Aircraft Wood & Structural Repair PDF
Document Details
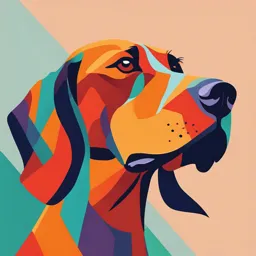
Uploaded by DaringDream
Tags
Summary
This document provides a detailed overview of aircraft wood and structural repair, including historical context, construction details, maintenance procedures, and inspection techniques. It covers various types of wood, repairs, and adhesives involved in the process.
Full Transcript
Chapter 6 Aircraft Wood & Structural Repair Introduction Wood was among the first materials used to construct aircraft. Most of the airplanes built during World War I (WWI) were constructed of wood frames with fabric coverings. Wood was the material of choice for aircraft construction into the 1930s...
Chapter 6 Aircraft Wood & Structural Repair Introduction Wood was among the first materials used to construct aircraft. Most of the airplanes built during World War I (WWI) were constructed of wood frames with fabric coverings. Wood was the material of choice for aircraft construction into the 1930s. Part of the reason was the slow development of strong, lightweight metal aircraft structures and the lack of suitable corrosion-resistant materials for all-metal aircraft. the primary structural material still exist and are operating, including certificated aircraft that were constructed during the 1930s and later. With the proper maintenance and repair procedures, these older aircraft can be maintained in an airworthy condition and kept operational for many years. Wood Aircraft Construction & Repairs In the late 1930s, the British airplane company DeHavilland designed and developed a bomber named the Mosquito. Well into the late 1940s, DeHavilland produced more than 7,700 airplanes made of spruce, birch plywood, and balsa wood. [Figure 6-1] During the early part of WWII, the U.S. government put out a contract to build three flying boats. Hughes Aircraft ultimately won the contract with the mandate to use only materials not critical to the war, such as aluminum and steel. Hughes designed the aircraft to be constructed out of wood. The information presented in this chapter is general in nature and should not be regarded as a substitute for specific instructions contained in the aircraft manufacturer’s maintenance and repair manuals. Methods of construction vary greatly with different types of aircraft, as do the various repair and maintenance procedures required to keep them airworthy. When specific manufacturer’s manuals and instructions are After many delays and loss of government funding, Howard Hughes continued construction, using his own money and completing one aircraft. On November 2, 1947, during taxi tests in the harbor at Long Beach, California, Hughes piloted the Spruce Goose for over a mile at an altitude of 70 feet, proving it could fly. This was the largest seaplane and the largest wooden aircraft ever constructed. Its empty weight was 300,000 pounds with a maximum takeoff weight of 400,000 pounds. The entire airframe, surface structures, and flaps were composed of laminated wood with fabric covered primary control surfaces. It was powered by eight Pratt & Whitney R-4360 radial engines, each producing 3,000 horsepower. [Figure 6-2] Figure 6-1. British DeHavilland Mosquito bomber. As aircraft design and manufacturing evolved, the development of lightweight metals and the demand for increased production moved the industry away from aircraft constructed entirely of wood. Some general aviation aircraft were produced with wood spars and wings, but today only a limited number of wood aircraft are produced. Most of those are built by their owners for education or recreation and not for production. Quite a number of airplanes in which wood was used as Figure 6-2. Hughes Flying Boat, H-4 Hercules named the Spruce Goose. 6-1 not available, the Federal Aviation Administration (FAA) Advisory Circular (AC) 43.13-1, Acceptable Methods, Techniques, and Practices—Aircraft Inspection and Repair, can be used as reference for inspections and repairs. The AC details in the first paragraph, Purpose, the criteria necessary for its use. In part, it stipulates that the use of the AC is acceptable to the FAA for the inspection and minor repair of nonpressurized areas of civil aircraft. It also specifies that the repairs identified in the AC may also be used as a basis for FAA approval of major repairs when listed in block 8 of FAA Form 337, Major Repair and Alteration, when: 1. The user has determined that it is appropriate to the product being repaired; 2. It is directly applicable to the repair being made; and 3. It is not contrary to manufacturer’s data. Certificated mechanics that have the experience of working on wooden aircraft are becoming rare. Title 14 of the Code of Federal Regulations (14 CFR) part 65 states in part that a certificated mechanic may not perform any work for which they are rated unless they have performed the work concerned at an earlier date. This means that if an