Indian Railways Track Machine Manual PDF
Document Details
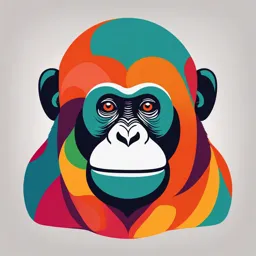
Uploaded by TriumphalNephrite9087
2019
Rakesh Goyal
Tags
Summary
This manual provides detailed information on the organizational structure, duties, and inspections of track machines within Indian Railways. It covers various aspects from machine types to maintenance procedures. It's intended for use by officers and staff involved in track machine operation and permanent way maintenance.
Full Transcript
GOVERNMENT OF INDIA MINISTRY OF RAILWAYS (RAILWAY BOARD) INDIAN RAILWAYS TRACK MACHINE MANUAL Second Edition September, 2019 GOVERNMENT OF INDIA MINISTRY OF RAILWAYS (RAILWAY BOARD) INDIAN RAILWAYS TRACK MACHINE MANUAL Second Edition September,...
GOVERNMENT OF INDIA MINISTRY OF RAILWAYS (RAILWAY BOARD) INDIAN RAILWAYS TRACK MACHINE MANUAL Second Edition September, 2019 GOVERNMENT OF INDIA MINISTRY OF RAILWAYS (RAILWAY BOARD) INDIAN RAILWAYS TRACK MACHINE MANUAL Second Edition September, 2019 FOREWORD TO SECOND EDITION TO IRTMM (2019) Indian Railways Track Machine Manual was first published in March, 2000. Many new types of Track Machines have since been inducted into Indian Railways which needed to be updated in the Manual. It was also being felt that some of the topics like tamping technology, technical detail of machines, maintenance infrastructure, organizational structure etc. need to be deliberated in more detail for better apprehension by field staff. Accordingly, second revision of Indian Railways Track Machine Manual has been prepared after including all types of machines working on Indian Railways, tamping technology, organizational structure of Track Machine and procedure for data entry in TMS. I am happy to note that now Indian Railways Track Machine Manual, covering every aspect of the track machine working, is being published. It is hoped that this manual will be very useful to the officers and staff associated with track machine as well as Permanent Way maintenance. New Delhi Vishwesh Chaube September, 2019 Member Engineering Railway Board, New Delhi ii FOREWORD TO FIRST EDITION TO IRTMM Mechanized track laying and maintenance has been introduced in a big way on Indian Railways to meet the challenges of growing traffic and changed socio-economic conditions. Based on the field experience and recommendations by the machine manufacturers, numbers of instructions have been issued from time to time by the zonal railways and Railway Board. However, these were not documented at one place. I am happy to note that now Indian Railways Track Machine Manual, covering every aspect of the track machine working, has been published. It is hoped that this manual will be quite useful to the officers and staff associated with track machine as well as Permanent Way maintenance. New Delhi V.K.Agnihotri 23rd March, 2000 Member Engineering Railway Board New Delhi iii PREFACE TO SECOND EDITION “Indian Railways Track Machine Manual” was published in 2000 for the guidance of the officials of Track Machine and Open Line/Construction organization. Mechanisation of track maintenance over IR stated with induction of 4 nos. of (B-60) on-track tamping machine of MATISA make during 1963. Now the fleet of track machines on Indian Railways has grown from 4 No. (B-60) on-Track Tampers to 904 (as on 01-12-2018) track machines covering almost all spheres of track maintenance and track laying/renewal activities. Railway Board appointed a committee to review and revise the Track Machine Manual – 2000 vide Letter No. 96/Track-III/TK/44 Vol. II dated 02-11-2015 based on latest developments, provisions and working rules with due consideration to provisions of IRPWM, G&SR and other codes/manuals, instructions/JPOs issues by Zonal Railways, instructions regarding operation, maintenance, troubleshooting manuals etc. of OEMs & RDSO. Following members of committee as nominated by Railway Board either by name or by virtue of post participated during meetings and finalized the draft of this manual – Sl. No. Designation Name (S/Shri) 1 Executive Director (TM), RDSO Brijesh Kumar Mudit Bhatnagar 2 Senior Professor, Track, IRICEN Chandra Shekhar Sharma 3 Chief Engineer/TM, Central Railway Naresh Lalwani Pradeep Kumar Garg 4 Chief Engineer/TM, Western Railway Vivek Kumar Gupta 5 Chief Engineer/TM, North Central Railway C. P. Gupta 6 Chief Engineer/TM, South Central Railway Gautam Srinivas Rakesh Yadav 7 Chief Engineer/TM, East Central Railway Vijay Kumar Sahu S/Shri Anil Choudhary/Director/TM-III/RDSO, Sanjay Asthana/Executive Engineer/NCR, Muslim Ahmed/Assistant Research Engineer/TM/RDSO and S. D. Mahajan/Assistant Engineer /TM/ Western Railway rendered the valuable assistance and contributions to committee during deliberations and preparation of this manual. The committee also received valuable inputs and contribution from S/Sh. A.K. Khandelwal/Executive Director Track (MC)/Railway Board & Tushar Kant Pandey/Director Track (MC)/Railway Board. I hope this detailed and reviewed version of manual will be very useful for the field staff and will succeed in its purpose of disseminating the art of track maintenance using sophisticated Track machines to the field engineers. Any comments and suggestions from the reader regarding any correction/further improvement for the manual will be highly appreciated. Rakesh Goyal New Delhi Additional Member/Civil Engg. September, 2019 Railway Board, New Delhi iv PREFACE TO FIRST EDITION Track Machines were introduced on Indian Railways during the early sixties. The use of the machines both for maintenance as well as track laying increased with the introduction of heavy track structures. For working of these machines, instructions had been issued by the Railway Board and Zonal Railways from time to time. However, no manual as such was issued on track machines. Under these circumstances, Railway Board vide their letter no.96/Track-III/TK/84 dated 11-12-96 appointed a committee for preparation of the manual, of Director/IRICEN, Executive Director (TM)/RDSO, Executive Director Track (MC)/Railway Board and Chief Track Engineers (MC) of Northern, Southern and South Central Railways. The following officers participated in the committee from time to time:- Designation Name Director, IRICEN Shri Vinod Kumar (Chairman) Executive Director (TM)/RDSO S/Shri i) A.P. Mishra ii) O.P. Agrawal iii) Dharm Singh Executive Director Track (MC)/ S/Shri Rly Board i) R.N. Verma ii) V. K. Agrawal Chief Track Engineer (MC)/N.Rly S/Shri i) S. K. Vij ii) A.P. Mishra iii) Harjinder Singh Chief Track Engineer (MC)/S.C.Rly S/Shri i) N. Ramasubramanian ii) P.N. Ram Chief Track Engineer(MC)/S.Rly S/Shri i) A.N. Parakalan ii) S.ParameshwaraIyer iii) K.J.S. Naidu v The committee held its first meeting on 10-04-97 at IRICEN/Pune. Subject matter of various chapters of the manual was discussed by the committee during subsequent sittings. Draft of the manual was finalised and circulated to Zonal Railways for suggestions, vide Railway Board’s letter no. 96/Track- III/TK/44 dated 08-06-98. In the light of comments/suggestions received from the railways, original draft was finalised with modifications as considered necessary. The prevailing instructions in regard to working of track machines over different railways, instructions issued by Railway Board, provisions in the IRPWM, Indian Railway General Rules, other relevant codes/manuals and circulars issued by RDSO, had also been kept in view while preparing this manual. While every effort has been made to cover all aspects of track machine working, the Chief Engineers of zonal railways may issue such supplementary instructions as necessary to suit local conditions on the railways. Such instructions, however, should not contravene any of the provision in this manual and other codes. The committee was rendered valuable assistance and contributions by S/Shri C.P. Tayal, Sr. Processor/IRICEN; Hitesh Khanna, Director Track (MC)/Rly Board and J. S. Mahrok, Director/TM RDSO, during deliberation and preparation of this manual. Though every care has been taken in preparing this manual, any error or omission, if found, may be brought to the notice of Railway Board. Suggestions for further improvement in this manual will be welcome. This manual has been issued in consultation with Finance and Traffic Directorates of Railway Board. New Delhi N. C. Bindlish March 10, 2000. Additional Member/Civil Engg. Railway Board, New Delhi. vi CONTENTS Para Details Page No CHAPTER 1 ORGANISATIONAL STRUCTURE, DUTIES AND INSPECTIONS 1-17 PART A - ORGANISATIONAL STRUCTURE AND DUTIES 101 Track Machine Organisation – Role 1 102 Functions and Organisation 2 (1) Functions of Track Machines Organisation (2) Organisation at Zonal Railway HQ (3) Field Organisation on Zonal Railway (4) Central Periodic Overhauling (CPOH) Workshop 103 Duties of Executive (XEN)/Assistant Executive Engineer (AXEN)/TM/Line 3 (1) General (2) Observance of Rules and Regulations (3) Inspection by Higher Officers 104 Duties of SSE/TM/SDI 5 105 Duties of SSE/TM(SD) 6 106 Duties of SSE/JE/TM Working on Machines 6 107 Duties of SSE/JE Machine In-Charge 7 108 Duties of SSE/JE/MCM/TMM in Control set up in HQ/ZMD/Division 8 109 Duties of Master Crafts Man (MCM) and Track Machine Maintainers (TMM) 8 110 Duties of Machine Assistant 8 111 