Spring Fire Department Self-Contained Breathing Apparatus Guidelines (SFD.066) PDF
Document Details
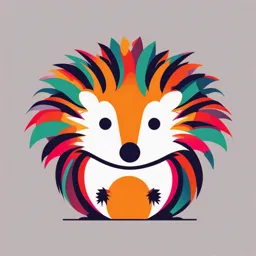
Uploaded by ExemplaryMinotaur
Spring Fire Department
2022
Tags
Related
- Respiratory Protection Program PDF
- Spring Fire Department Guidelines - Self-Contained Breathing Apparatus PDF (SFD.066.REV1)
- Hoffman Estates Fire Department Safety Guidelines - 2022 PDF
- Hoffman Estates Fire Department PDF - Emergencies Involving Asbestos
- Spring Fire Department Self-Contained Breathing Apparatus Guidelines PDF
- Spring Fire Department Post-Incident Air Monitoring Guideline PDF, 2024
Summary
This document outlines guidelines for the selection, use, and maintenance of Self-Contained Breathing Apparatus (SCBA) in the Spring Fire Department. It details risk assessments, responsibilities, and procedures for SCBA inspection, cleaning, and storage. The guidelines adhere to relevant NFPA standards.
Full Transcript
Manual Name: Document Number: Spring Fire Department Guidelines SFD.066 Document Title: Date: 01/21/2022 Self-Contained Breathing Apparatus Chief’s Sign...
Manual Name: Document Number: Spring Fire Department Guidelines SFD.066 Document Title: Date: 01/21/2022 Self-Contained Breathing Apparatus Chief’s Signature: Revision Number: 01 PURPOSE This guideline establishes a respiratory protection program as required by the Occupational Safety and Health Administration (OSHA) 29 CFR 1910.134, as well as the American National Standard for Respiratory protection, ANSI Z88.2.This guideline provides specific guidance concerning the selection, use, replacement, inspection, cleaning and maintenance of Respiratory Equipment as required by the Texas Commission on Fire Protection, and NFPA standards 1852, 1982, and 1989. SCOPE All Spring Fire Department personnel are responsible for knowing and complying with this guideline. REVIEW The Fire Chief or designee is responsible for reviewing this guideline annually and assuring its accuracy. DEFINITIONS Air-Supplied Respirators (SCBA): An air-supplied respirator provides a supply of breathable air from a clean source outside of the contaminated work area. Self-Contained Breathing Apparatus (SCBA): a device worn by rescue workers, firefighters, and others to provide breathable air in an IDLH atmosphere. Personal Protective Ensemble (PPE): Department issued structural firefighting helmet, hood, coat, pants, boots, and gloves. Self-contained breathing apparatus (SCBA) with face piece is also part of this ensemble and is to be worn anytime a member enters an IDLH atmosphere or it is deemed necessary by the Incident Commander (IC). Hazard Area: An area where members may be struck by flying/falling objects. This area would include the immediate area around a structure or operation. Hazardous atmospheres, particular substances, devices, events, circumstances or conditions that present a safety hazard to members of the fire department or public. Hazardous Atmosphere: Any atmosphere that is deficient of oxygen, contains toxins or disease- producing contaminants. A hazardous atmosphere may or may not be considered an IDLH atmosphere. IDLH atmosphere: An atmosphere which is immediately dangerous to life and health. This atmosphere is likely to cause death or immediate or delayed permanent adverse health effects or prevent escape from such an environment. Incident Commander (IC): The fire department member in overall command of an emergency incident. Page 1 of 9 Manual Name: Document Number: Spring Fire Department Guidelines SFD.066 Document Title: Date: 01/21/2022 Self-Contained Breathing Apparatus Revision Number: 01 CBRN: Chemical, Biological, Radiological, Nuclear. NFPA 1852: Standard on selection, care and maintenance of open-circuit self-contained breathing apparatus. NFPA 1981: Standard on open-circuit self-contained breathing apparatus (SCBA) for emergency services. NFPA 1982: Standard on personal alert safety systems. NFPA 1989: Standard on breathing air quality for emergency services respiratory protection GUIDELINE Risk Assessment In determining risk, Spring Fire Department will consider the expected hazards that can be encountered by users of the SCBA based on the type of duties performed, frequency of use, the organization’s experiences, and the organization’s geographic location and climactic conditions. In performing the risk assessment, the Spring Fire Department will follow the requirements as outlined in NFPA 1852 Ch. 5.1.5 – 5.1.5.1. Selection Spring Fire Department will only purchase, provide, and