B21MA0403 POM Unit 1 Notes PDF
Document Details
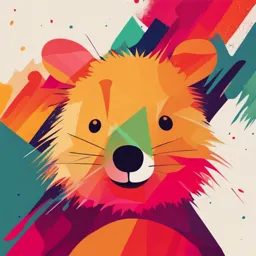
Uploaded by PromisedPipeOrgan
null
Tags
Summary
This document provides notes on production and operations management, covering topics like the historical evolution of production and operations management, and different types of production processes.
Full Transcript
UNIT 1 [ B21MA0403] Introduction to Production & Operations Management: Definition of Production and Operations. An overview of Manufacturing processes, Historical Evolution of Production and Operations Management, Concept of Production, Production System, Classification of Production System,...
UNIT 1 [ B21MA0403] Introduction to Production & Operations Management: Definition of Production and Operations. An overview of Manufacturing processes, Historical Evolution of Production and Operations Management, Concept of Production, Production System, Classification of Production System, Objectives of Production Management, Objectives of Operations Management, Managing Functions of Production, Planning & Control. Interface of Product Life Cycle & Process Life Cycle. Process design – Project, Job, Batch, Assembly and Continuous process. Historical Evolution of Production and Operations Management 1.Industrial Revolution: Industrial revolution has played an important role in shaping the manner, in which the goods are produced now. During the pre industrial revolution era, products were mostly hand-made by the persons having necessary expertise in their shops or homes. Each product was only one of its kind (unique) made in a meticulous manner by one person. However, in the year 1700, a revolutionary development took place in England, which changed the entire scenario in a holistic manner. This development is referred to as the Industrial Development Industrial revolution had two basic components, viz.: i) Large-scale replacement of human power with the machine power and water power, and The establishment of the factory system. The workers were brought together into factories on a large-scale, as a result of the growing need to organise them logically and scientifically with the objective of improving the productivity. ii) The significance and economic benefits arising out of the division of labour (also referred to as the specialisation of labour) was highlighted in Adam Smith's famous book The Wealth of Nations published in 1776. It envisaged the breaking up of the process of production into small but specialised tasks, which were entrusted to the workers along the production lines. iii) The factories set-up during late 1700s had the elements of planning. monitoring and controlling the work done by the factory workers along with the provisions of production machinery iv) The Industrial revolution had its origin the United Kingdom. where majority of the technological innovations took place The industrial revolution thereafter spread to other parts of European countries and the United States of America. v) Prior to the industrial revolution, each part used in the production process was exclusive or one of its kind it lacked inter-changeability, which meant that was of limited use However, in the year 1790, the concept of interchangeable-parts was introduced by Eli Whitney, which envisaged standardisation of parts so that each and every item in a batch fits equally. vi) It was a landmark development and its implication was that it became possible to move from one-at-a-time production to volume production Manufacturing of watches. clocks, and similar hems are good examples of interchangeable parts vii) Evolution of industrial revolution was taken forward in the year 1800 with the advent of the gasoline engine and electricity. This was followed by the emergence of new industries, simultaneously with the setting up of new factories. 2) Post-Civil War Period: In the middle of the 19th century, a new industrial period emerged in the United States. The post-civil war period (1865 1877) also known as the reconstruction period. provided necessary thrust to the large-scale growth potential of production capacity of various industries. Beginning of the modern type of organisations started in the form of joint stock companies which also coincided with the end of the Civil War This was a remarkable development, which led to the distinction between the capitalist and the employer, the managers became salaried employees of the financiers, who happened to be the owner of the capital Towards the end of 1990. The developments like enhanced capital and production capacity, burgeoning manpower in urban centres upcoming western markets, efficient transportation system at the national level, etc., created an environment most suitable for the great production outburst of the period 3) Scientific Management: The theory of Scientific Frederick Management was put forward by the renowned American mechanical engineer Winslow Taylor (1856-1915) (The focal point of his theory was machines and the system of their use. His theory was based on certain postulations. known as the Taylor's postulations, which simulates the following: i) Any kind of work is governed by the scientific laws, the scientific methods may be put to use for the proper analysis of the work. ii) Each worker performs with different ability their potential needs to be identified and matched with their jobs. iii) This may be followed by imparting appropriate training to them, so that their full potential can be utilised Self interest of an employee is the strongest motivational force; this may be used to encourage the employees for better performance, and iv) There should be segregation of responsibilities of workers and managers. Time and Motion Study : The time and motion study may be defined as a business efficiency technique. which analyses the combination of the Time Study work (Frederick