Maintenance Management Systems PDF
Document Details
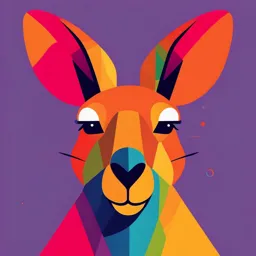
Uploaded by Reusl
Tags
Related
Summary
This document details maintenance management systems, covering various maintenance types like routine, preventative, projects, and emergency. It outlines key components of a maintenance management system (MMS), and procedures for work requests and work orders. The document includes examples of work request forms.
Full Transcript
Plant Communications • Chapter 3 Objective 3 Discuss the elements of Maintenance Management Systems, including work requests and work orders. A Maintenance Management System (MMS) is used to organize, plan, monitor, and evaluate maintenance activities. A well-functioning MMS is essential for: • Op...
Plant Communications • Chapter 3 Objective 3 Discuss the elements of Maintenance Management Systems, including work requests and work orders. A Maintenance Management System (MMS) is used to organize, plan, monitor, and evaluate maintenance activities. A well-functioning MMS is essential for: • Optimizing plant efficiency and safety • Minimizing environmental impact • Keeping costs at reasonable and manageable levels Types of Maintenance Maintenance can be classified as follows: Routine – Routine maintenance consists of regular scheduled tasks (daily, weekly, or monthly) associated with the continuous operation of a facility. Routine maintenance may include brief operation of standby pumps; placing engines on barring gear; checking the operation of smoke detectors and emergency lighting; and checking battery fluid levels. Preventative – Preventative maintenance involves the systematic inspection, detection, and correction of conditions, to prevent equipment failure. This may involve scheduled pump shaft alignment; checks of pulley alignment and gear lash; air filter replacement; vibration analysis; and testing of various fluids (such as oils and coolants). Projects – Projects are planned activities, such as the relocation of a control room. Projects involve both plant personnel and contractors. Detailed planning and organization is necessary for successful project completion. Smaller projects, like boiler room pipeline labeling, often involve only plant personnel, and have far fewer details. Emergency – Emergency maintenance involves unplanned and unscheduled events, such as sudden equipment mechanical failure. Sometimes, emergency maintenance is necessary due to the effects of hostile natural conditions (such as strong winds or flooding). Key Components of an MMS The following are key components of an MMS: a) An inventory program that accurately tracks maintenance costs, repairs, and other expenses associated with physical assets (such as buildings, roads, and equipment). b) Analyzes and documents the types, durations, and frequencies of maintenance activities needed for each piece of equipment in the plant. c) Provides an annual maintenance work schedule based on the information collected. d) Handles work requests, and issues work orders. e) Creates a realistic budget for all associated maintenance costs. These include such costs as internal labour, contract labour, parts, consumables, and equipment rentals. Emergency maintenance and repairs are impossible to predict. Maintenance plans may include labour, budget, and materials contingencies to deal with unexpected events. 4th Class Edition 3 • Part A 3-15 Unit A-10 • Fundamental Industrial Communication Skills Work Requests and Work Orders Work request systems are integrated with maintenance management systems. In power plants, very little maintenance or repair work is done without being formally requested. By tracking the work performed, companies learn the cost associated with maintenance and repair, and can use this information to accurately budget for upcoming expenses. For this reason, most plants have some system of requesting work. When a work request is submitted, it triggers many, if not all of, the following activities: a) Determining the costs for labour, parts, and consumable materials b) Planning and prioritizing work c) Scheduling labour for the: • Engineering department • Design department • Maintenance department • Operations department • Inspections department • Outside contractors d) Warehouse activities: • Ordering parts, specialized tools, and equipment • Receiving • Placing into inventory e) Accounting activities: • Administering contracts Work requests can originate from individuals working in various departments, such as operations, maintenance, information technology, and engineering. The work requested may be an equipment test, a process performance evaluation, a repair, an installation, an inspection, a replacement, or a renovation. Typical work orders include the following information: a) b) c) d) e) f) g) h) i) j) k) l) m) 3-16 Name, department, and title of the person making the request Name of an authorizing individual (the person who approved the request) Location of work to be performed Equipment number or designation Scope of work (description) Work permits required (such as hot work, confined space, and excavation) Trades department to be assigned, or operations department Specialized equipment, tools, or materials needed Type of outside contractor or specialized tradespersons required Justification of the work Date request was submitted Date the work must be completed Priority (safety concern, urgent, high, medium, or low) 4th Class Edition 3 • Part A Plant Communications • Chapter 3 Figure 3 shows an example of a work request used in a plant. Typically, safety concerns are regarded as the highest priority requests, followed by urgent and routine work. Figure 3 – Typical Work Request Form Workers usually submit verbal requests to their immediate supervisors. During this conversation, the worker and the supervisor decide on the priority and other job details. Together, they fill out the work request form and the supervisor signs it. For Power Engineers, the supervisor is usually the shift charge engineer. 4th Class Edition 3 • Part A 3-17 Unit A-10 • Fundamental Industrial Communication Skills Next, the request form is sent to a maintenance planner. The planner considers and organizes all aspects of the job. Routine maintenance tasks are usually scheduled by the planner, and work orders are generated automatically by a maintenance planning software package. For this reason, work requests are not usually submitted for routine maintenance. However, non-routine maintenance (such as repairing leaky pump seals or replacing non-functioning valves) always require work requests. Every work request is unique. Many jobs require new or modified designs, and engineering approval. Sometimes, heavy lifts that involve cranes and crane operators must be planned. Confined space entry can involve specialized safety equipment. Additional contracted safety watch personnel may be required during the confined space entry. Parts or replacement equipment must be specified and ordered by warehouse personnel. Some large jobs require plant shutdown, and are scheduled for a turnaround period. Substitution of parts or equipment, as well as changes to existing designs, must be approved through the engineering departments’ Management of Change (MOC) procedures. The planner co-ordinates and routes all tasks and sub-tasks for every work request. After work requests have been scheduled by the planner, work orders are assigned to the appropriate tradespeople, operators, technicians, or contractors. The work order outlines the scope of the work, and provides all supporting documents (such as piping and instrumentation diagrams). Before proceeding with the job, the assigned person must receive a work permit and all other supporting permits. The operations department issues these permits. A site inspection is performed when the job is completed. The worker signs-off and surrenders the work permits to the operations staff. Successful completion of the job is then relayed back to the maintenance planner, who completes the documentation. 3-18 4th Class Edition 3 • Part A