maintain breathing apparatus and PASS devices that are compliant with the current NFPA 1852, 1981, 1989 and 1982 standards. All purchased equipment will be inspected prior to acceptance from the manufacturer. Any equipment that is found defective or unsatisfactory will be returned to the vendor. Responsibilities District Chiefs and company officers are responsible for ensuring that all personnel under their control are completely knowledgeable of the respiratory protection requirements for the areas in which they work. It is the responsibility of all employees to have an awareness and follow the respiratory protection requirements as outlined in this guideline. All employees are also responsible for wearing, inspecting and ensuring proper decontamination and sanitization of respiratory equipment. Employees will be responsible for ensuring a quantitative fit testing is performed annually. The fit testing shall be done during the employee’s birth month, coordinated with the quartermaster’s office. The Quartermaster division is responsible for documenting the fit testing records of all respirators used by Spring Fire Department. Page 2 of 9 Manual Name: Document Number: Spring Fire Department Guidelines SFD.066 Document Title: Date: 01/21/2022 Self-Contained Breathing Apparatus Revision Number: 01 The Deputy Chief of Support Services in coordination with the quartermasters is responsible for the selection, technical support, issuance and maintenance of SCBA. The deputy Chief of Support Services is also responsible for breathing air quality of the department in accordance with NFPA 1989. The Spring Fire Department will create and maintain a quality assurance program including but not limited to: Assuring effective and safe performance of SCBA provided by users Confirm all policies and procedures are being followed. Determining the effectiveness of those policies and procedures Constant improvement of the organization’s respiratory protection program. Recordkeeping All Spring Fire Department SCBA, and PASS records will be maintained through PSTRAX. Respiratory Equipment The Spring Fire Department shall be responsible for purchasing only NFPA compliant respiratory equipment. The applicable NFPA standard applicable to the respiratory equipment will be the latest standard in effect at the time the equipment is contracted for new, purchased or rebuilt. All repairs and updates that may be needed or added to the SCBA units must meet the current standard at the time the department completes the repairs or updates – not the original manufacture date. SCBA are self-contained and provide 45-minute air supply for the air-supplied respirator. However, under emergency conditions, air may be supplied for significantly less than the specified time frames the cylinder is rated for. All in service SCBA will comply with the most current edition of NFPA 1981. SCBA used for department operations will comply with N.F.P.A. 1981. SCBA shall be used in areas where: Where an IDLH atmosphere exists. Where all hazardous atmospheres exist. In an area where the atmosphere may rapidly become hazardous. When instructed by any Officer. Required use of a SCBA means that the member has the face piece in place and is breathing air from the SCBA with PASS device activated. No SCBA shall be used without a properly functioning PASS device. It will be the responsibility of the company officer to ensure the use of a breathing apparatus when appropriate. Anytime a member is in an IDLH environment, they must breathe air from a SCBA. The breathing of air from the SCBA must be from the initial attack to the finish of overhaul. Page 3 of 9 Manual Name: Document Number: Spring Fire Department Guidelines SFD.066 Document Title: Date: 01/21/2022 Self-Contained Breathing Apparatus Revision Number: 01 Eyeglass straps or temple bars shall not be permitted to pass between the face piece seal and face. Members wishing to wear glasses will have spectacles fitted inside the face piece (with the approved Scott hardware) as not to interfere with the seal. Members may wear soft contact lenses if they have had successful long-term use. Hard contact lenses shall be prohibited from wear with an SCBA. Hard contacts may dislocate causing severe pain or may pop out in the wearer looks rapidly to the side. Any head covering which passes between the face piece seal and the members face shall not be worn. Members will not operate in SCBA with facial hair that is not in accordance with SFD.055 Uniform and Grooming