CnW Maintenance Manual - Inspection of Wagon Stock - PDF
Document Details
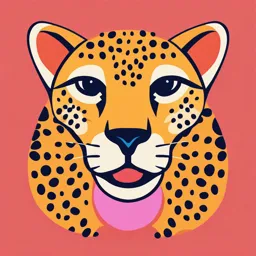
Uploaded by SolicitousOklahomaCity
Tags
Summary
This document provides a detailed check list for inspections of wagon stock, including freight depots, intensive examination of air brake trains, inspections of loads, and safety audits of wagon ROH depots. It also includes specific procedures for maintenance in various areas, such as coaching maintenance and freight operations, and contains information for various types of equipment and work areas. The maintenance manual style and structure implies its intended use as a technical manual for wagon maintenance inspection and safety.
Full Transcript
Page 1of 44 Appendix-VIII Check lists for Inspection of wagon stock Appendix-VIII Check Lists for Inspection of Wagon Stock CONTENTS SN...
Page 1of 44 Appendix-VIII Check lists for Inspection of wagon stock Appendix-VIII Check Lists for Inspection of Wagon Stock CONTENTS SN Particulars Page No. 01 Check list for Inspection of Freight Depots 04 02 Check list for Intensive Examination of Air brake trains 06 03 Check list for Super Checking of Examined loads in Yards 08 04 Check list for Freight Sick Line 10 05 Check list for Safety Audit of Wagon ROH Depots 12 (Part–I)- Vital information 06 Check list for Safety Audit of wagon ROH depots 14 07 Check list for Work Areas where attention to be given (Wagon) 15 08 Check list for Freight Sick Line Maintenance 20 09 Check list for Safety Audit of Wagon ROH Depots – Vital information 22 10 Check list for Safety Audit of Wagon Depots 23 11 Check list for Safety Audit of Wagon ROH Depots Air brake system 24 Reference G-97 12 Check list for Safety Audit of Wagon ROH Depots Casnub Bogie- 25 Reference G-95 13 Check list for Inspection of Wagon Tippler 26 14 Check list for Train Parting in Freight stock. 28 15 Check List for Investigation of CBC Uncoupling 31 16 Check List for Reporting Hot Axle on Wagon Stock 34 17 Check List for Inspection of In-Motion Weigh-bridges 35 18 Check list for analysis of BP Air hose uncoupling. 37 19 Check list for reporting Flat tyre 38 20 Check List for Wheel Impact Load Detector ( WILD) 40 21 Checklist for investigation of Brake binding 42 WAGON MAINTENANCE MANUAL Page 2of 44 Appendix-VIII Check lists for Inspection of wagon stock MECHANICAL DEPARTMENT MINIMUM QUOTA OF INSPECTION PER MONTH 1. DIESEL LOCO SHEDS. Activity per month JA SS JS Supervisors DF / EF Super check of Diesel 4 4 6 8 locomotives 2. OPERATIONAL ASPECTS SN Type of inspection JA SS JS Supervisors SLI/LI SSE/SE 1 Foot plate 3 5 8 - 12 2 Crew booking (Day/Night) 1/1 2/1 2/1 4/4 2/2 3 Running room 1 1 1 1 1 4 Ambush check 1 1 1 - 2 5 Safety seminar Qtly Qtly Qtly 1 - 6 DSL installation [RCD] 1 1 1 2 1 7 ART Qtly Qtly Qtly 1 - 8 Monitoring of Drivers and Each driver & Asstt. is assigned to a SLI/LI. Asstts. They must be covered once in three months 9 140 Te. Crane Qtly Mly Mly Bi Mly - 10 ARME/SPART Qtly Mly Mly Bi Mly - 3. COACHING MAINTENANCE SN Type of inspection JA SS JS Supervisors Rake inspection/Month (under gear & Passenger amenities) 1 Washing Line 2 3 4 10 2 Platform 2 3 4 10 3 Running 1 1 2 02 4 Sick line inspection 1 2 2 02 WAGON MAINTENANCE MANUAL Page 3of 44 Appendix-VIII Check lists for Inspection of wagon stock 4. COACHING DEPOT INSPECTION SN Type of Inspection JA SS JS Supervisors 1 Major 1 1 1 Once every month in the nominated beat 2 Medium 1 B.Mly 1 B.Mly 1 - do - 3 Minor 1 B.Mly 1 1 - do - 4 Bk.Power checks 1 2 4 04 5 Qly. Joint inspection of 1 1 1 1 (Mly) infrastructural facility of Coaching maintenance Depot, Examination Yard and Sick lines with Engg. & Elect. Officer. 6 Night inspection 1 2 2 2 5. FREIGHT OPERATION SN Type of inspection JA SS JS Supervisors 1 Sick line 1 2 2 2 2 Yard 2 2 3 3 3 ROH Depot 1 1 1 1 4 Night inspection 1 1 1 2 5 Super check of goods rake 1 2 4 4 6 SIG / Joint Inspection 1 1 1 - 7 Office inspection 1 1 1 1 8 Brake Power checks (Goods 2 2 4 4 trains) 9 Qualities of GDR Check 1 1 2 4 WAGON MAINTENANCE MANUAL Page 4of 44 Appendix-VIII Check lists for Inspection of wagon stock INSPECTION OF FREIGHT DEPOT [Railway Board's letter No.2009/M(Safety)/7/2/Check.List.Inspections dated 09.09.2009] Following areas to be inspected by the Supervisors/Officers to ensure general upkeep and smooth functioning of Freight Depots. SN Description Status 01 ROH RELATED ITEMS: 1. System for identification of repairs and ensuring the completeness thereof. 2. Availability of unit exchange spares mainly trolleys, springs and wheels. 3. Availability of must-change items, system, monitoring and audit checks. 4. Attention to welding practices, particularly of earthing. 5. Availability & use of gauges. 6. Quality of repairs and attention to schedule items. 02 SICK LINE RELATED ITEMS: 7. Adequacy of lifting facilities. 8. Attention to welding practices particularly earthing. 9. Cylinder overhauling. 10. Air pressure testing of stock after repairs in sick line. 11. NTXR rejection and analysis thereof. 12. Road access and availability of material handling equipment. WAGON MAINTENANCE MANUAL Page 5of 44 Appendix-VIII Check lists for Inspection of wagon stock SN Description Status 03 MANAGEMENT INFORMATION SYSTEM: 13. Analysis of failures. 14. Analysis of average examination time. 15. Compliance of imprest items and availability of critical materials like brake blocks, brake bloc keys, brake gear pins, etc. 16. Trend of expenditure - unit cost and inventory. 17. Identification of training needs and training. 18. 100% implementation of safety related modifications. 19. Use of bulb cotters in place of split cotters. 20. Ultrasonic testing of axles. Please make surprise check of an axle already cleared. 21. Provision of spare templates for worn out wheel profile for tyre-turning of wheels. 22. Analysis of freight trains. - Examined in loaded/empty condition. - Running with invalid BPCs. - Coming for intensive exam. with open doors. 04 BRAKE GEAR AND WHEELS: 1. Complete inspection of running gear fittings. 2. Correct fitment of brake gear pins, split pins & bulb cotters. 3. Tapping and gauging of wheels. 4. Check wheels free from defects as per IRCA rule book. 5. Hand brakes to check for working. 6. Check empty load box in correct position. WAGON MAINTENANCE MANUAL Page 6of 44 Appendix-VIII Check lists for Inspection of wagon stock 05 SAFETY FITTINGS: 1. Checking of Safety brackets, safety loops & safety fittings 2. Checking correct and sound fitment of AR holding straps 06 BOGIE FRAMES AND SPRING GEARS: 1. Check for cracks on horn gaps. 2. Replace cracked/Broken springs 3. Repair cracks/welding failures of SSB/DSB 4. Bridle bar fitment 07 BRAKE POWER: 1. Check for adequate pressure level 2. Ensure proper adjustment for piston stroke 3. Leakage rate should be within prescribed limit. 4. Check for proper mating of brake block on wheel treads. 5. Check, corrections of „A‟ Dimension clearance of SAB regulator and ensure proper working. 6. Ensure brake block thickness above 20 mm 7. Ensure minimum of brake power and six out of 8 wagons in front and rear to be operative 8. Fitment of quick coupling/Adopter‟B‟ in brake van to be ensured. 