Safety Management System (SMS) Manual PDF
Document Details
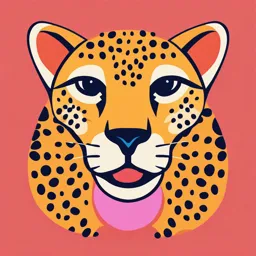
Uploaded by FreshestSparrow
Prince Sultan Aviation Academy
Tags
Summary
This document is a safety management system manual for Saudia Technic, a maintenance, repair, and overhaul (MRO) company in Saudi Arabia. It outlines the safety policies, procedures, and practices for all departments and personnel, aiming for a systematic and comprehensive approach to managing safety as part of the company's overall operations. It is likely intended for use by employees and staff within the organization.
Full Transcript
Issue # 03 SAFETY MANAGEMENT Revision # 00 SYSTEM (SMS) MANUAL Rev. Date...
Issue # 03 SAFETY MANAGEMENT Revision # 00 SYSTEM (SMS) MANUAL Rev. Date Pages 15-Feb-24 17 of 92 1.0 Introduction and Scope of SMS: Saudi Aerospace Engineering Industries (Saudia Technic), the technical arm of Saudi Arabian Airlines (SAUDIA) is the leading MRO in Saudi Arabia and MENA region with over 50 years of experience, providing complete technical solution for the commercial and general aviation industries including maintenance repair and overhaul of aircraft engines and components, Saudia Technic (ST) is strategically located in Jeddah, Saudi Arabia at the center of the fastest growing aviation market. Current facilities: a. Two hangars each one can accommodate a size or airplane of Boeing 747- 400/777-300. b. H75 inflatable hangar. c. Temporary hangar for Airbus A320. d. Helicopter hangar. e. 27 component workshops. f. Repair, maintenance and engines overhaul center. g. A (90,000Lb/Thrust) engines test center. h. Materials and spare parts warehouses with a total area about 22.000. Line Maintenance Stations located in the Kingdom of Saudi Arabia. 20 international line stations and 26 regional and domestic. 1.1 Safety Management System: ST Safety Management System is an explicit element of its management responsibility, which sets out the ST’s safety policy and defines how it manages safety as an integral part of its overall business including all approved facilities and contracted services. It is a systematic, precise and comprehensive process for managing the organizations Hazard Identification and Risk Management (HIRM) program. It is intended to become part of the culture and the way people do their jobs. There are five essential requisites for a Safety Management System: a. A comprehensive approach to safety based on the recognition and minimization of hazards through an inclusive and detailed assessment of risks and actions to reduce risk to as low as reasonably possible. b. An effective provision of safety resources. c. Defined safety responsibilities of all departments, management and employees including oversight of contracted services. d. Management ensuring that safety responsibilities are educated and communicated to all employees. e. Systems to achieve safety oversight. The elements of the Safety Program reflect the above-mentioned requirements and are also based on the following: THIS DOCUMENT IS UNCONTROLLED WHEN PRINTED OR DOWNLOADED Issue # 03 SAFETY MANAGEMENT Revision # 00 SYSTEM (SMS) MANUAL Rev. Date Pages 15-Feb-24 18 of 92 Philosophy – Safety Management starts with management philosophy by recognizing that there will always be threats to safety, setting the organization standards and ensuring that safety is everyone’s responsibility. Policies – specifying safety policy with clear statements of responsibility, authority and accountability. In addition, incorporating safety goals into every aspect of the operations will develop organizational processes, structures, relevant skills, and knowledge necessary to perform the job will also be developed. Procedures – the execution of safety policies shall be specified by the management by advocating clear directions to all staff and providing means of planning, organizing and controlling as well as means for monitoring and assessing safety status and processes. Practices – ensuring that when a job is done, well-designed and effective procedures are followed, avoiding the shortcuts that can detract from safety and taking appropriate action when a safety concern is identified. To have maximum value to the MRO, the Safety Management System requires involvement of all staff, to identify potential hazards that occur in or interface their normal operational function. Such hazards must be highlighted so that their adverse impact can be minimized by risk assessment and corrective actions. 