Caterpillar 50V Battery Pack PDF
Document Details
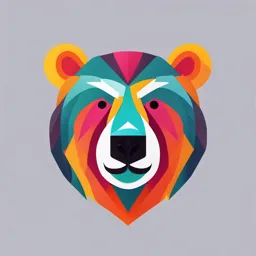
Uploaded by InspiringSerpentine6457
2024
Tags
Summary
This document is a Caterpillar training module detailing the operation and maintenance of a 50V battery pack. It includes diagrams, tables, and descriptions of the components of the battery pack.
Full Transcript
GLOBAL DEALER LEARNING CAT® BATTERY PACKS 50V Battery Pack MODULE 2 - TEXT REFERENCE SERVxxxx © 2024 Caterpillar. All Rights Reserved. CAT, CATERPILLAR, LET’S DO THE WORK, their respective logos, “Caterpillar Corporate Yellow”, the “Power Edge” and Cat “Modern Hex” trade dress as well as corp...
GLOBAL DEALER LEARNING CAT® BATTERY PACKS 50V Battery Pack MODULE 2 - TEXT REFERENCE SERVxxxx © 2024 Caterpillar. All Rights Reserved. CAT, CATERPILLAR, LET’S DO THE WORK, their respective logos, “Caterpillar Corporate Yellow”, the “Power Edge” and Cat “Modern Hex” trade dress as well as corporate and product identity used herein, are trademarks of Caterpillar and may not be used without permission. Caterpillar: Confidential Yellow SERVxxxx - 10/24 -2- Module 2 - 50V Battery Pack TABLE OF CONTENTS SAFETY BRIEFING 3 PURPOSE 4 REASON 5 ASSESSMENT CRITERIA 6 LEARNING OUTCOMES 7 PRODUCT OVERVIEW 8 PRODUCT SPECIFICATIONS 9 BATTERY MODULE CONFIGURATION 10 BATTERY MODULE CONNECTIONS - FRONT 11 BATTERY MODULE CONNECTIONS - REAR 12 PEM CONNECTIONS 13 PEM ARCHITECTURE 15 HAV CABLES WITH KEYED PLUGS 17 BMS DATA LINKS AND ANALOG FEEDBACK ARCHITECTURE 18 BMS ECM J1 COMMUNICATION 20 BMS ECM J2 COMMUNICATION 21 BMS ECM ISO-SPI COMMUNICATION 22 50V BATTERY PACK OPERATION - DISCHARGING 23 50V BATTERY PACK OPERATION - CHARGING 24 PURPOSE 25 REASON 26 ASSESSMENT CRITERIA 27 LEARNING OUTCOMES 28 MODULE CONCLUSION 29 Caterpillar: Confidential Yellow SERVxxxx - 10/24 -3- Module 2 - 50V Battery Pack SAFETY BRIEFING Emergency Phone Numbers First Aid Responders Location of Exits Location of Fire Extinguisher Room Alerts or Hazards Designated Location for Evacuation Storm Shelter Hazardous Material Safely Home. Everyone. Every Day.™ 3 SAFETY BRIEFING Provide a safety briefing. Before beginning this module, the following topics will be reviewed: Emergency Phone Numbers First Aid Responders Location of Exits Location of Fire Extinguisher Room Alerts or Hazards Designated Location for Evacuation Storm Shelter Hazardous Material Safely Home. Everyone. Every Day.™ NOTE: Any system or component specifications stated in this training module are used only for training purposes. Components and specifications may change as the product evolves. Always refer to Caterpillar Service information to obtain the most current specifications when servicing Cat® products. Caterpillar: Confidential Yellow SERVxxxx - 10/24 -4- Module 2 - 50V Battery Pack PURPOSE This module covers the components of the 50V Battery Pack. 4 PURPOSE Explain the purpose of this This module covers the components of the 50V Battery Pack. module. Caterpillar: Confidential Yellow SERVxxxx - 10/24 -5- Module 2 - 50V Battery Pack REASON Successful completion validates the knowledge, skills, and behaviors that are required to determine the location, function, and operation of 50V Battery Pack components. 5 REASON Explain the reason of this Successful completion validates the knowledge, skills, and behaviors that are module. required to determine the location, function, and operation of 50V Battery Pack components. Caterpillar: Confidential Yellow SERVxxxx - 10/24 -6- Module 2 - 50V Battery Pack ASSESSMENT CRITERIA Knowledge Assessment Closed Book Minimum passing score of 80% 6 ASSESSMENT CRITERIA Explain the assessment criteria After the completion of this module, the participant must complete a knowledge for this module. assessment with a minimum passing score of 80%. Caterpillar: Confidential Yellow SERVxxxx - 10/24 -7- Module 2 - 50V Battery Pack LEARNING OUTCOMES After the completion of this module, the participant will be able to: Identify 50V Battery Pack components. Describe 50V Battery Pack component function. Explain 50V Battery Pack operation. 