7/1 Apparatus General PDF
Document Details
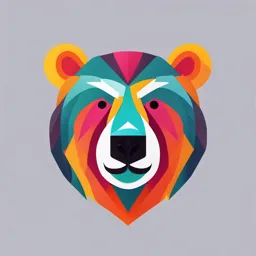
Uploaded by FancyDalmatianJasper
LAFD
Tags
Related
- Chesapeake Fire Department Apparatus/Vehicle Backing Policy PDF
- Apparatus Driving Safety PDF
- Bridgeport Fire Department Safety Belts PDF
- 207.002 Apparatus Backing Policy (Fresno Fire Department) PDF
- Fresno Fire Department Apparatus Startup and Shut Down Procedures PDF
- Spring Fire Department Self-Contained Breathing Apparatus Guidelines (SFD.066) PDF
Summary
This document provides information on various procedures and knowledge related to fire department apparatus operation and maintenance. It covers topics like required knowledge for apparatus operation and maintenance, official business use of apparatus, and driving procedures.
Full Transcript
7/1 APPARATUS GENERAL 1 7/1 APPARATUS GENERAL 7/1 APPARATUS/GENERAL -01. GENERAL.01 REQUIRED KNOWLEDGE Members whose duties may require them to operate and maintain engine and truck ap...
7/1 APPARATUS GENERAL 1 7/1 APPARATUS GENERAL 7/1 APPARATUS/GENERAL -01. GENERAL.01 REQUIRED KNOWLEDGE Members whose duties may require them to operate and maintain engine and truck apparatus shall possess a working knowledge of driving, pumping, and aerial ladder operation for all such apparatus. In addition, members shall be completely familiar with the operation of the apparatus assigned to their station. This includes limitations, restrictions, operating procedures and proper maintenance. Department publications (i.e., Apparatus Operator's Training Manual, pertinent log books, etc.) shall be referred to for the proper operation and maintenance of apparatus..12 REQUIRED KNOWLEDGE - HYDRAULICS All members shall have a thorough knowledge of the methods used to produce effective fire streams (refer to lessons 9 through 12 in the Apparatus Operator's Training Manual)..24 OFFICIAL BUSINESS Department apparatus is to be used only for official business of the Department. Visitors will be permitted to ride on Department apparatus only when the proper approval is obtained (refer to Vol. 5, 9/7-00.00 Visitor Waiver, F-1109)..36 REQUIRED KNOWLEDGE - DRIVING A. Firefighters shall complete a Driver's Training Program consisting of a written exam administered by the Division Driver Training Coordinator covering modules 1 through 8 in the Driver's Training Manual, and Chapters 3, 4 and 22 of the A.O.T.M. prior to advancement to Firefighter III. B. Prior to any member operating Department apparatus non-emergency or for training purposes, the concerned Company Commander shall ensure that: 1. Member has received the required training as specified in paragraph A. 2. Member holds a valid driver's license or learner's permit for the class of apparatus member is to operate. 3. A certified driver shall accompany non-certified members driving or practicing with any heavy apparatus. 4. Apparatus will be operated in proximity to the location where the apparatus is currently housed. 5. Members are in proper uniform and wearing Department-approved safety equipment. C. Prior to any member operating an aerial ladder truck or triple combination engine during an emergency without supervision, the Company Commander shall ensure that the member has completed the Certification Program for Aerial and/or Pumping Operations in the Drivers Training Manual, Book 8, Section 3. D. Apparatus traveling either emergency or non-emergency shall be operated with due caution, with particular emphasis placed on defensive driving. Any time apparatus or quarters are changed, station commanders shall cause a careful check to be made of height, length, width and angles of entry and departure for clearance and safety. Special attention shall be paid to parking markers which shall be moved as needed to fit newly assigned apparatus. 7/1 APPARATUS GENERAL 2.40 TRACTOR TRANSPORTS Surface streets shall be used by tractor transports carrying D-7 or D-8 dozers when they are operating non-emergency. The Equipment Engineering Unit will obtain the necessary permits from the City and County of Los Angeles allowing the tractor transports with D-7 or D-8 dozers aboard to legally operate non-emergency on surface streets..42 OFF-STREET PARKING If it becomes necessary to use off-street parking facilities for heavy duty apparatus during non-emergency operations, concerned members shall give consideration to the following: The condition of the paving on the lot, congestion within the lot, sufficient room for safe maneuvering of apparatus, and any inconvenience caused to the public. Members using off-street parking facilities with any Department vehicle shall park only in areas designated for public parking, avoid parking in a cramped or misaligned slot, and use good defensive driving tactics while maneuvering within parking lots..44 PARKING AT FIRE DEPARTMENT EMPLOYEE SERVICE/SUPPORT ORGANIZATIONS: Members shall not use Department emergency apparatus for visits or business at Fire Department employee service/support organization offices or facilities. Emergency apparatus includes heavy apparatus, rescue ambulances, and light vehicles equipped with “emergency light bars”. In all cases, members utilizing Department non-emergency vehicles, shall operate and park them in accordance with Department procedures and motor vehicle laws..48 SAFETY BELTS Seat belts shall be used by drivers and passengers during ALL driving operations..60 APPARATUS OFF-DUTY Station Commanders shall not allow apparatus to be taken off duty without first receiving permission from their Battalion Commander and Metro. Apparatus is not considered off duty under conditions where response could be made without a delay of more than 60 seconds..72 LOGBOOKS Operational and/or Service logbooks, where furnished for apparatus, shall be maintained according to instructions set forth in the logbook. Service records for apparatus not provided with logbooks shall be maintained in accordance with the system in effect at their places of assignment. An accurate, complete and up-to-date record of tires, lubrication, inventory, battery condition, mechanical work done and all other pertinent information concerning the history of the apparatus shall be maintained in the Service logbook. Changes made to apparatus which cause information in the logbook to become obsolete or in error shall be reported promptly. Officers concerned shall immediately notify Supply and Maintenance Division, Training and Support Bureau, using the Form F-225. F-225 Forward As indicated To Supply & Maintenance Division, Training and Support Bureau Number of Copies One Routing Forward to the Supply & Maintenance Division, Training and Support Bureau 7/1 APPARATUS GENERAL 3 Information Required A factual statement of the circumstances that caused the logbook instructions or information to become obsolete. Completed logbook record sheets which are not necessary to retain as part of apparatus history will be discarded..84 LOGBOOKS - WHERE CARRIED Logbooks will not be carried on apparatus, but will be kept in quarters at a place designated by the Station Commander. EXCEPTION: Logbooks shall accompany apparatus when assigned to relief duty, when going to the Shops for annual pump or ladder test, or when transferred..90 LOGBOOKS - LOST Station Commanders shall request replacement of lost logbooks by submitting an F-225. Forward As indicated To Bureau Commander, through channels Number of Copies Two Routing Bureau Commander to Supply and Maintenance Division, duplicate returned to point of origin. Information Required The circumstances surrounding the loss, the make, year and type of apparatus covered. -12. ACCIDENT.01 ACCIDENT PROCEDURE PACKET - F-620 An F-620 packet shall be carried on Department apparatus at all times. Each fire station will have two extra packets. A member using a privately owned vehicle in a manner which may be considered as Department business shall carry one of the extra packets..14 ACCIDENT PROCEDURE Reports are required whether apparatus is damaged or not. TYPE OF ACCIDENT REPORTS REQUIRED REPORTS INITIATED BY a. Department apparatus or personal car used on Department business 1. Form Gen. 88 (fill out 1. Driver Involved with civilian car, or property, of a third party; or; completely at scene) b. Department apparatus or personal car involved with Fire Department property or; 2. Form Gen. 84B 2. Civilian-Witness (License number, c. Department apparatus or personal car used on Department business if name not available) involved with a domestic animal or a non-domestic animal. 