Reciprocating Engine Principles PDF
Document Details
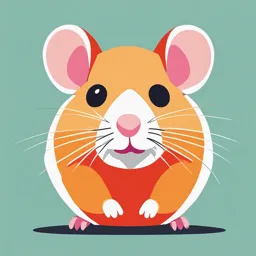
Uploaded by SnazzyDystopia5099
Fanshawe College, London, Ontario
AVIA
Tags
Summary
This document is an introduction to reciprocating engines, discussing their principles and design considerations within an aviation context. Topics include power and weight, fuel economy, and reliability, important aspects for aircraft.
Full Transcript
RECIPROCATING ENGINE Intro 1 Today Heat Engines Types of Engines and how they are classified 2 RECIPROCATING ENGINE - Intro Aircraft require thrust to produce enough speed for the wings to provide lift or enou...
RECIPROCATING ENGINE Intro 1 Today Heat Engines Types of Engines and how they are classified 2 RECIPROCATING ENGINE - Intro Aircraft require thrust to produce enough speed for the wings to provide lift or enough thrust to overcome the weight of the aircraft for vertical takeoff. 3 RECIPROCATING ENGINE - Intro For an aircraft to remain in level flight, thrust must be provided that is equal to and in the opposite direction of the aircraft drag. 4 RECIPROCATING ENGINE -Intro This thrust, or propulsive force, is provided by a suitable type of aircraft heat engine Reading: https://www.faa.gov/regulat ions_policies/handbooks_m anuals/aircraft/media/FAA- H-8083-32-AMT- Powerplant-Vol-1.pdf Chapter 1 5 RECIPROCATING ENGINE - All heat engines have one thing in common, the Intro ability to convert heat energy into mechanical energy. 6 This mechanical energy is used to form the propulsive force RECIPROCATING ENGINE - by the displacement of a working fluid (atmospheric air) Intro By displacing air opposite to the direction the aircraft is propelled, thrust can be developed 7 RECIPROCATING ENGINE -Intro In all cases, the heat energy is released at a point in the cycle where the working pressure is high relative to atmospheric pressure RECIPROCATING ENGINE -Intro Principles of operation of heat engines In thermodynamics, a heat engine is a system that performs the conversion of heat or thermal energy to mechanical work Examples – steam engine – diesel engine – gasoline engine – drinking bird toy – https://www.youtube.com/watch?v=UC KC-QVcVn0&ab_channel=engineerguy – Stirling engine RECIPROCATING ENGINE -Intro Types of Internal combustion engines Reciprocating Engines 2 Stroke Engines 4 Stroke Engines Rotary Engines Wankel Engines Gas Turbine Engines Jet Engine Fan Engines https://www.youtube.com/watch?v=gIdXLMVP6VU http://www.animatedengines.com 10 RECIPROCATING ENGINE PRINCIPLES Design Considerations AVIA-1065 11 Design Considerations General Requirements What do we need for the wings to produce lift? Forward movement How do we get forward movement? Thrust Aircraft require thrust to produce enough speed for the wings to provide lift, overcome the weight of the aircraft for vertical takeoff Must be equal to and in the opposite direction of the aircraft drag for an aircraft to remain in level flight, this thrust or propulsive force is provided by a suitable type of aircraft heat engine Design Considerations General Requirements All heat engines have in common the ability to convert heat energy into mechanical energy In the case of aircraft engines Fuel + air + spark = combustion Combustion is used to move a piston Piston moves a crankshaft Crankshaft moves a propeller Design Considerations General Requirements Thrust can be developed by displacing air in a direction opposite to that in which the aircraft is propelled this is an application of Newton’s third law of motion- it states that for every action there is an equal and opposite reaction the aircraft is moved forward as air is being displaced to the rear of the aircraft by this principle Design Considerations General Requirements A rocket: Carries its own oxidizer rather than using ambient air for combustion Discharges the gaseous byproducts of combustion through the exhaust nozzle at an extremely high velocity (action) is propelled in the other direction (reaction) how do rockets work in space 15 General Requirements Design Considerations The propellers of aircraft powered by either reciprocating engines or turboprop engines accelerate a large mass of air at a relatively lower velocity by turning a propeller – the air used for the propulsive force is a different quantity of air than that used within the engine to produce the mechanical energy to turn the propeller – the same amount of thrust can be generated by accelerating a small mass of air to a very high velocity 16 Design Considerations General Requirements Small general aviation aircraft use mostly horizontally opposed reciprocating