Drilling & Completion - Energy Innovation Master Course PDF
Document Details
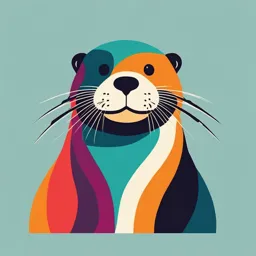
Uploaded by WellBredMaroon
Università degli studi di Cassino e del Lazio
2024
R. Poloni – D. Santoro
Tags
Summary
This document is course material for a Master's course in Energy Innovation, focusing on Drilling and Completion activities. It covers the technical aspects of well construction, drilling rigs, and completion techniques, alongside technological innovation and safety procedures. The course explores well operations within various environments, from remote to deepwater locations.
Full Transcript
Energy Innovation Second level specializing Master course Drilling and Completion R. Poloni – D. Santoro June 13th, 2024 1 Agenda Introduction D&C activities as part of Upstrea...
Energy Innovation Second level specializing Master course Drilling and Completion R. Poloni – D. Santoro June 13th, 2024 1 Agenda Introduction D&C activities as part of Upstream process Well Drilling and Completion Technical overview of well construction process Drilling rigs and equipment Drilling control and well data Well Drilling Problems Well Construction Contracts Technology Innovation in Drilling Role of Technological Innovation Innovation general processes and agreements Intellectual Property Drilling Safety Package 2 Agenda Introduction D&C activities as part of Upstream process Well Drilling and Completion Technical overview of well construction process Drilling rigs and equipment Drilling control and well data Well Drilling Problems Well Construction Contracts Technology Innovation in Drilling Role of Technological Innovation Innovation general processes and agreements Intellectual Property Drilling Safety Package 3 Well Operations in e&p Business Cycle Commercial Hand Over FID Decommissioning discovery to production Exploration Development Production average 5 – 6 years average 3 – 6 years average 20 – 30 years Well Operations 4 Drilling & Completion Operations in All Kind of Environment Remote Desert Nigeria Egypt Congo Lybia Pakistan Tunisia Ecuador Algeria Venezuela Iraq ENVIRONMENT GOM Ghana Offshore/Deepwater Arctic Nigeria Angola Norway Norway Alaska Cyprus Kazakhstan Indonesia Russia Vietnam Mozambique UK 5 Well Engineering Process Exploration Development Reservoir Well Production Engineering Geological and Pressure Prediction Environmental and facilities constraints Well Project 6 Well Construction Process Two-way continuous optimisation Well Well Logistics Construction Engineering Well Services Rig contractor rig contractor logistics well services 7 What happens next? Interface between Reservoir and Surface Facilities Well Completion makes possible the hydrocarbon Perforations production Packer Advanced Completion Techniques Artificial Lift 8 Agenda Introduction D&C activities as part of Upstream process Well Drilling and Completion Technical overview of well construction process Drilling rigs and equipment Drilling control and well data Well Drilling Problems Well Construction Contracts Technology Innovation in Drilling Role of Technological Innovation Innovation general processes and agreements Intellectual Property Drilling Safety Package 9 What is a Well? Main components of a well Christmas Tree WellHead Casing and Cement Completion 10 Why well drilling Well Types and Objectives Exploration / Appraisal Identify the presence of a reservoir Confirm the extension / limits of the discovery Development Produce hydrocarbons Injection / disposal Re-inject produced water / gas (environment / economics) Support the reservoir pressure (production) Relief Intercept uncontrolled flowing formation Kill a well in blow out 11 Drilling a Well Eni Well Operations Fundamentals 12 Well Location 13 Pressures in dowhole environment Rocks can be modeled as granular - porous material containing fluids trapped inside cavities (pores) of the solid phase Pore Pressure Fluids contained in pores have a pressure Pressure Normal (hydrostatic) pressure regime Pressure regimes can be Normal (hydrostatic) Overpressure Geological / Depositional Underpressure reasons Depth 14 14 Pressure gradients Pore gradient = Pore pressure Kg / cm2 / 10m h x 10 Pore Pressure (Kg/cm2/10m) Pore Gradient (Kg/cm2/10m) Depth Depth 15 Well Design Seismic Data Interpretation Lithological Interpretation Gradients profiles Wells Location Pore Gradient Calculated from Seismic / Offset wells Fracture Gradient Calculated from OBG and PPG Overburden Gradient from seismic Target Definition 16 Well Casing Profile and Mud Density programme Casing setting depths, casing size, mud densities Are defined together as they are strictly mutually dependent, based on Pore and Frac gradients (PPFG), lithology Anticipated or known well problems Need to consider a contingency casing profile Exploration well Objectives Target (s), primary / secondary Requirement to o test or logging Development well requirements Reservoir layer (s) to be put in production Completion type (open vs cased hole, dual string, smart, artifica lift etc…) Production rate, type of fluid (affects the casing