Guideline. The SCBA face piece straps shall not be worn over protective hoods. Helmets worn with face pieces will not interfere with the face piece or face seal. Inspection of Respiratory Equipment, PASS At the start of each tour of duty (including second morning of the our), each employee will conduct a daily inspection of the SCBA assigned to their riding position. A record shall be kept to document the inspection dates, inspection findings, and required maintenance for respirators through PSTRAX. Weekly checks shall be performed each apparatus day. All SCBA shall also be inspected after each use on scene, or in training. In all cases, the period between inspection for all breathing apparatus shall not exceed one week per NFPA 1852. Note: Additional SCBA available on the apparatus shall receive the same daily and weekly inspection, whether or not there is an assigned rider to the breathing apparatus. If any malfunctions or damage are noted during an inspection, the unit shall be removed from the truck and a tag placed on the stating “Out of Service” as well as the reason for being out of service. The SCBA shall be written up on PSTRAX to ensure the appropriate SCBA repair technician is notified. The following is a guideline for daily, weekly, and post use inspection: All of the following components shall be present: 1. Facepiece 2. Back Frame and Harness assembly 3. Cylinder 4. Hose 5. End-of-service-time-indicator (Vibe alert) Page 4 of 9 Manual Name: Document Number: Spring Fire Department Guidelines SFD.066 Document Title: Date: 01/21/2022 Self-Contained Breathing Apparatus Revision Number: 01 6. Regulators 7. Accessories SCBA components and operation Check cylinder pressure gauge for full indication (4500 psi). If cylinder pressure is below 4500 psi, replace with a fully charged cylinder or recharge cylinder. In service cylinders shall not fall below 90% of the rated pressure (4000psi), and must be refilled before being placed back in service. Open cylinder completely to ensure proper operation. Check bypass valve to ensure proper operation. Ensure doffing switch stops the flow through the regulator. Ensure the regulator gasket is present and free from cracks and gouges. Ensure regulator clicks and secures to mask, the regulator should not be able to free spin. Check end-of-service-time-indicator activation at 25% cylinder pressure. Ensure activation of integrated PASS device Ensure remote gauge and cylinder pressure deviate no more than 10% of each other Ensure all straps and harnesses are in good condition and fully extended. Face piece Inspect the frame for any damaged components, deterioration, cracks, tears and holes. Inspect head-harness buckles, straps and webbing for proper functionality. Inspect the lens for proper seal, scratches, abrasions and heat damage. Inspect voice amplifier for proper operation. SCBA Frame and Cylinder Inspect back plate and harness assembly for damage. Inspect all hoses for damage. Confirm that low-pressure (Vibe Alert) alarm and Integrated PASS are functioning properly. Inspect all gauges for proper reading and damage. Inspect the regulator for proper operation of controls and bypass valve. Inspect cylinder for current hydrostatic date, ensure date is no more than 5 years old. Check seal in high pressure hose to cylinder connector, thread damage, and proper connection to the cylinder. The proper connection should be hand tight, never use wrenches for this connection. Visual inspection of cylinder for dents, gouges and/or cuts to fiberglass wrapping, evidence of high heat or flame such as discolored paint, charred decals, melted gauge lens, or distorted bumper. Any of the findings above are cause for removing the unit from service. Integrated Personal Alert Safety System (PASS) Ensure the PASS enters pre-alert phase Ensue the pre-alert is shut off by motion Allow PASS to enter full alarm Page 5 of 9 Manual Name: Document Number: Spring Fire Department Guidelines SFD.066 Document Title: Date: 01/21/2022 Self-Contained Breathing Apparatus Revision Number: 01 Ensure PASS alarm reset button (yellow) shuts off the alarm Ensure the manual alarm button (red) activates full alarm Check for low battery indication. As the batteries begin to approach the end of their useful life, the low battery condition will be signified by the following: 1. The back-frame module will begin to sound a chirp approximately every two seconds. 2. The round LOW BATTERY indicator at the far right of the HEADSUP display will light for twenty (20) seconds and then begin to flash slowly at once a second. 