08 MISCELLANEOUS: 1. Check buffer heights 2. Check proper security of doors (covered wagons) 3. Check proper packing/lashing & securing of consignment 4. Inspection of draw and buffing gears 5. Ensure proper locking of CBC Date : Name of the Officer : Station : Designation : WAGON MAINTENANCE MANUAL Page 7of 44 Appendix-VIII Check lists for Inspection of wagon stock Intensive Examination of Air Brake Trains. [Railway Board's letter No.2009/M(Safety)/7/2/Check.List.Inspections dated 09.09.2009] Ensure 100% rolling-in-examination for loose brake gears / skidded wheels / hot box before intensive examination. SN Description Status 01 I. BRAKE GEAR AND WHEELS: 1. Complete inspection of running gear fittings. 2. Brake rigging pins & safety brackets in proper working condition. 3. Tapping and gauging of wheels to be ensured. 4. Wheels to be checked and should be free from defects as per IRCA rule book. 5. Hand brakes of wagons to be fully released. 6. Operating handle of empty load box in correct position. 02 II. BRAKE POWER: 1. Check brake pipe pressure and ensure :- No. of wagons Engine Brake Van 2 a Upto 56 wagons 5.0 Kg / cm 4.8 Kg / Cm2 b Above 56 wagons 5.0 Kg / cm2 4.7 Kg / Cm2 2. Ensure leakage rate within prescribed limit. 3. Proper adjustment of piston stroke. Ensure within specified limit after brake application. 4. Proper mating of brake block on wheel treads. 5. Proper working and correct 'A' dimension clearance of SAB Regulators. 6. Ensure minimum percentage of operative cylinders as per specified limits. 7. Ensure continuity of brake pipe connection and conduct continuity test. 8. Ensure working of guard's emergency brake valve and proper fitment and working of quick coupling. 9. Ensure brake cylinder piston fully inside and brake blocks having clearance from wheels, after release of brakes. WAGON MAINTENANCE MANUAL Page 8of 44 Appendix-VIII Check lists for Inspection of wagon stock 03 III. MISCELLANEOUS: 1. Ensure all angle cocks ( except at rear end of train) are kept open. 2. Ensure isolating cock of DVs to be in open position. 3. Ensure BP & FP coupling at rear end of train is placed on support. 4. Ensure CBCs are properly locked and operating handles properly secured. 5. Ensure proper closing of doors. 04 IV. ADDITIONAL ITEMS FOR BOBR / BOBR'N' WAGONS: 1. Load sensing Device (LSD) to be checked for proper working. 2. Ensure clearance between operating valve and spring buffer (LSD) within specified limits. 3. Bolts and nuts of LSD to be properly tack welded. Date : Name of the Officer : Station : Designation : WAGON MAINTENANCE MANUAL Page 9of 44 Appendix-VIII Check lists for Inspection of wagon stock SUPER CHECKING OF EXAMINED LOADS IN YARDS [Railway Board's letter No.2009/M(Safety)/7/2/Check.List.Inspections dated 09.09.2009] Following items to be inspected by the Supervisors/Officers to ensure super checking of examined load in yards. SN Description Status 01 I. BRAKE GEAR: 1. Correct size of fitment of Bk. gear pins, split pins & bulb cotters. 2. Correct sitting of brake blocks, brake shoe key & split pin. 3. Hand brake working. 4. Empty load box correct handle position & connection. 02 II. SAFETY FITTINGS: 5. Availability of sound safety brackets / loops. 6. Correct and sound fitment of AR / VR holding strap. 03 III. BOGIE FRAMES AND SPRING GEARS: 7. Cracks on horn gaps. 8. Bridle bar fitment. 9. Spring breakages / cracks. 10. Welding failures in SSB / DSB. 11. Overloading of wagon. WAGON MAINTENANCE MANUAL Page 10of 44 Appendix-VIII Check lists for Inspection of wagon stock SN Description Status 04 IV. BRAKE POWER: 12. Check of pressure level. 13. Proper adjustment of piston stroke. 14. Leakage rate within prescribed limit. 15. Proper mating of brake block on wheel treads. 16. Proper working and correct 'A' dimension clearance of SAB regulators. 17. Brake blocks thickness to be above 20 mm. 18. Six out of eight wagons to be operative in front and rear of load. 19. Fitment of quick coupling / Adopter 'B' in the brake van. 20. Ensure a minimum of 85% brake power for end-to- end running and 100% brake power for close- circuit running of Air Brake rakes. V. GUARD AND DRIVER CHECK (EXAMINATION) 21. Knowledge of Guard and Drivers for items to be checked. 22. Quality of check being done by Guard/Driver. 23. Check for correct method of continuity test being done by guard and driver. 24. Endorsement of GDR check on BPC by Guard/Driver. Date : Name of the Officer : Station : Designation : WAGON MAINTENANCE MANUAL Page 11of 44 Appendix-VIII Check lists for Inspection of wagon stock CHECK LIST FOR FREIGHT EXAMINATION POINT Railway : Type of attention : Division : Avg. no. of wagons attended : Type of stock : Availability SN Item Remarks Yes No 1 7.5 m centre to center distance between two lines 2 Concrete path way 3 Paved road for truck movement 4 Supervisors Room 5 Staff room 6 Rolling in/out huts 7 Field Store + Tool room 8 Compressor Room 9 Exhauster room 10 Battery Charging room 11 Tower light Street light along examination lines at two 12 levels 13 Portable rechargeable light 14 Hand Lamps 15 Welding line 16 Arc Welding set (Mounted on trolley) 17 Portable DG Set 18 DG set 250 KVA (for compressor, light & welding) 19 Electric Compressor (500 CFM) 20 Diesel Compressor (500 CFM) 21 Exhauster 22 Gas cutting set 23 Hyd. Cold cutting set/ Hand shears 24 Protective clothing with Helmet & Gloves 25 Welding Apron & Welding glass. 26 Pneumatic pipe line (32 mm dia.) 27 Rake test rig 28 Hydraulic Jacks 29 Wheel Barrow 30 Pick up van 31 Truck WAGON MAINTENANCE MANUAL Page 12of 44 Appendix-VIII Check lists for Inspection of wagon stock Availability SN Items Remarks Yes No 32 Lister truck 33 Road Mobile Crane 34 Hand Trolley 35 Portable drill machine 12mm 36 Drill Machine 37 Bending Machine 38 Fitter tool box 39 Pressure gauge test stand 40 Folding type portable wheel diameter gauge 41 Rail profile gauge cum recorder in box 42 Wheel distance measuring gauge 43 Buffer height guage 44 Tyre defect gauge 45 Electronic device/ infrared termometer for detecting worm box 46 Electric operated hand tools i.e. grinder 47 Pocket Jack (Hydraulic) 6 Ton capacity 48 Hand Tools 49 Storage rack with pigeon holes 50 Rack with Locker 51 Plain paper fax with P&T line 52 Walkie Talkie set/mobile phone 53 Railway Telephone 54 BSNL Telephone 55 Computer with printer, Scanner,UPS with preloaded softer & modem 56 C&W Office furniture 57 Railnet/Internet connection 58 Plain paper copier 59 First Aid Equipment Other observations: Signature of Inspecting Officer Name: Designation: WAGON MAINTENANCE MANUAL Page 13of 44 Appendix-VIII Check lists for Inspection of wagon stock Check Sheet for Safety Audit of Wagon ROH Depots (Part-1) – Vital information Sr Requirement Observations 1 No of Artisans on Roll 2 No of Artisans overdue Refresher 3 No of Supervisors on Roll 4 No of Supervisors overdue Refresher 5 No of Welders on Roll 6 No of Welders overdue training at CRWS/BPL 7 No of Wheels involved in ROH of BOXN/BCN in a month 8 No. of wheels re-profiled during ROH 9 % of BOXN/BCN Wheels re-profiled during ROH 10 No. of Wheels UST done during ROH 11 % of Wheels subjected to UST during ROH 12 Periodicity of calibration of tools 13 Records of Calibration of tools 14 Periodicity of calibration of gauges 15 Records of Calibration of gauges 16 No of Safety items pertaining to the Depot 17 No of Safety items out of stock (%) 18 No of Safety items demanded 19 No of Safety items supplied NIL 20 No of Safety items supplied more than 50% 21 No of Vital items pertaining to the Depot 22 No of Vital items out of stock (%) 23 No of Vital items demanded 24 No of Vital items supplied NIL WAGON MAINTENANCE MANUAL Page 14of 44 Appendix-VIII Check lists for Inspection of wagon stock 25 No of Vital items supplied more than 