Chapter 4 Metal Structure Repair PDF
Document Details
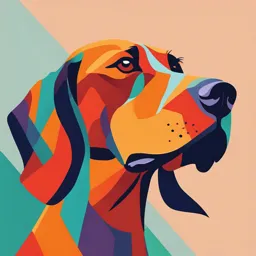
Uploaded by DaringDream
Tags
Summary
This document provides detailed instructions on the various techniques used for repairing and altering metal structures. It includes specific procedures for shaping metal into curved forms. It also covers procedures for repairing flat surfaces and lightening holes.
Full Transcript
out gradually by hammering lightly and gradually compressing the material in each buckle. The use of a small hardwood wedge block aids in working out the buckles. [Figure 4-152] 4. Planish the flange after it is flattened against the form block and remove small irregularities. If the form blocks are...
out gradually by hammering lightly and gradually compressing the material in each buckle. The use of a small hardwood wedge block aids in working out the buckles. [Figure 4-152] 4. Planish the flange after it is flattened against the form block and remove small irregularities. If the form blocks are made of hardwood, use a metal planishing hammer. If the forms are made of metal, use a soft-faced mallet. Trim the excess material away and file and polish. Stretching To form a flanged angle by stretching, use the same forming blocks, wooden wedge block, and mallet as used in the shrinking process and proceed as follows: 1. Cut the material to size (allowing for trim), determine bend allowance for a 90° bend, and round off the edge of the block to conform to the desired radius of bend. 2. Clamp the material in the form blocks. [Figure 4-153] 3. Using a soft-faced stretching mallet, start hammering near the ends and work the flange down smoothly and gradually to prevent cracking and splitting. Planish the flange and angle as described in the previous procedure, and trim and smooth the edges, if necessary. Curved Flanged Parts Curved flanged parts are usually hand formed with a concave flange, the inside edge, and a convex flange, the outside edge. The concave flange is formed by stretching, while the convex flange is formed by shrinking. Such parts are shaped with the aid of hardwood or metal forming blocks. [Figure 4-154] These blocks are made in pairs and are designed specifically for the shape of the area being formed. These blocks are made in pairs similar to those Figure 4-153. Stretching a flanged angle. Figure 4-152. Shrinking. Figure 4-154. Forming blocks. used for straight angle bends and are identified in the same manner. They differ in that they are made specifically for the particular part to be formed, they fit each other exactly, and they conform to the actual dimensions and contour of the finished article. 4-76 The forming blocks may be equipped with small aligning pins to help line up the blocks and to hold the metal in place or they may be held together by C-clamps or a vise. They also may be held together with bolts by drilling through form blocks and the metal, provided the holes do not affect the strength of the finished part. The edges of the forming block are rounded to give the correct radius of bend to the part, and are undercut approximately 5° to allow for spring-back of the metal. This undercut is especially important if the material is hard or if the bend must be accurate. The nose rib offers a good example of forming a curved flange because it incorporates both stretching and shrinking (by crimping). They usually have a concave flange, the inside edge, and a convex flange, the outside edge. Note the various types of forming represented in the following figures. In the plain nose rib, only one large convex flange is used. [Figure 4-155] Because of the great distance around the part and the likelihood of buckles in forming, it is rather difficult to form. The flange and the beaded (raised ridge on sheet metal used to stiffen the piece) portion of this rib provide sufficient strength to make this a good type to use. In Figure 4-156, the concave flange is difficult to form, but the outside flange is broken up into smaller sections by relief holes. In Figure 4-157, note that crimps are placed at equally spaced intervals to absorb material and cause curving, while also giving strength to the part. In Figure 4-158, the nose rib is formed by crimping, beading, putting in relief holes, and using a formed angle riveted on each end. The beads and the formed angles supply strength to the part. The basic steps in forming a curved flange follow: [Figures 4-159 and 160] 1. Cut the material to size, allowing about 1⁄4-inch excess material for trim and drill holes for alignment pins. 2. Remove all burrs (jagged edges). This reduces the possibility of the material cracking at the edges during the forming process. Holes Figure 4-156. Nose rib with relief holes. Crimps Figure 4-157. Nose rib with crimps. Flange Figure 4-158. Nose rib using a combination of forms. Figure 4-155. Plain nose rib. 3. Locate and drill holes for alignment pins. 4. Place the material between the form blocks and clamp blocks tightly in a vise to prevent the material from moving or shifting. Clamp the work as closely as possible to the particular area being hammered to 4-77 Figure 4-159. Forming a concave flange. prevent strain on the form blocks and to keep the metal from slipping. Concave Surfaces Bend the flange on the concave curve first. This practice may keep the flange from splitting open or cracking when the metal is stretched. Should this occur, a new piece must be made. Using a plastic or rawhide mallet with a smooth, slightly rounded face, start hammering at the extreme ends of the part and continue toward the center of the bend. This procedure permits some of the metal at the ends of the part to be worked into the center of the curve where it is needed. Continue hammering until the metal is gradually worked down over the entire flange, flush with the form block. After the flange is formed, trim off the excess material and check the part for accuracy. [Figure 4-159] Convex Surfaces Convex surfaces are formed by shrinking the material over a form block. [Figure 4-160] Using a wooden or plastic shrinking mallet and a backup or wedge block, start at the center of the curve and work toward both ends. Hammer the flange down over the form, striking the metal with glancing blows at an angle of approximately 45° and with a motion that tends to pull the part away from the radius of the form block. Stretch the metal around the radius bend and remove the buckles gradually by hammering on a wedge block. Use the backup block to keep the edge of the flange as nearly perpendicular to the form block as possible. The backup block also lessens the possibility of buckles, splits, or cracks. Finally, trim the flanges of excess metal, planish, remove burrs, round the corners (if any), and check the part for accuracy. 45° Figure 4-160. Forming a convex flange. Forming by Bumping As discussed earlier, bumping involves stretching the sheet metal by bumping it into a form and making it balloon. [Figure 4-161] Bumping can be done on a form block or female die, or on a sandbag. Either method requires only one form: a wooden block, a lead die, or a sandbag. The blister, or streamlined cover plate, is an example of a part made by the form block or die method of bumping. Wing fillets are an example of parts that are usually formed by bumping on a sandbag. Form Block or Die The wooden block or lead die designed for form block bumping must have the same dimensions and contour as the outside of the blister. To provide enough bucking weight 4-78 gouges, files, and rasps. 2. Smooth and finish the block with sandpaper. The inside of the form must be as smooth as possible, because the slightest irregularity shows up on the finished part. 3. Prepare several templates (patterns of the crosssection), as shown in Figure 4-161 so that the form can be checked for accuracy. 4. Shape the contour of the form at points 1, 2, and 3. 5. Shape the areas between the template checkpoints to conform the remaining contour to template 4. Shaping of the form block requires particular care because the more nearly accurate it is, the less time it takes to produce a smooth, finished part. 1 2 3 Templates for working the form block After the form is prepared and checked, perform the bumping as follows: 4 1 2 3 4 1. Cut a metal blank to size allowing an extra 1⁄2 to 1-inch to permit drawing. 2. Apply a thin coat of light oil to the block and the aluminum to prevent galling (scraping on rough spots). 3. Clamp the material between the block and steel plate. Ensure it is firmly supported yet it can slip a little toward the inside of the form. 4. Clamp the bumping block in a bench vise. Use a softfaced rubber mallet, or a hardwood drive block with a suitable mallet, to start the bumping near the edges of the form. 5. Work the material down gradually from the edges with light blows of the mallet. Remember, the purpose of bumping is to work the material into shape by stretching rather than forcing it into the form with heavy blows. Always start bumping near the edge of the form. Never start near the center of the blister. 6. Before removing the work from the form, smooth it as much as possible by rubbing it with the rounded end of either a maple block or a stretching mallet. 7. Remove the blister from the bumping block and trim to size. Form block Holddown plate Finished part Figure 4-161. Form block bumping. and bearing surface for fastening the metal, the block or die should be at least one inch larger in all dimensions than the form requires. Follow these procedures to create a form block: 1. Hollow the block out with tools, such as saws, chisels, Sandbag Bumping Sandbag bumping is one of the most difficult methods of hand forming sheet metal because there is no exact forming block to guide the operation. [Figure 4-162] In this method, a depression is made into the sandbag to take the shape of the hammered portion of the metal. The depression or pit has a tendency to shift from the hammering, which necessitates periodic readjustment during the bumping process. The degree of shifting depends largely on the contour or shape of the piece being formed, and whether glancing blows must be struck to stretch, draw, or shrink the metal. When forming 4-79 the sheet metal part. Hold one edge of the metal in the left hand and place the portion to be bumped near the edge of the pit on the sandbag. Strike the metal with light glancing blows. 