CnW Maintenance Manual - Wagon Body PDF
Document Details
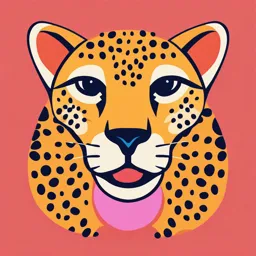
Uploaded by SolicitousOklahomaCity
null
Tags
Summary
This document provides an overview of wagon body construction for various types of wagons, including open, covered, flat, and hopper wagons. It details the components, materials, and general construction methods for each type. Specific details on doors, ends, sides, and roofs are also discussed.
Full Transcript
CHAPTER 4 - WAGON BODY Page 1 of 28 CHAPTER 4 WAGON BODY 401. INTRODUCTION The superstructure attached to the underframe of a wagon is called wagon body. It consis...
CHAPTER 4 - WAGON BODY Page 1 of 28 CHAPTER 4 WAGON BODY 401. INTRODUCTION The superstructure attached to the underframe of a wagon is called wagon body. It consists of body side and ends with their supporting structures such as stanchions, corner angle in case of open wagons, copings, roof structures, carlines; roof sheets in the case of covered wagons; hoppers and their supporting members in case of hopper wagons; tank barrels, cladding, if any, and supporting saddles in the case of tank wagons. Doors, door fittings, operating handles, louvers for ventilation and various fittings such as cleats, handles, hooks, footsteps, hand brake wheel and ladders also form part of the body. This chapter is concerned with the body or superstructure of general purpose open and covered wagons, hopper wagons, bogie flat wagons including container wagons and military wagons. The Superstructure and fittings of tank wagons are dealt with separately in the Chapter 9 on Tank wagon. 402. GENERAL CONSTRUCTION OF OPEN WAGON A. SIDES Sides are made up of side panels and side stanchions, which are attached to the underframe by crib angles and side stanchions. They include top copings, intermediate copings if any, doors, door fittings, hand holds, tarpaulin cleats and label holders. B. ENDS Ends are similar in construction to sides in that they consist of end panels, end stanchions, top copings and intermediate copings. Attachment to the underframe is by means of end floor angles, corner angles and through the stanchions. Corner angles connect the ends with the sides. Open wagons have reinforcing angles at each end together with reinforcing gussets and corner pressings at the corner top. C. DOORS Each side of the wagon is provided with door for manual unloading. The doors are hinged at the bottom with locking arrangement by chainless cotter at the top. In BOXN wagons two locking bolts per door have been provided to avoid slipping of chainless cotter during tippling of wagon. 403. GENERAL CONSTRUCTION OF COVERED WAGON A. SIDES Sides are made up of side panels and side stanchions, which are attached to the underframe by crib angles. They include top copings, doors, door fittings, label WAGON MAINTENANCE MANUAL CHAPTER 4 - WAGON BODY Page 2 of 28 holders, rain protection angles above swing doors, door striking plates and anti bleeding device below the flap doors. B. ENDS Ends are similar in construction to sides in that they consist of end panels, end stanchions, top copings and in some cases, intermediate copings. Attachment to the underframe is by means of end floor angles, end angles and through the stanchions. Covered wagons are provided with ventilators at the upper end of body ends. Corner angles connect the ends with the sides. C. ROOF Roofs of covered wagons consist of roof sheets and carlines. Roof sheets are much thinner than the sheets used for the body sides and end panels. D. DOOR Each side of the wagon is provided with door for manual unloading. The doors consist of swing doors at the top with label holder hinged to the angles on the sides and flap doors at the bottom, hinged at the bottom with Anti bleeding device. 404. GENERAL CONSTRUCTION OF FLAT WAGON AND WELL WAGON A. ENDS Flat/well wagons do not have side wall and roof. The superstructure consists of either fixed or flexible ends. These are fixed to the underframe through stanchions, side attachment plates and crib angle. B. SIDE STANCHION Flexible side stanchions are attached to the sole bar through brackets. In addition, support brackets are also provided in rail wagons and well wagon. In container flat wagons, retractable anchoring locks are provided. 405. GENERAL CONSTRUCTION OF HOPPER WAGON A. SIDES Sides are made up of side panels and side stanchions, which are attached to the underframe. They include top copings, side stiffeners, doors in side discharge wagons, and label holders. B. ENDS Ends consist of end panels, end stanchions, end top copings and in some cases, stiffeners. Attachment to the underframe is through the stanchions. Corner angles connect the ends with the sides. C. DOOR AND DOOR OPERATING MECHANISM Hopper wagons are provided with either side discharge/centre discharge doors or both. Door operating mechanism is generally manually operated by means of bevel wheel and worm wheel connected to door operating hand wheel. In some WAGON MAINTENANCE MANUAL CHAPTER 4 - WAGON BODY Page 3 of 28 special type of hopper wagons like BOBRN, pneumatically operated door operating mechanism has been provided. 