NOVA FAB LAB Wood II (Yellow) Safety Training PDF
Document Details
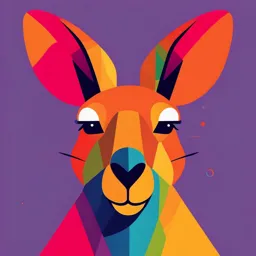
Uploaded by CheapestJadeite1998
Northern Virginia Community College
null
null
Tags
Summary
This document is a training guide for woodworking safety and techniques, specifically for Wood II (Yellow) safety training at NOVA Community College. It covers the usage of various woodworking tools and best safety practices.
Full Transcript
NOVA Makers – Wood II (Yellow) Safety Training Wood II (Yellow) Safety Training OBJECTIVES Training Objectives: Understand when to use each tool and plan common operations for safety, accuracy and precision Demonstrate correct, safe use of Yellow tools: Table Saw, Mite...
NOVA Makers – Wood II (Yellow) Safety Training Wood II (Yellow) Safety Training OBJECTIVES Training Objectives: Understand when to use each tool and plan common operations for safety, accuracy and precision Demonstrate correct, safe use of Yellow tools: Table Saw, Miter Saw, Jointer/Planer, Pole/Disc Sander Troubleshoot common issues on each machine Advanced Fabrication Concepts Fabrication Concept: Order of Operations Materials In fabrication, the order of operations refers to the systematic sequence of steps or processes that need to be followed to create a part or product accurately, safely, and efficiently. Cutting into Parts Assembly Fabrication Concept: Order of Operations Common Order of Operations: o Planning and Design o Marking and Measuring o Cutting and Milling o Drilling and Machining o Assembly o Finishing Yellow tools focus on the bold operations Fabrication Concept: Planning and Design Planning may involve: o Dimensioned Sketches with Several Views ▪ Technical Drawing ▪ General Sketches o Cut-list & Hardware List ▪ List of raw materials to buy ▪ List of different parts (with finished dimensions) made from raw materials ▪ List of hardware necessary for assembly Fabrication Concept: Design Tips for a better design: Look at similar products – build a reference library Generate multiple ideas and multiple results Refine ideas with lots of sketches. Bring a detailed sketch when asking Fab Lab staff for feedback Fabrication Concept: Milling Milling involves: o Order of Operations: ▪ Cross-cut materials to rough dimensions, creating smaller, more easily worked workpieces. ▪ Jointing and planning for 1 square corner ▪ Rip to width. ▪ Cross-cutting to length. Fabrication Concept: Ripping and Cross Cutting Ripping a board to width cuts along the grain Cross-cutting a board to length cuts across the grain. Plywood only has a grain on the veneers – ripping means cutting parallel to the longest dimension. Fabrication Concept: Lumber & Sheet Goods Wood is sold in different ways to different industries. Lumberyards sell soft- and hardwoods by the board-foot (volume) for fine furniture and trim carpentry applications. Hardwood Softwood Plywood Home centers and building supplies sell construction lumber sold by the piece to the construction industry. Wood Species Deciduous trees: lose leaves annually Evergreen trees: keep needles and cones all year Hardwood Softwood Oak Pines Walnut Firs Maple Spruces Cherry Cedars Beach Redwoods Ash Cypress Wenge Zebra Lace Jatoba Teak Purpleheart Wood Species Maple Alder Ash Ipe Cherry Teak Pine Brazilian Cherry Red Oak White Oak Hickory Purple Heart Rosewood Spruce Bocote Mahogany Birch Walnut Zebrawood Cedar Douglass Fir Wood Cuts / Grain Live Edge Wood Grades Species Grade Moisture Certification Mill Buying Good Materials Bow Cup Twist Crook Sheet Goods Sheet Goods Cores Amount of plies Grades Plywood Veneer Core Baltic Birch Grade A: The face and back of the sheet is nearly Composite MDF Core Russian Birch free of defects, with a smooth, sanded surface OSB Lumber Core and virtually no knots. Good for cabinet doors and Engineered wood Apple Core furniture, the surface is meant to be seen and can MDF be painted or stained. Plyboo Masonite Grade B: Sanded smooth, but the face and back Melamine