individual does not have the previous aviation woodworking experience performing the repair on an aircraft, regulation requires a certificated and appropriately rated mechanic or repairman who has had previous experience in the operation concerned to supervise that person. The ability to inspect wood structures and recognize defects (dry rot, compression failures, etc.) can be learned through experience and instruction from knowledgeable certificated mechanics and appropriately qualified technical instructors. Inspection of Wood Structures To properly inspect an aircraft constructed or comprised of wood components, the aircraft must be dry. It should be placed in a dry, well-ventilated hangar with all inspection covers, access panels, and removable fairings opened and removed. This allows interior sections and compartments to thoroughly dry. Wet, or even damp, wood causes swelling and makes it difficult to make a proper determination of the condition of the glue joints. If there is any doubt that the wood is dry, a moisture meter should be utilized to verify the percentage of moisture in the structure. Nondestructive meters are available that check moisture without making holes in the surface. The ideal range is 8–12 percent, with any reading over 20 percent providing an environment for the growth of fungus in the wood. External & Internal Inspection The inspection should begin with an examination of the external surface of the aircraft. This provides a general assessment of the overall condition of the wood and structure. The wings, fuselage, and empennage should be inspected for undulation, warping, or any other disparity from the original shape. Where the wings, fuselage, or empennage structure and skins form stressed structures, no departure from the original contour or shape is permissible. [Figure 6-3] Where light structures using single plywood covering are concerned, some slight sectional undulation or bulging between panels may be permissible if the wood and glue are sound. However, where such conditions exist, a careful check must be made of the attachment of the plywood to its supporting structure. A typical example of a distorted single plywood structure is illustrated in Figure 6-4. The contours and alignment of leading and trailing edges are of particular importance. A careful check should be made for any deviation from the original shape. Any distortion of these light plywood and spruce structures is indicative of deterioration, and a detailed internal inspection has to be made for security of these parts to the main wing structure. If deterioration is found in these components, the main wing structure may also be affected. Splits in the fabric covering on plywood surfaces must be investigated to ascertain whether the plywood skin beneath Ply skins Figure 6-3. Cross sectional view of a stressed skin structure. 6-2 Ply skins Figure 6-4. A distorted single plywood structure. is serviceable. In all cases, remove the fabric and inspect the plywood, since it is common for a split in the plywood skin to initiate a similar defect in the protective fabric covering. Although a preliminary inspection of the external structure can be useful in assessing the general condition of the aircraft, note that wood and glue deterioration can often take place inside a structure without any external indications. Where moisture can enter a structure, it seeks the lowest point, where it stagnates and promotes rapid deterioration. A musty or moldy odor apparent as you remove the access panels during the initial inspection is a good indication of moisture, fungal growth, and possible decay. Glue failure and wood deterioration are often closely related, and the inspection of glued joints must include an examination of the adjacent wood structure. Note: Water need not be present for glue deterioration to take place. The inspection of a complete aircraft for glue or wood deterioration requires scrutiny of parts of the structure that may be known, or suspected, trouble spots. In many instances, these areas are boxed in or otherwise inaccessible. Considerable dismantling may be required. It may be necessary to cut access holes in some of the structures to facilitate the inspection. Do such work only in accordance with approved drawings or instructions in the maintenance manual for the aircraft concerned. If drawings and manuals are not available, engineering review may be required before cutting access holes. Glued Joint Inspection The inspection of glued joints in wooden aircraft structures presents considerable difficulties. Even where access to the joint exists, it is still difficult to positively assess the integrity of the joint. Keep this in mind when inspecting any glue joint. Some common factors in premature glue deterioration include: Chemical reactions of the glue caused by aging or moisture, extreme temperatures, or a combination of these factors. Mechanical forces caused mainly by wood