406. NATURE OF REPAIRS REQUIRED IN WAGON BODY Apart from wagons involved in accidents or other serious mishaps, attention is normally necessitated because of the following defects:- i. Corrosion of panels, floor plates and roof sheets. ii. Puncturing of panels due to improper loading, inadequately secured consignments or deliberate tampering. iii. Bulging of ends due to shifting of loads. iv. Tearing of panels, fracture of stanchions and shearing of rivets due to severe impacts, and shifting of loads. v. Corrosion of end floor angles and crib angles. vi. Bulging of side usually occur after a prolonged period in service. vii. Slackening of rivets due to the combined effect of ageing, corrosion, wear and tear. viii. Weakening of welded joints due to loss of weld metal by corrosion, wear and tear. ix. Wearing out of door hinges. x. Damage to door fittings because of wear and tear or mishandling. xi. Distortion of doors mainly because of mishandling. xii. Failure of welded joints. xiii. Distortion or cracking of stanchions and other structural members because of abnormal loads, e.g., those due to defective clamping on tipplers. xiv. Wear and tear or breakage of miscellaneous fittings, such as ladders, cleats, label holders etc. xv. Damages due to mechanised loading/ unloading (Payloaders/ Tipplers) 407. CORROSION IN WAGON BODY The corrosion of wagon floor and roof sheets results from: i. Water logging in crevices and overlaps. This is greatly accentuated if cleaning is neglected, since the accumulated dust and refuse retain moisture for a prolonged period. ii. Contact of panels with residues from corrosive consignments e.g., salt, fertilizers etc. iii. Spillage of corrosive fluids due to defective packing or rough handling. iv. Escape of corrosive vapours from the consignment. v. Inadequate protection from weathering because of poor painting or inadequate surface preparation. vi. The current practice is to paint only the exterior of the wagon body and not the interior, except for inside panels up to a height of 230 mm from floor, rivet seams in the case of covered wagons, the swing and flap doors and the roof. The interior is left largely unpainted because paints have hitherto not been available which could withstand the constant scrubbing action of the consignment against the wagon walls. It is nevertheless a fact that most of the time corrosion originates from the interior of a wagon rather than the exterior. WAGON MAINTENANCE MANUAL CHAPTER 4 - WAGON BODY Page 4 of 28 408. ANTICORROSIVE MEASURES i. The most important anti corrosive measure to be taken in day to day working is to ensure that the wagon is kept thoroughly clean and receives special attention in this respect after it has transported a corrosive or hygroscope commodity. ii. The second important step to prevent corrosion is to ensure that cleaning, surface preparation and painting are carried out with due thoroughness. The correct procedure to be followed in major maintenance schedules is given at the end of this chapter. The procedure to be adopted at the time of minor repairs should come as close to this as practicable. iii. While attending to miscellaneous repairs, panel patching or welding; it is important to ensure that surfaces in contact are well fitted to avoid water pockets. Due care is to be taken to clean and paint the affected surfaces to prevent corrosion by electrochemical action. iv. Use of Stainless Steel (IRS: M44) has been started in wagon rehabilitation/ new manufacture. This material has much better corrosion resistance. 409. REJECTABLE DEFECTS The inspection of wagon body is to be carried out in sicklines and workshops as per procedure laid down in IRCA Part-III Rule 4.2 & 4.7. 410. REPAIRS IN SICKLINE & ROH DEPOT 410A PANEL PATCHING The bottoms of body side and end sheets are particularly vulnerable to destruction by corrosion and also puncturing by miscreants. If the area to be patched extends beyond 260 mm from the floor height, either two standard patches of 5 mm thickness should be used one above the other or a single special patch of 5 mm thickness and a width of 520 mm should be used. In case two or more adjacent panels require patching at a time, the complete length of corrosion can be covered by a special patch, which must, however, extend from stanchion to stanchion, as shown in figure 4.1. The standard panel patches for BOXN wagons are given in Table- 4.1. For detailed instructions of panel patching for BOXN wagon RDSO Drg. No. WD-94047-S-1 may be referred. In case of BCN/BCNA wagons, the thickness of plate should be 3.15 mm for end & sides and 1.6 mm for roof and the sizes depends on affected area to be covered for repair. WAGON MAINTENANCE MANUAL CHAPTER 4 - WAGON BODY Page 5 of 28 SPECIAL PATCH PLATE CORNER STANCHION STANCHION FIG 4.1 CUT ALONG THIS EDGE EXISTING PANEL CRIB ANGLE FIG 4.2 CUT ALONG THIS EDGE EXISTING PANEL END FLOOR ANGLE HEAD STOCK FIG 4.3 PATCH PLATE 13 PACKING STANCHION FIG 4.4 WAGON MAINTENANCE MANUAL CHAPTER 4 - WAGON BODY Page 6 of 28 TABLE- 4.1 PANEL PATCHES FOR BOXN WAGON S. Width (mm) Plate Plate Material No Step size Step size Step size length thickness specification A B C (mm) (mm) 1. 