Wood Aircraft Repair Techniques PDF
Document Details
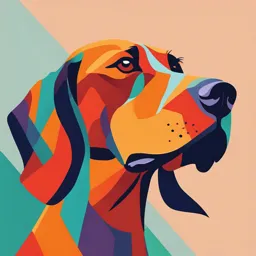
Uploaded by DaringDream
Tags
Summary
This document provides detailed instructions and diagrams for repairing wood components in aircraft. It covers various repair techniques, including scarf, patch, and splice methods for spars and ribs, along with detailed procedures.
Full Transcript
Damaged area Top A 10A A B C D and E are original C dimensions dimensions. B Face grain of plywood D Spruce block Damaged area and glue glue Plywood, nail, and E Figure 6-19. Rib trailing edge repair. Figure 6-17. Cap strip repair at a spar. A IIncorrect Incorr Inc ncorrectt B Incorr...
Damaged area Top A 10A A B C D and E are original C dimensions dimensions. B Face grain of plywood D Spruce block Damaged area and glue glue Plywood, nail, and E Figure 6-19. Rib trailing edge repair. Figure 6-17. Cap strip repair at a spar. A IIncorrect Incorr Inc ncorrectt B Incorrect Incorrectt Incorr Inc a standard rib with rectangle compression members added to one side and a plywood web to the other side. The method used in this repair is essentially the same as in Figure 6-20A, except that the plywood reinforcement plate, shown in Figure 6-20B-B, is continued the full distance between the spars. Figure 6-20C illustrates a compression rib of the I type with a rectangular vertical member on each side of the web. The method of repair is essentially the same as in Figure 6-20A, except the plywood reinforcement plates on each side, shown in Figure 6-20C-C, are continued the full distance between the spars. Wing Spar Repairs Wood wing spars are fabricated in various designs using solid wood, plywood, or a combination of the two. [Figure 6-21] C Correct Correc Correc Cor rectt Figure 6-18. Relationship of scarf slope to grain slope. and lower cap strips, the web member, and the compression members are cracked completely through. To facilitate this repair, cut the compression members as shown in Figure 6-20D and repair as recommended using replacement sections to the rear spar. Cut the damaged cap strips and repair as shown in Figure 6-20, replacing the aft section of the cap strips. Plywood side plates are then bonded on each side diagonally to reinforce the damaged web as shown in Figure 6-20, A-A. When a spar is damaged, the method of repair must conform to the manufacturer’s instructions and recommendations. In the absence of manufacturer’s instructions, contact the FAA for advice and approval before making repairs to the spar and following recommendations in AC 43.13-1. If instructions are not available for a specific type of repair, it is highly recommended that you request appropriate engineering assistance to evaluate and provide guidance for the intended repair. Shown in Figure 6-22 is a recommended method to repair either a solid or laminated rectangle spar. The slope of the scarf in any stressed part, such as a spar, should not be steeper than 15 to 1. Figure 6-20B illustrates a compression rib of the type that is 6-14 MAGE DA A Repair See D A 3A 3A A B MAGE DA Repair B B MAGE DA C Repair C C 12A recommended 10A minimum 6A ¼A A 6A D 2A A - A ¼A B - B C - C Plywood reinforcement same thickness and face grain direction as original Figure 6-20. Typical compression rib repair. Unless otherwise specified by the aircraft manufacturer, a damaged spar may be spliced at almost any point except at wing attachment fittings, landing gear fittings, engine mount fittings, or lift-and-interplane strut fittings. These fittings may not overlap any part of the splice. The reinforcement plates of the splice should not interfere with the proper attachment or alignment of the fittings. Taper reinforcement plates on the ends at a 5:1 slope [Figure 6-23]. of an aircraft is dependent on the accessibility to the damaged section. It may not be possible to utilize a scarf repair where recommended, so the component may have to be replaced. A scarf must be precisely cut on both adjoining pieces to ensure an even thin glue line; otherwise, the joint may not achieve full strength. The primary difficulty encountered in making this type of joint is obtaining the same bevel on each piece. [Figure 6-24] The use of a scarf joint to repair a spar or any other component The mating surfaces of the scarf must be smooth. You can 6-15 Box I Double I C Plain rectangular Routed Figure 6-21. Typical splice repair of solid rectangular spar. 6A recommended 5A minimum 2A A 6A recommended 5A minimum 15A minimum No fittings within these limits A / 1 4A Direction of grain if spruce or outer face grain if plywood Figure 6-22. Typical splice repair of solid rectangular spar. machine smooth a saw cut using any of a variety of tools, such as a plane, a joiner, or a router. For most joints, you need a beveled fixture set at the correct slope to complete the cut. Figure 6-25 illustrates one method of producing an accurate scarf joint. Once the two bevels are cut