Chapter 1 LM.pptx PDF
Document Details
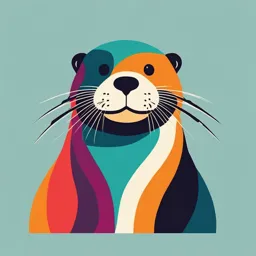
Uploaded by FastCanyon
Tags
Related
- Handling and Packaging Management PDF
- Reference Material-Introduction to Operations and Supply Chain Management PDF
- Supply Chain Associate Participant Handbook PDF
- Chapter 4: Logistical Processes In International Environments PDF
- Railway Store Department Code Vol-1, Ch-1 PDF
- Logistics Final Review PDF
Summary
This document provides an overview of logistics, defining it as the flow of material, information, and money between consumers and suppliers. It details the evolution of logistics through various phases, including workplace, facility, corporate, supply chain, and global logistics. Key concepts like economic utilities (e.g., place, time) are discussed.
Full Transcript
Chapter 1 An Overview of Logistics 1 2 1.1. Basic Concepts/Meanings of Logistics Logistics is the flow of material, information, and money between consumers and suppliers. Logistics is a process of managing and coordinating the flow of materials and information with...
Chapter 1 An Overview of Logistics 1 2 1.1. Basic Concepts/Meanings of Logistics Logistics is the flow of material, information, and money between consumers and suppliers. Logistics is a process of managing and coordinating the flow of materials and information within the 3 What is Logistics? Logistics definitions provided in Table 2- 1 on the following slide. 4 Table 2-1: Logistics Definitions 5 Logistics Definitions 6 What is Logistics? Popular logistics terms: Logistics Management Business Logistics Management Integrated Logistics Management Materials Management Physical Distribution Management Marketing Logistics Industrial Logistics Distribution 7 What is Logistics?: 21st Century View of Logistics Logistics is an area of management that has four sub- disciplines: business, military, service, and event. Business Logistics – supply chain process that plans, implements, and controls the efficient, effective flow of goods, services, and related information from the point of origin to the point of use or consumption in order to meet customer requirements. Military Logistics – design and integration of all aspects of support for the operational capacity of the military forces, and their equipment to ensure 8 readiness, reliability, and efficiency. What is Logistics?: 21st Century View of Logistics Event Logistics – network of activities, facilities, and personnel required to organize, schedule, and deploy the resources for an event to take place and to efficiently withdraw after the event. Service Logistics – acquisition, scheduling, and management of the facilities/assets, personnel, and materials to support and sustain a service operation or business. 9 What is Logistics?: Value-Added Role of Logistics Logistics is necessary to: Move goods from suppliers to buyers Move finished goods to the customer Products have little value to the customer until they are moved to the customer’s point of consumption Time utility- products are delivered at the right time. Place utility- products are delivered to the desired location. What is Logistics?: Value-Added Role of Logistics Most commonly referred to in terms of economic utilities: Form utility (what) Place utility (where) Time utility (when) Possession utility (why) Also referred to as the seven Rs --- Right product, Right quantity, Right condition, Right place, Right time, Right customer, and Right cost. 11 Figure 2.2 Utility Creation in the Economy Source: Center for Supply Chain Research, Penn State University Logistics adds place, time, and quantity utilities to products and enhances the form and possession utilities added by manufacturing and marketing. Economic utilities and means that add value to a product or service in the SCM Production Form Utility (by assembling parts into finished goods) Logistics Place Utility (by moving goods to where demand is) Time Utility (by moving goods when demand exists) Quantity Utility (by offering the right quantity) Marketing Possession Utility (by promotion and sale to 14 15 Logistics Defined Traces its origin to: Greek word logistikos meaning ‘skilled in calculating’ Latin word logisticus Meaning the science of computing and calculating. In ancient times, the term was frequently used in connection with moving armies and supplies of food and armaments to the war front. Its use can be traced back to 17th Century in French army. 16 Logistics Defined – Cont... It gained importance in army operations during WWII as it was used in reference to movement of supplies, men, and equipment across the border. The US army officially used the word after WWII. Today logistics has acquired a wider meaning and is used in business to refer to movement of raw materials from suppliers to the manufacturer and finished goods to the consumers. 