have a few defects Grade C: Unsanded with tight knots up to 1 ½ inches wide. There may be large areas that have been patched and filled. Grade D: Unsanded, with knot holes up to 2 ½ inches wide and liberal use of patches and filler. good for structural uses where it will not be seen. Yellow Tool Safety Miter Saw: Anatomy Miter Saw Trigger Safety Lock Trigger HIGH RISK Vacuum Dust Purpose: Chute Cross-Cut material to a rough or final dimension Miter-Cut trim for angled Blade joints Blade Guard Cut Complex Bevel cuts for crown-molding Fence Miter Indent Table Miter Lock Knob Miter Saw: Safety Considerations Laceration Risk: the blade of the miter saw can lacerate/amputate if it contacts the body of the user. Flying Debris: the workpiece can bind against the blade and be thrown from the machine Miter Saw: Material Considerations Cross cuts only! The miter saw can only safely crosscut. Rip cuts are very dangerous due to the chance of binding. Allowed Materials: Hardwoods, plywood, finished boards, melamine, MDF, foams. *aluminum (with correct blade) Miter Saw: Basic Operation 1. Check your PPE – tie up loose sleeves and hair. Put on hearing protection and safety glasses. 2. Check for entanglement hazards. 3. Inspect machine for damaged or loose parts. 4. Check blade for deviations from flatness, circularity, and missing teeth. 5. Test the miter mechanism and arm to ensure smooth operation. 6. Check dust collection hose is connected. 7. Adjust bevel and miter as needed for cut. 8. Locate, install, test any required jigs, fixtures or stops. 9. Place workpiece on table, press firmly against the table and fence. Clamp down if necessary. 10. Without touching the trigger, lower the blade to cut line. Make sure kerf is on waste side of board. 11. Ensure fingers and hands are > 4" from blade's path. 12. Turn on the saw with the trigger. Make sure saw is in full rotation before entering material 13. Perform cut. Miter Saw: Advanced Operation Gang-cutting – multiple pieces can be cut at the same time if the workpieces can be secured safely against the fence. Stops – allow repeatable, accurate crosscutting to a specific length. Stops can increase pinching hazards in warped boards. Miter Saw: Shut Down Procedure 1. Turn off saw by releasing the trigger while in the down position. 2. Remove work material from saw. 3. Bring saw to 90 deg, both miter and bevel, and lock the blade in the down position. 4. Vacuum dust on saw, stand, and surrounding area, do not blow off the saw. Table Saw: Anatomy Table Saw Blade Guard Table Fence GREATEST RISK Blade Purpose: Rip-Cut materials to a rough or final width Cross-Cut material to Power switch a rough or final dimension On/Off Switch Process large panels down to smaller Blade Tilting Handle pieces Blade Raising Handle Blade Tilt Gauge Table Saw: Safety Considerations Laceration/Amputation: The table saw poses the greatest risk of laceration/amputation in the wood shop. Kickback: When the wood pinches against the back of a blade, the wood can be "kicked back" at the user. This can cause internal injuries, broken bones, deep lacerations, punctures, etc. Table Saw: Safety Mitigation How to Mitigate Your Risk: Use the safety devices for every cut (i.e. rip fence for rip cut, riving knife installed, guard lowered to appropriate height) Use a push stick or push block for every cut. Verify new operations with staff member. Table Saw: Saw Blades Rip Blade: 24 teeth, large gullets, made to rip woods General Purpose Blade: 40 to 60-teeth, general use for all materials. Crosscut Blade: Above 60 teeth, made to create smooth crosscuts in lumber with little tear out. Plywood/Melamine: Specialized blade to cleanly cut specific materials. Dado Blade: A blade with an adjustable thickness, often up to 1" wide. Table Saw: Materials ** ALWAYS CHECK LUMBER FOR METALS, SCREWS, & FOREIGN OBJECTS BEFORE CUTTING ** Allowed: Hardwoods Hardwood ply-wood finished boards Melamine MDF Cardboard foam. Prohibited: Pressure-treated lumber. Softwoods Green lumber (branches, stumps, etc.) Metals. Concrete, glass, tile, etc. Table Saw: Materials Moisture Meter: checks moisture of material before use. Always check air- dried lumber. Magnetic Wand: checks for embedded metal in the wood before using on table saw. Table Saw: Basic Operations 1. Check your PPE – tie up loose sleeves and hair. Put on hearings protection and safety glasses. 