Winslow Taylor) and the Motion Study work Frank and Lillian Gilbreth It is a systematic and sophisticated method, which takes into account the limits of human physical and mental capacity, and the importance of a good physical environment 4) Human Relations Movement: The manner in which managers of an organisation-interact with their employees is termed as Human Relations If the management is able to motivate its employees properly, the outcome is good and of better quality Such an organisation is said to have effective human relations. On the contrary. if the management fails to motivate its employees, and as a result their efficiency and morale decline. the organisation is said to have ineffective human relations. The history of human relations started with the contribution of Elton Mayo, FJ Roethlisberger, TN White-head and WJ Dickson at the Hawthorne, Illinois Then contribution is referred to as the Hawthorne studies, which were initially started by industrial engineers with the objective of determining the most suitable level of lighting in order to have the optimum production from workers. The outcome of these studies was confusing with regard to the relationship between physical environment and workers efficiency. which made the researchers realise the significance of the human factors. This was the first time that the researchers and managers were on the same scale regarding the fact that psychological and sociological factors affected not only human motivation and attitude but also the production. 5) Operations Research: Operations research is a branch of management which uses modern and sophisticated analytical methods to i) Facilitate better decision-making and Solving complex problems. This approach was developed in the year 1940 which has a quantitative perspective of efficient allocation, monitoring, and controlling of various scarce resources such as material, skilled workers, machines, money and time. Operations research is also viewed as a branch of mathematics, as it makes use of various techniques from other mathematical sciences, such as mathematical modelling, statistical analysis and mathematical optimisation, etc. The technique of Operations Research may be applied in areas such as supply chain management, marketing and revenue management systems, manufacturing plants. financial engineering. telecommunication networks. healthcare management, transportation networks, energy and environment, service systems, web commerce. 6) Service Revolution: Service sector started taking shape at the global level before the beginning of the World War II and gathered momentum after the Was came to an end The momentum, which continued to gain speed thereafter, is still growing a fast pace (This is true especially in the context of an Emerging Market Economy (EME) like India. Where the share of service sector (tertiary sector) in the GDP has shown an increasing trend year after year, in comparison with that of the agriculture sector primary sector) or industrial sector (secondary sector). The phenomenal growth of service sector has influenced the production management in a major way ( has posed such a challenge before the production managers that they are compelled to chalk-out strategies and actions so that the services areas are managed properly for the improvement productivity, quality and competitive edge, Services sector is expected to gain more significance in the future or coming time 7) Computer Revolution: Application of computers in business started way back in the year 1970 which grew at an enormous speed subsequently Computers proved to be a great help in the widespread use of various quantitative models, which were developed by the management science, Data processing became much smoother and hassle free in the areas like forecasting scheduling and inventory management of the organisations operations were greatly influenced by the computer hardware and software. Organisations dependence upon the computers continued to grow unabatedly Due to the availability of a wealth of information in abundance and easy access to more information, operations decisions became easy to make in a prompt manner Advancement in computer technologies and software applications has ensured fast and better decision making. Evolution and expansion in the field of communication technologies have empowered companies to manage their operations efficiently at the global level they are also able to work in a smooth way on the international projects by having uninterrupted communication with their globally placed team members E-mail has enabled employees, other colleagues, vendors, and customers to communicate with each other in a prompt and hassle free manner on a 24x7 basis All these developments have made the decision- making process fast and operational activities have improved. 8) Supply Chain Management: The next of the supply chain management lies in the application of the Total System Approach, which enters the management of the flow of information, materials and services from the suppliers there of through factories and warehouses to the end users. re. customers. Latest developments in this regard like outsourcing and mass customization are indicative of major drift in the trend which have compelled the companies to seek easy ways to fulfil customers expectations. They are concentrating on prompt and quick action (optimizing their core activities) on their part. response to the fast changing customers preferences. 