3. F-150 3. Investigating Officer 4. F-80 (See E below) 4. Station Commander A. CALL METRO AND PROVIDE THE FOLLOWING: 1. Exact location of accident. 2. Shop number, type and assignment of apparatus. 7/1 APPARATUS GENERAL 4 3. Number of injured no matter how slight. If injury is serious or fatal, call on land line only. Give names and assignments of injured Department personnel (refer to Vol. 2, 4/6-80.84). 4. Amount of damage. 5. Type of assistance needed. 6. Request Commanding Officer to be notified. 7. Request Fire Department investigating officer. 8. Request Police traffic investigation for all third party accidents. B. MOVING APPARATUS INVOLVED: 1. Members shall use good judgment in moving vehicles prior to the arrival of the investigators. Normally apparatus will not be moved until pictures have been taken by Police investigating officers. 2. If an accident occurs during an emergency response and members and apparatus are in a safe condition to proceed, response may be continued. Leave member to obtain necessary information and to give assistance. Advise Metro of your action. C. OBTAIN DATA FOR REPORTS (refer to Department Bulletin No. 10-12). D. ASSIST INVESTIGATORS: 1. Cooperate fully with Fire, Police or City Attorney investigators. 2. Make no statements either written or verbal to anyone except authorized investigators in accordance with AB-220 (Firefighter Bill of Rights). 3. Necessary photographs of the accident will be taken by police officers dispatched to the scene. The Fire Department investigating officer may, in unusual circumstances, request a Fire Department photographer to respond if additional photographs of the accident would be beneficial for Department training, planning, etc. 4. If the other parties involved in the accident refuse to remain at the scene after being requested to await the arrival of responding investigators, obtain as much information as possible, but do not threaten nor attempt to forcefully restrain them. E. In all cases, where Fire Department apparatus is damaged, a requisition must be forwarded with other required reports (refer to Volume 4, 8/3-40.45)..72 TESTING EQUIPMENT AFTER ACCIDENTS Apparatus damaged in an accident, other than body or fenders, shall be placed temporarily off-duty pending a thorough examination of any working parts which may have been involved. This examination shall be made by the Company Commander or a Chief Officer. When possible, apparatus may be moved to a more convenient location for this examination. If a Department vehicle is involved in an accident with a third party, the Chief Officer will, depending upon the extent of the damage, take one of the following courses of action: A. If vehicle remains operable and does not jeopardize the safety of members involved with its use, vehicle will be returned to its quarters and the Supply and Maintenance Division will be notified. The Supply and Maintenance Division shall send a representative to make a cost estimate of the damage. B. If, however, the vehicle is damaged to the extent that it may jeopardize the safety of the members involved, it will be driven or towed to the Supply and Maintenance Division for cost estimate and repairs. 7/1 APPARATUS GENERAL 5.96 DEPARTMENT OF MOTOR VEHICLES NOTICE (SR-1C) Members who are involved in a traffic accident while driving in the course and scope of their employment and who receive communications from the Department of Motor Vehicles regarding that accident (Form SR-1C) shall not complete or sign any form or response. Any forms or correspondence from the D.M.V. shall be sent through channels, to the Emergency Services Bureau, for forwarding to the office of the City Attorney. The member shall not take any further action unless/until contacted by the Emergency Services Bureau or the City Attorney. -24. EQUIPMENT ON APPARATUS.01 GENERAL Members shall not change or alter the arrangements of firefighting equipment on apparatus, nor otherwise rearrange the system in effect without approval of the Fire Chief..12 DEFECTIVE EQUIPMENT Defects in equipment shall be reported immediately by all members concerned to their immediate superior. Repair or replacement of equipment shall be made in accordance with procedures in Vol. 4, 8/3-00.00, Services & Supplies/Services..24 PRIVATE USE OF EQUIPMENT Department tools and equipment, i.e., rectifiers, hydraulic hoists, air compressors, etc., shall be used for departmental purposes only..36 MARKING EQUIPMENT Refer to Vol. 3, 6/11-50.00, Equipment/General..48 INVENTORY OF EQUIPMENT ON APPARATUS Refer to Vol. 4, 8/8-55.40..60 REQUIRED OPERATIONAL CHECKS The following equipment shall be checked as required. The result of such checks shall be recorded on the F-973, Apparatus and Equipment Check Record. A. PORTABLE RADIOS Portable radios shall be checked in accordance with instructions set forth in Vol. 2, 4/7-90.60, Routine Operations/ Communications. B. PORTABLE GASOLINE ENGINES All portable gasoline engines shall be started and run until heated at least once each week. Detailed instructions for checking most equipment having gasoline engines can be found in the apparatus log book of the apparatus to which the equipment is assigned. C. DRY CHEMICAL EXTINGUISHERS Dry chemical extinguishers shall be maintained and serviced as set forth in Vol. 3, 6/11-01.90, Equipment/General. D. CO2 EXTINGUISHERS CO2 extinguishers carried on apparatus shall be checked in accordance with instructions in Vol. 3, 6/2-03.00, Tools and Equipment. The weight will be entered in the appropriate column of the F-973. E. COMBUSTIBLE GAS INDICATORS 7/1 APPARATUS GENERAL 6 Combustible gas indicators shall be checked monthly in accordance with operating instructions. F. RADIOLOGICAL INSTRUMENTS Radiological instruments shall be checked monthly in accordance with instructions in Vol. 3, 6/11-75.00, Equipment/General. G. RUBBER GAUNTLET GLOVES Rubber gauntlet gloves shall be field tested after each use and weekly, as part of the Monday checks as set forth in Vol. 3, 6/2-01.52. In addition, every 60 days gloves are to be tested with 10,000 volts of electricity by the Department of Water and Power. 72. TRANSPORTATION OF MATERIALS Any member who transports material or equipment in a Department vehicle will be held responsible for the safety of the vehicle and the items being transported. Items being transported shall be tied or otherwise secured to prevent damage to materials, equipment or vehicle..80 MOVING APPARATUS - DISLODGED ITEMS Whenever an equipment item is dislodged or dropped from moving apparatus, members shall at that time cause the officer or member in charge to be notified of the loss. The officer or member in charge will consider the urgency of the situation and the significance of the lost item and, if possible, stop and retrieve the item..84 ADDITIONAL INFORMATION For additional information regarding equipment, refer to Vol. 3, 6/2-00.00, Tools and Equipment. -36. DRIVER TRAINING.01 DEPARTMENT DRIVER'S TRAINING SPECIALIST One Captain assigned to the In-Service Training Section shall be designated as the Department Driver's Training Specialist. Duties will be to advise and support the designated Department Driver's Training instructors. The In-Service Training Section Engineer and Apparatus Operator shall assist with development and implementation of training programs for the safe operation and driving of Department apparatus..20 DEPARTMENT DRIVING INSTRUCTORS The following persons shall be designated Driving Instructors: All information pending, In-Service Training Section will provide in the future..30 DIVISION DRIVER TRAINING COORDINATOR Division Driver Training Coordinators shall: All information pending, In-Service Training Section will provide in the future..36 BATTALION DRIVER TRAINING INSTRUCTOR The Battalion Driver Training Instructor shall: All information pending, In-Service Training Section will provide in the future. 