7 LEARNING OUTCOMES Explain the learning outcomes of After the completion of this module, the participant will be able to: this module. Identify the components of the 50V Battery Pack. Describe the function of 50V Battery Pack components. Explain the operation of the 50V Battery Pack and its components. Caterpillar: Confidential Yellow SERVxxxx - 10/24 -8- Module 2 - 50V Battery Pack PRODUCT OVERVIEW 2 4 5 1 3 8 PRODUCT OVERVIEW Identify the main components of The 50V Battery Pack primarily consists of six battery modules (1). The battery the 50V Battery Pack. modules provide Direct Current (DC) power to a battery electric machine or other type of electrical equipment. A Power Electronics Module (2), or PEM, is situated on top of the battery modules. When the battery modules are charging, it is responsible for directing incoming DC voltage to the battery modules from a Hazardous Voltage (HaV) source. When the battery modules are discharging, the PEM is responsible for directing stored DC voltage from the battery modules to a HaV load. A Battery Management System (BMS) assembly is mounted to the front side of the battery modules. The assembly consists of a BMS Electronic Control Module (ECM) (3) and Cat Product Link™ radio (4). The BMS ECM monitors and controls the electronic components of the battery modules and PEM in order to facilitate proper battery system function. The 50V Battery Pack does not have an active coolant system. The battery module coolant ports are covered by protective caps (5). Caterpillar: Confidential Yellow SERVxxxx - 10/24 -9- Module 2 - 50V Battery Pack PRODUCT SPECIFICATIONS Variable Value Nominal Voltage 50.7 VDC Electric Charge 630.3 Ah Energy 31.9 kWh 9 PRODUCT SPECIFICATIONS Identify the specifications for the The specifications for the 50V Battery Pack are as follows: 50V Battery Pack. Nominal Voltage (Vnom): 50.7 VDC Electric Charge (Q): 630.3 Ah Energy (E): 31.9 kWh Caterpillar: Confidential Yellow SERVxxxx - 10/24 -10- Module 2 - 50V Battery Pack BATTERY MODULE CONFIGURATION 10 BATTERY MODULE CONFIGURATION Explain the configuration of the The 50V Battery Pack has its battery modules organized into two racks that are battery modules. positioned side-by-side with one another. Each battery rack consists of three battery modules stacked on top of one another vertically. The battery modules of each battery rack connect to one another in parallel, and the battery racks also connect to one another in parallel. Since the battery racks have their battery modules arranged in parallel, each battery rack has a nominal voltage identical to each of its battery modules (50.7 VDC). However, each battery rack has an electric charge of around 315.2 Ah. This is calculated by multiplying the electric charge of a battery module (105.1 Ah) by 3, the number of battery modules in the battery rack. The overall nominal voltage of the 50V Battery Pack is the same as the two battery racks that comprise it, because the battery racks are arranged in parallel. Its overall electric charge, however, is around 630.3 Ah. This is calculated by multiplying the electric charge of a battery rack by 2, the number of battery racks. The total energy of the 50V Battery Pack is thus calculated to be: 50.7 VDC x 630.3 Ah = 31,946 Wh, or 31.9 kWh Caterpillar: Confidential Yellow SERVxxxx - 10/24 -11- Module 2 - 50V Battery Pack BATTERY MODULE CONNECTIONS - FRONT 4 5 1 2 3 11 BATTERY MODULE CONNECTIONS - FRONT Identify the connections at the Each battery module has a negative (DC-) terminal receptacle (1) and a positive front of the battery modules. (DC+) terminal receptacle (2). HaV cables (3) connect these terminal receptacles to the battery terminals of the PEM. The six battery terminals inside the PEM above the left battery rack are the negative battery terminals (4), whereas the six battery terminals inside the PEM above the right battery rack are the positive battery terminals (5). Since the battery modules are all configured in parallel, each battery module is effectively its own battery string. This means that both terminal receptacles of each battery module require a dedicated connection to the PEM. The HaV cables going to