9) Electronic Commerce : The advent of the internet and the World Wide Web (WWW) during the late 1990s is considered as the most notable development of the time with far- reaching impact. E-commerce denotes the use of intimate as the backbone of the business activity Genesis of the internet may be traced back to the US Government network called Advanced Research Projects Agency Network (ARPANET), which was created in 1969 by the defence department of US Government. The manner in which people access information shop and communicate undergoes changes accordingly with the use of web pages, forms, and interactive search engines. The internet has also brought about drastic changes in the way operations managers coordinate production and distribution processes and execute 10) Globalisation: Globalization may be defined as the process of international integration, which is associated with the exchange of world views, products, ideas and various facets of culture. It has resulted in phenomenal increase in the international trade The inclination towards healthy competitiveness between the business organizations as well as the nations has become a regular feature through better communications and trade agreements. PRODUCTION MANAGEMENT : According to Elwood S. Buffa, "Production management deals with decision- making related to production process so that the resulting goods or services are produced according to specifications in amounts and by the schedules demanded, and at a minimum cost". OPERATIONS MANAGEMENT : ✓ It is defined as the design, operation, and improvement of the transformation process, which converts the various inputs into the desired outputs of products and services. There is a growing need for the application of the principles of operations management in the service industry. ✓ Operations Management' is an inclusive term which comprises both manufacturing and services organizations. Operations management sheds light on the significance of the service industry in the prevailing business environment. ✓ It can be explained as process of designing, operating and improving the conversion process, which aids the transfiguration of different inputs into various products and services. In present situations, there is an urgent need for the application of operations management principles to the service industry. Concept of Production ✓ Production is defined as “the step-by-step conversion of one form of material into another form through chemical or mechanical process to create or enhance the utility of the product to the user.” Thus production is a value addition process. At each stage of processing, there will be value addition. ✓ Elwood S.Buffa defines production as „a process by which goods and services are created‟. ✓ Some examples of production are: manufacturing custom-made products like, boilers with a specific capacity, constructing flats, some structural fabrication works for selected customers, etc., and manufacturing standardized products like, car, bus, motor cycle, radio, television, etc. Production System The production system of an organization is that part, which produces products of an organization. It is that activity whereby resources, flowing within a defined system, are combined and transformed in a controlled manner to add value in accordance with the policies communicated by management. A simplified production system is shown above. The production system has the following characteristics: 1. Production is an organized activity, so every production system has an objective. 2. The system transforms the various inputs to useful outputs. 3. It does not operate in isolation from the other organization system. 4. There exists a feedback about the activities, which is essential to control and improve system performance. Classification of Production System / OVERVIEW OF MANUFACTURING PROCESS 1. Job Shop Production Job shop production are characterised by manufacturing of one or few quantity of products designed and produced as per the specification of customers within prefixed time and cost. The distinguishing feature of this is low volume and high variety of products. Characteristics The Job-shop production system is followed when there is: 1. High variety of products and low volume. 2. Use of general purpose machines and facilities. 3. Highly skilled operators who can take up each job as a challenge because of uniqueness. 4. Large inventory of materials, tools, parts. 5. Detailed planning is essential for sequencing the requirements of each product, capacities for each work centre and order priorities Advantages Following are the advantages of job shop production: 1. Because of general purpose machines and facilities variety of products can be produced. 2. Operators will become more skilled and competent, as each job gives them learning opportunities. 3. Full potential of operators can be utilized. 4. Opportunity exists for creative methods and innovative ideas. Limitations 1. Following are the limitations of job shop production: 2. Higher cost due to frequent set up changes. 3. Higher level of inventory at all levels and hence higher inventory cost. 4. Production planning is complicated. 5. Larger space requirements. 2. Batch Production Batch production is defined by American Production and Inventory Control Society (APICS) “as a form of manufacturing in which the job passes through the functional departments in lots or batches and each lot may have a different routing.” It is characterized by the manufacture of limited number of products produced at regular intervals and stocked awaiting sales. Characteristics Batch production system is used under the following circumstances: 1. When there is shorter production runs. 2. When plant and machinery are flexible. 3. When plant and machinery set up is used for the production of item in a batch and change of set up is required for processing the next batch. 4. When manufacturing lead time and cost are lower as compared to job order production. Advantages Following are the advantages of batch production: 1. Better utilization of plant and machinery. 2. Promotes functional specialization. 3. Cost per unit is lower as compared to job order production. 4. Lower investment in plant and machinery. 