Caterpillar 50V, 300V, and 600V Battery Pack Overview PDF
Document Details
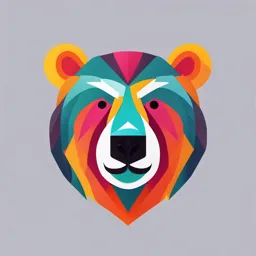
Uploaded by InspiringSerpentine6457
2024
Tags
Summary
This Caterpillar document provides an overview of the 50V, 300V, and 600V battery packs, including their components, safety, and operation.
Full Transcript
GLOBAL DEALER LEARNING CAT® BATTERY PACKS 50V, 300V, 600V Battery Pack Overview MODULE 1 - TEXT REFERENCE SERVXXXX © 2024 Caterpillar. All Rights Reserved. CAT, CATERPILLAR, LET’S DO THE WORK, their respective logos, “Caterpillar Corporate Yellow”, the “Power Edge” and Cat “Modern Hex” trade dr...
GLOBAL DEALER LEARNING CAT® BATTERY PACKS 50V, 300V, 600V Battery Pack Overview MODULE 1 - TEXT REFERENCE SERVXXXX © 2024 Caterpillar. All Rights Reserved. CAT, CATERPILLAR, LET’S DO THE WORK, their respective logos, “Caterpillar Corporate Yellow”, the “Power Edge” and Cat “Modern Hex” trade dress as well as corporate and product identity used herein, are trademarks of Caterpillar and may not be used without permission. Caterpillar: Confidential Yellow SERVXXXX - 10/24 -2- Module 1 - Battery System Overview TABLE OF CONTENTS SAFETY BRIEFING 3 PURPOSE 4 REASON 5 ASSESSMENT CRITERIA 6 LEARNING OUTCOMES 7 CAT BATTERY PACK OVERVIEW 8 BATTERY MODULE 9 BATTERY CELLS 10 BATTERY MODULE ARCHITECTURE 11 BATTERY MODULE CONFIGURATION 12 BATTERY MODULE SAFETY 13 POWER ELECTRONICS MODULE (PEM) 14 PEM ARCHITECTURE 15 HAZARDOUS VOLTAGE (HAV) CABLES 16 HAZARDOUS VOLTAGE (HAV) CABLE PLUGS 17 BATTERY MANAGEMENT SYSTEM (BMS) 18 BMS CONNECTIONS 19 BMS ECM 20 BATTERY MODULE STATE 21 BATTERY CAPACITY 22 CAT PRODUCT LINK RADIO 23 BMS BOARDS 24 BMS OPERATION - INPUTS 25 BMS OPERATION - OUTPUTS 26 PURPOSE 27 REASON 28 ASSESSMENT CRITERIA 29 LEARNING OUTCOMES 30 MODULE CONCLUSION 31 Caterpillar: Confidential Yellow SERVXXXX - 10/24 -3- Module 1 - Battery System Overview SAFETY BRIEFING Emergency Phone Numbers First Aid Responders Location of Exits Location of Fire Extinguisher Room Alerts or Hazards Designated Location for Evacuation Storm Shelter Hazardous Material Safely Home. Everyone. Every Day.™ 3 SAFETY BRIEFING Provide a safety briefing. Before beginning this module, the following topics will be reviewed: Emergency Phone Numbers First Aid Responders Location of Exits Location of Fire Extinguisher Room Alerts or Hazards Designated Location for Evacuation Storm Shelter Hazardous Material Safely Home. Everyone. Every Day.™ NOTE: Any system or component specifications stated in this training module are used only for training purposes. Components and specifications may change as the product evolves. Always refer to Caterpillar Service information to obtain the most current specifications when servicing Cat® products. Caterpillar: Confidential Yellow SERVXXXX - 10/24 -4- Module 1 - Battery System Overview PURPOSE This module covers the components that are common to the Cat 50V, 300V, and 600V Battery Packs. 4 PURPOSE Explain the purpose of this This module covers the components that are common to the Cat 50V, 300V, and module. 600V Battery Packs. Caterpillar: Confidential Yellow SERVXXXX - 10/24 -5- Module 1 - Battery System Overview REASON Successful completion validates the knowledge, skills, and behaviors that are required to determine common 50V, 300V, and 600V Battery Pack components, their function, and operation. 5 REASON Explain the reason of this Successful completion validates the knowledge, skills, and behaviors that are module. required to determine common 50V, 300V, and 600V Battery Pack components, their function, and operation. Caterpillar: Confidential Yellow SERVXXXX - 10/24 -6- Module 1 - Battery System Overview ASSESSMENT CRITERIA Knowledge Assessment Closed Book Minimum passing score of 80% 6 ASSESSMENT CRITERIA Explain the assessment criteria After the completion of this module, the participant must complete a knowledge for this module. assessment with a minimum passing score of 80%. Caterpillar: Confidential Yellow SERVXXXX - 10/24 -7- Module 1 - Battery System Overview LEARNING OUTCOMES After the completion of this module, the participant will be able to: Identify common battery pack components. Describe common battery pack component function. Explain common battery pack component operation. Explain BMS operation. 