5. Continue bumping toward the center, revolving the metal, and working gradually inward until the desired shape is obtained. Shape the entire part as a unit. 6. Check the part often for accuracy of shape during the bumping process by applying the template. If wrinkles form, work them out before they become too large. 7. Remove small dents and hammer marks with a suitable stake and planishing hammer or with a hand dolly and planishing hammer. 8. Finally, after bumping is completed, use a pair of dividers to mark around the outside of the object. Trim the edge and file it smooth. Clean and polish the part. Figure 4-162. Sandbag bumping. by this method, prepare a contour template or some sort of a pattern to serve as a working guide and to ensure accuracy of the finished part. Make the pattern from ordinary kraft or similar paper, folding it over the part to be duplicated. Cut the paper cover at the points where it would have to be stretched to fit, and attach additional pieces of paper with masking tape to cover the exposed portions. After completely covering the part, trim the pattern to exact size. Open the pattern and spread it out on the metal from which the part is to be formed. Although the pattern does not lie flat, it gives a fairly accurate idea of the approximate shape of the metal to be cut, and the pieced-in sections indicate where the metal is to be stretched. When the pattern has been placed on the material, outline the part and the portions to be stretched using a felt-tipped pen. Add at least one inch of excess metal when cutting the material to size. Trim off the excess metal after bumping the part into shape. If the part to be formed is radially symmetrical, it is fairly easy to shape since a simple contour template can be used as a working guide. The procedure for bumping sheet metal parts on a sandbag follows certain basic steps that can be applied to any part, regardless of its contour or shape. Joggling A joggle, often found at the intersection of stringers and formers, is the offset formed on a part to allow clearance for a sheet or another mating part. Use of the joggle maintains the smooth surface of a joint or splice. The amount of offset is usually small; therefore, the depth of the joggle is generally specified in thousandths of an inch. The thickness of the material to be cleared governs the depth of the joggle. In determining the necessary length of the joggle, allow an extra 1⁄16-inch to give enough added clearance to assure a fit between the joggled, overlapped part. The distance between the two bends of a joggle is called the allowance. This dimension is normally called out on the drawing. However, a general rule of thumb for figuring allowance is four times the thickness of the displacement of flat sheets. For 90° angles, it must be slightly more due to the stress built up at the radius while joggling. For extrusions, the allowance can be as much as 12 times the material thickness, so, it is important to follow the drawing. 1. Lay out and cut the contour template to serve as a working guide and to ensure accuracy of the finished part. (This can be made of sheet metal, medium to heavy cardboard, kraft paper, or thin plywood.) 2. Determine the amount of metal needed, lay it out, and cut it to size, allowing at least 1⁄2-inch in excess. 1. Lay out the boundary lines of the joggle where the bends are to occur on the sheet. 3. Place a sandbag on a solid foundation capable of supporting heavy blows and make a pit in the bag with a smooth-faced mallet. Analyze the part to determine the correct radius the pit should have for the forming operation. The pit changes shape with the hammering it receives and must be readjusted accordingly. 2. Insert the sheet in the brake and bend the metal up approximately 20° to 30°. 3. Release the brake and remove the part. 4. Turn the part over and clamp it in the brake at the second bend line. Select a soft round-faced or bell-shaped mallet with a contour slightly smaller than the contour desired on 5. Bend the part up until the correct height of the joggle is attained. 4. There are a number of different methods of forming joggles. For example, if the joggle is to be made on a straight flange or flat piece of metal, it can be formed on a cornice brake. To form the joggle, use the following procedure: 4-80 6. Remove the part from the brake and check the joggle for correct dimensions and clearance. Material being joggled Joggle block When a joggle is necessary on a curved part or a curved flange, forming blocks or dies made of hardwood, steel, or aluminum alloy may be used. The forming procedure consists of placing the part to be joggled between the two joggle blocks and squeezing them in a vice or some other suitable clamping device. After the joggle is formed, the joggle blocks are turned over in the vice and the bulge on the opposite flange is flattened with a wooden or rawhide mallet. [Figure 4-163] Since hardwood is easily worked, dies made of hardwood are satisfactory when the die is to be used only a few times. If a number of similar joggles are to be produced, use steel or aluminum alloy dies. Dies of aluminum alloy are preferred since they are easier to fabricate than those of steel and wear about as long. These dies are sufficiently soft and resilient to permit forming aluminum alloy parts on them without marring, and nicks and scratches are easily removed from their surfaces. Clamping device Joggle block STEP 1 Place material between joggle blocks and squeeze in a vice or other clamping device. Wooden mallet When using joggling dies for the first time, test them for accuracy on a piece of waste stock to avoid the possibility of ruining already fabricated parts. [Figure 4-164] Always keep the surfaces of the blocks free from dirt, filings, and the like, so that the work is not marred. Lightening Holes Lightening holes are cut in rib sections, fuselage frames, and other structural parts to decrease weight. To avoid weakening the member by removal of the material, flanges are often pressed around the holes to strengthen the area from which the material was removed. Lightening holes should never be cut in any structural part unless authorized. The size of the lightening hole and the width of the flange formed around the hole are determined by design specifications. Margins of safety are considered in the specifications so that the weight of the part can be decreased and still retain the necessary strength. Lightening holes may be cut with a hole saw, a punch, or a fly cutter. The edges are filed smooth to prevent them from cracking or tearing. Flanging Lightening Holes Form the flange by using a flanging die, or hardwood or metal form blocks. Flanging dies consist of two matching parts: a female and a male die. For flanging soft metal, dies can be of hardwood, such as maple. For hard metal or for more permanent use, they should be made of steel. The pilot guide should be the same size as the hole to be flanged, and the shoulder should be the same width and angle as the desired flange. Bulge caused by forming joggle STEP 2 Turn joggle blocks over in vice and flatten bulge with wooden mallet. Figure 4-163. Forming joggle using joggle blocks. Figure 4-164. Samples of joggled metal. 4-81 When flanging lightening holes, place the material between the mating parts of the die and form it by hammering or squeezing the dies together in a vise or in an arbor press (a small hand operated press). The dies work more smoothly if they are coated with light machine oil. [Figure 4-165] Working Stainless Steel Corrosion-resistant-steel (CRES) sheet is used on some parts of the aircraft when high strength is required. CRES causes magnesium, aluminum, or cadmium to corrode when it touches these metals. To isolate CRES from magnesium and aluminum, apply a finish that gives protection between their mating surfaces. It is important to use a bend radius that is larger than the recommended minimum bend radius to prevent cracking of the material in the bend area. When working with stainless steel, make sure that the metal does not become unduly scratched or marred. Also, take special precautions when shearing, punching, or drilling this metal. It takes about twice as much pressure to shear or punch stainless steel as it does mild steel. Keep the shear or punch and die adjusted very closely. Too much clearance permits the metal to be drawn over the edge of the die and causes it to become work hardened, resulting in excessive strain on the machine. When drilling stainless steel, use an HSS drill bit ground to an included angle of 135°. Keep the drill speed about one-half that required for drilling mild steel, but never exceed 750 rpm. Keep a uniform pressure on the drill so the feed is constant at all times. Drill the material on a backing plate, such as cast iron, which is hard enough to permit the drill bit to cut completely through the stock without pushing the metal away from the drill point. Spot the drill bit before turning on the power and also make sure that pressure is exerted when the power is turned on. Working Inconel® Alloys 625 & 718 Inconel® refers to a family of nickel-chromium-iron super alloys typically used in high-temperature applications. Corrosion resistance and the ability to stay strong in high temperatures led to the frequent use of these Inconel® alloys Figure 4-165. Lightening hole die set. in aircraft powerplant structures. Inconel® alloys 625 and 718 can be cold formed by standard