CnW Maintenance Manual Chapter 5 - Underframe PDF
Document Details
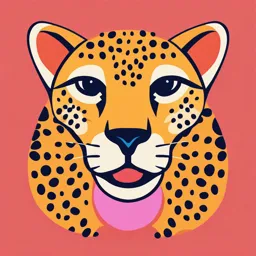
Uploaded by SolicitousOklahomaCity
null
Tags
Summary
This document provides details of wagon underframe design, construction, and maintenance procedures relating to various types and classes of railway wagons. It is aimed at professionals working in a railway capacity and contains detailed technical information and diagrams.
Full Transcript
CHAPTER 5 - UNDERFRAME Page 1 of 14 CHAPTER 5 UNDER FRAME 501. GENERAL The type and size of a particular underframe is intimately related to the type and design...
CHAPTER 5 - UNDERFRAME Page 1 of 14 CHAPTER 5 UNDER FRAME 501. GENERAL The type and size of a particular underframe is intimately related to the type and design of a wagon, as it constitutes the main load bearing sub-assembly for the vehicle. The overall dimensions and design of this structure take into account the quantum and pattern of loading on the vehicle as well as the track considerations. This in turn determines the permissible wheel base of a bogie wagon would be required for the purpose of carrying the required load. Accordingly, while designing an underframe, the loading per meter is also taken into account as this is to be permitted by the type of track available. The buffing and impact loads also govern the strength of the underframe and the shunting speeds permitted for the marshalling of the goods stock. In the case of bogie wagons, the load transfer to the bogie frame is by means of pivot arrangement and thus the bogie frame also assumes an equally important function. 502. GENERAL CONSTRUCTION OF BG WAGON UNDERFRAME A. The main members of a typical conventional BG wagon underframe are as under: i. Sole bars ii. Head stock iii. Longitudinal iv. Cross bars v. Bolster vi. Floor vii. Crib angle viii. End angle ix. Gusset plates and knees x. Centre Sill B. The main underframe of a vehicle generally consists of two outer longitudinal member’s viz. Sole bars and the two head stocks which are strengthened by two middle longitudinals and various cross members. The diagonals and gusset plates protect the under frame against diagonal deflection and help in absorbing and distributing the buffing loads over different members. As already mentioned, the gusset plates and knees are provided at critical locations to impart additional strength to the joints. The whole structure is so designed that various loads are uniformly distributed and no single member has to bear excessive load than designed for. Various rolled/CRF sections are used for the underframe members. Channel/CRF/Press Z-section/Hat section are generally used for headstock and sole bars for facilitating fitment of Z-Sections etc. are used for centre sills. Welding is generally used for joining the underframe members. But in earlier wagons, riveting had been used for joining these members. In the case of bogie wagons, the underframe has comparatively stronger cross members, known as bolsters, for fitting the upper centre pivot casting, which rests on the bogie pivot. C. All under-frames are given an initial camber at the time of manufacture so that under actual loading conditions, these do not sag. D. The under-frame and all its members are necessarily to be true and square and these should conform to the manufacturing tolerances. WAGON MAINTENANCE MANUAL CHAPTER 5 - UNDERFRAME Page 2 of 14 E. The following tolerances are permitted in the new wagon construction: i) Inside length + 5 mm (riveted) - 5 mm + 7 mm (welded) - 3 mm ii) Inside width + 3 mm - 3 mm iii) Inside height + 3 mm - 3 mm iv) Difference between diagonals a. Under frame 5 mm b. Body side 5 mm c. Body end 5 mm d. Door opening 4 mm e. Door 3 mm v) Distance between bogie pivot + 3 mm (riveted) centres - 3 mm + 5 mm (welded) - 2 mm vi) Distance between bogie pivot centre +2 mm and adjacent headstock - 2 mm vii) Distance between stanchions: (a) Body side + 3 mm - 3 mm (b) Body end +1.5 mm - 1.5 mm viii) Door opening (vertical or horizontal) + 0 mm - 3 mm ix) Door length + 5 mm - 0 mm x) Door width + 3 