy form features, and the x-y-z coordinates can be other than light displayed and recorded to obtain dimensional data about geometry Advantages of noncontact inspection: Coordinate Measuring Machine Avoids possible damage to surface of object Inherently faster than contact inspection Can often be accomplished in production without additional part handling Increased opportunity for 100% inspection Conventional Measuring and Gaging Techniques CMM Components Measuring instruments - provide a quantitative value of the part feature of Probe head and probe to contact workpart interest surfaces Examples: o Steel rules, calipers, Mechanical structure that provides motion of micrometer, dial indicator, protractor the probe in x-y-z axes, and displacement transducers to measure the coordinate values Gages - determines whether a part of each axis feature falls within a certain acceptable range Optional components (on many CMMs): Examples: o Snap gages for external Drive system and control unit to move dimensions, plug gages for hole diameters, each axis thread gages Digital computer system with application software Contact Probe Configurations construction of a machine tool. The x- and y-axis movements are achieved by moving the worktable, while the probe quill is moved vertically along a rigid column to achieve z- axis motion. CMM Mechanical Structure Six common types of CMM mechanical structures: 1. Cantilever - the probe is attached to a vertical quill that moves in the z-axis direction relative to a horizontal arm that overhangs a fixed worktable. 2. Moving bridge - the probe is mounted on a bridge that is translated relative to a stationary table on which the part is positioned to be measured. 3. Fixed bridge - the bridge is attached to the CMM bed, and the worktable is moved in the x-direction beneath the bridge. 4. Horizontal arm - The horizontal arm configuration consists of a cantilevered horizontal arm mounted to a vertical column. The arm moves vertically and in and out to achieve y-axis and z-axis motions. 5. Gantry - is generally intended for inspecting large objects. The probe quill CMM Operation and Controls – Four (z-axis) moves relative to the horizontal Main Categories arm extending between the two rails of 1. Manual drive CMM – human operator the gantry. physically moves the probe and records x-y- 6. Column - is similar to the z- data 2. Manual drive and computer- general all measurements of a given part assisted data processing – can perform can be made in one setup calculations to assess part features Surface Measurement 3. Motor-driven CMM with Most surface measuring devices use a computer-assisted data processing – contacting stylus uses joystick to actuate electric motors to drive probe Therefore, classified as contact inspection 4. Direct computer control (DCC) – As stylus is traversed across surface, tip operates like a CNC machine tool and also moves vertically to follow the surface requires part program topography DCC Programming Movement is converted to electronic signal that can be displayed as either Manual leadthrough 1. Profile of the surface Operator leads the CMM probe through the various motions in the inspection 2. Average roughness value of the sequence, indicating points and surfaces surface to be measured and recording these into control memory Machine Vision Off-line programming Acquisition of image data, followed by the Program includes motion commands, processing and interpretation of these data by measurement commands, and report computer for some useful application formatting commands and is prepared off-line Also called “computer vision” Machine Vision Applications Advantages of Using CMMs over 1. Inspection: Manual Inspection Dimensional measurement Reduced inspection cycle time – Dimensional gaging translates to higher throughput rate Verify presence or absence of Especially with DCC, approximately components in an assembly (e.g., PCB) 90% reduction in certain tasks Verify hole locations or number of Flexibility – CMMs are general- holes purpose machines Detection of flaws in printed labels Reduced operator errors in 2. Identification – for parts sorting or measurement and setup counting Greater inherent accuracy and 3. Visual guidance and control – for precision bin picking, seam tracking in continuous Avoidance of multiple setups – in arc welding, part positioning.