size) Requirement to perform sand control / stimutaion / other production otimisation jobs 17 Well Program Casing and Well Profile BOP and Wellhead Cement Program Time and Cost Analysis Well Program Drillstring Program Casing Design Bit Program Rig Specification Mud and Hydraulics 18 Drilling a Development Well Achieve the maximum recovery of hydrocarbon reserves in complete safety, in a short Target time and with the lowest investment Extended Reach Well Directional Wells from Platform High controll of wells trajectories Possibility to realize different kind of wells, according to surface limitations Drilling of multiple wells from cluster or platform Reservoir Directional Well from Cluster Horizontal Well Multi-target Well Focus on reduction of the environmental impact and soil consumption 19 Directional Profiles Vertical Slant S-Shaped Horizontal Extended reach 20 Well Drilling Process To drill a well it is important to have 3 conditions: Weight on Bit Rotation of the drill string Circulation of the mud 21 How to apply and measure Weigth on Bit Weigth of drill string (off bottom) Weigth of drill string (on bottom) Martin Decker Weight Indicator Weigth On Bit (WOB) Yellow dial indicates the weigth of string (Hookload) White dial indicates the weigth on bit (WOB) 22 Drill string is supported at surface by rig’s hoisting system and its weight can be measured - Hookload Difference of Weight on Hook with string off bottom and on bottom is the Weight on Bit (WOB) DRILLING SEQUENCE Drill till ‘’stand down’’ 23 DRILLING SEQUENCE Drill till ‘’stand down’’ Pick up off bottom Stop rotation and circulation Install slips 24 DRILLING SEQUENCE Drill till ‘’stand down’’ Pick up off bottom Stop rotation and circulation Install slips Disconect Top Drive Move Top Drive to upper position Pick up new stand Make up new stand to drill string and top drive 25 DRILLING SEQUENCE Drill till ‘’stand down’’ Pick up off bottom Stop rotation and circulation Install slips Disconect Top Drive Move Top Drive to upper position Pick up new stand Make up new stand to drill string and top drive Remove slips Resume circulation, rotation and drill ahead 26 Drilling Fluid Main functions of the mud Provide hydrostatic pressure to contain the formation fluids and prevent influx into the well Provide support to well bore to prevent instability problems Formation Pressure Formation Pressure (collapse or breakouts) Transport cuttings to surface and keep them in suspension when circulation is stopped Hydrostatic Pressure Hydrostatic Pressure Consolidate the wellbore through mud cake and prevent mud loss into the formation Provide hydraulic power to downhole equipment as mud motor, measuring while drilling (MWD), logging while drilling (LWD), etc… Lubricate drill string and BHA and cool the bit and electronic equipment 27 Mud densiy vs pore pressure ’Normal’’ pressure regime is generally equal to 1,03 Kg / cm2 / 10m equivalent to sea water Salinity : 30 g / lt Mud (specific) weight shall be set at a higher value to avoid influx of formation fluids Gradiemts (EMW, s.g.) Pressure (Kg/cm2) 1,03 1,20 Mud Pressure (hydrostatic) Pore Pressure Pore Mud Depth Depth Weight Gradient 28 We often consider the pressure gradients as an ‘’equivalent mud weight’’ (EMW) for ease of comparison with actual MW Mud Balance P P P Underbalance Overbalance Mud Pressure too low Mud Pressure just right Mud Pressure too high (< Pore pressure) ( Pore < Mud < Frac ) ( Mud Press > Frac ) Influx (formation fluids) Optimal Drilling conditions, Breaking of formation 29 Borehole collapse no problems Mud lossess Mud Density vs Pore – Frac Gradients Gradiemts (EMW, s.g.) Pressure (Kg/cm2/10m) 1,03 Frac Pressure Pore Pressure Pore Frac Depth Depth (m) Gradient Mud Pressure Gradient (static and dynamic) MW 30 Cementing Cement slurry Cement (powder) + Water + Additives Compress. Strength (Mpa) Key characteristics Density (neat slurry 1,9 s.g.) Temperature Pumpability, thickening time Hydraulic seal casing-open hole annulus (main Time (hrs) function) Cement hardening produces compressive strength build-up. Its mechanical capabilities are not considered in casing design 31 Well Completion After the well is drilled a production tubing of a selected material is run and set in the well in order to bring hydrocarbons from reservoir to surface in a safe manner. Main Completion Item Open Hole Cased hole Tubing string TR-SCSSV (Tubing Retrievable- Surface Controlled Subsurface Safety Valve) Seating/Landing Nipple Production Packer Chemical Injection Mandrel Sliding Sleeve Down Hole Permanent Gauge Mandrel Monitoring System 32 Well Completion Typologies Single Dual Intelligent Multilateral X-mas Tree – dry One Flowing Zone Two Indipendent Flowing Two or more Commingling Two or more Commingling Zones at same time Flowing Zones (same bore) with Flowing Zones (different X-mas Tree – subsea remote flow control system bores) 33 Agenda Introduction D&C activities as part of Upstream process Well Drilling and Completion Technical overview of well construction process Drilling rigs and equipment Drilling control and well data Well