Duties of Assistant Divisional Engineer (Open Line) ADEN 9 112 Duties of SSE/JE (P.Way) Deployed with the Machine 10 PART B – INSPECTION OF TRACK MACHINES 113 Inspection Schedule of Track Machine Officials 11 114 Inspection Schedule of Open Line Officials 11 115 Items to be Inspected 12 (1) Inspecting Officials of TMO as well as Open Line (2) Inspecting Officials of TMO- Additional Items (3) Inspecting Official of Open line - Additional Items CHAPTER 2 TAMPING MACHINE AND DYNAMIC TRACK STABILIZER 18-98 201 General 18 202 Tamping Machine 18 (1) Functions (2) General Layout 203 Important Assemblies of Tamping Machines 18 (1) Engine (2) Tamping Units (3) Tamping Tool vii (4) Lifting and Lining Unit (5) Satellite Unit (6) Trolleys (7) Brake System 204 Types of Tamping Machines 21 (1) Tampers without Satellite Unit (2) Tampers with Satellite Unit 205 Tamping Mechanism 23 206 Tamping Parameters 24 (1) Squeezing Pressure (2) Tamping Depth (3) Tamping Tool Vibration, Amplitude & Frequency (4) Vibration Pressure (5) Tamping Cycle & Squeezing Time (6) Tamping Tool Surface Area 207 Optional Equipment 27 (1) Laser Beam System (2) Geometry Value Assessment (GVA) (3) Automatic Guiding Computer (ALC) System (4) Data Recording Processor (DRP) System (5) Computerized Measuring System (CMS) (6) Computerized Working System (CWS) 208 Lining System 28 (1) Reference Rail (2) Lining Method 209 4 Point Lining Method 29 (1) Lining Principle (2) Application of 4-Point Lining Method 210 Corrections to be Applied in 4 Point Lining Method 31 (1) Correction (FD) (2) Versine Compensation (V) 211 Modes of Tamping using 4-Point Lining Method (Only for curves) 38 (1) 4-Point Smoothening or Compensation Mode (2) 4- Point Design Lining 212 3 Point Lining Method 39 (1) Lining Principle (2) Application of 3-Point Lining Method 213 Corrections to be applied in 3- Point Lining 40 214 Determination of Target Versine Values for the 3-Point Lining Method 41 (1) Curve with Parabolic Transitions (2) Curve without Transition 215 Mode of Tamping using 3-Point Lining Method 45 (1) 3- Point Elementary Mode Lining (2) 3- Point Design Mode Lining viii (3) Measuring Run (with ALC) Lining Modes 216 Comparison between 3 Point and 4 Point Lining System 46 (1) 3-Point Lining elementary mode/4-point Lining Smoothening Mode (2) 3 -Point Lining /4-point Lining in Design Mode 217 Levelling of Track 48 (1) Datum Rail and Cant Rail (2) Selector Switch 218 Levelling and Lifting System 48 (1) Equipment (2) Working (3) Reduction Ratio (4) Reduction Ratio of Various Machines 219 Mode of working for levelling 50 (1) Smoothening or Compensation Levelling Mode (2) Design or Precision Levelling mode (3) Measuring Run (ALC) Levelling Mode 220 General Lift 51 (1) Deciding General Lift (2) Quantum of General Lift (3) General Lift on Curves 221 Ramp in Ramp Out 52 (1) Value of Ramp (2) Method of Ramping (3) Feeding of Ramp Values 222 Input of the Lifting Values 53 (1) Method of feeding of Cant in Curves (2) Correction (K) in Cross-Level (3) Attention to Vertical Curve 223 Survey and working of Tamping Machines in Design Mode 57 224 Works required Before, During and After Tamping 57 (1) General (2) Preparatory Works (3) Pre-Tamping Works (4) Operations During Tamping (5) Post Tamping Operations 225 Dynamic Track Stabilizer (DTS) 63 (1) General (2) General Layout (3) Advantages of DTS (4) Brake System 226 Working Principle of Dynamic Track Stabilizer 64 (1) Mechanism of DTS (2) Levelling System in DTS (3) Speed of Working of DTS ix (4) Stabilization Achieved by DTS 227 Modes of working of Dynamic Track Stabilizer 65 (1) Maximum Settlement/Constant Pre Load Mode (2) Controlled Settlement/Variable Pre Load Mode 228 Types of Dynamic Track Stabilizer 65 (1) Types of DTS (2) Salient Features of Different DTS 229 Working of DTS 67 (1) General (2) Precautions in DTS Working Annexure-2.1 : Position of Tamping Tools In Tamping Machines 70 Annexure 2.2 : Important Features/Dimensions of DUOMATIC & WST 72 METEX Annexure-2.3 : Important Features/Dimensions of Points & Crossing 73 Tamping Machine Annexure- 2.4 : Important Features/Dimensions of UNIMAT Split Head 74 MFI & Multipurpose Tamping Machine Annexure- 2.5 : Important Features/Dimensions of Continuous Tamping 75 Machine 09-32-CSM Annexure- 2.6 : Important Features/Dimensions of Tamping Express (09- 76 3X) (Plain Track Tampers) of Different Models Annexure- 2.7 : Laser Sighting System 77 Annexure- 2.8 : Automatic Guiding Computer (ALC) System 79 Annexure- 2.9 : Machine Trolley Distances 81 Annexure- 2.10 : Sample - Versine Compensation (V) 82 Annexure- 2.11 : Sample- F Values 83 Annexure- 2.12 : Example- Sequence of Tamping of Track by WST 08-32C 84 Annexure- 2.13 : Example – Ramp In and Ramp Out 88 Annexure- 2.14 : Sample - Correction (K) for Curvature 91 Annexure- 2.15 : Sample - Value of X for Vertical Curves 92 Annexure- 2.16 : Guidelines for Surveying of Track for getting Offset values 93 for Design Mode of Tamping Annexure- 2.17 : Sequence of Tamping of Different Points & Crossing 96 (UNIMAT-2S) CHAPTER 3 BALLAST CLEANING AND HANDLING MACHINES 99-129 301 General 99 302 Ballast Cleaning Machines (BCM) 99 303 Important Assemblies of Ballast Cleaning Machines 100 (1) Engine (2) Excavating Unit (3) Screening Unit (4) Conveyer System for Distribution of Ballast and Disposal of Muck x (5) Track Lifting and Slewing Unit (6) Recording Unit (7) Brake System 304 Types of Ballast Cleaning Machines 101 (1) Plain Track Ballast Cleaning Machine (2) Points and Crossing Ballast Cleaning Machine (3) Plain Track and Points & Crossing Ballast Cleaning Machine 305 Working Principle and Capability of Ballast Cleaning Machines 102 (1) Excavation Width (2) Excavation Depth (3) Lifting and Slewing of Track (4) Disposal of Muck (5) Screening Capacity of BCM (6) Controlled Ballast Distribution (7) Total Excavation (8) Deep Screening of Points and Crossing 306 Works Required Before, During and After Deployment of Ballast Cleaning 106 Machines (1) Introduction of Ballast Cleaning Machines for Plain Track and Turnouts (2) Preparatory Works (3) Operations During Traffic Block (4) Operations after Deployment of Machine 307 Shoulder Ballast Cleaning Machine (SBCM) 111 308 Important Assemblies of Shoulder Ballast Cleaning Machines 111 (1) Engine (2) Excavating Unit (3) Screening Unit (4) Conveyor System for Distribution of Ballast and Disposal of Muck (5) Ballast Profiling Plough (6) Broom (7) Brake System 309 Types of Shoulder Ballast Cleaning Machines 112 (1) Shoulder Ballast Cleaning Machine - FRM 80 (2) Shoulder Ballast Cleaning Machine - FRM 85 310 Capacity of Shoulder Ballast Cleaning Machines 112 (1) Width of Excavation (2) Depth of Excavation (3) Muck Disposal System (4) Ballast Distribution System (5) Screening Capacity (6) Total Excavation 311 Works Required Before, During and After Deployment of Shoulder Ballast 113 Cleaning Machines (1) Operations Prior to Deployment of Machine xi (2) Operations During Block 312 Ballast Regulating Machine (BRM) 114 313 Important Assemblies of Ballast Regulating Machines 114 (1) Shoulder Plough (2) Front Plough (3) Centre Plough (4) Broom (5) Hopper (6) Rail Fastening Sweepers (7) Welded-on-Tunnels for covering Rail and Fastenings (8) Brake System 314 Types of BRM 115 (1) Without Hopper (2) With Hopper 315 Working Principle and Capacity of Ballast Regulating Machines 116 (1) The Regulation Width (2) Ballast Handling Capacity 316 Works Required Before and During Deployment of Ballast Regulating 119 Machines (1) Operations Prior to Deployment of Machine (2) Operations During Block Annexure-3.1 : Important Features/Dimensions of Ballast Cleaning 121 Machine (RM-80) Annexure-3.2 : Important Features/Dimensions of Ballast Cleaning 122 Machine (RM-76 & RM-80-92U) Annexure-3.3 : Important Features/Dimensions of Shoulder Ballast 123 Cleaning Machine (FRM-80) Annexure-3.4 : Important Features/Dimensions of Shoulder Ballast 124 Cleaning Machine (FRM-85 F) Annexure-3.5 : Important Features/Dimensions of Ballast Regulating 125 Machine (Model - 56-3 & 66-4) Annexure-3.6 : Important Features/Dimensions of Ballast Regulating 126 Machine (Model BRM PBR 400R) Annexure-3.7 : Important Features/Dimensions of Ballast Regulating 127 Machine (GEMAC) Annexure-3.8 : Important Features/Dimensions of Ballast Regulating 128 Machine (BRM 2000 SWS) Annexure-3.9 : Important Features/Dimensions of Ballast Regulating 129 Machine (BRM METEX) CHAPTER 4 TRACK RELAYING MACHINES 130-154 401 Track Relaying Machines 130 402 Planning for Working of Track Relaying Machines 130 xii 403 Track Laying Equipment (TLE) 130 404 Important Assemblies of Track Laying Equipment (TLE) 130 (1) Side Frames (2) Bridge (3) Sleeper Gripper (4) Rail Clamps (5) Turn Table 405 Types of Track Laying Equipment 131 406 Working Mechanism and Capability of Track Laying Equipment 131 407 Setting-up of TLE Base Depot 133 408 Pre-Relaying Operations 136 (1) At Base Depot (2) At Work-Site 409 Operation During Block 138 410 Post Relaying Operations 139 411 Track Relaying Train (TRT) 139 (1) Functions of TRT (2) Works by TRT (3) Advantages of TRT (4) General Layout 412 Important Units of TRT- Model No. P 811-S 140 (1) Beam Car (2) Handling Car (3) Power Car 413 Working Mechanism of TRT 140 414 Operations Prior to Deployment of TRT 142 415 Operations