Battery Electric Machine Systems Fundamentals PDF
Document Details
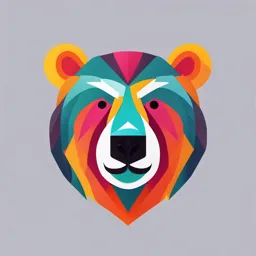
Uploaded by InspiringSerpentine6457
2024
Tags
Summary
This Caterpillar training module details the fundamentals of Battery Electric Machine (BEM) systems. It covers the components, functions, and operation of these systems, including charging, power distribution, and propulsion. The module also includes safety briefings.
Full Transcript
GLOBAL DEALER LEARNING Battery Electric Machine Systems Fundamentals Battery Electric Machine Systems MODULE 2 - TEXT REFERENCE SERVxxxx © 2024 Caterpillar. All Rights Reserved. CAT, CATERPILLAR, LET’S DO THE WORK, their respective logos, “Caterpillar Corporate Yellow”, the “Power Edge” and...
GLOBAL DEALER LEARNING Battery Electric Machine Systems Fundamentals Battery Electric Machine Systems MODULE 2 - TEXT REFERENCE SERVxxxx © 2024 Caterpillar. All Rights Reserved. CAT, CATERPILLAR, LET’S DO THE WORK, their respective logos, “Caterpillar Corporate Yellow”, the “Power Edge” and Cat “Modern Hex” trade dress as well as corporate and product identity used herein, are trademarks of Caterpillar and may not be used without permission. Caterpillar: Confidential Yellow SERVxxxx - 10/24 -2- Module 2 - Battery Electric Machine Systems TABLE OF CONTENTS SAFETY BRIEFING 4 PURPOSE 5 REASON 6 ASSESSMENT CRITERIA 7 LEARNING OUTCOMES 8 BATTERY ELECTRIC MACHINE (BEM) SYSTEMS OVERVIEW 9 GROUND LEVEL SERVICE CENTER 11 ELECTRICAL ISOLATION 12 BONDING AND GROUNDING WIRE SYSTEM 13 HAZARDOUS VOLTAGE (HAV) CABLES 14 CAT BATTERY PACK 15 R1700 XE 715 VDC BATTERY SYSTEM 17 DC CHARGING SYSTEM 19 AC CHARGING SYSTEM 20 POWER DISTRIBUTION UNIT (PDU) 21 INVERTER 22 PROPULSION MOTOR 24 PUMP MOTOR 26 DC / DC CONVERTER 28 AUXILIARY COMPONENTS 29 BATTERY SYSTEM CONTROL 30 HAV ELECTRICAL SYSTEM CONTROL 31 POWERTRAIN CONTROL 32 BATTERY SYSTEM COOLING - R1700 XE LHD 33 BATTERY SYSTEM COOLING - 950 GC MWL 34 HAV ELECTRICAL SYSTEM COOLING - R1700 XE LHD 35 HAV ELECTRICAL SYSTEM COOLING - 906 CWL 36 HAVE ELECTRICAL SYSTEM COOLING - 950 GC MWL 37 MOTOR COOLING AND LUBRICATION - R1700 XE LHD 38 MOTOR COOLING AND LUBRICATION - 950 GC MWL 39 PROPULSION MODE - 906, 950 GC, R1700 XE 40 Caterpillar: Confidential Yellow SERVxxxx - 10/24 -3- Module 2 - Battery Electric Machine Systems PROPULSION MODE - 301.9, 320 42 CHARGE MODE - R1700 XE 43 CHARGE MODE - 301.9, 320, 906, 950 GC 44 RETARDING MODE - 906, 950 GC, R1700 XE 45 PURPOSE 47 REASON 48 ASSESSMENT CRITERIA 49 LEARNING OUTCOMES 50 MODULE CONCLUSION 51 Caterpillar: Confidential Yellow SERVxxxx - 10/24 -4- Module 2 - Battery Electric Machine Systems SAFETY BRIEFING Emergency Phone Numbers First Aid Responders Location of Exits Location of Fire Extinguisher Room Alerts or Hazards Designated Location for Evacuation Storm Shelter Hazardous Material Safely Home. Everyone. Every Day.™ 4 SAFETY BRIEFING Provide a safety briefing. Before beginning this module, the following topics will be reviewed: Emergency Phone Numbers First Aid Responders Location of Exits Location of Fire Extinguisher Room Alerts or Hazards Designated Location for Evacuation Storm Shelter Hazardous Material Safely Home. Everyone. Every Day.™ NOTE: Any system or component specifications stated in this training module are used only for training purposes. Components and specifications may change as the product evolves. Always refer to Caterpillar Service information to obtain the most current specifications when servicing Cat® products. Caterpillar: Confidential Yellow SERVxxxx - 10/24 -5- Module 2 - Battery Electric Machine Systems PURPOSE This module covers the components of the Battery Electric Machine (BEM) systems. 5 PURPOSE Explain the purpose of this This module covers the components of the Battery Electric Machine (BEM) module. systems. Caterpillar: Confidential Yellow SERVxxxx - 10/24 -6- Module 2 - Battery Electric Machine Systems REASON Successful completion validates the knowledge, skills, and behaviors that are required to determine the location, function, and operation of BEM systems components. 6 REASON Explain the reason of this Successful completion validates the knowledge, skills, and behaviors that are module. required to determine the location, function, and operation of BEM systems components. Caterpillar: Confidential Yellow SERVxxxx - 10/24 -7- Module 2 - Battery Electric Machine Systems ASSESSMENT CRITERIA Knowledge Assessment Closed Book Minimum passing score of 80% 7 ASSESSMENT CRITERIA Explain the assessment criteria After the completion of this module, the participant must complete a knowledge for this module. assessment with a minimum passing score of 80%. Caterpillar: Confidential Yellow SERVxxxx - 10/24 -8- Module 2 - Battery Electric Machine Systems LEARNING OUTCOMES After the completion of this module, the participant will be able to: Identify BEM systems components. Describe BEM systems component function. Explain BEM systems and component operation. 8 LEARNING OUTCOMES Explain the learning outcomes of After the completion of this module, the participant will be able to: this module. Identify the components of the BEM systems. Describe the function of BEM systems components. Explain the operation of the BEM systems and their components. Caterpillar: Confidential Yellow SERVxxxx - 10/24 -9- Module 2 - Battery Electric Machine Systems BEM SYSTEMS OVERVIEW 1 7 9 9 6 8 5 2 3 4 9 BATTERY ELECTRIC MACHINE (BEM) SYSTEMS OVERVIEW Identify the main components In a Cat® machine with BEM systems, stored electric power from a battery pack (1) and explain the basic operation is discharged to a Power Electronics Module (PEM) (2) of the battery system. The of a battery electric machine PEM serves as a connection point between the battery system, the charging system. system(s) (3) of the machine, and the Hazardous Voltage (HaV) electrical system of the machine. NOTE: The illustration above shows one of two battery boxes that comprises the battery pack of the R1700 XE Load-Haul-Dump (LHD). The other battery box, located on the opposite side of the inverter and pump motor, is not shown for illustrative purposes. When the battery system is charging, the PEM receives electric power from the charging system(s) of the machine. This enables the battery system to be resupplied with DC voltage from an external power source. When the battery system is discharging, the PEM supplies electric power to the Power Distribution Unit (PDU) (4) of the HaV electrical system. The PDU directs electric power to one or more inverters (5) of the HaV electrical system, one or more DC/DC converters (6) of the low voltage electrical system, and one or more auxiliary components that require hazardous levels of voltage for their power supply. Some battery electric machines, such as the example shown above, have a unit that functions as both a PEM and a PDU. Caterpillar: Confidential Yellow SERVxxxx - 10/24 -10- Module 2 - Battery Electric Machine Systems An inverter changes and controls the incoming electric power from the PDU, and then supplies precisely controlled voltage and current to a propulsion motor (7) and/or a pump motor (8). The propulsion motor converts electric power into mechanical power, and uses it to propel the machine by directing mechanical power through a gear box, drive shafts, differentials, axle shafts, final drives, and finally the wheels of the machine. The pump motor also converts electric power into mechanical power, but uses it to actuate a hydraulic pump or pump drive that operates all of the hydraulic systems of the machine. Many HaV components of battery electric machine systems require dedicated systems for cooling their electrical components and lubricating their mechanical components. Control over battery electric machine systems is managed by multiple Electronic Control Modules (ECMs) (9). This module will cover the systems and components mentioned above in detail, as well as some other supporting systems and features that are vital to the safe operation of the battery electric machine systems. Caterpillar: Confidential Yellow SERVxxxx - 10/24 -11- Module 2 - Battery Electric Machine Systems GROUND LEVEL SERVICE CENTER 1 2 11 GROUND LEVEL SERVICE CENTER Identify the HaV indicator lamp Battery electric machines have a ground level service center which contains safety and the battery disconnect features critical to its safe shutdown. switch. The HaV indicator lamp (1) monitors the voltage levels of the DC bus regardless of the position of the low voltage system’s battery disconnect switch (2). When hazardous voltage is present on the DC bus, the amber lamp is illuminated as shown above. Caterpillar: Confidential Yellow SERVxxxx - 10/24 -12- Module 2 - Battery Electric Machine Systems ELECTRICAL ISOLATION 12 ELECTRICAL ISOLATION Explain electrical isolation. The HaV components of the battery electric machine systems and any conductors within their component housings are electrically isolated from their component housings. This is done to prevent contact with hazardous voltage during service. The HaV components and their assemblies are sealed from outside moisture, oils, and other contaminants. Care should be taken to ensure these components and assemblies are clean, dry, and properly sealed after service is performed on them. Failure to properly clean and/or torque electrical connectors can lead to random ground fault conditions and unplanned down time. Caterpillar: Confidential Yellow SERVxxxx - 10/24 -13- Module 2 - Battery Electric Machine Systems BONDING AND GROUNDING WIRE SYSTEM 1 2 13 BONDING AND GROUNDING WIRE SYSTEM Identify the bonding and HaV components are connected to one another using bonding wires (1). grounding wires. Component housings are also connected to the machine frame using grounding wires (2). The lugs and fasteners of the wires ensure that all component housings are at the same electrical potential as the machine frame. This is done to reduce electrical noise and electric shock hazard. If a bonding or grounding wire must be temporarily disconnected to service a HaV component or conductor within a component housing, the wire must be reconnected before the machine returns to service. Clean and properly torqued lugs and fasteners are important to ensure good contact between the bonding or grounding wires and the component housings to which they are fitted. Caterpillar: Confidential Yellow SERVxxxx - 10/24 -14- Module 2 - Battery Electric Machine Systems HAZARDOUS VOLTAGE (HAV) CABLES 1 2 14 HAZARDOUS VOLTAGE (HAV) CABLES Identify the HaV cables. To convey electric power to the HaV components of the battery electric machine systems, orange-clad HaV cables (1) are used. Beneath the cladding is a woven, stranded, stainless wire overbraid (2). This strengthens the cable, provides it with protection from abrasion, and ensures a safe ground path for any voltage that may escape the insulation of the cable. In the event that conductor insulation fails while the Cat machine is in operation, hazardous voltage flows to the machine frame ground through the grounded conductor shield. The ground fault detection feature of the Cat machine will detect this electrical fault and will activate a ground fault event to protect the operator and the components of the battery electric machine systems. Ground faults are displayed on the Cat machine’s monitoring system. Caterpillar: Confidential Yellow SERVxxxx - 10/24 -15- Module 2 - Battery Electric Machine Systems CAT BATTERY PACK 2 1 3 15 CAT BATTERY PACK Identify the components of a Cat Most battery electric machines have a Cat Battery Pack as their battery system. Battery Pack. A Cat Battery Pack consists of three main components: Multiple Cat-branded battery modules (1) that store electric power A PEM (2) that directs hazardous voltage into and out of the battery system The PEM of the 50V Battery A Battery Management System (BMS) (3) that monitors and controls the Pack essentially functions as battery modules and PEM in the charging and discharging of the battery both a PEM and PDU for small system or compact battery electric machines. The battery modules of a Cat Battery Pack are organized into two columns placed side-by-side with one another. The battery modules are connected in specific configurations to either increase the voltage of the battery system (when connected in series) or extend the period in which electric power can be supplied by the battery system (when connected in parallel). The PEM of a Cat Battery Pack connects the battery modules to the machine’s HaV electrical system. Its internal components are configured by the BMS to direct the flow of hazardous voltage when the Cat Battery Pack is in either a charging or discharging state. Caterpillar: Confidential Yellow SERVxxxx - 10/24 -16- Module 2 - Battery Electric Machine Systems The BMS of a Cat Battery Pack consists of a BMS ECM, a Cat Product Link® radio, and multiple interface connectors which allow it to connect to the battery modules, the PEM, and the machine’s electronic control system. Caterpillar has 