piston engines 17 Design Considerations General Requirements Some aircraft still use radial reciprocating piston engines Their use is limited Crop dusting/spraying aircraft Vintage aircraft Other heat engines consist of gas turbine engines: Turboprop, turbojet, turboshaft and turbofan engine Wright R-3350 Duplex-Cyclone 18 Design Considerations General Requirements What are some requirement that the design of an aircraft engine would need? All aircraft engines must meet certain general requirements of: – efficiency – economy – reliability – being as compact as possible – being as vibration free as possible – being able to cover a wide range of power output General Requirements All aircraft engines must meet certain general requirements of: Efficiency Efficiency means: low weight- to-horsepower ratio Economy – in fuel consumption – Both in the cost of original procurement (to make it) and to maintain it Reliability – capable of sustained high- power output with no sacrifice in reliability – have the durability to operate Design Considerations for long periods of time between overhauls (TBO) 20 Design Considerations General Requirements All aircraft engines must meet certain general requirements of: being as compact as possible, yet having easy accessibility for maintenance being as vibration free as possible – having a system of damping units – to dampen out the vibrations of the engine when it is operating being able to cover a wide range of power output – at various speeds and altitudes Design Considerations Additional Design Requirements Engines need an oil system – delivers oil under the proper pressure to all of the operating parts of the engine – when it is running to lubricate and cool Engines need an ignition system – that deliver the firing impulse to the spark plugs at the proper time in all kinds of weather under other adverse conditions Engines need a fuel delivery system – provide metered fuel at the correct proportion of fuel/air ingested by the engine regardless of: the attitude the altitude the type of weather 22 Design Considerations Power and Weight Thrust is the useful output of all aircraft powerplants or the force which propels the aircraft gas turbine engine is rated in thrust horsepower (thp) reciprocating engine is rated in brake horsepower (bhp) the formula for Power= Force x distance Time Consequently, if a 33,000-lb weight is lifted through a vertical distance of 1 foot in 1 minute, the power expended is 33,000 ft-lb per minute, or exactly 1 hp 23 Design Considerations Power and Weight the aircraft engine operates at a relatively high percentage of its maximum power output throughout its service life the aircraft engine is at full power output whenever a takeoff is made it may hold this power for a period of time up to the limits set by the manufacturer the engine is seldom held at a maximum power for more than 2 minutes 24 Power and Weight Once take off is achieved, the power is reduced to a setting for climbing that can be maintained for longer periods of time The power of the engine(s) is further reduced to a cruise power which can be maintained for the duration of the flight after the aircraft has climbed to cruising altitude Design Considerations Design Considerations Power and Weight If the weight of an engine per brake horsepower (called the specific weight of the engine) is decreased: – the useful load that an aircraft can carry, and the performance of the aircraft obviously are increased – every excess pound of weight carried by an aircraft engine reduces its performance Tremendous improvement in reducing the weight of the aircraft engine is achieved through improved design and metallurgy This has resulted in reciprocating engines with an improved power-to-weight ratio (specific weight) 26 Design Considerations Fuel Economy specific fuel consumption usually, the basic parameter for describing the fuel economy of aircraft engines Fuel to Horsepower - the fuel flow is measured in (lb/hr) divided by thrust horsepower for gas turbines called thrust-specific fuel consumption The fuel flow (lb/hr) divided by brake horsepower for reciprocating engines called brake specific fuel consumption 27 Design Considerations Durability and Reliability Usually considered identical factors since it is difficult to mention one without including the other built into the engine by the manufacturer Reliability An aircraft engine is reliable when it can perform at the specified ratings – in widely varying flight attitudes – in extreme weather conditions 28 Design Considerations Durability and Reliability Standards of powerplant reliability are agreed upon