shrinkage. Development of fungal growths. An aircraft painted in darker colors experiences higher skin temperatures and heat buildup within its structure. Perform a more detailed inspection on a wooden aircraft structure immediately beneath the upper surfaces for signs of deteriorating adhesives. Aircraft that are exposed to large cyclic changes of temperature and humidity are especially prone to wood shrinkage that may lead to glue joint deterioration. The amount of movement of a wooden member due to these changes varies with the size of each member, the rate of growth of the tree from which it was cut, and the way the wood was converted in relation to the grain. This means that two major structural members joined to each other by glue are not likely to have identical characteristics. Over a period of time, differential loads are transmitted across the glue joint because the two members do not react identically. This imposes stresses in the glue joint that can normally be accommodated when the aircraft is new and for some years afterwards. However, glue tends to deteriorate with age, and stresses at the glued joints may cause failure of the joints. This is a fact even when the aircraft is maintained under ideal conditions. The various cuts of lumber from a tree have tendency to shrink and warp in the direction(s) indicated in the yellow area around each cut in Figure 6-5. When checking a glue line (the edge of the glued joint) for condition, all protective coatings of paint should be removed by careful scraping. It is important to ensure that the wood is not damaged during the scraping operation. Scraping should 6-3 but use the thinnest feeler gauge whenever possible. The illustration indicates the points a feeler gauge should probe. [Figure 6-6] Plain sawed (tangential cut) Pressure exerted on a joint either by the surrounding structure or by metal attachment devices, such as bolts or screws, can cause a false appearance of the glue condition. The joint must be relieved of this pressure before the glue line inspection is performed. A glued joint may fail in service as a result of an accident or because of excessive mechanical loads having been imposed upon it. Glued joints are generally designed to take shear loads. If a joint is expected to take tension loads, it is secured by a number of bolts or screws in the area of tension loading. In all cases of glued joint failure, whatever the direction of loading, there should be a fine layer of wood fibers adhering to the glue. The presence of fibers usually indicates that the joint itself is not at fault. Quarter sawed (radial cut) Figure 6-5. Effects of shrinkage on the various shapes during drying from the green condition. cease immediately when the wood is revealed in its natural state and the glue line is clearly discernible. At this point in the inspection, it is important that the surrounding wood is dry; otherwise, you will get a false indication of the integrity of the glue line due to swelling of the wood and subsequent closing of the joint. Inspect the glue line using a magnifying glass. Where the glue line tends to part, or where the presence of glue cannot be detected or is suspect, probe the glue line with a thin feeler gauge. If any penetration is observed, the joint is defective. The structure usually dictates the feeler gauge thickness, Metal fitting Bolt Examination of the glue under magnification that does not reveal any wood fibers, but shows an imprint of the wood grain, indicates that the cause of the failure was the predrying of the glue before applying pressure during the manufacture of the joint. If the glue exhibits an irregular appearance with star-shaped patterns, this is an indication that precuring of the glue occurred before pressure was applied, or that pressure had been incorrectly applied or maintained on the joint. If there is no evidence of wood fiber adhesion, there may also be glue deterioration. Wood Condition Wood decay and dry rot are usually easy to detect. Decay Shrinkage Laminated spar Ply spar web A A A A A At all points marked A , check for glue condition and separation with a feeler gauge. Shrinkage Inspection hole in web Figure 6-6. Inspection points for laminated glue joints. 