Powerplant 1 - AEE 654 - Reciprocating Engines PDF
Document Details
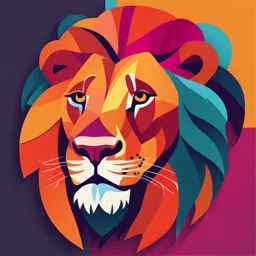
Uploaded by CompatibleWormhole4473
WCC Aeronautical and Technological College - North Manila
Tags
Summary
This document is an excerpt from a powerplant textbook, covering various aspects of reciprocating engine systems, including induction, fuel, cooling, and ignition. It details the different components of these systems and how they function.
Full Transcript
POWERPLANT 1 – AEE 654 SYSTEMS OF RECIPROCATING ENGINES Induction Systems Fuel system Lubrication Systems Ignition Systems Cooling Systems INDUCTION SYSTEMS o TURBOCHARGER – The turbocharger incorporates a turbine, which is driven by exhaust gases, and a...
POWERPLANT 1 – AEE 654 SYSTEMS OF RECIPROCATING ENGINES Induction Systems Fuel system Lubrication Systems Ignition Systems Cooling Systems INDUCTION SYSTEMS o TURBOCHARGER – The turbocharger incorporates a turbine, which is driven by exhaust gases, and a compressor that pressurizes the incoming air. o THROTTLE BODY – This regulates airflow to the engine. o INTAKE MANIFOLD – Pressurized air from the turbocharger is supplied to the cylinders. o WASTE GATE – This controls the amount of exhaust through the turbine. Waste gate position is actuated by engine oil pressure. o AIR INTAKE – Intake air is ducted to the turbocharger where it is compressed. o EXHAUST MANIFOLD – Exhaust gas is ducted through the exhaust manifold and is used to turn the turbine which drives the compressor. o EXHAUST GAS DISCHARGE INDUCTION SYSTEMS POWERPLANT 1 – AEE 654 Induction system – The primary purpose of an induction system in a reciprocating engine is to provide a sufficient quantity of air to support normal combustion. AIR INTAKE – collects ambient air from outside of the aircraft. To take maximum advantage of ram air pressure, the location of an intake is typically found in the propeller slipstream. INDUCTION AIR FILTER – Induction filters are typically installed to prevent dust, sand, abrasive materials, and other contaminants from entering the engine. FLOCK – AIR filters that were constructed from screen wire that was filled with a reusable fiber material. FUEL METERING SYSTEM – The fuel delivery system on a normally aspirated engine is either a carburetor or fuel injection system. INDUCTION MANIFOLD – horizontally opposed engine, the intake manifold provides the connecting point of all the individual pipes that deliver air to the cylinders. ICING OCCURS WHEN aircraft flies at high altitudes where temperature, pressure and density drops. ICING may cause lose of power (low RPM) and poor engine performance. 3 TYPES OF ICING: 1. FUEL EVAPORATION ICE – Fuel evaporation ice, sometimes referred to as carburetor ice, is a result of the temperature drop that occurs when fuel is vaporized. 2. THROTTLE ICE – Throttle ice forms on the downstream side of a throttle, or butterfly valve, when it is in a partially closed position. 3. IMPACT ICE – caused by visible moisture striking an aircraft and then freezing. The air intake and air filter are the area’s most susceptible to impact icing. INDUCTION SYSTEMS POWERPLANT 1 – AEE 654 ICE DETECTION AND REMOVAL the first indication of icing is a decrease in engine power. However, for CONSTANT SPEED PROPELLERS the first indication of induction ice is a decrease in manifold pressure with no change in engine speed. CARBURETOR HEAT SYSTEM - is designed to overcome icing in the induction system. It uses the heat of exhaust pipe or HEATER MUFF to heat the air coming in and supply it to the carburetor. the carburetor heat control should be left in the "COLD" position when starting an engine. If the heat control is placed in the "hot" position, damage to a carburetor heat air box could result if the engine backfires. o FUEL/AIR MIXTURE – The blend of fuel and air is routed to the combustion chambers to be burned. o THROTTLE VALVE – The flow of the fuel/air mixture is controlled by the throttle valve. The throttle valve is adjusted from the flight deck by the throttle o VENTURI - The shape of the venturi creates an area of low pressure. o DISCHARGE NOZZLE – Fuel is forced through the discharge nozzle into the venturi by greater atmospheric pressure in the float