Construction Equipment Operations & Management PDF
Document Details
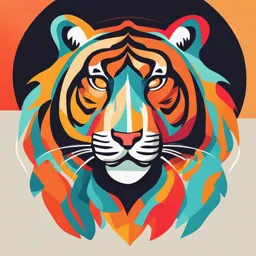
Uploaded by CheerfulCotangent3675
Universidad de Dagupan
Tags
Summary
This document provides an overview of construction equipment operations and management. It discusses different types of construction equipment, selection criteria, and maintenance. It also covers important aspects of equipment management.
Full Transcript
CONSTRUCTION OPERATION "Construction operations" means operations of any of the following descriptions: 1. The construction, alteration, repair, extension, demolition or dismantling of buildings or structures; 2. The construction, alteration, repair, extension or demolition of any works...
CONSTRUCTION OPERATION "Construction operations" means operations of any of the following descriptions: 1. The construction, alteration, repair, extension, demolition or dismantling of buildings or structures; 2. The construction, alteration, repair, extension or demolition of any works forming, or to form, part of the land, including walls, road-works, power lines, telecommunication apparatus, aircraft runways, docks and harbors, railways, inland waterways, pipelines, reservoirs, water mains, wells, sewers, industrial plant and installations for purposes of land drainage; 3. The installation in any building or structure of systems of heating, lighting, air- conditioning, soundproofing, ventilation, power supply, drainage, sanitation, water supply, burglar or fire protection; The external cleaning of buildings (other than cleaning of any part of a building in the course of normal maintenance) or the internal cleaning of buildings and structures, in so far as carried out in the course of their construction, alteration, extension, repair or restoration; 4. The external cleaning of buildings (other than cleaning of any part of a building in the course of normal maintenance) or the internal cleaning of buildings and structures, in so far as carried out in the course of their construction, alteration, extension, repair or restoration; 5. Operations which form an integral part of, or are preparatory to, or are for rendering complete such operations as are described in paragraphs (a) to (d), including site clearance, earth-moving, excavation, tunneling and boring, laying of foundations, erection of scaffolding, site restoration, landscaping and the provision of roadways and other access works; 6. Operations which form an integral part of, or are preparatory to, or are for rendering complete, the drilling for or extraction of minerals, oil, natural gas or the exploration for, or exploitation of, natural resources; 7. The haulage for hire of materials, machinery or plant for use, whether used or not, in any of the construction operations referred 1|Page CONSTRUCTION EQUIPMENT Construction Equipment refers to heavy-duty vehicles, specially designed for executing construction tasks, most frequently ones involving earthwork operations. They are also known as heavy machines, heavy trucks, heavy equipment, engineering equipment, heavy vehicles, or heavy hydraulics. They usually comprise five equipment systems: implement, traction, structure, power train, control and information. Heavy equipment functions through the mechanical advantage of a simple machine, the ratio between input force applied and force exerted is multiplied. Some equipment uses hydraulic drives as a primary source of motion. EQUIPMENT SELECTION Typically, construction equipment is used to perform essentially repetitive operations, and can be broadly classified according to two basic functions: 1) Operators such as cranes, graders, etc. which stay within the confines of the construction site, and 2) Haulers, such as dump trucks, ready mixed concrete truck, etc. which transport materials to and from the site. In both cases, the cycle of a piece of equipment is a sequence of tasks which is repeated to produce a unit of output. For example, the sequence of tasks for a crane might be to fit and install a wall panel on the side of the building; similarly, the sequence of task of a ready mixed concrete truck might be to load, haul and unload one truck load of fresh concrete. One of the most important tasks in the pre-construction planning process is equipment selection. There are many variables to consider when selecting equipment. Following factors should be considered at the time of selecting construction equipment: 1. The Equipment should be Standard Equipment if possible. 2. It should give the best service at low cost. 3. Its unit cost of production should be moderate. 4. It should be easily repairable with low shutdown period 5. It should be easily disposed off 6. It should suit the majority of the requirements of the job. 7. It should be capable of doing more than one function. 