7/1 APPARATUS GENERAL 7.38 CLASS "'A" DRIVER TRAINING INSTRUCTOR The Tractor Operators assigned as Driver Training Instructors shall: A. Implement the Department Driver Training Program as it relates to Class "A" vehicles. B. Train approved members in the operation of Class "A" vehicles. C. Administer driving exams for the issuance of Class "A" licenses at the direction of the Commander, Bureau of Fire Suppression and Rescue..40 STATION COMMANDERS Station Commanders shall conduct training sessions for the purpose of maintaining proficiency of members under their command in: All information pending, In-Service Training Section will provide in the future..50 DRIVER REACTION APTITUDE TESTING The In-Service Training Section, is updating this section in the future..60 APPARATUS TILLER TRAINING When a member is learning to tiller, a minimum of three training sessions shall be held with the trainee placed in an observer position behind a Firefighter certified to tiller. This will enable the trainee to get more of a feel of what is expected of the Tiller position before being actually placed in the position of tillering the aerial. It shall be the Captain's responsibility to personally ascertain the readiness of a member to progress in the learning phase of driving and tillering in traffic situations. When the Captain determines the member is ready to tiller after at least three observer rides, the Captain shall ensure that a Firefighter certified to tiller is in the position of observer. While in the observer position, the member shall be secured to the truck by means of a safety belt. New members are naturally under greater pressure to do well than a Firefighter who is off probation. This "extra" pressure and the member's ability to handle it shall be taken into consideration before a probationary Firefighter is allowed to tiller..70 OFF-DUTY PRACTICING ON RESERVE HEAVY APPARATUS Any member who desires to make use of the Department's fleet of reserve apparatus for training purposes, while off-duty, must be under the direct supervision of a volunteer member certified on the requested apparatus. Members having held or currently holding the rank of Apparatus Operator or Engineer are deemed to be certified to drive all heavy apparatus. Requesting members shall: 1. Schedule practice sessions with the concerned Station Commander. 2. Be thoroughly familiar with F-620 Accident Packet, Apparatus Log Book, and apparatus procedures as stated in the Manual of Operation and the Apparatus Operator's Training Manual. 3. Perform appropriate preventative maintenance checks before and after each session. 4. Be responsible for proper cleaning of apparatus upon completion of each session. 5. Be wearing the work uniform and have full protective gear in their possession. Station Commanders will have the authority to grant or deny requests according to criteria developed between all shifts with the first consideration being the safety of personnel and apparatus. The second consideration will be providing equal opportunity for all members. Station Commanders shall: 1. Journalize the name, assignment and certification of the volunteer member and the name and assignment of the members practicing. 2. Ensure that a certified tillerman is utilized when operating aerial ladder trucks. 7/1 APPARATUS GENERAL 8 3. Ensure that any member receiving permission to operate a vehicle can do so in a safe manner. Each training session shall be limited to one hour per member and confined to the first alarm district of the Station where the apparatus is housed. -48. MAINTENANCE OF APPARATUS.01 DEFECTIVE APPARATUS Defects in apparatus will be promptly reported by all members concerned. If the defect has not been remedied by the time of platoon change, the Station Commander concerned shall make a written memorandum concerning the defect and hand it to the oncoming Station Commander, supplemented by any verbal instructions necessary..06 REPAIRS Care and operation of apparatus shall be in accordance with Department manuals, log books and instructions received from the Supply and Maintenance Division. No other repairs, adjustments or alterations shall be made by company members without authorization from the Supply and Maintenance Division. For repairs, alteration, maintenance, or additional information, refer to Vol. 4, 8/3-00.00, Service and Supplies/ Services..13 PAINT “Paint applied in less than ideal conditions often causes more harm than good.” All apparatus purchased by the LAFD must meet strict specifications including painting requirements. The high quality paint applied to the undercarriage by the manufacturer is designed to provide the necessary protection for the life of the apparatus. Most paint applied by Fire Department members over the factory paint does not adhere as well and subsequently flakes or peels off, particularly when it is pressure washed. Members shall not paint the undercarriage of apparatus or any portion thereof, except as noted: Paint may be applied to bare metal, but only when needed to protect surfaces from corrosion. No spray painting of apparatus is allowed except by Supply & Maintenance personnel. Supply & Maintenance personnel will inspect apparatus undercarriage paint during annual test. Members may request apparatus undercarriage painting through the Supply Requisition System according to the instructions in the Manual of Operations, 8/7-20.49. After evaluation, personnel assigned to Supply & Maintenance will paint apparatus undercarriages as necessary..16 ENGINE HEATERS Engine Heaters of apparatus so equipped shall be operated at all times in quarters and in service..19 ITEMS NOT TO BE PAINTED Members shall not apply paint to any part of the apparatus or tools, if such painting might hinder their operation. Examples: A. Magnetos or parts of magnetos B. Distributors C. High tension wires D. Spark plugs E. Timing marks on flywheels F. Adjustment threads on brake rods G. Brake cables and yokes H. Clutch linkage and adjustment nuts I. Carburetors 7/1 APPARATUS GENERAL 9 J. Radiator Hose K. Bright Work L. Working parts of governors and relief valves, and any linkage thereof..26 CLEANING APPARATUS Cleaning is the best method of visual and tactile inspection.10 SAFETY CONCERNS Wear appropriate protective equipment: goggles, gloves, coveralls etc. Pressure washers are dangerous and can cause an “injection” injury where foreign material is injected under the skin. Members should read the manual and be familiar with the safe and proper application of any equipment they are using, particularly power washing equipment..20 CLEAN AT A STATION WITH A CLAFIFIER Each station was required to create a Stormwater Pollution Prevention Plan (SWPP), and post that plan on the official bulletin board. Members can refer to their station’s plan for specific information about runoff. Apparatus undercarriage cleaning creates runoff with significant contamination, and must be performed at a location where runoff is collected in a clarifier. A list of municipal clarifiers is included as Part VI of Training Bulletin #127. Company Commanders and Battalion Commanders should provide CAV time for undercarriage cleaning when possible, and may need to adjust inspection schedules to accommodate cleaning. It is expected that major undercarriage cleaning will be done when the company is CAV. In cases where this is not possible, and undercarriage cleaning must be done while the company is available, Company Commanders shall monitor cleaning activities to prevent conditions that could delay a response. When companies have been placed CAV for undercarriage cleaning, the Company Commander shall ensure that the apparatus is able to safely respond and members are clean and ready for response prior to making the company