7 LEARNING OUTCOMES Explain the learning outcomes of After the completion of this module, the participant will be able to: this module. Identify common battery pack components. Describe the function of common battery pack components. Explain the operation of common battery pack components. Explain the operation of the Battery Management System (BMS). Caterpillar: Confidential Yellow SERVXXXX - 10/24 -8- Module 1 - Battery System Overview CAT BATTERY PACK OVERVIEW 2 4 1 3 8 CAT BATTERY PACK OVERVIEW Identify the main components of The 50V, 300V, and 600V Battery Packs consist of four main components: the battery packs. Multiple battery modules (1) that store electric charge A Power Electronics Module (PEM) (2) that directs Hazardous Voltage (HaV) into and out of the battery modules A BMS Electronic Control Module (ECM) (3) that monitors and controls the battery modules and PEM in the charging and discharging of DC voltage A Cat Product Link™ radio (4) that communicates BMS data to remote users This module will provide an overview of the function and operation of each of these components. Caterpillar: Confidential Yellow SERVXXXX - 10/24 -9- Module 1 - Battery System Overview BATTERY MODULE 2 1 3 4 9 BATTERY MODULE Identify the battery module The battery modules of the 50V, 300V, and 600V Battery Packs contain Li-ion connections. batteries. These batteries store and release electric charge to provide power to the HaV electrical systems of machines or other types of electrical equipment. Each battery module has a positive (DC+) terminal receptacle (1) and a negative (DC-) terminal receptacle (2) that connects it to the PEM. There are also a pair of data link connectors (3) that connect the battery module to the BMS ECM, and a pair of coolant ports (4) that are utilized when the battery module is connected to an active coolant system. Each battery module has a nominal voltage (Vnom) of around 50.7 VDC, and an electric charge of around 105.1 Ah. This means that each battery module contributes around 5.3 kWh of energy, which is calculated by multiplying the nominal voltage by the electric charge. NOTE: Some applications of the battery modules do not make use of the coolant ports. For such applications, the ports are covered by protective caps. Caterpillar: Confidential Yellow SERVXXXX - 10/24 -10- Module 1 - Battery System Overview BATTERY CELLS 1 10 BATTERY CELLS Identify the battery cell The battery modules of the 50V, 300V, and 600V Battery Packs contain 28 battery configuration. cells (1) that are arranged in a 14S2P configuration. The “14S” indicates that there are 14 battery cells connected in series, and the “2P” denotes that there are two such sets of 14 battery cells connected to one another in parallel. Each battery cell is a prismatic cell, which is wrapped in insulation to prevent heat transfer between cells. Each prismatic cell has a nominal voltage of 3.6 VDC and an electric charge of 52.5 Ah. Caterpillar: Confidential Yellow SERVXXXX - 10/24 -11- Module 1 - Battery System Overview BATTERY MODULE ARCHITECTURE 6 4 5 3 1 7 2 11 BATTERY MODULE ARCHITECTURE Identify the battery module The interior of the battery modules is designed to provide the battery cells with internal components. insulation from heat transfer. The battery cells rest upon a gap pad, have a layer of foam between them, and have mylar insulation at the front and rear ends of the module. The casing (1) that surrounds the battery cells consists of a base plate (2) that forms the bottom of the battery module. There are aluminum extrusions that are welded to the sides and center rib of the base plate. This also forms the cooling jacket for the battery cells within the casing. A BMS board (3) is bolted onto the front of the battery module casing, and a bus bar carrier assembly (4) consisting of a bus bar that is welded together onto a flex circuit is mounted to the top. The flex harness (5) of the bus bar carrier assembly is connected to the back of the BMS board. A lid (6), end plates (7), terminal insulators, and terminal receptacles are then added to form the outer casing of the battery module. NOTE: The components of a battery module, including the BMS board, are not serviceable. The battery module should not be disassembled. Caterpillar: Confidential Yellow SERVXXXX - 10/24 -12- Module 1 - Battery System Overview BATTERY MODULE CONFIGURATION 1 2 12 BATTERY MODULE CONFIGURATION Explain battery module When multiple battery modules are stacked on top of one another forming a column configuration. of battery modules, it is referred to as a battery rack (1). The number of battery modules that comprise a battery rack varies, depending on the application. A battery rack will either have its battery modules connect to one another in series or in parallel, depending on the application. Battery modules connected to one another in series are referred to as a battery string. 50V, 300V, and 600V Battery Packs have two battery racks positioned side-by-side with one another, with both battery racks facing the same direction. 