During The Block of TRT 144 416 Post Block Operations for TRT 144 417 Precautions During TRT Working 145 418 Points and Crossing Laying/Changing Machine (PCCM) 145 419 Important Units of AMECA T-28 145 (1) Portal Crane (2) Trolleys (3) Jib Crane 420 Working Mechanism and Capability of AMECA T- 28 147 (1) Longitudinal/Forward Launching (2) Transverse/Side Launching 421 Pre-Block Operations of T-28 M/c 149 422 Operations During Block of T-28 M/c 150 423 Post Block Operations of T-28 M/c 151 424 Miscellaneous 151 Annexure- 4.1 : Important Features/Dimensions of Track Relaying 152 Machine Annexure- 4.2 : Important Features/Dimensions of Track Relaying Train 153 xiii Annexure -4.3 : Important Features/Dimensions of Points & Crossing 154 Changing Machine (AMECA T-28) CHAPTER 5 SPECIAL PURPOSE MACHINES 155-183 501 Rail Grinding Machine (RGM) 155 (1) Purpose of Rail Grinding (2) Advantages of Rail Grinding 502 Important Assemblies of RGM 156 (1) Components of RGM (2) Front Control Car (FCC) (3) Grind Car (4) Water Tank Wagon (5) Camp Coach Cum Rear Control Car (RCC) (6) Rail Corrugation Analyzer (RCA) (7) Obstacle Detection System (8) Rail Profile Measurement System (Optical) (9) Dust Collection System (10) Brake System 503 Grinding Strategy 159 (1) Strategy (2) Corrective Grinding (3) Preventive Grinding (4) Preventive-Gradual Grinding (5) Target Rail Profiles (6) Patterns (7) Grind Data Management System (GDMS) (8) Grind Quality Index (GQI) 504 Capability of RGM 161 505 Working Parameters of RGM 162 (1) General (2) Target Profile (3) Rail Wheel Contact Points (4) Selection of Target Profile (5) Grind Patterns (6) Grind Cycle 506 Monitoring Equipment for Grind Quality 164 (1) MINIPROF (2) Bar Gauge (3) Star Gauge (4) Digital Inclinometer (5) Surface Roughness Measuring Gauge (6) Rail Hardness 507 Working of RGM 165 xiv 508 Quality Inspection of Grinding 165 (1) Test Site Monitoring (2) Other Quality Checks 509 Preparatory Works for Introduction of RGM 167 510 Pre-Block Activity Before Deploying RGM 168 511 Operation During RGM Block 168 (1) On the Track (2) On the Machine 512 Post Grinding Operation 170 513 Utility Track Vehicle 170 (1) General (2) Main Assemblies of UTV and their Functions (3) Models of UTVs 514 Rail Borne Maintenance Vehicle 172 (1) General (2) Main Assemblies of RBMV and their Functions (3) Salient Features of RBMV 515 Works Required Before, During and After Deployment of UTVs and RBMV’s 173 Annexure-5.1 : Important Features/Dimensions of RGI Control Car 175 Annexure-5.2 : Pattern Sheet 176 Annexure-5.3 : Proforma for Data to be Fed in GDMS 177 Annexure-5.4 : Rail Grinding Monitoring Proforma 179 Annexure-5.5 : Important Features/Dimensions of Utility Track Vehicle & 183 Rail Borne Maintenance Vehicle CHAPTER 6 PLANNING AND DEPLOYMENT 184-190 601 Planning 184 602 Pre-requisites for Deployment of Track Machines on Construction 185 Projects/Other Agencies 603 Inter- Railways Deployment 186 604 Line Blocks, Stipulated Corridors and Monitoring 187 605 Types of Blocks 187 (1) Regular Traffic Blocks (2) Blocks on Construction Projects and Multiple Lines (3) Special Blocks 606 Minimum Duration of Blocks 188 607 Measures for Ensuring Block 189 608 Through Tamping and Spot Attention 189 (1) Types of Tamping (2) Tamping Frequency xv CHAPTER 7 RULES FOR MOVEMENT AND BLOCK WORKING 191-232 701 General 191 (1) Categorization of Track Machines (2) Self-Propelled Track Machines (3) Provision of G&SR (4) Knowledge of G&SR (5) Manning of Track Machines and Possession of Safety Equipment (6) Salient information of Track Machine 702 Operation and Working of Track Machine 192 (1) Responsibility of Track Machines (2) Supervision of work of Track Machines (3) Working – General 703 Competencies of Track Machine Staff 194 (1) Medical Fitness and PME (2) Technical Training (3) G & SR Training (4) Route/Road Learning (5) Competency Certificate 704 Safety Equipment 195 (1) General (2) Head and Tail Lights 705 Rules for Operation – General 196 (1) Stabling of Track Machines (2) Shunting of Track Machines (3) Machine Ready Memo (4) Movement of Track Machines (5) Working in Group (6) Run Through Movement in Group (7) Working of Track Machine in Block (8) Working in Automatic Block Sections (9) Working in Integrated Traffic Blocks (10) Use of Cell Phone on Track Machine (11) Requirement of Pilot (12) SSE/JE(P.way) as Guard 706 Working Of Track Machines In Single and Double Line Sections 198 (1) Single Line Section – Work and Proceed (2) Single Line Section – Work and Return (3) Double Line Section – Work and Proceed (4) Double Line Section - Work and Return 707 Important Instructions and Precautions 201 (1) Protection of Work Site (2) Fouling of Adjacent Lines (3) Information to Level Crossings xvi (4) Safe Distance and Speed of Machine in Group (5) Setting of Points of Stabling Siding (6) Shunting in Line occupied by Track Machine (7) Safety of Men (8) Checking Infringement After Work 708 Failure and Accidents of Track Machines 203 (1) Protection in case of Breakdown (2) Failures in Block Section (3) Accidents involving Track Machine (4) Action in case of Failure in Block (5) Request for ART/Breakdown 709 Permissible Speed 204 710 Speed Certification for Track Machines 204 (1) Speed Certification for New type of Track Machine for Regular Movement (2) Sanction for running of Machine by other Zonal Railways (3) One Time Movement of New Machine 711 Infringements 209 712 Special Precautions while working in Special Circumstances 210 (1) Working of Machines in Ghat Sections (2) Night Working Annexure- 7.1 : List of Standard Forms 212 Annexure- 7.2 : Personal Diary 214 Annexure -7.3 : Competency Certificate 219 Annexure- 7.4 : Proforma of Machine Ready Memo 220 Annexure -7.5 : Proforma of Block Permit 221 Annexure -7.6 : Instructions for Machine Working in Automatic Signalling 222 Section Annexure -7.7 : Infringement to Indian Railways Schedule of Dimension by 225 Various Track Machines CHAPTER 8 PERIODICAL MAINTENANCE AND ASSOCIATED INFRASTRUCTURAL FACILITY 233-275 801 General 233 802 Maintenance Schedule for Track Machines 233 (1) Maintenance Schedule for Various Track Machine (2) Inspection of Wheel and Axle of On-Track Machine 803 Types of Workshops 235 804 Central Periodical Overhauling Workshop (CPOH) 236 (1) Functions of CPOH (2) POH Planning for Track Machines to be Attended (3) POH Execution (4) Dispatch of Machine after POH 805 Intermediate Overhauling Workshop (IOH)/Zonal Machine Depot (ZMD) 238 (1) Functions of ZMD xvii (2) Facilities at ZMD (3) Programme of IOH & POH (4) Planning of IOH 806 Satellite Depot 240 (1) Functions of Satellite Depot (2) Facilities at Satellite Depot 807 Mobile Workshop-cum-Transport Van 240 (1) Functions of Mobile Workshop (2) Facilities in Mobile Workshop 808 Camping Coach Workshop 240 (1) Functions of Camping Coach Workshop (2) Facilities in Camping Coach Workshop 809 Infrastructure Facility for Operation and Maintenance of Track Machines 241 (1) Infrastructural Facilities for CPOH, ZMD and Satellite Depot (2) Storage and Carriage Facilities for Fuel and Oil (3) Transportation of Spare Parts & Assemblies (4) Communication Facilities (5) Repairs and Stabling Facilities for Machines (6) Resting & Cooking Facilities for Staff 810 Camp Coach Facilities 242 (1) Living Area (2) Kitchen (3) Bathing Area & Toilet (4) Electrification Plan (5) Store Management Annexure- 8.1 : Maintenance Schedule of Track machines 245 Annexure -8.2 : Formats for POH Planning 240 Annexure -8.3 : POH Flow Chart 247 Annexure -8.4 : Requirement of Facilities in Various Depots 248 Annexure -8.5 : Machine wise list of 'Masters' required for Calibration of 257 Parameters Annexure -8.6 : Format for Master Calibration 261 Annexure -8.7 : Format for Repair Summary Sheet for POH 262 Annexure -8.8 : Format for 90 Days Feedback of POH 263 Annexure -8.9 : Typical Facilities to be provide in a Mobile Workshop 265 Annexure -8.10 : List of Equipment to be kept in Camp Coach Workshop 266 Annexure -8.11 : Typical Layout of Track Machine Siding 267 Annexure -8.12 : Rest House for Track Machine Staff 268 Annexure -8.13 : Layout of Camping Coach (Based on RDSO Drg. No.CSC- 269 1592) Annexure -8.14 : Layout of Camping Coach (Based on RDSO Drg. No.CSC- 270 1640) Annexure -8.15 : Layout of Camping Coach (Based on RDSO Drg. No.CSC- 271 1686) xviii Annexure -8.16 : Amenities to be provided in Camping Coaches 272 Annexure -8.17 : Paint Scheme for Camping Coach 274 Annexure -8.18 Electric Circuit Diagram of Camping Coach 275 CHAPTER 9 MANPOWER 276-285 901 General 276 902 Requirement of Manpower 276 903 Training 276 (1) Officers (2) SSEs/JEs/TM(s) (3) Technical Staff (4) Machine Assistant 904 Roster 277 (1) Weekly Roster (2) Three Weeks Roster (3) Duty Hours for Field (4) Duty Hours for Zonal Depot and Satellite Depot (5) Duty Hours for HQ Office & Control Annexure- 9.1 : Weightage Factors for Track Machines and Yardsticks for 279 staff Annexure-9.2 : Scale of Staff for Repairs and Maintenance for POH - 283 CPOH Workshop Annexure-9.3 : Man Power for POH of 24 Track Machine Units and 200 284 Tamping Banks Annexure-9.4 : Man Power for POH of 50 Track Machine Units and 200 285 Tamping Banks CHAPTER 10 STORES AND CONTRACTS 286-294 1001 Store Depot 286 1002 Inventory Control 286 1003 Procurement of Consumables, Components