for the intended splice, clamp the pieces to a flat guide board of similar material. Then, work a sharp, fine-tooth saw all the way through the joint. Remove the saw, decrease pressure, and tap one of the pieces on the end to close the gap. Work the saw again through the joint. Continue this procedure until the joint is perfectly parallel 6-16 Feathered end Undamaged section 5:1 slope New section to be spliced in Figure 6-23. Tapered faceplate. Guide board Figure 6-25. Making a scarf joint. Slope 10 to 1 in solid wood Routed scaft A Edges are guide for router base Correctly beveled pieces Gap B Incorrect beveled pieces Figure 6-24. Beveled scarf joint. with matching surfaces. Then, make a light cut with the grain, using a sharp plane, to smooth both mating surfaces. Slope fixed as appropriate 10:1 to 12:1, etc. Clamp work piece to fixture Another method of cutting a scarf uses a simple scarf-cutting fixture that you can also fabricate for use with a router. Extend the work piece beyond the edge so the finished cut results in a feathered edge across the end of the scarf. [Figure 6-26] There are numerous tools made by individuals, and there are commercial plans for sale with instructions for building scarfcutting tools. Most of them work, but some are better than others. The most important requirement for the tool is that it produces a smooth, repeatable cut at the appropriate angle. Local damage to the top or bottom edge of a solid spar may be repaired by removing the damaged portion and fabricating a replacement filler block of the same material as the spar. Full width doublers are fabricated as shown and then all three pieces are glued and clamped to the spar. Nails or screws should not be used in spar repairs. A longitudinal crack in a solid spar may be repaired using doublers made from the proper thickness plywood. Care must be taken to ensure the doublers extend the minimum distance beyond the crack. Figure 6-26. Scarf cutting fixture. [Figure 6-27] A typical repair to a built-up I spar is illustrated using plywood reinforcement plates with solid wood filler blocks. As with all repairs, the reinforcement plate ends should be feathered out to a 5:1 slope. [Figure 6-28] Repair methods for the other types of spar illustrated at the start of this section all follow the basic steps of repair. The wood used should be of the same type and size as the original spar. Always splice and reinforce plywood webs with the same type of plywood as the original. Do not use solid wood to replace plywood webs because plywood is stronger in shear than solid wood of the same thickness. The splices and scarf cuts must be of the correct slope for the repair with the face 6-17 Scarf at ends of insert No less than 12 to 1 5 to 1 slope (minimum) Insert block—same species as spar No fitting within these limits A Local damage 3A / B 10 (max) 3A ¼A LONGITUDINAL CRACK B Face grain direction of Note: 1. Make doublers from plywood for longitudinal crack repairs on spar face 2. Make doublers from solid wood (same species as spar) for insert repair of top doublers or bottom of spar Figure 6-27. A method to repair damage to solid spar. grain running in the same direction as the original member. Not more than two splices should be made in any one spar. When a satisfactory repair to a spar cannot be accomplished, the spar should be replaced. New spars may be obtained from the manufacturer or the holder of a PMA for that part. An owner-produced spar may be installed provided it is made from a manufacturer-approved drawing. Care should be taken to ensure that any replacement spars accurately match the manufacturer’s original design. 6A Bolt & Bushing Holes All bolts and bushings used in aircraft structures must fit snugly into the holes. If the bolt or bushing is loose, movement of the structure allows it to enlarge the hole. In the case of elongated bolt holes in a spar or cracks in close proximity to the bolt holes, the repair may require a new section to be spliced in the spar, or replacement of the entire spar. All holes drilled in a wood structure to receive bolts or bushings should be of such size that inserting the bolt or bushing requires a light tapping with a wood or rawhide mallet. If the hole is so tight that heavy blows are necessary, 15A 2A 6A 2A 2A A No fitting within these limits ½B A A Direction of grain in plywood reinforcement plates to be same as original web B Solid wood filler block Solid wood filler block Plywood Solid wood filler block Plywood Solid wood filler block Figure 6-28. Repairs to a built-up I spar. 6-18 deformation of the wood may cause splitting or unequal load distribution. For boring accurate smooth holes, it is recommended that a drill press be utilized where possible. Holes should be drilled with sharp bits using slow steady pressure. Standard twist drills can be used in wood when sharpened to a 60° angle. However, a better designed drill was developed for wood boring