300 610 1275 552 5 IS:2062 E250 2. 300 610 - 552 5 " 3. 300 680 - 1470 5 " 4. 300 680 - 1445 5 " 5. 300 525 1170 1445 5 " 6. 315 - - 1470 5 " 7. 300 600 850 445 5 " 8. 820 - - 445 5 " 9. 300 600 850 555 5 " 10. 820 - - 555 5 " 11. 300 600 850 700 5 " 12. 820 - - 700 5 " i. For locations other than the skirting plates, damaged panels should be replaced by using standard patches. These patches should invariably be of the same thickness as the damaged panel. ii. Sick lines may weld or rivet smaller patches to take care of minor damages, but in no case, should a patch of less than 100 mm on any one side be used. If the patch is attached by riveting there should not be less than 8 rivets securing the patch. The pitch of the rivets must also not exceed 90 mm. iii. Standard patch plates should, preferably be kept ready in stock in shops and sicklines after proper surface cleaning and painting with two coats of zinc chromate primer. 410B. PROCEDURE FOR WELDED PATCHES i. Examine and mark the area of patch to be cut. Cut the corroded panel along crib/end floor angle and up to a height suitable for standard patches, as shown in Fig. 4.2 and 4.3. The 2.5 mm thick old panel sheet at the stanchion should be retained as a packing piece if not badly corroded. Otherwise use fresh 5 mm thick packing (RDSO Drawing No. WD-94047-S-1). The packing should extend 13mm wherever lap welding of the new patch with packing piece is involved (See Fig. 4.4). ii. Cut rivets on stanchion as required and end floor angle horizontal leg by 10 mm when fitting patches at the corners as shown in Fig.4.5. Take a standard patch plate from stock or prepare the same from plate of requisite thickness. WAGON MAINTENANCE MANUAL CHAPTER 4 - WAGON BODY Page 7 of 28 iii. Cut floor plates by 8mm for fitting new patch, as shown in Fig. 4.5. As an alternative, the patch plate may be made to rest over the floor plate, as shown in Fig. 4.6 & 4.7. In case, floor plates also require renewal, the width of the floor plates should be reduced to follow the arrangement shown in Fig. 4.8 & and 4.9. Secure the standard patch on the wagon by means of tack welding. Weld all around. iv. Rivet 2.5mm packing piece in position as shown in Fig. 4.10. v. Overlapping portions should be welded on both sides as shown in Fig. 4.11 and 4.12. vi. Ensure continuous welding without any craters. vii. In case of bulged panels, the patch should be riveted to the panels, as shown in Fig. 4.13. viii. Clean and repaint the welded portion at locations where paint has been burnt off. WAGON MAINTENANCE MANUAL CHAPTER 4 - WAGON BODY Page 8 of 28 END FLOOR ANGLE CUT HERE 10 CORNER STANCHION FIG. 4.5 PATCH PLATE FLOOR PLATE CRIB ANGLE FIG. 4.6 WELD PATCH PLATE WELD FLOOR PLATE CRIB ANGLE FIG. 4.7 PORTION OF FLOOR PLATE 8 TO BE CUT OR REDUCED FLOOR PLATE CRIB ANGLE FIG. 4.8 WELD PATCH PLATE WELD FLOOR PLATE CRIB ANGLE FIG. 4.9 WAGON MAINTENANCE MANUAL CHAPTER 4 - WAGON BODY Page 9 of 28 PACKING PATCH PLATE STANCHION FIG 4.10 PATCH PLATE WELD WELD PACKING STANCHION FIG 4.11 EXISTING PANEL WELD WELD PATCH PLATE FIG 4.12 EXISTING PANEL 10 DIA RIVET PATCH PLATE FIG 4.13 WAGON MAINTENANCE MANUAL CHAPTER 4 - WAGON BODY Page 10 of 28 410C. RIVETED PATCH Riveted patch should be avoided in workshops. These can however be applied in sickliness and ROH depots as per following procedure. i. Examine and mark the area of the patch to be cut. ii. Take a standard patch plate from stock or prepare the same from plate of requisite thickness. iii. Position the patch on the wagon and mark the location of the rivet holes. iv. Drill/punch the holes on both the patch and the wagon panel and secure the latter in position by temporary bolts and nuts. v. Rivet the patch in position. vi. Ensure that riveting is sound and with concentric snap heads, and also that mating edges are set properly leaving no gap in between. 410D. REPAIRS TO BULGED ENDS If there are no serious damages to wagon ends other than bulging, the bulges can be effectively removed without dismantling. If two wagons with bulged ends are coupled together and a hydraulic jack is applied between them at the bulges, suitable packing being interposed between the jack and the wagon body. This method is particularly effective in dealing with dread-naught ends. 410E. REPAIRS TO BODY STRUCTURAL MEMBERS (STANCHIONS, CARLINES AND COPINGS) a. Damages to these members are usually due to rough handling, heavy shunting impacts or shifting of loads due to improper packing/stacking of the consignments. At first these components bulge out, but later even the rivets holding them to the underframe/superstructure members break out. It should be ensured that the bulging of these components does not cause infringements with the maximum moving dimensions. Bulging of these components by more than 25mm should be rectified. These components should be straightened without dismantling by pulling into correct position with the help of a chain and screw coupling or stripped and straightened either cold or by heating, as required and then riveted in position. Spot heating and cooling to straighten the stanchions can rectify bulging of all welded ends. b. In certain cases, these components may have developed cracks, or may have broken in pieces. Such of these components should be repaired by welding both the pieces and applying a stiffener angle prepared by bending a 6mm plate in the shape of an angle with its outer faces sitting flush in the inner profile of the member to be patched and welding it all round to the member. Elongated holes in these components should be filled up by welding and refilled. 