50% 26 Quality of riveting 27 Quality of Welding 28 Check that correctly procedure being followed for Ultrasonic Testing of Wheels 29 Availability of Safety Brackets for a. Truss bar b. Push Rod c. Pull Rod 30 Documentation of ROH Repairs: i. Schedule Forms ii. Check Sheets iii. Selected items recorded in Work Diary/ Register iv. Computerized Data Signature _________________ Name _____________________ Designation ________________ Inspecting Official WAGON MAINTENANCE MANUAL Page 15of 44 Appendix-VIII Check lists for Inspection of wagon stock Check Sheet for Safety Audit of Wagon ROH Depots Sr. Requirement Ref. No. Observation 1. Provision of Boiler for Steam Cleaning 2. Steam Cleaning of Tank Barrels 3. Steam Cleaning of Bitumen and Molasses Tank Wagons 4. Cleaning of Tank for corrosive repairs 5 Hydraulic Testing of Barrel 6 Testing procedure for Barrel is ensured 7 Testing of Sulfuric Acid Tanks and Caustic Soda Tanks at testing pressure of 4.22 Kg/cm2 8 Pneumatic test at a pressure of 2.1 Kg/cm2 for Hydrochloric Acid Tank Wagons provided with Rubber lining (no Hydraulic Test should be done) 9 Testing of Tank Wagons used for Petrol and middle distillates of Petroleum and Vegetable oil. 10 Overhauling and testing facilities for Master Valve. 11 Overhauling and testing facilities for Bottom Discharge Valve. 12 Testing of Safety Valve 13 Testing of Blank Flange Signature of _________________ Name _____________________ Designation ________________ Inspecting Official WAGON MAINTENANCE MANUAL Page 16of 44 Appendix-VIII Check lists for Inspection of wagon stock WORK AREAS WHERE ATTENTION TO BE GIVEN IN ROH SN Nature of Repairs Observation 1. BODY REPAIR WORK (Common for all) UNDER FRAME – Sole Bar Scrap the portion of the sole bar at door ways, clean and apply primer paint followed by Top coat SIDE WALL – Skirting 1. Check and patch if corroded then apply primer and top coat on the patch 2. Side Doors – Check damage and repair clean & lubricate hinges 3. Side Pillars – Check cracks at the base & repair 4. Patching of body, roof, door or floor plates straightening buldged ends repairs to angle irons. Stanchions and crib angles etc. 5. Making wagons water-tight (Covered wagons) 6. Fitting/replacement of door fastening road, door cotter pin eye, both hook and eye locking pin on empty wagons and closing of doors. 7. Fitting/replacement of door fastening rod guide, door hasp which requires riveting on empty wagons. Repairs by welding to door fittings. 8. Hand rail/foot board deficient/ or damaged, insecurely fastened at door way of guard‟s brake van. 2. UNDER GEAR REPAIR WORK (Common for all) 1. Brake Linkage – Check free movement 2. Hand Brake – Check proper working 3. BOGIE REPAIR WORK CASNUB BOGIE BOLSTER 1. Pocket slope liner Change liner if thickness less than 5 mm 2. Rotation stop lugs Provide liners (thickness to suit) if dimensions less than 514 mm 3. Inner Column Gib Provide liners (thickness to suit) if dimension less than 142 mm 4. Land surface Provide liners (thickness to suit) if dimension less than 442 mm 5. Outer Column Gib Renew by welding if dimension more than 241 mm SIDE FRAME 1. Column Friction Liner Change liner if dimension more than 455 mm 2. Column sides Provide liners (thickness to suit) if dimension less than 209 mm 3. Anti rotation lugs Provide liners (thickness to suit) if dimension more than 526 mm 4. Key seat to pad 22 W Provide liners (thickness to suit) if dimension more than 276 mm WAGON MAINTENANCE MANUAL Page 17of 44 Appendix-VIII Check lists for Inspection of wagon stock SN Nature of Repairs Observation 5. Crown Roof 22 WM Provide liners (thickness to suit) if dimension more than 321 mm 6. Crown Roof 22 NL Provide liners (thickness to suit) if dimension more than 326 mm 7. Pedestal Crown Sides Renew by welding if dimension less than 147 mm 8. Pedestal Jaw 22 W Provide liners (thickness to suit) if dimension more than 275 mm 9. Pedestal Jaw 22 WM Provide liners (thickness to suit) if dimension more than 283 mm 10. Pedestal Jaw 22 NL Provide liners (thickness to suit) if (Short) dimension more than 195 mm 11. Pedestal Jaw 22 NL Provide liners (thickness to suit) if (Long) dimension more than 241 mm 12. Pedestal Sides 22 W Provide liners (thickness to suit) if dimension less than 102 mm 13. Pedestal Sides 22 WM Provide liners (thickness to suit) if dimension less than 102 mm 14. Pedestal Sides 22 NL Provide liners (thickness to suit) if dimension less than 78 mm WEDGE 1. Slope Surface Renew by welding if dimension less than 7 mm 2. Vertical Surface If vertical surface from centre line of spigot less than 56 mm provide liner of 6 mm thickness CENTRE PIVOT (BOTTOM) 1. Vertical Side 22 W Renew by welding if wear more than 4 mm 2. Vertical Side 22 WM Renew by welding if wear more than 3 mm 3. Vertical Side 22 NL Renew by welding if wear more than 3 mm 4. Seat Side 22 W Renew by welding if wear more than 3 mm 5. Seat Side 22 WM Renew by welding if wear more than 3 mm 6. Seat Side 22 NL Renew by welding if wear more than 3 mm COIL SPRING 1. Outer Group and use in sets. Replace if free height at or less than 245 mm 2. Inner Group and use in sets. Replace if free height at or less than 247 mm 3. Snubber Group and use in sets. Replace if free height at or less than 279 mm ADEPTER 1. Crown Surface Replace if worn 3.5 mm or more 2. Side lug Replace if wear more than 3 mm on either side 3. Thrust shoulder Replace if depth exceeds 0.7 mm 4. Machined relief Replace if depth less than 0.8 mm WAGON MAINTENANCE MANUAL Page 18of 44 Appendix-VIII Check lists for Inspection of wagon stock BOGIE BRAKE GEAR Pins & Bushes Change if clearance more than 1.5 mm 4. AIR BRAKE SYSTEM Distributor Valve Overhauling Distributor Valve Test on SWTR DV Isolating Cock Examine operation DV Release Valve Examine operation DV Filter Clean BRAKE CYLINDER Filter of Escorts & RPIL Clean make Brake Cylinder of Lubricate Greysham & WSF make CUT OFF ANGLE COCK Angle cock Examine and lubricate Rubber Seals Change DIRT COLLECTOR Dirt Collector Clean Sealing Ring Change RESERVOIR AR & CR Drain Sealing Ring Change METAL PIPES & JOINTS Pipe Joints Examine leakage & repair Seal (20 mm & 32 mm) pipe Change Guard’s Emergency Brake Examine operation Van Isolation cock of BVZC Examine operation Brake Van Quick Coupling Examine operation Load Sensing Device Examine operation 5. SLACK ADJUSTER (COMMON FOR ALL) Slack Adjuster Testing Functioning, repair if required “A” dimension Adjust “e” dimension Adjust M20 Anchor Pin nut Ensure securing by welding to pin Air Brake System Test on SWTR as per procedure Brake Block Ensure Std. Key, Split pin & all new brake blocks NB: For detailed main procedure refer RDSO manual G-97 6. CENTRE BUFFER COUPLER (COMMON FOR ALL) CBC BODY Coupler Body Examine & replace on condition basis CBC Counter Examine,replace if required Shank Wear Plate Replace on condition KNUCKLE WAGON MAINTENANCE MANUAL Page 19of 44 Appendix-VIII Check lists for Inspection of wagon stock Nose Replace if wear more than 9.5 mm with HTE Knuckle Knuckle Pin Replace on condition Knuckle Stretch Examine,replace if required STRIKER CASTING Wear Plate Replace Striker Casting Replace on condition COUPLER MECHANISM Anti Creep Protection Examine and repair Lock lift assembly Examine Operation Mechanism Examine Lock Examine DRAFT GEAR Slack Measure & take correction GENERAL Yoke pin support Replace on condition Buffer Height Examine & Correct if required 1. For detailed maintenance Practice in Open line refer