8. It should be of moderate size, as they have fewer moving parts and have low working cost. 2|Page HEAVY EQUIPMENT OPERATION Not everyone is fit to operate equipment. If you wish to operate equipment, one must undergo training. The purpose of the program is to familiarize and prepare the operator of the usage and specialties of the equipment in the different maintenance job in forestry, trucking, earth moving, or construction industries. Through intensive shop and field oriented courses, students are introduced to a variety of heavy equipment and learn to operate and maintain, repair and rebuild it. Emphasis is placed on the maintenance of drive train, running gear, external engine components, and hydraulic systems, as well as on the proper operation of bulldozers, trucks, pay- loaders, backhoes, and other heavy equipment. TYPES OF CONSTRUCTION EQUIPMENT 1. Earth Moving Equipment 2. Construction Vehicle 3. Material Handling Equipment 4. Construction Equipment EARTH MOVING EQUIPMENT Earth moving equipment are large, heavy duty vehicles that are often seen in the mining and construction sites to move and relocate heavy materials, rocks, and mud, dirt and debris or lumber. The following are examples of earth moving equipment: 3|Page Excavators: An excavator is a construction vehicle used to excavate or move large objects. An Excavator is basically made up of 2 parts: a driving base associated a powerful boom arm with an attachment designed for excavating. The operator sits within a small cab connected to the base and controls the arm. Graders: Graders are mostly been used in road construction for construction and maintenance of dirt roads and gravel roads. The grader typically consist of three axles, with the engine and cab situated top, the rear axles at one end of the vehicle and a third axle at the front end of the vehicle, with the blade in between. Loader: Loader is a heavy equipment machine frequently used in construction industry, mainly used to Load material (such as demolition waste, feed, gravel raw minerals, used material ,rock, and plywood) into or onto another type of machinery (such as a dump truckload) 4|Page Backhoe: A backhoe, also known a rear actor or back actor, is a section of excavating equipment or digger consisting of a digging bucket on the end of a two-part articulated arm. They are typically mounted on the back of a tractor or front loader. Crawler Loader: The crawler loader combines the stability of the crawler tractor with the abilities of a wheel loader. However, to construct a reliable crawler loader it requires more than simply attaching a loader bucket onto a crawler tractor. It must be considered with its specific purpose in mind to ensure. It has the strength to survive heavy excavating Bulldozer: A bulldozer is a crawler (continuous Tracked tractor) with a substantial metal plate used (known as blade) fitted to push large amounts of soil, sand, dirt or other materials when construction or remodeling and usually push on the back with a claw mechanism (Known as ripper) to loosen densely-compacted materials 5|Page Ditches: Ditchers or Trenches, are similar to excavator in the sense that penetrate the soil, break soil and rock, and from the earth. They differ from excavators in that the soil is removed in one continuous movement. Digging trenches for pipes used specifically for, but other machines have been improvised in the past in order to serve this purpose. Scraper: The scraper is a large piece of equipment used in mining, construction, agriculture and other earth moving applications. Loading Shovel: Loading shovels are loaded where it counts, pushing the front end bucket loader efficiency higher. From mini loaders to large production machines, find the right fit for the work in load and carry operations, civil & building construction, earth moving, waste handling, recycling, landscaping, quarrying, aggregates, block handling, lumber yards, agriculture and more. 6|Page CONSTRUCTION VEHICLE Construction vehicles are designed huge to transport engineering materials from one place to another. Tippers: Tippers are suited for the rough and tumble of mining & quarrying operations, as well as for carrying bulk loads in construction and infrastructure industries. Complete maneuverability, high performance and long-term endurance are common to all trucks, resulting in lower operational costs. Trailer: A trailer is generally an unpowered vehicle towed by a powered vehicle. It is commonly used for the transport of goods and materials. Tank truck: A tank truck (USA usage) or road tanker (UK usage) is a motor vehicle designed to carry liquefied loads, dry bulk cargo or gases on roads. The largest such vehicles are similar to railroad tank cars which are also designed to carry liquefied loads. Many variants exist due to the wide variety of liquids that can be transported. In construction its use for carrying concrete mixed 7|Page MATERIAL HANDLING EQUIPMENT Material handling equipment are used to assist other equipment by conveying, hoisting and lifting, and others. The following are example of handling equipment: 8|Page Crane: Cranes are commonly employed in the transport industry for the loading and unloading of goods for the movement of materials and manufacturing industries for mounting agricultural machinery, in the construction industry. Conveyor: Conveyors are mainly useful in applications involving the transportation of heavy or bulky materials. Conveyor systems allow quick and efficient transportation for a wide variety of materials, which make them very popular in