6-4 may be evident as either a discoloration or a softening of the wood. Dry rot is a term loosely applied to many types of decay, but especially to a condition that, in an advanced stage, permits the wood to be crushed to a dry powder. The term is actually a misnomer for any decay, since all fungi require considerable moisture for growth. Dark discolorations of the wood or gray stains running along the grain are indicative of water penetration. If such discoloration cannot be removed by light scraping, replace the part. Disregard local staining of the wood by dye from a synthetic adhesive hardener. In some instances where water penetration is suspected, a few screws removed from the area in question reveal, by their degree of corrosion, the condition of the surrounding joint. [Figure 6-7] Another method of detecting water penetration is to remove the bolts holding the fittings at spar root-end joints, aileron hinge brackets, etc. Corrosion on the surface of such bolts and wood discoloration provide a useful indication of water penetration. Plain brass screws are normally used for reinforcing glued wooden members. For hardwoods, such as mahogany or ash, steel screws may be used. Unless specified by the aircraft manufacturer, replace removed screws with new screws of identical length, but one gauge larger in diameter. Inspection experience with a particular type of aircraft provides insight to the specific areas most prone to water penetration and moisture entrapment. Wooden aircraft are more prone to the damaging effects of water, especially without the protection of covered storage. Control system openings, fastener holes, cracks or breaks in the finish, and the interfaces of metal fittings and the wood structure are points that require additional attention during an inspection. Additionally, windshield and window frames, the area under the bottom of entrance and cargo doors, and the lower sections of the wing and fuselage are locations that require detailed inspections for water damage and corrosion on all aircraft. The condition of the fabric covering on plywood surfaces provides an indication of the condition of the wood underneath. If there is any evidence of poor adhesion, cracks in the fabric, or swelling of the wood, remove the fabric to allow further inspection. The exposed surface shows water penetration by the existence of dark gray streaks along the grain and dark discoloration at ply joints or screw holes. Cracks in wood spars are often hidden under metal fittings or metal rib flanges and leading edge skins. Any time a Fuselage inner and outer ply skins Reinforced laminated fuselage member Position to check for separation Screw hole e Wood screw Bulkhead frame member Bulkhead ply web Corrosion indicating failure of bulkhead glued joint to fuselage side Expansion gap (not to be confused with joint separation) Figure 6-7. Checking a glued joint for water penetration. 6-5 reinforcement plate exists that is not feathered out on its ends, a stress riser exists at the ends of the plate. A failure of the primary structure can be expected at this point. [Figure 6-8] Compression failure As part of the inspection, examine the structure for other defects of a mechanical nature, including any location where bolts secure fittings that take load-carrying members, or where the bolts are subject to landing or shear loads. Remove the bolts and examine the holes for elongation or surface crushing of the wood fibers. It is important to ensure the bolts are a good fit in the holes. Check for evidence of bruises or crushing of the structural member, which can be caused by overtorquing of the bolts. Check all metal fittings that are attached to a wood structure for looseness, corrosion, cracks, or bending. Areas of particular concern are strut attach fittings, spar butt fittings, aileron and flap hinges, jury strut fittings, compression struts, control cable pulley brackets, and landing gear fittings. All exposed end grain wood, particularly the spar butts, should be inspected for cracking or checking. Inspect structural members for compression failures, which is indicated by rupture across the wood fibers. This is a serious defect that can be difficult to detect. If a compression failure is suspected, a flashlight beam shown along the member and running parallel to the grain, will assist in revealing it. The surface will appear to have minute ridges or lines running across the grain. Particular attention is necessary when inspecting any wooden member that has been subjected to abnormal bending or compression loads during a hard landing. If undetected, compression failures of the spar may result in structural failure of the wing during flight. [Figure 6-9] When a member has been subjected to an excessive bending load, the failure appears on the surface that has been compressed. The surface subject to tension normally shows Figure 6-9. Pronounced compression failure in wood beam. no defects. In the case of a member taking an excessive direct compression load, the failure is apparent on all surfaces. The front and rear spars should be checked for longitudinal cracks at the ends of the plywood reinforcement plates where the lift struts attach. [Figure 6-8] Check the ribs on either side of the strut attach points for cracks where the cap strips pass over and under the spars, and for missing or loose rib-to-spar attach nails. All spars, those in the wing(s) and empennage, should be inspected on the face and top surface for compression cracks. A borescope can be utilized by accessing existing inspection holes. Various mechanical methods can be employed to enhance the visual inspection of wood structures. Tapping