and Spares 288 1004 Sourcing of Components & Spares and Procurement Procedure 288 1005 Inspection and Acceptance of Materials 290 1006 Modes of Procurement, Repairs and Maintenance 290 (1) Cash Imprest (2) Emergency Repairs/Purchase (3) Annual Maintenance Contract (AMCs) (4) Contracts other than AMCs 1007 Condemnation of Track Machine 291 1008 Codal Life of Machines And POH/IOH Frequencies 291 1009 Calculation of Unit Cost of Working of Different Track Machines 292 (1) Capital Recovery Factor xix (2) Codal Life of Machines (3) Proportional POH and IOH Cost (4) Fixed and Variable Cost (5) Working and Approval of Unit Cost CHAPTER 11 MONITORING 295-311 1101 GENERAL 295 (1) Data Collection & Entry (2) Generation of Reports and Alerts (3) Periodical Meetings 1102 Organization for Monitoring 298 (1) Track Machine Control at Headquarters (2) Track Machine Control at Zonal Maintenance Depot (ZMD) Level (3) Divisional Control (4) Satellite Depot (SD) 1103 Functions of Divisional Control in respect of Track Machines 299 1104 Functions of Track Machine Control at ZMD Level 299 1105 Functions of Track Machine Control at Headquarter Level 300 1106 Monitoring Modules of Track Machines 301 (1) Parameters for Monitoring Productivity and Utilization of Machines (2) Parameters for Monitoring Health of Machine 1107 Reports and Documentation for Track Machines 303 (1) Daily Performance Report (2) Daily Log (3) Breakdown Report (4) Monthly Appreciation Report (5) Monthly Summary (6) Record for 3 years 1108 Track Management System (TMS) – Present Module 304 Annexure-11.1 : Track Machines Organization 306 Annexure-11.2 : Breakdown Report of Track Machine 309 Annexure-11.3 : Types of Reports in TMS 310 LIST OF ABBREVIATIONS 312-316 xx CHAPTER 1 ORGANISATIONAL STRUCTURE, DUTIES AND INSPECTIONS PART A - ORGANISATIONAL STRUCTURE AND DUTIES 101 Track Machine Organisation – Role (1) Track Machine Organisation on Zonal Railway will be the custodian of on-track machines and will be responsible for making the machines available as per the approved deployment programme with requisite staff for efficient working of the machines. Each zone shall have at least one zonal maintenance depot and each division shall have at least one satellite depot for overhauling, repair & maintenance of machines. (2) Track Machine Organization will maintain machines in good condition. The periodical schedules for maintenance of the machines shall be drawn out and the divisions will be advised of the same in advance. IOH and POH should be catered for and shown in the annual deployment programme. Scheduled maintenance activities could be combined with breakdown repairs wherever possible instead of idling the machine exclusively for such activities. (3) Track Machine Organisation will monitor the output of machines for quality and performance with respect to blocks given. (4) Track Machine Organization shall strive for development of its officials and staff to be technically sound, professionally competent, medically fit and safety conscious. All efforts shall be made to impart necessary training – technical as well as G&SR, road learning etc. timely and effectively. (5) Before giving the machine ready for block working, after daily schedule, the machine shall be checked as per stipulations of OEM’s manuals/RDSO instructions for ensuring trouble-free working. (6) Immediately after major schedules/repairs of the machine, performance of machine shall be closely monitored for the first few blocks. (7) In the event of breakdowns of machine in block, immediate action should be taken to rectify the defect. In case it is not possible to rectify the defect in the block, all efforts should be made to clear the block section as early as possible to avoid detention to trains. (8) Efforts shall be made to rush spares, staff and other assistance to site for immediate repairing of the machine. Division shall provide necessary assistance like transport of spares, welding equipment, gas cutting equipment, manpower etc. and assist in expediting the repairs. The objective is to reduce down time to minimum. (9) In case, it is necessary to bring the machine to satellite depot, division should ensure its expeditious movement to and from the depot. Decision on whether the 1 machine has to be brought to the depot for repairs shall be taken by Dy.CE/TM (line) considering relevant factors. (10) The track machines shall be worked as per divisionalised system of working with division managing all day to day affairs including fixation of roaster, minor repairs, arrangement of consumables, staff matters and ensuring suitable working conditions for track machine staff. There may be some variations among the zonal railways. (11) It shall be endeavour of Track Machine Organisation to utilize IT based applications to improve management of information of track machines. Modules for the same shall be provided in TMS to aim for paperless working. 102 Functions and Organisation (1) Functions of Track Machines Organisation -Track Machine Organisation (TMO) shall be under the overall charge of Chief Engineer/Track Machines (CE/TM) of the Zonal Railway. TMO shall be responsible for the following functions: (a) Manpower planning including training and development. (b) Planning, and deployment of track machines. (c) Operation and monitoring of track machines. (d) Repair and maintenance of track machines. (2) Organisation at Zonal Railway HQ (a) CE/TM shall be assisted by one or more Deputy Chief Engineer(s) at HQ , (b) Deputy Chief Engineer/TM/HQ in Headquarter shall be responsible for deployment of machines, finalization of AMCs, planned procurement of spares and consumables, co-ordination with division etc. He shall be assisted by XEN/AXEN/TM/HQ(s) and SSE/JE/TM/HQ(s) working in HQ office and HQ control. (3) Field Organisation on Zonal Railway (a) Deputy Chief Engineer/TM/Line, posted in Zonal Maintenance Depot, shall be responsible for operation and maintenance of machines including emergency repairs and procurement. He will ensure proper deployment of staff, initiation of proposal for AMC as well as that of procurement of spares and consumables. The maintenance workshops in Zone i.e. Zonal Maintenance Depots (ZMD) and Satellite Depots (SD) in the divisions shall also be under his control. He shall be assisted by XEN/AXEN/TM/D for ZMD and XEN/AXEN/TM/Line for Satellite Depots and for monitoring of machines in field. He shall also have a 24x7 control set up in ZMD office. (b) XEN/AXEN/TM/D shall be assisted by SSE/JE/TM/D(s). One of the SSE/TM/D shall be nominated as Depot in-charge called SSE/TM/DI, who in turn, shall be assisted by other SSE/JE/TM/D(s), MCMs, Track Machine Maintainers (TMMs) and Machine Assistants. 2 (c) XEN/AXEN/TM/Line will be assisted by SSE/TM /SDI who shall be in-charge of Satellite Depot and fleet of designated machines. He shall be assisted by SSE/JE/TM/SD, SSE/JE/TM(s) working on the Track Machines, MCMs, TMMs and Machine Assistants. SSE/JE/TM/SD can also be made in-charge of fleet of designated machines and will be assisted by SSE/JE/TM(s) working on the track machines, MCMs and TMMs and Machine Assistants. (d) Each machine will be manned by one or more SSE/JE/TM as per the yardsticks, of which one will be machine in-charge assisted by other SSE/JE/TM(s), MCMs, TMMs and Machine Assistants. (4) Central Periodic Overhauling (CPOH) Workshop (a) CPOH workshops will be setup on Indian Railways for carrying out Periodic Overhauling (POH) of Track Machines. These will function under CE/TM of the respective railway. (b) Deputy Chief Engineer/TM/CPOH shall be in charge of CPOH workshop and will be responsible for periodic overhauling of machines. He shall be assisted by XEN/AXEN/TM/CPOH(s) and SSE/JE/TM/CPOH(s), TMMs and Machine Assistants. 103 Duties of Executive (XEN)/Assistant Executive Engineer (AXEN)/TM/Line (1) General – He shall be responsible for operation and maintenance of all the track machines in his charge. He shall perform following duties: (a) Inspection and maintenance of all machines to ensure these being in a satisfactory, efficient and effective working condition. For this he shall ensure availability of tools & gadgets for inspection of the machines. (b) Ensure adherence to stipulated maintenance schedules. (c) Ensure availability of necessary staff, consumables and spares of fast wearing components and unit replacement assemblies etc. for the operation and optimum utilisation of machines. (d) Ensure achievement of stipulated targets in respect of both the quantity and quality of output. (e) Breakdown repairs shall be organised by him so as to ensure that idle time of machine is minimum. (f) Initiate proposals and plan for major schedules, ensure their execution and submit completion reports for all such works. He shall personally supervise important schedules and major repairs. (g) Ensure co-ordination with other units of Engineering Department as well as those of other departments as necessary. (h) Verification of stores held by the field units, once a year. He should ensure that scraps and obsolete stores are returned to the zonal depot or disposed off. 3 (i) Ensure maintenance of various records and submission of various returns pertaining to machines from the field units. (j) Satellite depot in the division