construction Hoist : Hoist is a device for raising or lowering a load by means of a drum or wheel lift to which wraps the rope or chain. It can be operated by hand, is driven electrically or pneumatically, and the chain or wire rope fibers are used as lifting device. Forklift trucks: Forklift trucks are available in many variations and load capacities. In a typical warehouse setting most forklifts used have load capacities between one to five tons. Larger machines, up to 50 tons lift capacity are used for lifting heavier loads. CONSTRUCTION EQUIPMENT These are equipment used in the construction site to ease the labor of mixing, compacting and the like. The following are examples: 9|Page Concrete Mixer: A Concrete (Cement Mixer) is a machine that combines cement evenly to form aggregates such as sand or gravel and water to concrete. A typical concrete mixer using a rotating drum for mixing the components. Compactor: Compactor is a machine or mechanism used to material soil through compaction in construction industry. Road roller : Road roller (sometimes called a roller-compactor, or just roller) is a compactor type engineering vehicle used to compact soil, gravel, concrete, or asphalt in the construction of roads and foundations, similar rollers are used also at landfills or in agriculture. Paver: A paver (paver finisher, asphalt finisher, paving machine) is an engineering vehicle used to lay asphalt on roadways. It is normally fed by a dump truck. A separate machine, a roller, is then used to press the hot asphalt mix, resulting a smooth, even surface. 10 | P a g e CONSTRUCTION TOOLS AND OTHER EQUIPMENT Air compressors and pumps are widely used as the power sources for construction tools and equipment. Common pneumatic construction tools include drills, hammers, grinders, saws, wrenches, staple guns, sand blasting guns and concrete vibrators. Pumps are used to supply water or to dewater at construction sites and to provide water jets for some types of construction. AIR COMPRESSOR WATER PUMP DRILL GRINDER 11 | P a g e SAW HAMMER SAND BLASTING GUN WRENCH II. EQUIPMENT MANAGEMENT Construction equipment management refers to continuous evaluation of the construction equipment fleet and its cost while at the same time considering the projects at hand. The process of balancing the expense and use of the construction equipment against the timelines and income from the projects can be called construction equipment management. A construction equipment manager needs to be able to take practical 12 | P a g e decisions with regards to management of the construction equipment to ensure maximum benefits with minimal expenses for the company. Construction equipment management can either be taken up project wise or for the company as a whole. Cost-effectiveness is a major criteria of construction equipment management. Following are the things to be considered for effective construction equipment management: 1. The choice of construction equipment and the number in which each of the equipment is required for a certain project or projects. 2. Whether it makes more sense to own, lease or rent the equipment and its effect on the bottom line of the balance sheet. 3. Planning which equipment will be working on which job site at what time and for how long. 4. Considering the transportation and operating costs when dealing with multiple projects and their time lines. 5. How to make the most of the construction equipment at hand. 6. Another major aspect of effective construction equipment management is preventive maintenance of the construction equipment which can help save a lot of down time, money and reduce delays in the project. All in all effective construction equipment is the answer to making construction projects more cost effective while ensuring timely completion of projects. i. EQUIPMENT MANAGEMENT OVERVIEW ROLE IN QUALITY MANAGEMENT SYSTEM Equipment management is one of the essential elements of a quality management system. Proper management of the equipment in the laboratory is necessary to ensure accurate, reliable, and timely testing. The benefits of a good equipment management program are many: Helps maintain a high level of laboratory performance; Reduces variation in test results, and improves the technologist’s confidence in the accuracy of testing results; 13 | P a g e Lower repair costs, as fewer repairs will be needed for a well- maintained instrument; Lengthens instrument life; Reduces interruption of services due to breakdowns and failures; Increases safety for workers; Produces greater customer satisfaction. PROGRAM CONSIDERATIONS A great deal of thought and planning should go into equipment management. As the laboratory puts an equipment management program in place of the following elements should be considered: SELECTION AND PURCHASING- When obtaining new equipment what criteria should be used to select equipment? Should equipment be purchased, or would it be better to lease? INSTALLATION- For new equipment, what are the installation requirements, and who will install the new instrument? CALIBRATION AND PERFORMANCE EVALUATION- What is needed to calibrate and validate that the equipment is operating correctly? How will these important procedures be conducted for both old and new instruments? MAINTENANCE- What maintenance schedule is recommended by the manufacturer? Will the laboratory need additional preventive maintenance procedures? Are current maintenance procedures being conducted properly? TROUBLESHOOTING- Is there a clear procedure for troubleshooting for each instrument? SERVICE AND REPAIR- What is the cost? Can the laboratory obtain the necessary service and repair in its geographical area? RETIRING AND DISPOSING OF EQUIPMENT- What must be done to dispose of old equipment when it needs to be replaced? 