procedures used for steel and stainless steel. Normal drilling into Inconel® alloys can break drill bits sooner and cause damage to the edge of the hole when the drill bit goes through the metal. If a hand drill is used to drill Inconel® alloys 625 and 718, select a 135° cobalt drill bit. When hand drilling, push hard on the drill, but stay at a constant chip rate. For example, with a No. 30 hole, push the drill with approximately 50 pounds of force. Use the maximum drill rpm as illustrated in Figure 4-166. A cutting fluid is not necessary when hand drilling. The following drilling procedures are recommended: Drill pilot holes in loose repair parts with power feed equipment before preassembling them. Preassemble the repair parts and drill the pilot holes in the mating structure. Enlarge the pilot holes to their completed hole dimension. When drilling Inconel®, autofeed-type drilling equipment is preferred. Working Magnesium Warning: Keep magnesium particles away from sources of ignition. Small particles of magnesium burn very easily. In sufficient concentration, these small particles can cause an explosion. If water touches molten magnesium, a steam explosion could occur. Extinguish magnesium fires with dry talc, calcium carbonate, sand, or graphite. Apply the powder on the burning metal to a depth of 1⁄2-inch or more. Do not use foam, water, carbon tetrachloride, or carbon dioxide. Magnesium alloys must not touch methyl alcohol. Magnesium is the world’s lightest structural metal. Like many other metals, this silvery-white element is not used in its pure state for stressed application. Instead, magnesium is alloyed with certain other metals (aluminum, zinc, zirconium, manganese, thorium, and rare earth metals) to obtain the strong, lightweight alloys needed for structural uses. When alloyed with these other metals, magnesium, yields alloys with excellent properties and high strength- Drill Size Maximum RPM 80–30 500 29–U 300 3/8 150 Figure 4-166. Drill size and speed for drilling Inconel®. 4-82 to-weight ratios. Proper combination of these alloying constituents provide alloys suitable for sand, permanent mold and die castings, forging, extrusions, rolled sheet, and plate with good properties at room temperature, as well as at elevated temperatures. Lightweight is the best known characteristic of magnesium, an important factor in aircraft design. In comparison, aluminum weighs one and one half times more, iron and steel weigh four times more, and copper and nickel alloys weigh five times more. Magnesium alloys can be cut, drilled, and reamed with the same tools that are used on steel or brass, but the cutting edges of the tool must be sharp. Type B rivets (5056-F aluminum alloy) are used when riveting magnesium alloy parts. Magnesium parts are often repaired with clad 2024-T3 aluminum alloy. While magnesium alloys can usually be fabricated by methods similar to those used on other metals, remember that many of the details of shop practice cannot be applied. Magnesium alloys are difficult to fabricate at room temperature; therefore, most operations must be performed at high temperatures. This requires preheating of the metal or dies, or both. Magnesium alloy sheets may be cut by blade shears, blanking dies, routers, or saws. Hand or circular saws are usually used for cutting extrusions to length. Conventional shears and nibblers should never be used for cutting magnesium alloy sheet because they produce a rough, cracked edge. Shearing and blanking of magnesium alloys require close tool tolerances. A maximum clearance of 3 to 5 percent of the sheet thickness is recommended. The top blade of the shears should be ground with an included angle of 45° to 60º. The shear angle on a punch should be from 2° to 3°, with a 1° clearance angle on the die. For blanking, the shear angle on the die should be from 2° to 3° with a 1° clearance angle on the punch. Hold-down pressures should be used when possible. Cold shearing should not be accomplished on a hard-rolled sheet thicker than 0.064-inch or annealed sheet thicker than 1⁄8-inch. Shaving is used to smooth the rough, flaky edges of a magnesium sheet that has been sheared. This operation consists of removing approximately 1⁄32-inch by a second shearing. Hot shearing is sometimes used to obtain an improved sheared edge. This is necessary for heavy sheet and plate stock. Annealed sheet may be heated to 600 °F, but hardrolled sheet must be held under 400 °F, depending on the alloy used. Thermal expansion makes it necessary to allow for shrinkage after cooling, which entails adding a small amount of material to the cold metal dimensions before fabrication. Sawing is the only method used in cutting plate stock more than 1⁄2-inch thick. Bandsaw raker-set blades of 4- to 6-tooth pitch are recommended for cutting plate stock or heavy extrusions. Small and medium extrusions are more easily cut on a circular cutoff saw having six teeth per inch. Sheet stock can be cut on handsaws having raker-set or straight-set teeth with an 8-tooth pitch. Bandsaws should be equipped with nonsparking blade guides to eliminate the danger of sparks igniting the magnesium alloy filings. Cold working most magnesium alloys at room temperature is very limited, because they work harden rapidly and do not lend themselves to any severe cold forming. Some simple bending operations may be performed on sheet material, but the radius of bend must be at least 7 times the thickness of the sheet for soft material and 12 times the thickness of the sheet for hard material. A radius of 2 or 3 times the thickness of the sheet can be used if the material is heated for the forming operation. Since wrought magnesium alloys tend to crack after they are cold-worked, the best results are obtained if the metal is heated to 450 °F before any forming operations are attempted. Parts formed at the lower temperature range are stronger because the higher temperature range has an annealing effect on the metal. The disadvantages of hot working magnesium are: 1. Heating the dies and the material is expensive and troublesome. 2. There are problems in lubricating and handling materials at these temperatures. The advantages to hot working magnesium are: 1. It is more easily formed when hot than are other metals. 2. Spring-back is reduced, resulting in greater dimensional accuracy. When heating magnesium and its alloys, watch the temperature carefully as the metal is easily burned. Overheating also causes small molten pools to form within the metal. In either case, the metal is ruined. To prevent burning, magnesium must be protected with a sulfur dioxide atmosphere while being heated. Proper bending around a short radius requires the removal of sharp corners and burrs near the bend line. Layouts should be made with a carpenter’s soft pencil because any marring of the surface may result in fatigue cracks. Press brakes can be used for making bends with short radii. Die and rubber methods should be used where bends are 4-83 to be made at right angles, which complicate the use of a brake. Roll forming may be accomplished cold on equipment designed for forming aluminum. The most common method of forming and shallow drawing of magnesium is to use a rubber pad as the female die. This rubber pad is held in an inverted steel pan that is lowered by a hydraulic press ram. The press exerts pressure on the metal and bends it to the shape of the male die. Monel® rivets or standard close-tolerance steel fasteners should be used when installing titanium parts. The alloy sheet can be formed, to a limited extent, at room temperature. The forming of titanium alloys is divided into three classes: The machining characteristics of magnesium alloys are excellent, making possible the use of maximum speeds of the machine tools with heavy cuts and high feed rates. Power requirements for machining magnesium alloys are about one-sixth of those for mild steel. Over 5 percent of all titanium in the United States is produced in the form of the alloy Ti 6Al-4V, which is known as the workhorse of the titanium industry. Used in aircraft turbine engine components and aircraft structural components, Ti 6Al-4V is approximately 3 times stronger than pure titanium. The most widely used titanium alloy, it is hard to form. Filings, shavings, and chips from machining operations should be kept in covered metal containers because of the danger of combustion. Do not use magnesium alloys in liquid deicing and water injection systems or in the integral fuel tank areas. Working Titanium Keep titanium particles away from sources of ignition. Small particles of titanium burn very easily. In sufficient concentration, these small particles can cause an explosion. If water touches molten titanium, a steam explosion could occur. Extinguish titanium fires with dry talc, calcium carbonate, sand, or graphite. Apply the powder on the burning metal to a depth of 1⁄2-inch or more. Do not use foam, water, carbon tetrachloride, or carbon dioxide. Cold forming with no stress relief Cold forming with stress relief Elevated temperature forming (built-in stress relief) The following are procedures for cold forming titanium 6Al4V annealed with stress relief (room temperature forming): 1. It is important to use a minimum radius chart when forming titanium because an excessively small radius introduces excess stress to the bend area. 2. Stress relieves the part as follows: heat the part to a temperature above 1,250 °F (677 °C), but below 1,450 °F (788 °C). Keep the part at this temperature for more than 30 minutes but less than 10 hours. 3. A powerful press brake is required to form titanium parts. Regular hand-operated box and pan brakes cannot form titanium sheet material. 