17 Just a thought!!!! What is Logistics = Logical thinking + Statistics 18 Definitions – Cont… Logistics refers to the movement of materials within a production facility and to incoming (inbound/upstream) and outgoing (outbound/downstream) shipments of goods and materials. (William J. Stevenson) 19 Definitions – Cont... “Logistics is that part of SCM that plans, implements, and controls the efficient, effective forward and reverse flow and storage of goods, services, and related information between the point of origin and point of consumption in order to meet customers’ requirements.” (Council of Supply Chain Management Professionals) 20 21-21 A Generalization of a Typical Logistics System Raw Materials Raw Materials Finished Goods Markets Supply Points Storage Manufacturing Distribution Movement/ Movement/ Movement/ Movement/ Transportation Transportation Transportation Transportation Distribution Storage Plant 1 Center A Distribution Storage Plant 2 Center B Storage Plant 3 Distribution Center C 21-22 1.2. The Evolution of Logistics Logistics has evolved in scope and influence in the private sector since the mid to late 1940s. In the 1950s and ‘60s, the military was the only organization using the term logistics. There was no true concept of logistics in private industry at that time. Instead, departmental divisions including material handling, warehousing, machining, accounting, marketing, 23 This evolution has passed through the following five phases of logistics development— 1. workplace logistics, 2. facility logistics, 3. corporate logistics, 4. supply chain logistics, and 5. global logistics 24 1. Workplace Logistics/ Ergonomics Workplace logistics is the flow of materials within a single workstation. The objective of workplace logistics is to streamline the movements of an individual working at a machine or along an assembly line. The principles and theory of workplace logistics were developed by the founders of industrial 25 26 2. Facility Logistics Facility logistics is the flow of material between workstations within the four walls of a facility (that is, inter- workstation and intra-facility). The facility could be a factory, terminal, warehouse, or distribution center. Facility logistics has been more commonly referred to as material handling The roots of facility logistics was in the mass 27 28 3. Corporate Logistics As management structures advanced and information systems accordingly, the ability to assimilate and synthesize departments (material handling, warehousing, and so on) into functions (physical distribution and business logistics) in the 1970s permitted the first application of true logistics within a corporation Corporate logistics became a process with the common objective to develop and maintain a profitable customer service policy while maintaining and reducing total logistics costs. Corporate logistics is the flow of material and information between the facilities and processes of a corporation (inter-workstation, inter-facility, and intra-corporate). Corporate logistics is sometimes associated with the phrase physical distribution that was popular in the 1970s. 29 30 4. Supply Chain Logistics Supply chain logistics is the flow of material, information, and money between corporations (inter-workstation, inter-facility, inter-corporate, and intra-chain). There is a lot of confusion surrounding the terms logistics and supply chain management. We can distinguish b/n the two by explaining that: “the supply chain is the network of facilities (warehouses, factories, terminals, ports, stores, and homes), vehicles (trucks, trains, planes, and ocean vessels), and logistics information systems (LIS) connected by an enterprise’s supplier’s suppliers and its customer’s customers.” Logistics is what happens in the supply chain. Logistics activities (customer response, inventory management, supply, transportation, and warehousing) connect and activate the objects in the supply chain. What do you think is the difference between SC31 SCM: GENERAL FUNCTIONS MANAGING FLOWS – Information, Materials, and Money SUPPLIER’S FOCAL CUSTOMER’S SUPPLIERS CUSTOMERS SUPPLIERS FIRM CUSTOMERS Information, materials, and money flow freely back-and-forth between the supply chain entities. This ever-present need for information, materials, and money is what drives the need for cooperation in supply chains. The best supply chains typically have the best flows. 33 5. Global Logistics Global logistics is the flow of material, information, and money between countries. Global logistics connects our suppliers’ suppliers with our customers’ customers internationally. Global logistics flows have increased dramatically during the last several years due to globalization in the world economy, expanding use of trading blocs, and global access to Web sites for buying and selling merchandise. 34 35 6. Next-Generation Logistics There are many theories as to the next phase of logistics development. Many logisticians believe that collaborative logistics, logistics models built with continuous and real-time optimization and communication between all supply chain partners will be the next phase of evolution. Other camps in the logistics community believe the next phase of evolution will be virtual logistics or fourth-party logistics, where all logistics activities and management will be outsourced to third-party logistics providers who are in turn managed by a master or fourth-party logistics providers acting kind of like a general contractor. 36 37 LOGISTICS ACTIVITIES In our definition, logistics is comprised of five interdependent activities: customer response, inventory planning and management, supply, transportation, and warehousing. 