410F. WATER TIGHTENING OF WAGON Covered wagons must be kept watertight at all times. Covered wagons must be tested for water tightness at the time of leaving the workshop after POH or other repairs. All empty covered wagons attended to in sicklines, should also be tested for leaks, and made watertight by applying sealing compound before the onset of the monsoon season, a special drive should be instituted and sealing compound must be applied at WAGON MAINTENANCE MANUAL CHAPTER 4 - WAGON BODY Page 11 of 28 all points of covered wagon bodies, which are likely to leak particularly peripheries of riveted patches other overlaps and small holes. Before the application of sealing compound, mechanical defects such as bulged panels severely distorted body structural members, gaping joints, loose rivets and other corroded areas must be attended to. It should be ensured that the surfaces are clean and dry before sealing compound is applied. An attempt must not be made to fill up large gaps or other openings with sealing compound. Holes more than 6 mm in diameter should be filled by rivets. Irregular openings and cuts with more than 25 mm length and 3 mm width should be repaired by patching or welding. After a wagon has been made watertight, it should be marked “WT” with station code and date on the left-hand bottom corner of both sides. 410G. REPAIRS TO DOORS AND DOOR FITTINGS (FOR MILD STEEL WAGONS) The main defects arising in doors are:- Distortion due to wedging or other mishandling Jamming of hinges Excessive clearances in hinges Inadequate overlap between flaps and door leaves Gaping of doors at the stanchions Distortion or breakage of tower bolts Breakage of hinges and Damage to gravity cotters, hooks and hasps. Damaged doors of covered wagons are responsible for a very large proportion of claims due to wetting or pilferage of consignments. Warpage of flap doors is often responsible for jamming of flap door hinges. Special care must therefore, be taken in attending to doors. Distorted or bulged doors must be taken down and straightened to ensure proper fit. Worn out hinges are responsible for sagging or gaping doors and inadequate overlap. Such hinges must be replaced with new or reconditioned ones. Bent door stanchions and depressed crib angles must be straightened to ensure free functioning of doors and prevent gaping. Corroded crib angles must be cut out and replaced. Graphite grease should be introduced in all hinges, sliding cotters and other working parts. After repairs, doors must sit flush against striking plates with adequate overlap between leaves and without gaping at the stanchions or crib angles. Anti-bleeding devices and rain protection angles should also be checked and rectified where necessary. In the case of hopper wagons, it should be ensured that when the doors are closed, no gap is left between the chute plate and frame, and that the operating gear works freely and is in good condition. WAGON MAINTENANCE MANUAL CHAPTER 4 - WAGON BODY Page 12 of 28 410H. REPAIRS TO DOORS AND DOOR FITTINGS (FOR BCNHL WAGONS) BCNHL wagons have been fitted with doors which are different from conventional BCN doors. The first original design was initiated in May-2008, but some problems/defects were observed by the Zonal railways in field during loading unloading. The original(first) design is given in photo-4.1. BCNHL with BCNA door BCNHL Door designs: Original (First) Design (May’2008) Photo -4.1 WAGON MAINTENANCE MANUAL CHAPTER 4 - WAGON BODY Page 13 of 28 MMD & BCNHL Design Modification-I (June’2009) Existing Design modified by improving securing of doors (Drg. No. WD5-STD-S-1 & S-02) Observing problems in the field, design Modification-I was done in June-2009 vide Modification to eliminate gap between side wall and door at RDSO drawing No. WD5-SRD-S-01 & S-02 and existing design was modified to hinge, eliminate gap improving between door side wall and doorsecuring & hence at hinge, improving dooreliminating the securing & hence eliminatingpossibility of door the possibility hitting of door hitting&&rain rain water seepage. water seepage. See photo-4.2 Chainless cotter Door catch Photo-4.2 Further after gaining experience, design modification-II was incorporated in june- 2010 by providing tower-bolt on out side in place of inside the door. In this modification, small chainless cotter, (02 nos.) on outside were