chamber. o AIR INLET – Air enters the carburetor through the air inlet. o AIR BLEED – The air bleed allows air to be mixed with fuel being drawn out of the dis- charge nozzle to decrease fuel density and promote fuel vaporization o FLOAT CHAMBER – Fuel level is maintained by a float-type device. o FUEL INLET – Fuel is received into the carburetor through the fuel inlet o FUEL o MIXTURE NEEDLE – The mixture needle controls fuel to the discharge nozzle. Mixture needle position can be adjusted using the mixture control. INDUCTION SYSTEMS POWERPLANT 1 – AEE 654 IMPACTS OF HEATER MUFF SYSTEM improper or careless use OF THIS HEAT SYSTEM can damage an engine. unfiltered, excessive use increases the chance of dirt and foreign material entering the engine. A reduction in volumetric efficiency causes a noticeable loss in power. Furthermore, high intake air temperatures that result from using carburetor heat can lead to DETONATION, especially during takeoff or other highpower operations. DETONATION – the fuel/air charge (or pockets within the charge) explodes rather than burning smoothly. Because of this explosion, the charge exerts a much higher force on the piston and cylinder, leading to increased noise, vibration, and cylinder head temperatures. ALCOHOL DE-ICING SYSTEM – Another system IS used to eliminate induction icing works by spraying a deicing fluid (ALCOHOL) into the air stream ahead of the carburetor. It was usually placed ahead of the carburetor. Density affects evaporation HIGHER density fluid has lower rate of evaporation. LOWER density fluid has higher rate of evaporation. TYPES OF INDUCTION SYSTEM INDUCTION SYSTEMS POWERPLANT 1 – AEE 654 SUPERCHARGED INDUCTION SYSTEMS SUPERCHARGER – is an engine-driven air pump that increases manifold pressure. The higher the manifold pressure, the denser the fuel/air mixture is and the more power the engine can produce. And also INCREASING VOLUMETRIC EFFICIENCY. Compresses fuel-air mixture. Directly connected to CRANKSHAFT. Some power created is OFFSET (diminishes) by the power required to drive the supercharger. The temperature is limited to a level to avoid DETONATION. Main advantage – improved performance at altitude MORE POWER FOR TAKE-OFF. Easy to RESPOND. Main Disadvantage – POWER gain is offset resulting for LESS EFFICIENCY, INCREASES risk for detonation. TURBO CHARGER INDUCTION SYSTEM TURBOCHARGER – are powered by engine exhaust. In other words, a turbocharger recovers energy from a source that would otherwise be lost. TURBOCHARGERS are driven by turbine which uses exhaust gas to drive the compressor Only COMPRESSES INTAKE AIR and supplies it to the cylinders. The charged engine will maintain sea level performance to higher altitudes Advantages – uses recovered energy to do work thus having MORE EFFICIENCY. Disadvantage – Needs more time to produce power. TURBO LAG TURBOCHARGER CONTROL SYSTEMS MANUAL CONTROL SYSTEM – Simplest form mechanical linkage between the engine throttle valve and the wastegate valve. Critical altitude is defined as the maximum altitude that a turbocharged engine can produce its rated horsepower under sea-level. SEA LEVEL-BOOSTED ENGINES – turbocharger systems that are designed to maintain sea level engine performance from sea level up to their critical altitude. INDUCTION SYSTEMS POWERPLANT 1 – AEE 654 AUTOMATIC CONTROL SYSTEM WASTEGATE ACTUATOR – Automatic control system. the wastegate is held open by spring pressure and closed by oil pressure that acts on a piston. ABSOLUTE PRESSURE CONTROLLER – A type of turbo charger that LIMITS maximum discharge pressure the turbochargers. upper deck pressure - the absolute pressure of the air before it enters the fuel metering device. PRESSURE-RATIO CONTROLLER – The pressure-ratio controller monitors both the ambient and upper deck pressures to prevent the turbocharger from boosting upper deck pressure more than 2.2 times the ambient pressure. RATE-OF-CHANGE CONTROLLER – controller to prevent the upper deck pressure from increasing too rapidly. Under normal conditions, the rate-of-change controller remains seated. EXHAUST BYPASS VALVE ASSEMBLY – similar to the wastegate actuator, amount of oil pressure acting on the exhaust bypass valve assembly is controlled by the