mm - 0 mm xi) Distance between door centre line to + 1.5 mm centre line of door hinge - 1.5 mm xii) Coupler height from rail level in case + 0 mm the bogies are fabricated by the wagon - 5 mm builder himself. xiii) Coupler height from bogie top pivot + 0 mm in case bogies are provided as free - 3 mm supply items. xiv) Tolerances on dimensions of non-pressure tank wagon barrels shall be as under: a) Length of barrel measured over the centre + 10mm/-3mm of the two dished ends. WAGON MAINTENANCE MANUAL CHAPTER 5 - UNDERFRAME Page 3 of 14 b) Diameter including ovality + 3mm/-3 mm c) Inside dia of man hole + 3mm/-3 mm d) Height of dome + 3mm/-3 mm NOTE: Butting faces of two courses or a barrel course and dished end should be aligned to + 1 mm accuracy before welding. F. The other major sub-assemblies fitted to the underframe are as under: i. Draw gear/CBC sub assembly ii. Container locking/anchoring arrangement (on container flats only). iii. Side stanchions & lashing chains. iv. Door operating mechanism on hopper wagons. v. Top centre pivot G. The underframe is main load bearing member in the vehicle which is not only subjected to static loads but also dynamic impacts owing to the unevenness in the track. In addition to this, it has to successfully withstand heavy buffing impacts during the course of marshalling as well as heavy jerks have to be sustained by the draw gear at the time of starting of goods trains. Hence in order to ensure safe and smooth running of vehicles, the maintenance of underframe has to be done very carefully. H. It is therefore the duty of all supervisors both in workshops and divisions, to ensure that a thorough inspection of underframe is carried out at the time of POH. Other major repairs and all defects and deficiencies that come to notice must be given meticulous and thorough attention. The defects and deficiencies generally noticed together with recommended repair practices have been discussed in detail in this chapter. WAGON MAINTENANCE MANUAL 1. SOLE BAR-ISMC 250X82X9 2. CROSS BAR-5/8 mm PLATE 3. STRINGER-ISMC-100X50X5 4. HEAD STOCK-10 mm PRESSING 5. BOLSTER - 10/12mm PLATE 6. CENTRE SILL-Z Section 7. CROSS BAR AT OVERHANG- HEAD STOCK ISMC 100X50X5 CHAPTER 5 - UNDERFRAME WAGON MAINTENANCE MANUAL 14450 OVER COUPLER (NON TRANSITION) 13521 OVER HEAD STOCKS 9500 BOGIE CENTERS Fig. 5.1 BG WAGON TYPE “BCNA” FIG. 5.11 BG WAGON TYPE "BCNA" 2 3 7 5 6 1 4 CL OF WAGON Figures of the some typical BG bogie underframe are given at Fig. 5.11 to 5.13. Page 4 of 14 1. CROSS BAR 5/8 mm pla te 4. BOLSTER 10/12 mm pla te 5. HEAD STOCK 10 mm PRESSING 6. CENTRE SILL OF WAGON CENTER LINE 3 4 5 CHAPTER 5 - UNDERFRAME 8 6 WAGON MAINTENANCE MANUAL 8 6 6 6 275 275 1630 2 1630 1 6524 BOGIE CENTRES 9784 OVER HEAD STOCK 10713 LENGTH OVER Fig 5.2 UNDERFRAME TRANSITION) OPEN BOGIE(NON OFCOUPLER WAGON ( TYPE BOXN) FIG 5.13 UNDERFRAME OF BOGIE OPEN WAGON (TYPE BOXN) Page 5 of 14 CHAPTER 5 - UNDERFRAME WAGON MAINTENANCE MANUAL Fig. 5.3 BOGIE OPEN WAGON TYPE `BOXNHL UNDERFRAME ARRANGEMENT Page 6 of 14 CHAPTER 5 - UNDERFRAME Page 7 of 14 Fig 5.4 BOGIE OPEN WAGON TYPE `BOXNHL (MBS)' UNDERFRAME ARRANGEMENT WAGON MAINTENANCE MANUAL CHAPTER 5 - UNDERFRAME Page 8 of 14 Fig 5.5 BOGIE COVERRD WAGON TYPE 'BCNHL' UNDERFRAME ARRANGEMENT WAGON MAINTENANCE MANUAL CHAPTER 5 - UNDERFRAME Page 9 of 14 503. NEED OF THE REPAIRS TO BOGIE WAGON UNDERFRAME FOR MILD STEEL WAGONS a. The underframe is built up of suitable rolled and pressed steel sections welded together. In earlier design underframe members were riveted construction by providing gussets, knees etc. It is a general practice to provide a positive camber in the underframe to obviate any chances of sagging after loading in service. This is necessary since the underframe of a bogie wagon is considerably longer than that of a four wheeler. b. The general damages to the headstock and other under frame members in bogie wagons are attended as per para 506 to 508. Some of these underframes are susceptible to development of cracks at side bearer location on the underframe bolster bottom flange. The