50V, 300V, and 600V Battery Packs that supply electric power to its battery electric machines, but they can be used for other applications as well. Depending on the machine, one or more of such products may be needed to supply sufficient electric power for a sufficiently long operation period. Caterpillar: Confidential Yellow SERVxxxx - 10/24 -17- Module 2 - Battery Electric Machine Systems R1700 XE 715 VDC BATTERY SYSTEM 3 2 1 17 R1700 XE 715 VDC BATTERY SYSTEM Identify the components of the The R1700 XE LHD has a battery system that is distinct from other battery electric R1700 XE battery system. machines. The battery system of the R1700 XE supplies 715 VDC to the HaV electrical system of the machine. The battery system of the R1700 XE consists of three main components: A battery pack consisting of two battery boxes (1) that store electric power The HaV junction box of the A HaV junction box (2) that connects the battery boxes to the charger R1700 XE essentially functions receptacle box, power inverter, and DC/DC converter as both a PEM and PDU in other A BMS (3) that monitors and controls the battery modules, HaV junction box, battery electric machines. and charger receptacle box in the charging and discharging of the battery system Each battery box of the R1700 XE organizes the battery modules inside them into five sets of battery strings. The modules of each string, and the strings that comprise each box, are connected in a specific configuration to provide 715 VDC to the HaV electrical system. Caterpillar: Confidential Yellow SERVxxxx - 10/24 -18- Module 2 - Battery Electric Machine Systems The HaV junction box connects the battery boxes to the charger receptacle box (charging system), the DC/DC converter (low voltage electrical system), and the inverter (HaV electrical system). Its internal components are configured by the BMS to direct the flow of hazardous voltage when the battery boxes are in either a charging or discharging state. The BMS for the R1700 XE is considerably more complex than the one for the Cat Battery Packs, requiring two Battery ECMs as well as many other control units to monitor and control the battery system at the battery string and battery module level. This is explained in further detail later in this module. Caterpillar: Confidential Yellow SERVxxxx - 10/24 -19- Module 2 - Battery Electric Machine Systems DC CHARGING SYSTEM 1 3 2 19 DC CHARGING SYSTEM Identify the components of the Battery electric machines have a DC charging system to recharge their battery DC charging system. modules using an external DC power source. For the R1700 XE LHD, it is equipped with a charger receptacle box (1) at the left rear of the machine. There are two DC charger ports (2), each of which allows the LHD to connect to a Mobile Equipment Charger (MEC) unit. Both DC charger ports can connect to a MEC unit in order to charge the machine faster. The charger receptacle box also contains several safety features (fuses, relays, vehicle electrical center) to ensure proper voltage and current is being delivered to the HaV junction box when the LHD is charging. The charger receptacle box is monitored by the BMS and controlled by the battery ECMs. The DC charging system for the other battery electric machines simply consists of a DC charger port (3) that directly connects to the PDU. The PDU contains the components needed to control the voltage and current entering into the Cat Battery Pack from the external DC source, and the port is monitored by the machine’s electronic control system. Caterpillar: Confidential Yellow SERVxxxx - 10/24 -20- Module 2 - Battery Electric Machine Systems AC CHARGING SYSTEM 3 1 2 20 AC CHARGING SYSTEM Identify the components of an AC Battery electric machines other than the R1700 XE LHD also have an AC charging charging system. system to recharge the battery modules of their Cat Battery Pack using an external AC power source. A machine’s AC charging system consists of an AC charger port (1), whose port type varies depending on region. Type 1 charger ports (upper left image) are for machines located in the U.S., whereas Type 2 charger ports (upper right image) are for machines located in the European Union (EU). The AC charging system connects to the PDU of the machine in a similar fashion as its DC charging system. AC voltage coming from the AC charger port must be rectified by one or more onboard chargers (2) into DC voltage before entering the PDU. The AC charging system makes use of fuses (3) to control the current of the AC voltage that is entering the onboard chargers. NOTE: If an AC power source is being used to charge the Cat Battery Pack, a DC power source cannot be used to charge it at the same time. If a DC power source is being used to charge the Cat Battery Pack, an AC power source cannot be used to charge it at the same time. Caterpillar: Confidential Yellow SERVxxxx - 10/24 -21- Module 2 - Battery Electric Machine Systems POWER DISTRIBUTION UNIT (PDU) 21 POWER DISTRIBUTION UNIT (PDU) Explain the operation of the PDU. The 320 Medium Hydraulic Excavator (MHEX), 906 Compact Wheel Loader (CWL), and 950 GC Medium Wheel Loader (MWL) are equipped with a PDU. When the Cat Battery Pack is in a discharging state, the PDU distributes the electric power provided by the battery modules to the inverter(s) of the machine, where electric power can be tailored to meet specific power/load demands during machine operation. It also supplies electric power to the DC/DC converter(s), which is essential for the operation of the low voltage electrical system. The PDU may also supply one or more auxiliary components that require hazardous voltage for their power supply. When the Cat Battery Pack is in a charging state, the PDU directs electric power provided by one of the charging systems of the machine to the battery modules. The HaV junction box of the R1700 XE LHD and the PEM of the 50V Battery Pack essentially function as both a PEM and PDU. Caterpillar: Confidential Yellow SERVxxxx - 10/24 -22- Module 2 - Battery Electric Machine Systems INVERTER 1 2 1 2 2 3 2 1 3 3 22 INVERTER Explain the operation of the An inverter of a battery electric machine converts incoming DC voltage into a inverter. specific voltage, current, and frequency for the electric motor(s) being supplied with electric power. The components within the inverter vary depending on the Cat machine. The incoming DC voltage is transmitted through the entry section (1) of the inverter, where it energizes the DC bus of the inverter. Electric charge