called a lip and spur or brad point. The center of the drill has a spur with a sharp point and four sharp corners to center and cut rather than walk as a conventional drill sometimes does. It has the outside corner of the cutting edges leading, so that it cuts the periphery of the hole first and maximizes the chance that the wood fibers cut cleanly, leaving a smooth bore. Forstner bits bore precise, flat bottomed holes in wood, in any orientation with respect to the wood grain. They must be used in a drill press because more force is needed for their cutting action. Also, they are not designed to clear chips from the hole and must be pulled out periodically to do this. A straight, accurate bore-through hole can be completed by drilling through the work piece and into a piece of wood backing the work piece. All holes bored for bolts that are to hold fittings in place should match the hole diameter in the fitting. Bushings made of steel, aluminum, or plastic are sometimes used to prevent crushing the wood when bolts are tightened. Holes drilled in the wood structure should be sealed after being drilled. This can be accomplished by application of varnish or other acceptable sealer into the open hole. The sealer must be allowed to dry or cure thoroughly prior to the bolts or bushings being installed. Plywood Skin Repairs Plywood skin can be repaired using a number of different methods depending on the size of the hole and its location on the aircraft. Manufacturer’s instructions, when available, should be the first source of a repair scheme. AC 43.13-1 provides other acceptable methods of repair. Some of those are featured in the following section. Fabric Patch A fabric patch is the simplest method to repair a small hole in plywood. This repair is used on holes not exceeding 1-inch in diameter after being trimmed to a smooth outline. The edges of the trimmed hole should first be sealed, preferably with a two-part epoxy varnish. This varnish requires a long cure time, but it provides the best seal on bare wood. The fabric used for the patch should be of an approved material using the cement recommended by the manufacturer of the fabric system. The fabric patch should be cut with pinking shears and overlap the plywood skin by at least 1-inch. A fabric patch should not be used to repair holes in the leading edge of a wing, in the frontal area of the fuselage, or nearer than 1-inch to any frame member. Trim to circular shape (15T maximum diameter) Minimum distance to frame = 15T Face grain of patch parallel to face grain of skin Weights or clamp Pressure plate 8" or ¼" plywood T = 10" or less Waxed paper or plastic wrap 5T 5T Plywood skin Figure 6-29. Splayed patch. 6-19 Splayed Patch A splayed patch is a flush patch. The term splayed denotes that the edges of the patch are tapered, with the slope cut at a 5:1 ratio to the thickness of the skin. This may be used for small holes where the largest dimension of the hole to be repaired is not more than 15 times the skin thickness and the skin is not more than 1»10-inch thick. This calculates to nothing larger than a 1½-inch trimmed hole in very thin plywood. Using the sample 1»10-inch thick plywood and a maximum trimmed hole size of 1½-inches, and cutting a 5:1 scarf, results in a 2½-inches round section to be patched. The patch should be fabricated with a 5:1 scarf, from the same type and thickness plywood as the surface being repaired. Glue is applied to the beveled edges and the patch is set with the grain parallel to the surface being repaired. A pressure plate of thicker plywood cut to the exact size of the patch is centered over the patch covered with waxed paper. A suitable weight is used for pressure until the glue has set. The repair is then sanded and finished to match the original surface. [Figure 6-29] Surface Patch Plywood skins not over 1»8-inch thick that are damaged between or along framing members may be repaired with a surface or overlay patch. Surface patches located aft of the 10 percent chord line, or which wrap around the leading edge and terminate aft of the 10 percent chord line, are permissible. You can use surface patches to patch trimmed holes up to a 50-inch perimeter, and may cover an area as large as one frame or rib space. Trim the damaged area to a rectangle or triangular shape with rounded corners. The radius of the corners must be at least 5 times the skin thickness. Doublers made of plywood at least ¼-inch thick are reinforcements placed under the edge of the hole inside the skin. Nail and glue the doublers in place. Extend the doublers from one framing member to another and strengthen at the ends by saddle gussets attached to the framing members. [Figure 6-30] The surface patch is sized to extend beyond the cutout as indicated. All edges of the patch are beveled, but the leading edge of the patch should be beveled at an angle at least 4:1 of the skin thickness. The face-grain direction of the