will be under his control through SSE/JE/TM/SDI. (k) Training of Probationers – The Assistant/Executive Engineer shall take interest in training of all probationers sent to him and see that training is given according to the specified programme. He should periodically examine the notes made by them. (l) Staff Matters –He shall ensure that (i) Strict discipline is maintained within the framework of the rules. (ii) Service and leave records are maintained correctly and up-to-date. He will ensure this by sample checks. (iii) Appeals and representations are dealt with promptly and welfare of staff looked after. (iv) Assist Dy.CE/TM(Line) in selections for various skilled and semi-skilled posts so that the same are held in time and the posts are promptly filled up. (v) All the SSE/JEs and other staff working under him possess necessary medical, competency and other certificates, receive route learning and proper training in maintenance practices, safety and protection rules. (m) Ensure adoption of safe operation and maintenance practices and check availability and functioning of safety devices provided on the machines. (n) Ensure proper operation of Service Agreements in force. (o) Counselling of machine staff for immediate action to be taken in case of failure. (2) Observance of rules and regulations - He shall ensure observance of rules, regulations and procedures laid down in this Manual, G&S Rules, IRPW Manual, Engineering Code and other departmental codes, extant orders and circulars issued from time to time. He shall ensure that the staff under him possess these codes and manuals and are acquainted with the relevant rules of operation and maintenance procedures & stipulations connected with their duties and they perform duties, accordingly. (3) Inspection by higher officers - He shall accompany the higher officers during their inspections. Following records shall be made available by him during inspections: (a) History book of the machine, engine and major unit assemblies. (b) Failure registers. (c) Progress bar charts and analysis. (d) Unit cost statement. (e) Maintenance schedule register. 4 (f) Inspection notes of higher officers and compliance report. (g) Operation and maintenance instructions of the machines issued by OEM/RDSO. (h) Programme of deployment of machines. (i) Track Machine Manual and G&S Rules. (j) Record of the training given to supervisors and their competency certificates, road learning and medical certificates. (k) Scale and Position of critical spares and consumables. (l) Inspection checklist and maintenance schedule instruction issued by OEM/RDSO. 104 Duties of Senior Section Engineer/TM/SDI (1) SSE/TM (SDI) shall be responsible for the satisfactory operation, maintenance and productivity of the fleet of machines under his charge and quality of work performed. He shall inspect the machine(s) under his charge, as per laid down schedule and take remedial measures wherever required within reasonable time. He shall submit the report of inspection to his next higher authority. He shall be able to work/operate the machine(s) under his charge when needed and shall be in possession of valid competency certificate, road learning and medical certificate. He shall also ensure that the SSE/JE/TM working under him in the depot and on the track machines have valid competency certificates, road learning and medical certificates etc. (2) He shall be well acquainted with the working systems, operating instructions, maintenance schedules, specifications of the oils & lubricants to be used, critical components etc. of machine(s) under his charge. He shall have thorough knowledge of the manuals supplied by the manufacturers of the machines and associated instructions issued by RDSO. (3) He shall have thorough knowledge of the rules and regulations and procedures concerning his work and duties as laid down in this Manual, G&S Rules, IRPWM, Engineering Code and other departmental codes, extant orders and circulars issued from time to time. He shall guide all the staff working under him in faultless operation and efficient maintenance practices pertaining to the machines in his overall charge and educate them in rules and regulations. He shall ensure that the staff perform their duties efficiently. (4) He shall have in his possession up-to-date copies of the rule books/documents/manuals pertaining to the safe, efficient and trouble-free working of the machines and also other codes and books applicable and needed for the day-to-day working. (5) He shall maintain the records in the depot, pertaining to the machines under his charge and submit the prescribed returns regularly. He shall periodically verify the physical condition and quantities of stock in his charge and arrange to submit 5 periodical returns/requisitions of Tools & Plant, spares, consumables and other stores, carry out verification of all stores including spares held by him, assist in stock verification by Stock Verifiers, and ensure compliance of Account/Audit Reports etc. (6) He shall ensure discipline of the staff working under him within the framework of rules and endeavour to keep their moral high and look after their welfare. (7) He shall ensure proper handing over/taking over of the charge when transfer/change of portfolio is affected. (8) He shall plan and ensure timely execution of the maintenance schedules of the machines within the specified time. (9) He shall keep himself abreast of the various methods and techniques of reconditioning of components and availability status of spares at the Zonal Maintenance Depot for efficient re-commissioning of the machine during breakdowns. He shall render technical assistance to the higher authorities in developmental activities/import substitution and indigenisation activities. (10) He shall investigate major failures of the machine critically for corrective actions/remedial measures and also for fixing responsibilities in case of failures occurring due to lapses of staff. He shall obtain the first information reports during breakdowns, inspect the machines and take action for expeditious repairs. (11) He shall be conversant with the provisions in various Service Agreements/Contracts and organise the visits of Service Engineers (scheduled or break down). Effective utilisation of expert advice and follow-up action on “Service Report Observations” shall form part of his duties. 105 Duties of SSE/TM/SD - Where SSE/TM/SD is available in addition to SSE/TM/SDI depending upon the machine units attached to satellite depot, he will carry out all the duties assigned to SSE/TM/SDI for the fleet of machines assigned to him except those related to stores. He shall follow the instructions of SSE/TM/SDI for improving effective utilization of machines and such other duties assigned to him. 106 Duties of SSE/JE/TM working on machines - Each machine shall be worked under the direct charge of SSE/JE/TM during the movement and working of track machine. He shall be in possession of the valid competency certificate, road learning and medical fitness certificate for working the machine. He shall perform the following duties: (1) Operate the machine following the instructions issued by RDSO/OEM including calculation and input of data as required. (2) Carrying out pre-block maintenance daily as per schedule, other maintenance schedules, and making the machine fit for working and give machine ready memo to SSE/JE/P.way or station master. 6 (3) Ensure proper functioning of all the systems and components and keeping a watch on the controls/indicators/gauges. (4) Initial setting out for the block working and closing the work of the machine. (5) Taking precautions for Design Mode operations such as slewing, lifting etc. in case of tamping machines. (6) Deploying of MCMs, TMMs and Machine Assistants at respective places around the machine for monitoring the work of various systems, maintenance activities during block and also to attract attention of the SSE/JE/TM working in operating cabin and assist him in the event of malfunctioning of the machine or obstructions in track. (7) He shall ensure safety of staff working around the machine. (8) Participate in IOH and POH activities of the machine as required. (9) Assist SSE/JE/TM (in-charge) on the machine in all aspects of machine working and maintenance within his competency. 