4. A power slip roller is often used if the repair patch needs to be curved to fit the contour of the aircraft. Description of Titanium Titanium in its mineral state, is the fourth most abundant structural metal in the earth’s crust. It is lightweight, nonmagnetic, strong, corrosion resistant, and ductile. Titanium lies between the aluminum alloys and stainless steel in modulus, density, and strength at intermediate temperatures. Titanium is 30 percent stronger than steel, but is nearly 50 percent lighter. It is 60 percent heavier than aluminum, but twice as strong. Titanium and its alloys are used chiefly for parts that require good corrosion resistance, moderate strength up to 600 °F (315 °C), and lightweight. Commercially pure titanium sheet may be formed by hydropress, stretch press, brake roll forming, drop hammer, or other similar operations. It is more difficult to form than annealed stainless steel. Titanium can also be worked by grinding, drilling, sawing, and the types of working used on other metals. Titanium must be isolated from magnesium, aluminum, or alloy steel because galvanic corrosion or oxidation of the other metals occurs upon contact. Titanium can be difficult to drill, but standard high-speed drill bits may be used if the bits are sharp, if sufficient force is applied, and if a low-speed drill motor is used. If the drill bit is dull, or if it is allowed to ride in a partially drilled hole, an overheated condition is created, making further drilling extremely difficult. Therefore, keep holes as shallow as possible; use short, sharp drill bits of approved design; and flood the area with large amounts of cutting fluid to facilitate drilling or reaming. When working titanium, it is recommended that you use carbide or 8 percent cobalt drill bits, reamers, and countersinks. Ensure the drill or reamer is rotating to prevent scoring the side of the hole when removing either of them from a hole. Use a hand drill only when positive-power-feed drills are not available. The following guidelines are used for drilling titanium: The largest diameter hole that can be drilled in a single step is 0.1563-inch because a large force is required. 4-84 Larger diameter drill bits do not cut satisfactorily when much force is used. Drill bits that do not cut satisfactorily cause damage to the hole. Holes with a diameter of 0.1875-inch and larger can be hand drilled if the operator: - Starts with a hole with a diameter of 0.1563-inch. - Increases the diameter of the hole in 0.0313-inch or 0.0625-inch increments. Cobalt vanadium drill bits last much longer than HSS bits. The recommended drill motor rpm settings for hand drilling titanium are listed in Figure 4-167. The life of a drill bit is shorter when drilling titanium than when drilling steel. Do not use a blunt drill bit or let a drill bit rub the surface of the metal and not cut it. If one of these conditions occurs, the titanium surface becomes work hardened, and it is very difficult to start the drill again. When hand drilling two or more titanium parts at the same time, clamp them together tightly. To clamp them together, use temporary bolts, Cleco clamps, or tooling clamps. Put the clamps around the area to drill and as near the area as possible. When hand drilling thin or flexible parts, put a support (such as a block of wood) behind the part. Titanium has a low thermal conductivity. When it becomes hot, other metals become easily attached to it. Particles of titanium often become welded to the sharp edges of the drill bit if the drill speed is too high. When drilling large plates or extrusions, use a water soluble coolant or sulphurized oil. Note: The intimate metal-to-metal contact in the metal working process creates heat and friction that must be reduced or the tools and the sheet metal used in the process are quickly damaged and/or destroyed. Coolants, also called cutting fluids, are used to reduce the friction at the interface of the tool and sheet metal by transferring heat away from the tool and sheet metal. Thus, the use of cutting fluids increases productivity, extends tool life, and results in a higher quality of workmanship. Hole Size (inches) Drill Speed (rpm) 0.0625 920 to 1830 rpm 0.125 460 to 920 rpm 0.1875 230 to 460 rpm Figure 4-167. Hole size and drill speed for drilling titanium. Basic Principles of Sheet Metal Repair Aircraft structural members are designed to perform a specific function or to serve a definite purpose. The primary objective of aircraft repair is to restore damaged parts to their original condition. Very often, replacement is the only way this can be done effectively. When repair of a damaged part is possible, first study the part carefully to fully understand its purpose or function. Strength may be the principal requirement in the repair of certain structures, while others may need entirely different qualities. For example, fuel tanks and floats must be protected against leakage; cowlings, fairings, and similar parts must have such properties as neat appearance, streamlined shape, and accessibility. The function of any damaged part must be carefully determined to ensure the repair meets the requirements. An inspection of the damage and accurate estimate of the type of repair required are the most important steps in repairing structural damage. The inspection includes an estimate of the best type and shape of repair patch to use; the type, size, and number of rivets needed; and the strength, thickness, and kind of material required to make the repaired member no heavier (or only slightly heavier) and just as strong as the original. When investigating damage to an aircraft, it is necessary to make an extensive inspection of the structure. When any component or group of components has been damaged, it is essential that both the damaged members and the attaching structure be investigated, since the damaging force may have been transmitted over a large area, sometimes quite remote from the point of original damage. Wrinkled skin, elongated or damaged bolt or rivet holes, or distortion of members usually appears in the immediate area of such damage, and any one of these conditions calls for a close inspection of the adjacent area. Check all skin, dents, and wrinkles for any cracks or abrasions. Nondestructive inspection methods (NDI) are used as required when inspecting damage. NDI methods serve as tools of prevention that allow defects to be detected before they develop into serious or hazardous failures. A trained and experienced technician can detect flaws or defects with a high degree of accuracy and reliability. Some of the defects found by NDI include corrosion, pitting, heat/stress cracks, and discontinuity of metals. When investigating damage, proceed as follows: Remove all dirt, grease, and paint from the damaged and surrounding areas to determine the exact condition of each rivet, bolt, and weld. 4-85 Inspect skin for wrinkles throughout a large area. Check the operation of all movable parts in the area. Determine if repair would be the best procedure. In any aircraft sheet metal repair, it is critical to: Maintain original strength, Maintain original contour, and Minimize weight. Maintaining Original Strength Certain fundamental rules must be observed if the original strength of the structure is to be maintained. Ensure that the cross-sectional area of a splice or patch is at least equal to or greater than that of the damaged part. Avoid abrupt changes in cross-sectional area. Eliminate dangerous stress concentration by tapering splices. To reduce the possibility of cracks starting from the corners of cutouts, try to make cutouts either circular or oval in shape. Where it is necessary to use a rectangular cutout, make the radius of curvature at each corner no smaller than 1⁄2-inch. If the member is subjected to compression or bending loads, the patch should be placed on the outside of the member to obtain a higher resistance to such loads. If the patch cannot be placed there, material one gauge thicker than the original shall be used for the repair. Replace buckled or bent members or reinforce them by attaching a splice over the affected area. A buckled part of the structure shall not be depended upon to carry its load again, no matter how well the part may be strengthened. The material used in all replacements or reinforcements must be similar to that used in the original structure. If an alloy weaker than the original must be substituted for it, a heavier thickness must be used to give equivalent cross-sectional strength. A material that is stronger, but thinner, cannot be substituted for the original because one material can have greater tensile strength but less compressive strength than another, or vice versa. Also, the buckling and torsional strength of many sheet metal and tubular parts depends primarily on the thickness of the material rather than its allowable compressive and shear strengths. The manufacturer’s SRM often indicates what material can be used as a substitution and how much thicker the material needs to be. Figure 4-168 is an example of a substitution table found in an SRM. Care must be taken when forming. Heat-treated and coldworked aluminum alloys stand very little bending without cracking. On the other hand, soft alloys are easily formed, but they are not strong enough for primary structure. Strong alloys can be formed in their annealed (heated and allowed to cool slowly) condition, and heat treated before assembling to develop their strength. The size of rivets for any repair can be determined by referring to the rivets used by the manufacturer in the next parallel rivet row inboard on the wing or forward on the fuselage. Another method of determining the size of rivets to be used is to multiply the thickness of the skin by three and use the next larger size rivet corresponding to that figure. For example, if the skin thickness is 0.040-inch, multiply 0.040inch by 3, which equals 0.120-inch; use the next larger size rivet, 1⁄8-inch (0.125-inch). The number of rivets to be used for a repair can be found in tables in manufacturer’s SRMs or in Advisory Circular (AC) 43.13-1 (as revised), Acceptable