2. Check for entanglement hazards and make sure other makers know not to walk behind the table saw. 3. Inspect the machine for damage or loose parts, specifically cords, blades and rip fence. 4. Turn on start-switch with the paddle switch off. 5. Check wood for dryness. Test if concerned. 6. Check rip fence or miter gauge for squareness. 7. Collect appropriate safety devices. 8. Ensure jigs & fixtures work as expected. 9. ALWAYS USE THE RIVING KNIFE FOR RIP AND CROSS CUTS. 10. If you need to change the blade for a dado cut, ask staff. 11. Adjust blade height and angle. 12. Turn on the start-up switch. Wait for a green light. 13. Turn on the dust collector. 14. Turn on SawStop (pull knee switch). 15. Listen for unexpected noises. 16. Perform operation. Table Saw: Shut Down Procedure 1. Turn off SawStop (knee switch), paddle switch off. 2. Turn off dust collector. 3. Return SawStop to original state. o Proper blade re-installed and 90 degrees. o Blade parked at zero-depth (under the table) 4. Vacuum dust on SawStop and surrounding area, do not blow off the machine. Table Saw: Rip Cut Set Up: Set fence at appropriate width. Gather push sticks and push blocks. Install feather board if cut is especially awkward. Adjust height of blade to 1 tooth above material. Table Saw: Rip Cut Operation: Turn on machine while workpiece is not in contact with the blade. Push workpiece along fence, maintaining contact throughout. When appropriate, use push sticks when your hands get too close to blade – never let go of board, but use one hand to control. Push all the way through the blade. Maintain proper speed throughout cut. Table Saw: Rip Cut Troubleshooting Burning: Some woods (cherry, Maple) burn easily Moving too slow through operation. Wrong blade installed Table Saw: Cross Cut Set Up: Set up miter gauge at appropriate degree. Move the rip fence away from cut. Check for contact between metal portion of gauge and blade. Check for pinching between blade and rip fence. Do not use if blade can touch metal or work slides along rip fence Adjust height of blade to 1 tooth above material. Table Saw: Cross Cut Operation: Turn on machine while workpiece is not in contact with the blade. Firmly hold workpiece against miter gauge. Push all the way through the blade. Maintain proper speed throughout cut. Table Saw: Cross Cut Troubleshooting Tear Out: Use a backer board to minimize tear out – especially useful for locating precise cuts Check to make sure a cross-cut or general-purpose blade is installed. Table Saw: Bevel Cuts The blade angled to the table surface creates a bevel cut. Set Up: Use the hand wheel to set the angle. Use a digital angle gauge to set up for a precise angle. Set up for a rip or cross Table Saw: Bevel Cuts Safety Considerations: Bevel cuts increase the chance of kickback by the offcut. Offcuts from bevel cuts can be long and pointy – minimize bodily exposure to cuts as much as possible. Jointer: Anatomy Jointer High RISK Fence Purpose: Create one flat side Infeed and edge of a board Create a perfect 90º square edge Blade Guard Blade (Underneath Blade Guard) Outfeed Jointer: Safety Considerations Jointer High Risk Laceration/Amputation: Contact with the blade will result in severe injuries. Entanglement: Contact with the spinning blade due to long sleeves, loose jewelry, etc, will result in severe injuries. Jointer: Safety Considerations Allowed: Hardwoods Hard- and softwoods only. Wood must be 12" or longer. Wood must be clear of nails, screws, metal shavings, etc. Prohibited: Pressure-treated lumber Green lumber Softwoods Foams, plastics, etc. Jointer: Basic Operation 1. Check your PPE – tie up loose sleeves and hair. Put on hearings protection and safety glasses. 