the subject area with a light plastic hammer or screwdriver handle should produce a sharp solid sound. If the suspected area sounds hollow and dull, further inspection is warranted. Use a sharp metal awl or thin-bladed screwdriver to probe the area. The wood structure should be solid and firm. If the area is soft and mushy, the wood is rotted and disassembly and repair of the structure is necessary. Repair of Wood Aircraft Structures Compression failure Crack Decay Rib attach nail holes Elongated bolt hole Plywood plates Strut attach point The standard for any repair is that it should return the aircraft or component to its original condition in strength, function, and aerodynamic shape. It should also be accomplished in accordance with the manufacturer’s specifications and/or instructions, or other approved data. The purpose of repairing all wood structural components is to obtain a structure as strong as the original. Major damage probably requires replacement of the entire damaged assembly, but minor damage can be repaired by removing or cutting away the damaged members and replacing them with new sections. This replacement may be accomplished by gluing, glue and nails, or glue and screw-reinforced splicing. Figure 6-8. Areas likely to incur structural damage. 6-6 Materials Several forms of wood are commonly used in aircraft. Solid wood or the adjective “solid” used with such nouns as “beam” or “spar” refers to a member consisting of one piece of wood. Laminated wood is an assembly of two or more layers of wood that have been glued together with the grain of all layers or laminations approximately parallel. Plywood is an assembled product of wood and glue that is usually made of an odd number of thin plies, or veneers, with the grain of each layer placed 90° with the adjacent ply or plies. or construct an aircraft. The type, location, and amount or size of the defects grade the wood for possible use. All woods used for structural repair of aircraft are classified as softwood. Softwood is typically used for construction and is graded based on strength, load carrying ability, and safety. Hardwoods, on the other hand, are typically appearance woods and are graded based on the number and size of clear cuttings from the tree. Defects Permitted The following defects are permitted in the wood species used for aircraft repair that are identified in Figure 6-10: 1. Cross grain—Spiral grain, diagonal grain, or a combination of the two is acceptable if the grain does not diverge from the longitudinal axis of the material more than specified in Figure 6-10 column 3. A check of all four faces of the board is necessary to determine the amount of divergence. The direction of free-flowing ink frequently assists in determining grain direction. 2. Wavy, curly, and interlocked grain—Acceptable, if local irregularities do not exceed limitations specified for spiral and diagonal grain. 3. Hard knots—Sound, hard knots up to 3»8-inch in diameter are acceptable if: (1) they are not projecting portions of I-beams, along the edges of rectangular or beveled unrouted beams, or along the edges of flanges of box beams (except in portions of low stress); (2) they do not cause grain divergence at the edges of the board or in the flanges of a beam more than specified in Figure 6-10 column 3; and (3) they are in the center third of the beam and not closer than 20-inches to another knot or other defect (pertains to 3»8-inch knots; smaller knots may be proportionately closer). Knots greater than ¼-inch must be used with caution. 4. Pin knot clusters—Small clusters are acceptable if they produce only a small effect on grain direction. 5. Pitch pockets—Acceptable in center portion of a beam if they are at least 14-inches apart when they lie in the same growth ring and do not exceed 1½-inches in length by 1»8-inch width by 1»8-inch depth, and if they are not along the projecting portions of I-beams, along the edges of rectangular or beveled unrouted beams, or along the edges of the flanges of box beams. 6. Mineral streaks—Acceptable if careful inspection fails to reveal any decay. High-density material includes compreg, impreg, or similar commercially made products, heat-stabilized wood, or any of the hardwood plywoods commonly used as bearing or reinforcement plates. Suitable Wood The various species of wood listed in Figure 6-10 are acceptable for structural purposes when used for the repair of aircraft. Spruce is the preferred choice and the standard by which the other wood is measured. Figure 6-10 provides a comparison of other wood that may be suitable for aircraft repair. It lists the strength and characteristics of the wood in comparison to spruce. The one item common to all the species is that the slope of the grain cannot be steeper than 1:15. All solid wood and plywood used for the construction and repair of aircraft should be of the highest quality and grade. For certificated aircraft, the wood should have