available. This policy shall not prohibit members from performing follow-up cleaning, or cleaning of small areas of the undercarriage as part of their ongoing maintenance duties, while the company is in service..30 CHEMICALS ALLOWED AND PROHIBITED Members shall not use any equipment that creates an aerosol spray of any flammable liquids such as kerosene. The approved product for undercarriage cleaning is available through SRS from Supply and Maintenance. It is listed in the catalog as: “degreaser, gunk type.” Inspection component While cleaning, members should keep in mind that one of the most important aspects of cleaning apparatus is the thorough visual and hands on inspection. It is through this process that many problems can be detected and corrected before they become severe and cause collateral damage or a catastrophic failure. The use of pressure washers can force water into areas that are intended to contain only grease, and grease is forced out of those areas. Members should avoid directing high-pressure spray at rubber seals. Prompt lubrication can correct the problem before corrosion damages bearings, splines, kingpins, etc. In all cases where power washers are used, lubrication should be done the same day cleaning takes place, and in no case later than the next day. Negative impact of power washing Although power washing can be an effective method of removing dirt, grease and other contaminants, it is not a replacement for the hands-on approach. Members are encouraged to follow up any pressure washing with a thorough wiping and inspection of the various components of the apparatus. Members using power wash equipment shall avoid injection of highpressure water into boots, seals, bearings, and electrical components. Although all of these specific areas are susceptible to damage by injection of water, the most significant damage to apparatus from 7/1 APPARATUS GENERAL 10 pressure washers occurs when water is sprayed into electrical and electronic components such as the alternator, diodes, wiring connectors, and engine control electronics. Members shall be extra cautious to protect these areas and prevent damage of this type. Areas to avoid with power washers High-pressure water can damage many of the components. Do not directly spray the following components: Alternators Diodes Electronics Electrical connectors Electronic throttle behind pump panel Indications of abuse with power washers When pressure washers are operated at excessive pressure settings, several telltale signs may be observed including: Paint stripping Water in lube areas Erosion of softer materials Water in sealed electrical components.40 COMMERCIAL STEAM CLEANERS Station personnel are prohibited from using industrial steam cleaners. Supply and Maintenance personnel are permitted to use steam cleaners..30 LUBRICATION “In most areas, too little lube is far worse than too much.” Safety Concerns Members should take all necessary precautions to protect themselves from hot surfaces, sharp objects and contamination, as well as electrical hazards when working under apparatus. Alert other members to not move or operate apparatus. When to perform lubrication: Members shall adhere to appararatus lubrication schedules outlined in Training Bulletin #127, and shall provide additional lubrication as necessary after cleaning or repair. Lubrication products Chevron “Black Pearl” chassis grease Aqualube for Fire Pumps Engine oil 15-40 Transmission oil (only to be handled by shops) Differential oil (only to be handled by shops) Negative impact of power lube equipment (Use power lube equipment with a maximum air pressure of 60 psi.) Boots on steering components tear when overpressurized Excessive pressure will permanently distort seals Areas to be lubed with hand pumped lube guns only: All steering connections with rubber “boots” Any failure of boots on TAK 4 independent suspension should be promptly reported to Supply & Maintenance for repair or replacement. Clutch Throwout bearings 7/1 APPARATUS GENERAL 11 Use of powered lube equipment here can over-lube the bearing and cause grease to collect on the clutch and pressure plate. Rubber Seals on Bearings Seals that are damaged will allow grease to leak excessively and unevenness could allow water to remain inside. Zerk fittings Zerk or “Alemite” fittings provided for attachment of lube equipment should be wiped clean prior to attaching the lube equipment to prevent forcing contaminants into the area being lubricated. Evacuation of water and old grease When lubricating apparatus after pressure washing, members should be careful to ensure that all water is evacuated from lubrication spaces. Likewise, grease should be forced out until the grease appears free of contaminants..32 APPARATUS PREVENTATIVE MAINTENANCE Station Commanders shall ensure that sufficient time is allotted on a routine basis for the proper care and maintenance of apparatus. Station Commanders of stations housing reserve apparatus shall develop a schedule of apparatus preventative maintenance and lubrication and shall forward to Battalion for approval. Once approved, the schedule shall be posted as an element of the station's apparatus maintenance schedule and included in the Apparatus Log Book. All preventative maintenance and lubrication shall be accomplished during the first two weeks of the appropriate month. F-377's and F-377RA's shall arrive in the Battalion Office no later than the day prior to battalion inspection, or the 15th of the month, whichever comes first. The Battalion Commander shall initial the F-377/ F-377RA and shall return it to the station on the day of inspection for inclusion in the log book. A. Front-Line Emergency Heavy Apparatus Heavy Apparatus have an engine displacement of 465 cubic inches and greater. Lubrication and F-377 Preventative Maintenance Heavy Apparatus shall be lubricated based on the company's annual mileage, not the apparatus' annual mileage. If the company travels more than 12,000 miles annually, the apparatus currently in use shall be lubricated monthly during the first two weeks of the month. Companies that travel less than 12,000 miles annually shall be lubricated once every two months on the even months. An F-377 shall be completed bi-monthly on even months during the first two weeks of the appropriate month and shall arrive in the Battalion Office no later than the day prior to Battalion inspection or the 15th of the month, whichever comes first. The F-377 shall be returned by the Battalion Commander at inspection for inclusion in the apparatus log book. Oil Change Heavy Apparatus shall have the oil changed every 4,000 apparatus miles. Oil Filter The oil filter shall be changed annually by Supply and Maintenance during the Annual Pump or Aerial Ladder Test. Aerial Ladders Aerial ladders and related components shall be lubricated a minimum of every two months or sooner if needed due to high use, i.e., high activity, training, apparatus operator practicals, etc. One of the lubrications may be in preparation for the Annual Ladder Test. Battalion Commanders shall be notified on the shift before the ladder is to be lubricated so that it may be inspected during the lubrication process. B. Front-Line Emergency Light Apparatus Emergency Light Apparatus have an engine displacement of less than 465 cubic inches. Lubrication and F-377 Preventative Maintenance Emergency Light Apparatus shall be lubricated based on the company's annual mileage, not the apparatus' annual mileage. If the company travels more than 12,000 miles annually, the apparatus currently in use shall be lubricated monthly during the first two weeks of the month. Companies that travel less than 12,000 miles annually shall be lubricated once every two months during the first two weeks of the month on odd months. An F-377 shall be completed on front-line Emergency 7/1 APPARATUS GENERAL 12 Light Apparatus bi-monthly on odd months during the first two weeks of the appropriate month and shall arrive in the Battalion Office no later than the day prior to Battalion inspection or the 15th of the