Offshore Drilling and Petroleum Production Practices PDF
Document Details
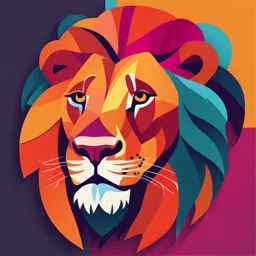
Uploaded by HighSpiritedChalcedony3557
IIT (ISM) Dhanbad
Raj Kiran, PhD
Tags
Related
- ADNOC Offshore Technical Standard (A0-LOG-V-STD-002) PDF July-2020
- ADNOC Offshore Standing Instructions for Marine Operations (SIMO) PDF February-2019
- ADNOC Offshore Marine Notice - 03/2022
- Drilling Rigs Types Chapter 4 PDF
- Assessing Impacts Of Offshore Wind Farms On Fishers And Fish Catch PDF
- UT7. Parques Eólicos Marinos - Offshore PDF
Summary
This document provides an overview of offshore drilling and petroleum production practices, focusing on unit 6: offshore well completion. It covers topics such as well completion, equipment, and specific operations. The document likely serves as a technical guide for professionals in the oil and gas industry.
Full Transcript
Offshore Drilling and Petroleum Production Practices Unit 06: Offshore Well Completion Raj Kiran, PhD Assistant Professor Disclaimer: This material is created for academic purpose and property of IIT (ISM). It should not be reproduced or freely distributed in any form. Content ❑ Plat...
Offshore Drilling and Petroleum Production Practices Unit 06: Offshore Well Completion Raj Kiran, PhD Assistant Professor Disclaimer: This material is created for academic purpose and property of IIT (ISM). It should not be reproduced or freely distributed in any form. Content ❑ Platforms and subsea completions ❑ Deep water applications of subsea technology Slide 2 Overview What is well completion? ▪ Process of making a well ready for production. ▪ Incorporates steps taken to transform a drilled well into a producing one. ▪ Link between drilling the borehole and the production phase. Slide 3 Overview What is well completion? ▪ After reaching target depth, the formation is tested and evaluated to determine whether the well is to be completed for production or plugged and abandoned. ▪ To complete the well production, casing is installed and cemented, and the drilling rig installations are dismantled and moved to the next site. ▪ A service rig is brought in to perforate the production casing and run production tubing along with down hole equipment. ▪ The installation of surface safety equipment takes place and production begins. Slide 4 Overview Steps for well completion 1. Drilling fluid in the well displaced with a completion fluid composed of brine (i.e., Water + NaCl or CaCl2 or ZnBr2). 2. Perforation of the casing/liner. 3. Gravel packing to stop the production of sand 4. Work string replaced by the completion string (tubing with packer, safety devices, circulation and communication devices, and accessories). 5. After setting of packer, completion fluid displaced with a permanent, corrosion-resistant fluid 6. Removal of BOP and installation of the X-mas tree over the wellhead 7. Connection of flowlines with X-mas tree Slide 5 Well Completion Equipment Subsurface Completion Equipment Slide 6 Well Completion Equipment Surface Completion Equipment: wellhead, tubing hanger and Christmas tree. Slide 7 Completion Specific Operations ▪ Perforation and gravel packing ▪ To make the well fluid flow to the wellbore continuously without any problem ▪ Stimulation operation in case of damaged formation Slide 8 Completion Specific Operations Perforation ▪ Carried out either in underbalanced conditions using tools such as tubing conveyed perforation (TCP) or in overbalanced conditions, using perforation tools that are deployed down the wellbore on wireline. Slide 9 Completion Specific Operations Gravel Packing ▪ Unconsolidated Sand – cause erosion of equipment, and wellbore and flow string plugging to the extent that well operation becomes uneconomical ▪ Screening techniques include: ✓ Use of slotted or screen liners ✓ Gravel packing Slide 10 Well Completion Design Basic decisions in designing the well completion ▪ Method of completion ▪ Number of completions within the wellbore, ▪ Casing-tubing configuration, ▪ Diameter of the production conduit ▪ Completion interval. Slide 11 Offshore Well Completion Methods ▪ Reduction in weight and minimization of space requirements in offshore completion ▪ Use of composite valves and closer spacing between the wells ▪ SSSV installed in the tubing string below the mud line in order to close the well automatically ▪ Preferable technique – multiple completion techniques ▪ Well can either be completed at the deck level or subsea ▪ Classified as deck level completion / platform completion and subsea completion Slide 12 Offshore Well Completion Methods Deck Level Completion ▪ Most preferred completion ▪ Well-established technology ▪ Field proven equipment ▪ Knowhow available for drilling, production and remedial functions ▪ Workover, artificial lift, water injection/enhanced recovery possible with standard and established tools and technology ▪ Constant monitoring by personnel ▪ Higher platform cost Slide 13 Deck Level Completion ▪ Possible with fixed bottom or compliant type platforms like steel jacket platforms, steel gravity platforms, concrete gravity platforms, tension leg platforms, guyed towers ▪ While drilling from mobile drilling structures the strings of downhole casing are run and suspended at the mud line ▪ Mud line suspension equipment includes tieback devices (abandonment caps attached) ▪ Jacket structure positioned and installed over the subsea template ▪ Connection of the casings at the deck level. ▪ Wells tied back with casing extensions, called risers. Slide 14 Deck Level Completion Installation of Jacket over Template ▪ Technique – Bumper pile jacket installation ▪ Jacket first delivered to template area and ballasted to the vertical position with the legs approximately 30 ft above sea floor. ▪ Winch lines rigged to fixed mooring points. ▪ After prealigning, slowly winched toward template until jacket guides contact bumper piles. ▪ Jacket then ballasted and fixed in position. Slide 17 Deck Level Completion Installation of Jacket over Template ▪ Technique – Guide pile jacket installation ▪ Jacket lowered over guide piles of uneven height. ▪ Piles installed either just prior to, or just after, the wells are drilled. ▪ Uneven pile height allows the jacket to be landed on the taller pile first. ▪ Jacket turned on the taller pile until properly positioned over the shorter pile. ▪ Lowered to the bottom and fixed in place. Approach used primarily for lightweight platforms. Slide 18 Deck Level Completion Tie-Back Methods ▪ After positioning and installation of platform over the subsea template, the outer, or largest, casing tie-back string connected to the subsea wellhead. ▪ First tie-back string accurately guided into position on the subsea wellhead using the platform conductor guides ▪ Two methods compatible with template wells ▪ Methods employ two different tie-back adapters – standard and external lock tie-back adapter Slide 19 Deck Level Completion Tie-Back Methods Standard tie-back adapter ▪ Incorporates a downward-looking funnel that serves to align the tie-back string with the wellhead. ▪ Threaded internal lock-down sub ▪ Funnel stronger than the casing string in terms of resistance to bending. ▪ Weight of the casing used (sometimes additional weight) to seat the adapter over the wellhead housing. Slide 20 Deck Level Completion Tie-Back Methods Standard tie-back adapter ▪ After landing the adapter, an internal lockdown sub made up into the left- hand running threads of the wellhead housing by a torque tool ▪ Torque tool run on a drill pipe inside the casing. ▪ Casing and the adapter not rotated during make-up of the internal lockdown sub. Slide 21 Deck Level Completion Tie-Back Methods Standard tie-back adapter ▪ Guide ribs or centralizers used on outer tie-back string. ▪ Centralizers can be either concentric or eccentric (depending on the severity of offset or angular misalignment encountered when tying-back the wells) ▪ Concentric centralizers impose no offset and can be used if wellhead-to- platform offset is minimal (