provided in place of existing long chainless cotters. See photo-4.3 WAGON MAINTENANCE MANUAL Design Modification-II (June’2010) Provision of small chainless cotter, ( 2 nos.) on outside, in place of existing long CHAPTER 4 chainless - WAGON BODY cotters. Page 14 of 28 Provision of Tower-Bolt on outside (instead of inside door). Swing bolt with double hasp Chainless cotter latch Hinged Door- Modification-II- (Current, latest Design of Hinge Door). Outer view of door locking arrangement Inner view of additional door locking arrangement Photo- 4.3 B. Some other Door designs used in limited numbers on the wagons 1. Design alteration (Pressed Door Design-4 hinges)-Variant-II was developed by RDSO in June-2009. See photo-4.4 WAGON MAINTENANCE MANUAL CHAPTER 4 - WAGON BODY Page 15 of 28 Design Iteration ( Pressed Door design- 4 hinges)-Variant-II (June’2009) Photo -4.4 Sliding door (Fabricated design): 2. Sliding door (Fabricated design) Bottom Roller design was developed by RDSO in Bottom roller design (Aug’2009) August-2009 and was provided on trial on limited no. of wagons. See photo-4.5 Photo -4.5 3. Sliding door ( Pressed design) Top mounted Rollers on Guide channel was developed in April-2010 and was provided on the wagons on trial basis. See photo- Sliding door (Pressed design): 4.6 Top mounted Roller on Guide Channel (Apr’2010) Photo -4.6 WAGON MAINTENANCE MANUAL CHAPTER 4 - WAGON BODY Page 16 of 28 C. BCNHL POPULATION DISPERSION ( IN TERMS OF TYPE OF DOORS USED) (Till the Rly Board Contract of -2012). See table below 1000 3064 D. NEED OF DOOR MODIFICATIONS BY RDSO Owing to severe Field issues in earlier versions (Original and Mod-I), Zonal Railways have already been advised to undertake retro fitment of modified locking arrangement (As per Mod-II) in the earlier versions of door assemblies. For above retro fitment, RDSO has issued procedure and drawing No. WD-10036-S-01/WD-06076-S-13 in June-2010. WAGON MAINTENANCE MANUAL CHAPTER 4 - WAGON BODY Page 17 of 28 E. PROVISION OF MODIFIED DOORS IN NEW BCNHL WAGONS From amongst the designs tried in the field, the door design with top mounted rollers ( 300 Wagons) have performed with the least field problems. This door design with modifications to address all field issues has been standardised for new BCNHL wagons. See Photo-07 Photo -07 F. DESIGN MODIFICATIONS IN SINGLE PIECE PRESSED SLIDING DOOR (BCNHL DESIGN-D WAGONS). (a) Roller Support Bracket: The Roller support bracket, welding has been strengthened. (b) Roller Design & associated changes in guide channel: b.1 The roller diameter increased to in order to ensure a roller overlap (with the guide channel) of 12mm in place of the existing 8 mm. b.2 The roller profile be modified from a flat profile to a convex profile, so that the existing line contact of the roller-guide channel , be modified to a point contact, to ensure smoother sliding motion of the door. b.3 The number & location of rollers be modified from the existing three rollers, equidistant along the door width to FOUR rollers, with two rollers each in the front & end of the door width. (c) Rain Protector Strengthening: The thickness of the rain protector channel be modified from the existing 2.5mm to 4mm. In order to provide support, additional ribs be provided, in the rain protector member. WAGON MAINTENANCE MANUAL CHAPTER 4 - WAGON BODY Page 18 of 28 (d) Provision of additional lateral stop member: In order to prevent a lateral falling/ movement of door sheet, an additional lateral stop member, needs to be provided. (e) Support in Bottom guide: To prevent blockage of the bottom guide owing to loose cement, a continuous slot has been provided. In order to provide strength to the bottom support, strengthening of the support be done by providing ribs at a pitch of 180mm between the auxiliary sole bar & the vertical face of the inside sole bar channel. (f) Back Sheet on door: The pressed impression on the door, results in a cavity that could lock/entangle loaded commodity bags, during the sliding motion of the door. To prevent the above, the depressed cavity be covered using off-cuts of the 1.6mm thick sheet. Sections of suitable sizes of this sheet (1.6mm thick) be welded on the inside of the pressed door sheet to cover the portion of the pressing & ensure a smooth door surface on the inside. (g) Strengthening the Bottom part of door sheet: During service in the field, the bottom part of the door, is reported to working-out from the provided slot. To strengthen the bottom portion of the door & to prevent its working out, a 6mm flat be welded at the bottom portion of the door sheet. WAGON MAINTENANCE MANUAL CHAPTER 4 - WAGON BODY Page 19 of 28 G. RETROFITABLE SLIDING DOOR FOR OLDER BCNHL WAGONS For older BCNHL wagons (manufactured prior to June’2010), & NECESSARILY warranting door replacements, a retrofitable two-part door design has been developed. Retrofit-able Sliding Door Retrofit-able Sliding Door Highlights of the Retrofitable sliding door design: 2 Part Sliding Door. Sliding using 3 sets of rollers (on each door ) mounted on top portion