Methods, Techniques, and Practices—Aircraft Inspection and Repair. Figure 4-169 is a table from AC 43.13-1 that is used to calculate the number of rivets required for a repair. Extensive repairs that are made too strong can be as undesirable as repairs weaker than the original structure. All aircraft structure must flex slightly to withstand the forces imposed during takeoff, flight, and landing. If a repaired area is too strong, excessive flexing occurs at the edge of the completed repair, causing acceleration of metal fatigue. Shear Strength & Bearing Strength Aircraft structural joint design involves an attempt to find the optimum strength relationship between being critical in shear and critical in bearing. These are determined by the failure mode affecting the joint. The joint is critical in shear if less than the optimum number of fasteners of a given size are installed. This means that the rivets will fail, and not the sheet, if the joint fails. The joint is critical in bearing if more than the optimum number of fasteners of a given size are installed; the material may crack and tear between holes, or fastener holes may distort and stretch while the fasteners remain intact. Maintaining Original Contour Form all repairs in such a manner to fit the original contour perfectly. A smooth contour is especially desirable when making patches on the smooth external skin of high-speed aircraft. Keeping Weight to a Minimum Keep the weight of all repairs to a minimum. Make the size of the patches as small as practicable and use no more rivets than are necessary. In many cases, repairs disturb the original balance of the structure. The addition of excessive weight in each repair may unbalance the aircraft, requiring adjustment of the trim-and-balance tabs. In areas such as the spinner on the propeller, a repair requires application of balancing patches in order to maintain a perfect balance of the propeller. 4-86 Shape Replacement Material Initial Material Sheet 0.016 to 0.125 Clad 2024–T42 F Clad 2024–T3 2024–T3 Clad 7075–T6 A 7075–T6 A Clad 2024–T3 2024–T3 Clad 7075–T6 A 7075–T6 A Clad 7075–T6 Formed or Extruded Section 7075–T6 2024–T42 F 7075–T6 A B Material Replacement Factor Sheet Material to be Replaced Clad 7075–T6 7075–T6 C C H Clad 2024–T3 2024–T3 F 2024–T4 2024–T42 F Clad 2024–T4 Clad 2024–T42 D E D E D E D E 7075–T6 1.00 1.10 1.20 1.78 1.30 1.83 1.20 1.78 1.24 1.84 Clad 7075–T6 1.00 1.00 1.13 1.70 1.22 1.76 1.13 1.71 1.16 1.76 2024–T3 1.00 A 1.00 A 1.00 1.00 1.09 1.10 1.00 1.10 1.03 1.14 Clad 2024–T3 1.00 A 1.00 A 1.00 1.00 1.00 1.00 1.00 1.00 1.03 1.00 2024–T42 1.00 A 1.00 A 1.00 1.00 1.00 1.00 1.00 1.00 1.00 1.14 Clad 2024–T42 1.00 A 1.00 A 1.00 1.00 1.00 1.00 1.00 1.00 1.00 1.00 7178–T6 1.28 1.28 1.50 1.90 1.63 2.00 1.86 1.90 1.96 1.98 Clad 7178–T6 1.08 1.18 1.41 1.75 1.52 1.83 1.75 1.75 1.81 1.81 1.00 A 1.00 1.00 1.00 1.00 1.00 1.00 1.00 1.00 5052–H34 G H 1.00 A Notes All dimensions are in inches, unless given differently. A These materials cannot be used as replacements for the initial material in areas that are pressured. B They also cannot be used in the wing interspar structure at the wing center section structure. It is possible for the material replacement factor to be a lower value for a specific location on the airplane. To get that value, contact Boeing for a case by case analysis. C Use the next thicker standard gage when you use a formed section as a replacement for an extrusion. D For all gages of flat sheet and formed sections. Refer to Figure 3 for minimun bend radii. E For flat sheet less than 0.071 thick. Example: To refer 0.040 thick 7075–T6 with Clad 7075–T6, multiply the gage by the material replacement factor to get the replacement gage 0. 040 x 1.10 = 0.045. F For flat sheet 0.071 thick and thicker, and for formed sections. G 2024–T4 and 2024–T42 are equivalent. H A compound to give protection from corrosion must be applied to bare material that is used to replace 5052–H34. It is possible that more protection from corrosion will be necessary when bare mineral is used to replace Clad material. Refer to 51-10-2. Figure 4-168. Material substitution. When flight controls are repaired and weight is added, it is very important to perform a balancing check to determine if the flight control is still within its balance limitations. Failure to do so could result in flight control flutter. Flutter & Vibration Precautions To prevent severe vibration or flutter of flight control surfaces during flight, precautions must be taken to stay within the design balance limitations when performing maintenance or repair. The importance of retaining the proper balance and rigidity of aircraft control surfaces cannot be overemphasized. 4-87 No. of 2117–T4 (AD) protruding head rivets required per inch of width “W” Thickness “t” in inches No. of Bolts Rivet size 3/32 1/8 5/32 3/16 1/4 4.9 -- -- -- AN–3 --.016 6.5.020 6.5 4.9 3.9 -- -- --.025 6.9 4.9 3.9 -- -- --.032 8.9 4.9 3.9 3.3 -- --.036 10.0 5.6 3.9 3.3 2.4 --.040 11.1 6.2 4.0 3.3 2.4 --.051 -- 7.9 5.1 3.6 2.4 3.3.064 -- 9.9 6.5 4.5 2.5 3.3.081 -- 12.5 8.1 5.7 3.1 3.3.091 -- -- 9.1 6.3 3.5 3.3.102 -- -- 10.3 7.1 3.9 3.3.128 -- -- 12.9 8.9 4.9 3.3 Notes a. For stringer in the upper surface of a wing, or in a fuselage, 80 percent of the number of rivets shown in the table may be used. b. For intermediate frames, 60 percent of the number shown may be used. c. For single lap sheet joints, 75 percent of the number shown may be used. Engineering Notes a. The load per inch of width of material was calculated by assuming a strip 1 inch wide in tension. b. Number of rivets required was calculated for 2117–T4 (AD) rivets, based on a rivet allowable shear stress equal to percent of the sheet allowable tensile stress, and a sheet allowable bearing stress equal to 160 percent of the sheet allowable tensile stress, using nominal hole diameters for rivets. c. Combinations of shoot thickness and rivet size above the underlined numbers are critical in (i.e., will fail by) bearing on the sheet; those below are critical in shearing of the rivets. d. The number of AN–3 bolts required below the underlined number was calculated based on a sheet allowable tensile stress of 55.000 psi and a bolt allowable single shear load of 2.126 pounds. Figure 4-169. Rivet calculation table. The effect of repair or weight change on the balance and CG is proportionately greater on lighter surfaces than on the older heavier designs. As a general rule, repair the control surface in such a manner that the weight distribution is not affected in any way, in order to preclude the occurrence of flutter of the control surface in flight. Under certain conditions, counterbalance weight is added forward of the hinge line to maintain balance. Add or remove balance weights only when necessary in accordance with the manufacturer’s instructions. Flight testing must be accomplished to ensure flutter is not a problem. Failure to check and retain control surface balance within the original or maximum allowable value could result in a serious flight hazard. Aircraft manufacturers use different repair techniques and repairs designed and approved for one type of aircraft are not automatically approved for other types of aircraft. When repairing a damaged component or part, consult the applicable section of the manufacturer’s SRM for the aircraft. Usually the SRM contains an illustration for a similar repair along with a list of the types of material, rivets and rivet spacing, and the methods and procedures to be used. Any additional knowledge needed to make a repair is also detailed. If the necessary information is not found in the SRM, attempt to find a similar repair or assembly installed by the manufacturer of the aircraft. Inspection of Damage When visually inspecting damage, remember that there may be other kinds of damage than that caused by impact from foreign objects or collision. A rough landing may overload one of the landing gear, causing it to become sprung; this would be classified as load damage. During inspection and sizing up of the repair job, consider how far the damage caused by the sprung shock strut extends to supporting structural members. A shock occurring at one end of a member is transmitted throughout its length; therefore, closely inspect all rivets, 4-88 bolts, and attaching structures along the complete member for any evidence of damage. Make a close examination for rivets that have partially failed and for holes that have been elongated. Whether specific damage is suspected or not, an aircraft structure must occasionally be inspected for structural integrity. The following paragraphs provide general guidelines for this inspection. When inspecting the structure of an aircraft, it is very important to watch for evidence of corrosion on the inside. This is most likely to occur in pockets and corners where moisture and salt spray may accumulate; therefore, drain holes must always be kept clean. While an injury to the skin covering caused by impact with an object is plainly evident, a defect, such as distortion or failure of the substructure, may not be apparent until some evidence develops on the surface, such as canted, buckled or wrinkled covering, and loose rivets or working rivets. A working rivet is one that has movement under structural stress, but has not loosened to the extent that movement can be observed. This situation can sometimes be noted by a dark, greasy residue or deterioration of paint and primers around rivet heads. External indications of internal injury must be watched for and correctly interpreted. When found, an investigation of the substructure in the vicinity should be made and corrective action taken. Warped wings are usually indicated by the presence of parallel skin wrinkles running diagonally across the wings and extending over a major area. This condition may develop from unusually violent maneuvers, extremely rough air, or extra hard landings. While there