traceability to a source that can provide certification to a military specification (MIL-SPEC). The term “aircraft quality” or “aircraft grade” is referred to and specified in some repair documents, but that grade wood cannot be purchased from a local lumber company. To purchase the material, contact one of the specialty aircraft supply companies and request a certification document with the order. The MIL-SPEC for solid spruce is MIL-S-6073 and for plywood it is MIL-P-6070B. When possible, fabricated wood components should be purchased from the aircraft manufacturer, or someone who may have a Parts Manufacturer Approval (PMA) to produce replacement parts for the aircraft. With either of these sources supplying the wood components, the mechanic can be assured of installing approved material. At the completion of the repair, as always, it is the responsibility of the person returning the aircraft to service to determine the quality of the replacement wood and the airworthiness of the subsequent repair. To help determine the suitability of the wood, inspect it for defects that would make it unsuitable material to repair Defects Not Permitted The following defects are not permitted in wood used for aircraft repair. If a defect is listed as unacceptable, please refer to the previous section, Defects Permitted, for acceptable conditions. 6-7 Species of Wood Strength Properties (as compared to spruce) Maximum Permissible Grain Deviation (slope of grain) Remarks 1 2 3 4 Spruce (Picea) 100% 1.15 Excellent for all uses. Considered standard for this table. Exceeds spruce 1.15 May be used as substitute for spruce in same sizes or in Sitka (P. sitchensis) Red (P. rubra) White (P. glauca) Douglas fir (Pseudotsuga taxifolia) slightly reduced sizes if reductions are substantiated. Difficult to work with hand tools. Some tendency to split and splinter during fabrication and much greater care in manufacture is necessary. Large solid pieces should be avoided due to inspection difficulties. Satisfactory for gluing. Noble fir Slightly exceeds spruce (Abies procera, also except 8% deficient in and splitting. May be used as direct substitute for spruce in known as Abies nobilis) shear same sizes if shear does not become critical. Hardness Satisfactory characteristics of workability, warping, 1.15 somewhat less than spruce. Satisfactory for gluing. Western hemlock Slightly exceeds spruce Less uniform in texture than spruce. May be used as direct 1.15 (Tsuga heterophylla) substitute for spruce. Upland growth superior to lowland growth. Satisfactory for gluing. Excellent working qualities and uniform in properties, but Northern white pine, also Properties between known as Eastern white 85% and 96% those somewhat low in hardness and shock-resistance. pine (Pinus strobus) of spruce Cannot be used as substitute for spruce without increase in 1.15 sizes to compensate for lesser strength. Satisfactory for gluing. Exceeds spruce May be used as substitute for spruce in same sizes or in 1.15 Port Orford white cedar slightly reduced sizes if reductions are substantiated. (Chamaecyparis Easy to work with hand tools. Gluing is difficult, but satisfactory lawsoniana) joints can be obtained if suitable precautions are taken. Slightly less than spruce Excellent working qualities. Should not be used as a direct 1.15 Yellow poplar except in compression substitute for spruce without carefully accounting for slightly (Liriodendron (crushing) and shear reduced strength properties. Somewhat low in shock-resistance. Satisfactory for gluing. tulipifera) Figure 6-10. Selection and properties of wood for aircraft repairs. 1. Cross grain—unacceptable. 2. Wavy, curly, and interlocked grain – unacceptable. 3. Hard knots—unacceptable. 4. Pin knot clusters—unacceptable, if they produce large effect on grain direction. 5. Spike knots—knots running completely through the depth of a beam perpendicular to the annual rings and appear most frequently in quarter-sawed lumber. Reject wood containing this defect. 6. Pitch pockets—unacceptable. 7. Mineral streaks—unacceptable, if accompanied by decay. 8. Checks, shakes, and splits—checks are longitudinal cracks extending, in general, across the annual rings. Shakes are longitudinal cracks usually between two annual rings. Splits are longitudinal cracks caused by artificially induced stress. Reject wood containing these defects. 9. Compression—very detrimental to strength and is difficult to recognize readily, compression wood is characterized by high specific gravity, has the appearance of an excessive growth of summer wood, and in most species shows little contrast in color between spring wood and summer wood. If in doubt, reject the material or subject samples to toughness machine test to establish the quality of the wood. 6-8 Reject all material containing compression wood. structures are satisfactory, provided they are found to be compatible with existing structural materials in the aircraft and fabrication methods to be used in the repair. 