patch must be in the same direction of the original skin. Where possible, weights are used to apply pressure to a surface patch until the glue has dried. If the location of the patch precludes the use of weight, small round head wood screws can be used to apply glue pressure to secure the patch. After a surface patch has dried, the screws can be removed and the holes filled. The patch should be covered with fabric that overlaps the original surface by at least 2-inches. The fabric should be from one of the approved fabric covering systems using the procedures recommended by the manufacturer to cement and finish the fabric. Plug Patch Two types of plug patch, oval and round, may be used on plywood skins. Because the plug patch is only a skin repair, use it only for damage that does not involve the supporting structure under the skin. Cut the edges of a plug patch at right angles to the surface of the skin. Cut the skin also to a clean round or oval hole with edges at right angles to the surface. Cut the patch to the exact size of the hole; when installed, the edge of the patch forms a butt joint with the edge of the hole. You can use a round plug patch where the cutout repair is no larger than 6-inches in diameter. Sample dimensions for holes of 4-inches and 6-inches in diameter appear in Figure 6-31. The following steps provide a method for making a round plug patch: 1. Cut a round patch large enough to cover the intended repair. If applicable for size, use the sample dimensions in Figure 6-31. The patch must be of the same material and thickness as the original skin. 2. Place the patch over the damaged spot and mark a circle of the same size as the patch. 3. Cut the skin inside the marked circle so that the plug patch fits snugly into the hole around the entire perimeter. 4. Cut a doubler of soft quarter-inch plywood, such as poplar. A small patch is cut so that its outside radius LV »LQFK JUHDWHU WKDQ WKH KROH WR EH SDWFKHG DQG WKH LQVLGH UDGLXV LV »LQFK OHVV )RU D ODUJH SDWFK WKHGLPHQVLRQVZRXOGEHLQFUHDVHGWR»LQFKHDFK If the curvature of the skin surface is greater than a ULVH RI »LQFK LQ LQFKHV WKH GRXEOHU VKRXOG EH preformed to the curvature using hot water or steam. As an alternative, the doubler may be laminated from WZRSLHFHVRI»LQFKSO\ZRRG 5. Cut the doubler through one side so that it can be inserted through the hole to the back of the skin. Place the patch plug centered on the doubler and mark around its perimeter. Apply a coat of glue outside the line to the outer half of the doubler surface that will bear against the inner surface of the skin. 6. Install the doubler by slipping it through the cutout 6-20 C B B Front Spar C Trimmed Opening A Minimum Radius 5T A Ribs B B Damage A B A B Saddle Gusset A C A Rear Spar C 30T T 12T Patch Plywood skin T 3T (¼" Minimum) Rib cap 8T (1" minimum) Plywood saddle gusset Minimum thickness = T Nailed and glued in place Section A-A 12T T T Patch 12T T 4T T Patch Spar Rib cap Unsupported lap Section B-B Section C-C Figure 6-30. Surfaces patches. 6-21 Grain direction of skin, patch, and doubler Saw cut in doubler Butt joint of patch to skin Inner edge of doubler A B C Outer edge of doubler Nail holes Screw holes—to be filled before finishing Butt joint of patch to skin Plug patch ¼" Plywood skin Saw cut in doubler Plywood doubler (Laminate doubler from two pieces of 1 8" ply in areas of skin curvature.) DIMENSIONS A Small circular plug patch Large circular plug patch 2 ∕" » 58 B 2" C 1 ³∕8" » (Two rows of screws and nails are required for a large patch.) Figure 6-31. Round plug patch assembly. 6-22 hole and place it so that the mark is concentric with the hole. Nail it in place with nailing strips, while holding a bucking bar or similar object under the doubler for backup. Place waxed paper between the nailing strips and the skin. Cloth webbing under the nailing strips facilitates removal of the strips and nails after the glue dries. Scarf Patch 7. After the glue has set for the installed doubler, and you have removed the nail strips, apply glue to the inner half of the doubler and to the patch plug. Drill holes around the plug’s circumference to accept No. 4 round head wood screws. Insert the plug with the grain aligned to the surface wood. 8. Apply the pressure to the patch by means of the wood screws. No other pressure is necessary. Much of the outside surface of a plywood aircraft is curved. If the damaged plywood skin has a radius of curvature not greater than 100 times the skin thickness, you can install a scarf patch. However, it may be necessary to soak or steam the patch, to preform it prior to gluing it in place. Shape backing blocks or other reinforcements to fit the skin curvature. 