may be no actual rupture of any part of the structure, it may be distorted and weakened. Similar failures may also occur in fuselages. Small cracks in the skin covering may be caused by vibration and they are frequently found leading away from rivets. Aluminum alloy surfaces having chipped protective coating, scratches, or worn spots that expose the surface of the metal should be recoated at once, as corrosion may develop rapidly. The same principle is applied to aluminum clad (Alclad™) surfaces. Scratches, which penetrate the pure aluminum surface layer, permit corrosion to take place in the alloy beneath. A simple visual inspection cannot accurately determine if suspected cracks in major structural members actually exist or the full extent of the visible cracks. Eddy current and ultrasonic inspection techniques are used to find hidden damage. Types of Damage & Defects Types of damage and defects that may be observed on aircraft parts are defined as follows: Brinelling—occurrence of shallow, spherical depressions in a surface, usually produced by a part having a small radius in contact with the surface under high load. Burnishing—polishing of one surface by sliding contact with a smooth, harder surface. Usually there is no displacement or removal of metal. Burr—a small, thin section of metal extending beyond a regular surface, usually located at a corner or on the edge of a hole. Corrosion—loss of metal from the surface by chemical or electrochemical action. The corrosion products generally are easily removed by mechanical means. Iron rust is an example of corrosion. Crack—a physical separation of two adjacent portions of metal, evidenced by a fine or thin line across the surface caused by excessive stress at that point. It may extend inward from the surface from a few thousandths of an inch to completely through the section thickness. Cut—loss of metal, usually to an appreciable depth over a relatively long and narrow area, by mechanical means, as would occur with the use of a saw blade, chisel, or sharp-edged stone striking a glancing blow. Dent—indentation in a metal surface produced by an object striking with force. The surface surrounding the indentation is usually slightly upset. Erosion—loss of metal from the surface by mechanical action of foreign objects, such as grit or fine sand. The eroded area is rough and may be lined in the direction in which the foreign material moved relative to the surface. Chattering—breakdown or deterioration of metal surface by vibratory or chattering action. Although chattering may give the general appearance of metal loss or surface cracking, usually, neither has occurred. Galling—breakdown (or build-up) of metal surfaces due to excessive friction between two parts having relative motion. Particles of the softer metal are torn loose and welded to the harder metal. Gouge—groove in, or breakdown of, a metal surface from contact with foreign material under heavy pressure. Usually it indicates metal loss but may be largely the displacement of material. Inclusion—presence of foreign or extraneous material wholly within a portion of metal. Such material is 4-89 introduced during the manufacture of rod, bar or tubing by rolling or forging. Nick—local break or notch on an edge. Usually it involves the displacement of metal rather than loss. Pitting—sharp, localized breakdown (small, deep cavity) of metal surface, usually with defined edges. Scratch—slight tear or break in metal surface from light, momentary contact by foreign material. Score—deeper (than scratch) tear or break in metal surface from contact under pressure. May show discoloration from temperature produced by friction. Stain—a change in color, locally causing a noticeably different appearance from the surrounding area. Upsetting—a displacement of material beyond the normal contour or surface (a local bulge or bump). Usually it indicates no metal loss. Classification of Damage Damages may be grouped into four general classes. In many cases, the availabilities of repair materials and time are the most important factors in determining if a part should be repaired or replaced. Negligible Damage Negligible damage consists of visually apparent, surface damage that do not affect the structural integrity of the component involved. Negligible damage may be left as is or may be corrected by a simple procedure without restricting flight. In both cases, some corrective action must be taken to keep the damage from spreading. Negligible or minor damage areas must be inspected frequently to ensure the damage does not spread. Permissible limits for negligible damage vary for different components of different aircraft and should be carefully researched on an individual basis. Failure to ensure that damages within the specified limit of negligible damage may result in insufficient structural strength of the affected support member for critical flight conditions. Small dents, scratches, cracks, and holes that can be repaired by smoothing, sanding, stop drilling, or hammering out, or otherwise repaired without the use of additional materials, fall in this classification. [Figure 4-170] the damaged part, but one gauge heavier. In a patch repair, filler plates of the same gauge and type of material as that in the damaged component may be used for bearing purposes or to return the damaged part to its original contour. Structural fasteners are applied to members and the surrounding structure to restore the original load-carrying characteristics of the damaged area. The use of patching depends on the extent of the damage and the accessibility of the component to be repaired. Damage Repairable by Insertion Damage must be repaired by insertion when the area is too large to be patched or the structure is arranged such that repair members would interfere with structural alignment (e.g., in a hinge or bulkhead). In this type of repair, the damaged portion is removed from the structure and replaced by a member identical in material and shape. Splice connections at each end of the insertion member provide for load transfer to the original structure. Damage Necessitating Replacement of Parts Components must be replaced when their location or extent of damage makes repair impractical, when replacement is more economical than repair, or when the damaged part is relatively easy to replace. For example, replacing damaged castings, forgings, hinges, and small structural members, when available, is more practical than repairing them. Some highly stressed members must be replaced because repair would not restore an adequate margin of safety. Repairability of Sheet Metal Structure The following criteria can be used to help an aircraft technician decide upon the repairability of a sheet metal structure: Type of damage. Crack Stop-drill cracks Damage Repairable by Patching Damage repairable by patching is any damage exceeding negligible damage limits that can be repaired by installing splice members to bridge the damaged portion of a structural part. The splice members are designed to span the damaged areas and to overlap the existing undamaged surrounding structure. The splice or patch material used in internal riveted and bolted repairs is normally the same type of material as Figure 4-170. Repair of cracks by stop-drilling. 4-90 Tools and equipment available to make the repair. The following methods, procedures, and materials are only typical and should not be used as the authority for a repair. Structural Support During Repair During repair, the aircraft must be adequately supported to prevent further distortion or damage. It is also important that the structure adjacent to the repair is supported when it is subject to static loads. The aircraft structure can be supported adequately by the landing gear or by jacks where the work involves a repair, such as removing the control surfaces, wing panels, or stabilizers. Cradles must be prepared to hold these components while they are removed from the aircraft. When the work involves extensive repair of the fuselage, landing gear, or wing center section, a jig (a device for holding parts in position to maintain their shape) may be constructed to distribute the loads while repairs are being accomplished. Figure 4-171 shows a typical aircraft jig. Always check the applicable aircraft maintenance manual for specific support requirements. Assessment of Damage Before starting any repair, the extent of damage must be fully evaluated to determine if repair is authorized or even practical. This evaluation should identify the original material used and the type of repair required. The assessment of the damage begins with an inspection of riveted joints and an inspection for corrosion. Inspection of Riveted Joints Inspection consists of examining both the shop and manufactured heads and the surrounding skin and structural parts for deformities. During the repair of an aircraft structural part, examine adjacent parts to determine the condition of neighboring rivets. The presence of chipped or cracked paint around the heads may indicate shifted or loose rivets. If the heads are tipped or if rivets are loose, they show up in groups of several consecutive rivets and are probably tipped in the same direction. If heads that appear to be tipped are not in groups and are not tipped in the same direction, tipping may have occurred during some previous installation. Inspect rivets that are known to have been critically loaded, but that show no visible distortion, by drilling off the head and carefully punching out the shank. If upon examination, the CL 7 5/8 4 Type of repair required. 3 5/8 3 5/8 7 1/4 4 CL 16 3 5/8 6 7/8 2 22 4 Location of the damage. 3 9/16 3 5/16 3 2 1/8 6 1/4 5 5/8 4 3/4 5 5/8 2 1/8 4 24 Type of original material. 