density controller and differential pressure controller. DIFFERENTIAL PRESSURE CONTROLLER – The differential pressure controller monitors the pressure differential, or drop, across the throttle body. DENSITY CONTROLLER – regulates the bleed oil flow from the exhaust bypass valve assembly only during full throttle operation. POWERPLANT 1 – AEE 654 POWERPLANT 1 – AEE 654 COOLING SYSTEMS TYPES OF COOLING SYSTEM 1. AIR COOLING 2. LIQUID COOLING 1. AIR COOLING – Means of cooling by using ambient air to decrease the temperature of a working engine. ▪ COOLING FINS o The fins increase surface area to transfer heat to the surrounding airflow. o Fins provide additional surface area to transfer heat to the engine oil. ▪ COWLING – A part of Engine or Fuselage that house the engine and acts as a metal cover around it. PRESSURE COOLING – Happens because of RAM EFFECT, cooling air enters cowling with the pressure above ambient. RAM EFFECT – works by reducing the intake air velocity by increasing the cross-sectional area of the intake ducting. INCREASING STATIC PRESSURE. ▪ BAFFLES AND DEFLECTORS o baffles and deflectors are installed to maximize effectiveness of the airflow. o Baffles and deflectors block and redirect airflow to provide effective cooling. o Baffles and deflectors are installed between the cowling and engine, as well as between the engine cylinders. ▪ COWL FLAPS – Installed to control the amount of cooling air. Full open means more air into the cylinder. During ground operations, cowl flaps are typically in their full open position for maximum cooling. COOLING SYSTEMS POWERPLANT 1 – AEE 654 ▪ AUGMENTOR SYSTEMS – An augmenter routes the exhaust gases from the engine into a collector that discharges them into the inlet of a stainless-steel augmenter tube. ▪ BLAST TUBES – A blast tube is a small pipe, or duct, that channels air from the main cooling airstream onto heat- sensitive components and accessories. (Such as magnetos, alternators, and generators). INTEGRAL PART OF THE BAFFLE STRUCTURE. 2. LIQUID COOLING – A type of cooling that uses liquid coolant (anti-freeze and water) to reduce the temperature of the engine. COOLANT – A mixture of ANTI-FREEZE (Usually ETHYLENE GLYCOL) and WATER. ADVANTAGES OF LIQUID COOLING It can get the engine up to optimum operating temperature as quickly as possible and maintain it. Control the heat produce by combustion chamber so that engine parts are not damaged and oil does not break down. MAIN DISADVANTAGE More weight complicated installation not applicable in all parts of engine. ▪ WATER PUMP – The heart of the engine liquid cooling. Has a RADIAL IMPELLER and it is driven by the engine itself. ▪ RADIATOR – cools the hot coolant coming from the engine then supplying the cooled coolant to the engine back. ▪ THERMOSTAT – Acts as a valve for coolant where it allows flow to radiator only when the coolant reach a certain temperature where. ▪ RUBBER HOSE – The connection between water pump radiator and the engine. ▪ WATER JACKET – Open spaces between the outside of cylinder and inside of the cylinder block and head. NOTE THAT when engine is running normal the coolant is forced through inside of water jacket. POWERPLANT 1 – AEE 654 POWERPLANT 1 – AEE 654 FUEL SYSTEMS Fuel Systems – main job is to supply sufficient fuel into the cylinder TYPES OF FUEL SYSTEMS 1. CARBURETOR SYSTEMS 2. FUEL INJECTOR SYSTEMS 1. CARBURETOR SYSTEMS – Carburetors are classified as updraft or downdraft depending on the direction air flows through the device. All carburetors depend on the differential pressure created by a venturi to meter the proper amount of fuel for a volume of air. FLOAT-TYPE CARBURETORS – Fuel is stored in a float chamber, the amount controlled by a float-operated needle valve installed in the fuel inlet. MAIN COMPONENTS OF CARBURETOR SYSTEM MAIN METERING – main metering system supplies the engine with the correct amount of fuel for all speeds above idle system. ❖ IDLING SYSTEM - At idle speed the throttle valve is nearly closed. In some cases, the differential can be so low that sufficient fuel cannot be drawn through the main discharge nozzle. idle discharge ports (or idle jets) are connected to the main metering jet by an idle emulsion tube. MIXTURE