from the DC bus is stored in capacitors to assist the inverter in being able to respond to changing power demands of the propulsion motor (if applicable) and pump motor. The DC voltage of the DC bus then travels through the exit section(s) (2) of the inverter, where modules with transistors and diodes invert the DC voltage to a Pulse Width Modulated (PWM) AC output voltage that has its voltage, current, and frequency precisely controlled. Once the inverter has attenuated the AC voltage, electric power is sent to the propulsion motor and/or pump motor via HaV cables. Some inverters require coolant to control the temperature of their internal components. Coolant ports (3) allow coolant to enter and exit the inverter. Caterpillar: Confidential Yellow SERVxxxx - 10/24 -23- Module 2 - Battery Electric Machine Systems The 301.9 Mini Hydraulic Excavator (MiniHEX) and 320 MHEX have one inverter that supplies the pump motor with electric power. The excavators do not have a propulsion motor. The 906 CWL and 950 GC MWL have two inverters; one dedicated to the propulsion motor, and one dedicated to the pump motor. The R1700 XE LHD has one inverter that supplies both its propulsion motor and pump motor with electric power. Caterpillar: Confidential Yellow SERVxxxx - 10/24 -24- Module 2 - Battery Electric Machine Systems PROPULSION MOTOR 1 4 3 2 3 2 1 1 24 PROPULSION MOTOR Identify the components of a The 906 CWL, 950 GC MWL, and R1700 XE LHD are equipped with a propulsion propulsion motor. motor (1). Electric power from the inverter is directed to the propulsion motor by way of HaV cables. The propulsion motor provides output torque needed to propel the machine. The propulsion motor of the 906 CWL directly connects to the rear axle assembly of the machine. The propulsion motor of the 950 GC MWL and R1700 XE LHD is part of a propulsion module consisting of the motor and an attached output transfer gear box (2). The motors of these machines are Switched Reluctance (SR) type motors that consists of a rotor assembly and stator assembly. The propulsion motors require coolant to control the temperature of their stator assembly. Coolant ports (3) allow coolant to enter and exit the cooling jacket surrounding the stator assembly within the motor housing. The R1700 XE LHD propulsion motor also requires oil to lubricate and cool the components of the rotor assembly. Lubrication ports (4) allow Powertrain Oil (PTO) to enter and exit the motor housing. Caterpillar: Confidential Yellow SERVxxxx - 10/24 -25- Module 2 - Battery Electric Machine Systems The rotor assembly of the SR motor found on the 950 GC MWL and R1700 XE LHD is made of laminated plates and is designed such that it has eight rotor poles. These rotor poles have no inherent magnetic properties. Through electromagnetic induction, a magnetic field within the cavity of the stator assembly exerts a magnetic force that causes the rotor assembly to rotate. The stator assembly of the SR motor found on the 950 GC MWL and R1700 XE LHD is designed to have 12 stator poles with stator coil windings that are wound around each pole in such a way that three-phase current is produced, inducing a magnetic field within the cavity of the stator assembly. The stator assembly of a SR motor takes turns having each of its phases of stator coil windings becoming ENERGIZED. This occurs when the position of a rotor pole is aligned with a stator pole. As a magnetic field builds around the stator pole that is energizing, electric flux is induced in the small gap between the aligned stator pole and rotor pole. As the rotor pole moves away from the energized stator pole, the reluctance within the air gap is reduced. This causes the electric flux in the air gap to increase. This increases the current being produced within the stator coil windings. When the rotor pole gets too far from the stator pole, it becomes DE-ENERGIZED. The collapse of the magnetic field induces a current in the stator coil windings of the stator pole that is de-energizing. Electric power is delivered to the bus bars of the SR motor via HaV cables. The three-phase AC power emulates a rotating magnetic field inside the cavity of the stator assembly. This magnetic field produces a force that acts upon the rotor assembly, causing a mechanical rotation. This rotation is transferred to the output transfer gear box of the propulsion module. These gears in turn cause the differentials and final drives to rotate. The rotational speed and direction of a propulsion motor will ultimately determine the speed and direction of the machine’s travel. Caterpillar: Confidential Yellow SERVxxxx - 10/24 -26- Module 2 - Battery Electric Machine Systems PUMP MOTOR 3 1 2 2 1 1 26 PUMP MOTOR Identify the components of a Electric power from the inverter is directed to the pump motor (1) by way of HaV pump motor. cables. The pump motor drives a hydraulic pump (2) directly or is attached to a pump drive (3) that transfers power to hydraulic pump(s) that provide oil to the hydraulic systems of the machine. The pump motor consists of a rotor assembly and stator assembly. Their design and construction varies depending on the machine. Like the propulsion motors, some pump motors require coolant to control the temperature of their stator assembly. The pump motors of the 906 CWL and 950 GC MWL have coolant ports which allow coolant to enter and exit the cooling jacket surrounding the stator assembly within the motor housing. The R1700 XE LHD pump motor requires oil to lubricate and cool the components of the rotor assembly. Lubrication ports allow PTO to enter and exit the motor housing. Caterpillar: Confidential Yellow SERVxxxx - 10/24 -27- Module 2 - Battery Electric Machine Systems Electric power is delivered to the bus bars of the pump motor via HaV phase cables. The three-phase AC power emulates a rotating magnetic field inside the cavity of the stator assembly. This magnetic field produces a force that acts upon the rotor assembly, causing a mechanical rotation. This rotation is transferred to the attached hydraulic pump or pump drive. In the case of a pump drive, there are multiple hydraulic pumps that it actuates. The pump or pumps driven by the pump motor circulate hydraulic oil within all the hydraulic systems for the machine. For the 301.9 MiniHEX and the 320 MHEX, this includes the hydraulic system that propels the tracks of the machine. Caterpillar: Confidential Yellow SERVxxxx - 10/24 -28- Module 2 - Battery Electric Machine Systems DC / DC CONVERTER 2 3 2 1 2 1 1 2 