RDSO’s Manual G-76 2. For detailed maintenance Practice in open Workshop RDSO’s Manual G-80 3. Knuckle with nose more than 4.3 mm and less than 9.0 mm can be used in Yard. 7. WHEEL AXLE & BEARING (COMMON FOR ALL) AXLE 1. Ultrasonic Testing To be carried in every ROH & reject if fails 2. Deep Notches due to Reject if deep is more than 5 mm gearing 3. Axle end holes Clean and lubricate in case end cover is opened WHEEL 1. Tread profile Check with tyre defect gauge 2. Height of flange If height is more than 31 mm do not use under ROH wagon 3. Smooth flange If flange not completely smooth do not use under ROH wagon 4. Wheel profile Turn to WWP if above clause are not met for use under ROH wagon. BEARING TAPERED CARTRIDGE 1. Cup Rotate the bearing for unusual sound check up for Crack/chipping 2. Seal Check seal for external damage/dent 3. Backing Ring Check backing ring for looseness & vent fitting on backing ring with vent hole (the vent fitting should be intact or the vent hole should be plugged) 4. Locking Plate Use new locking plate when ever and cover is opened WAGON MAINTENANCE MANUAL Page 20of 44 Appendix-VIII Check lists for Inspection of wagon stock 5. Axle end Cap screw Clean and lubricate in case end cover is opened 6. Load Zone Change Change load zone area of the cup while lowering bogie side frame. Signature of Inspecting Authority:_________________ Name:____________________________ Designation:_______________________ WAGON MAINTENANCE MANUAL Page 21of 44 Appendix-VIII Check lists for Inspection of wagon stock CHECK LIST FOR FREIGHT SICKLINE MAINTENANCE SN Facilities Recommended Facilities Available 1 Covered Shed 100 M x 50 Mx 25 M 2 SAB Repair Room 4x20 M 3 DV Test room 4x14 M 4 Service Building 4 x 25 M 5 Computer room 4x14M or 5x7 M 6 Store Room + Sub Store 4x30M or 5x15 M 7 Machine shop 4x30M 8 Compressor room 4x12 M or 5x9M 9 SE/JE Room 4x7 M or 5x5 M 10 Required 4 lines under covered shed. 11 Distance between two lines. 12 Other observations of Sick Line 13 EOT Crane 15 T/5T -2 Nos. 14 EOT Crane 10 T/5T -2 Nos. 15 Road Crane 10 T. Cap. - 1 No. 16 Jib Crane 2.5 T. - 6 Nos. 17 Electrical stationary Screw Air Comp. (500CFM) 18 Portable Diesel Compressor - 1 No. 19 Trestles - 12 sets. 20 DG set 500 KVA - 1 No. 21 Work Station for Bogie Repair - 10 Nos. 22 Fixture for Riveting spring plank - 2 Nos. 23 Welding machines - 10 Nos. 24 Bogie Mainpulators - 3 Nos. 25 Fork lifter 3 Ton. - 2 Nos. 26 Truck 10 Ton capacity - 1 No. 27 Tractor with Hydraulic lifting Machine & 3 Trolleys (Trailers) 28 Fork lifter 2 Ton - 2 Nos. 29 Platform truck 2 Ton - 2 Nos. 30 Light Store Vehicle - 1 No. 31 Hand Trolleys with Rubber Wheels -- 10 Nos. WAGON MAINTENANCE MANUAL Page 22of 44 Appendix-VIII Check lists for Inspection of wagon stock SN Facilities Recommended Facilities Avail. 32 First Aid Equipment - 4 sets. 33 VHF sets / Mobile phones. - 10 Nos. 34 Storage racks - As per layout. 35 Portable Hydraulic Riveter - 1 No. 36 Stores Bin - 20 Nos. 37 CBC & Draft Gear Replacement equipment - 01 No. 38 SAB Test bench - 1 No. 39 DV Test stand - 1 No. 40 Single Car Test Rig - 2 Nos. 41 Ultrasonic Flaw Detector - 2 Nos. 42 Pneumatic/Electrical hand tools - As per reqmnt. 43 Pneumatic Torque Wrench With stockets 1" to 2" - 4 sets 44 Repair facilities of DV 45 Repair facilities of SAB 46 Test & Repair facilities of Vac. Cylinders. 47 Test & Repair facilities of Air brake cylinders 48 Test & Repair facilities of Release valves 49 Repair facilities of Brake beams 50 Boiler for steam cleaning of tank wagons. 51 Any other new items introduced WAGON MAINTENANCE MANUAL Page 23of 44 Appendix-VIII Check lists for Inspection of wagon stock Check Sheet No.1 for Safety Audit of Wagon ROH Depots – Vital information SN Requirement Observation 1 No.of Technician on Roll 2 No.of Technician overdue Refresher 3 No.of Supervisors on Roll 4 No.of Supervisors overdue Refresher 5 No.of Welders on Roll 6 No.of Welders overdue training 7 TSO's circulars and instructions whether acknowledged by Supervisors 8 Competency certificate issued to safety category artisans as per TSO's 9 Training programme of skilled artisans for promotional and refresher course. 10 No.of Wheels dealt in ROH of BOXN/BCN in a month 11 No.of wheels reprofiled during ROH 12 % of BOXN/BCN wheels reprofiled during ROH. 13 No.of wheels UST done during ROH. 14 % of Wheels subjected to UST during ROH. 15 Techniques being followed for Ultrasonic Testing of wheels. 16 Periodicity of calibration of tools. 17 Records of calibration of tools. 18 Periodicity of calibration of gauges 19 Records of calibration of gauges. 20 No.of Safety items pertaining to the depot. 21 No.of safety items available and out of stock (%) 22 No.of Vital items available and out of stock (%) 23 No.of Vital items pertaining to depot. 24 Availability of Safety Brackets for Truss bar, Push Rod, Pull Rod. 25 Type of Documentation of ROH Repairs maintained: i. Schedule Forms ii. Check Sheet. iii. Selected items recorded in Work Diary/Register iv. Computerized Data WAGON MAINTENANCE MANUAL Page 24of 44 Appendix-VIII Check lists for Inspection of wagon stock CHECK SHEET NO. 1A OF SAFETY AUDIT 1 Adequacy of Tools and equipments. 2 Whether air compressor, exhauster, welding plants. EOT are in working order. Whether any Machine due for schedule repair. 3 v) General cleanliness of shed. vi) Housekeeping of depot. 4 Whether placement and removal of sick wagons is timely done. 5 Knowledge of Artisans. 6 Condition of Service Building. 7 Condition of floor, roof, valley gutters and drainage system. 8 Condition of staff Toilets. 9 Condition of insulation of power cables. 10 Adequacy of power supply and illumination. 11 Adequacy of water supply 12 Adequacy of drinking water. 13 Standby DG set arrangement. 14 Stores section v) Stacking of spares, oil and grease vi) Stacking of scrap materials. vii) Disposal of scrap materials. viii) Record of receipts and issues 15 Monitoring of safety and vital items. 16 Accountal of despatch & receipt of wheels. 17 Accountal of despatch & receipt of springs. 18 Any other remarks Signature of __________________ Design. Inspecting Official WAGON MAINTENANCE MANUAL Page 25of 44 Appendix-VIII Check lists for Inspection of wagon stock Check sheet for safety Audit of Wagon ROH depots AIR BRAKE SYSTEM REFERENCE G- 97 Wagon No. SN Requirement Observation 1 Testing of individual wagon using single wagon testing Rig as per prescribed procedure & proforma 2 All pipe joints and connections are tested with soap soluation for defecting leakages. 3 Cut off angle cock is replaced, if it is leaking or damaged, by required and tested Angle cock Smooth operation of angle cock. 4 Drain plug of dirt collector & Aux. Reservoir are Opened, condensate is drained out and leather washer is replaced, if found defective, Condition of Drain plugs. 5 Filter is removed cleaned in soap solution Tank, Blown dry with compressed air and refitted back 6 Brake cylinder is tested for smooth movement of piston and piston is lubricated. 7 Defective Brake cylinder is replaced by duly tested Brake cylinder. 8 Visual examination for Gaskets of Hose Couplings and replaced, if found damaged. 9 Provision of Hose coupling support and APD on Angle cocks at both end. 10 Dismantling/assembling of DV assembly and pipe bracket is done as prescribed. 11 Specified Tools and ROH Kits are available for DV repair. 12 Overhauling is being done by Trained persons. 13 DVs tested for all the parameters on a Test Bench as given in the format. Check the record. 