9. After the glue has set, remove the screws and fill the nail and screw holes. Sand and finish to match the original surface. The steps for making an oval plug patch are identical to those for making the round patch. The maximum dimensions for large oval patches are 7-inches long and 5-inches wide. Oval patches must be cut, so when installed, the face grain matches the direction of the original surface. [Figure 6-32] A properly prepared and installed scarf patch is the best repair for damaged plywood and is preferred for most skin repairs. The scarf patch has edges beveled at a 12:1 slope; the splayed patch is beveled at a 5:1 slope. The scarf patch also uses reinforcements under the patch at the glue joints. You can make scarf cuts in plywood with various tools, such as a hand plane, spoke shave, a sharp scraper, or sanding block. Sawn or roughly filed surfaces are not recommended because they are normally inaccurate and do not form the best glue joint. The Back of the Skin is Accessible for Repair When the back of a damaged plywood skin is accessible, such as a fuselage skin, repair it with scarf patches cut and Outer edge of doubler Butt joint of patch to skin Inner edge of doubler C Nail holes A E D Screw holes—to be filled before finishing B 1" 1" PATCH DIMENSIONS A F Butt joint of patch to skin Plug patch (grain parallel to skin) Small Large 1½" 2" B 2 x8" 3 x8" C D E F 1½" 78 " 3" 4½" 2 ½" 1x8" 5" 7" (Two rows of screws and nails required for large patch.) Plywood doubler (grain parallel to skin) Plywood skin Figure 6-32. An oval plug patch. 6-23 installed with the grain parallel to the surface skin. Details for this type of repair are shown in Figure 6-33. Figure 6-33, Section A-A, shows methods of support for a scarf between frame members using permanent backing and gussets. When the damage follows or extends to a framing member, support the scarf as shown in section B-B. When the scarf does not quite extend to a frame member, support the patch as shown in section C-C. Damage that does not exceed 25 times the skin thickness (31»8-inches for 1»8-inch thick skin) after being trimmed to a circular shape can be repaired as shown in section D-D, provided the trimmed opening is not nearer than 15 times the skin thickness to a frame member (17»8-inches for 1»8-inch thick skin). A temporary backing block is carefully shaped from solid wood and fitted to the inside surface of the skin. A piece of waxed paper or plastic wrap is placed between the block and the underside of the skin. The scarf patch is installed and temporarily attached to the backing block, being held together in place with nailing strips. When the glue sets, remove the nails and block, leaving a flush surface on both sides of the repaired skin. The Back of the Skin Is Not Accessible for Repair To repair a section of the skin with a scarf patch when access to the back side is not possible, use the following steps to facilitate a repair, as shown in Figure 6-34. Cut out and remove the damaged section. Carefully mark and cut the scarf around the perimeter of the hole. Working through the cutout, install backing strips along all edges that are not fully backed by a rib or spar. To prevent warping of the skin, fabricate backing strips from soft-textured plywood, such as yellow poplar or spruce, rather than a piece of solid wood. Use nailing strips to hold backing strips in place while the glue sets. Use a bucking bar, where necessary, to provide support for nailing. A saddle gusset of plywood should support the end of the backing strip at all junctions between the backing strips and ribs or spars. If needed, nail and bond the new gusset plate to the rib or spar. It may be necessary to remove and replace an old gusset plate with a new saddle gusset, or nail a new gusset over the original. Unlike some of the other type patches that are glued and installed as one process, this repair must wait for the glue to set on the backing strips and gussets. At that point, the scarf patch can be cut and fit to match the grain, and glued, using weight for pressure on the patch as appropriate. When dry, fill and finish the repair to match the original surface. 6-24 B C C B C C A A Saddle Gusset Nailing strips D B D B Maximum diameter 25T C Minimum thickness T bonded in place C Temporary backing 30T 12T Patch T Backing T 8T 3T (¼" minimum) Plywood saddle gusset minimum thickness “T” bonded in place Section A - A 12T T Patch Patch 12T Framing member 3T 3T Backing Clamp and bond backing to frame and skin Section B - B Waxed paper or plastic wrap T Backing Nailing a g strips st ps 12T T Clamp and bond backing to frame and skin Section C - C Temporary backing block-shape to fit skin Section D - D 3T Figure 6-33. Scarf patches, back of skin accessible. 6-25 B B C C Front spar B C C B A A Ribs B B A A B A B Saddle gusset A C Rear spar C 30T 12T T 3T (¼" minimum) 8T (1" minimum) Section A - A T Plywood skin Rib cap 12T Plywood skin Patch Rib cap Plywood saddle gusset nail and glue in place (minimum thickness T ) 12T Patch Spar 3T (¼" minimum) Plywood or spruce Section S i B - B T Plywood skin Section C - C Figure 6-34. Scarf patches, back of skin not accessible. 6-26