3 28 DC / DC CONVERTER Explain the operation of a DC/DC Battery electric machines are equipped with one or more DC/DC converters. These converter. converters take the hazardous voltage from the DC bus of the PDU and convert it to either 12 VDC or 24 VDC, depending on the machine. This supplies electric power to the low voltage batteries for the low voltage system of the machine. The low voltage system consists of components such as lights, control panels, and other electrical and electronic components of the machine that require low voltage in order to function. A DC/DC converter typically has one HaV input port (1) that receives hazardous voltage from the PDU, and multiple low voltage output ports (2) that directly supply key components of the low voltage system. Some DC/DC converters require coolant to control the temperature of their internal components. Coolant ports (3) allow coolant to enter and exit the converter. Caterpillar: Confidential Yellow SERVxxxx - 10/24 -29- Module 2 - Battery Electric Machine Systems AUXILIARY COMPONENTS 2 1 4 3 29 AUXILIARY COMPONENTS Identify the battery electric Some battery electric machines have components that need to be supplied with machine auxiliary components. hazardous voltage but are not considered part of the HaV electrical system. They are supplied with electric power by the PDU of the machine. Examples of auxiliary components that require hazardous voltage to be supplied to them include the optional cab heater (1) of the 301.9 MiniHEX, the Positive- Temperature-Coefficient (PTC) heating elements (2) of the 906 CWL and 950 GC MWL, and the Air Conditioning (A/C) compressor (3) and Thermal Management System (TMS) (4) of the 950 GC MWL. NOTE: The cab heater of the 301.9 MiniHEX connects directly to the PEM of the 50V Battery Pack. This is because there is no PDU for the 301.9 MiniHEX; the PEM of the 50V Battery Pack essentially functions as a PDU for the machine as well. Caterpillar: Confidential Yellow SERVxxxx - 10/24 -30- Module 2 - Battery Electric Machine Systems BATTERY SYSTEM CONTROL 3 1 3 4 2 7 5 6 9 8 6 30 BATTERY SYSTEM CONTROL Identify the electronic control There are two main electronic control systems that pertain to battery electric system components. machine systems: the BMS and the Electric Drive Control System. The BMS is responsible for monitoring and controlling the functions of the battery modules, HaV junction box, and charger receptacle box for the R1700 XE LHD. For all other battery electric machines, the BMS is responsible for monitoring and controlling the functions of its accompanying battery modules and PEM. The BMS of a Cat Battery Pack consists of a BMS ECM (1), a Cat Product Link® radio (2), and multiple interface connectors (3) which allow it to connect to the battery modules, the PEM, and the ECM responsible for the HaV electrical system of the machine. The BMS for the R1700 XE LHD is considerably more complex than the system for other battery electric machines. Each battery module is monitored by a Safety Module Unit (SMU) (4) that is fitted to them. Each string of battery modules has their SMUs monitored by a Battery Management Unit (BMU) (5) located in a battery control compartment (6) on the outside of each battery box. A Master Battery Management Module (MBMM) (7) inside the left battery control compartment oversees all of the BMUs in both battery control compartments. The BMUs and MBMM in the left battery control compartment are also controlled by a dedicated Battery ECM (8). The BMUs in the right battery control compartment are also controlled by a dedicated Battery ECM (9). Caterpillar: Confidential Yellow SERVxxxx - 10/24 -31- Module 2 - Battery Electric Machine Systems HAV ELECTRICAL SYSTEM CONTROL 2 1 3 31 HAV ELECTRICAL SYSTEM CONTROL Identify the battery electric Just as there is at least one ECM responsible for managing the battery system of a machine ECMs. battery electric machine, there is an ECM responsible for monitoring and controlling the functions of the HaV electrical system components. The R1700 XE LHD has an Electric Drive ECM (1), which directly monitors and controls the function of the inverter and DC/DC converter. The 301.9 MiniHEX has a Machine ECM (2) which, among its many functions, includes monitoring and controlling the inverter and DC/DC converter. It also monitors and controls the onboard chargers and charger ports of the charging systems of the machine. The 906 CWL has an Electric Drive ECM (3) located near the machine’s PDU that is responsible for monitoring and controlling the PDU, inverters, and DC/DC converter. It also monitors and controls the onboard chargers and charger ports of the charging systems of the machine. Indirect monitoring and control of the pump motor and propulsion motor (if applicable) for battery electric machines can be performed by interpreting or adjusting the voltage, current, and frequency of the electric power being sent to them by their inverter. Caterpillar: Confidential Yellow SERVxxxx - 10/24 -32- Module 2 - Battery Electric Machine Systems POWERTRAIN CONTROL 2 1 2 32 POWERTRAIN CONTROL Identify the ECMs that control the The ECMs responsible for managing the battery electric machine systems are powertrain of the battery electric typically governed by an ECM that monitors and controls the functions of the machines. powertrain as a whole. The R1700 XE LHD has a Powertrain ECM (1) located within an ECM enclosure above the propulsion motor of the machine. Both Battery ECMs and the Electric Drive ECM are overseen by this ECM. The 301.9 MiniHEX only has one ECM, which is the Machine ECM. The BMS ECM of the 50V Battery Pack is overseen by this ECM. The 906 CWL and 950 GC MWL both have a Machine ECM (2) located behind the operator’s seat inside the cab of the machine. The BMS ECM(s) of the 300V Battery Pack or 600V Battery Packs and the Electric Drive ECM are overseen by this ECM. By processing sensor inputs throughout the machine and input commands from the controls within the operator station, the ECM that governs the powertrain of the battery electric machine can issue specific outputs to the ECMs that directly control the battery system and HaV electrical system components when the machine is in operation. Caterpillar: Confidential Yellow SERVxxxx - 10/24 -33- Module 2 - Battery Electric Machine Systems BATTERY SYSTEM COOLING - R1700 XE LHD 1 4 7 8 9 6 3 5 2 33 BATTERY SYSTEM COOLING - R1700 XE LHD Identify the main components Some battery systems require a dedicated cooling circuit to control