1.2 Safety Management Documentation: 1.2.1 Safety Management System Manual (ST-SMS): This ST-SMS defines the policies and processes by which ST complies with the requirements of GACAR Part-5 Safety Management Systems. It is documented in accordance with GACAR Part-5 and ICAO Doc 9859 Version 3 Safety Management System The manual is structured as recommended in GACAR Part-5 and ICAO Doc 9859, Chapter 5 Appendix 4: a. Safety Policy and Objectives: (1) Safety Policy. (2) Management commitment and safety accountabilities. (3) Appointment of key safety personnel. (4) Coordination of emergency response planning. (5) Safety management documentation. b. Safety Risk Management: (1) Hazard identification. (2) Safety risk assessment and mitigation. c. Safety Assurance: (1) Safety performance monitoring and measurement. (2) The management of change. (3) Continuous improvement of safety management. THIS DOCUMENT IS UNCONTROLLED WHEN PRINTED OR DOWNLOADED Issue # 03 SAFETY MANAGEMENT Revision # 00 SYSTEM (SMS) MANUAL Rev. Date Pages 15-Feb-24 19 of 92 d. Safety Promotion: (1) Training and education. (2) Safety communication. ST-SMS is intended to serve as a guide for safe ST operations and is applicable to all ST’s organizations/departments functions. It is the responsibility of every employee to comply with its content. This manual, as depicted below, reflects ST positioning of the SMS relative to administrative and technical/functional departments within ST and as applicable, to ST contractors, vendors and visitors. Note: The effectiveness of SMS and ST-SMS will be subject to verification by a full Gap Analysis audit on a Bi-annual basis IAW SMS Gap Analysis checklist: Reference ICAO Doc 9859 Ver.3 Appendix 7 to Chapter 5 Notwithstanding safety-related procedures within each department, the ST-SMS constitutes the official Safety Management System. Furthermore, this manual meets the regulatory requirements set out in KSA General Authority of Civil Aviation (GACA) Regulation Part-5 Safety Management System (SMS). This requirement is based on ICAO DOC 9859 Rev.3 Safety Management System (SMS). THIS MANUAL IS INTENDED FOR INTERNAL USE IN SAUDIA TECHNIC AND SHALL NOT BE MADE AVAILABLE IN ANY FORM TO ANY EXTERNAL PARTY WITHOUT THE WRITTEN APPROVAL OF THE DIRECTOR SAFETY AND QUALITY ASSURANCE. 1.2.2 Manual Control: a. The overall responsibility for the update and control of ST-SMS is with Director Safety and Quality Assurance. b. The continued coordination for ST-SMS shall be the responsibility of Manager Safety. c. The overall task and responsibility shall include the following activities: (1) Approval of documents prior to publication. (2) Annual review, update, and re-approve the ST-SMS when necessary. (3) Ensure that the current revision status of this manual is identified. (4) Ensure all users of this manual have access to the latest revision, including all relevant documents. (5) Prevent the use of obsolete documents. d. The proposed changes to ST-SMS shall be submitted to Director Safety and Quality Assurance. THIS DOCUMENT IS UNCONTROLLED WHEN PRINTED OR DOWNLOADED Issue # 03 SAFETY MANAGEMENT Revision # 00 SYSTEM (SMS) MANUAL Rev. Date Pages 15-Feb-24 20 of 92 e. The proposed changed to ST-SMS shall be conferred with affected departments by Manager Safety prior to acceptance for any necessary amendments. f. The proposed changes to ST-SMS shall be rejected with full justification, and the requester shall consider these justifications prior re-submitting any changes. 1.2.3 Safety Database System Description: ST is utilizing Safety Database (Q-Pulse Quality, Compliance and Safety Modules) controlled by Safety and Quality Assurance (S&QA) department. The Safety Database will receive the following inputs: a. Event/Hazards Reporting. b. Saudia Accident/Damage Report. c. Ground Accident/Incident Report. d. Industrial Injury/Occupational illness Report. e. Safety Audit Outcome. f. Surveillance/Spot Checks Results. g. Risk Assessment Level. h. Data Analysis. i. Customer Air Safety Reports (ASR). j. Monitoring Programs/Engine Monitoring Program/Reliability Program. THIS DOCUMENT IS UNCONTROLLED WHEN PRINTED OR DOWNLOADED Issue # 03 SAFETY MANAGEMENT Revision # 00 SYSTEM (SMS) MANUAL Rev. Date Pages 15-Feb-24 21 of 92 Event/Hazard Event/Hazard SAFETY AND QUALITY DATABASE (SDB) Reporting Reporting SAUDIA TECHNIC DEPARTMENTS SAFETY AND QUALITY ASSURANCE SAUDIA Accident/ SAUDIA Accident/ Damage Report Damage Report Ground Accident/ Ground Accident/ Incident Report Incident Report Industrial Injury/ Industrial Injury/ Occupational Illness Occupational Illness Report Report Safety Concern Corrective/ Report Preventive Action Internal Audit Investigation Report Outcome Safety Audit Risk Assessment Outcome Level 1 Surveillance/Spot Data Analysis Checks Results Risk Assessment Reliability Program Level 1 Data Analysis Corporate Safety Reports Safety Performance Safety Data Trends Safety Data Trends Inspection Results Reliability Reports Managing SC Inspections Indicator SAFETY COMMITTEE (SC) (Review/Compare Input, Risk Assessment (LVL II), Risk Mitigation) SC REPORTS MANAGEMENT REVIEW SDB Inputs and Outputs THIS DOCUMENT IS UNCONTROLLED WHEN PRINTED OR DOWNLOADED Issue # 03 SAFETY MANAGEMENT Revision # 00 SYSTEM (SMS) MANUAL Rev. Date Pages 15-Feb-24 22 of 92 ST departments review their assigned significant items within their retrievable capability of SDB, other applicable system, or as per S&QA department requirements. These items are analyzed to reach root cause and provide Corrective Action into the SDB. Moreover, Risk Assessment is practiced as a main process within each department consequently, appropriate action is taken to mitigate risk. Data analysis is another main process that is practiced in dealing with safety related data. Noticed trends are addressed by Preventive Actions, as appropriate. ST S&QA department exercises a full pledge oversight over ST that is visible through the conduct of regular Safety Audits, Surveillance, and Inspections. Over and above, the S&QA department shall monitor the Safety Database (SDB) continuously ensuring proper addressing of required corrective actions assigned to each respective Department. Irregularities within SDB inputs are resolved in coordination between S&QA and concerned department. 