5. Flexibility to accommodate and process number of products. 6. Job satisfaction exists for operators. Limitations Following are the limitations of batch production: 1. Material handling is complex because of irregular and longer flows. 2. Production planning and control is complex. 3. Work in process inventory is higher compared to continuous production. 4. Higher set up costs due to frequent changes in set up. 3. Mass Production Manufacture of discrete parts or assemblies using a continuous process are called mass production. This production system is justified by very large volume of production. The machines are arranged in a line or product layout. Product and process standardization exists and all outputs follow the same path. Characteristics Mass production is used under the following circumstances: 1. Standardization of product and process sequence. 2. Dedicated special purpose machines having higher production capacities and output rates. 3. Large volume of products. 4. Shorter cycle time of production. 5. Lower in process inventory. 6. Perfectly balanced production lines. 7. Flow of materials, components and parts is continuous and without any back tracking. 8. Production planning and control is easy. 9. Material handling can be completely automatic. Advantages Following are the advantages of mass production: 1. Higher rate of production with reduced cycle time. 2. Higher capacity utilization due to line balancing. 3. Less skilled operators are required. 4. Low process inventory. 5. Manufacturing cost per unit is low. Limitations Following are the limitations of mass production: 1. Breakdown of one machine will stop an entire production line. 2. Line layout needs major change with the changes in the product design. 3. High investment in production facilities. 4. The cycle time is determined by the slowest operation. 4. Continuous Production Production facilities are arranged as per the sequence of production operations from the first operations to the finished product. The items are made to flow through the sequence of operations through material handling devices such as conveyors, transfer devices, etc. Characteristics Continuous production is used under the following circumstances: 1. Dedicated plant and equipment with zero flexibility. 2. Material handling is fully automated. 3. Process follows a predetermined sequence of operations. 4. Component materials cannot be readily identified with final product. 5. Planning and scheduling is a routine action. Advantages Following are the advantages of continuous production: 1. Standardization of product and process sequence. 2. Higher rate of production with reduced cycle time. 3. Higher capacity utilization due to line balancing. 4. Manpower is not required for material handling as it is completely automatic. 5. Person with limited skills can be used on the production line. 6. Unit cost is lower due to high volume of production. Limitations Following are the limitations of continuous production: 1. Flexibility to accommodate and process number of products does not exist. 2. Very high investment for setting flow lines. 3. Product differentiation is limited. OBJECTIVES OF PRODUCTION MANAGEMENT AND OPERATIONS MANAGEMENT Following are the main objectives of production and operations management: 1) Ultimate Objectives: The main function of the manufacturing activities is to produce goods and services with following qualities: i) Right Quality: The appropriate quality standard for a product is determined keeping in view the requirements of the customer. It may or may not be the best quality as the production management needs to keep costs and other technical features in mind as well. ii) Right Quantity: The production should be done in right quantity to ensure that there is no significant under or over production. In case of over production, the capital is unnecessarily tied up in inventories while in case of under production, the supply will not be enough to meet the demand. iii) Right Time: Another factor to determine the efficacy of production division is related to its ability to deliver the goods and services on timely basis. For this purpose, it is important to make optimal utilisation of resources. iv) Pre-Established Cost: The determination of manufacturing costs is done before the actual manufacturing is done. The firm should endeavour to stick to the predetermined costs and not have much variation. 2) Intermediate Objectives: Following are the main intermediate objectives: i) Machinery and Equipment: The main objectives in this regard are a) Procurement of machinery and apparatus and b) Utilization of machinery and equipment. There should be proper availability of machines. The efficiency of machines can be maintained or enhanced through proper maintenance, occupancy and repair. ii) Materials: This objective should be presented with regard to units, monetary units or space units. Costs should be enumerated on per unit basis. It should be endeavored to increase the inventory turnover rate for all kinds of inventory. iii) Manpower: Human resources are a vital input. For this purpose, proper attention must be paid to the process of selecting, placing, training ,compensating and utilizing manpower. The efficiency of these processes can be measured using safety measurements, employee turnover rate, absenteeism and industrial relations. IV) Manufacturing Services: Utilization of various inputs including materials, machines and manpower resources is determined by the provision of adequate and proper services. The appropriate aims should be fixed for maximum efficiency. FUNCTIONS OF PRODUCTION PLANNING AND CONTROL : Production Planning Functions Following are the main functions of the production planning and control: 1) Routing: ✓ It refers to the formation of path and developing of a sequence on the