10. Compression failures—caused from overstress in compression due to natural forces during the growth of the tree, felling trees on rough or irregular ground, or rough handling of logs or lumber. Compression failures are characterized by a buckling of the fibers that appears as streaks substantially at right angles to the grain on the surface of the piece, and vary from pronounced failures to very fine hairlines that require close inspection to detect. Reject wood containing obvious failures. If in doubt, reject the wood or make a further inspection in the form of microscopic examination or toughness test, the latter being more reliable. New adhesives have been developed in recent years, and some of the older ones are still in use. Some of the more common adhesives that have been used in aircraft construction and repair include casein glue, plastic resin glue, resorcinol glue, and epoxy adhesives. 11. Tension—forming on the upper side of branches and leaning trunks of softwood trees, tension wood is caused by the natural overstressing of trying to pull the branches and leaning trunk upright. It is typically harder, denser, and may be darker in color than normal wood, and is a serious defect, having higher than usual longitudinal shrinkage that may break down due to uneven shrinkage. When in doubt, reject the wood. Note: Some modern adhesives are incompatible with casein adhesive. If a joint that has previously been bonded with casein is to be reglued using another type adhesive, all traces of the casein must be scraped off before a new adhesive is applied. If any casein adhesive is left, residual alkalinity may cause the new adhesive to fail to cure properly. 12. Decay—rot, dote, red heart, purple heart, etc., must not appear on any piece. Examine all stains and discoloration carefully to determine whether or not they are harmless or in a stage of preliminary or advanced decay. Glues (Adhesives) Because adhesives play a critical role in the bonding of aircraft structure, the mechanic must employ only those types of adhesives that meet all of the performance requirements necessary for use in certificated aircraft. The product must be used strictly in accordance with the aircraft and adhesive manufacturer’s instructions. All instructions must be followed exactly, including the mixing ratios, the ambient and surface temperatures, the open and closed assembly times, the gap-filling ability, or glue line thickness, the spread of the adhesive, whether one or two surfaces, and the amount of clamping pressure and time required for full cure of the adhesive. AC 43.13-1 provides information on the criteria for identifying adhesives that are acceptable to the FAA. It stipulates the following: 1. Refer to the aircraft maintenance or repair manual for specific instructions on acceptable adhesive selection for use on that type aircraft. 2. Adhesives meeting the requirements of a MILSPEC, Aerospace Material Specification (AMS), or Technical Standard Order (TSO) for wooden aircraft Casein glue should be considered obsolete for all aircraft repairs. The adhesive deteriorates when exposed to moisture and temperature variations that are part of the normal operating environment of any aircraft. Plastic resin glue, also known as a urea-formaldehyde adhesive, came on the market in the middle to late 1930s. Tests and practical applications have shown that exposure to moist conditions, and particularly to a warm humid environment, under swell-shrink stress, leads to deterioration and eventual failure of the bond. For these reasons, plastic resin glue should be considered obsolete for all aircraft repairs. Discuss any proposed use of this type adhesive on aircraft with FAA engineering prior to use. Resorcinol glue, or resorcinol-formaldehyde glue, is a two-component synthetic adhesive consisting of resin and a catalyst. It was first introduced in 1943 and almost immediately found wide application in the wood boat-building and wood aircraft industry in which the combination of high durability and moderate-temperature curing was extremely important. It has better wet-weather and ultraviolet (UV) resistance than other adhesives. This glue meets all strength and durability requirements if the fit of the joint and proper clamping pressure results in a very thin and uniform bond line. The manufacturer’s product data sheets must be followed regarding mixing, usable temperature range, and the open and close assembly times. It is very important that this type of glue is used at the recommended temperatures because the full strength of the joint cannot be relied on if assembly and curing temperatures are below 70 °F. With that in mind, higher temperatures shorten the working life because of a faster cure rate, and open and closed assembly times must be shortened. 