3/8 8 2 3/4 5 1/4 5 1/4 30 1/4 felt glued on Canvas or strong cloth tacked on to cover felt 2X8 1/4 plywood both sides 2X3 30 Figure 4-171. Aircraft jig used to hold components during repairs. shank appears joggled and the holes in the sheet misaligned, the rivet has failed in shear. In that case, determine what is causing the stress and take necessary corrective action. Countersunk rivets that show head slippage within the countersink or dimple, indicating either sheet bearing failure or rivet shear failure, must be replaced. Joggles in removed rivet shanks indicate partial shear failure. Replace these rivets with the next larger size. Also, if the rivet holes show elongation, replace the rivets with the next larger size. Sheet failures, such as tearouts, cracks between rivets, and the like, usually indicate damaged rivets, and the complete repair of the joint may require replacement of the rivets with the next larger size. The presence of a black residue around the rivets is not an indication of looseness, but it is an indication of movement (fretting). The residue, which is aluminum oxide, is formed by a small amount of relative motion between the rivet and the adjacent surface. This is called fretting corrosion, or smoking, because the aluminum dust quickly forms a dark, dirty looking trail, like a smoke trail. Sometimes, the thinning of the moving pieces can propagate a crack. If a rivet is 4-91 suspected of being defective, this residue may be removed with a general purpose abrasive hand pad, such as those manufactured by Scotch Brite™, and the surface inspected for signs of pitting or cracking. Although the condition indicates the component is under significant stress, it does not necessarily precipitate cracking. [Figure 4-172] Airframe cracking is not necessarily caused by defective rivets. It is common practice in the industry to size rivet patterns assuming one or more of the rivets is not effective. This means that a loose rivet would not necessarily overload adjacent rivets to the point of cracking. Rivet head cracking is acceptable under the following conditions: The depth of the crack is less than 1⁄8 of the shank diameter. The width of the crack is less than ⁄16 of the shank diameter. The length of the crack is confined to an area on the head within a circle having a maximum diameter of 11⁄4 times the shank diameter. Cracks should not intersect, which creates the potential for the loss of a portion of a head. 1 Inspection for Corrosion Corrosion is the gradual deterioration of metal due to a chemical or electrochemical reaction with its environment. The reaction can be triggered by the atmosphere, moisture, or other agents. When inspecting the structure of an aircraft, it is important to watch for evidence of corrosion on both the outside and inside. Corrosion on the inside is most likely to occur in pockets and corners where moisture and salt spray may accumulate; therefore, drain holes must always be kept clean. Also inspect the surrounding members for evidence of corrosion. Damage Removal To prepare a damaged area for repair: 1. Remove all distorted skin and structure in damaged area. Figure 4-172. Smoking rivet. 2. Remove damaged material so that the edges of the completed repair match existing structure and aircraft lines. 3. Round all square corners. 4. Smooth out any abrasions and/or dents. 5. Remove and incorporate into the new repair any previous repairs joining the area of the new repair. Repair Material Selection The repair material must duplicate the strength of the original structure. If an alloy weaker than the original material has to be used, a heavier gauge must be used to give equivalent cross-sectional strength. A lighter gauge material should not be used even when using a stronger alloy. Repair Parts Layout All new sections fabricated for repairing or replacing damaged parts in a given aircraft should be carefully laid out to the dimensions listed in the applicable aircraft manual before fitting the parts into the structure. Rivet Selection Normally, the rivet size and material should be the same as the original rivets in the part being repaired. If a rivet hole has been enlarged or deformed, the next larger size rivet must be used after reworking the hole. When this is done, the proper edge distance for the larger rivet must be maintained. Where access to the inside of the structure is impossible and blind rivets must be used in making the repair, always consult the applicable aircraft maintenance manual for the recommended type, size, spacing, and number of rivets needed to replace either the original installed rivets or those that are required for the type of repair being performed. Rivet Spacing & Edge Distance The rivet pattern for a repair must conform to instructions in the applicable aircraft manual. The existing rivet pattern is used whenever possible. Corrosion Treatment Prior to assembly of repair or replacement parts, make certain that all existing corrosion has been removed in the area and that the parts are properly insulated one from the other. Approval of Repair Once the need for an aircraft repair has been established, Title 14 of the Code of Federal Regulations (14 CFR) defines the approval process. 14 CFR part 43, section 43.13(a) states that each person performing maintenance, alteration, or preventive maintenance on an aircraft, engine, propeller, or appliance shall use the methods, techniques, and practices prescribed in 4-92 the current manufacturer’s maintenance manual or instructions for continued airworthiness prepared by its manufacturer, or other methods, techniques, or practices acceptable to the Administrator. AC 43.13-1 contains methods, techniques, and practices acceptable to the Administrator for the inspection and repair of nonpressurized areas of civil aircraft, only when there are no manufacturer repair or maintenance instructions. This data generally pertains to minor repairs. The repairs identified in this AC may only be used as a basis for FAA approval for major repairs. The repair data may also be used as approved data, and the AC chapter, page, and paragraph listed in block 8 of FAA Form 337 when: a. The user has determined that it is appropriate to the product being repaired; b. It is directly applicable to the repair being made; and c. It is not contrary to manufacturer’s data. Engineering support from the aircraft manufacturer is required for repair techniques and methods that are not described in the aircraft maintenance manual or SRM. FAA Form 337, Major Repair and Alteration, must be completed for repairs to the following parts of an airframe and repairs of the following types involving the strengthening, reinforcing, splicing, and manufacturing of primary structural members or their replacement, when replacement is by fabrication, such as riveting or welding. [Figure 4-173] covering exceeding six inches in any direction Repair of portions of skin sheets by making additional seams Splicing of thin sheets Repair of three or more adjacent wing or control surface ribs or the leading edge of wings and control surfaces between such adjacent ribs For major repairs made in accordance with a manual or specifications acceptable to the Administrator, a certificated repair station may use the customer’s work order upon which the repair is recorded in place of the FAA Form 337. Repair of Stressed Skin Structure In aircraft construction, stressed skin is a form of construction in which the external covering (skin) of an aircraft carries part or all of the main loads. Stressed skin is made from high strength rolled aluminum sheets. Stressed skin carries a large portion of the load imposed upon an aircraft structure. Various specific skin areas are classified as highly critical, semicritical, or noncritical. To determine specific repair requirements for these areas, refer to the applicable aircraft maintenance manual. Minor damage to the outside skin of the aircraft can be repaired by applying a patch to the inside of the damaged sheet. A filler plug must be installed in the hole made by the removal of the damaged skin area. It plugs the hole and forms a smooth outside surface necessary for aerodynamic smoothness of the aircraft. The size and shape of the patch is determined in general by the number of rivets required in the repair. If not otherwise specified, calculate the required number of rivets by using the rivet formula. Make the patch plate of the same material as the original skin and of the same thickness or of the next greater thickness. Box beams Monocoque or semimonocoque wings or control surfaces Wing stringers or chord members Spars Spar flanges Members of truss-type beams Patches Thin sheet webs of beams Skin patches may be classified as two types: Keel and chine members of boat hulls or floats Lap or scab patch Corrugated sheet compression members that act as flange material of wings or tail surfaces Flush patch Wing main ribs and compression members Wing or tail surface brace struts, fuselage longerons Members of the side truss, horizontal truss or bulkheads Main seat support braces and brackets Landing gear brace struts Repairs involving the substitution of material Repair of damaged areas in metal or plywood stressed Lap or Scab Patch The lap or scab type of patch is an external patch where the edges of the patch and the skin overlap each other. The overlapping portion of the patch is riveted to the skin. Lap patches may be used in most areas where aerodynamic smoothness is not important. Figure 4-174 shows a typical patch for a crack and or for a hole. When repairing cracks or small holes with a lap or scab patch, the damage must be cleaned and smoothed. In repairing cracks, a small hole must be drilled in each end and sharp 4-93 Federal Aviation Administration (As shown on registration certificate) 2. Owner 3. For FAA Use Only 4. Type 5. Unit Identification (As described in Item 1 above) 6. Conformity Statement 7. Approval for Return to Service Figure 4-173. FAA Form 337, Major Repair and Alteration (Airframe, Powerplant, Propeller, or Appliance). 