14 All the components of ROH Kit replaced irrespective of condition. 15 Repaired and tested DVs being stored in a clean and dry place. 16 All Inlet ports of DV and pipe bracket are covered with protective cap. 17 Wagon is again tested on SWTR. 18 Fitment of single piece load sensing Device on BOBRN/BCC Wagons circulated vide RDSO's Letter No.MW/APB/LSD/ dated 06.02.02 & their working. 19 Single wagon testing proforma used. 20 Piston stroke. 21 SAB Regulator 22 Empty / Load Box 23 Brake Ratio 24 BP pipe line all joints with soap solution. 25 Air reservoir condition, Security of straps. Signature of ________________________ Name: Design. Inspecting Official WAGON MAINTENANCE MANUAL Page 26of 44 Appendix-VIII Check lists for Inspection of wagon stock Check sheet for Safety Audit of Wagon ROH depots CASNUB BOGIE - REFERENCE - G-95. SN Requirement Status 1 Free height determined and Grouping of Coil springs is done and mixing of new and oil springs avoided. 2 Retro fitment of EM Pads with wide Jaw Adapter. 3 Dis-assembly of Casnub Bogie as per procedure. 4 Reassembling of Casnub Bogie as per procedure. 5 Nominal clearance and tolerance are maintained as prescribed. 6 Wear of Bolster, Side Frame and Wedge surfaces. 7 Repairs being undertaken on Bolster and Side frame on manipulators for down hand welding. 8 Check the use of class of electrode, Gauge of electrode, Welding current and Welding precautions during repair as prescribed and procedure for welding of liner. 9 Usage of Gauge to measure wear on Bolster Column gibs and Seat and sides of Centre Pivot Bowl. 10 Determination of wear on outside and inside of side frame columns, Friction Plate, Pedestal Jaw crown roof and sides with proper gauge. 11 Use of proper size and material of liner on side frame columns, Friction Plate, Bolster pocket slope & CBC. 12 Check determination of wear (by using proper gauges) on, Thrust Shoulder, Adapter Bore, Adapter Crown Lug and Adapter sides. 13 Visually inspected for crack or breakage. 14 Whether nominal dimensions of EM pad and CC pad are recorded and condition for cracks, breakages, band failure and crushing of rubber checked. 15 Wear of Friction shoe wedge block on both surfaces is determined by using proper gauge and reclaimed by welding Manganese Steel Liner of 120x10x2 mm using H2 Electrodes. 16 Condition of Brake Gear Pins is visually inspected. 17 Brake Power is adjusted by relocation of Pins in End Pull Rod 18 Brake shoe is replaced when worn-out to 48 mm. 19 Reclamation of Brake Beam on account of worn-out Brake Heads is done through welding on a fixture following proper procedure. 20 Axle End screws are tightened by Torque Wrench at the specified Torque of 34-37 Mkgs. 21 Fitment of modified side bearer housing of 95 mm height as per Drg.No.SK-69594 Alt.30 22 Spring Plank deformation and condition of rivets inspected. 23 Availability of set of 24 gauges for checking wear limit of: Side Frames, Bolster, Wedge & Adapter. Signature of ________________________ Name: Design. Inspecting Official WAGON MAINTENANCE MANUAL Page 27of 44 Appendix-VIII Check lists for Inspection of wagon stock CHECK LIST FOR INSPECTION OF WAGON TIPPLER SN Component/Unit Sr. Items to be checked Tippler Tippler No.1 No.2 A. End frame 01 Side beam to be examined for damages platform side beam or defects 02 Check the condition & thickness for side beam rubber pad. The thickness of the pad should not be less than 50 mm. 03 Check & record the gap between the side stanchion B. Drive Gear 01 Check proper matching of rack and pinion teeth & teeth wear. 02 Check whether coupling gives jerk during rotation.The tippling operation should be smooth & without any jerks. C. Top hydraulic 01 Check the level of clamp pad whether clamp sitting properly or not. 02 Check the condition & thickness of clamp pad (thickness should not be less than 50 mm) 03 Check the smoothness of clamp movement. 04 Check for provision of indicator on the tippler table for all types of wagon stock which are likely to be tippled on the tippler. This is to ensure that wagons are placed on the tippler table in such a manner that the top clamping pads position is near the side stanchions. Force exerted by the top clamps should not exceed 1.5 Tonnes per clamp pad. 05 Check & record the value. Check for provision of a wagon bogie spring relief mechanism in the top clamp locks for permitting release of bogie springs. D. Rail Table of 01 Check the level and alignment of the rail. Wagon Tippler The level of track on tippler table and that of approach rails should be the same so that the wagons do not experience any jerk during in-haul and out-haul. E. Limit Switches 01 Check proper function WAGON MAINTENANCE MANUAL Page 28of 44 Appendix-VIII Check lists for Inspection of wagon stock SN Component/Unit Sr. Items to be checked Tippler Tippler No.1 No.2 F. In-haul & Out- 01 Check satisfactory working of stop haul Stop Linkage movement. 02 Check the Gradient on the out-haul side. 03 Check for provision of “Retarders” on the out-haul side G. Side Arm Charger 01 Check damage /Defects of steel work. Check proper matching of drive. 02 Check Pinion and rack & tooth wear 03 Check smooth movement and final position of arm hoist. 04 Check the proper tightening of fastener & condition of track. 05 Check for functioning of Limit switches and proximity switches. H. Wagon Retarder 01 Check for proper function, speed of the rolling wagons, it should not exceed 5 Kmph. I. Damages to 01 Damage during tippling & Post Wagons Tippling Damages. Dents/Nick on the side stanchion, the copping wagon body etc. Displacement of bogie pivot or suspension springs Damages to air brake pipes. Axle box adapter shifting. Coupler damages Any other defect. Note: 1. After Tippling, empty wagons should not be coupled by loose shunting with the rake of loaded wagons. This is not acceptable. 2. Side Arm Chargers to be provided on the tipplers. 3. stamping of Weight & Measurer Department should be available on tippler Signature : Name : WAGON MAINTENANCE MANUAL Page 29of 44 Appendix-VIII Check lists for Inspection of wagon stock Check List for Joint Investigation Report of Train Parting General particulars: Date Km No. Division Section blocked Time Signal aspect Section Curvature Gradient Weather condition C/Order Kms of caution Order: Train Particulars: Train No. Loco (s) No Load / Tonnes- Homing Shed of loco Commodity Loading station Last Exam. Station BPC Date / % Rly / Divn. - BPC No CC /Pm /End to end Air/Vacuum brake Driver‘s particulars / (Train Engine & Banker) Driver’s Name HQ Qualification Safety Category Date of Appointment Guard’s Name HQ Affected & Adjacent Wagon‘s Particulars Sr. Wagon Class Rly R / Date POH ROH Position from No. No. Loco 1 2 Screw coupling / CBC (Alliance II / AAR-HT): Bearing: 16T RB / 20T RB / 20.3 T CTRB: Whether empty / loaded — WAGON MAINTENANCE MANUAL Page 30of 44 Appendix-VIII Check lists for Inspection of wagon stock Checklist for Affected Wagons CBC & Knuckles – HT/NHT Stamping Particulars – Knuckle broken – CBC -crack any location – Zone of breakage (A / B / C / D) – Structure of broken surface (uniform / coarse) – Any mark of Blow Hole - Origin of breakage (External / Internal / dent or hit mark) - Nature of breakage (Fresh or partially fresh) – Approximate % age of crack (Fresh/old/any hair crack existing previously) – Any foreign material inside casting (stone / hard material, etc.) -- Any other casting defect (Core sand