14 | P a g e OVERSIGHT It is the responsibility of the management director to: Oversee all the equipment management systems in the laboratory; Ensure that all persons who will be using the instrument have been appropriately trained and understand how to both properly operate the instrument and perform all necessary routine maintenance procedures. Equipment management responsibility may be specifically assigned to a technologist in the laboratory. In many laboratories there is a person who has good skills with equipment maintenance and troubleshooting. Giving this person the role of oversight of all equipment is recommended. Oversight of an equipment management program includes: Assigning responsibilities for all activities; Assuring that all personnel are trained on operation and maintenance; Monitoring the equipment activities; Review all equipment records routinely; Update maintenance procedures as necessary; Ensure that all procedures are followed. Note: Day-to-day maintenance should be the responsibility of the technical operator. ii. SELECTING AND ACQUIRING EQUIPMENT SELECTING EQUIPMENT Selecting the best instrument for the laboratory is a very important part of equipment management. Some criteria to consider when selecting laboratory equipment are listed below. Why and how will the equipment be used? The instrument should be matched against the service the laboratory provides. 15 | P a g e What are the performance characteristics of the instrument? Is it sufficiently accurate and reproducible to suit the needs of the testing to be done? How easy will it be for staff to operate? Will instructions be available in a language that is understood? Is there a retailer for the equipment in the country, with available services? Does the equipment have a warranty? Are there any safety issues to consider? ACQUIRING EQUIPMENT Is it better to purchase, rent or lease equipment? When making this decision, it is a good idea to factor in repair cost. The initial cost of an instrument may seem reasonable, but it may be expensive to repair. Also consider savings that could be negotiated if the laboratory needs more than one piece of equipment. The manufacturer should provide all of the necessary information to operate and maintain equipment. Before purchasing it ask if: Wiring diagrams, computer software information, a list of parts needed, and an operator’s manual are provided; The manufacturer will install the equipment and train staff as part of the purchase price; The warranty includes a trial period to verify that the instrument performs as expected; The manufacturer’s maintenance can be included in the contract and if so, whether maintenance is provided on a regular basis. INSTALLING EQUIPMENT Before equipment is installed, verify that all physical requirement (electrical, space, doors, vent, and water supply) have been met. Other things to consider are: 16 | P a g e The vendor’s responsibilities for installation should be confirmed in writing prior to beginning the installation process. A checklist of the expected performance specification should be developed, so that performance can be quickly verified as soon as the equipment is installed Whenever possible, it is best to have the manufacturer install laboratory equipment; this will likely improve the conditions of the warranty, and also may ensure that the installation is done properly and quickly. If equipment is installed by the laboratory: Check that the package contents contain all the parts; Make a copy of any software that is part of the system; Do not allow the equipment to be used before it is completely installed, performance is verified, and testing personnel are trained. iii. GETTING EQUIPMENT READY FOR SERVICE AFTER INSTALLATION After equipment has been installed, the following details need to be addressed before putting the equipment into service: Assign responsibility for performing the maintenance and operation programs; Develop system for recording the use of parts and supplies; Implement a written plan for calibration, performance, verification and proper operation of the equipment; Establish a scheduled maintenance program that includes daily, weekly, and monthly maintenance task; Provide training for all operators; only personnel who have been trained specifically to properly use the equipment should be authorized as operators; 17 | P a g e Designate those authorized to use the equipment and when it is to be used. EQUIPMENT CALIBRATION Follow the manufacturer’s directions carefully when performing the initial calibration of the instrument. It is a good idea to calibrate