month, whichever comes first. The F-377 shall be returned by the Battalion Commander at inspection for inclusion in the apparatus log book. F-377RAAn F-377RA shall be completed monthly on all rescue ambulances, both front-line and reserve, during the first two weeks of each month. The F-377RA shall be forwarded to the appropriate Battalion Commander and arrive in the Battalion Office no later than the day prior to Battalion inspection or the 15th of the month, whichever comes first. Oil and Filter The oil and filter on Emergency Light Apparatus shall be changed every 4,000 apparatus miles. C. Reserve Apparatus and Non-Emergency Light Apparatus Station commanders of stations housing reserve apparatus and non-emergency light apparatus, i.e., plug buggy, etc., shall develop a schedule of reserve apparatus preventative maintenance and lubrication and forward to the Battalion Commander for approval. Approved copies shall be posted as an element of the station's apparatus maintenance schedule, one copy filed at Battalion, and one copy filed in the apparatus log book. At no time shall apparatus preventative maintenance (F-377) or lubrication exceed four months except with the approval of the Battalion Commander. ANYTIME A RESERVE APPARATUS IS PLACED IN RELIEF, IT SHALL BE MAINTAINED AND LUBRICATED ACCORDING TO THE SCHEDULE OF THE FRONT-LINE APPARATUS IT REPLACED. LubricationBoth Reserve Heavy and Reserve Light Apparatus shall be lubricated every four months. Oil Change Reserve Heavy and Reserve Light Apparatus shall have the oil changed every 4,000 miles or 6 months. Oil Filter Reserve Heavy Apparatus shall have the filter changed annually at the Pump/Aerial Test. Reserve Light Apparatus shall have the filter changed at each oil change. F-377RA An F-377RA shall be completed on all reserve rescue ambulances each month. See "Front-Line Emergency Light Apparatus" for specific instructions. F-377 An F-377 shall be completed on reserve apparatus once every two months according to the schedule developed by the Station Commander. At no time shall apparatus preventative maintenance (F-377) exceed two months except with the approval of the Battalion Commander. Aerial Ladders (Reserve) Aerial ladders and related components shall be lubricated every two months, one of which may be in preparation for the Annual Ladder Test. Battalion Commanders shall be notified on the shift before the ladder is to be lubricated so that it may be inspected during the lubrication process. D. Non-Emergency Light Apparatus Non-Emergency Light Apparatus shall be maintained according to the following requirements utilizing the schedule developed by the station commander. Lubrication Non-Emergency Light Apparatus shall be lubricated once every four months. Oil and Filter Change The oil and filter shall be changed every 4,000 apparatus miles. E. Specialized Apparatus Station Commanders requesting modified maintenance schedules for specialized apparatus shall forward written requests direct to the Supply and Maintenance Division Commander, with recommendations and justifications. Approved copies shall be maintained in the Apparatus Log Book, posted as an element of the station's apparatus maintenance schedule, and a copy at the Battalion Office. 7/1 APPARATUS GENERAL 13.35 AUTOMATIC TRANSMISSION Heavy apparatus equipped with automatic transmissions shall be serviced in accordance with instructions in the log books and as follows: A. Transmission fluid and filter will be changed by the Shops annually at the scheduled aerial ladder and pump test, or at any time requested, if debris, discoloration, or a burnt odor indicate fluid deterioration. B. Transmission fluid level and condition shall be checked weekly and in compliance with instructions in the F-377, Bi-Monthly Preventive Maintenance Record Instructions..36 COOLING SYSTEM COOLANT Heavy apparatus cooling system coolant will be diagnostically tested by the Test Engineer as a part of the Annual Pump and Aerial Ladder Tests. If the test results indicate substandard or unfit coolant, a complete cooling system flush will be done and fresh coolant added. Heavy apparatus cooling system coolant shall also be tested bi-monthly in accordance with the F-377 Bi-Monthly Preventive Maintenance Instructions and the station test kit instructions. Diluted cooling system coolant shall be reported to the Shop Office (Ext. 6111). They will arrange for coolant additive to be sent to the station. Proper concentration of coolant additive shall be ensured by a subsequent coolant test. At any time coolant is found to exhibit scale, rust, oil film, or other contaminants, the condition shall be reported to the Shop Office (Ext. 6111) and arrangements made for a cooling system flush. Lubrication is based on Annual Company miles not apparatus miles. F-377’s shall be completed during the first 2 weeks of the appropriate month or the day before Battalion inspection, whichever comes first. Notify B/C when lubricating Aerial. 7/1 APPARATUS GENERAL 14.39 AIR BRAKES Apparatus equipped with air brakes shall be serviced in accordance with instructions in log books and as follows: A. Air tanks shall be thoroughly bled on a weekly basis, preferably on each Monday morning. During inclement weather, tanks may need to be drained daily. B. Repair for leaking air brake systems shall be requested when the low pressure warning device operates when the apparatus has not been run for 12 hours or less. C. System shall be checked at least each 2 months to determine if an adjustment is needed. Refer to "Service Log Book" for proper procedure..45 BATTERIES Members shall use good judgment and initiative in conserving batteries during periods of extended operation, taking into consideration the capabilities of alternators and conventional generators. When a battery becomes discharged beyond use during emergency operations, the fact will be reported to the incident commander. Batteries for in service rescue ambulance apparatus should be connected to chargers at all times when the apparatus is in quarters..52 TIRES - CARE OF Tires shall be brushed following each daytime run. Tires must be examined closely for damage. If they are muddy or dirty, they should be washed with a minimum of water. For additional information regarding tires, refer to Vol. 4, 8/3-40.80..56 AUTOMATIC DOOR LOCKS Members shall visually check vehicles equipped with automatic door locks to ensure proper operation of the automatic door locks each morning after change of platoon, when relieving another member, and at other times as necessary to ensure the security of the apparatus (e.g.,hospital transports, emergency operations, when apparatus is left unattended, etc). When members are confronted with automatic door locks that are defective, they shall immediately contact the Supply and Maintenance Division and be guided by their instructions. Members shall manually lock apparatus equipped with malfunctioning automatic door locks. When out of quarters and not at the scene of an incident, ignition keys are to be removed from the vehicle and secured by the driver. All members share a responsibility to ensuring apparatus security anytime the apparatus is left unattended..58 APPARATUS WATER TANK - FILLING Before water tanks are filled, the caps must be removed. Damage to water tanks can be eliminated if they are filled slowly..65 FLUSHING Pumping mechanisms, engine cooling systems, or any other equipment in which salt water or foam has been used, must be thoroughly flushed or cleaned with fresh water after use..71 DRAFTING DRILLS Before engaging in drafting drills, pump operators and Company Commanders shall determine that water does not contain sand or other abrasive material, and that the suction strainer is free from obstructions. Strainer end of suction shall be kept at least 12" from bottom of reservoir and 24" or more below the surface of the water. At fires where this cannot be done, reasonable precautions will be taken, if at all possible, to draw only clean water into the pump. 7/1 APPARATUS GENERAL 15.84 APPARATUS CHECKS - ROAD CHECKS The following apparatus shall be road checked at least once each month: A. Reserve apparatus B. Service utilities C. Foam carriers D. Transportation rigs E. Light utilities F. Gasoline truck G. Buses H. Field command truck I. Communications truck J. Air utility truck K. Helicopter tenders L. Seldom used on-duty apparatus as determined by the Station Commander The F-973 shall be used to record road checks for the apparatus listed in the previous column. Refer to Vol. 5, 9/7-00.00, F-973..86 APPARATUS CHECKS-POWER ACCESSORIES Pumps, aerial ladders, and other power operated features shall be operated on all apparatus at least once each thirty days. The F-974 shall be used to record these checks..89 ANNUAL SERVICE TESTS Members will be notified of the time and place they are to report with apparatus for the annual service test..91 ELECTRICAL Members shall adhere to the following policy regarding electrical components on automotive apparatus: A. Repairs may be made by members, but they shall be reported to the Supply and Maintenance Division and a follow-up inspection may be made by a Department mechanic. Such repairs of work normally consists of the following: 1. Loose or broken wires. 