repair procedure for this defect is given in RDSO technical pamphlets WM-74002 and 74003. c. Pressings of the head stock get damaged and at the time of POH they are invariably required to be stripped, straightened and refitted, for proper head stock alignment. In case head stock pressings are badly damaged, these should be replaced. It is also a good practice to keep stock of some spare head stock pressings to reduce the cycle time and the damaged ones can then be brought into reuse after repairs in the blacksmith shop. d. Centre sills, of bogie wagons, are generally fabricated with rolled Z-Section. In service, centre sills are not damaged. However, some times due to accident or over loading, centre sills may get damaged. Such center sills should be repaired as per RDSO Drg.No.WD-99031-S-1. e. In case of BRN wagons, the problem of breakage/detachment of fixed ends/ headstock and sagging of sole bar/centre girder was noticed within first POH period. RDSO vide letter no.MW/BRN Dt. 7.1.99 asked Railways to modify the wagon to arrest such failures. These modifications are shown in RDSO Drg.No.WD-95010-S-1,S-2 and S-3. Procedure for re-cambering of bogie Rail wagon type BRN/BRNA/BRNHS as per RDSO pamphlet No.G-107 to be followed 504. REPAIR PROCEDURE A. Inspection of underframe At the time of POH, the underframe is to be inspected in respect of following points specifically, as the underframe is the most important sub assembly of the wagon which imparts necessary rigidity to the wagon body as a whole. a) Rivets/Lock bolts All the rivets/Lock bolts specifically those of axle guard, scroll irons, head stock, stanchions and knees joining the main members are checked for looseness. Ensure that these are not broken. All slack/broken rivets/lock bolts are to be replaced by sound ones at the time of POH. b) Cracks The underframe is also inspected for any cracks. In case of a horizontal crack, it is drilled at both ends and the cracked portion gauged out and welded. In case of vertical cracks, patching strengthens the cracked portion. WAGON MAINTENANCE MANUAL CHAPTER 5 - UNDERFRAME Page 10 of 14 B. Alignment The underframe is inspected for its proper alignment and any deflection of its members either in the form of sagging or buckling should be attended to or rectified. Since the alignment of the underframe has a very important role to play in guiding the wheels to run properly, the alignment is to be checked at various planes. 505. CLEANING AND DE-RUSTING OF THE UNDERFRAME The cleaning of the underframe and its fittings can be carried out after the wagon is placed on the trestles. Both the de-rusting and cleaning of underframe and its fittings can be carried out simultaneously. The members of the underframe are de-rusted by scraping and hammering so that it can be checked if any members are by heavily corroded or deformed requiring rectification. 506. REPAIRS TO HEAD STOCK i. Slightly bent members or portions of them as the case may be, are heated in position by hack’s burner and straightened by means of straightening devices or by applying blows with sledge hammer. For carrying out this repair, the buffer assembly is stripped off and if necessary, the floor plate which is riveted to the head stock is gas cut and rivets punched out to facilitate the proper straightening of the bent portion. ii. Stripping the heavily bent/damaged members and getting them straightened and aligned in the smith shop. iii. All the underframe members are to be inspected as per IRCA Part III (Latest). 507. REPAIRS TO DIAGONALS AND CROSS BARS The repair procedure for these items is also done as per procedure given in para 506. 