the instrument with each test run, when first putting it into service. Determine how often the instrument will need to be recalibrated, based on its stability and on manufacturer’s recommendation. It may be advantageous to use calibrators provided by or purchases from the manufacturer. FUNCTION CHECKS In order to verify that equipment is working according to manufacturer’s specifications. It is necessary to monitor instrument parameters by performing periodic function checks. This should be done before using the instrument initially, then with the frequency recommended by the manufacturer. These function checks should also be done following any instrument repairs. Some examples of function checks are daily monitoring of temperatures and checking the accuracy of wavelength calibration. iv. IMPLEMENTING AN EQUIPMENT MAINTENANCE PROGRAM PREVENTIVE MAINTENANCE Preventive maintenance includes measures such as systematic and routine cleaning, adjustment, and replacement of equipment parts at scheduled intervals. Manufacturers generally recommend a set of equipment maintenance tasks that should be performed at regular intervals: daily, weekly, monthly, or yearly. Following these recommendations will ensure that the equipment performs at maximum efficiency and will increase the lifespan of the equipment. This will also help to prevent: Inaccurate test results due to equipment failure Delays in reporting results Lower productivity Large repair cost. 18 | P a g e MAINTENANCE PLAN A maintenance plan will include preventive maintenance procedures as well as provisions for inventory, troubleshooting, and repair of equipment. When implementing an equipment maintenance program, some of the initial steps will include the following: Assign responsibility for providing oversight Develop written policies and procedures for maintaining equipment, including routine maintenance plans for each piece of equipment. The plan should specify the frequency with which all maintenance tasks should be performed. Develop the formats for records, create logs and forms, and establish the processes to maintain records. Train staff on the use and maintenance of the equipment, and assure that all staff understand their specific responsibilities. NOTE: It is recommended that a label be attached to the instrument indicating when the next maintenance or service should be performed. v. TROUBLESHOOTING, SERVICE REPAIR, AND RETIRING EQUIPMENT WHAT IS THE SOURCE OF THE PROBLEM? Problems with equipment may present in many ways. The operator may notice subtle changes such as drift in quality control or calibrator values or obvious flaws in equipment function. Sometimes, the equipment fails to operate. It is important to teach operators to troubleshoot equipment functioning and resume testing as rapidly as possible. When an operator observes instrument drift, it is important to repeat the preventive maintenance procedures as a first step to resolve the problem. If it does not work, proceed with troubleshooting processes. TROUBLESHOOTING Manufacturers frequently provide a flowchart that can help determine the source of problems. Is the problem related to a poor sample? 19 | P a g e Is there a problem with the reagents? Is there a problem with the equipment? SERVICE AND REPAIR Manufacturers may provide service and repair of equipment that is purchased from them. Be sure to set up a procedure for scheduling service that must be periodically performed by the manufacturer. When instruments need repair, remember that some warranties require that repairs be handled only by the manufacturer. RETIRING AND DISPOSING OF EQUIPMENT It is very important to have a policy and procedures for retiring older equipment. This will usually occur when it is clear that the instrument is not functioning and is not reparable, or when it is outmoded and should be replaced with new equipment. Once a piece of equipment is fully retired and it has been determined that it has no further usefulness, it should be disposed of in an appropriate manner. This last step is often neglected, and old equipment accumulates, taking up valuable space and sometimes creating a hazard. When disposing of equipment, salvage any useable parts, particularly if the equipment is being replaced with another similar one. Then consider any potential biohazards, and follow all safety disposal procedures. vi. EQUIPMENT MAINTENACE DOCUMENTATION DEVELOPING DOCUMENTS AND POLICIES FOR RECORDKEEPING Equipment document and records are an essential part of the quality system. The policies and procedures for maintenance should be defined in appropriate documents, and keeping good equipment records will allow for thorough evaluation of any problems that arise. RECORDING MAINTENANCE INFORMATION Each piece of equipment should have a dedicated logbook documenting all characteristics and maintenance elements: Preventive maintenance activities and schedule 20 | P a g e Recording of function checks and calibration Any maintenance performed by the manufacturer; Full information on any problem that the instrument develops, the subsequent troubleshooting activity and follow up information regarding resolution of the problem 21 | P a g e