deposit / uneven hard surface) – Knuckle is reclaimed by welding (Yes / No) CBC lock broken, fresh / Old with % - Any manufacturing defects on CBC lock (crack / unusual metal projections, etc) Draft & Assembly Type of draft gear – (RF 361 / SL – 76 / MK-50 / HR-40) Draft gear condition (dislocated / tilted / stiff) Front end follower (intact with rivet / worn out)- Yoke pin (badly embedded in the yoke pin support plate) - Yoke pin support plate (intact with sound rivet) - Any other defect noticed – Operational Aspects Statement of train drivers obtained or not - Statement of Banker’s drivers obtained – Conclusions from statement of the drivers - Statement of Guard obtained or not - Obtained. Is there any empty wagon between two loaded wagons? Fluctuation of OHE voltage (as per SCADA report) – Tripping of DJ- as per driver statement & speedometer floppy– Operation of dynamic braking as per driver statement – Effectiveness of brake system from locomotive to the load – as per Dr’s statement - Any evidences of wheel slipping – as per Dr’s statement - Any evidences of brake binding of the rake as per Dr & Gd statement – Signal aspect. (Raised up on approach/ given on approach) – AFI condition while notching up. WAGON MAINTENANCE MANUAL Page 31of 44 Appendix-VIII Check lists for Inspection of wagon stock Loco particulars: Dynamic Brakes : Working/Not working : Air Flow Indicator: Working/Not working : Notches – BP Pressure ( Engine & Brake van ) – MR / PT set No. – Flasher light ( Wkg / Not working) – Speedometer ( Wkg / Not working) – Release time after dropping 1 kg/cm2 of BP pressure – Jerk while starting– Conjunction braking ( Working / Not working) – Track Particulars: - (a) Level (b) Rising (c) Falling (d) Curve right / left (e) Straight (f) Banner flag on track (g) Uneven rail joints (h) Cross over turn out (i) Camel hump (j) Vertical curve Time particulars:- Time left from station ------------------------- at-----------------hrs. Time arrival next station -----------------------at ----------------hrs. Running time of section – Total section blocked – Nature of Occurrence – (a) While notching up (b) While notching down (c) During normal run (d) Coasting (e) While starting after stopping (f) While controlling (g) While observing caution order at km no.------------- (h) Signal on approach (i) Running at the time of starting (j) Brake binding -on wagon no _________ ,position from engine (k) Gap between two portions _________mtrs (i) While entering loop line. Speed of train at the time of incidence - ________kmph Date of investigation: Investigation: Findings/Conclusion: Responsibility: Signature - Signature - Signature – Name - Name - Name – Designation - Designation - Designation – WAGON MAINTENANCE MANUAL Page 32of 44 Appendix-VIII Check lists for Inspection of wagon stock Check List for Investigation of CBC Uncoupling General particulars: Date Block Section &KM Division Section blocked Time Signal aspect Section Curvature Gradient Weather condition C/Order Kms of caution Order: Train Particulars Train No. Loco(s) No. Load / Tonnes- CC+8+2/CC+6+2 Commodity Loading station Last Exam. Station BPC Date / % Rly / Divn. - BPC No CC /Pm /End to end Air/Vacuum brake Driver‘s particulars / (Train Engine & Banker) Driver’s Name HQ Qualification Safety Category Date of Appointment Nominated LI Guard’s Name HQ Affected & Adjacent Wagon‘s Particulars Sr. Wagon Class Rly R / Date POH ROH Position from Loco No. No. 1 2 Screw coupling / CBC (Alliance II / AAR-HT): Bearing: 16T RB / 20T RB / 20.3 T CTRB: Whether empty / loaded — WAGON MAINTENANCE MANUAL Page 33of 44 Appendix-VIII Check lists for Inspection of wagon stock Observations Recorded by CWI/SSE/SE(C&W) for CBC Uncoupling SN Components Affected Wagon Adjacent Wagon A CBC Uncoupling lever handle ---- ---- 01 Over all length in straight line (Centre of hook to centre of rod) Std. 1414 mm, for BLC- 1063 mm 02 Total length of bent end (Std. 400 mm) 03 Geometry of CBC uncoupling lever handle ( Straight/Bent) 04 Anti rotational lug size ( 210 mm long, cross section 16X16 mm) 05 Condition of uncoupling lever handle bracket & additional bracket B Bearing piece ---- ---- 01 Slot gap in the bearing piece (Std. 17.5 mm) 02 Bearing piece pin (Bent/Straight) 03 Bearing piece pin secured with proper washer/Nut or not 04 Bearing piece pin dia (Std. 24 mm) C CBC Knuckle, Coupler & Fittings ---- ---- 01 Dropping of locking piece to proper depth & Toggle is seen. 02 Gap between knuckle nose & guard arm to be checked by gauge No.2 first and then with gauge No.1 ( Max. gap 133 mm) 03 Wear of the knuckle to be checked with gauge No. 3 ( Within limit/Beyond permissible limit) D CBC Drooping ---- ---- 01 CBC height from centre of track (Std. Min.1030 mm & Max. 1105 mm) 02 CBC Shank wear plate ( Worn out/Missing or OK) 03 CBC Striker casting wear plate ( Worn out/Missing or OK) E Condition of Knuckle thrower (Worn out/Missing or OK) F Lock lift assembly ---- ---- 01 Condition of lock & its slot for free movement of toggle pin. ( worn out or OK) 02 Condition of toggle ( Worn out/Missing or OK) 03 Condition of both rivets ( Worn out/Missing or OK) WAGON MAINTENANCE MANUAL Page 34of 44 Appendix-VIII Check lists for Inspection of wagon stock SN Components Affected Wagon Adjacent Wagon 04 Condition of Auxiliary Anti-creep lug ( Worn out or OK). The condition to be checked by pressing rotary lever with the help of thumb towards striker casting to enter in the bottom cavity of CBC body (Through which toggle enters) without operating/Touching CBC operating handle. If it goes in that, indicates anti-creep protection failure, in that case, necessary repairs to articulated assembly be ensured on the wagon. 05 Whether toggle is seen properly when CBC lock piece is in fully dropped condition and CBC in locked condition. G Any other observations: H Conclusion: I Responsibility J Repercussion Signature : Name of CWI/SSE/SE(C&W) : Depot : WAGON MAINTENANCE MANUAL Page 35of 44 Appendix-VIII Check lists for Inspection of wagon stock Check List for Reporting Hot Axle on Wagon Stock Train No./ Loco No./Base shed of Loco Load/Tonnege Last Exam station /Date/% / BPC No./(CC/PM/Int) Wagon No./Class/ Rly. Last POH Workshop / Date Last ROH station/Date : Return date: Commodity : Loading station : weight of contents Position of wagon from engine Position of affected wheel Type of bearing-22.9 T./20.3 T/ CT RB Make of Bearing & year of Manufacture Latest UST particulars stamped/ punched Axle Particulars Return date stamped on backing ring of Bearing Rotation of Axle box (Free / Jam ) Condition of Rollers (Damaged / seized) Condition of Outer race (Broken / Damaged) Condition of Inner race (Broken / Damaged) / Condition of grease Condition of grease seal Condition of Locking studs (loose /deficient) Condition of Locking plate Any symptoms of brake binding Flat places /Skidding of wheels (size of flat if any) Any other unusual occurrences on bogies which could have prevented free rotation of bearing. Any other unusual noticed (EM pad / Adapter) Probable cause of failure Responsibility Spring height Weight WAGON MAINTENANCE MANUAL Page 36of 44 Appendix-VIII Check lists for Inspection of wagon stock Check List for Inspection of In-Motion Weigh-bridges (Once in 03 Months) by team of JA Grade, Senior Scale and Jr. Scale Officers from Operating, Commercial Mechanical, Civil, and Finance Department for proper functioning and follow up of proper procedure. [ Ref: Railway Board’s letter No. TC-1/2004/109/4 dated. 