the terminal receptacles of each battery module provide DC voltage to the battery modules from the PEM when the battery system is charging, and supply voltage to the PEM from the battery modules when the battery system is discharging. Caterpillar: Confidential Yellow SERVxxxx - 10/24 -12- Module 2 - 50V Battery Pack BATTERY MODULE CONNECTIONS - REAR 3 1 2 5 4 12 BATTERY MODULE CONNECTIONS - REAR Identify the connections at the Each battery module is connected to a bonding cable (1) by a clamp (2). One end rear of the battery modules. of the bonding cable runs to a ground inside the PEM (3), and along the bonding cable is a clamp (4) that connects the cable to the battery pack’s base frame (5). The bonding cable is made of a continuous stainless steel braided cable. The cable ensures that the battery modules, PEM, and base frame are kept at the same potential in the event of a ground fault. A continuous cable is used to ensure that in a scenario where a bonding point becomes loose or not fitted, the whole bonding architecture is not compromised. Caterpillar: Confidential Yellow SERVxxxx - 10/24 -13- Module 2 - 50V Battery Pack PEM CONNECTIONS 1 4 2 5 3 7 6 13 PEM CONNECTIONS Identify the PEM connections. The PEM is designed to control and monitor the voltage and current leaving the battery modules when the 50V Battery Pack is in a discharging state. It also controls and monitors the voltage and current entering the battery modules when the 50V Battery Pack is in a charging state. In order to do this, the PEM contains multiple terminals that permit flow of HaV electric power into and out of it. At the rear of the PEM, there are three sets of terminals connected to bus bars. The charging system bus bars (1) receive DC voltage from an external DC charging system. The main drive bus bars (2) supply DC voltage to an external HaV electrical system of a machine or other type of electrical equipment when the 50V Battery Pack is in a discharging state. The auxiliary circuit bus bars (3) supply DC voltage to one or more auxiliary HaV components that are considered separate from the HaV electrical system of a machine or other type of electrical equipment. One such example is the cab heater of the 301.9 Mini Hydraulic Excavator. For illustrative purposes, the lighter color indicates a negative (DC-) bus bar, whereas the darker color indicates a positive (DC+) bus bar. NOTE: Some Cat machine applications, such as the 301.9 Mini Hydraulic Excavator, use an AC charging system to supply the PEM with DC voltage via the main drive bus bars by using onboard chargers on the machine when the 50V Battery Pack is in charging mode. It is important to note that the PEM supports such functionality via the main drive bus bars. Caterpillar: Confidential Yellow SERVxxxx - 10/24 -14- Module 2 - 50V Battery Pack Between the charging system bus bars and the main drive bus bars is a ground connection (4). This connects the bonding cable outside of the PEM to a ground inside the PEM. At the front of the PEM, there are six negative battery terminals (5) that connect to the negative terminal receptacles of the battery modules, and six positive battery terminals (6) that connect to the positive terminal receptacles of the battery modules. Between the negative and positive battery terminals are a pair of interface connectors (7). These allow the interface board inside the PEM to communicate with the BMS ECM. Caterpillar: Confidential Yellow SERVxxxx - 10/24 -15- Module 2 - 50V Battery Pack PEM ARCHITECTURE 2 1 3 14 6 7 8 11 5 2 12 10 13 9 4 2 15 16 15 PEM ARCHITECTURE Identify the internal components The internal components of the PEM provide the BMS with a means to monitor and of the PEM. control the flow of hazardous voltage into and out of the PEM. This enables the 50V Battery Pack to enter either a charging state or discharging state. The PEM main circuit board (1) contains contactors (2) which can isolate the PEM outputs from the battery terminals. There is also a precharge contactor (3) that is located near the interface board (4). NOTE: This image shows three contactors, which were located in the PEM