by the Federal Aviation Administration (FAA) and the airframe manufacturer the engine manufacturer ensures the reliability of the product by: Design-close control of manufacturing and assembly procedures is maintained research Testing-each engine is tested before it leaves the factory The continued reliability of the engine is determined by – the maintenance – the overhaul – the operating personnel 29 Design Considerations Durability and Reliability Durability The amount of engine life obtained – while maintaining the desired reliability – the fact that an engine has successfully completed its type or proof test indicates that it can be operated in a normal manner over a long period before requiring overhaul 30 Design Considerations Durability and Reliability No definite time interval between overhauls is specified or implied in the engine rating The time between overhauls (TBO) varies with the operating conditions, engine temperatures amount of time the engine is operated at high-power settings the maintenance received Who determines TBO?? Recommended TBOs are specified by the engine manufacturer 31 Design Considerations Durability and Reliability The following make engine failure a rare occurrence careful maintenance and overhaul methods thorough periodical and preflight inspections strict observance of the operating limits established by the engine manufacturer 32 PISTON ENGINE CLASSIFICATION TERMINOLOGY Types of Engines AVIA-1065 33 Types of Engines Types of Engines Aircraft engines can be classified by several methods operating cycles cylinder arrangement the method of thrust production Most of the current aircraft engines are of the internal combustion type because the combustion process takes place inside the engine 34 Types of Engines Types of Engines Aircraft engines come in many different types such as gas turbine reciprocating piston rotary two or four cycle spark ignition diesel air cooled water cooled 35 Types of Engines Types of Engines Reciprocating piston – manufacturers have developed some designs that are used more commonly than others – They may be classified according to the cylinder arrangement – In line – V-type – Radial – Opposed Types of Engines Reciprocating piston may be classified according to the method of cooling air cooled All piston engines are cooled by transferring excess heat to the surrounding air (eventually) This heat transfer is direct from the cylinders to the air It is necessary to provide thin metal fins on the cylinders of an air-cooled engine in order to have increased surface for sufficient heat transfer 37 Types of Engines Types of Engines The method of cooling-liquid cooled a few high-powered engines use an efficient liquid-cooling system 38 Types of Engines Types of Engines-Inline 39 Inline Engines generally, have an even number of cylinders, some three-cylinder engines have been constructed may be either liquid cooled or air cooled have only one crank shaft which is located either above or below the cylinders called an inverted engine with the cylinders below the crankshaft offers the added advantages of: a shorter landing gear greater pilot visibility have small frontal areas better adapted to streamlining Types of Engines 40 Types of Engines Inline Engines offers additional problems such as poor cooling of aft cylinders – for the air cooled, inline type – worse with increase in engine size – is confined to low- and medium- horsepower engines – used in very old light aircraft long crankshaft prone to twisting 41 Types of Engines V-type 42 Types of Engines V-type Engines the cylinders are arranged in two in-line banks generally set 60° apart most of the engines have 12 cylinders which are either liquid cooled (most common) air cooled the engines are designated by a V followed by a dash, then the piston displacement in cubic inches for example, V-1710 was used mostly during the second World War mostly limited to older aircraft 43 Types of Engines Radial 44 Types of Engines Radial Engine consists of a row, or rows, of cylinders arranged radially about a central crankcase the number of cylinders which make up a row may be Three, five, seven, nine the single-row, nine-cylinder radial engine is of relatively simple construction having a one- piece nose, a two-section main crankcase 45 Types of Engines Radial Engine the larger twin-row engines are of slightly more complex construction than the single row engines Pratt and Whitney engines of comparable size incorporate the same basic sections, although the construction and the nomenclature differ considerably some have two rows of seven or nine cylinders arranged radially