107 Duties of SSE/JE/Machine In-Charge - One of the SSE/JE/TM on the machine, shall be nominated as the machine-in-charge i.e. SSE/JE/TM/I. In addition to his normal work as detailed in Para 106 above, he shall be responsible for the following functions in which he will be assisted by all the staff posted on the machine: (1) Carrying out the prescribed schedule of maintenance and keeping proper records of the same. (2) Safe custody, accountal and replacement of the spares, Tools & Plants and consumables issued for the machine and returning of released spares to zonal depot for reclamation/condemnation. (3) Keeping systems of the machine in working condition and ensuring the target output, duly maintaining quality. (4) Maintaining log books and other records, sending daily and other periodical reports/statements using appropriate fastest mode of communication. (5) Liaison with the divisional officials and Engineering control for efficient working of his machine, co-ordination with the permanent way staff and planning daily programme of machine work and interacting with the permanent way staff for working e.g. working in design mode for slewing and lifting of track etc. (6) Actively associating during visit of firm’s Service Engineer, furnishing of such information as may be needed for proper examination of the machine and taking necessary follow up action. (7) Furnishing necessary reports to and keeping SSE/TM/SDI or SD informed as the case may be, about all the relevant aspects of the machines as also other records and details as asked by him and carry out necessary actions as directed for proper operation and maintenance of his machine. (8) In the event of breakdown of the machine, he will be responsible for setting right the defect in shortest possible time with the help of machine and other staff. In 7 case the machine cannot be repaired in the block, he shall be responsible for winding up using all resources including back-up systems and clear the block section as early as possible. He shall be assisted by SSE/JE/P.Way and demand the engine/breakdown train through SSE/JE/P.Way, if required, without undue delay. 108 Duties of SSE/JE/MCM/TMM in Control Set Up in HQ/ZMD/Division - The duties of the above staff in control offices are as given in Chapter 11. 109 Duties of Master Crafts Man (MCM) and Track Machine Maintainers (TMM) - MCMs and TMMs attached with the machine(s) shall assist the SSE/JE/TM in operation and maintenance of track machines. Their main functions are: (1) To attend to the daily and weekly maintenance schedules of machine and record the compliance in log book. To attend and assist service checks by the service engineers. (2) To attend to breakdown and repairs of machines in block with due urgency. (3) To keep in his custody the various tools, plants and equipment necessary to attend repairs and ensure their working condition. (4) To attend to the repairs and maintenance of machines including during IOH and POH. (5) To guide and supervise the machine assistants and other staff in attending to the maintenance/repairs. (6) To remain vigilant during movement and working of machine and to inform the concerned SSE/JE/TM of any abnormalities. (7) To ensure safety of the machine and staff working at machine site. (8) Accompany the machines during shifting as directed, especially T-28 machine and PQRS portals. (9) Any other work assigned to him by the SSE/JE/TM. (10) MCMs and TMMs posted in depots and work areas other than machines will perform duties assigned by their controlling officials. 110 Duties of Machine Assistant - He shall assist SSE/JE/TMs and TMMs in performing their functions and their main duties would be as below: (1) To keep the machine in neat and clean condition. (2) To replace spares like tamping tools as directed by SSE/JE/TM or TMMs. (3) To recoup HSD oil as required. (4) To assist TMM for carrying out daily and other specified schedule maintenance of track machine including that for IOH and POH. (5) Transportation of material, spares and consumables from depot to machine and vice versa. 8 (6) To bring all necessary tools and plants from coach to machine or otherwise as specified by TMM or machine-in-charge. (7) To be vigilant during machine working and promptly inform machine-in-charge regarding any obstruction in track viz. SEJ, Level Crossing, Bridge, joggled fish plates etc. boulders, rail pegs etc. so as to enable SSE/JE/TM to take necessary preventive action. (8) To warn for any abnormal sound, bursting of hose, breakage of any assembly etc. to machine-in-charge. (9) To assist machine-in-charge in attending the failure in shortest possible time. (10) Extend help during service check by service engineer. (11) Ensure safety of self and colleagues during block. (12) Perform duty of watchman for machine and coach, if required. (13) Accompany the machines during shifting as directed, especially T-28 machine and PQRS portals. (14) At the end of the day, facilitate safe/proper stabling of machine in siding. (15) Any other duties assigned by TMO officers or SSE/JE/TM or TMM. (16) Machine assistants posted in depots and work areas other than machines will perform duties assigned by their controlling officials. 111 Duties of Assistant Divisional Engineer (Open Line) ADEN - He shall perform following duties regarding track machines working in his section: (1) He shall ensure that the pre-requisites for introduction of various track machines as specified in this manual are complied with, well in advance of deployment of the machine(s). (2) In the stretches where the requirement of tamping is more than the normal tamping cycle, the cause should be analysed and suitable remedial action taken to restore the normal cycle. (3) He shall make arrangements for pre-block, during block and post block activities. (4) He shall ensure that machines are utilised in continuous stretches as per planned programme avoiding frequent shifting of the machines. (5) He shall ensure suitable accommodation for machine staff as required with the facility of water supply, power supply and resting arrangements. (6) He shall periodically inspect track machines working in his jurisdiction as per specified schedule. (7) He shall arrange HSD for machines including transportation of consumables, spares etc. required by the machines from the depot to site of work. (8) He shall ensure adequate lighting arrangements when night working of machines is involved. (9) He shall monitor the output and quality of work done by the machines. 9 (10) He shall co-ordinate with other departments like Traffic, OHE and S&T in the field to facilitate machine working. (11) In the eventuality of breakdown of machine, he shall take all possible actions to clear the block section expeditiously, once it is known that machine cannot be repaired in the block. 112 Duties of SSE/JE/P.Way Deployed with the Machine - He shall be the in-charge of the supervision of the work of track machine. He shall perform following duties: (1) He shall ensure that the pre-requisites for introduction of various track machines as specified in IRTMM are complied with, well in advance of deployment of the machine like collection of site details and computation of values to be fed for design mode of working. (2) He shall be responsible for pre-block operations, block operations (other than machine operation) and post block operations as detailed for various machines. (3) During working of track machines, he shall check the track parameters and condition of track, attending to any shortcomings, ensuring that the track parameters are well within the tolerances. He shall also ensure that track is free of obstructions and infringements for safe passage of traffic before clearing the line block. As required or stipulated he shall allow traffic at suitable speed restriction based on the condition of track after machine working. He shall be responsible for issue of all necessary caution orders for machine working. (4) Transportation of tamping tools to be reconditioned and bringing back reconditioned tamping tools will be his responsibility. Similarly, he will be responsible for temporary storage and timely arrangement and transportation of diesel oil, lube oil, hydraulic oil and other consumables from the depots to various machines working in his jurisdiction. (5) In case the quality of work done by the machine is not satisfactory, he shall investigate and take suitable remedial measures in coordination with SSE/JE/TM. (6) He is responsible for protection of the site of work and adjoining track wherever necessary. He will be responsible for arranging adequate precautionary measures for the safety of staff working with machine in the block section against danger of trains on the adjoining line(s). He shall arrange for track protection and provide look out men for safety at site. (7) He is responsible to ensure that the machine(s) are stabled in suitable sidings and at such stations as to minimise idle run of the machines as well as wastage of block hours in entering and clearing of the block section. (8) He shall provide all assistance to SSE/JE/TM for repairing of machine and winding up for expeditious clearing of the block section in case of failure of the track machines in mid-section, duly calling for necessary assistance of light engine, breakdown special etc. as necessary. 10 (9) He shall arrange for protecting and watching of stabled machines and he shall also ensure that no sick vehicles etc. are pushed into the same siding affecting the taking out of the machines to avail blocks. (10) He shall co-ordinate with other departments like Traffic, OHE and S&T in the field to facilitate working. PART B – INSPECTION OF TRACK MACHINES 113 Inspection Schedule of Track Machine Officials - Track machines shall be inspected as per prescribed schedule in accordance with detailed checklist of individual machines issued by RDSO. Periodicity of inspection for officers and supervisors of track machine shall be as given below: (1) Inspection by Officials of Track Machine Organisation Table 1.1 Track machine* Inspection frequency of Track Machine Officials Dy.CE/TM/ Line AXEN /XEN/ SSE/TM/SDI or SD TM/Line RGM 3 months (owning Monthly (owning Fortnightly railway) railway) (owning railway) Monthly (working Fortnightly Weekly (working railway) (working railway) railway) TRT 6 Months Monthly Fortnightly TLE/PCCM 1 Year 2 Months Fortnightly TEX/CSM/UNIMAT 1 Year 3 Months Monthly WST BCM/SBCM 1 Year 2 Months Monthly MPT/DTS/BRM/ Need Basis 4 Months 2 Months UTV/RBMV *The inspection schedule is for individual machine. e.g. if there are 3 BCMs under one division, then AEN/TM/Line shall inspect each BCM, once in 2 months The inspecting officials shall issue inspection reports to their concerned immediate subordinates with a copy marked to immediate concerned superior. 