38 12/21/2024 Matiwos Ensermu(PhD) 39 Customer Response Customer response links logistics externally to the customer base and internally to sales and marketing. Customer response is optimized when the customer service policy (CSP) yielding the lowest cost of lost sales, inventory carrying, and distribution is identified and executed 40 Inventory Planning and Management The objective of inventory planning and management (IP&M) is to determine and maintain the lowest inventory levels possible that will meet the customer service policy requirements stipulated in the customer service policy. 41 Supply Supply is the process of building inventory (through manufacturing and/or procurement) to the targets established in inventory planning. The objective of supply management is to minimize the total acquisition cost (TAC) while meeting the availability, response time, and quality requirements stipulated in the customer service policy and the inventory master plan 42 Transportation Transportation physically links the sources of supply chosen in sourcing with the customers we have decided to serve chosen as a part of the customer service policy 43 Warehousing Warehousing is the last of the five logistics activities because good planning in the other four activities may eliminate the need for warehousing or may suggest the warehousing activity be outsourced 44 45 1.3. Logistics versus SCM Many logistics veterans believe we have progressed from transportation physical distribution logistics supply chain management. By contrast, purchasing managers have evolved their thinking from purchasing management procurement supply chain management (SCM). So what makes SCM different from logistics? 46 …………………………………………………………… Manufacturing professionals hold a perception of SCM: the task of allocating and as committing resources for obtaining necessary supplies and capacity, handling, and positioning products to meet customer demands. In marketing—as well as the broader functionality that includes business and consumer research, promotions, and sales—SCM addresses the needs and market potential of not only immediate customers and consumers who buy products and services, but also 47 Logistics vs SCM 48 Logistics and Supply Chain Management Three views on the relationship between logistics and SCM Logistics vs SCM Some authors regard SCM and Logistics as synonymous. Cooper (1997) regards Logistics as concerned with material and material flows and SCM as the integration of all business processes across the supply chain. 50 Logistics vs SCM – Cont... According to the UK Institute of Logistics and Transport: LM makes possible the optimized flow and positioning of goods, materials, information and all resources of an enterprise. SC is the flow of materials through procurement, manufacture, distribution, sales and disposal, together with the associated transport and storage. SCM views the SC as a single entity and thus demands system integration. 51 1.4 Objectives of Business Competing through Logistics Logistics Organisations of today have to be adept at managing a number of goals and objectives to be successful. Often these goals and objectives appear to be at conflict with one another. For example an organisation does not want to incur the monetary cost of carrying a high level of inventory but at the same time it must carry enough in order to be responsive on delivery to any reasonable rise in unforecasted customer demand. Against this backdrop customers, once they have decided to purchase, typically want the product or service now and at minimum cost. These factors have a strong influence on the design of the supply chain. Competing through Logistics To be successful and gain that crucial competitive advantage the various partners must come together to identify the critical success factors for the supply chain as a whole and the key capabilities they must each individually have or develop through investment in training, processes, quality etc. Competing through Logistics Organisations cannot do everything all of the time. They have a finite level of resource that means they have to develop their ability to prioritise and focus on the right activities. This brings us back to the need for alignment across the supply chain. Let us look at the competitive priorities that can be delivered by logistics in the supply chain. Competitive Advantage There are various ways in which products compete in the marketplace. For example; Quality Price Technical features Brand name Competitive Advantage Product availability in the marketplace at low cost is a key advantage provided by logistics. Logistics supports competitiveness of the supply chain as a whole by: …meeting end customer demand through supplying what is needed, in the form it is needed, when it is needed, at a competitive cost. 1.4.1 Hard Objectives The Quality Advantage The most fundamental objective, in that it is a foundation for all the other, is to carry out all processes across the supply chain so that the end product does what it is supposed to do. Quality is the most visible aspect of the supply chain. Business processes must be designed to not just meet the needs of customers, but to delight them. The Quality Advantage Many things influence customer loyalty: product does what it is supposed to do value for money quality of processes way the customer is treated quality of the staff in the organisation organisation makes a commitment and keeps that commitment The Quality Advantage Product unavailability, defects and late deliveries are all symptoms of quality problems in supply chain processes. Such problems are visible to the end customer, and negatively