of door. Door Supported at Bottom. Top pivoted door with ability to move laterally (on being pushed by loaded bags). Retrofitable design. Can be fabricated as a unit & be mounted on existing BCNHL wagons. WAGON MAINTENANCE MANUAL CHAPTER 4 - WAGON BODY Page 20 of 28 Lower Weight (75 kgs of each door vs 105 kgs of Hinge door). No chances of hitting any fixed structure, since lateral projection less than side stanchions. Secured locking arrangement, easily operational from non-platform line. Ease of Loading/ Unloading owing to Sliding Door design. Ease of Maintenance- rollers fitted in guide channel, with end covers which can be replaced/ opened easily. Bearings in Rollers provided with dust cover & concealed to prevent ingress of dirt. To facilitate lateral movement transfer balls provided at door bottom. 410I. CLEANING, SURFACE PREPARATION AND PAINTING The correct sequence and procedure for cleaning, preparation of metal surfaces to be painted and the painting thereof; a. Preparation of surface before painting The purpose of cleaning is to remove dirt, oil, grease, rust and other contaminants, which would prevent the paint film from adhering to the metal or would provide a nucleus for commencement of corrosion. Cleaning by hammering, chiselling or scraping is unsatisfactory and should not be resorted to. The surface cleaning may be done by vigorously scrubbing with a stiff brush. All welded parts and adjacent surfaces should be thoroughly cleaned to remove residual alkaline flux and washed with hot water. b. A coat of priming paint should be applied immediately after the surface has been cleaned and dried. A delay of more than 4 hours may result in development of fresh rust on the surface. A second coat of primer must be given when the first coat is dry. Painting must be done under cover in a shed or shop. The painted surfaces must remain under cover until the paint is dry. c. Panel patches and riveting strips must be cleaned, as prescribed above, and given two coats of primer before storage or fitment. d. After completion of all repairs a final coat of finishing paint should be given to all painted surfaces. e. When the paint film is only partially damaged, it should be touched up with one coat of primer and then given the finishing coat. f. Surfaces, which will become inaccessible after assembly must be given complete painting before assembly. WAGON MAINTENANCE MANUAL CHAPTER 4 - WAGON BODY Page 21 of 28 411. REPAIRS AND MAINTENANCE IN WORKSHOPS DURING POH AND NPOH a. For body repairs, same procedure as described in para 410 A to 410 I above is to be followed. Note :- The detailed procedure for painting and specifications for different coats of paint are given in general standard specification G-72 read with latest amendments which may be referred to for more details. In addition to the above, following items to be carried out during POH in workshops. b. Lettering Lettering to be carried out as per IRCA Part III Rule 2.4 by stencilling the relevant figures. c. Punching of wagon particulars. d. PR plate e. Tare weight to be measured after POH and it should be marked up to one decimal. 412. IMPORTANT PRECAUTIONS TO BE TAKEN WHILE CARRYING OUT WELDING Welding entails the risk of fire if combustible materials are present near the area being welded. To prevent such accidents, the following precautions must be taken: A. Loaded wagons It should be ensured that the content is not inflammable. Should the contents be inflammable they must be transhipped before welding is attempted. Tank wagons should never be welded when loaded. B. Empty wagons It should first be ensured that no portion of an inflammable consignment packing material or dunnage is present in the area to be welded. Empty tank wagons should be given welding repairs only in depots specially equipped for this purpose and only after thorough steam cleaning and testing to ensure that there are no inflammable/explosive vapours left. C. Wagons fitted with CTRBs No welding should be attempted without effectively earthing the member or component to be welded. Neglect in taking this precaution will result in passage of the return current through the CTRB, which may suffer severe damage leading to premature failure. WAGON MAINTENANCE MANUAL CHAPTER 4 - WAGON BODY Page 22 of 28 413. IMPORTANT DO'S AND DON'TS Do's i. Ensure that you have the proper tools required for the job. Use of improper tools can make matters worse. ii. Ensure that tools and equipment are in good condition. iii. See that rivet heads are properly formed with correctly profiled snaps. iv. While fitting patches to structural members, ensure that the pitch of rivets conforms to the original pitch in the structural members. v. See that doors are provided with all required fittings so as to ensure proper securing and prevent unauthorised opening. vi. Ensure that door hooks are intact and so placed that they will engage with the door eye in open position. vii. Ensure that all chains links and other attachments are in position and in working order. Don’ts i. Do not use patches of less thickness than the original panel. ii. Do not patch existing patches. iii. Do not build up perforations in panel due to corrosion. Cut out and fit a new patch. iv. Do not permit empty wagons to run with open doors. v. Do not permit loaded wagons to run without properly secured doors. vi. Do not allow wagons with inadequately secured/lashed consignments. 