2. Replacement of fuses other than radio fuses. B. Installation of light bulbs from the stock maintained at quarters may be made by members. C. Maintenance of spark plugs is to be done by replacement when needed and at annual performance test. D. Members shall not adjust distributor, breaker points or ignition timing. 7/1 APPARATUS GENERAL 16 -60. GAS AND OIL.01 GENERAL A Company Commander shall personally supervise the filling of the house supply tanks. In addition, each Monday morning a Company Commander shall cause the house fuel storage tank to be checked and shall reorder fuel when necessary. Refer to Vol. 4, 8/7-80.01. This procedure shall be followed to prevent water and contaminants in station fuel tanks: A. Always refuel all apparatus prior to receiving a new load of gasoline or diesel fuel. B. After a fuel delivery has been made, wait twelve hours before pumping gasoline, and twenty-four hours before pumping diesel fuel. C. Clear the cavity around the fill pipe of all dirt and water prior to refilling the station fuel tank. D. If water is suspected in a station fuel tank, handle as an emergency repair. Public Buildings will make a check of the tank using water detecting paste. Refer to Vol. 4, 8/3-80.12 B.1..10 AQMD AND WASTEWATER COMPLIANCE INSPECTIONS Each Monday fuel dispensers and oil separator/clarifiers shall be inspected. Contact Fire Facilities for repair and Underground Tank Unit for technical advice on fuel systems. A. Dispenser and nozzle assembly - Check vapor hose to ensure that it is not torn, cut or crimped. The retractor operates correctly and the boot is not torn or missing. Also check for loose spouts, latching devices, nozzle leaks correct signs, etc. B. Underground storage tanks - Check the tank fill, poppet valve and vapor caps for serviceability, gaskets and water leaks. Also check to ensure that the tank fill tube is in place and tank vents are not damaged. The gasoline overfill container should be checked to ensure it is not dirty or full. C. Stations with oil separator/clarifiers - must be reset after each rain. Notify Building/Administration when wastewater needs to be removed..25 GASOLINE In addition to its recognized fire hazard, all gasoline used in Department operations contains tetraethyl lead which is poisonous by skin absorption and vapor inhalation and has a cumulative effect. It shall be used for motor fuel only..59 REFUELING AT FIRE STATIONS During refueling of apparatus, extreme caution shall be exercised. Smoking shall not be permitted within 25 feet of gasoline pumps or the motor vehicle being refueled. No petroleum supplies in Fire Department custody shall be dispensed to other than Fire Department vehicles or equipment. Exception If city vehicles belonging to other Departments are out of fuel, officers may provide a sufficient quantity for the vehicle to reach its own garage. When gasoline is dispensed directly from the gasoline pump to a gasoline tank of a motor vehicle, the entire apparatus shall be removed from the building. If this is impossible, the vehicle shall be removed from the building so the fuel tank, and as much of the apparatus as possible, are outside. When gasoline is dispensed to a chain saw engine, generator, or like equipment, the filling of the gasoline tank shall be done outside of buildings. Whenever a container is used to dispense gasoline, it shall be a safety can. When gasoline is dispensed from a gasoline pump to a safety can, the can shall be outside of the building. If it is impossible to follow the above orders in any manner, a request for the deviation shall be made in writing to the Fire Chief. 7/1 APPARATUS GENERAL 17.75 USED OIL & OTHER WASTE PETROLEUM PRODUCTS A. Used engine oil and other petroleum products shall not be put into the same waste drum. B. Used engine oil only shall be put in waste oil drums. C. Other waste petroleum products shall be disposed of in a separate waste product drum. This drum shall contain the label(s) of all products put into it. D. Disposal - Arrangement for the disposal of all hazardous waste generated by Department facilities will be handled by Supply and Maintenance. When waste oil drums or other miscellaneous hazardous waste containers are filled, Station Commanders shall call the "Storeroom Counter" (5-6124) at Supply and Maintenance and request that a pick up be made..80 SMALL ENGINE GASOLINE USE Responsible officers shall ensure that all fuel used in small portable gasoline engines meets the following criteria. A. 4-cycle engine - gasoline only B. 2-cycle engines - gasoline and 2-cycle 50-to-1 oil premix only C. Engines shall have fuel tanks drained every 30 days and replenished with fresh fuel. NOTE Disposal of unused fuel shall be accomplished by pouring it in the fuel tanks of gasoline powered vehicles. D. Fuel tanks of small engines shall be drained before sending the equipment to S & M for repair..82 IDENTIFICATION OF CONTAINERS Responsible officers shall ensure that fuel safety containers for small engines are identified in accordance with the following policy: A. 4-cycle: All 4-cycle safety containers shall be painted red and marked "4-CYCLE". B. 2-cycle: All 2-cycle safety containers shall be painted yellow and marked "2-CYCLE"..84 GASOLINE-POWERED EQUIPMENT FUEL TANK IDENTIFICATION All fuel tanks on gasoline-powered equipment shall be painted and marked to correspond with the gasoline and storage container identification delineated in 7/1-60.82..87 TWO-CYCLE OIL Company Commanders shall personally see that two-cycle portable gasoline powered equipment carried on apparatus use the 50-to-1 oil and gasoline mixture provided by Supply and Maintenance. The following procedures must be adhered to: A. For greater engine efficiency, fresh 50-to-1 fuel shall be mixed every 30 days and placed in the portable equipment. 