influence that customer’s loyalty. The Quality Advantage Robust processes are at the heart of supply chain performance. Through the adherence to process management, defects or errors will be highlighted earlier reducing the impact on customer and cost. Commitment to quality and a customer- centred attitude must start at senior management and permeate down through, all levels of the organisation and every organisation in the supply chain. The Time Advantage The time a customer has to wait to receive a given product or service is measured. Volkswagen calls this time the customer lead- time: that is, the time it takes from the moment a customer places an order to the moment that customer receives the car they have specified. Such lead-times can vary from zero (the product is immediately available, such as goods on a supermarket shelf) to months or years (such as the construction of a new building). The Time Advantage Companies that have learned that some customers don’t want to wait can use time to win orders. They are prepared to pay a premium to get what they want quickly. An example is Vision Express, which offer prescription spectacles, ‘in about one hour’. Technicians machine lenses from blanks, on the premises. Staff are given incentives to maintain a 95% service level against the one-hour target. Vision Express has been successful in the marketplace by re-engineering the supply chain so that parts and information can flow rapidly from one process to the next. Compare this with other opticians in the high street, who must send customer orders to a central factory. The Time Advantage Under the remote factory system, orders typically take about 10 days to process. An individual customer’s order must be dispatched to the factory and then compete in a queue with orders from all the other high street branches around the country. Once it has been processed, it must return to the branch that raised the order. While this may be cheaper to do (a single, remote factory replaces many small factories in the branches), it takes much longer. The Cost Advantage Cost is important for all supply chain processes. Low costs translate into advantages in the marketplace in terms of low prices or high margins, or a bit of both. Many products compete specifically on the basis of low price. From a supply chain point-of-view this may translate into low-cost manufacture, distribution and servicing. The Cost Advantage Examples of products that compete on low price are supermarkets’ own brand goods that reduce the high margins and heavy advertising spend of major brands. They also perhaps cut some of the corners in terms of product specification in the hope that the customer will consider low price as being more important than minor differences in product quality. The Cost Advantage The pressure to reduce prices at car component suppliers is intense. The assemblers have been setting annual price reduction targets for their inbound supply chains for some years. Unless a supplier can match reduced prices for which products are being sold, by reducing costs, that supplier will gradually go out of business. As a result, many suppliers are cynical about the price down policies of the assemblies. The Cost Advantage The benefit of cutting costs is reduced prices, often a collaborative effort on the part of several partners in the supply chain. Tesco can make only limited in-roads into its in-store costs without collaboration from its supply chain partners. Many small UK dairy farmers are being forced out of business, because the price of milk in supermarkets is less than the price of water. For them, there are few opportunities to cut costs. 1.4.2 Supportive Capabilities Controlling Variability: The Dependability Advantage Time is not just about speed. It is also about meeting promises. Organisations can do themselves a power of good by adopting one clear but very simple message: make a promise and keep that promise. Questions an organisation should be asking itself: are we always meeting our delivery promises do we answer calls when we said, how we said and answer what the customer wanted reflect the right standards and commitments, can I make promises knowing that the company will be able to fulfil them. The Dependability Advantage Firms who do not offer instantaneous availability need to tell the customer when the product or service will be delivered. Delivery dependability measures how successful the firm has been in meeting those promises. For example, the UK based Royal Mail offers a first class service for letters where there is a 92% chance that a letter posted today will reach its destination tomorrow. The Dependability Advantage It is important to measure dependability in the same end to end way that speed is measured. Although Vision Express offers a one-hour service for prescription glasses, the 95% service level target is a measure of the dependability of that service. Dependability measures are widely used in industries such as train and air services to monitor how well published timetables are met. In manufacturing firms, dependability is used to monitor a supplier’s performance in such terms as: > On time (% orders delivered on time) > In full (% orders delivered complete) > On quality (% of defects, and the variability against target) Dealing with Uncertainty: The Agility Advantage An organisation needs robust and predictable processes