414 MAINTENANCE OF STAINLESS STEEL WAGONS The Maintenance of Stainless Steel Wagons is covered in APPENDIX-VI 415 UPGRADED REHABILITATION OF BOXN TO BOXNR Vide Rly. Board’s letter no. 2005/ M (N)/204/2 (RSP) dated 02.11.07 it has been decided that rehabilitation of BOXN wagons would be done to BOXNR design (stainless steel body). The constructional differences between BOXN & BOXNR are as follows: WAGON MAINTENANCE MANUAL CHAPTER 4 - WAGON BODY Page 23 of 28 A. TECHNICAL REQUIREMENTS FOR UPGRADED REHABILITATION OF BOXN WAGONS TO BOXNR SHALL BE DONE AS PER RDSO SPEC. NO. WD.16.BOXNR-2010 OR LATEST After the rehabilitation and upgradation, the wagon shall be marked as BOXNR in place of BOXN. The major differences in constructional features of BOXN & BOXNR are as under: SIDE WALL BOXN BOXNR (i) Material mild steel (i) Material stainless steel(IRS:M44) (ii) Provided with 6 Nos. of side (ii) Provided with 9 Nos. of side stanchions with 8mm thick hat stanchions with 6mm thick CRF hat section ( on one side) section (on one side) (iii) Side sheets of 5mm thickness (iii) Side sheets of 3 mm thickness. (vi) Inside height of side wall is (iv) Inside height is 2127mm from floor 1950mm from floor level. level. (v) Two Nos. middle coping (v) Middle copings are not provided provided in sidewall. in side walls, except at corner side panels. (vi) Top coping provided with (vi) Top coping provided with press ISMC-100 section of BOX 100x100x6mm thick. (vii) Side stanchion riveted with (vii) Side stanchion huck bolted with sole sole bar with two rows rivets. bar with single row. DOOR PLATE (i) Door Plate provided with (i) Door plate provided with stainless Mild Steel for 5 mm thickness steel of 4 mm thickness. END WALL (i) Made with mild steel. (i) Made with stainless steel (IRS:M44) (ii) Each End wall provided with (ii) End wall provided Two end 4 Nos. of End stanchions of stanchion in three pieces and two ISMC-150mm. middle coping of Hat section 6 mm thickness. (iii) End top coping provided (iii) End top coping provided with with ISMC-150 channel. CRF section of BOX 100x100x6mm thickness (iv) End Sheet provided with 5 (iv) End Sheet provided with 3 mm mm thick thick FLOOR PLATE Floor Plate provided with Floor plate provided with stainless (i) Mild Steel for 6 mm thickness (i) steel of 4 mm thickness. WAGON MAINTENANCE MANUAL CHAPTER 4 - WAGON BODY Page 24 of 28 B. DESCRIPTION OF WORK: The rehabilitation of BOXN wagon body by using of CRF section (to RDSO’s specification no. WD– 01 – CRF – 08 or latest) and stainless steel (IRS:M 44: 97 latest revision) will provide additional strength to body and reduce corrosion. The volume will also increase to fully utilize the capacity upto 22.9 Tonne axle load for coal. Note: The procedure, precautions and facilities required for repairs to Stainless steel wagons will be similar to above upgradation. 416 LOCK BOLTS Almost all new wagons specially stainless steel wagons are provided with lock bolting instead of riveting. In repair/maintenance CP top of all wagons irrespective of materials are to be lock bolted. entire lock bolting is to be done with zinc plated/galvanized lock bolts (grade-8) having a minimum yield strength of 250 N/mm2. Lock Bolts have been introduced in the fabrication of Wagons. Lock bolt fasteners consist of Lock bolt pin and collar, and are installed with the help of special installation tools, as follows- Lock bolt pin is placed in drilled hole, and collar is placed onto the lock bolt pin. Installation tool engages and pulls the lock bolts pin. Tool swages the collar onto lock bolt grooves. Pin tail breaks off the lock bolt pin. The advantages of Lock bolts are – High strength Vibration resistant Fast and easy installation Maintenance free FIG. 4.14 LOCK BOLT WAGON MAINTENANCE MANUAL CHAPTER 4 - WAGON BODY Page 25 of 28 a) Proper Installation of lock bolts:- It should be ensured that: (i) The collar of lock bolt are completely swaged. The collar of lock bolt fasteners not completely swaged may be causes of improper tool operation or worn anvil in nose. (ii) The pintail of fastener break without fail. The pintail of fastener fails to break due to improper installation/incorrect fasteners. (iii) After breaking of pintail, the extruded/projected portion of lock bolt should be in the range of 2.00 to 10 mm and collar should always be on annular groove of lock bolt. (iv) Mismatch of holes to be reamed properly to align and gas cutting to match holes is strictly prohibited. b) Recommendations for Zonal Railways/ ROH depots: (RDSO vide letter No.MW/Lock Bolt dated 21.03.2014) The Yard examination/ rake inspection should include checks for any failed/missing/ loose Lock bolts/ Collars, especially in critical locations. Necessary