about the crankcase, one in front of the other called doublerow radials one type has four rows of cylinders with seven cylinders in each row for a total of 28 cylinders 46 Types of Engines General characteristics Type: 28-cylinder supercharged air-cooled four-row radial engine Bore: 5.75 inches (146 mm). Stroke: 6.00 inches (152 mm). Displacement: 4,362.5 cubic inches (71,489 cm3). Length: 96.5 inches (2,450 mm). Diameter: 55 inches (1,400 mm). Dry weight: 3,870 pounds (1,760 kg). Components Supercharger: Gear-driven single stage variable speed centrifugal type supercharger Turbocharger: General Electric CHM-2 Pratt & Whitney R-4360 Wasp Major Fuel type: 115/145 Aviation gasoline Cooling system: Air-cooled Performance Power output: 4,300 hp (3.2 MW) Compression ratio: 6.7 : 1 Power-to-weight ratio: 1.11 hp/lb (1.83 kW/kg) 47 Types of Engines Radial Engine 48 Types of Engines Radial Engine proven to be very rugged and dependable still used in some older cargo planes, war birds, crop spray planes Their use is limited although many of these engines still exist 49 Rotary Engines early type of internal-combustion engine odd number of cylinders per row the crankshaft remained stationary Types of Engines entire cylinder block rotated The rotating mass of the engine had a significant gyroscopic precession – depending on the type of aircraft – this produced stability control problems – fundamentally inefficient use of fuel and lubricating oil 50 Types of Engines Rotary Engines very high fuel consumption because the engine was typically run at full throttle also the valve timing was often less than ideal oil consumption was also very high due to primitive carburetion lubricating oil was added to the fuel/air mixture made engine fumes heavy with smoke from partially burnt oil Castor oil was the lubricant of choice unfortunate side-effect was that World War I pilots inhaled and swallowed a considerable amount of the oil during flight leading to persistent diarrhea flying clothing worn by rotary engine pilots was routinely soaked with oil. https://youtu.be/WfEEmdz7-Fk 51 Types of Engines Types of Engines - Opposed 52 Types of Engines Opposed or O-type engine has two banks of cylinders directly opposite each other with a crankshaft in the center the pistons of both cylinder banks are connected to the single crankshaft can be either liquid cooled or air cooled-the air-cooled version is used predominantly in aviation generally mounted with the cylinders in a horizontal position has a low weight-to-horsepower ratio its narrow silhouette makes it ideal for horizontal installation on the aircraft wings in twin engine applications another advantage is its low vibration characteristics 53 RECIPROCATING ENGINE PRINCIPLES Design and Construction AVIA-1065 54 Design and Construction Design and Construction the basic major components of a reciprocating engine are: crankcase cylinders pistons connecting rods valves valve-operating mechanism crankshaft 55 Design and Construction Design and Construction Figure 1-4 illustrates the basic parts of a reciprocating engine 56 Design and Construction Crankcase Sections The foundation of an engine is the crankcase it contains: the bearings the bearing supports in which the crankshaft revolves 57 The crankcase must: provide a tight enclosure for the lubricating oil Support various external and internal mechanisms attachment of the cylinder assemblies the powerplant to the aircraft Design and Construction Crankcase Sections 58 Crankcase Sections the crankcase must: – be sufficiently rigid and strong to prevent misalignment of the crankshaft and its bearings – have sufficient stiffness to withstand these bending moments without major deflections – [Figure 1-5] Design and Construction 59 Design and Construction Crankcase Sections cast or forged aluminum alloy is generally used for crankcase construction because it is light and strong the crankcase is subjected to many variations of mechanical loads and other forces the tremendous forces placed on the cylinder tend to pull the cylinder off the crankcase the unbalanced centrifugal and inertia forces of the crankshaft acting through the main bearings subject the crankcase to bending There are moments which change continuously in direction and magnitude Design and Construction Crankcase Sections the front or drive end is subjected to additional forces if the engine is equipped with a propeller reduction gear, there are severe centrifugal forces a large centrifugal bearing is used in the nose section to absorb centrifugal loads gyroscopic forces-particularly severe when a heavy propeller is installed in