Drilling Problems Well Construction Contracts Technology Innovation in Drilling Role of Technological Innovation Innovation general processes and agreements Intellectual Property Drilling Safety Package 34 Drilling Rig Overview Main systems of a drilling rig: Hoisting and Rotation Surface Well Control Mud Circulation Power Generation 35 Drilling Rig Overview 1. Crown block 15. Driller's console 29. Mud pits 2. Mast 16. Doghouse 30. Desander 3. Monkey board 17. Rotary hose 31. Desilter 4. Traveling block 18. Accumulator unit 32. Mud pumps 5. Hook 19. Catwalk 33. Mud discharge lines 6. Swivel 20. Piperamp 34. Bulk mud components storage 7. Elevators 21. Pipe rack 35. Mud house 8. Kelly 22. Substructure 36. Water tank 9. Kelly bushing 23. Mud return line 37. Fuelstorage 10. Master bushing 24. Shale shaker 38. Engines and 11. Mousehole 25. Choke manifold generators 12. Rathole 26. Mud gas separator 39. Drilling line 13. Drawworks 27. Degasser 14. Weight indicator 28. Reserve pit 36 Hoisting System Main functions of the hoisting system Sustain the drill string Allow to Run in hole (RIH) and pull out of hole (POOH) the drill string Provide weight on bit (WOB) during the drilling operations 37 Rotation System Rotary table system Top drive system Main functions of the rotation system Provide torque and rotation to the drill string to perform the drilling process Through the rotary table support and suspend the drill string and any other material during tubular material connections. 38 Drilling String Drill Pipes Jar Drilling Bit Natural Diamond Stabilizers Tricone Drill Collars PDC 39 Mud Circulation System Main functions of the mud circulation system Mud pits Supply, with a necessary pressure and flow, the energy necessary for the mud circulation Mix new drilling mud Maintain physical and rheological characteristics of drilling mud Contain the drilling mud in a closed system Separate the drilling cuttings and gas from the mud before being re-injected to the wellbore Maintain adequate mud reserve quantity 40 Power Generation System Power Generator Top Drive rotary system Drawworks Mud Pump 41 Surface Well Control System Anular Preventer Main functions of the well control system Activated in case of influx to prevent occurence of uncontrolled flow Close and seal on the drill pipe, tubing, casing, and allow well control operations Close and seal on open hole and allow BOP: Blow Out Preventer secondary well control operations Ram Preventer Shear the tubulars and seal the wellbore 42 Well Barriers The key safety objective in well operations is to maintain full control of formation fluids at all Drilling and Completion Production times, preventing their migration from the formation to the external environment. Primary Well Barrier Primary Well Barrier Wellbore Fluid Column Production Packer This purpose is achieved by using one or more Secondary Well Barrier Completion String SCSSV Well Barrier Envelopes “WB’s”, comprised of Casing Cement Production Casing various mechanical and hydraulic systems Casing Production Casing Cement Casing Hanger termed Well Barrier Elements “WBE’s” and by Wellhead Secondary Well Barrier applying appropriate principles and Drilling BOP Casing Cement Casing techniques. Wellhead Tubing Hanger At least two independent and tested WB’s Production Tree shall be present at all times during the execution of well operations in each flow path between hydrocarbon bearing permeable zones and surface: Two Barriers Policy 43 Drilling Rig – Classification by Location Bottom sea supported Floaters Land Rig Drilling Barge Platform Rig Jack-Up Rig Semi-Sub & Drillship Semi-Sub & Drillship (on shore) (shallow waters) (up to 150/200 m (up to 150 m (Anchored) (Dynamic positioning) (1000/1500 m (up to 3000 m water depth) water depth) water depth) water depth and more) 44 Drilling Rig – Classification by Location Land Rig Platform Rig Jack Up Rig Semi Submersible Rig Drilling Ship Rig 45 Drilling Rig – Classification by Hoisting Capacity CLASSES I II III IV V DRAWWORKS hp 700 1000 1500 2000 3000 MAX DEPTH 2500 m 3500 m 4500 m 5500 m More WITH 5” DP 700 hp 1000 hp 1500 hp 2000 hp 3000 hp 46 Agenda Introduction D&C activities as part of Upstream process Well Drilling and Completion Technical overview of well construction process Drilling rigs and equipment Drilling control and well data Well Drilling Problems Well Construction Contracts Technology Innovation in Drilling Role of Technological Innovation Innovation general processes and agreements Intellectual Property Drilling Safety Package 47 Control During Drilling Operations During the drilling operations all the drilling parameters (pressure, volume, temperature, density, flow rate, lithologies, formation fluids, …) are kept under control and monitored in real time by means of surface instrumentation and downhole instrumentation. ROP Surface measurements Downhole measurements Temperature MUD Pressure LOGGING Volume Flow Rate Cuttings Logging While Drilling Samples (LWD) Sonic Analysis CBL WIRELINE VDL LOGGING Drilling Parameters Flow rate measurement CCL CBL Gamma Rays Measuring While