repair/ re-installation of correct lock bolt/ collars, should be subsequently ensured. Lock bolts, if found failed/ missing should not be replaced with bolt-nut. Such a fitment, would invariably render the assembly differentially fastened, leading to consequential failure of the assembly/ component. During procurement of lock bolts/ collars, pre-despatch inspection of lock bolts/collars should be specified. WTC detailing functional properties, detailed in RDSO’s guideline or RITES inspection covering properties detailed in RDSO’s circulated guideline, should be ensured/ specified in PO’s. Lock bolt/ Collars failure noticed in wagons, should necessarily be reported to RDSO. For the guidance of ZR’s the head marking details in lock bolts of all the three known sources are detailed in Annexure-VI. Records of the make of lock bolt/ collars, noticed issues in fitment & any probable reasons for noticed failure, should also be communicated. In case of under-warranty wagons, necessary warranty claims, should also be lodged, as per defined procedure/process. WAGON MAINTENANCE MANUAL CHAPTER 4 - WAGON BODY Page 26 of 28 417 NEW WAGON NUMBERING SCHEME Monitoring and liquidating overage arrears of rolling stock is a focus area in the interest of safety of train operations. However, some of the Railways have reported difficulty in ascertaining the age of wagons where the manufacturer’s plate is missing. Also computerization of wagon data is becoming cumbersome with development of various versions in a category e.g. BG bogie open wagons BOXN, BOXNHS, BOXNAHA, BOXNCR, BOXNHL, BOXNR and BOXNLW are being clubbed together by the computer cell and shown as BOXN in the holding. To overcome the above-mentioned problems and to facilitate computerization of the wagon data base, a new wagon numbering system was introduced by Railway Board as per letter no. 2000/M(N)/60/2/wagon census. Dated 4th July, 2003 In the new scheme, the wagon number shall consist of 11 digits as follows: Type of Owning Year of Individual Wagon Check wagon Railway Manufacture Number Digit C1 C2 C3 C4 C5 C6 C7 C8 C9 C10 C11 The codification for various types of wagons, owning railways, year of manufacture and individual wagon no. are as follows: Type of Wagon Codes (C1, C2) i) Open Wagon Code allotted 10 to 29 BOXN 10 BOXNHA 11 BOXNHS 12 BOXNCR 13 BOXNLW 14 BOXNB 15 BOXNF 16 BOXNG 17 BOY 18 BOST 19 BOXNAL 20 BOXN-HL 22 ii) Covered Wagon Code allotted 30 to 39 BCNA 30 BCNAHS 31 BCCNR 32 BCN-HL 33 iii) Tank Wagon Code allotted 40 to 54 BTPN 40 BTPNHS 41 BTPGLN 42 BTALN 43 BTCS 44 BTPH 45 40 to 54 BTAP 46 WAGON MAINTENANCE MANUAL CHAPTER 4 - WAGON BODY Page 27 of 28 iv) Flat Wagon Code allotted 55 to 69 BRNA 55 BRNAHS 56 BFNS 57 BOMN 58 BRSTH 59 BFAT 60 BLCA 61 BLCB 62 v) Hopper Wagon Code allotted 70 to 79 BOBYN 70 BOBYNHS 71 BOBRN 72 BOBRNHS 73 BOBRAL 74 vi) Well Wagon Code allotted 80 to 84 BWTB 80 vii) Brake Van Code allotted 85 to 89 BVZC 85 BVZI 86 OWNERSHIP (RAILWAYS’) CODES (C3, C4) : SNo. Name of Railways Numerical codes 1 Central Railway 01 2 Eastern Railway 02 3 Northern Railway 03 4 North East Railway 04 5 Northeast Frontier Railway 05 6 Southern Railway 06 7 South Eastern Railway 07 8 Western Railway 08 9 South Central Railway 09 10 East Central Railway 10 11 North Western Railway 11 12 East coast Railway 12 13 North Central Railway 13 14 South East Central Railway 14 15 South Western Railway 15 16 West Central Railway 16 17 Wagons owned by CONCOR 25 18 Wagons owned by other private parties 26 WAGON MAINTENANCE MANUAL CHAPTER 4 - WAGON BODY Page 28 of 28 YEAR OF MANUFACTURE CODE (C5, C6): This will consist of last two digits of the year of manufacture. For example wagon manufacture in 2016 will have code 16. INDIVIDUAL WAGON No. (C7, C8, C9, C10): This will be running serial number from 0001 to 9999. Numbers 0001 to 0999 will be departmental stock and 1000 to 9999 will be other (traffic) stock. This will be running number irrespective of year. For departmental, after 0999, the number will begin from 0001. For others, after 9999, the number will begin from 1000. The series will not change with type of wagon. For example on ECR if 1001 is BOXNHS next wagon which may be BCNHS will be 1002. CHECK DIGIT – Method of calculation The CHECK DIGIT for each wagon is calculated using a six-step algorithm based on ten digit wagon number arrived at as indicated below. Type of Railway Year of Individual wagon Check wagon Code Manufacture Number Digit C1 C2 C3 C4 C5 C6 C7 C8 C9 C10 C11 Step – 1 Starting from the left, add all the characters in the even position. S 1 = C2 + C4 + C6 + C8 + C10 Step – 2 Multiply the sum by 3 to get 3. S1 Step – 3 Starting from the left, add all the characters in the odd position. S 2 = C1 + C3 + C5 + C7 + C9 Step – 4 Add the sum of step 2 to the sum of step 3 to get S4 = 3S 1 + S2 Step – 5 Round this total up to the next multiple of 10 Step – 6 The check digit is the number required to be added to round up to the next multiple of 10. * NOTE: If the total in S4 is already of 10, then the check digit is 0. WAGON MAINTENANCE MANUAL