7/1 APPARATUS GENERAL 18.88 FUEL MIXTURE (50-TO-1 OIL) With five gallons of gasoline, add 16 ounces of 50-to-1 oil. With one gallon of gasoline, add three ounces of 50-to-1 oil. A. Required mixing method: Use the required container and fill it half full with gasoline, then add the 50-to-1 outboard oil. Complete the operation by filling the container with gasoline, securing the cap on the container and shaking it vigorously to obtain a compatible mixture. B. Supply: Single fire stations should mix a one-gallon supply at a time and hold the remaining oil in reserve. Task Force stations should mix a five-gallon supply at a time and hold the remaining oil in reserve..90 HOLMATRO RESCUE TOOL Refer to Training Bulletin #67 Holmatro Rescue Tool -72. RESERVE AND RELIEF APPARATUS.01 DEFINITIONS Reserve Apparatus A piece of apparatus maintained on a stand-by basis to temporarily replace or augment first line apparatus. Relief Apparatus A reserve apparatus which is temporarily assigned to replace a piece of first-line apparatus. Ready Reserve Engine A reserve engine apparatus which includes a full complement of hose, fittings, tools, breathing apparatus, portable radios, and EMS equipment. Note These engines are designed to provide surge capacity during high hazard days, emergency recall, and redeployment of staff personnel. Appropriate use of a Ready Reserve Engine includes cases where a company may put the apparatus in service while their first-line apparatus is at pump test, in and out repairs, etc. Ready Reserve Engines are normally used for short-term immediate need only. However, there may be instances when they are deployed for extended periods of time. They shall not be used in place of a Reserve Apparatus when a change over is necessary. Ready Reserve Rescue Ambulance A reserve rescue ambulance which includes a full complement of BLS ambulance equipment. Note These ambulances are designed to provide surge capacity for mass casualty incidents and other medical emergencies. They shall not be used in place of reserve apparatus when a change over is necessary. In addition to the supplies in these ambulances, Advanced Life Support (ALS) medical supply caches are available and secured in the medical supply office at Supply and Maintenance in the event the Ready Reserve Ambulances will be deployed as a paramedic ambulance. 7/1 APPARATUS GENERAL 19.15 IDENTIFICATION Reserve apparatus shall be identified in numerical sequence regardless of where they are regularly assigned. 1. Reserve Engines - "400" series numbering (i.e., Engine 401, 402, Engine 403, etc.). 2. Reserve Trucks - Numbered starting with "500" (i.e., Truck 501, Truck 502, Truck 503, etc.). 3. Reserve Ambulances - Numbered starting with "600" (i.e., Rescue 601, Rescue 602, Rescue 603, etc.). 4. Reserve Aircraft Firefighting Apparatus and Special Reserves - Numbered starting with "700" (i.e., Foam 780, Crash 780, Heavy Rescue 789). Note Any apparatus in the Shops for repair may be activated (as needed) during large scale emergencies. Before activating, apparatus shall be determined mechanically sound and safe to operate by Shops' personnel and will be identified by numbering "701" through "712" (i.e., Engine 702, Rescue Ambulance 711). 5. Anytime a "reserve" apparatus is placed into "relief", the visual ID signs from the first-line apparatus will be placed on the relief apparatus. The signs from the reserve apparatus will be stored in a safe location in quarters where the reserve apparatus is normally assigned. Responsible officers shall insure that when the relief apparatus is returned to reserve status, the visual ID numbers are replaced. EXAMPLE "RESERVE 411" in relief for "ENGINE 11" will be identified as "11". The apparatus going to the Shops for repair will not be identified with visual ID signs..25 ROSTER A roster of all reserve apparatus in the Department and its current location is maintained at Metropolitan Fire Communications. Metro shall be notified whenever reserve apparatus is assigned as relief or of any other circumstance that may alter its status. In addition, each Saturday morning before 0800 hours, any commander or individual having a reserve apparatus in service as a relief, or the commander of any station having a reserve apparatus in quarters in reserve, shall so notify Metro..50 CARE OF When reserve or special apparatus is placed in service or returned to its regular quarters, it shall be inspected to determine that the equipment is complete and that the apparatus is clean. Entries shall be made on the logbook copy of the F-974. In addition, when it is found that the apparatus is damaged, dirty or that the inventory is not complete, Station Commanders concerned shall make an immediate report by telephone to their Battalion Commander. -78. HOME GARAGED VEHICLES.01 GENERAL City vehicles are purchased and made available to department personnel to conduct City business. Normally, City vehicles are garaged at department work locations. Sometimes it is necessary to garage vehicles at decentralized locations within the City or at an employee's residence. Authority to regularly garage a City vehicle at a decentralized location is granted based on the needs of the department, such as the lack of secure overnight parking at the employee's regular work location. Authority to regularly home-garage a City vehicle is granted to designated Fire Department essential personnel and to personnel working in a position with on-call responsibilities. Home garaging is a cost effective way to provide emergency response by department members for emergency situations in the City. Members may be assigned to any function within the National Incident Management System (NIMS). 7/1 APPARATUS GENERAL 20 Citizens and taxpayers quickly notice and criticize the unauthorized and improper use of City-owned automobiles. The use of these vehicles must be confined strictly to the business of the City..06 DEFINITIONS DEFINITIONS City Vehicle A motor vehicle, purchased by and for the Fire Department, over which the Department has direction and control. Decentralized A location, other than a regular work location, where a City vehicle is garaged during off-duty hours. Garage Home Garage A location, at or near the employee's residence, where the City vehicle will be garaged during off-duty hours. On-Call Special duty personnel who are subject to call-out where direct response serves the public interest. Employees who, because of Personnel their individual expertise, their use of specialized equipment or the assignment of a specially equipped vehicle are, without prior notice, required to respond, due to an emergency incident. Regular Work The location where the department requires the member to report for work at the beginning of each workday. Location.12 ADMINISTRATIVE PROCEDURES FOR DECENTRALIZED GARAGING Requests to garage a department vehicle at a decentralized location (not at the regular work location) shall be submitted on an F-225 through channels to Operations for approval. Approved requests will be forwarded to Supply & Maintenance Division and a copy of the approved request shall be provided to the requestor. The following information shall be included in the request: 1. Regular work location. 2. Department vehicle shop number. 3. Location where vehicle is to be garaged. 4. Facility manager's approval. If the facility is a Fire Station, then approval must be obtained from the Station Commander on each platoon. 5. Brief narrative describing the reason that decentralized garaging is necessary..18 ADMINISTRATIVE PROCEDURES FOR HOME GARAGING The Operations Commander shall designate essential personnel and positions with on-call responsibility by Departmental Bulletin annually by August 1. The following information shall be provided by personnel issued home-garaged vehicles to the Supply and Maintenance Division annually by September 1, or when information changes: 1. Completed Form CAO 34 (Enter vehicle shop number in the "Special Equipment" box). 2. Proof that the employee is covered by a standard automobile liability insurance policy (as evidenced on a certificate of insurance or policy declaration page, bearing an original signature, which shows the limits and coverage) or is the named insured on a non-owned automobile insurance policy if the employee does not own a vehicle. Temporary requests to home-garage a department vehicle shall be submitted on an F-225 through channels to the Operations Commander. The following information shall be included in the request: 1. Regular work location. 2. Department vehicle shop number. 3. Location where vehicle will be home garaged. 4. Duration (start date / end date) that vehicle will be home garaged. 5. Justification / benefit to the Department for the home garaging request. 