Drilling (MWD) LOGGING Physical Data WILE Mud logging DRILLING 48 Data Transmission System Rig Floor Visualization Annular Pressure Drawworks Top Drive Mud Pumps DH Tool Bore Pressure Temperature Telemetry Distributed Measurements Vibration Bi-Directional Compression & Tension At bit Motor or Survey Formation Drilling Mechanics Comunications Caliper Measur. RSS Measur. Evaluation Meas. Formation evaluation Optimized BHA Fluid identification Telemetry Technology Features Mud pulses Wired DP Cableless Telemetry systems provide consistent Transmission rate [bps] 120 57000 Up to 1000 amount of Real Time data from Down Maximum depth [ft] Limited Unlimited Unlimited Hole and allows Real Time control of Down Hole tools Costs Low High High 49 Agenda Introduction D&C activities as part of Upstream process Well Drilling and Completion Technical overview of well construction process Drilling rigs and equipment Drilling control and well data Well Drilling Problems Well Construction Contracts Technology Innovation in Drilling Role of Technological Innovation Innovation general processes and agreements Intellectual Property Drilling Safety Package 50 Drilling Problems Main Drilling Problems Formation Fluid influx (kick) Mud Losses Stuck Pipe Upon occurrence of such events, current operation are stopped and problem fixed prior of resuming normal operability. Key driver is to correctly address Drilling Problems to prevent any escalation to a larger event which my pose threats to: Safety Environment Loss of Asset integrity Company reputation However, the occurrence of a Drilling Problem, requires time to fix it, till operations can be resumed. This time has a cost for the Company – Concept of NPT 51 Time coding and defintions For KPI monitoring reasons, all well operations are classified on the basis of a Time Coding. The first level of time coding includes: Planned Operations (code P): Time spent to carry out the operations that are part of the original well program and are included in the authorized budget (AFE). Regular operations Unplanned Operations (code U): Time spent to carry out operations not included in the original well program, requested by a change of scope, objectives, strategy while activity is ongoing “Non Productive Time” (NPT) or “Downtime” (cote T or X): Time elapsed between the occurrence of a “trouble” breaking the planned or unplanned operations, till the Trouble time moment in which previous conditions (before problems occurrence) are restored. Do not mistake NPT with Unplanned. An NPT can occur during Unplanned Operations (code X) 52 Fluid Influx (Kick) Definition of Kick – IADC (International Association of Drilling Contractors) “An entry of water, gas, oil, or other formation fluid into the wellbore during drilling. It occurs because the pressure exerted by the column of drilling fluid is not great enough to overcome the pressure exerted by the fluids in the formation drilled. If prompt action is not taken to control the kick or kill the well, a blowout may occur” Pressure exerted by drilling fluid density (mud) is affected by: Density (hydrostatic) Mud friction in annulus, generating change in Equivalent Circulation Density (ECD), Swab & Surge effects (BHA acts as a “piston” during tripping into or out of hole) Factors which could potentially generate a kick Incorrect Mud Density compared to Pore Gradient (unexpected overpressure) Loss of hydrostatic during cement setting Loss of hydrostatic head due to mud losses Operational procedure Failure of equipment 53 To shale shakers – mud pits Normal Drilling BOP Wellhead Casing Choke line – to flare 54 Fluid Influx : kick Abnormal flow out / Increse of mud volume at surface BOP BOP Closed Pressure increase P inside well Barrier envelope Wellhead Casing Fracture Pressure P Fluid influx inside well i.e. Weak point 55 Formation Fluid Kick Control BOP Establish slow rate circulation with heavy mud through choke valve to P keep pressure control inside well Wellhead Kick is safely circulated out of well and internal pressure will eventually be brought back to zero Casing Fracture Pressure P i.e. Weak point 56 Mud Losses Mud / Circulation loss classification Partial losses Total losses / Lost circulation : no mud returns to surface during circulations, loss of mud hydrostatic Well control issues => fluid influx Well bore stability issues => stuck pipe Casing collapse ….. Causes of mud losses Mud hydrostatic pressure higher than fracture pressure High porosity – permeability formations Fractured / karst formations Equivalent Circulation Density (ECD) Surge Effect 57 To shale shakers – mud pits Lost circulation BOP Choke line – to degasser / flare Mud level drop -> Loss of hydraulic control Wellhead Risk of kick from higher pressure formations Impossible to remove cutting from hole Solutions: Circulate with lower mud density Seal of loss zone with cement or other material Insert LCM (lost circulation material) in mud Casing Loss of mud through low pressure / hi permeability formations 58 Mud Losses Recovery actions in case of Mud Losses Partial Losses Use of Lost Circulation Materials (mica, fibers, nut shells) Assess the possibility to keep drilling with acceptable loss rate (depends on several factors) Total Losses Cement or other materials plugs to isolate specifi zones Generally is not considered acceptable to drill ahead in case of total loss of circulation Loss of primary well control barrier No hole cleaning (will generate pack-off or pipe stuck) Loss of information about drilled formations Switch to advanced drilling method such as Mud Cup Drilling Requires accurate preparation / engineering prior of drilling operation 59 Stuck Pipe Main causes for Stuck Pipe Differential Pressure sticking Consequence of mud weight much higher than pore pressure in presence of permeable formations and mud cake (typically sandstone Borehole collapse As consequence of incorrect mud density (too low) As consequence of circulation losses (drop of mud level) Unstable formations (poor hole cleaning) Geometry Key seat (in high curvature hole sections) Other hole geometry reasons 60 Stuck Pipe Recovery actions in case of stuck pipe Mechanical actions with drill string tools: Jar / Bumper Specific mud pills: Oil (lubricant) , HCl (acid sensitive formations i.e carbonates) In case of no success: 1. Determine Free Point: mechanical methods, electric log 2. Back off : mechanical, explosives 3. Fishing BHA (c/w fishing jar) or 3. Cmt plug & Side Track (extreme solution) Critical decision: How long to keep trying (unsuccessfully?) to recover the drill string before deciding for side track ? Technical and economical reasoning (rig rate vs value of equipment left in hole, presence of specific materials, etc…) 61 Agenda Introduction D&C activities as part of Upstream process Well Drilling and Completion Technical overview of well construction process Drilling rigs and equipment Drilling control and well data Well Drilling Problems Well Construction Contracts Technology Innovation in Drilling Role of Technological Innovation Innovation general processes and agreements Intellectual Property Drilling Safety Package 62 Well Construction Contracts Operator (Company): Contractors / Providers Holds the rights to drill the well, Execute operations on behalf of to deploy the asset Operator Is the owner of the assets Provide specialised and ancillary (platform, well(s), facilities… services involved with operations Provide tangible materials and take care of installation when required 63 Everything is regulated by one or several contracts Contracts are awarded at the end of a Tendering Process Material Purchase – Contract Awarding Once the well program is ready and the rig is selected procurement department proceeds: To purchase MATERIALS Casings and accessories Well Head Mud chemicals Cement Bits To award the contracts with the SERVICE COMPANIES Drilling contractor Cementing service Mud service Mud logging Wire Line logging Other auxiliary services 64 Type of Contracts per invoicing structure Time based – daily rate Rig (main contractor) Different rates depending on operations ongoing Mob / Demob rate Auxiliary Services (e.g. Directional Drilling, Mud Logging…) Costs are affected by performance: Stand-by / operational rate for equipment more time elapses, more costs for Fixed rate per operation (e.g. pumping, logging) Operator Consumable materials e.g. mud chemicals Daily rate for personnel Logistic services (e.g. base rental, transports, communication) Price per unit (fixed costs) Tangible matierials (e.g. casings, wellhead, X-mas tree, completion) Sometimes installation service is included (e.g. wellhead) Mostly fixed costs, Consignment basis (e.g. Mud chemicals, bits) not related to time Material is stocked at well site and invoiced when actually used 65 65 Other Types of Contracts Level of supervision by Operator Bundle / Integrated Contracts More services are bundled into a unique conctract (e.g. all ancillary services) TOTAL Operator interfaces with one only entity who is in charge of coordinating the other sub- contractors => pro: easier management for Company Incentive scheme The natural consequence of Bundles Target time or performance is pre agreed along with all planned operations In case of performance better than target which leads to savings for operator, part of MEDIUM these savings are paid back to contractor(s) Pro: contractors are directly committed in seeking the optimal performance / quality of their services. All parties need to be involved and share the same objective Turnkey contract Operator and One main contractor agree on the well to be delivered, quality, objectives etc. Operator pays a fixed price for the well delivered LOW (Follow All operations are demanded to Conctractor up) 66 66 Well Cost Breakdown Example Exploration well, drilled in 2022 with Semisub rig Info for consideration Total time and cost: 75 days, 50 M US$ Rig’s rate: 145 US$ / day - rigs rate are highly volatile Tangible included WH, Casings; no completion & X-mas tree Tecnical services included Directional Drilling, Cementing, subsea ops / ROV and all other services related to operations Other services incuded HSE, MPD, Insurance etc Materials included