CONTROL – provides the pilot with a method of adjusting the mixture supplied to an engine. Types of mixture control: Variable Orifice Mixture Control - The amount of fuel available to the engine is restricted only by the main metering jet. Back Suction Mixture Control - differential pressure controls fuel delivered to the discharge nozzle. Automatic Mixture Control – system that continuously adjusts the fuel/air mixture during flight. With this system, the mixture is LEANED as the aircraft climbs, ENRICHED as the aircraft descends, and otherwise adjusted for normal changes in atmospheric pressure during flight. FUEL SYSTEMS POWERPLANT 1 – AEE 654 ACCELERATION SYSTEM – System that gives a quick, supplemental charge of fuel is provided to the carburetor until the discharge nozzle can deliver fuel at a rate proportional to the airflow. Types of acceleration system: Acceleration Well Accelerator Pump POWER-ENRICHMENT/ECONOMIZER SYSTEM – MAIN FUNCTION IS TO HELP COOL THE SYSTEM WHILE AT MAXIMUM OPERATING POWER typically function at throttle settings above cruise power. Not only does a power enrichment system increase fuel flow at high power settings, it also permits the pilot to use a leaner mixture at cruise power. Types of economizers: ❖ NEEDLE TYPE economizer system uses an enrichment metering jet and nozzle parallel with the main metering jet and nozzle. ❖ Air Bleed Type the air bleed economizer system adjusts the size of the air bleed for the main discharge nozzle. Changing the size of the air bleed orifice adjusts the fuel/air mixture. TWO MAJOR LIMITATIONS OF CARBURETOR 1. First, because intake manifolds differ in length and shape, the fuel/air mixture is not evenly distributed to the cylinders of a carbureted engine. High performance aircraft engines operating with high compression ratios can be damaged by the introduction of a lean mixture in a cylinder. 2. Second, all carburetors, susceptible to carburetor icing. GOOD TO KNOW!!! SPRING BACK The amount of control travel possible between the carburetor stop and the cockpit. FUEL SYSTEMS POWERPLANT 1 – AEE 654 2. FUEL INJECTION SYSTEMS – a fuel injection system atomizes fuel directly in each cylinder assembly. Types of Fuel Injection Systems: ❖ Direct Fuel Injection system – A fuel injection system used mostly on radial engines. ❖ Continuous-Flow fuel injection system – is the most common type of fuel injection system in reciprocating aircraft engines. Instead of mixing the fuel and air in the combustion chamber, fuel is continuously injected into each intake port. COMPONENTS IN FUEL INJECTION FUEL METERING UNIT – MAIN FUNCTIONS IS TO CONTROL THE PROPER FUEL/AIR RATIO in Fuel injection system (part of the venturi housing) consists of a fuel strainer, a mixture control valve, an idle valve, a main metering jet, and an enrichment metering jet. FUEL REGULATOR – supplies the engine with the necessary amount of fuel. The fuel regulator consists of four distinct chambers (venturi suction, inlet air, inlet fuel, and metered fuel), two diaphragms (fuel and air), and a ball valve. IDLE SYSTEM – At idle, airflow through the engine is low and the air metering force is insufficient to open the ball valve to maintain a pressure differential across the metering jet. In the RSA system, a constant head idle spring provides the necessary force required to hold the ball valve off its seat. AUTOMATIC MIXTURE CONTROL – An automatic mixture control is installed parallel with the manual mixture control. USED BELLOWS THAT IS FILLED WITH HELIUM. As an aircraft climbs, air density decreases and the bellows expands, which results in a leaner mixture for combustion. FLOW DIVIDER – A flow divider, consisting of a diaphragm-operated valve and a spring, is typically installed centrally on top of an engine. Note that: When no fuel pressure is present, a combination of atmospheric and spring pressures holds the valve closed. INJECTOR NOZZLE – system uses air bleed nozzles threaded into the cylinder head intake ports. Each nozzle consists of a brass body constructed with a metering orifice, an air bleed hole, and an emulsion chamber. TYPES OF FUEL DELIVERY SYSTEM GRAVITY FED FUEL SYSTEM – typically used on high wing aircrafts, must be located higher than