508. REPAIRS TO SOLE BARS Sole bars are made from ISMC-250x9.0 web channel of copper bearing mild steel for most of the bogie wagons except on BOXNCR wagons where the channel is of IRSM- 41 carton steel. Most of the new wagons sole bars are made from CRF sections of IRSM-44 or micro alloyed steel. Generally, damage to sole bar occurs at locations adjacent to head stock stanchions at door location. The mild steel/IRSM-41 sole bar repaired in the following methods:- i. Cutting of entire sole bar portion and grafting a new portion prepared out of channel of the same section. Such type of replacement is always supported with double flanged U shaped sole bar patch, not less than 10 mm thick and a back plate is to be also provided. ii. Cracks at flanges and web are given proper repairs by electric welding as per instructions contained in IRCA Part III(Latest) rulebook and issued by authorities from time to time. Cracks extending up to webs are duly support with plain or flanged patch as the case may be. iii. Slightly bent sole bars are, however, repaired by local heating and straightening. If the flanges are only bent, the same are straightened by a jawed crow bar. iv. The patching has to confirm to IRCA part III rule No. 2.11.3. v. No patch shall be less than 10mm thick. Every patch shall be riveted to sole bar web and flange. WAGON MAINTENANCE MANUAL CHAPTER 5 - UNDERFRAME Page 11 of 14 vi. The outer patch shall cover the full depth of the web and the full width of the crack flange, top or bottom. vii. The inner patch shall cover the full depth of the channel and shall be of the same length as per the outer patch to the extent possible. viii. Where inner and outer patches cannot be fitted due to the presence of other fittings on the sole bar, only the outer or inner patch may be fitted. The thickness of the patch plate in such cases shall not be less than the thickness of parent material. ix. The cracks in mild steel sole bar flange may be repaired by welding. x. Existing rivet holes shall be utilised for patch rivets. xi. Additional rivets shall be of diameter not less than 10 mm at a pitch of not more than 90 mm. xii. The length of the sole bar patch plate should not be less than 508 mm. xiii. Experience shows that on BG, the underframe of open wagon gets damaged more often than covered wagon because heavier loads are generally carried in open wagons. This also leads to higher incidence of damage during shunting in case of uneven loading or when the consignment is not secured properly inside the wagon. xiv. A sketch of a typical straightening device used for repairs of headstock is given at Fig. 5.10. xv. Generally pitting/ corrosion on sole bar occur at door ways on open wagons. The provision of protection plates to sole bars is made at these locations, 3.15 mm thick copper bearing mild steel protection sheet is to be welded around the web below the door opening area if the thickness of the web has not been reduced by more than 2 mm where as by 5 mm copper bearing mild steel plate if the reduction in the web thickness is more than 2 mm but less than 5mm. As the web thickness of the sole bar of ISMC 250 X 82 is 9 mm, it concludes that any sole bar web found to be less than 4 mm should be replaced. 509. REPAIRS TO FLOOR PLATE The underframe also derives strength from the floor plates, which are generally of 4mm /5mm /6mm thickness. These floor plates are generally riveted/welded to the underframe members, thus providing additional strength to the underframe. As this method is very time consuming, most of the workshops are now resorting to the welding of floor plates as an alternative. This is now an approved practice and RDSO has issued standard sketches for various types of wagons showing how it is to be done. 510. UNDERFRAME OF BRAKE VAN It has been observed that underframe of brake vans have a tendency to buckle in service. One method of straightening of the drooping ends is to hold the main members in a fixed position by means of screw couplings anchored against a fixed structure and then raising the ends by means of screw jacks. No heating is required in this case and as such damages to the underframe steel structure which may occur as a result of heating are also avoided. WAGON MAINTENANCE MANUAL CHAPTER 5 - UNDERFRAME Page 12 of 14 511. BVZI BRAKE VAN The bogie brake van type BVZI with ICF trolley has been introduced in 2004. The under frame of BVZI brake van is 5 meters longer than 4-wheeled BVZC brake van under frame. Owing to frequent failure in service