50V, 300V, and 600V Battery Packs will have their two battery racks connect to one another either in series or in parallel, depending on the application. This is independent of how the battery racks have their modules connect to one another. Caterpillar: Confidential Yellow SERVXXXX - 10/24 -13- Module 1 - Battery System Overview BATTERY MODULE SAFETY 13 BATTERY MODULE SAFETY Explain battery module safety. There are two key safety considerations when servicing battery modules. A battery module discharges hazardous levels of voltage. This can pose an electrocution hazard when servicing a battery module. Always assume hazardous voltage is present when making contact with battery modules. Always make sure to use proper Personal Protective Equipment (PPE) and insulated tooling when making contact with battery modules. A battery module contains Li-ion batteries. If their temperature is not properly controlled, a thermal runaway can occur. In minor cases, it can cause the battery to melt or become damaged beyond repair. In extreme cases, the battery can explode and start a chemical fire. Once such a fire starts, it can be nearly impossible to extinguish. It is important to properly store and maintain battery modules such that the temperature of the battery cells is carefully controlled to minimize the risk of a thermal runaway. In the event of a chemical fire caused by thermal runaway, use fire extinguishers or other fire suppressants specifically approved to put out Li-ion battery fires. DO NOT use water to attempt to put out the fire; it will react violently with lithium and make the reaction even worse. Consult Special Instruction M0168725 “Battery Packaging Instructions and Catalog” for further information about proper storage and maintenance of 50V, 300V, and 600V Battery Packs. Caterpillar: Confidential Yellow SERVXXXX - 10/24 -14- Module 1 - Battery System Overview POWER ELECTRONICS MODULE (PEM) 4 1 2 1 3 3 2 4 4 3 1 2 14 POWER ELECTRONICS MODULE (PEM) Identify the PEM connections. The PEM houses the circuitry that manages the conversion, control, and monitoring of DC voltage throughout the battery pack. The PEM has one or more negative (DC-) battery terminals (1) and positive (DC+) battery terminals (2) that connect it to the battery modules. There are also two Power Electronics Module Interface Connectors (PEMICs) (3) that connect the PEM to the BMS ECM. The PEM also has one or more pairs of HaV terminals (4). Each pair of HaV terminals enables the PEM to connect to one or more of the following: A charging system of a machine or other type of electrical equipment The HaV electrical system of a machine or other type of electrical equipment An auxiliary component or device (e.g., cab heater, high-powered fans) The number of battery terminals and paired HaV terminals, as well as their location on the PEM, varies by application. Caterpillar: Confidential Yellow SERVXXXX - 10/24 -15- Module 1 - Battery System Overview PEM ARCHITECTURE 15 PEM ARCHITECTURE Identify the PEM internal There are several major components within the PEM that provide the means to components. monitor and control the flow of hazardous voltage into and out of the PEM. The PEM contains a circuit board. The circuit board features several key electrical and electronic components that contribute to the overall function of the PEM. Contactors (1) isolate different sections of the PEM from one another to control HaV flow when the battery modules are in a charging or discharging state. Fuses (2) prevent excess current from entering or leaving the PEM in a fault condition. Specialized sensors called IVT-S sensors (3) monitor the current (I), voltage (V), and/or temperature (T) entering the PEM from the battery modules. Bus bars connect the PEM to external sources or loads. Most bus bars are connected to terminal receptacles (4) mounted to the exterior of the PEM. These terminal receptacles are connected to source(s) or load(s) via HaV cables. Battery terminals inside the PEM connect it to the terminal receptacles of the battery modules via HaV cables. An interface board connects the BMS ECM to the electronics of the PEM by way of the two PEMICs. Caterpillar: Confidential Yellow SERVXXXX - 10/24 -16- Module 1 - Battery System Overview HAZARDOUS VOLTAGE (HAV) CABLES 5 4 2 1 3 1 5 2 4 16 HAZARDOUS VOLTAGE (HAV) CABLES Identify the HaV cable layers. The HaV cables of 50V, 300V, and 600V Battery Packs are a type of PowerLink HaV shielding cable. The conductor (1) of the HaV cable is a series of stranded bare copper wires. Surrounding the conductor is a cross-linked polyethylene (XLPE) Orange type insulation (2). Around the insulation is a polyethylene terephthalate (PET) mylar film (3). Atop the mylar film is a braiding shielding (4) that is made of tinned, annealed copper wire with aluminum-mylar tape. The braiding shielding is encased in a XLPE Orange jacket (5) sheath. Caterpillar: Confidential Yellow SERVXXXX - 10/24 -17- Module 1 - Battery System Overview HAZARDOUS VOLTAGE (HAV) CABLE PLUGS 2 1 2 1 3 3 17 HAZARDOUS VOLTAGE (HAV) CABLE PLUGS Explain how to connect and The HaV cables that connect to the battery modules have a specially designed disconnect the HaV cables with plug (1) that mates with the terminal receptacles (2) of the battery modules. plugs and receptacles. When disconnecting a HaV cable with a plug, press the button (3) on the upward- facing side of the plug, then pull out the plug directly as shown in the images above. Do not use a tool or other device to press the button or separate the plug from the terminal receptacle, as it may damage the button or plug. When connecting a HaV cable with a plug, push the plug directly into the terminal receptacle until a “click” is heard. This indicates the plug and terminal receptacle are mated. Pull the plug lightly by hand to confirm they are fully mated. When inserting a plug into the terminal receptacle, be careful to keep the plug correctly aligned. Incorrect alignment of the plug will result in damage to the plug and terminal receptacle. Caterpillar: Confidential Yellow SERVXXXX - 10/24 -18- Module 1 - Battery System Overview BATTERY MANAGEMENT SYSTEM (BMS) 2 1 18 BATTERY MANAGEMENT SYSTEM (BMS) Identify the main components of The battery modules and PEM have their components monitored and controlled by the BMS. an electronic control system called the BMS. The BMS consists of sensors and other electronic devices that monitor or control the battery modules and PEM by exchanging information between them and the BMS ECM (1) via data links. The main components of the BMS consist of the BMS ECM, a Cat Product Link radio (2), and the BMS boards (not shown) of each battery module. Caterpillar: Confidential Yellow SERVXXXX - 10/24 -19- Module 1 - Battery System Overview BMS CONNECTIONS 4 3 1 2 19 BMS CONNECTIONS Identify the BMS connections. The BMS has several key connection points that enable the BMS ECM to communicate with other components of the battery pack as well as an external electronic control system. The BMS has two PEMICs (1) that connect the BMS ECM to the interface board inside the PEM. This enables the BMS ECM to communicate with the electronic components of the PEM. The BMS also has multiple International Organization for Standardization Serial Peripheral Interface (ISO-SPI) data link connectors (2) that form a communication network consisting of the BMS ECM and the BMS boards of the battery modules. The Battery Interface Connector (BIC) (3) is a connection port that allows the BMS ECM to communicate with the ECM(s) of the electronic control system of the machine or other type of electrical equipment being supplied DC voltage by the battery system. There is also a radio interface connector (4) that enables the BMS ECM to communicate with the Cat Product Link radio. Caterpillar: Confidential Yellow SERVXXXX - 10/24 -20- Module 1 - Battery System Overview BMS ECM 3 2 1 20 BMS ECM Describe the functions of the The BMS ECM is an A6:B3 ECM. Its two main connection ports are a 70-pin J1 BMS ECM. connector (1) and 70-pin J2 connector (2). These have analog feedback and Controller Area Network (CAN) data link connections that connect the ECM to various electronic control system inputs (such as sensors) and outputs (such as contactors) that are found in the PEM. The BMS ECM also has eight ISO-SPI data link connectors (3). These are used to connect to the BMS boards of the battery modules. Of these eight data link connectors, only two are used for the BMS of the battery packs; the rest are capped. The BMS ECM is responsible for controlling the major functions of the battery pack. It has four key functions: Measurement: The BMS ECM uses sensors to measure the voltage, current, temperature, and battery module charge/discharge rates. Fault Detection: The BMS ECM uses system inputs to detect electrical issues (such as open circuits) and electronic issues (such as communication problems). State Estimation: The BMS ECM interprets data to determine the state of the battery modules. Protection: The BMS ECM ensures that temperature, voltage, current, and rate of charge/discharge remain within specifications. Caterpillar: Confidential Yellow SERVXXXX - 10/24 -21- Module 1 - Battery System Overview BATTERY MODULE STATE Battery Module State State of Health (SoH) - battery condition State of Charge (SoC) - available capacity