Wagon Maintenance Manual PDF
Document Details
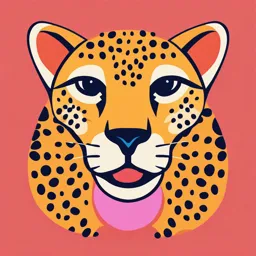
Uploaded by SolicitousOklahomaCity
null
Tags
Summary
This document contains technical information on tippler machines, including their construction, safety requirements, and positioning systems. It provides guidelines for maintaining and operating these machines, ensuring the safety of the equipment and people around it.
Full Transcript
APPENDIX- I Tippler Page 1 of 6 APPENDIX- I TIPPLER 1.0 Introduction The tippler machines are used by private...
APPENDIX- I Tippler Page 1 of 6 APPENDIX- I TIPPLER 1.0 Introduction The tippler machines are used by private siding owner for tippling of BOX ‘N’ wagons loaded with coal. The loaded wagons are marshaled in the tippling line and placed on the tippling unit one by one for unloading. Types of tipplers: There are two types of tipplers being installed in the pvt. Sidings. 1. Side discharge tippler 2. Rotary type wagon tippler 2.0 General requirements 2.1 The design and construction of components of tipplers and auxiliary handling equipment coming into contact with any part of wagon shall be such that no damage whatsoever is caused to the wagon equipment or its paint. 2.2 The top clamping pressure shall be such as will hold the wagons firmly in position on rails and keep the running gear from getting dislodged without causing any deformation to the wagon structure. 2.3 Adequate compensating measures shall be taken in top clamps and side support beam to compensate for manufacturing imperfections, within the permissible limits, in the top copings and side stanchions of the wagon, so that clamping pressure on the contacting area on the side and top of the wagon is uniformly distributed. 2.4 The side supports for tipplers shall meet the following requirements: a) The side support shall consist of a longitudinal beam, which shall be as long as the longest wagon to be tippled. This beam shall be continuous. b) The side support shall be articulated so that it can take the tapered as well as parallel stanchions on the body of the wagons. Alternatively, the cradle shall be articulated on trunion to achieve this. c) Full-face contact between the side support beam and the side stanchions shall be ensured. The side supports shall extend from a height of 1000 mm up to 2950mm, from rail level, i.e. contact the side of the wagon over a width of not less than 1950mm. [For wagons of height less than 2950mm, typically iron ore wagons, (user shall have to consult the concerned zonal railway for this confirmation) suitable slots shall be provided in the side support beam, to permit the top clamping of the wagons] There shall be metal to metal contact between the side support beam and the side stanchions of the wagon i.e. no rubber pad or WAGON MAINTENANCE MANUAL APPENDIX- I Tippler Page 2 of 6 any other alternative, shall be provided on the contact face of the side support beam d) The side support beam shall be moveable type, the movement being done by hydraulic arrangement. (No external or moveable counter weights should be used with the side support beam) Facility of forward/ backward movement should exist, such that it should be able to move & touch the wagon without applying any pressure on the wagon side-wall. At this position it should get locked and the tilting operation can begin. At the end of the tippling cycle, the side support should return to its home position, so that the next wagon can be positioned on the tippler Movement of the side support should be controlled & the speed should be crawling just before making contact with the wagon sidewall. e) Pressure gauge/s should be mounted, at easily accessible location, for reading the hydraulic pressure of the side support hydraulic arrangement. 3.0 Safety requirements – Safety requirements for tipplers, divided into the following three stages, construction stage shall be followed as under: 3.1 Construction stage a. The design of the tippler shall avoid, as far as possible, any spillage of the material handled by the wagons. b. Devices shall be built-in to prevent any over run of the wagons in either direction. c. The tippler shall be designed so that the wagon is securely held in all operating positions. d. Automatic devices shall be provided to hold the tipplers securely in any position in the event of failure of the drive unit. e. All tipplers shall have means to limit the angle of tippling. f. Arrangement shall be made on tipplers to prevent feet being trapped between the platform and the base of the tippler. g. Whenever possible mechanical or electrical devices shall be built-in to ensure that all the conditions allowing wagon tipping are coordinated. h. Additionally, a device shall be provided to prevent an empty wagon from being released until the tippler is back in original position. i. A device shall be provided to prevent the entry of a non-scheduled wagon into a tippler. Sharp edges and corners in all working spaces shall be avoided. k. The parts projecting into working spaces shall be as small as possible. WAGON MAINTENANCE MANUAL APPENDIX- I Tippler Page 3 of 6 l. All the frequently used lubrication points shall be accessible without it being necessary to remove the guards. m. It is recommended that equipment shall be so designed that maintenance and cleaning is facilitated. n. Fully integrated controls should be provided for wagon positioning system, wagon holding devices and wagon tippler. The controls should be interlocked so that there is no chance of accident due to error in sequence of operation. 