addition to the thrust forces developed by the propeller under high power output Design and Construction Crankcase Sections the shape of the nose or front of the crankcase section varies considerably it is either tapered or round in general used quite frequently on direct-drive, low-powered engines because extra space is not required to house the propeller reduction gears the nose or front area of the crankcase varies somewhat depending upon the type of reciprocating engine less area is needed for the crankcase if the propeller is driven directly by the crankshaft the crankcases used on engines having opposed or inline cylinder arrangements vary in form for the different types of engines they are approximately “cylindrical” Design and Construction Crankcase Sections one or more sides are surfaced to serve as a base to which the cylinders are attached by means of: cap screws bolts Studs these accurately machined surfaces are frequently referred to as cylinder pads provided with a suitable means of retaining or fastening the cylinders to the crankcase the general practice is to mount studs in threaded holes in the crankcase – the inner portion of the cylinder pads are sometimes chamfered or tapered to permit the installation of a large rubber O-ring around the cylinder skirt – This seals the joint between the cylinder and the crankcase pads against oil leakage Design and Construction Crankcase Sections cylinder Pads 64 Crankcase Sections the cylinder skirts extend a considerable distance into the crankcase sections to reduce the flow of oil into the inverted cylinders because oil is thrown about the crankcase – especially on inverted inline and radial-type Design and engines – the piston and ring assemblies must be Construction arranged so that they throw out the oil splashed directly into them 65 Design and Construction Crankcase Sections mounting lugs are spaced about the periphery of the rear or bottom of the crankcase or the diffuser section of a radial engine these are used to attach the engine assembly to the engine mount The engine mount is the framework provided for attaching the powerplant to the fuselage of single- engine aircraft Or to the wing nacelle structure of multiengine aircraft the mounting lugs may be either Integral with the crankcase diffuser section or detachable as in the case of flexible or dynamic engine mounts Design and Construction Crankcase Sections 67 Crankcase Sections the mounting arrangement supports the entire powerplant including the propeller therefore designed to provide ample strength for rapid maneuvers and other loadings Design and Construction 68 Design and Construction Crankcase Sections the intake pipes which carry the mixture from the diffuser chamber through the intake valve ports are arranged to provide a slip joint slip joint must be leak proof because of the elongation and contraction of the cylinders Must have considerable length on some radial engines, flexibility of the intake pipe or its arrangement eliminates the need for a slip joint at right angles to the cylinders on some inline engines, flexibility of the intake pipe or its arrangement eliminates the need for a slip joint the engine induction system must be arranged so that it does not leak air and change the desired fuel/air ratio Accessory Section The back of the engine Design and Construction Typically made of cast construction, the material may be either aluminum alloy (used most widely) magnesium (has been used to some extent) on some engines it is cast in one piece it is provided with means for mounting the accessories in the various locations required to facilitate accessibility such as: – magnetos – Fuel pump – Oil pump – vacuum pumps – starter – Generator/alternator – tachometer drive 70 Accessory Section Design and Construction accessory drive shafts are mounted in suitable drive arrangements that are carried out to the accessory mounting pads the various gear ratios can be arranged to give the proper drive speed to: – magnetos – pumps – other accessories to obtain correct: – timing – functioning 71 Accessory Gear Trains used in the different types of engines for driving engine components and accessories Contains both: spur-type gears-generally used to drive: – the heavier loaded accessories – those requiring the least play or backlash in the gear train bevel-type gears – permit angular location of short stub shafts leading to the various accessory mounting pads – usually simple arrangements on opposed, reciprocating engines – many of these engines use simple Design and Construction gear trains to drive the engine’s accessories at the proper speeds 72