4-94 8. Description of Work Accomplished Figure 4-173. FAA Form 337, Major Repair and Alteration (Airframe, Powerplant, Propeller, or Appliance) continued. 4-95 Original damage Stop holes—drill 3/32" diameter holes in each sharp corner or crack or break and clean up edges Rivet hole Edge distance 5° 45° Neutral axis T 1/2 T Skin Figure 4-175. Lap patch edge preparation. Reinforcement material—ALCLAD 2024-T3 same gauge or one gauge heavier Rivets—material thickness of 0.032 inch or less. Use 1/8 " rivets—material thickness greater than 0.032", use 5/32" rivets. Damage Space rivets aproximately 1" apart in staggered rows 1/2" apart. Doubler Maintain minimum edge distance of 1" when skin thickness is 0.032" or less and 1/8" when skin thickness is more than 0.032". Minimum edge distance using 1/8" rivets is 1/4" and using 5/32" rivets is 5/16". Damaged area cut to a smooth rectangle with corner radil Figure 4-174. Lap or scab patch (crack). bend of the crack before applying the patch. These holes relieve the stress at these points and prevent the crack from spreading. The patch must be large enough to install the required number of rivets. It may be cut circular, square, or rectangular. If it is cut square or rectangular, the corners are rounded to a radius no smaller than 1⁄4-inch. The edges must be chamfered to an angle of 45° for 1⁄2 the thickness of the material, and bent down 5° over the edge distance to seal the edges. This reduces the chance that the repair is affected by the airflow over it. These dimensions are shown in Figure 4-175. Flush Patch A flush patch is a filler patch that is flush to the skin when applied it is supported by and riveted to a reinforcement plate which is, in turn, riveted to the inside of the skin. Figure 4-176 shows a typical flush patch repair. The doubler is inserted through the opening and rotated until it slides in place under the skin. The filler must be of the same gauge and material as the original skin. The doubler should be of material one gauge heavier than the skin. Filler Doubler riveted in place Filler riveted in place Figure 4-176. Typical flush patch repair. 4-96 Usually, repairs to open skin can be made in the conventional manner using standard rivets, but in repairing closed skin, some type of special fastener must be used. The exact type to be used depends on the type of repair being made and the recommendations of the aircraft manufacturer. Design of a Patch for a Non-pressurized Area Damage to the aircraft skin in a non-pressurized area can be repaired by a flush patch if a smooth skin surface is required or by an external patch in noncritical areas. [Figure 4-177] The first step is to remove the damage. Cut the damage to a round, oval, or rectangular shape. Round all corners of a rectangular patch to a minimum radius of 0.5-inch. The minimum edge distance used is 2 times the diameter and the rivet spacing is typically between 4-6 times the diameter. The size of the doubler depends on the edge distance and rivet spacing. The doubler material is of the same material as the damaged skin, but of one thickness greater than the damaged skin. The size of the doubler depends on the edge distance and rivet spacing. The insert is made of the same material and thickness as the damaged skin. The size and type of rivets should be the same as rivets used for similar joints on the aircraft. The SRM indicates what size and type of rivets to use. E Insertion E Open & Closed Skin Area Repair The factors that determine the methods to be used in skin repair are accessibility to the damaged area and the instructions found in the aircraft maintenance manual. The skin on most areas of an aircraft is inaccessible for making the repair from the inside and is known as closed skin. Skin that is accessible from both sides is called open skin. Skin P Doubler Insertion Doubler Skin Insertion patch method Patch Skin Skin 1/4 inch deep dent Cover patch method Typical Repairs for Aircraft Structures This section describes typical repairs of the major structural parts of an airplane. When repairing a damaged component or part, consult the applicable section of the manufacturer’s SRM for the aircraft. Normally, a similar repair is illustrated, and the types of material, rivets, and rivet spacing and the methods and procedures to be used are listed. Any additional knowledge needed to make a repair is also detailed. If the necessary information is not found in the SRM, attempt to find a similar repair or assembly installed by the manufacturer of the aircraft. Figure 4-177. Repair patch for a non-pressurized area. Floats Corrugated Skin Repair To maintain the float in an airworthy condition, periodic and frequent inspections should be made because of the rapidity of corrosion on metal parts, particularly when the aircraft is operated in salt water. Inspection of floats and hulls involves examination for damage due to corrosion, collision with other objects, hard landings, and other conditions that may lead to failure. Note: Blind rivets should not be used on floats or amphibian hulls below the water line. Sheet-metal floats should be repaired using approved practices; however, the seams between sections of sheet metal should be waterproofed with suitable fabric and sealing compound. A float that has undergone hull repairs should be tested by filling it with water and allowing it to stand for at least 24 hours to see if any leaks develop. [Figure 4-178] Some of the flight controls of smaller general aviation aircraft have beads in their skin panels. The beads give some stiffness to the thin skin panels. The beads for the repair patch can be formed with a rotary former or press brake. [Figure 4-179] Replacement of a Panel Damage to metal aircraft skin that exceeds repairable limits 4-97 Extrusion angle stiffener Repair to step station Replace skin Splice in new portion Replace skin A Replace skeg Detail A Splice Station 5 Splice Shims Repairs to keelson Repair to step Figure 4-178. Float repair. 4-98 Patch 0.016" AlcladTM 2024-T4 0.25" edge distance 0.7 5˝ r spa ivet cin g 0.25" radius Cut out damaged area Skin Use MS20470AD4 or MS20600 self-plugging rivets or equivalent Figure 4-179. Beaded skin repair on corrugated surfaces. requires replacement of the entire panel. [Figure 4-180] A panel must also be replaced when there are too many previous repairs in a given section or area. In aircraft construction, a panel is any single sheet of metal covering. A panel section is the part of a panel between adjacent stringers and bulk heads. Where a section of skin is damaged to such an extent that it is impossible to install a standard skin repair, a special type of repair is necessary. The particular type of repair required depends on whether the damage is repairable outside the member, inside the member, or to the edges of the panel. Outside the Member For damage that, after being trimmed, has 81⁄2 rivet diameters or more of material, extend the patch to include the manufacturer’s row of rivets and add an extra row inside the members. Inside the Member For damage that, after being trimmed, has less than 81⁄2 manufacturer’s rivet diameters of material inside the members, use a patch that extends over the members and an extra row of rivets along the outside of the members. Edges of the Panel For damage that extends to the edge of a panel, use 4-99 Repair seam same as strongest parallel adjacent seam. Repair seam same as strongest parallel adjacent seam. Use original holes and add as needed. Additional Rivets 3/16" 5/32" Trimmed hole radiused corners 1/8" Figure 4-180. Replacement of an entire panel. only one row of rivets along the panel edge, unless the manufacturer used more than one row. The repair procedure for the other edges of the damage follows the previously explained methods. the original holes, locate and drill the remaining holes. Remove the burrs from the rivet holes and apply corrosion protective material to the contacting surfaces before riveting the patch into place. The procedures for making all three types of panel repairs are similar. Trim out the damaged portion to the allowances mentioned in the preceding paragraphs. For relief of stresses at the corners of the trim-out, round them to a minimum radius of ½-inch. Lay out the new rivet row with a transverse pitch of approximately five rivet diameters and stagger the rivets with those put in by the manufacturer. Cut the patch plate from material of the same thickness as the original or the next greater thickness, allowing an edge distance of 21⁄2 rivet diameters. At the corners, strike arcs having the radius equal to the edge distance. Repair of Lightening Holes Chamfer the edges of the patch plate for a 45° angle and form the plate to fit the contour of the original structure. Turn the edges downward slightly so that the edges fit closely. Place the patch plate in its correct position, drill one rivet hole, and temporarily fasten the plate in place with a fastener. Using a hole finder, locate the position of a second hole, drill it, and insert a second fastener. Then, from the back side and through As discussed earlier, lightening holes are cut in rib sections, fuselage frames, and other structural parts to reduce the weight of the part. The holes are flanged to make the web stiffer. Cracks can develop around flanged lightening holes, and these cracks need to be repaired with a repair plate. The damaged area (crack) needs to be stop drilled or the damage must be removed. The repair plate is made of the same material and thickness as the damaged part. Rivets are the same as in surrounding structure and the minimum edge distance is 2 times the diameter and spacing is between four to six times the diameter. Figure 4-181 illustrates a typical lightening hole repair. Repairs to a Pressurized Area The skin of aircraft that are pressurized during flight is highly stressed. The pressurization cycles apply loads to the skin, and the repairs to this type of structure requires more rivets 4-100