as of the ITTP publication date. One of the contactors will be removed in later production PEMs. There are fuses to prevent excess current when the 50V Battery Pack is charging or discharging. A charger fuse (5) limits current between the main circuit board and the negative main drive bus bar (6), and a main drive fuse (7) limits current between the main circuit board and the positive main drive bus bar (8). The auxiliary circuit bus bars (9) also have fuses. There is an auxiliary high current fuse (10), and a pair of auxiliary low current fuses (11). Caterpillar: Confidential Yellow SERVxxxx - 10/24 -16- Module 2 - 50V Battery Pack On the left side of the PEM, there are five IVT-S sensors (12) that monitor the current coming from or going to the negative (DC-) battery terminals (13) of the PEM. There is also one IVT-S sensor (14) that monitors both the current and voltage. This sensor measures both the pre-contactor and post-contactor voltage for the whole battery system. Lastly, there are six string fuses (15) near the positive (DC+) battery terminals (16). They prevent excess current from entering or leaving the PEM in a fault condition. Caterpillar: Confidential Yellow SERVxxxx - 10/24 -17- Module 2 - 50V Battery Pack HAV CABLES WITH KEYED PLUGS 1 3 5 4 2 2 4 1 17 HAV CABLES WITH KEYED PLUGS Explain how to connect and The terminal receptacles of the PEM are keyed; this means that HaV cables with disconnect the HaV cables with keyed plugs must be used to connect to them. This is done so that the HaV cable is keyed plugs. oriented in a very specific direction relative to the PEM, and eliminates the ability to insert the plugs into the incorrect terminal receptacle. Disconnecting a HaV cable with a keyed plug is identical to how it would occur for a normal plug. However, when connecting a HaV cable with a keyed plug (1) to a keyed terminal receptacle (2), proper alignment is critical. When connecting a HaV cable with a keyed plug to a terminal receptacle of the 50V Battery Pack, align the keys (3) of the plug with the keyways (4) of the terminal receptacle. The terminal receptacle may have a keyed collar (5) that rotates. If it does, rotate the collar such that the keyways of the collar are aligned with the keys of the plug. Once the keys of the plug are correctly aligned with the keyways of the terminal receptacle, push the plug directly into the terminal receptacle. Caterpillar: Confidential Yellow SERVxxxx - 10/24 -18- Module 2 - 50V Battery Pack BMS DATA BMS LINKS/ANALOG FEEDBACK DATA LINKS AND ANALOG ARCHITECTURE FEEDBACK ARCHITECTURE BIC (2) Battery Modules (1) Cat Product Link Radio (3) J4 PEM (4) Port (9) PEMIC 1 (10) J1 Port (6) J3 Port (8) LEGEND PEMIC 2 CAN A Data Link J2 Port (7) (11) CAN B Data Link BMS ECM CAN C Data Link (5) CAN D Data Link ISO-SPI Data Link Analog Feedback 18 BMS DATA LINKS AND ANALOG FEEDBACK ARCHITECTURE Identify the BMS data links and The diagram shows the overall electronic architecture of the BMS and illustrates the analog feedback architecture. the connectivity between all the electronic devices over the data links and analog feedback. The J1 port (6) of the BMS ECM (5) uses CAN Data Links for communications with external monitoring or control systems and the PEM. The CAN A and CAN C Data Links allow communications between the BMS ECM and the electronic control system of a machine or other type of electrical equipment via the Battery Interface Connector (BIC) (2). The CAN B Data Link allows communications between the BMS ECM and the sensors inside the PEM (4) via the left Power Electronics Module Interface Connector (PEMIC) (10). The CAN D Data Link allows communications between the BMS ECM and the Cat Product Link radio (3). The BMS also incorporates analog feedback connections. The BMS ECM directs analog feedback communications between it and the PEM, Cat Product Link radio, and an external electronic control system using its J1 port. There is an additional analog feedback connection between the J2 port (7) of the BMS ECM and the right PEMIC (11) of the PEM. This allows the BMS ECM to monitor and control the contactors inside the