engine to feed the engines from the tank. Uses gravity as force mechanism. PUMP FED FUEL SYSTEM – typically used in low wing aircrafts. SYSTEM DEPENDENT ON PUMP. used redundant components such as primary and backup pump so that it can operate under conditions. Capable of supplying the engine 125% of max requirement performance each pump. FUEL SYSTEMS POWERPLANT 1 – AEE 654 GRAVITY FED FUEL SYSTEMS PUMP FED FUEL SYSTEMS POWERPLANT 1 – AEE 654 POWERPLANT 1 – AEE 654 IGNITION SYSTEMS BATTERY IGNITION SYSTEM – a type of IGNITION SYSTEM A typical battery ignition system consists of an ignition switch, a battery, an ignition coil, a set of breaker points, a cam, a capacitor, a distributor, and spark plugs. IGNITION coil – is a device that steps up the voltage to the level necessary to create a spark in each cylinder. A capacitor – (or condenser), a device that momentarily stores electrical energy. DISTRIBUTOR – directs high voltage current produced by the ignition coil to the spark plugs. MAGNETO IGNITION SYSTEMS – PERMANENT MAGNET alternating current generator that uses electromagnetic field. 2 types of Magneto Ignition Systems: o LOW TENSION SYSTEM – PRODUCES LOW VOLTAGE PULSE, minimizes flashover, uses transformers to produce high current voltage, not commonly use because dita has many parts that increases weight. o HIGH TENSION MAGNETO - uses a rotating magnet to induce voltage into an ignition, or magneto, coil. The coil steps up voltage just before it reaches the distributor for distribution to a spark plug. GOOD TO KNOW!!! During high altitude operations, a phenomenon called FLASHOVER can cause the spark to jump to the wrong electrode. Flashover often leads to CARBON TRACKING which appears as a fine pencil like carbon trail inside the distributor 3 TYPES OF MAGNETO CIRCUIT 1. THE MAGNETIC CIRCUIT - magnetic circuit includes a rotating permanent magnet, pole shoes, pole shoe extensions, and a coil core. Rotating magnets are often made from alnico. Alnico alloy – aluminum, iron, nickel, cobalt Full register position – this position the magnetic field is strongest and the density of flux lines is greatest. Neutral position in this position the magnetic field is weakest. 2. THE PRIMARY CIRCUIT - primary electrical circuit in a magneto includes the primary winding of an insulated magneto coil, a set of breaker points, and a capacitor. 3. THE SECONDARY CIRCUIT - secondary magneto circuit produces the high voltage energy required to cause a spark. The components that make up the secondary circuit include the secondary winding in the magneto coil and the distributor. IGNITION SYSTEMS POWERPLANT 1 – AEE 654 MAGNETO SPEED – distributor rotor in a magneto always turns at one-half the engine crankshaft speed. The speed of a rotating magnet shaft varies depending on the number of engine cylinders and the number of poles on the rotating magnet. RETARD breaker points to delay the spark during engine starting. Usually doing this to prevent backfiring. MAGNETO COMING-IN SPEED The rotational speed necessary for a magneto to fire a spark plug. IGNITION SWITCH – Located in cockpit, The typical ignition switch controls both magnetos on an engine and has at least four positions: OFF, LEFT, RIGHT, and BOTH. SPARK PLUGS – The spark plugs transmit the high voltage current from the ignition harness into the combustion chamber. POWERPLANT 1 – AEE 654 LUBRICATION SYSTEMS FUNCTIONS OF ENGINE LUBRICATION OILS 1. REDUCES FRICTION. 2. ABSORBS HEAT. 3. SEALS AND COAT METAL SURFACE. 4. CLEANS FOREIGN PARTICLES. 5. PROTECTS AGAINST CORROSION. 6. CUSHION EFFECT ON COMPONENTS. OIL PROPERTIES: VISCOSITY – Measure oils resistance to flow. Viscosity of liquid(oil) decreases at high temperature. TEMPERATURE DEPENDENT lower viscosity oils are used in cold climates and higher viscosity oils are used in warm climates. Oil viscosity is measured using an instrument known as the Saybolt Universal Viscosimeter Oils used in reciprocating engines typically have a relatively high viscosity ❖ SPECIFIC GRAVITY ❖ COLOR – 1.00 PURE WHITE, 8.00 DARK (CLARED RED) ❖ CLOUD POINT - At this temperature, the oil begins to lose clarity and appears cloudy or hazy. ❖ POUR POINT - represents the lowest temperature at which it can flow or be