the temperature of the R1700 XE LHD battery of the cells within the battery modules. cooling circuit. The R1700 XE LHD has a battery cooling circuit. It consists of a shunt tank (1) located between the battery boxes at the rear of the machine. Battery coolant is directed to a holding tank (2) near the bottom of the machine. Coolant pumps (3) direct flow from the holding tank into the battery boxes by way of coolant hoses and lines (4). As battery coolant travels past the battery modules within each battery box, heat is exchanged. Once the coolant has made its way through the battery boxes, it is directed to the heat exchanger (5). A heat exchanger cooling circuit consisting of a thermal expansion valve (6), compressor (7), condenser (8), and dryer (9) serves to cool the heat exchanger. Heat is exchanged between the two cooling circuits. Battery coolant is then pumped back to the holding tank to complete the cycle. Caterpillar: Confidential Yellow SERVxxxx - 10/24 -34- Module 2 - Battery Electric Machine Systems BATTERY SYSTEM COOLING - 950 GC MWL 1 4 5 3 2 34 BATTERY SYSTEM COOLING - 950 GC MWL Identify the components of the The battery cooling circuit of the 950 GC MWL consists of a tank (640-7336) (1) 950 GC MWL battery cooling that supplies battery coolant to the four 600V Battery Packs (2) that are equipped circuit. on the machine with a network of coolant hoses and tubes (3). The temperature of the battery coolant is controlled by the TMS (4). The TMS is cooled by a pair of fans (616-1480) (5). The TMS has a coolant pump inside of it that circulates the coolant throughout the cooling circuit. Caterpillar: Confidential Yellow SERVxxxx - 10/24 -35- Module 2 - Battery Electric Machine Systems HAV ELECTRICAL SYSTEM COOLING - R1700 XE LHD 1 3 4 5 6 2 35 HAV ELECTRICAL SYSTEM COOLING - R1700 XE LHD Identify the components of the Some battery electric machines require a dedicated cooling circuit to control the R1700 XE LHD HaV electrical temperature of their HaV electrical system components. system cooling circuit. The R1700 XE LHD has a HaV component cooling circuit. It consists of a shunt tank (1) located between the battery boxes at the rear of the machine. A coolant pump (2) directs flow from the shunt tank into the DC/DC converter (3), followed by the inverter (4), then the propulsion motor (5). As the coolant travels through each component, heat is exchanged. Once the coolant has made its way through the cooling jacket of the propulsion motor, the coolant is directed to a radiator (6). Air directed across the radiator coils by a hydraulically-driven cooling fan serves to lower the temperature of the coolant within the radiator. The coolant is then pumped back towards the coolant pump to complete the cycle. Caterpillar: Confidential Yellow SERVxxxx - 10/24 -36- Module 2 - Battery Electric Machine Systems HAV ELECTRICAL SYSTEM COOLING - 906 CWL 2 1 11 4 10 6 5 3 9 7 8 36 HAV ELECTRICAL SYSTEM COOLING - 906 CWL Identify the components of the The HaV component cooling circuit for the 906 CWL has a shunt tank (1) located to 906 CWL HaV electrical system the left of the radiator (2) near the rear of the machine. A coolant pump (3) directs cooling circuit. flow to the propulsion motor inverter (4), pump motor inverter (5), and DC/DC converter (6). As the coolant travels through each component, heat is exchanged. Coolant that flows through the propulsion motor inverter next makes its way through the stator cooling jacket of the propulsion motor (7). Coolant that flows through the pump motor inverter next enters the stator cooling jacket of the pump motor (8). As the coolant travels through the cooling jackets, heat is exchanged. Once the coolant has made its way through the DC/DC converter, it rejoins with the coolant from the propulsion motor and pump motor. The coolant then passes through the hydraulic oil cooler (9). As coolant travels through the cooler, heat is exchanged. Coolant that has passed through the hydraulic oil cooler next arrives at a pump valve (10). The pump valve directs coolant to the radiator. Air directed across the radiator coils by the radiator fans (11) serves to lower the temperature of the coolant within the radiator. The coolant is then pumped back towards the coolant pump to complete the cycle. Caterpillar: Confidential Yellow SERVxxxx - 10/24 -37- Module 2 - Battery Electric Machine Systems HAV ELECTRICAL SYSTEM COOLING - 950 GC MWL 1 2 2 1 4 3 8 5 9 6 10 7 37 HAVE ELECTRICAL SYSTEM COOLING - 950 GC MWL Identify the components of the The HaV component cooling circuit for the 950 GC MWL has a shunt tank (1) 950 GC MWL HaV electrical located to the left of the motor cooling group (616-1475) (2) on the right side of the system cooling circuit. machine. This cooling circuit uses two coolant pumps. The upper coolant pump (3) directs flow to the DC/DC converter (4), whereupon exiting the converter it then enters the onboard charger (5). Coolant that flows through the onboard pump enters the pump motor inverter (6) next. Coolant that flows through the pump motor inverter then makes its way through the stator cooling jacket of the pump motor (7). As the coolant travels through these components, heat is exchanged. The lower coolant pump (8) directs flow to the propulsion motor inverter (9). Coolant that flows through the propulsion motor inverter next enters the stator cooling jacket of the propulsion motor (10). As the coolant travels through these components, heat is exchanged. Once the coolant has made its way through the motors, the coolant is directed into the motor cooling group. Air directed across the radiator core by three fans (640-2353) serves to lower the temperature of the coolant within the module. The coolant is then pumped back towards the coolant pumps to complete the cycle. Caterpillar: Confidential Yellow SERVxxxx - 10/24 -38- Module 2 - Battery Electric Machine Systems MOTOR COOLING AND LUBRICATION - R1700 XE LHD 6 5 4 3 2 1 38 MOTOR COOLING AND LUBRICATION - R1700 XE LHD Identify the components of the Some battery electric machine motors require a dedicated cooling and lubrication R1700 XE LHD motor cooling and circuit to maintain their moving parts. lubrication circuit. The R1700 XE LHD has a motor cooling and lubrication circuit that provides Powertrain Oil (PTO) to the propulsion motor (1) and pump motor (2). It also cools and lubricates the components within the output transfer gear box (3). This system is kept separate from the axle oil cooling and lubrication system that has its own