3. If the respirator is equipped with a PASS DEVICE distress alarm, the green lights on the control module and back frame will go out. 4. While in low battery condition, the heads-up display and the PASS device distress alarm will continue to operate for a period of time greater than the longest duration cylinder available for the respirator. However, all 6 double “A” (AA) batteries must be replaced before the respirator is used again. Only the Duracell MN 1604 or PC 1604 type batteries shall be utilized in the PASS, as this maintains the tested intrinsic safety rating. Note: Failure to replace the batteries and continuing with multiple uses of the respirator after the low battery condition has been indicated by the PASS device distress alarm may result in failure of the PASS device distress alarm during use. Breathing Air Cylinder Filling Prior to filling Breathing Air Cylinders, the following items should be inspected: Hydrostatic date Pressure in the cylinder and pressure gauge for any damage Cylinder body checked for cracks, dents, weakened areas, heat damage, or chemical damage. Composite portion of the cylinder checked for cuts, gouges, loose composite materials and the absence of resin. Cylinder outlet thread checked for damage Valve hand wheel checked for damage Outlet checked for debris Note: A breathing air cylinder refill log shall be completed for each cylinder refilled. A link to the form can be found on the Spring Fire Department home page. Care, Cleaning, Disinfecting and Decontamination SCBA and facemasks are exposed to the same products of combustion as turnout gear. They are contaminated any time they are exposed to a smoky atmosphere, including, but not limited to, structure fires, car fires, dumpster fires, training fires or burnt food on the stove. If not properly Page 6 of 9 Manual Name: Document Number: Spring Fire Department Guidelines SFD.066 Document Title: Date: 01/21/2022 Self-Contained Breathing Apparatus Revision Number: 01 cleaned, contaminated equipment will continue to expose personnel to carcinogens long after the fire. Decontamination of all contaminated equipment shall follow the guideline referenced in SFD.002 Cancer reduction initiative. When a SCBA has been exposed to Chemical, Biological, Nuclear, Radiological, and Explosive Materials (CBRNE), it shall be considered contaminated beyond the ability to decontaminate it and return it to service. The SCBA shall be removed from service, and shall be retired and disposed of in coordination with the quartermaster’s office. SCBA cleaning Contaminated SCBA shall be placed out of service and segregated from other equipment and personnel to prevent further exposure to personnel. All decontaminated SCBA shall be cleaned and decontaminated after each use and prior to being placed back in service. 1. The cylinder needs to be removed from the backpack for proper cleaning. It should be washed with warm, soapy water and thoroughly rinsed, making sure to clean all components of the cylinder. After cleaning, the cylinder valve should be cracked open to blow out any moisture that has collected in the valve opening. 2. The frame, straps and harness (minus cylinder) should be thoroughly cleaned in accordance to the manufacturer’s recommendation. Warm soapy water, sponge and soft bristled brush should be used, with care taken to make sure water is not directly applied to electronics, i.e. pack alert. 3. If SCBA is left out to air dry ensure it is not placed in direct sunlight. Note: Under no circumstances should bleach be used to clean any part of the Scott Airpak. Facemask Cleaning Masks should be cleaned inside and out to remove all contaminants and sanitized prior to being placed back in service. 1. Remove the facemask from the low-pressure regulator. If the facemask is equipped with a VoiceAmp, remove before continuing. 2. Wipe the exterior surfaces of the facemask using a cloth and warm, soapy water made from liquid dish detergent or a manufacturer approved mask cleaner. A 10:1 water:bleach mixture is also acceptable as a disinfectant. 3. Use a soft-bristled brush and soap to further cleanse any dirt, grime or debris. 4. Rinse with a low-pressure water stream. 5. Allow facemask to air dry. 6. inspect facemask for cracks or leaks and for proper seal and operation before putting unit back in service. 