PEM. Caterpillar: Confidential Yellow SERVxxxx - 10/24 -19- Module 2 - 50V Battery Pack There are also ISO-SPI Data Link connections that allow communications between the BMS boards of the battery modules (1) and the BMS ECM. The battery modules connect to one another, then to the J3 port (8) and J4 port (9) of the BMS ECM, forming a ring or loop of connections. Caterpillar: Confidential Yellow SERVxxxx - 10/24 -20- Module 2 - 50V Battery Pack BMS ECM J1 COMMUNICATION 4 3 2 6 1 5 20 BMS ECM J1 COMMUNICATION Explain BMS ECM The J1 connector (1) of the BMS ECM communicates with the PEM and other communication via the J1 port. components of the BMS using both CAN Data Links and analog feedback. Communication with the PEM is done via a 31-pin PEMIC (2) that is fitted to the left interface connector of the PEM. CAN B Data Link and analog feedback communication enables the BMS ECM to monitor the sensors inside the PEM. The J1 connector enables the BMS ECM to communicate with an external electronic control system by way of the 29-pin BIC (3) near the top of the BMS assembly. The J1 connector enables the BMS ECM to communicate with the Cat Product Link radio by way of the 14-pin connector (4) at the top of the BMS assembly. The CAN B Data Link going to the PEM has an external terminal resistor (5) located near the J2 connector. There are also two external terminal resistors (6) located near the J1 connector for the CAN D Data Link between the BMS ECM and the Cat Product Link radio. There are no external terminal resistors for the CAN A and CAN C Data Links between the BMS ECM and the BIC. Caterpillar: Confidential Yellow SERVxxxx - 10/24 -21- Module 2 - 50V Battery Pack BMS ECM J2 COMMUNICATION 2 1 21 BMS ECM J2 COMMUNICATION Explain BMS ECM The J2 connector (1) of the BMS ECM communicates with the PEM using only communication via the J2 port. analog feedback. Communication with the PEM is done via a 29-pin PEMIC (2) that is fitted to the right interface connector of the PEM. This line of communication enables the BMS ECM to monitor and control the contactors inside the PEM. Caterpillar: Confidential Yellow SERVxxxx - 10/24 -22- Module 2 - 50V Battery Pack BMS ECM ISO-SPI COMMUNICATION 7 6 1 1 5 4 3 2 22 BMS ECM ISO-SPI COMMUNICATION Explain BMS communication via The BMS ECM forms a communication network with the BMS boards of the battery ISO-SPI (J3 and J4) ports. modules using ISO-SPI Data Links. The J3 and J4 connectors (1) of the BMS ECM connect to the lower data link connectors (2) of the BMS boards in the bottom row of battery modules. The upper data link connectors (3) of these BMS boards are connected to the lower data link connectors (4) of the BMS boards in the middle row of battery modules. The upper data link connectors (5) of the middle row of BMS boards are connected to the lower data link connectors (6) of the BMS boards for the top row battery modules. The upper data link connectors (7) of the top two battery modules are connected to one other, completing the communication loop. Caterpillar: Confidential Yellow SERVxxxx - 10/24 -23- Module 2 - 50V Battery Pack 50V BATTERY PACK OPERATION - DISCHARGING 2 3 1 1 23 50V BATTERY PACK OPERATION - DISCHARGING Explain the operation of the 50V When the 50V Battery Pack is in a discharging state, it is considered to be in its Battery Pack when discharging. normal mode of operation. DC voltage from the battery modules is directed to the PEM by way of HaV cables (1) connected to battery terminals inside the PEM. The BMS ECM configures the contactors of the PEM such that DC voltage is supplied to its main drive bus bars and auxiliary circuit bus bars (if applicable). Once DC voltage has traversed through the PEM and ENERGIZES the bus bars, HaV cables connected to the main drive bus bar terminals (2) and auxiliary circuit bus bar terminals (3) (if applicable) supply a machine or other type of electrical equipment with the electric charge stored by the battery modules, causing the State of Charge (SoC) of the battery modules to decrease over time. While the 50V Battery Pack is in a discharging state, the BMS ECM continually