04.11.2004 ] SN Description of Items to be checked Remarks Additional Remarks if any 1. Availability of Certificate of Stamping & Available / verification issued by Weight and Measures Not Department of State Government. available 2. Availability of breakdown register showing Available / date and time the weigh bridge went out of Not order, put back into commission, problem available reported, remark of service Engineer with signature of Weigh Bridge in charge and nominated mechanical official. 3. Digitizer and control panel should be locked Yes/No. and sealed. 4. Locking of weigh bridge room when not in use. 5. Locking of junction boxes. 6. Locking of all doors provided on cubical/cabinet of control equipments and putting paper seal with date of seal, duly signed by weigh bridge in charge and suppliers service engineer. 7. Weighment readings recorded at speed less Yes/No. than 15 kmph. 8. Rakes to be moved through weigh bridge with uniform speed below 15 kmph without any acceleration / declaration. 9. No electric connections taken from junction box provided between UPS and weigh bridge computer, digitizer etc. 10 Working of Diesel generator set. Working / Not Working 11. Weigh bridge is under Annual Maintenance Yes/No. Contract or otherwise. 12. Testing of Weigh Bridge is done as per Yes/No. procedure and within duration laid down. 13. Rakes for movement should be moved through Weigh Bridge without stopping short of Weigh Bridge. 14. Weighment to be made in pulling mode only. WAGON MAINTENANCE MANUAL Page 37of 44 Appendix-VIII Check lists for Inspection of wagon stock SN Description of Items to be checked Remarks Additional Remarks if any 15. Availability of ‘Weigh Bridge Ahead’ board on Yes/No both sides about 300m in advance of Weigh Bridge. 16. Track upto 100 m on either side of Weigh Bridge should be level tangent. 17. Approach rail of 52 kg/m with PSC sleepers should be available. 18. The track should have adequate ballast cushioning and proper drainage. 19. Creep Anchors should be provided to take care of possible creep. 20. Proper maintenance of weigh cabin/control room such as cleanliness, whitewashing, good condition of window and doors shall be ensured. 21. Availability of water connection is to ensured for wetting of earth pit. 22. Two separate 230 V.AC supply points of Available / adequate capacity, one for weigh bridge Not Available equipment and other for AC & lighting load in Weigh Bridge shall be provided. 23. Standby power supply arrangement through Available / Diesel generating set is to be made available. Not Available 24. Provision of earthing and its maintenance as per 153043-1966 shall be ensured and earth resistance & its continuity shall be subjected to annual checks. 25. UP Keep of electrical equipments such as lights, fans and AC unit provided inside the weigh room and also in the general area around the weigh rails and track side switches for security reasons. 26. The AMC of the associated electrical equipment viz. UPS, air-conditioner, voltage-stabilizer etc. necessary for proper operation of the weigh bridge. 27. S&T department shall maintain the jumpers for the track circuit wherever provided by passing the weigh rails. 28. RDSO type block joints shall be provided and maintained on both sides of the weigh rails to provide electrical isolation of weigh rails. 29. Inspector / RPF In charge of the area shall exercise the necessary superintendence for the security of the weigh bridge ensuring general security of the weigh bridge installation. Sr DCM Sr DOM Sr DME Sr DEN Sr DFM WAGON MAINTENANCE MANUAL Page 38of 44 Appendix-VIII Check lists for Inspection of wagon stock CHECKLIST FOR ANALYSIS OF BP AIR HOSE UNCOUPLING SN Description Std.dimensions Remarks 01 Whether the length of Rubber hose is 660 mm 660 mm 02 Whether the length of complete BP air 835 mm hose( including palm & nipple) is 835 mm 03 Condition of crimped clamps & their -- availability at both the ends of rubber hose 04 Condition of check nut on nipple and -- its availability 05 Condition and availability of MU -- washer 06 Condition of palm locking pin and its -- diameter in mm. 07 Condition of palm lugs. Check for worn -- out lugs 08 Check for any dashing/scratch marks -- on the bottom of palm ends 09 Check make of air hose and stamping -- particulars 10 Whether BP hose found torn, twisted -- or normal 12 Check geometry of BP Metallic pipe for -- proper positioning. 14 Check worn out palm end lug edges -- and leakage of air 15 Check position of ball lever of coupling -- in case of coaching stock 16 Screw coupling ball lever modified or -- not in case of coaching stock 17 Ensure correct fitting of BP air hose -- with angle cock. 18 Ensure correct fitment of spare screw -- coupling in suspension hook in case of coaching stock. 19 Any ballast unloading is observed in -- the section where air hoses uncoupled. 20 Ensure condition of Nipple of BP air -- hose for worn out threads. 21 Ensure condition of angle cock for -- worn out threads. Signature : Name : Depot : WAGON MAINTENANCE MANUAL Page 39of 44 Appendix-VIII Check lists for Inspection of wagon stock CHECK LIST FOR REPORTING FLAT TYRE ( Wagon/Coach No. …………………….Train No………..….Date………………….) SN Description Remarks 01 Date 02 Division 03 Station / section of unusual 04 Train No. 05 Load 06 Loco No. 07 Loco Pilot 08 Train coming from 09 Stock: ( CC/PM/End to end ) 10 Last examination station/Rly/Date 11 Wagon No. 12 PRO Particulars POH ROH R/date 13 Validity of BPC & BPC No. 14 Brake Binding reporting station: (Reported by ASM, Gateman, Driver,Guard, PWI & Other) 15 Flat tyre reporting station: (Reported ASM, Gateman, Driver, Guard, PWI & Other) 16 Detaching station / section 17 Size of Flat in mm (Max. 50 mm for coaching stock & Loco) (Max. 60 mm for Wagon stock) 18 Cause of flat tyre (DV/SAB/Bad Engineman ship /BC, etc.) 19 Check for shelled tread wheels 20 Check metal deposition on wheels 21 Cattle run over if any 22 Loco change if any 23 Attaching / Detaching at station 24 Signal on approach 25 Caution order in previous section 26 Hand brake ‘On’/’Off’ 27 Position of Empty/loaded box handle 28 Functioning of LSD in case of BLC 29 Condition of Brake system. (DV isolated / working/any other detail) 30 Check proper functioning of brake gear pin suitable to wheel diameter. 31 Check end pull rod hole position is correct or not ( according to dia of wheel) 32 Detailed cause of flat tyre (i.e. exact cause of DV/SAB/Brake Cylinder etc.) WAGON MAINTENANCE MANUAL Page 40of 44 Appendix-VIII Check lists for Inspection of wagon stock SN Description Remarks Check A‖ dimension a. 70+2-0 for air brake stock other than BOBRN 27+2-0 for BOBRN wagons b. Check ―E‖ dimension 575+25 mm for wagons c. Check ―A‖ dimension 22+2-0 mm for Coaching d. Check ―E‖dimension 375+25 mm for Coaching e. Check Piston Stroke 60- 70 mm for (Modified) & 32-40 mm for BMBC Coaching stock f. Check releasing time of wagon/Coach g. Check Sensitivity/Insensitivity of DV h. Check whether brake cylinder releasing or not i. Check hand brake for brake application j. Check functioning of SAB ( Pay-in/Pay-out is smooth or not k. Check SAB pull rod for correct length l. Type of brake block (composite /cast iron) Additional information: 33 Make of DV & Stamping particulars 34 Date of manufacturing of DV 35 Last POH date of DV 36 Make of SAB & Stamping particulars 37 Date of manufacturing of SAB 38 Last POH date of SAB 39 Check Brake cylinder make & Stamping particulars 40 Make of Brake block 41 DV/SAB test report from BSL/ET 42 Any other detail 43 Conclusion: Date : Name of the Officers : Depot: Designation : WAGON MAINTENANCE MANUAL Page 41of 44 Appendix-VIII Check lists for Inspection of wagon stock Check List for Wheel Impact Load Detector ( WILD) SN Description Status 01 Purpose and capability: The wheel impact load detector system is capable of automatic detection of defective wheel of rolling stock by measuring vertical impact load on the rails. The system is also capable of detection of over loaded wagons, speed of train & generation of automatic exception report. Check all aspects 02 Scope of supply: The specification covers manufacture, supply, installation and commissioning of 36 channel wheel impact load detection system with signal processor, 02 nos. instrumented rails of 52/60Kg. with length of 13 M each and other accessories. Check installation as per scope. 