114 Inspection Schedule of Open Line Officials - The schedule of inspection of Track Machines for open line officials shall be as here under: 11 Table 1.2 Track Machine Inspection frequency of open line officials SSE (P.Way) in- JE (P.Way) Sr.DEN ADEN charge sectional TEX, CSM, DTS, 3 Fortnightly During supervision During supervision WST, UNIMAT Months of pre-block, of pre-block, during and SBCM during block and block and post- post-block works block works but RGM, TRT, TLE, 2 Fortnightly but not less than once a week not less than once PCCM and BCM Months a week Once during MPT, BRM, UTV, As per the RBMV etc. need deployment Sr. DEN/DEN and ADEN shall inspect the track machines as per above schedule, duly covering other aspects like, adequacy of all allied track works, quality of machine work, safety aspects involved, items pertaining to the welfare of machine staff, records such as programme of tamping, actual tamping, variations, repeated tamping, speed restriction etc. Copy of inspection report of ADEN shall be sent to AEN/TM/Line and that of Sr. DEN/DEN shall also be sent to Chief Engineer/TM and Deputy Chief Engineer/TM/Line and Dy.CE/TM/HQ in addition to concerned subordinate officials. 115 Items to be Inspected - RDSO has issued checklist for inspection of each type of track machine, which is available on the web site of RDSO. The list of the same is also given in Chapter 8. However, the broad list of items to be checked and inspected by track machine as well as open line officials is given below. (1) Inspecting Officials of TMO as well as Open Line (a) Pre Block Inspection - They shall reach the stabling siding or station at least one hour before the block time. They shall check the following: (i) Staff accommodation/facilities. (ii) Infrastructural facilities like sidings, rest house, water supply and electrical connection etc. (iii) Knowledge of safety rules of SSE/TM, MCM, TMM & machine assistants. (iv) Working of emergency backup system for clearing block in case of machine failure. (v) Adequate safety of staff working in block section against danger of incoming trains on adjacent lines. 12 (vi) Staff attendance. (vii) Checking of competency certificates, route learning and medical fitness of staff, issues of field staff. (viii) Records of the machine failures and general health of machine. (ix) Availability of Codes and manuals with latest correction slips. (x) Availability of safety items/equipment as per prescribed norms. (xi) Availability and expiry date of detonators, fire extinguisher and first aid box. (xii) Availability of machine deployment plan and the actual deployment vis-a-vis the plan. (xiii) Working of braking system. SSE/JE/P.Way shall inspect item (i) to (v). They will check the knowledge of safety rules for MCM, TMM and machine assistant. (b) During Block Working - Inspecting officials shall inspect working of the machine(s) and safety precautions and practices observed, during traffic block in addition to attention to pre-requisites, works to be done during and post machine-working activities. They shall record the results of their inspection and ensure compliance within a reasonable time. Immediate action shall be initiated in respect of areas where the condition of machine or track aspects needs quick attention. A report shall be submitted to the next higher authority at the end of every month indicating inspections carried out, deficiencies noticed and remedial actions taken. (c) Machine Specific Items - Items to be checked for different machines by TMO as well as open line officials are listed below: (i) TAMPERS Adequacy of track data required for the selected mode of working. Mode of working and its appropriateness. Condition of tamping tools. Tamping parameters like; tamping depth, squeezing time, squeezing pressure, vibration pressure. General lift, ramp in and ramp out, slew, lift, versine values, SE etc. Tamping quality. (ii) BCM Condition of cutting chain and its fingers. Condition of Screens. Pre-survey and removal of obstructions. Quality of screening and ballast distribution. 13 Waste conveyor safety switch operation. Width and depth of cutting of ballast profile. Safety precaution at closing of work. (iii) TRT Condition of BFR, gantry rail and bridge rail. Sleeper picking and laying system (NT and OT conveyor). Sleeper spacing system (Index wheel). (iv) BRM Functioning of all systems for dressing and distribution of ballast. Condition of broom and conveyor belt. Condition of different ploughs. Working of hopper system where provided. Quality of profiling done. (v) SBCM Condition of cutting chain and its cap. Condition of Screens. Screening width. Operations of waste conveyor safety switch. Quality of screening. (vi) TLE Proper laying of auxiliary track and its support system. Working mode and working speed of machine. Condition of BRNs. (vii) PCCM Function of motorized trolleys. Arrangement of wooden block support for crawler. Proper hooking of turnout. Condition of hooks and pins. Quality of laying (alignment) by machine. (viii) UTV/RBMV Condition of crane and its attachments for lifting materials. Availability of all specified tools and plant and their condition. Condition of BRNs. 14 (ix) RGM Condition of Grinding stone and spark arrestors. Check track data in GDMS format uploaded in machine, particularly direction of curve. Grinding inputs (pattern) and input system. Measurements at identified test locations wherever existing. Sufficient water in water wagon and its discharge system. Grinding quality and improvement in GQI. Cleaning of machine of iron dust and its proper disposal. Precautions at location of obstructions like points and crossing curve with checkrail etc. (x) DTS Frequency of Vibration and static load. Working mode and working speed. Track parameter after work. Precautions taken on bridges, tunnels etc. (2) Inspecting Officials of TMO- Additional items - Track Machine officials shall carry out inspections as per laid down schedule and in accordance with detailed check list issued by RDSO. Few important additional items to be checked are given below for guidance. (a) General (i) Details of work done since last POH, IOH, and adherence to other maintenance schedules of machines. (ii) Condition of camping coach. (iii) Availability of critical spares and consumables. (iv) Functioning of safety devices, control unit and measuring units and general cleanliness of the machine. (v) Tightness of the nuts and bolts of all moving and vibrating items. (vi) Availability of tools and plants. (vii) Follow up action on Service Engineer’s reports. (viii) Availability and proper maintaining of records. Log Book. History Book. Register of Periodical Maintenance Schedules. Critical Spare part List. 15 Failure register. Follow up action on Service Engineer’s reports. OEM manuals. (b) Engine (i) General condition of engine with respect to starting problem. (ii) Engine hours total, since last POH, and last attention given. (iii) Smoke condition. (iv) Belt condition and tension. (v) RPM. (vi) Oil pressure. (vii) Oil temperature. (viii) Oil leakages if any. (c) Hydraulic System (i) Measurement of hydraulic pressure of various units. (ii) Maximum hydraulic temperature. (iii) Condition of hydraulic cooler. (iv) Quality of fitment of hose assemblies, leakages. (v) Quality of hydraulic oil. (vi) Level of hydraulic oil etc. (d) Pneumatic System (i) Air pressure and leakages. (ii) Working of water separator. (iii) Functioning of air oiler and air dryer. (iv) Functioning of various valves. (v) Functioning of brakes. (vi) Condition of brake shoe and gap. (e) Electrical and Electronics (i) Condition of battery. (ii) Condition of self-starter and alternator. (iii) Condition of transducer. (iv) Condition of all gauges, meters. (v) Condition of lights, hooter. (vi) Condition of safety devices like limit switches etc. (vii) Condition of cable code and terminal code in junction box. 16 (f) Oil and Water Level – Level of oils like engine oil, diesel, transmission gearbox and other gearboxes oil, axles gear oil and coolant/water in radiator etc. (g) Filters – Replacement/cleaning of air filters, air dryer filters, diesel filters, hydraulic filters and lube oil filters as per schedule. (h) Lubrication (Oiling and Greasing) –Adequacy of oiling and greasing of all ball and socket joints, movable parts and cardon shaft as per schedule. (i) Specific Items to be seen in Different Machines – Following items specific to machines should also be checked in addition to that mentioned at Para 114 (1)(c) above: (i) TAMPERS – Condition of rail clamps, hooks, trolleys, tamping bank, tool tilting system, lining & lifting system, satellite, working of ALC, Laser, GVA system etc. (ii) BCM – Condition