poured. ❖ FLASH POINT AND FIRE POINT Flash point is the temperature at which oil begins to emit ignitable vapors. FIRE POINT - temperature beyond flash point where it emits sufficient vapor to support flame. ❖ CARBON RESIDUE TEST – The percentage weight difference before and after the test ❖ ASH TEST - ash test is an extension of a carbon residue test in that it requires the carbon residue to be burned until only ash remains. LUBRICATION SYSTEMS POWERPLANT 1 – AEE 654 TYPES OF OIL ❖ Mineral-Based oil are more chemically stable than vegetable oil ❖ Synthetic and Mineral based oil are used for reciprocating engine. STRAIGHT MINERAL OIL – No additives, HIGH TENDENCY TO OXIDIZE AT HIGH TEMPERATURE, only USED in new or newly overhauled engine. ASHLESS-DISPERSANT OILS – Most common oil for RECIPROCATING ENGINE. Contain DISPERSANT that repels sludge forming. MULTIVISCOSITY OILS – Created to address drawbacks for single viscosity oil. Can generally used AT WIDER TEMPERATURE RANGE SYNTHETIC OILS – Has MULTIVISCOSITY trait, contains chemical additives and certain DIESTERS, has LOW INTERNAL FRICTION, HIGH RESISTANCE TO THERMAL BREAKDOWN. EXTEREME PRESSURE LUBRICANTS HYPOID LUBRICANTS – FORMULATED TO PROVIDE PROTECTION UNDER HIGH LOADS. PRESSURE LUBRICATION – PRIMARILY USED, uses engine driven pumps SPLASH LUBRICATION – effective when oil is stored in crankcase splashed by the engine components. SPRAY LUBRICATION – uses same pressurized oil but uses spray NOZZLE 2 TYPES OF OIL SYSTEM 1. WET SUMP – All oil is stored in CRANKCASE Lightweight and simple construction. x Limited oil capacity x Difficult to cool 2. DRY SUMP – All oil is stored in OIL RESERVOIR Larger capacity of oil, EASY to cool Uses SCAVENGE pump to transport oil back to tank x More weight LUBRICATION SYSTEMS POWERPLANT 1 – AEE 654 SYSTEM COMPONENTS OIL RESERVOIR – tank that holds oil lubricant. Wet and Dry sump are cast from aluminum alloy. SCUPPER DRAIN – catches overflow of oil OIL PUMPS – constant displacement pump moves a fixed volume of fluid per pump revolution or cycle. 3 TYPES OF PUMP: GEAR PUMP SCAVENGE PUMP GEROTOR PUMP PRESSURE RELIEF VALVE – To ensure adequate engine lubrication. Oil pressure must be maintained. OIL FILTER – To remove the solid particles from oil. FULL FLOW FILTER SYSTEM – All Oil is filtered every time it circulates. To accomplish this, the filter is in series with the oil pump, between the pump and the engine bearings. PARTIAL FLOW SYSTEM – 10 percent of oil is being filtered as it circulates. the filter is parallel with passages to the engine bearings. OIL COOLER - excess heat is removed by an oil cooler, or oil temperature regulator. An oil cooler is simply an oil-to-air heat exchanger. SURGE PROTECTION VALVE - A typical surge protection valve is installed at the oil cooler inlet and is held in a normally closed position by spring pressure. OIL SEPARATOR – Use to eliminate bubbles and air mixed with the fuel. Usually located after the vacuum pump. OIL DILUTION – Happens on cold weather gas is mixed with oil to flow freely in cold temperatures. system consists of a cockpit-controlled oil dilution solenoid, an oil dilution valve, and the necessary plumbing. OIL PRESSURE GAUGE - engine lubrication system supplies oil under pressure to the moving parts of the engine. To monitor the effectiveness of the lubrication system. SYSTEM MAINTENANCE OIL CHANGE AND SERVICING - Routine service, Additional contaminants that can be trapped in lubricating oils include gasoline, moisture, acids, dirt, carbon, and metal particles. OIL FILTER REPLACEMENT - When replacing a disposable filter, it is common practice to cut open the used filter and inspect the element for the presence of any metal particles which might indicate an impending engine failure. OIL RESERVOIR – REMOVING THE OIL, removing connections of, inlet valve and vent lines, remove scupper drain hose, safety wire and clams then lift the tank out the aircraft. Reverse this sequence to reinstall tank. OIL COOLER - normally removed and cleaned out DURING OVERHAUL, if there is sludge formation cooler must immediately be cleaned and inspect for cracks. RELIEF VALVE ADJUSTMENT - over time, the spring in a relief valve can weaken and require minor adjustment.