03 The wheel impact load detection system is supplied on Tunkey basis which consists of construction of one room of size 4.0MX3.0MX3.0M for housing computer, control electronics, data acquisition system and air conditioner. This should be ensured as per standard specifications. 04 Specific characteristics: 01. The system is comprising of 36 Channels system. 34 will be used for detection of impact load & 2 are utilized for activation of system. To be checked. 02. For detection of impact load, each channel comprises of 4- resete type Strain gauge fixed on rail. Condition to be checked. 03. The system detects defective wheels of 770 mm to 1100 mm diameter by measuring impact load on rails. 04. The system will work effectively in the speed range of 30 KMPH to 160 KMPH. Check effectiveness at suitable speed. 05. The system will measure impact load up to 60 Tonnage or more for the complete speed range of measurement. 06. The system is capable of detecting 95% or more defective wheels on first pass, to be checked. 07. The system is capable of functioning with trains consisting up to 100 vehicles(400 axles), to be checked. 08. The system shall have 3 levels of alarm ranging from 3 to 30 T & emergency alarm for loads higher than 30 t, this aspect should be checked. 09. The interconnection of both computers i.e. at site and remote control is through DOT telephone line of optical fiber cable. The provision between site and control is provided by Railways, its connectivity to be checked. 10. Software is able to generate the reports with following items a. Date of run b. Time of train passing c. Run No. d. Trains name & No. e. Axle no. from front f. Average normal dynamic wheel load g. Maximum dynamic wheel load h. Impact load factor i. Speed of each axle j. Overloaded wheel details WAGON MAINTENANCE MANUAL Page 42of 44 Appendix-VIII Check lists for Inspection of wagon stock k. Speed of Trains l. 03 level alarm generation. Printed reports to be checked for ensuring above parameters. 11. The system is rugged and temper proof so as to work round the clock through out the year in harsh and dusty out door environment exposed to sun. Any abnormality to be checked. 5 Site Condition: Whether the system is installed on straight and level track of minimum 250 m length including approaches to the site. 6 There shall be no fish plated joint within 13 on either side of the instrumented portion of the track. 7 The rail section shall be 52 Kg/m or 60 Kg/m with flat foot laid on Pre-stressed Concrete (PSC) sleepers at 60 cm to 65 cm spacing with elastic fastenings viz. pandrol clips on rubber grooved sole and clean ballast cushion 300 mm 8 The site shall not be very close to any station or at the approach of a signal to avoid acceleration or braking over the instrumented rails. 9 Training: Whether technical experts of the manufacturer has given full and adequate 03 days training to the operators and maintenance staff nominated by the consignee during commissioning of machine. Other facilities: 10 Availability of Drinking water facility 11 Security arrangement by RPF. 12 Condition of Telephone line or optic fibre for better connectivity of system at site to the remote control room. 13 Availability of Power Supply 230 V. ± 10%, 50 Hz up to room & Earthing arrangement. 14 Quality of construction of one room of size 4.0MX3.0MX3.0M for housing computer, control electronics and data acquisition system, air conditioner. 15 Whether approach road is available or not to the site. 16 There will be no any welded joint in the instrumented portion of the rails. 17 Track condition should be as close to new-condition of track as possible. 18 Rail head profile should be relatively new and sleeper/ballast interface should be stable. 19 Rail head use for instrumentation should be ultrasonically tested and to be defect free. 20 Whether AMC visits are being done timely by the Firm’s representative, check maintenance schedule forms. 21 Check record of Incidences/defects and action taken by nearest TXR point to avoid running of defective Wagon/Coach/Loco. 22 Any other problem Date : Name of the Officers : Depot: Designation : WAGON MAINTENANCE MANUAL Page 43of 44 Appendix-VIII Check lists for Inspection of wagon stock CHECK LIST FOR INVESTIGATION OF BRAKE BINDING 1 General Particulars: Date Time Division Section Caution order Block section Weather condition Km No. 2. Train particulars: Train no. Loco no. Load Banker no. BPC no. Last examination station PM/ CC/End to End CC+6 / CC+8 3. Particulars of Driver: Name HQ Date of Date of promotion appointment Safety category Last PME Involved in Train parting / Accident in last two years Details of Ghat - Driver Guard’s name HQ 4. Particulars of affected wagons: Wagon no. Type Built date POH ROH R/D Position from loco Type and condition of brake blocks Whether empty / Consignment loaded loaded 5. Type of DV and make : Make Last overhauling Sr. no. - Charging time Releasing time Any leakage from - DV 6. Brake binding reporting: Station Reported by (Dy. SS/Gateman/Guard/ Driver/ Points man/C&W staff of any other) Reporting time WAGON MAINTENANCE MANUAL Page 44of 44 Appendix-VIII Check lists for Inspection of wagon stock 7. Other information Whether cattle run over Any Loco changed enroute Any shunting carried out enroute Signals on approach Any Caution order observed before brake binding Any air leakage on train Condition of Hand brake Position of empty load box change over lever Functioning of load sensing device in case of BLC/BLL/BCC/BOBRN (Any leakage from VTA valve) Condition of Air brake equipments a) Working of DV (Working / Isolated) b) Brake cylinder (Working / any leakage/ Piston sticky) c) Piston stroke: 60-70 mm for modified & 32-40 mm for BMBC Coaching stock 130+10 mm for loaded BOX-N/BCN wagons & 85+10 mm for empty d) Condition of SAB (Working / Not working) e) ‗A‘ dimension: 70+2-0 mm for air brake stock other than BOBRN 27+2-0 mm BOBRN wagons 22+2-0 mm for Coaching stock f) ‗E‘ dimension: 575+25 mm for wagons 375+25 mm for coaching Brake gear system (standard / non standard pins fitted or related parts missing) End pull rod hole position with respect to wheel diameter(Correct /Incorrect) Any application of emergency braking during run Whether driver did brake feeling test at first opportunity and given Releasing time to release the train fully. Whether complete train was released or not after Traction change, if any. Brief History: Statement of Loco pilot: Statement of Guard:- Analysis: 1. 2. Conclusion: Responsibility: Repercussion: WAGON MAINTENANCE MANUAL