1.2.4 Revision Mechanism: a. Revision Proposal: Any person may propose changes to ST-SMS. Director Safety and Quality Assurance evaluates proposed changes to ensure compliance with current GACAR Part-5 requirements. Accepted changes shall be incorporated in the proposed revision to GACA for acceptance. b. GACA Acceptance: GACA communicates acceptance of the manual by issuing an acceptance page or by any means indicating GACA acceptance of the revision. c. Identification of Revision: The revised text will be identified by a bold vertical line in the left-hand column of the affected text. Further, each revision will be identified with a new revision number starting from Rev.0, Rev.1, and Rev.2 onwards and with new revision date. d. Identification of Re-issue: Following requirement for major revision, the manual will be re-issued. The issue number will be identified on the footer of the cover page and GACA acceptance page, header of the following sections of this manual, list of effective pages, and record of revisions. e. Temporary Revision: Temporary (Email) revision to incorporate urgent policy matter when normal revision process is considered too protracted. Upload approved temporary (email) revision to ST intranet. Incorporate temporary revision to ST-SMS and indicate reference on section 0.3. THIS DOCUMENT IS UNCONTROLLED WHEN PRINTED OR DOWNLOADED Issue # 03 SAFETY MANAGEMENT Revision # 00 SYSTEM (SMS) MANUAL Rev. Date Pages 15-Feb-24 23 of 92 f. Responsibility: Director Safety and Quality Assurance is responsible to provide revisions to the GACA. g. Access to electronic copy manuals: All ST manuals, including this manual, are uploaded to the ST intranet called ST Portal (Safety and Quality Manuals). CDs are provided where applicable. All applicable organization access ST Safety and Quality Manuals at the ST portal by following the link: https://saudiamrocom.sharepoint.com/sites/SafetyandQuality/SQManualsLibrar y/Forms/AllItems.aspx (Select the folder titled: ‘10. ST – SAFETY MANAGEMENT SYSTEM (SMS) MANUAL’) 1.2.5 SMS Records: ST maintains records of outputs of safety risk management processes in this manual. Such records will be retained for as long as the control remains relevant to the operation. ST is utilizing Safety Database (Q-Pulse Quality, Compliance and Safety Modules) controlled by S&QA department. The Q-Pulse will receive the following inputs: a. Event/Hazards Reporting. b. Accident/Damage Report. c. Ground Accident/Incident Report. d. Industrial Injury/Occupational illness Report. e. Safety Audit Outcome. f. Surveillance/Spot Checks Results. g. Risk Assessment Level. h. Data Analysis. i. Customer Air Safety Reports (ASR). ST departments review their assigned significant items within their retrievable capability of SDB, other applicable system, or as per S&QA department requirements. These items are analyzed to reach root cause and provide Corrective Action into the SDB. Moreover, Risk Assessment is practiced as a main process within each department consequently, appropriate action is taken to mitigate risk. Data Analysis is another main process that is practiced in dealing with safety related data. Noticed trends are addressed by Preventive Actions, as appropriate. S&QA department exercises a full pledge oversight over ST that is visible through the conduct of regular Safety Audits, Surveillance, and Inspections. Over and above, the S&QA shall monitor the Safety Database (SDB) continuously ensuring proper addressing of required corrective actions assigned to each respective department. Irregularities within SDB inputs are resolved in coordination between S&QA and concerned department. THIS DOCUMENT IS UNCONTROLLED WHEN PRINTED OR DOWNLOADED Issue # 03 SAFETY MANAGEMENT Revision # 00 SYSTEM (SMS) MANUAL Rev. Date Pages 15-Feb-24 24 of 92 Safety Manager shall review the SMS reports as mentioned above and document all associated risks in the central Risk registry (RR). The RR shall define the hazards, risk assessment and risk controls. The RR shall be reviewed quarterly for validation as described in Safety Review Committees as per section 5.5(B). ST maintains records of outputs of safety assurance processes as described in this manual such records shall be retained for a minimum of five (5) years. ST maintains a record of all training provided for each individual. Such records must be retained for a minimum of 5 years after completion of the training. ST shall retain records of all communications provided for a minimum of 5 years. 1.2.6 SMS Backup Record: ST-IT shall backup and retain SMS records in the Q-Pulse in accordance with the table below to ensure the continuity of safety and quality assurance operations without disruption while maintaining compliance. Action Type Daily Weekly Monthly Yearly Backup Incremental Full Full Full Data Retention 7 Days 1 Month 3 Months 12 Months THIS DOCUMENT IS UNCONTROLLED WHEN PRINTED OR DOWNLOADED