differential and final drive oil. The motor cooling and lubrication circuit consists of a PTO pump (4) located on the upper left section of the pump module. The oil flows to a PTO filter (5) positioned between the pump module and propulsion motor. The filtered oil then lubricates the rotor assemblies of the propulsion motor and pump motor. Oil from the rotor assembly of the propulsion motor also lubricates and cools the gears inside the output transfer gear box. Once the rotor assemblies and gears have been lubricated and cooled, oil is directed to the PTO cooler (6) located in front of the cooling fan at the rear of the machine. Moving air from the cooling fan is used to cool the oil as it travels through the oil cooler. The cooled oil is then directed into the bottom of the output transfer gear box, where it is pulled back towards the PTO pump to complete the cycle. Caterpillar: Confidential Yellow SERVxxxx - 10/24 -39- Module 2 - Battery Electric Machine Systems MOTOR COOLING AND LUBRICATION - 950 GC MWL 5 1 2 3 4 39 MOTOR COOLING AND LUBRICATION - 950 GC MWL Identify the components of the The 950 GC MWL has a motor cooling and lubrication circuit that provides PTO to 950 GC MWL motor cooling and the propulsion motor (1) only. It also cools and lubricates the components within the lubrication circuit. output transfer gear box (2). The 950 GC MWL motor cooling and lubrication circuit consists of a PTO pump (3) located on the lower section of the pump module. The oil flows to a PTO filter (4) positioned to the left of the output transfer gear box. The filtered oil then lubricates the gears inside the output transfer gear box and the rotor assembly of the propulsion motor. Once the rotor assemblies and gears have been lubricated and cooled, oil is directed to the oil radiator (5) located on the rear right side of the machine. Moving air from a fan (640-2354) is used to cool the oil as it travels through the cooler core. The cooled oil is then directed into the bottom of the output transfer gear box, where it is pulled back towards the PTO pump to complete the cycle. Caterpillar: Confidential Yellow SERVxxxx - 10/24 -40- Module 2 - Battery Electric Machine Systems PROPULSION MODE - 906, 950 GC, R1700 XE 2 5 1 4 6 3 7 40 PROPULSION MODE - 906, 950 GC, R1700 XE Explain machine propulsion When the 906 CWL, 950 GC MWL, or R1700 XE LHD are in propulsion mode, the mode in the 906, 950 GC, and battery system is discharging DC voltage to the HaV electrical system. R1700 XE machines. In order to propel the machine, the ECM (1) responsible for overseeing the machine’s powertrain system determines torque output based on operator input and the demands of the system. It also communicates actionable data to the ECM(s) responsible for the BMS and the ECM responsible for the HaV components of the machine’s HaV electrical system. The ECM(s) (2) responsible for the battery system has the BMS check the status of every battery module that comprises the battery pack (3). If no faults are detected, the battery system is enabled and DC voltage is discharged from the battery modules to the PEM(s) or HaV junction box (4). The ECM responsible for the HaV electrical system checks the status of the PDU (if applicable) (5) and the inverter (6) responsible for supplying the propulsion motor (7) with electric power. If no faults are detected, the PDU and inverter are enabled, and DC voltage from the PEM or HaV junction box can flow to the DC bus of the inverter. The inverter converts the incoming DC voltage into AC voltage, whose voltage, current, and frequency is precisely controlled by commands from the governing ECM. Caterpillar: Confidential Yellow SERVxxxx - 10/24 -41- Module 2 - Battery Electric Machine Systems AC voltage from the inverter is received by the propulsion motor. The speed and direction of the propulsion motor determines the speed and direction of machine travel. For the 950 GC MWL and R1700 XE LHD, this is passed on mechanically to the gears of the output transfer gear box, where it is then transferred to the lower power train, propelling the machine. For the 906 CWL, this mechanical power is transferred directly to the rear axle assembly. Caterpillar: Confidential Yellow SERVxxxx - 10/24 -42- Module 2 - Battery Electric Machine Systems PROPULSION MODE - 301.9, 320 4 5 3 1 2 6 42 PROPULSION MODE - 301.9, 320 Explain propulsion mode in the When the 301.9 MiniHex or 320 MHEX are in propulsion mode, the battery system 301.9 and 320 machines. is discharging DC voltage to the HaV electrical system. In order to propel the machine, the ECM (1) responsible for overseeing the machine’s powertrain system determines torque output based on operator input and the demands of the system. It also communicates actionable data to the BMS ECM and the ECM responsible for the components of the machine’s HaV electrical system. The BMS ECM (2) checks the status of every battery module (3). If no faults are detected, the PEM (4) is enabled, and DC voltage is discharged from the battery modules. The ECM responsible for the HaV electrical system checks the status of the PDU (if applicable) and the inverter (5) responsible for supplying the pump motor (6) with electric power. If no faults are detected, the PDU and inverter are enabled, and DC voltage from the PEM can flow to the DC bus of the inverter. The inverter converts the incoming DC voltage into AC voltage, whose voltage, current, and frequency is precisely controlled by commands from the governing ECM. AC voltage from the inverter is received by the pump motor. The pump motor actuates a hydraulic pump, which pumps hydraulic oil to the track motors of the machine. The speed and direction of the tracks is determined by the direction and flow of hydraulic oil sent to the track motors. Caterpillar: Confidential Yellow SERVxxxx - 10/24 -43- Module 2 - Battery Electric Machine Systems CHARGE MODE - R1700 XE 6 2 5 3 7 4 1 43 CHARGE MODE - R1700 XE Explain charge mode in an When the R1700 XE LHD is in charge mode, the battery system is being supplied R1700 XE machine. with DC voltage from the charging system. When a MEC unit is connected to a DC charger port (1), the Battery ECM (2) responsible for that port checks the status of the charger receptacle box (3). If no faults are detected, the HaV junction box (4) is enabled, and DC voltage can flow to the HaV junction box. The Battery ECMs then have the BMS check the status of every battery module. If no faults are detected, the battery box terminals (5) permit flow of DC