monitors the system for any conditions which may require the rate of discharge to be reduced, or if the product must become isolated from the HaV electrical system of the machine or other type of electrical equipment the product is supplying. Caterpillar: Confidential Yellow SERVxxxx - 10/24 -24- Module 2 - 50V Battery Pack 50V BATTERY PACK OPERATION - CHARGING 1 2 3 3 3 3 24 50V BATTERY PACK OPERATION - CHARGING Explain the operation of the 50V When the 50V Battery Pack is in a charging state, it is considered to be in its Battery Pack when charging. charging mode of operation. DC voltage originating from either a DC or AC voltage source is directed to the PEM by way of HaV cables. If an external DC voltage source (left image) is being used to charge the battery pack, the BMS ECM configures the contactors of the PEM such that DC voltage being supplied to the PEM by way of HaV cables connected to its charging system terminal receptacles (1) is able to flow through the PEM. If an external AC voltage source (right image) is being used to charge the battery pack, the voltage is rectified by an AC charging system before arriving at the PEM. The BMS configures the contactors of the PEM such that rectified DC voltage being supplied to the PEM by way of HaV cables connected to its main drive terminal receptacles (2) is able to flow through the PEM. Once DC voltage has traversed through the PEM, HaV cables (3) connected to the battery terminals of the PEM then supply this DC voltage to the battery modules, causing their SoC to increase over time. While the 50V Battery Pack is in a charging state, the BMS ECM continually monitors the system for any conditions which may require the rate of charge to be reduced, or if the product must become isolated from the HaV cables supplying the charging system bus bars or main drive bus bars with electric power. Caterpillar: Confidential Yellow SERVxxxx - 10/24 -25- Module 2 - 50V Battery Pack PURPOSE This module covers the components of the 50V Battery Pack. 25 PURPOSE Explain the purpose of this This module covers the components of the 50V Battery Pack. module. Caterpillar: Confidential Yellow SERVxxxx - 10/24 -26- Module 2 - 50V Battery Pack REASON Successful completion validates the knowledge, skills, and behaviors that are required to determine the location, function, and operation of 50V Battery Pack components. 26 REASON Explain the reason of this Successful completion validates the knowledge, skills, and behaviors that are module. required to determine the location, function, and operation of 50V Battery Pack components. Caterpillar: Confidential Yellow SERVxxxx - 10/24 -27- Module 2 - 50V Battery Pack ASSESSMENT CRITERIA Knowledge Assessment Closed Book Minimum passing score of 80% 27 ASSESSMENT CRITERIA Explain the assessment criteria After the completion of this module, the participant must complete a knowledge for this module. assessment with a minimum passing score of 80%. Caterpillar: Confidential Yellow SERVxxxx - 10/24 -28- Module 2 - 50V Battery Pack LEARNING OUTCOMES After the completion of this module, the participant will be able to: Identify 50V Battery Pack components. Describe 50V Battery Pack component function. Explain 50V Battery Pack operation. 28 LEARNING OUTCOMES Explain the learning outcomes of After the completion of this module, the participant will be able to: this module. Identify the components of the 50V Battery Pack. Describe the function of 50V Battery Pack components. Explain the operation of the 50V Battery Pack and its components. Caterpillar: Confidential Yellow SERVxxxx - 10/24 -29- Module 2 - 50V Battery Pack MODULE CONCLUSION 29 MODULE CONCLUSION Conclusion This concludes the 50V Battery Pack module for the Cat Battery Packs course. When used in conjunction with the service manuals, the information in this module will enable the participant to determine the location, function, and operation of 50V Battery Pack components. For service recommendations, always refer to the Operation and Maintenance Manual (OMM), service manuals, and other related Cat service publications. Caterpillar: Confidential Yellow