State of Function (SoF) - available power 21 BATTERY MODULE STATE Explain battery module states. When determining the state of the battery modules, there are several key terms to consider. The battery modules’ State of Health (SoH) refers to how their condition has deteriorated compared to their nominal condition. Over time, the capacity of the battery cells within the battery modules will decrease, and their cell resistance will increase. The battery modules’ State of Charge (SoC) refers to how much of the battery module’s cell capacity is available. This is often expressed as a percentage of the module’s maximum cell capacity. As battery cells age, their maximum cell capacity will decrease, affecting the battery module’s maximum SoC. The battery modules’ State of Function (SoF) refers to how much power the battery modules are able to deliver or receive. Both the power and current of the battery modules need to be known in order to determine their SoF when either in a charging state or a discharging state. As battery cells age, their cell resistance will increase, affecting the cells’ ability to deliver or receive power, and lowering the modules’ SoF. One of the key functions of the BMS is to determine the SoC, SoH, and SoF of each battery module. Caterpillar: Confidential Yellow SERVXXXX - 10/24 -22- Module 1 - Battery System Overview BATTERY CAPACITY SOC % as shown on the Display 5% Buffer 100% 85% of Gross 64 54.4 Factory Shipping kWh kWh SOC 20 - 30% 10% 10% Buffer 0% Operator Alarm Total Capacity Usable Capacity Warnings & Derates (gross) (net) 22 BATTERY CAPACITY Explain battery capacity. When discussing a battery module’s SoC, it is important to make a distinction between two different types of battery capacity: total (gross) capacity and usable (net) capacity. Gross or total capacity refers to the total amount of energy a battery can theoretically hold. Net or usable capacity indicates the amount of energy a load can draw upon to operate. The battery modules of the 50V, 300V, and 600V Battery Packs are designed by their manufacturer to be able to make use of their battery cells’ net capacity only. This is done to optimize battery life. This design also serves to prevent the critical discharge of a battery cell (which renders its battery module inoperable or dramatically shortens its battery life) or the overcharge of a battery cell (which can result in a thermal runaway event). The manufacturer of Cat-branded battery modules has implemented a 10% buffer to the lower limit of the batteries’ gross capacity, and a 5% buffer to the upper limit of the batteries’ gross capacity. This means that the batteries have a net capacity that is 85% of their gross capacity. When a Cat 50V, 300V, or 600V Battery Pack is connected to a machine with a SoC display, it is the net capacity of the batteries that is being displayed. When the machine displays a SoC of 100%, for example, the batteries’ net capacity is at 100%, but its gross capacity is at 95%. Conversely, when the machine displays a SoC of 0%, the batteries’ net capacity is at 0%, but it still has a gross capacity of 10%. Caterpillar: Confidential Yellow SERVXXXX - 10/24 -23- Module 1 - Battery System Overview CAT PRODUCT LINK RADIO 1 23 CAT PRODUCT LINK RADIO Describe the information The Cat Product Link radio is a PL542V2 radio that communicates information transmitted by the Cat Product about the battery pack to remote users. Link radio. The PL542V2 radio has a 14-pin connector (1) that allows it to communicate electronically with the BMS ECM. The information transmitted may include the battery pack’s location and operational data. Such operational data may include: Fault codes Battery usage Service meter hours Software and hardware version numbers The transmitted information may be used for various purposes, such as: Providing services to the customer and/or the battery pack Checking or maintaining Cat Product Link radio Monitoring the health or performance of the battery pack Maintaining or improving the efficiency of the battery pack Evaluating or improving Cat products and services Caterpillar: Confidential Yellow SERVXXXX - 10/24 -24- Module 1 - Battery System Overview BMS BOARDS 2 1 3 24 BMS BOARDS Identify the BMS board Each battery module has a BMS board (1) that monitors and controls its battery connections. module. A BMS board uses Voltage Transducers (VTs) to monitor the voltage of the battery cells within its battery module. The BMS board has a flex harness connector (2) that connects it to the bus bar carrier assembly inside the battery module. This allows the BMS board to communicate with temperature sensors that monitor the battery cell temperature