Operations Management (MEL 356) PPT PDF
Document Details
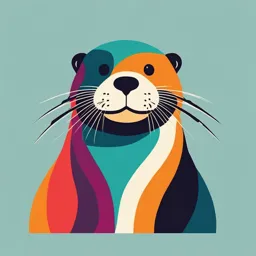
Uploaded by RiskFreeGreatWallOfChina
National Institute of Technology Uttarakhand
Dr. Hitesh Sharma
Tags
Summary
This presentation covers Operations Management (MEL 356), including production systems, performance measures, and learning objectives. It discusses the role of OM in business, decisions made by operations managers, and contrasts service and manufacturing operations.
Full Transcript
OPERATIONS MANAGEMENT(MEL 356) Dr. Hitesh Sharma Assistant Professor (Grade-II) Department of Mechanical Engineering National Institute of Technology, Uttarakhand Srinagar (Garhwal)-246174 Course Code: MEL356 Course Title: Operations Management Structure (L-T-P): 3-...
OPERATIONS MANAGEMENT(MEL 356) Dr. Hitesh Sharma Assistant Professor (Grade-II) Department of Mechanical Engineering National Institute of Technology, Uttarakhand Srinagar (Garhwal)-246174 Course Code: MEL356 Course Title: Operations Management Structure (L-T-P): 3-0-0 Pre-requisite: NIL Contents: Production systems and performance measures. Life Cycle of a production system. Major managerial decisions in the life of a production system, Product design and process selection. Location and Layout of production systems, Product, Process and Cellular layouts. Demand Forecasting, Aggregate production planning. Inventory and MRP, Scheduling decisions and emerging trends. Text Book: 1. Russell, R.S. and Taylor, B.W., Operations Management, 7th ed., Wiley India, 2013. Additional Books: 1. Martinich, J.S., Production and Operations Management, Wiley India, 2009 2. Gaither, N. and Frazier, G., Operations Management, 9th ed., Cengage Learning, 2002. 3. Krajewski, L.J., Operations Management: Processes and Supply Chains with MyOMLab, Pearson Education, 2013. 5. Boeuf, M.L., Essence of Time Management, Jaico Publishing House, 2001. 6. Gupta, A.K. and Sharma, J.K., Management of Systems, Macmillan India Limited, 2010. Method of Assessment End-term Examination : 40/50 Sessional I Examination : 15/20 Sessional II Examination : 15/20 Teacher’s Assessment : 20 Class Test/Quiz/Assignment Mid-term Examination: Duration 1hr Two mid-term examinations will be conducted on schedule date as per academic calendar. All questions shall be compulsory. End-term Examination: Duration 2hrs End term examination shall be on entire syllabus. All the questions will be compulsory. Chapter 1 - Introduction to Operations Management Operations Management 5 Learning Objectives Define and explain OM Explain the role of OM in business Describe the decisions that operations managers make Describe the differences between service and manufacturing operations 6 Operations Management is: The business function responsible for planning, coordinating, and controlling the resources needed to produce products and services for a company 7 Operations Management is: A management function An organization’s core function In every organization whether Service or Manufacturing, profit or Not for profit 8 Typical Organization Chart 9 What is Role of OM? OM Transforms inputs to outputs – Inputs are resources such as People, Material, and Money – Outputs are goods and services 10 OM’s Transformation Process 11 OM’s Transformation Role To add value – Increase product value at each stage – Value added is the net increase between output product value and input material value Provide an efficient transformation – Efficiency – means performing activities well for least possible cost 12 Manufacturers vs Service Organizations Manufacturers: Services: Tangible product Intangible product Product is inventoried Product cannot be Low customer contact inventoried Longer response time High customer contact Capital intensive Short response time Labor intensive 13 Similarities for Service/Manufacturers Both use technology Both have quality, productivity, & response issues Both must forecast demand Both can have capacity, layout, and location issues Both have customers, suppliers, scheduling and staffing issues 14 Service vs Manufacturing Manufacturing often provides services Services often provides tangible goods Some organizations are a blend of service/manufacturing/quasi-manufacturing (QM) organizations QM characteristics include – Low customer contact & Capital Intensive 15 Growth of the Service Sector Service sector growing to 50-80% of non-farm jobs Global competitiveness Demands for higher quality Huge technology changes Time based competition Work force diversity 16 OM Decisions All organizations make decisions and follow a similar path – First decisions very broad – Strategic decisions Strategic Decisions – set the direction for the entire company; they are broad in scope and long-term in nature 17 OM Decisions Following decisions focus on specifics - Tactical decision – Tactical decisions: focus on specific day-to-day issues like resource needs, schedules, & quantities to produce – are frequent Strategic decisions less frequent Tactical and Strategic decisions must align 18 OM Decisions 19 Production systems Enterprise The task of the enterprise is economic decision-making and optimization of objectives in all aspects (Durlik I. 1993): marketing, product development, purchase of the necessary elements for the production, processing (final product and service), sales and customer service. Company’s operation comprise following areas: Production and technical area, Organizational and administrative area, The financial and economic area, Legal area. The company is composed of one or more production systems Production systems Production system – is deliberately designed and organized arrangement of material, energy and information used by humans and aimed to manufacture certain products (goods or services) in order to meet the needs of consumer. (Durlik I. 1993). Difference Between Production and Operations Management Sl.No. Production Management Operations Management 1. It can be defined as the administration It is used to mean that branch of of the set of activities concerning the management which deals with the creation of goods or transformation of administration both production of goods raw material into finished goods and provision of services to the customers. 2. In production management,, the The operations manager looks after the manager has to make decisions product design, quality, quantity, process regarding the design, quality, quantity design, location, manpower required, and cost of the product manufactured storing, maintenance, logistics, inventory by the department. management, waste management, etc. 3. Production Management can only be Operations management can be found in found in the firms where production of every organization, i.e. manufacturing goods is undertaken. concerns, service-oriented firms, banks, hospitals, agencies, etc. 4. The basic objective of production In contrast, operations management management is to provide the right aims at making the best possible use of quality goods in the right quantity at organization’s resources, in order to fulfil right time and best price. the customer’s wants Production system consists of five basic elements: 1. Input vector (data input), 2. Output vector (data output), 3. Processing (input into output), 4. Management system, 5. Feedback Value-Added-Process The difference between the cost of inputs and the value or price of outputs. Value added Inputs Transformation/ Outputs Land Conversion Goods Labor process Services Capital Feedback Control Feedback Feedback R1 R2 R3 M1 M1 M1 The M1 M1 M2 production M1 M1 M3 system may M1 M1 M4 M5 M6 M7 be very M1 M2 Offices M1 M1 M3 M4 M5 V complex M1 M1 M6 Operations Machines Resources Raw Materials 27 Many design issues arise for the production system Business Design Product Design Schedule Design Service System Distribution Design Design Production Control System Process Design System Design Design Machine Facility Design Design 28 Manufacturing system – production system Production Objectives High Profitability Low High Costs Sales Low Unit Quality High Customer Costs Product Service High High Low Fast Many Throughput Utilization Inventory Response products Less Short Low High More Variability Cycle Times Utilization Inventory Variability Production and Inventory Control- Introduction (30) Types of production systems 1. Computer Integrated Manufacturing 2. Flexible Manufacturing systems 3. Quick Response Manufacturing 4. Concurrent Engineering 5. Mass Customization 6. Lean Manufacturing, Toyota Production System 7. Canon Production System 8. Electrolux Manufacturing System 9. Kanban System 10.CONVIP System