to provide the foundation for supply chain processes. This is no different for dependability if the organisation wants to gain an important advantage. Toyota UK manages inbound deliveries of parts from suppliers in southern Europe by a process called chain logistics. Trailers of parts are moved in four-hour cycles, they are then exchanged for the returning empty trailer on its way back from the UK. Dealing with Uncertainty: TheAgility The Flexibility Advantage … Advantage While doing things the same way at the same time may be good from a point of view of keeping costs down, few markets are in tune with such an idealised way of doing business. A supply chain needs to be responsive, to new products and markets, and to changing customer-demand. This means in turn that it must be capable of changing what is done. The Flexibility Advantage Flexibility takes four forms: Product Flexibility which measures how quickly a new product can be introduced Mix Flexibility which measures the time it takes to change between different products in a given range. Volume Flexibility which measures the time it takes to respond to increases or decreases in overall demand Delivery Flexibility which measures the ability to change deliveries (intentionally) by bringing them forward or pushing them back. 1.4.3 Soft Objectives Logistics is not the only way in which product competitiveness in the marketplace can be enhanced. The performance objectives listed above can be added to (and in some cases eclipsed by) other ways in which products may win orders, such as design and marketing features. Thus superior product or service design, often supported by brand image, may create advantage in the marketplace, as it does for BMW cars and the Dorchester Hotel, for example. Here, the logistics task is to support the superior design. BMW’s supply chain is one of the most efficient there is, mainly because its products are sold (at least in Europe) as soon they have been made. Finished cars do not accumulate in storage on airfields like those of the mass producers. Storing finished products adds cost, with no value added to the end consumer. Logistics Systems Costs Costs Order OrderProcessing Processing Minimize MinimizeCosts Costsof of Submitted Submitted Attaining Logistics Attaining Logistics Processed Processed Objectives Objectives Shipped Shipped Logistics Transportation Functions Warehousing Warehousing Water, Truck, Rail, Storage Pipeline & Air Storage Distribution Distribution Inventory Inventory When Whento toorder order How How much toorder much to order Just-in-time Just-in-time 1.5 Functions of Logistics Given a set of logistics objectives, the company is ready to design a logistics system that will minimize the cost of attaining these objectives. The major logistics functions include order processing, warehousing, inventory management and transportation. Order Processing The orders once received, must be processed quickly and accurately. The order processing system prepares invoices and sends order information to those who need it. The appropriate warehouse receives instruction to pack and ship the ordered items. 78 Cont’d Shipped items are accompanied by shipping and billing documents, with copies going to various departments. Both the company and its customers benefits when the order- processing steps are carried out efficiently. Warehouse Every company must store its goods while they wait to be sole. A storage function is needed because production and consumption cycles rarely match. A company must decide on how many and what types of warehouse it needs, and where they will be located. Cont’d The more warehouse the company uses, the more quickly goods can be delivered to customers. However, more locations mean higher warehousing costs. The company, therefore, must balance the level of customer service against distribution costs. Inventory Inventory levels also affect customer satisfaction. The major problems to maintain the delicate balance between carrying too much inventory and carrying too little. Cont’d Carrying too much inventory results in higher-than necessary inventory carrying costs and stock obsolescence. Carrying too little may result in stock-outs, costly emergency shipments or production, and customer dissatisfaction. In making inventory decisions, management must balance that costs of carrying larger inventories against resulting sales and profit. Inventory decisions involve knowing both when to order and how much to order. Cont’d In deciding when to order, the company balances the risks of running our of stock against the cost of carrying too much. In deciding how much to order, the company needs to balance order-processing costs against inventory carrying costs. Larger average-order size results in fewer orders and lower order-processing costs, but it also means larger inventory carrying costs. Cont’d Transportation Marketers need to take an interest in their company’s transportation decisions. The choice of transportation carries affects the pricing of products, delivery performance, and condition of the goods when they arrive – all of which will affect customer satisfaction. Cont’d The company can choose among five transportation modes: road, rail, sea, air and pipeline. In choosing a transportation mode for a product, senders consider as many as five criteria, viz. speed, dependability, capability, availability and cost.