at key locations throughout the battery module. Each BMS board also has a pair of ISO-SPI data link connectors (3) for communicating battery cell voltage, temperature, balancing, and heating data to the BMS ECM. NOTE: The BMS board of a battery module is not serviceable. Caterpillar: Confidential Yellow SERVXXXX - 10/24 -25- Module 1 - Battery System Overview BMS OPERATION - INPUTS BMS Inputs Responses from Battery Modules Sensor Readings Contactor Position System Voltage Communications from Electronics 25 BMS OPERATION - INPUTS Explain the role of inputs in BMS The BMS operates by having the BMS ECM obtain inputs from the BMS boards of operation. the battery modules, the sensors and contactors of the PEM, and other sources. Input from the BMS boards of the battery modules include information about battery cell voltages, battery module temperature, data from BMS boards’ memory, and the results of diagnostic checks by the BMS boards. Input from sensors include readings from the IVT-S sensors of the PEM. The BMS ECM also receives input regarding the position of the PEM contactors and whether low voltage is being supplied to the BMS. The BMS ECM may also receive communication from the Cat Product Link radio or external electronic control systems. Caterpillar: Confidential Yellow SERVXXXX - 10/24 -26- Module 1 - Battery System Overview BMS OPERATION - OUTPUTS BMS Outputs Commands to BMS Boards Commands to PEM Contactors Communications to other Electronics 26 BMS OPERATION - OUTPUTS Explain the role of outputs in Once the BMS ECM processes the inputs provided to it, it may then issue BMS operation. command outputs to the other components of the BMS. The BMS ECM may issue commands to the BMS boards of the battery modules. These may include requesting information, activating a balancing resistor, writing information to BMS board memory, or performing a diagnostic check. Based on sensor information and/or the presence or absence of low voltage power supply, the PEM contactors may be commanded to open or close. The BMS ECM may also communicate data about the BMS to the Cat Product Link radio or external electronic control systems. Caterpillar: Confidential Yellow SERVXXXX - 10/24 -27- Module 1 - Battery System Overview PURPOSE This module covers the components that are common to the Cat 50V, 300V, and 600V Battery Packs. 27 PURPOSE Explain the purpose of this This module covers the components that are common to the Cat 50V, 300V, and module. 600V Battery Packs. Caterpillar: Confidential Yellow SERVXXXX - 10/24 -28- Module 1 - Battery System Overview REASON Successful completion validates the knowledge, skills, and behaviors that are required to determine common 50V, 300V, and 600V Battery Pack components, their function, and operation. 28 REASON Explain the reason of this Successful completion validates the knowledge, skills, and behaviors that are module. required to determine common 50V, 300V, and 600V Battery Pack components, their function, and operation. Caterpillar: Confidential Yellow SERVXXXX - 10/24 -29- Module 1 - Battery System Overview ASSESSMENT CRITERIA Knowledge Assessment Closed Book Minimum passing score of 80% 29 ASSESSMENT CRITERIA Explain the assessment criteria After the completion of this module, the participant must complete a knowledge for this module. assessment with a minimum passing score of 80%. Caterpillar: Confidential Yellow SERVXXXX - 10/24 -30- Module 1 - Battery System Overview LEARNING OUTCOMES After the completion of this module, the participant will be able to: Identify common battery pack components. Describe common battery pack component function. Explain common battery pack component operation. Explain BMS operation. 30 LEARNING OUTCOMES Explain the learning outcomes of After the completion of this module, the participant will be able to: this module. Identify common battery pack components. Describe the function of common battery pack components. Explain the operation of common battery pack components. Explain the operation of the Battery Management System (BMS). Caterpillar: Confidential Yellow SERVXXXX - 10/24 -31- Module 1 - Battery System Overview MODULE CONCLUSION 31 MODULE CONCLUSION Conclusion This concludes the 50V, 300V, 600V Battery Pack Overview module for the Cat Battery Packs course. When used in conjunction with the service manuals, the information in this module will enable the participant to determine common 50V, 300V, and 600V Battery Pack components, their function, and operation. For service recommendations, always refer to the Operation and Maintenance Manual (OMM), service manuals, and other related Cat service publications. Caterpillar: Confidential Yellow