C4 - Operation & Production PDF
Document Details
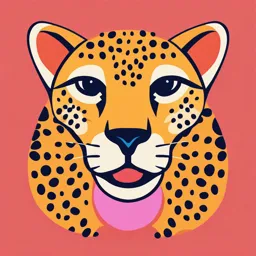
Uploaded by DefeatedAwe2648
UNITAR国际大学
Tags
Summary
This document explores the concepts of production and operations management. It discusses different types of operations, including manufacturing and service operations, and compares their characteristics. The document also covers topics such as mechanization, automation, computers and robotics in operations. Furthermore, it explains various approaches for system design and layout, location planning, and capacity planning for both manufacturing and service sectors.
Full Transcript
Chapter 4 Understanding Production/ Operations Productions and Operations Management...
Chapter 4 Understanding Production/ Operations Productions and Operations Management Production Process Effective production and operations management can lower a company's costs of production, boost the quality of its goods and services, allow it to respond dependably to customer demands, and enable it to grow while creating new value for customers by providing new products. Production the activities and processes used in making tangible products (converting raw materials and other inputs to finishing product) Operations the activities and processes used in making both tangible and intangible products Differences Between Manufacturing & Service Defining Operations Operations Service Operations: Manufacturing Service Operations Produce tangible and intangible does not deal directly with deal directly with customers customers produces intangibles services. produces tangible products quality is delivered instantly that can be stored to the consumer Goods Production: products’ quality may be Produces tangible inspected before the product products. reach the consumers. Differences Between Manufacturing & Service Operations Mechanization & Automation Mechanization Manufacturing Service Operations Refers to work done by machines or mechanical standardized variable / customized forces consistent varies: difficult to measure duration to complete a job is duration to complete a job standard varies Automation machine intensive labour intensive Extension of mechanization Totally replacing human labor with machines Mechanization & Automation Mechanization & Automation Advantages Suitable for repetitive work Quality is consistent Do not need motivational factors Higher productivity than human labor Human conflict can be avoided Disadvantages It is costly It causes unemployment It requires highly skilled personnel for maintenance Computers & Robotics Computers & Robotics Robots Programmable machines designed to perform a variety of tasks Controlled by computer systems Examples of tasks : Welding Assembly line production, Loading & unloading Computers & Robotics Scope of Operation Management Advantages: System Design System Operation Replace human labor for highly repetitive & dangerous jobs Planning Perform jobs with a high degree of accuracy Planning Aggregate Planning Capacity MRP Disadvantages: Layout Scheduling Company has to employ specialized engineers to maintain the robots Location Waiting Lines Some are designed for special purpose & cannot perform other tasks Design Management Product & Services Inventory Management Design & Selection Project Management Work System Design Quality Assurance Service Operations Differ Markedly From Manufacturing SERVICE Focus on: Performance Process and outcome Service characteristics Customer-service link Service quality considerations Operations Planning System Design: Capacity Planning Capacity is the upper limit or load that an Capacity operating unit can handle Example: Location Quality Operating Unit Capacity Factory 10,000 units per week Layout Process Lorry 45 kilometers per liter of petrol Product Methods Printer 100 pages per minute Cellular System Design: Capacity Planning System Design: Layout Planning Basic questions to be answered : What kind of capacity is needed? (output) Facility planning involves deciding the location for the work areas How much is needed? (quantity) When it is needed? Example, where should the following be located: Machines employee work stations Good capacity planning customer service areas The firm’s capacity matches the demand requirements or material storage area slightly exceeds the normal demand for its products Restrooms Administrative offices Computer rooms Layout of a Typical Piccadilly Cafeteria System Design: Layout Planning Three types of layout: Product layout Process layout Fixed position layout Figure 7–3 System Design: Product Layout Product Layout Used in continuous & repetitive process production. Resources being processed move through the same fixed sequence of steps to become finished goods. Equipment & people are set up to produce only one type of goods & are arranged according to the production requirement for that goods Often use assembly lines Examples Automobile plants, food processing plants Serving food at a cafeteria Product Layout System Design: Process Layout Equipment & people are grouped together according to their function Machines are usually arranged according to the type of process being performed. Example all machining in 1 department, all assembly in another department, all printing in another department Common in non manufacturing environments: hospitals, universities PROCESS LAYOUT Process Layout System Design: Fixed Position Layout It is a way of organizing production activities such that equipment & people are all assembled in one place Product to be made too big to be moved from one place to another Labor, materials & equipment are brought to the location where the work is done Example: Construction of ships, planes, homes, dams System Design: Fixed Position Layout Location Planning Layout Planning Planning work areas within an operations unit (factory) Should the assembly line be near the stock room or the administrative building? Location Planning Planning the location of an operations unit (factory) Should the factory be in Kulim or Nilai? System Design: Product & Service System Design: Location Planning Design and Selection In