bits, mud and cement products Logistics included shore base rental, transports (helicopters, supply vessels), communication etc… 67 67 Agenda Introduction D&C activities as part of Upstream process Well Drilling and Completion Technical overview of well construction process Drilling rigs and equipment Drilling control and well data Well Drilling Problems Well Construction Contracts Technology Innovation in Drilling Role of Technological Innovation Innovation general processes and agreements Intellectual Property Drilling Safety Package 68 Technology Innovation Technology plays a strategic role for operational success Eni’s drilling, completion and production optimization activities are distinguished by strong efforts in technology developments Innovation is supported by outstanding skills for a sustainable and efficient business Eni has developed and patented several technologies, well-known and internationally applied in the oil and gas field Technology development to match Eni needs Technical Identify Enhanced safety needs Solution Improve performance & efficiency Technology Plan Optimize time & cost 69 Technology Innovation Activities in Drilling and Completion Research Iniatives Collect the company’s technical needs related to Drilling & Completion activities Identify solutions to cover the need Define new initiatives and activities to be covered within the Technology Plan Technical Identify needs Solution R&D projects to prove or develop technologies with low TRL for the Upstream sector R&D projects to prove or develop technologies with low TRL for Energy Transition which involved Drilling & Completion aspects Technology Plan Digital Initiatives Evaluate a set of commercial Drilling Digital Solutions available in the market: Test different commercial Drilling Digital Solutions covering the whole spectrum of activities, from design to operational follow-up, to automation and post analysis The packages will be tested on selected wells Enhanced Safety Tests will be carried out by Engineering R&D + COAP teams in PERF, and involve/inform Subsurface teams (Ops Geology, Reservoir, GEODATA) to verify interfaces (data inputs, data outputs and compatibility with their Improve performance & efficiency workflows) The whole spectrum of activity and implementation of all Digital initiatives is financing by means of Job Order Optimize time & cost system 70 D&C Innovation Portfolio Research & Development in Well Operations Operational Efficiency Safety Enhancement Energy Transition Digital Solutions New tools and systems to New solutions to increase New energy frontiers for Implementation of digital enhance operational efficiency, personnel safety on site business decarbonization solutions for performance reducing well delivery time & enhancement and trouble cost recognition 71 Technologies to Improve Safety and Performances Upcoming Technologies Virtual Reality Casing Automatic Valve New Wellhead Aluminium Safety Valve Drilling Real Time Centres Drill Pipe Concept CART 18” 3/4 Downhole Housing 18” 3/4 Isolation Packer Housing 30” GRA 36” Hole Conductor pipe 30” Casing 20” Casing 13-3/8” Inner string DP 5” 17-1/2” Hole DIGITAL TRANSFORMATION 1994 2000 2001 2005 2008 2009 2013 2014 2015 2017 2018 – 2021 72 R&D Project – General Process TECHNICAL NEED Provider’s Eni Idea BRAINSTORMING Technology and/or IP MARKET SCOUTING PATENT PARTNER IDENTIFICATION (Single source or Tender) PARTNER IDENTIFICATION DEVELOPMENT COST SHARING FUTURE (Tender) AGREEM. R&D DEVELOP. CONDITIONS R&D EXCLUSIVITY DEVELOPMENT R&D PROJECT ROYALTIES AGREEM. DISCOUNTS Prototype IP OWNERSHIP Qualifica R&D PROJECT Manufacturing Prototype or Prototype Prototype Eni owned Pilot tools Acceptance Tests provider owned Manufacturing Acceptance Tests END OF FIELD TEST FIELD TEST R&D PHASE Depl Depl LINKED TO T&C T&C COST Deployment Deployment OF R&D CONTR. RENOGATIATED PAYMENT Agreement / Agreement / 73 Service contract Service contract Typical contracts and agreements in R&D activities Framework Cooperation Agreement (FCA) : Signed between Organisations (e.g. an Energy Company and a Service Provider) to freely discuss and identify areas of common interest to launch common Projects such as JDAs. It can include Confidentiality / includes Joint Devlopment Agreement (JDA) an agreement between an Operator and a Service Provider to join efforts to R&D develop a specific Technolofy or Product. Splitting of costs and tasks are regulated in the JDA Technology / Product developed within JDA => regulated by future Service Contract The JDA can include some key elements of the future Service Contrac Term Sheet: a preliminary, simplified agreement signed to establish the intention to proceed with JDA and fix some key points Joint industry Project (JIP): similar to JDA, in which more parties (often more Operators) join the efforts to develop a Technology or Product and eventully share the relevant benefits. Commercial Service Contract / Supply Contract: regulates the provision of Technology, Services or Goods. domain In case they are deriving from a joint R&D effort, (JDA o JIP) Operator may