4.0 Positioning system for wagon Wagon tipplers shall be provided with side arm charger for positioning of wagons on the tipplers, such that a. Side arm charger should be of sufficient capacity, depending on whether complete train or some wagons are to be moved / positioned. There should be some positive system for centering of wagon on the tippler table. b. Drive unit for the side arm charger should be of positive type e.g. rack & pinion, so that sudden jerks/slippages are avoided. Suitable technology should be used, so that the wagon can be moved at slow speeds for placement on tippler table e.g. Low speed hydraulic motors, Variable frequency AC motors or thyrister controlled DC motors (through epicyclical reduction gearing), etc. c. Charger should be able to slow down to creeping speed just before the final positioning 5.0 Wagon & Train holding devices 5.1 Wheel grippers a. These are mandatory & should be located on the tippler table, to prevent inadvertent motion of the wagons during tippling operation. b. These should be so designed that balanced pressure is applied on both sides of the wheel rim. It should have a floating arrangement so as to ensure that force on each gripper is same and should have some lateral float so that it can take a new position in case of variation in wheel gauge. Wheel grippers should be free from serrations or any such provision on its holding face. Wheel grippers should be made of soft material. 5.2 Retractable wheel chocks a. These are mandatory & should be fitted at the in-haul & out –haul tracks, to prevent accidental rolling of the wagons on the tippler table. WAGON MAINTENANCE MANUAL APPENDIX- I Tippler Page 4 of 6 b. They should be so designed that flange of the wheel is not contacted while blocking tread of the wheel. Shape of the chock should take into account the wheel incline, so that a line contact is made with the wheel. 6.0 Check sheet for joint inspection Check sheet for the six monthly joint inspection of the tipplers to be conducted by DME/ Sr.DME (C&W) of the concerned division or his authorised representative and representative of the siding owner, as per Railway Board letter No.98/M(N)/951/12 dated 27.11.02, is as follows: SN Item Check Remarks 1 End frame platform (i) Steel work to be examined for side beam damage or defects. (ii) Check & record the gap between the side beam and the wagon side stanchion, during tipping operation. 2 Drive gear (i) Check proper matching of rack and pinion tooth & tooth wear. (ii) Check whether coupling gives jerk during rotation. The tippling operation should be smooth & without any jerks 3 Top hydraulic clamp (i) Check the level of clamp pad. Whether sitting properly or not. (ii) Check the condition & thickness of clamp pad (thickness should not be less than 50 mm) (iii) Check the smoothness of clamp movement (iv) Check for provision of indicators on the tippler table for all types of wagon stock, which are likely to be tippled on the tippler. This is to ensure that wagons are placed on the tippler table in such a manner that the top clamping pads position is near the side stanchions. Force exerted by the top clamps should not exceed 1.5t per clamp pad. Check & record the value. (v) Check for provision of a wagon bogie spring relief mechanism in the top (vi) clamp locks for permitting release of bogie springs. WAGON MAINTENANCE MANUAL APPENDIX- I Tippler Page 5 of 6 4 Rail table of wagon (i) Check the level and alignment of rail. tippler The level of track on tippler table and that of approach rails should be the same so that the wagons do not experience any jerk during in-haul and out-haul 5 Limit switches (i) Check for proper function 6 In haul & out haul (i) Check satisfactory working of stop stop linkage Movement. (ii) Check the gradient on the outhaul side. 7 Side arm charger* (i) Check damage / defects of steel work. Check proper matching of drive pinion (ii) & rack & tooth wear. Check the smooth movement and final position of arm hoist. (iii) Check the proper tightening of fastener & condition of track. (iv) Check for proper functioning of limit switches & proximity switches (v) 8 Damages to wagons. (i) Damages during tippling & post tippling damages: Dents/nick on the side stanchions, top copings, wagon body, etc Displacement of bogie pivot or suspension springs Damages to air brake pipes Axle box adopter shifting Coupler damages Any other *Note: (1) There should not be any loose shunting of the wagons. In-haul and out-haul arrangements consisting of side arm charger should be used for placement and removal of wagon on tippler table. The practice of shunting empty wagon after tippling by rake of loaded wagons is not acceptable as it results into large scale damages to CBC and bogies. Representative of the Sr DME (C&W) /DME Siding owner or Authorised representative WAGON MAINTENANCE MANUAL APPENDIX- I Tippler Page 6 of 6 WAGON MAINTENANCE MANUAL