7/1 APPARATUS GENERAL 21 6. Completed Form CAO 34 (Enter vehicle shop number in the "Special Equipment" box. Proof that the employee is covered by a standard automobile liability insurance policy (as evidenced on a certificate). Approved requests will be forwarded to Supply & Maintenance Division to be filed and a copy of the approved request shall be provided to the requestor..24 CARE AND MAINTENANCE Personnel approved for home or decentralized garaging shall maintain vehicles according to the procedures set forth in Volume 3, Section 710 of the Manual of Operation and Rules and Regulations, Section 8-b. Home-garaged vehicles should be parked in a garage, carport, or driveway and not left on a public or private street or alley. Appropriate security should be provided to protect the vehicle and its contents..32 VEHICLE OPERATION Personnel authorized to home-garage or decentralized-garage a Department vehicle shall operate the vehicle in a prudent and responsible manner and not impugn the reputation of the Department. Members should be cognizant of how they drive, where they park, and the impression they portray to the public, so as not to bring discredit upon the Department. All members having the responsibility of driving City vehicles shall do so in a safe manner with due regard for the welfare of the public and the Department. When members are on-call they shall be available for rapid response should they be called back. On-call shall require that the person and assigned vehicle remain within 50 miles from the City. Travel shall be by the most reasonable, direct route available to meet department objectives. Recalled members will normally respond non-emergency unless otherwise directed. The red light and siren may be used to access fire lines or restricted areas. The use of City vehicles is restricted to transportation to and from the member's work location and for Department related activities. Vehicles should only be driven by authorized City employees and passengers should be limited to City employees or other persons incidental to City business. To ensure that City vehicles are readily available for response while on-call, short local trips may be made and non-department personnel may be passengers if it will not delay response or bring discredit to the Department. Personnel who cannot meet the responsibilities for on-call response shall find a qualified replacement (short or long term) and make appropriate notification to the Metro Floor Captain and the on-call IMT leader. -84. APPARATUS IDENTIFICATION.01 GENERAL Front line apparatus shall be identified with numbers using white reflective adhesive material affixed directly to the apparatus as follows: a. Front: 7 ½” b. Rear: 7 ½” c. Side: 9” d. Top: 15 ¾” Supply and Maintenance Division shall be the sole reflective number, lettering, striping provider for Department apparatus. Fire Stations shall not alter apparatus number, lettering or striping. Magnetic numbers shall continue to be used to identify reserve apparatus placed in relief. Community titles designating areas served will also be solely provided by Supply and Maintenance. Reflective lettering used for this purpose shall be 4 ¼” tall, contrasting color, and be placed on the 6” reflective stripe on each side of the apparatus. Community designators shall be pre-approved by the Commander of the Bureau of Emergency Services. (Requests shall be forwarded in F-225 format through channels). 7/1 APPARATUS GENERAL 22.50 SYMBOLS A. The following symbols will precede company numerical designation and/or assignment number (*except where indicated): AR Arson Investigation Unit BP Brush Patrol CP Command Post – Community Activity Resource CR Airport Crash Rescue D Dozer (* designated as D1, D2,) DT Dozer Tender (* designated at DT1, DT2,) E Engine FM Airport Foam FT Foam Tender HM Hazardous Materials HR Heavy Rescue RA Rescue Ambulance (Paramedic or Basic Life Support) RAT Rehab Air Tender (replaces Emergency Air & Food Service Utility) SW Swift Water Rescue T Truck TP Tractor Transport (*designated as TP 1, TP 2…) TT Triage Trailer TU Tunnel Utility UR Urban Search & Rescue WT Water Tender Apparatus not identified as exceptions to assignment identification above, (e.g., D1, D2), shall be identified with assignment number as follows: Aerial Trucks (example): T1 Ambulances: RA1 Battalion Commanders: B1 Engine Companies: E1 Engine (second triple): E201 Reserve Engines: “400” series numbering, E401 Reserve Trucks: “500” series numbering, T501 Reserve Ambulances: “600” series numbering, RA601 Misc.: Identification numbering for specified combinations of resources, (e.g., Strike Teams, Tactical Task Forces, etc.) is referenced in Manual of Operations, Emergency Operations/General, Resource Types. 7/1 APPARATUS GENERAL 23 -90. SCHEDULING NON-EMERGENCY HELICOPTER FLIGHTS.01 GENERAL The Fire Chief is the authority to approve non-emergency use of Fire Department helicopters. For specified purposes, that authority has been delegated to appropriate levels within the Department. The following identifies the approving authority for various non-emergency uses of the Department's helicopters: A. Fire Chief: 1. Requests for all flights that include civilians, elected officials, or other City personnel shall be directed to the Office of the Fire Chief for approval. This does not apply to Fire Department civilian employees. 2. Mayor's Directive No. 7 states, "In cases when any other City department may want to use a Fire Department helicopter because of its specialized equipment, passenger capacity, or lift capability, such use must be authorized in advance by the Mayor or his designee." The Fire Chief or Acting Fire Chief would approve all requests after authorization per the Mayor's directive. All such requests shall be submitted to the Fire Chief or the Acting Fire Chief for review and final approval. 3. All other requests not otherwise identified in this policy shall be directed to the Fire Chief for consideration. NOTE After business hours, Metro must be contacted to obtain approval for these flights from the Fire Chief or Deputy Department Commander. B. Assistant Bureau Commander, Emergency Services Bureau: 1. The Assistant Bureau Commander, Emergency Services Bureau, is the approving authority for requests originating within the Department for needs arising out of the conduct of Department business. These flights will only be approved for uniformed and civilian members of the Department who have a specific need to perform their duties, i.e., drills, surveys, aerial photographing, mapping, etc. 2. Officers/members shall obtain permission from their Division Commander, Section Commander, or civilian supervisor prior to requesting authorization for these flights from the Assistant Bureau Commander, Emergency Services Bureau. 3. After business hours, Metro must be contacted to obtain approval for these flights from the Deputy Department Commander. C. Commander, Air Operations: The Commander of Air Operations is the approving authority for all flights originating as a result of pilot and/or helitac training..10 REQUESTS A. Telephone, verbal, and written requests (submitted at least five (5) days prior to the requested flight) shall include the following information: 1. Date and time of flight. 2. Pickup location. 3. Name and rank of requesting member. 4. Name and rank of approving authority. 5. Names and title of passengers, if not Department members. 6. Number of passengers. 7. Destination. 8. Mission. 7/1 APPARATUS GENERAL 24 9. Location of any landings. 10. Estimated duration of mission. In order to permit proper planning of helicopter operations, verbal approval for verification of helicopter availability may be obtained prior to submission of requests. Helicopter flights, once approved, may be coordinated directly with Air Operations. When notified of flight approval, Air Operations will place the flight on the flight schedule. Air Operations shall be notified of any cancellation or change of flight plans as soon as possible. References http:/ / lafdtraining. org/ ists/ tb067v0608. pdf Article Sources and Contributors 25 Article Sources and Contributors 7/1 APPARATUS GENERAL Source: http://lafd.info/index.php?oldid=13435 Contributors: RBARNA, Sjoseph Image Sources, Licenses and Contributors image:vol3mainchart.png Source: http://lafd.info/index.php?title=File:Vol3mainchart.png License: unknown Contributors: RBARNA