BUS 100 Fall 2024 Chapter 15 Operations_Mayne PDF
Document Details
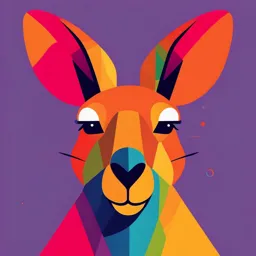
Uploaded by FabulousRhenium
2024
Peter Mayne
Tags
Summary
This document is a lecture presentation on operations management, focusing on concepts like managing operations, design planning, facilities planning, and supply chain management. It covers various aspects of operations from production to customer delivery, in the context of a business class. The presenter, Peter Mayne is referencing operations for manufacturing and service, and the business considerations involved.
Full Transcript
Managing Operations BUS 100-001(031) – Fall 2024 Class 23 – Thursday, November 28 Instructor: Peter Mayne Your cup of coffee has been a long, complicated journey… A carefully planned process is needed to turn ideas and raw materials into a finished product delivered to a custome...
Managing Operations BUS 100-001(031) – Fall 2024 Class 23 – Thursday, November 28 Instructor: Peter Mayne Your cup of coffee has been a long, complicated journey… A carefully planned process is needed to turn ideas and raw materials into a finished product delivered to a customer. Production turns inputs such as natural resources, raw materials, human resources, and capital into goods that can be sold to customers. Operations planning is equally important for companies that provide services. Our lineup for today’s class 1. Operations – all the steps required to take a product from idea to reality 2. Design planning 3. Facilities planning 4. Supply chain management 5. Operations schedules and quality management Planning the transformation process Once a company has an idea for a product, planning begins. The company considers the resources available and its own strategic goals to find the best production methods. Need to balance things like quality, speed to market, costs, sustainability goals, profit margins, etc. Requires close coordination with marketing, sales, finance, and other areas of the company. Manufacturing is a big part of the Canadian business scene Canadian manufacturers contribute: $174 billion toward Canada’s GDP 68% of Canadian exports Spin-off spending from suppliers and businesses that support the manufacturing sector Companies that produce services must carefully plan operations too Companies that provide services have a lot in common with companies who provide goods. They need to convert production inputs (human, material, financial, information) into a finished service. Production of services is different in some ways: Types of resources used (people are the most utilized resource) Inventory issues (services are typically consumed at the time of production) How quality is measured (customers judge the overall experience, not just the quality of a finished product) As discussed in Chapter 13, companies need to constantly innovate and bring new products to market to keep up with technology, consumer wants and needs, and competitors. They need a plan to create the product – there are 3 stages Bringing a new product or service to market Design Planning The development of a plan for converting an idea into an actual product What is design planning? Design planning is the development of a plan for converting an idea into an actual product. There are five major decisions in design planning. Develop Ensure Design a timelines: Evaluate Estimate sustainability product line: A continuous technology: Balance between capacity: process for high- : How much Meeting the needs a “long” product Trying to balance volume, low- automation and of the present, line that gives how much is variety products technology will be without consumers produced in a (low costs, simpler used versus compromising the options and a period so as not to scheduling) or an manual labor? future, e.g., “short” product waste resources intermittent Trade-off between optimizing the use line that is easier or turn away and process with high/low initial of fossil fuels, to produce. frustrate short, varied costs and eliminating waste, Marketing and customers, losing production runs. high/low recycling Operations need sales. Services are operating costs materials, and to work it out. usually intermittent recovering energy. Facilities planning Deciding where to locate a facility and choosing from three general types of facility layouts Facilities planning – where and how the product gets produced If possible, a business will make use of an existing facility, i.e., an existing factory to produce goods, or an existing location where a service is provided. The existing facility must have enough capacity and costs to refurbish it must be reasonable If building new, the company needs to consider these variables in picking a location: Proximity to major customers – reduce shipping costs and/or high contact with the customer is needed. Availability and cost of labour – volume of skilled labor and size of wages Costs of construction and operation – cost of land/rent, taxes, environmental regulations, availability of construction materials/labor and other costs that could affect profitability Access to key resources – close to transportation, natural resources, and/or major materials suppliers Facility layouts – three general types Separate stations for distinct tasks – equipment arranged in areas according to its function Products may move from station to station as needed. Proc Common for services, e.g., auto repair shop, restaurant, hospital but also some goods ess created in manufacturing plants that make lower volumes of specialized or custom products layo (job shops). ut Also known as an “assembly line”. The work flows from station to station. Prod All products undergo the same operation in the same sequence. uct For high-volume, standardized production runs, e.g., car factory. layo ut For producing very large products, e.g., aircraft or ships Fixed - The product remains stationary and people and machines are moved into place Positi Services like housecleaning or a hospital operating room also apply on layo ut Supply Chain Management Developing a strong supply chain, from production inputs all the way to the delivery of goods and services to customers. Supply chain management basics The goal of supply chain management is to create a fluid end-to-end system that reduces inefficiencies, costs, and redundancies while satisfying customers. Considerations: Building close relationship with suppliers and retailers Proximity of suppliers/retailers Quality and cost of inputs Contingency planning The increased focus on effective supply management has made it a lucrative profession Just enough materials, just in time In the past… Emerging best practices… Constant communication up and down the Companies had transaction-based relationships with raw materials supply chain suppliers Material Requirements Planning (MRP): computerized system that integrates We’re running out – time to place an production planning and inventory and order allows for just-in-time purchasing Delayed delivery could cause Enterprise Resource Planning (ERP): problems in serving the end includes quality stats, sales results, and customer in a timely manner more. Allows for Just-in-Time inventory supplyt As a work-around, companies would carry large amounts of raw Suppliers can monitor needs down the materials as inventory. Improved chain and adjust their production to meet delivery to customers but wasteful needs and costly Outcome: reduces production lags, minimizes inventory costs and keeps customers happy Quiz question To eliminate lengthy lead time required by raw materials suppliers, improve delivery times to retailers, and keep end-customers happy, a tablet manufacturing business typically holds vast amounts of raw materials, parts, and inventory. This costs money that could be better used within the business. As the business’s consultant, what would you recommend for top management? 1. Find less-costly suppliers that are located closer to the business 2. Consider implementing ERP and a JIT inventory system 3. Offer rebates to end customers, which would increase sales to retailers 4. Consider using less-costly sources of funding The importance of scheduling Operations managers are responsible for ensuring that machines, materials, and people are scheduled to be in the right place at the right time so that production can run smoothly without costly delays and that materials from the supply chain can be ordered just in time Schedulers must pay close attention to “critical path” tasks – those that take the longest from start to finish and could delay the whole project Quality control Successful businesses recognize that quality and productivity must go together Why quality control? Quality control involves creating quality standards, creating goods and services that meet them, and measuring finished goods and services against them. Companies make choices around how to balance costs and quality, i.e., offering lower prices for goods of reasonable (but not high) quality. Why quality control matters: Poor quality causes customer dissatisfaction and erodes a company’s brand Can cause safety issues Defective products waste materials and time, increasing costs A culture of quality and continuous improvement needs to be built into every aspect of a company’s operations – not just checking products at the end of the production line. The high cost of defects Suppose you’re the new quality control supervisor at Widgets Inc., which produces 100 widgets a day at a cost of $10 each. Your first quality audit revealed a 20% defect rate. How much are defects costing Widgets Ltd. each day? How much could the company save by cutting the defect rate in half? A. $20 B. $200 C. $2,000 D. Indeterminable Quality control procedures should be integrated into the entire production process and focus on root causes of problems. Quality improvement does more than save money. It also leads to better utilization of materials and labour, fewer production delays, and higher customer satisfaction. Formal quality management programs like TQM and Six Sigma can help. Optional class discussion questions 1. Discuss the advantages and disadvantages of having long/short product line for a cosmetics start-up 2. Discuss how an error in creating the right quantities of a product may hamper efficiency and/or profitability 3. Evaluate technology options for a small-scale apparel manufacturer that deals in customized clothing