basis of which the manufacturing activities will take place. ✓ This sequence is pre-decided so that the manufacturing activities can take place without hassle Under routing, the movement path for both the materials and the components are pre-decided through different set of machines and the work stations till the time they are converted into the finished product. ✓ It comprises of seven different activities: i) Determining what to manufacture and purchase, ii) Determining the requirement of the material, iii) Determining the required operations and arranging them in a sequence iv) Determining lot sizes to be manufactured, v) Determining different discarded materials, vi) Determining costs associated in the production, and vii) Organizing different forms of production controlling. According to Spriegal and Lansburgh, "Routing includes the planning of where and by when work shall be done, the determination of path that work shall follow and necessary sequence of operations, it forms a ground work for most of the scheduling and dispatching functions of planning department". 2) Scheduling : ✓ It refers to assigning time slots to each of the activity that is present in the sequence of the operations. ✓ It assigns the starting time and the termination time for function and ensures that the overall task is completed within the designated time It may also be referred to as the time phase of the loading. For any operation, scheduling is the key to meet the delivery deadlines. According to Spriegal and Lansburgh, "Scheduling involves establishing the amount of work to be done and the time when each element of work will start or order of work". 3) Loading ✓ It means allotment of tasks to different machines depending on their capacity or load handling. ✓ It ensures that optimum load is allocated to each of the machine.After establishing the route, the next step is the allocation of the load to respective machines and the workstations. ✓ After multiplying allotted units with processing time for each of the unit, the total processing time for the machine can be calculated. This time calculated signifies the standard time within which the work is expected to be completed. ✓ This time is further added in the work that is planned for the machine. Finally, a chart is prepared representing the various jobs that a machine is handling. Poduction Control Functions The various production control functions are as follows: 1) Dispatching: ✓ The routing and scheduling function that is discussed above forms a part of documentation only. ✓ Actual production takes place at this stage Dispatching takes the responsibility of transforming what is documented in a written form into the practical form following the functions of routing and scheduling. According to James L. Landy, "The dispatching function involves the actual granting of permission to proceed according to plans already laid down. 2) Expediting/Follow-Up/Progressing: o Control is said to have been exercised when actual performance follows the same path as that of the budgeted performance. o In case the starting and the terminating times are duly met, there is no need to feel concerned about whether the commitments will meet the deadlines or not. o The machine is said to fully utilise its capacity if it is working on the directions laid down by the plans. 3) Inspection: ✓ It refers to the examination of a product, and verifying it for the quality control purposes and other such attributes. ✓ For controlling the product's quality, it is as important as any of the other techniques/Inspection compares the delivered results with the set- standards and can occur at three distinct stages: i) Before production commences, ii) During the production, and iii) After production terminates. PROCESS DESIGN : The transformation process which is used to convert inputs into desire outputs is known as process design. The process can be various types as shown in the below : 1. Continuous Process Design 2. Semi Continuous Process Design 3. Intermittent Process Design 4. Project Process Design 1. Continuous Process Design : As the name suggest it is Continuous in nature. The Set Up time for starting such process is usually very long and once they started they continue for a longer duration. The products produced by such process are highly standardised with almost no customization. Fox example : Plastic, Chemicals, ceria, Sugar. 2. Semi- continuous Process Design : They are assembly processes, which are repetitive in nature. They produce high volume of output and products produced have little variety. Examples are : Automobiles, electronic items etc. This process requires highly specialized machines, semi-skilled workforce. 3. Intermittent Process Design : It stops at regular intervals of time because the product requires processing on a variety of machines. The products made are of different varieties, thus the production will be slow compared to continuous and semi -continuous system. A) Job Shop: This process design can handle a larger variety of products than the batch process. The products maybe so different from each other and there processing requirements may be varied processes, on different machines in different sequence, and with different processing times. Example -Restaurant service B) Batch Process :. This process is adopted when batch or lots of items are to be produced using the same set of machines in the same sequence.The equipment used is same in all the cases with the same processing steps. Example- Bakery - Biscuits & Chocolate manufacturing. 4. Project process : Projects are processes that handle very complex and unique set of activities , which have to be completed in a limited span of time. For example : R&D projects, implementation of Specialized Software in an organization, construction plants, innovations for developing existing product.