7. Return facemask back to service. Storage Page 7 of 9 Manual Name: Document Number: Spring Fire Department Guidelines SFD.066 Document Title: Date: 01/21/2022 Self-Contained Breathing Apparatus Revision Number: 01 The following are guidelines to ensure proper storage of SCBA and SCBA Cylinders All in service SCBA cylinder shall be stored fully charged. Apparatus mounted SCBA will only be stored in a secure compartment or NFPA approved cylinder storage device. If compressed breathing air has been stored in a cylinder greater than 12 months, the air must be purged and cylinder refilled. To minimize exposure to harmful contaminants, Contaminated SCBA shall be decontaminated prior to storage in the apparatus. SCBA shall never be worn or brought in the living quarters of the station. Members of the public shall not be exposed at any time, except during emergency operations, to soiled or potentially soiled contaminated SCBA or SCBA components. Annual SCBA Inspection and Testing It is the responsibility of Spring Fire Department to ensure all SCBA assemblies and Face Pieces undergo annual full-function testing by a factory authorized service provider in accordance with NFPA 1852. Records of the testing will be maintained by the Deputy Chief of Support services for no less than 3 years. If any SCBA or component thereof is found to exhibit signs of failure, near failure, or significant degradation of performance as a result of normal use, the item or component will be removed from service and tagged “for repair- do not use.” The Deputy Chief of Support Services will be notified and he will promptly notify the SCBA manufacturer in writing of the specific condition or cause, and the circumstances involved with the specific conditions or cause. If the situation warrants, The Deputy Chief of Support Services will also provide the manufacturer with prior data logs on the apparatus and video or photo of the condition. A copy of the notification shall also be sent to the Texas Commission on Fire Protection, NIOSH, and NPPTL (National Personal Protective Technology Laboratory). The Deputy Chief of Support Services will ensure that cascade systems are inspected, tested, maintained and documented in accordance with NFPA 1989. Maintenance Maintenance or repairs of SCBA and PASS devices will be done by a specially trained person(s) with parts designed for the Equipment/Respirators. No attempt will be made to replace components or to make repairs beyond the manufacturer’s recommendations. The Spring Fire Department SCBA Shop Manager / Personnel will be responsible for the repair and maintenance of all Equipment/Respirators. With authorization from the SCBA manufacturer, the SCBA Manager will send members from the Quartermaster Department to the SCBA Technician Course and maintain their certifications and qualifications as outlined by the manufacturer’s parameters and continuing education requirements. All of Spring Fire Department SCBA Technicians certifications and licenses will be displayed in the Airpack Shop as outlined by the manufacturer technician course. Page 8 of 9 Manual Name: Document Number: Spring Fire Department Guidelines SFD.066 Document Title: Date: 01/21/2022 Self-Contained Breathing Apparatus Revision Number: 01 The members from the Quartermaster Department who hold and maintain an SCBA technician course certification will only be the selected members of Spring fire department authorized to make any manufacturer approved repairs, alteration, maintenance and testing. Retirement and Disposal SCBA air cylinders and Air Packs will be retired if any of the following criteria is met: Self-Contained Breathing Apparatus SCBA has been in service through four (4) NFPA edition cycles SCBA not maintained in accordance with annual testing SCBA beyond the ability to be decontaminated SCBA Air Cylinders Cylinders that have reached 15 years of age Cylinders not maintained in accordance with annual testing Cylinder beyond the ability to be decontaminated Retired SCBA and Air cylinders are not authorized to be used in training. All retired equipment will be rendered incapable of operation and discarded. Misuse/Destruction of PPE or Equipment The Spring Fire Department will not tolerate any member misusing or destroying their department issued PPE or any other department issued equipment. Members are not permitted to perform any alterations to the SCBA’s form, fit or function. The individual could face disciplinary action including, but not limited to suspension and/or termination. The individual that recklessly damages department issued equipment can be held responsible to pay for the cost of replacing the item(s). Page 9 of 9