2. Check for entanglement hazards. 3. Inspect the machine for damage or loose parts. 4. Adjust the Jointer Guard: 1. For face jointing: Raise the guard higher than the workpiece's thickness. 2. For edge jointing: Pull the guard back to expose the minimum cutting head necessary. 5. Ensure the fence angle meets your needs, usually 90 degrees. 6. Collect appropriate safety devices. 7. Perform a dry run with the machine off. 8. Jointing End Grain is Prohibited 9. Do not adjust depth of cut – make more passes. 10. Turn on the dust collector, check for proper suction, and adjust blast-gate as necessary. 11. Turn on the jointer and listen for unexpected noises. 12. Begin operation. Jointer: Face Jointing Face Jointing: Creates a flat face on the widest face of the workpiece. This is a long-grain operation – do not joint the end grain of a board. Jointing end-grain causes massive blowouts and increases your risk of injury. Do not use the fence to while face jointing – refer to the illustration for proper safety guard set up. Jointer: Edge Jointing Edge Jointing: Creates a flat edge square to the jointed face, creating a square corner. Proper guard set up, use of push blocks and hand position are crucial for safety. Jointer: Troubleshooting Burning: Some woods (cherry, Maple) burn easily Moving too slow through operation. o Lower depth of pass o Increase feed speed. Spindle Sander: Anatomy Spindle Sander MEDIUM RISK Oscillating Sander Purpose: Worktable Sand materials quickly and safely. Disc Sander Sand concave and convex curves. Worktable Square a cross-cut surface for joints Miter Gauge On/Off Switch Bandsaw: Safety Considerations Entanglement Hazard: The disc/oscillating sander can cause scrapes and cuts if loose clothes get caught in machinery. Respiratory Hazard: Dust can irritate lungs and trigger asthma – long term exposure carries more risks. Dual Sander: Air Filtration Air Filters are turned on by switch and remote. Switch: By lumber rack. Remote: in Shop Supplies drawer. Dual Sander: Material Considerations Allowed: Kiln-dried lumber Plywood Melamine MDF *Foam *Plastics Prohibited: Pressure-treated lumber Green lumber NO METAL – FIRE HAZARD * May require cleaning of sandpaper. Please notify staff before using these materials on sander. Oscillating Sander: Basic Operation 1. Check your PPE - tie up loose sleeves and hair. Put on hearing protection and safety glasses. 2. Check for entanglement hazards. 3. Inspect the machine for damage or loose parts. 4. Install the appropriate diameter sanding drum for your operation. 5. Turn on sander. 6. Begin sanding operation from the appropriate side of the sanding drum. Dual Sander: Shut Down Procedure 1. Turn off the dual sander. 2. Turn off dust collector. 3. Wait until disc and oscillating drum stop spinning. 4. Vacuum dust on sander and surrounding area, do not blow off the machine. Dual Sander: Troubleshooting Burning: Some woods (cherry, Maple) burn easily Sandpaper is clogged – ask staff to clean or replace sandpaper. Sandpaper is too fine for operation – ask staff to switch to lower grit. Material and Hardware Policy in the Woodshop MATERIAL & HARDWARE IN THE WOODSHOP The Fab Lab provides a limited selection of plywood for purchase. Makers may bring materials from outside sources, but all materials must be vetted by Fab Lab staff. Fab Lab provides a variety of hardware and fasteners in the hardware section of the woodshop. Makers must provide their own hardware and fasteners if not available in hardware selection. Makers can request hardware using the appropriate request form for class and club projects only. Hardware requests are not guaranteed to be filled. Fab Lab provides 80-, 120-, 180-, 220- and 320- grit sandpaper. The Fab Lab does not provide spray paint and finishes; however, leftover spray paint and finishes may be available for use.