voltage into the battery boxes (6), where DC voltage is supplied to battery modules based on specific charge demand from the BMUs found inside the battery control boxes (7). Caterpillar: Confidential Yellow SERVxxxx - 10/24 -44- Module 2 - Battery Electric Machine Systems CHARGE MODE - 301.9, 320, 906, 950 GC 7 4 3 8 2 1 7 4 3 8 6 5 1 44 CHARGE MODE - 301.9, 320, 906, 950 GC Explain charge mode in the 301.9, When a battery electric machine with a Cat Battery Pack is in charge mode, the 320, 906, and 950 GC machines. battery system is being supplied with voltage from a power source via one of the machine’s charging systems. If the Cat Battery Pack (1) is being charged through the DC charger port (2) of the machine, the ECM (3) responsible for the machine’s charging system checks the status of the DC charger port and PDU (4). If no faults are detected, DC voltage is allowed to flow to the PDU. If the Cat Battery Pack is being charged through the AC charger port (5) of the machine, the ECM responsible for the machine’s charging system checks the status of the AC charger port, onboard charger(s) (6), and PDU. If no faults are detected, AC voltage is allowed to flow to the onboard chargers, where it is rectified into DC voltage. The rectified DC voltage is then directed to the PDU. Once the charging system of the machine has become active, the BMS ECM(s) (7) check the status of the PEM(s) (8) and battery modules. If no faults are detected, DC voltage from the PDU is allowed to flow to the PEM, where it is then directed into the battery modules. DC voltage is supplied to the battery modules based on specific charge demand from the BMS ECM. Caterpillar: Confidential Yellow SERVxxxx - 10/24 -45- Module 2 - Battery Electric Machine Systems RETARDING MODE - 906, 950 GC, R1700 XE 1 5 4 7 3 2 9 8 6 45 RETARDING MODE - 906, 950 GC, R1700 XE Explain the retarding mode for When the machine is traveling downhill and exceeds a specified speed, the the 906, 950 GC, and R1700 XE machine will enter retarding mode. In this mode of operation, the battery system is machines. being supplied with DC voltage by the HaV electrical system. When the ECM (1) responsible for overseeing the machine’s powertrain system has it enter retarding mode, the ECM responsible for the HaV electrical system has the propulsion motor (2) begin to operate as though it were a generator. Mechanical power from the rotor assembly is converted into electric power by the stator assembly. This electric power is then supplied to the inverter (3) of the propulsion motor. For the 906 CWL and 950 GC MWL, the DC voltage from the inverter would then flow to the PDU (4). The ECM(s) (5) responsible for the battery system has the BMS check the status of every battery module of the Cat Battery Pack(s) (6) for the 906 and 950 GC wheel loaders, or the battery boxes for the R1700 XE LHD. If no faults are detected, and the battery modules are capable of receiving electric charge, the PEM (7) or HaV junction box is enabled, permitting DC voltage to flow through it and supply the battery modules based on specific charge demand determined by the BMS. Caterpillar: Confidential Yellow SERVxxxx - 10/24 -46- Module 2 - Battery Electric Machine Systems In the event that the battery modules are no longer able to receive charge, the ECM responsible for the HaV electrical system directs electric power to the pump motor (8) instead. For the R1700 XE LHD, its power inverter is configured by the ECM to receive voltage from the propulsion motor and send voltage to the pump motor. For the 906 CWL and 950 GC MWL, the HaV electrical system is configured by the ECM to send voltage from the propulsion motor to PDU via the propulsion motor inverter, then to the pump motor via the pump motor inverter (9). Once the pump motor is supplied with voltage, the hydraulic pump for the 906 CWL or the pump module of the 950 GC MWL and R1700 XE LHD can utilize multiple hydraulic retarding methods to either dissipate this excess energy in the form of heat (using hydraulic fans) or store the energy hydraulically (such as using an electro-hydraulic retarding valve). Caterpillar: Confidential Yellow SERVxxxx - 10/24 -47- Module 2 - Battery Electric Machine Systems PURPOSE This module covers the components of the Battery Electric Machine (BEM) systems. 47 PURPOSE Explain the purpose of this This module covers the components of the Battery Electric Machine (BEM) module. systems. Caterpillar: Confidential Yellow SERVxxxx - 10/24 -48- Module 2 - Battery Electric Machine Systems REASON Successful completion validates the knowledge, skills, and behaviors that are required to determine the location, function, and operation of BEM systems components. 48 REASON Explain the reason of this Successful completion validates the knowledge, skills, and behaviors that are module. required to determine the location, function, and operation of BEM systems components. Caterpillar: Confidential Yellow SERVxxxx - 10/24 -49- Module 2 - Battery Electric Machine Systems ASSESSMENT CRITERIA Knowledge Assessment Closed Book Minimum passing score of 80% 49 ASSESSMENT CRITERIA Explain the assessment criteria After the completion of this module, the participant must complete a knowledge for this module. assessment with a minimum passing score of 80%. Caterpillar: Confidential Yellow SERVxxxx - 10/24 -50- Module 2 - Battery Electric Machine Systems LEARNING OUTCOMES After the completion of this module, the participant will be able to: Identify BEM systems components. Describe BEM systems component function. Explain BEM systems and component operation. 50 LEARNING OUTCOMES Explain the learning outcomes of After the completion of this module, the participant will be able to: this module. Identify the components of the BEM systems. Describe the function of BEM systems components. Explain the operation of the BEM systems and their components. Caterpillar: Confidential Yellow SERVxxxx - 10/24 -51- Module 2 - Battery Electric Machine Systems MODULE CONCLUSION 51 MODULE CONCLUSION Conclusion This concludes the Battery Electric Machine Systems module for the Battery Electric Machine Systems Fundamentals course. When used in conjunction with the service manuals, the information in this module will enable the participant to determine the location, function, and operation of BEM systems components. For service recommendations, always refer to the Operation and Maintenance Manual (OMM), service manuals, and other related Cat service publications. Caterpillar: Confidential Yellow