of CP top bracket of BVZI brake van, the CP top bracket has been modified for new manufacturing vide RDSO letter No. MW/BVZI dated 25.01.2011. A separate design (Drawing No.WD-11065-S-01) CP top bracket for replacing old design bracket with new unitized design for compulsory replacement during POH/ROH has been issued vide RDSO letter No. MW/BVZI dated 29.12.2011. Design of foot step of old BVZI wagon was similar to BVZC brake van and during maintenance, bottom foot step was cut by the maintenance depots. Therefore, a separate design for foot step arrangement drawing No. WD-81035-S-19(sheet-2) has been issued for new manufacturing and repair purposes. For guard seat of BVZI wagon, drawing No.WD-04059-S-01 has been issued. 512. LIST OF MODIFICATIONS i. Provision of side bracket with link on BRN wagons to facilitate securing of steel plant consignments to wagon body vide letter No. MW/ACT/BG dated 27.05.94. ii. Provision of stiffener angle on axle guard of BVZC brake van vide letter No. MW/CWSC/SECRETARIAT dated 23.11.93 & 28.2.94. iv. Strengthening of BRN wagon underframe vide letter No. MW/BRN dated 7.1.99. v. Corrosion in BRN Wagons vide letter No. MW/BRN dated 31.03.1999. vi. Modification of CP top bracket of BVZI brake van vide letter No. MW/BVZI dated 25.01.2011. vii. Procedure for Re-cambering of Bogie Rail Wagon type “BRN/BRNA/BRNAHS” as given in RDSO’s letter No. MW/BRNA dated 03.07.2015. NOTE: Repair procedure of stainless steel wagons are discussed in the APPENDIX- VI WAGON MAINTENANCE MANUAL CHAPTER 5 - UNDERFRAME Page 13 of 14 LENGTH OF PLATE NOT TO BE LESS THAN 508 57 32 32 SOLE BAR 57 SCROLL IRON 16 DIA RIVETS PLATE 10 THICK CRACKED POSITION 6 FIG. 5.9 PATCHING OF SOLE BAR 6 DRAW BAR WASHER BRACKET DISTANCE PIECE HEAD STOCK PLATE NUT FOR TIGHTENING FIG. 5.10 HEAD STOCK STRAIGHTENING DEVICE LENGTH OF PLATE NOT TO BE LESS THAN 508 57 32 32 SOLE BAR 57 WAGON MAINTENANCE MANUAL SCROLL IRON 16 DIA RIVETS PLATE 10 THICK CRACKED POSITION CHAPTER 5 - UNDERFRAME Page 14 of 14 513. REPAIR AND MAINTENANCE IN SICKLINE & ROH DEPOT Thorough inspection of underframe is to be carried out. Major repairs as well as all defects and deficiencies that come to the notice must be given meticulous and thorough attention. The following work is to be carried out: Buffer sub assemblies and draw gear should be within prescribed minimum and maximum dimensions Ensure that the buffers are not dead i.e. the springs have not become ineffective otherwise all the buffing load will have to be directly taken by the underframe members leading to extensive damage. Head stock, sole bars and diagonal members to be repaired. For stocks having chronic failure of the main members, action to be taken to strengthen these members. In order to increase the rigidity of the joints, cast steel/fabricated knees and brackets to be provided. All the rivets, specifically of axle guard, scroll irons, head stock and knees joining the main members, are checked for looseness In case of a horizontal crack, it is drilled at both ends. The cracked portion is gouged out and welded. In case of vertical cracks, patching is done to strengthen the cracked portion. Repairs to head stock to be done as given in para 506. Repairs to diagonals and cross bars to be done as given in para 507. Repairs to sole bars to be done as given in para 508. 514. REPAIR & MAINTENANCE IN WORKSHOP DURING POH/NPOH Thorough inspection of underframe is to be carried out. Major repairs as well as all defects and deficiencies that come to the notice must be given meticulous and thorough attention. In addition to the work indicated in Para 512, the following work is to be carried out in workshops during POH/NPOH :- Inspection of underframe, as given in para 504, to be done for i. Rivets ii. Cracks iii. Alignment The cleaning and de-rusting of the underframe and its fittings. Repairs to floor plate as given in para 509. Underframe of brake van as given in para 510. Underframe of Bogie wagon as given in para 503. Paint underframe as per Spec. G-72 (Rev.3) or latest amendment. XXXXXXXXX WAGON MAINTENANCE MANUAL