of cutter bar, screens, wear plates, corner rollers, turret gear, plough, conveyors belts etc. (iii) TRT – Condition and working of conveyer pads, sled, dynamic plough, clamping and guiding rollers etc. (iv) BRM – Condition of wear plates of different ploughs, rail top clearing, rubber elements etc. (v) SBCM – Condition of conveyor belts, tooth bucket & ditcher wheel etc. (vi) TLE – Condition of sleeper gripper, rail clamps, sliding frames, simplex and duplex chains etc. (vii) PCCM – Condition of clamps, sliding frames, crawler and trolleys etc. (viii) UTV/RBMV – Condition of outrigger and lifting capacity of crane. (ix) RGM – Grind modules tilting system, dust collection system, working of all grind motors and automatic system of its operation linked with grind stone, working of front and rear camera, functioning of obstruction detection system, working of buggy up and down system and its locking. (x) DTS- Roller clamp condition, working of vibration unit and preloading unit. (3) Inspecting Official of Open line - Additional Items - Open line officials shall look for the following items also in addition to those listed above: (a) Output of the machine vis-a-vis traffic block. (b) In Tampers, they should check tamping charts and check reasons and suggest for remedies to increase tamping cycle. (c) In BCM’s they shall ensure that depth of cutting is a judicious mix of lifting and excavation based on advance survey and proposed L-section. (d) Check benchmarks & reference marks and obligatory points. 17 CHAPTER 2 TAMPING MACHINE AND DYNAMIC TRACK STABILIZER 201 General - Purpose of tamping and stabilization of track (ballast bed) is to produce well compacted sleeper supports in order to improve the load distribution across sleepers, restore track to correct geometry and have long lasting retentivity of packing. Tamping machines are used for correcting the track geometry and tamp the ballast while Dynamic Track Stabilizer (DTS) is used for better anchoring of the track skeleton in the ballast bed to improve the durability of track geometry under running traffic. 202 Tamping machine - Tamping machine measures the existing track parameters and lifts it to enable correction of the cross level and alignment, to achieve target or pre-determined parameter values, with an aim to improve the track geometry. It simultaneously packs the ballast under sleeper(s), using tamping tools fitted on tamping unit, to provide well compacted ballast bed. (1) Functions - The main functions of tamping machines are- (a) Correction of alignment, (b) Correction of longitudinal and cross levels, (c) Tamping of ballast under the sleepers. Some of the tamping machines have additional fitments for track ballast stabilization also. (2) General Layout - General layout and important units of a tamping machine (09-32 CSM) are shown below- WORKING DIRECTION LEVELLING CHORD FRONT CABIN REAR/WORKING SATELLITE LIFTING AND LINING UNIT CABIN FRAME REAR BOGIE TAMPING FRONT TROLLEY REAR WHEEL LINING TROLLEY FRONT BOGIE UNIT TROLLEY MEASURING SATELLITE WHEEL TROLLEY Fig. 2.1 203 Important assemblies of tamping machines (1) Engine - Diesel engine is the main source of power. The engine converts chemical energy of fuel into mechanical energy, part of which is used directly 18 and remaining further converted into different forms of power for the working of machine. (a) Mechanical power through gear boxes - A part of mechanical power generated is used, by means of hydrodynamic gearboxes (in most of the machines), for movement of tamping machine. Remaining mechanical power is converted to other forms as mentioned below. (b) Hydraulic power through hydraulic pump - Hydraulic power is generated by means of hydraulic pump driven by mechanical power. It provides power for operations during working through various hydraulic motors and cylinders. (c) Pneumatic power through compressor - Pneumatic power is generated by means of compressor driven by mechanical power. It is used for brakes and locking/unlocking system of assemblies, up and down movements of feelers, operation of bogies for datum selection, horn operation and chord tension etc. (d) Electrical power through alternator and batteries - Electrical power is generated through alternator, or sourced from batteries. It is used to provide electrical power for sensing devices, feedback of corrected parameters, signals to hydraulic units, like directional valves, proportional valve and servo valve for operations. (2) Tamping units - Two or more independent tamping units are provided in tamping machine (one or more for each rail depending on the make and model of the tamper). These are mounted on the machine frame by means of vertical guiding columns. In some of the machines, the tamping units are fitted to the satellite frame. The tamping units on Indian Railways have the capability for tamping one/two/three sleepers at a time depending upon type and model of the tamping machine. The tools are arranged in pairs and each of the two sides of sleeper is tamped by four such pairs, four numbers on either side of each rail. The units are held on horizontal guide columns in order to slide sideways, which allow their manual/automatic centering over the rails in curves. The tools are vibrated by piston rods pivoted on eccentric shaft driven by hydraulic motors. A typical layout of tamping unit and its different components are shown as Fig 2.2 The lifting and lowering of tamping units is achieved by means of a hydraulic tamping units lifting/ lowering cylinder. The insertion depth of tamping tools and squeezing pressure can be varied for different types of sleepers. In case of simultaneous tamping of double/triple sleepers, the opening width of tamping tools can be changed pneumatically by changing the clapper piece to suit the sleeper opening and by pneumatic operation of clapper cylinders for joint sleepers. 19 1. TAMPING BANK 7. PLATE GUARD 2. CENTER PIN 8. CLAPPER CYLINDER 3. BIG TAMPING ARM 9. SQUEEZING PLATE 4. BIG SQUEEZING CYLINDER 10. SMALL SQUEEZING CYLINDER 5. GUIDE ROD 11. SMALL TAMPING ARM 6. OIL BATH 12. TAMPING TOOL Fig. 2.2 (3) Tamping Tool - The size & shape of the blade of tamping tool has a bearing on the quality of compaction (tamping) of ballast. The size of tamping tools differs, depending on model/make of tamping machine. Tamping tool with carbide shield called Tungsten Carbide Tamping Tool (TCTT) are now being used for improving the performance of tools. The positions of tamping tools (TCTT) for various machines with important dimensions are depicted at Annexure 2.1. (4) Lifting and Lining unit - The lifting and lining unit is positioned in front of the tamping units. Lifting is carried out using one lifting cylinder with the help of roller clamps/hook on each side. The lining operation starts simultaneously with the lifting operation. As soon as the target values are reached, lining and lifting operations are automatically stopped. (5) Satellite unit - Continuous sleeper tamping machines have tamping & lifting cum lining unit, provided on the separate unit called satellite unit. Satellite unit is placed on an independent under-frame, which is mounted on wheels. 20 It can move independent of the main frame, capable of cyclic movement from sleeper to sleeper. (6) Trolleys - These are wheels mounted units provided with sensing feelers used for measurement and correction of the track parameters. Four trolleys are used in tamping machine, which are- front trolley, lining trolley, height transducer trolley, measuring trolley and rear trolley. (7) Brake system - Following types of braking system are provided on tamping machine- (a) Direct brake- It is applied only on machine during transit. (b) Indirect brake-This brake is used for application on machine and coupled camping coach/wagon while running. This brake system is provided in machines with KE valve. KE valve is available in all new tamping machines. It works with single piping system. (c) Emergency brake- This brake is applied on machine during transit alone or coupled with camping coach/wagon only when KE valve is in ‘ON’ position. It is applied through indirect brake system. (d) Safety brake- This brake is applied automatically by switching off hydrodynamic transmission gear (ZF Gear in Plasser machines). Normally this should not be used for service brake application. (e) Parking brake- This is hand operated mechanical brake, applied when machine is stabled. 204 Types of tamping machines (1) Tampers without Satellite unit - The tamping unit and the lifting cum lining unit are mounted on the main frame of the machine itself. The machine moves and stops at every sleeper for lining, levelling and tamping. One to two sleepers can be tamped simultaneously in one operation. Following machines fall in this category. (a) Duomatic (Plain Track Tamper) - It is a Plain track tamper and with 32 tamping tools to pack two sleepers at a time. These machines are also referred as Work Site Tampers (WST) for purpose of nomenclature. The names of the models of Duomatic tamping machines presently in use on Indian Railways; and the name of manufacturer, are given below- (i) 08-32 Duomatic (Plasser India). (ii) 08-32C Duomatic (Plasser India). (iii) 08-32 WST with flat car(Metex–JSC Moscow, Russia). (iv) VPR-02M without fl