require specific benefits such as Exclusivity or Priority of access to technologies Royalties Discount in comparison to market price Public recognition of common effort 74 Intellectual Property Intellectual property (IP) refers to creations of the mind, such as inventions; literary and artistic works; designs; and symbols, names and images used in commerce. Patents: exclusive right granted for an invention. Copyright: literary / artistic works Trademarks: sign capable of distinguishing the goods or services Industrial Design: ornamental or aesthetic aspect of an article Geografical Indications: signs used on goods that have a specific geographical origin Trade secrets: IP rights on confidential information which may be sold or licensed IP is protected in law by. For example, patents, copyright and trademarks, which enable people to earn recognition or financial benefit from what they invent or create. 75 Source: WIPO World Intellectual Property Organisation Intellectual Property (I.P.) agreements Patent : Intellectual Property, internationally recognised by governmental bodies, that gives its owner the legal right to exclude others from making, using, or selling an invention for a limited period of time and for specific countries , in exchange for publishing an enabling disclosure of the invention. License Agreement : an agreement by which the owner of the IP (e.g. by patent) allows another Party to use the relevant IP. The License Agreement can be used by an Operator to let a Service Provider develop the Technology and bring it to commercial level through a JDA or Let other parties to freely use the Technology in exchange of Royalties Non Disclosure Agreement (NDA) Signed by two (rarely more) parties to freely share sensitive information. Binding each Party not to disclose or use without permission the information gathered in the framework of the NDA Often used to start discussion and share information not (yet) covered by Patent. Quite critical agreement. What if the Party A shares information already legally in possession of Party B, but not previously declared ? 76 TRL: Technology Readiness Level scale 77 According to IEA : International Energy Agency Prevention: Drilling Safety Package Process safety Risk Definition & Mitigation Prevention Safety devices with Innovative Activation Systems O&G Industry New Wellhead Casing Valve DownHole Eni current value Safety Valve Control Line Less Isolation Packer High density data Advanced algorithms Eni safety technologies 3 hours anticipation of stuck pipe e-wise calculation Statistic Value Wired Drill Pipe Ref. IOGP Benefits: 10-5 CERTIFICATED 10-6 Blowout risk REDUCTION OF Blowout risk RISK OF BLOWOUT 78 Risk Evaluation – e-wiseTM e-wiseTM: Eni Well Incident Systematic Evaluation: Eni’s advanced risk management model for blowout probability calculation Structured process able to calculate blowout risk probability for a specific well design Integrated and managed by a dedicated task force of D&C experts Based on fault tree methodology, considering 3 main root causes for each operative scenarios (Human Error, Mechanical Failure, Geological Conditions) MECHANICAL FAILURE (statistics) GEOLOGICAL HUMAN ERROR CONDITIONS (statistics) (offset wells + expertise) BLOWOUT PROBABILITY Certified by DNV GL 79 Drilling Safety Technologies VIDEO DRILLING SAFETY TECHNOLOGIES 80 THANKYOU 81 BACKUP MATERIAL 82 Electro Hydraulic Casing Valve Control Line Less Description/Status Casing Valve Extension Downhole Flapper Valve & Indipendent Safety barrier Springs Hinge Conceived for dry tree and subsea applications and run as an integral part of the casing string Valve Seat Flapper Valve Sizes: 13 5/8’’ field proven September 2018 9 5/8’’ available by Q3 2019 Electro-hydraulic system using RFID solution for the activation Able to isolate the reservoir from surface Benefits Flapper valve RFID Tags Enhance safety when drill string is out of well (off bottom) Reduce risk of swabbing thus reducing tripping time Enable safe deployment of slotted liners or production screens without killing the well Acronyms: Establish a mechanical barrier RFID: Radio Frequency Identification Can be applied for drilling and work over purpose 83 Electro Hydraulic Casing Valve Control Line Less – System Reliability STANDARD DDV WITH CONTRO LINE R&D Project – NEW ELECTRO HYDRAULIC CASING VALVE 13 5/8’’ size is available and 9 5/8’’ and 10 3/4’’ sizes available 9 5/8’’ size will be available in Q3 2019 No control line. Control line needed High Tech Solution RFID sub Not Applicable in subsea Suitable for subsea operations operations Run in hole/cementing issues Receiver and No issue due to control line battery Pack due to presence of control line Hydraulic Control line Micropumps Casing Valve Casing Valve Technology Reliable – more than 500 INSTALLATION so far 84 Electro Hydraulic Casing Valve Control Line Less – Main Operations Benefits Drill reservoir ✓ section: e.g. high Replacement of Hydrostatic Barrier permeability, reduced drilling ✓ margin, etc... RFID Activation – High Tech Solution Trip into casing shoe and activate valve ✓ Compatible with MPD / PMCD methods ✓ In case of failure, no NPT Safely POOH ✓ Reduced Blowout Risk ✓ Activation on demand 85 New Electro Hydraulic Casing Valve – Technology Details The Casing Valve without control line features a new activation performed through an Antenna electro-hydraulic system using a full RFID Gas solution HydroPump Influx Unit The Casing Valve is activated by hydraulic pump feed by downhole power batteries Assy Length : 13 m triggered though RFID tags installed in a sub. The whole system is incorporated in the casing POOH string with internal control lines above csg shoe RFID Tags are installed in the bit sub, in 9 5/8” casing shoe or in wireline BHAs as required Actuator Sleeve An antenna embedded in the tool interprets instruction provided by RFID tags enabling the Close opening/closing of the flapper valve, activated the RESERVOIR ISOLATED Flapper Valve Valve FROM SURFACE by hydraulic pumps and POOH Size: 13 5/8’’ 86 Downhole Isolation Packer – DHIP DHIP - Isolation element Description/Status Drilling Rig Additional Indipendent Safety barrier on the top of the BHA Bypass valve Activated with Wired Drill Pipes from surface Inflated packer Able to seal the annulus between formation and drill string by element inflating a rubber element Able to isolate the inner of drill pipe by closing a ball valve String valve Enable the circulation above the packer Size Available 8 ½” hole– Field proven December 2018 DHIP stored in warehouse Benefits Decrease environmental and blow out risk Improve operations safety levels and well control procedures Represent a downhole mechanical device Simplify the well control operation 87 DHIP – System Overview Battery BCPM Sub Power & Com RSS MWD Wired Pipe WDP Downhole Adapter Isolation Packer Bypass String Valve Valve Sub DHIP - Isolation element Inflatable Packer 88 Downhole Isolation Packer – DHIP Bypass Valve Packer String Valve Bit Kicking Formation 89 New Wellhead Safety Valve – NWSV New Wellhead Safety Valve System Description/Status Fully autonomous and independent safety barrier Able to cut most tubulars which may be present in the well in case of BOP failure (3rd barrier) Able to seal the well from the external environment, even in case of uncontrolled well flow Control Unit Actuated by a dedicated and independent Power & Control System NWSV Under Qualification Benefits Provide an independent surface well device Decrease environmental and blow out risk NWSV NWSV disassembled after test Improve operations safety levels and well control procedures 90 NWSV – Shearing Test Test performed in May/June 2018 Description Characteristics 9 5/8” Casing 53.5# - P110 5 1/2” Drill Pipe (Body 24.7# - S135 and Tool Joint) 91 NWSV – Way Forward Dry Wellhead SubSea Wellhead NWSV Control Unit Feasibility / Conceptual Design by Q2 2019 92 Upstream Process PROSPECTS RESERVOIR BASINS/AREAS DEFINITION/ DELINEATION & DEVELOPMENT PRODUCTION ABANDONMENT ASSESSMENT DISCOVERY MODELLING Regional studies Seismic survey & Appraisal drilling Development plan Production Wells plugging interpetation & environmental management & Geological Reservoir studies Plant removal aspects optimization modelling Drilling Reservoir Environmental Drilling & Reservoir Bid evaluation Subsurface modelling & restoration completion management geology reserves definition Farm in/out Surface facilities Wells opportunities Production tests Feasibility studies construction & interventions installation (4%) (10%) (10%) (12%) (60%) (4%) Life cycle project (2%) (5%) (8%) (45%) (35%) (5%) Costs project Cumulative Cash flow Time 93 How to Drill a Well? Rig Floor Mud Pits Drill Bits Drill Mud 94 Petroleum System Erosion Sedimentation Gas Oil accumulation Cap rock Migration Displacement Expulsion Source rock Maturation Compaction/Diagenesis 95 Geophysical Prospecting - Seismics The ground is examined using sound waves to obtain a seismic echo. The onshore exploration for deposits with seismics is generally conducted using shot seismics or vibro-trucks. In offshore seismics, special ships equipped with air guns are used to explore oil and gas fields under the ocean with air pressure waves. 96 Seismics Data Interpretation The reflection or refraction of sound waves at the boundary surfaces of different layers of rock allows geological formations to be identified. The time that it takes for the wave to return to the surface tells us how far down the geological boundary is located. Interpreting the sound waves recorded by geophones makes it possible to determine the size and depth of crude oil and natural gas deposits. 97 Reservoir Model The reservoir model is obtained through the integration of geophysical and geological data. In the image: seismic section velocities section top of the exploration target with two structural traps highlighted tracks of drilled wells three levels of the geological model 98 Operational Safety Assurance 1 Design Well Design 2 Prevention Drilling Fluids Blow-out Preventer (BOP) Additional Well Barrier 3 Mitigation Dual ROV - Killing System Rapid CUBE Clean Sea Dispersants Surface Containment Capping Stack 99