location planning, manager must take many factors into account, such as… Specifying the kind of materials that are to be purchased How close to the supply of raw materials & market Raw materials can only be purchased after specifications are made Availability of labor, energy & transportation costs in the in the product & service design nearby area Business environment change continuously, as company wants Local & state regulations & taxes to increase profit & market share, products & services are Community living conditions (climate) redesigned for improvement & competition Potential markets System Design: Product & Service Design and System Design: Selection Work System Design Organization conduct research & development (R&D) to improve the About designing maximum benefits for the satisfaction of product & service design workers for them to be productive Pressure for design changes can come from customers, competitors Job design and within organization Specify what tasks to be done Example Specify how best to get it done From Pentium III to Pentium IV Group tasks into a job that one person is responsible for From general shampoo to shampoo 3-in-1 What kinds of qualifications, skills and experience needed to From traditional retail shops to dot.com Internet companies do the job System Design: System Design: Work System Design Work System Design Benefits and Compensation Work measurement Ways of rewarding workers to keep them satisfied so that Determining how a particular work is to be evaluated they will work as hard as they can and be loyal to the How to tell if the work is well done or poorly done organization Example: Example Pack 150 boxes every day Annual increments and bonus Make at least 10 trips a day Allowances Write 180 lines of programming codes a day Medical benefits Commission Life insurance Paid holidays System Operation System Operation Planning: Material Planning: Aggregate Planning Requirement Planning (MRP) A computer-based information system that provides Aggregate plans or Production plans are based on forecasts (prediction, immediate information on detailed demand for raw materials calculated guesses) It is a broad level plan and determine overall annual manpower requirements, production rates, inventory levels Three components of MRP Use aggregate plans (year) as a guide to creating detail schedules (monthly, weekly, daily) 1. Master schedule Goal : To effectively utilize the organization’s resources to satisfy expected 2. Bill of materials file demand. Example: 3. Inventory record file How many cars to produce this year? How much raw materials to purchase for the entire year? System Operation Planning: Material Requirement Planning Operations Scheduling Material Requirement Planning Master schedule Scheduling Goods Operations states which products are to be produced, when it is needed, in what Scheduling Service Operations quantities they are needed Bill of materials file a listing of all the parts and raw materials that are needed to produce 1 unit of a finished product Inventory record file record information on the status of each type of raw material by time period such as gross requirements, scheduled receipts and expected amount on hand System Operation Planning: Scheduling System Operation Planning: Scheduling Specify the following on a daily basis: Quantity and type of items to be produced Gantt charts are used in scheduling to help manager How, when and where they should be produced visualize workloads Involves the following: Allocating equipment and workers to work centers Specifying a sequence for the work Develop work schedule Initiating work performance Updating the status of the work Revising the schedule Gantt Chart PERT Chart Figure 7–5 Figure 7–4 System Operation Management: System Operation Planning: Waiting Lines Inventory Management When the demand for a product or service is more than the Inventory is a storage: capacity to supply it, then we should create a waiting line of raw materials (waiting to be used) of finished products (waiting to be sold) Customers may have to stand in line, or take a number (and they will be served when their number is called) Goal: To avoid not having enough raw materials when Example: they are needed for production Waiting lines at supermarket checkouts To avoid not having enough products when Waiting lines at fast food restaurants, immigration office, banks demanded by customers System Operation Management: System Operation Management : Project Inventory Management Management Manager need to decide the level of inventory to be kept in Deals with large one-off set of activities warehouse. Once the project is completed the people involved will return to their respective departments or organizations If there is more inventory stocked than needed, lead to wastage of money Similar to a matrix organization Example: If there is too little inventory, lead to shortage for Building a shopping complex production or sale Organizing the Commonwealth Games Implementing a rescue mission for an earthquake disaster System Operation Management: Operations Control Monitors Results, Quality Assurance Which Ensures Performance Strategy for managing each part of an operation so that mistakes Materials Managers plan, organize, and control the flow of can be corrected quickly materials from design through distribution. Correcting mistakes after an operation is completed is more costly than if we correct it immediately Transportation Warehousing Purchasing Monitoring closely performance to detect any unplanned outcomes, Supplier Inventory and taking quick actions to correct them Selection Control Tools for Operations Process Control Total Quality Management Worker Training Always Delivering High Quality Planning for quality Just-in-time Production Systems (JIT) Organizing for quality Directing for quality Material Requirements Planning Controlling for quality Quality Control Tools for Total Quality Management Process Control Chart at Honey Nuggets Cereal Statistical Quality/Cost Process ISO 9000 Studies Control Getting Close Process to the Outsourcing Reengineering Customer Figure 7–6 THANK YOU