6-9 Epoxy adhesive is a two-part synthetic resin product that depends less on joint quality and clamping pressure. However, many epoxies have not exhibited joint durability in the presence of moisture and elevated temperatures and are not recommended for structural aircraft bonding unless they meet the acceptable standards set forth by the FAA in AC 43.13-1, as referenced earlier in this chapter. Definition of Terms Used in the Glue Process Close contact adhesive—a non-gap-filling adhesive (e.g., resorcinol-formaldehyde glue) suitable for use only in those joints where the surfaces to be joined can be brought into close contact by means of adequate pressure, to allow a glue line of no more than 0.005inch gap. Gap-filling adhesive—an adhesive suitable for use in those joints in which the surfaces to be joined may not be close or in continuous contact (e.g., epoxy adhesives) due either to the impracticability of applying adequate pressure or to the slight inaccuracies of fabricating the joint. Glue line—resultant layer of adhesive joining any two adjacent wood layers in the assembly. Single spread—spread of adhesive to one surface only. Double spread—spread of adhesive to both surfaces and equally divided between the two surfaces to be joined. Open assembly time—period of time between the application of the adhesive and the assembly of the joint components. Closed assembly time—time elapsing between the assembly of the joints and the application of pressure. Pressing or clamping time—time during which the components are pressed tightly together under recommended pressure until the adhesive cures (may vary from 10 to 150 pounds per square inch (psi) for softwoods, depending on the viscosity of the glue). Caul—a clamping device, usually two rigid wooden bars, to keep an assembly of flat panel boards aligned during glue-up. It is assembled with long bolts and placed on either side of the boards, one on top and another below, and parallel with the pipe/bar clamps. A caul is usually finished and waxed before each use to keep glue from adhering to it. Adhesive pot life—time elapsed from the mixing of the adhesive components until the mixture must be discarded, because it no longer performs to its specifications. The manufacturer’s product data sheet may define this as working time or useful life; once expired, the adhesive must not be used. It lists the specific temperature and quantity at which the sample amount can be worked. Pot life is a product of time and temperature. The cooler the mix is kept, within the recommended temperature range, the longer it is usable. Preparation of Wood for Gluing Satisfactory glue joints in aircraft should develop the full strength of the wood under all conditions of stress. To produce this result, the conditions involved in the gluing operation must be carefully controlled to obtain a continuous, thin, uniform film of solid glue in the joint with adequate adhesion to both surfaces of the wood. The following conditions are required: 1. Proper and equal moisture content of wood to be joined (8 to 12 percent). 2. Properly prepared wood surfaces that are machined or planed, and not sanded or sawed. 3. Selection of the proper adhesive for the intended task, which is properly prepared and of good quality. 4. The application of good gluing techniques, including fitment, recommended assembly times, and adequate equal pressure applied to the joint. 5. Performing the gluing operation under the recommended temperature conditions. The surfaces to be joined must be clean, dry, and free from grease, oil, wax, paint, etc. Keep large prepared surfaces covered with a plastic sheet or masking paper prior to the bonding operation. It is advisable to clean all surfaces with a vacuum cleaner just prior to adhesive application. Smooth even surfaces produced on planers and joiners with sharp knives and correct feed adjustments are the best surfaces for gluing solid wood. The use of sawn surfaces for gluing has been discouraged for aircraft component assembly because of the difficulty in producing a surface free of crushed fibers. Glue joints made on surfaces that are covered with crushed fibers do not develop the normal full strength of the wood. Some of the surface changes in plywood, such as glazing and bleed-through, that occur in manufacture and may interfere with the adhesion of glue in secondary gluing are easily recognized. A light sanding of the surface with 220-grit sandpaper in the direction of the grain restores the surface fibers to their original condition, removes the gloss, and improves the adhesion of the glue. In contrast to these recognized surface conditions, wax deposits from cauls used during hot pressing produce unfavorable gluing surfaces that are not easily detected. 6-10 Gap Wetting tests are a useful means of detecting the presence of wax. A finely sprayed mist or drops of water on the surface of wax-coated plywood bead and do not wet the wood. This test may also give an indication of the presence of other materials or conditions that would degrade a glue joint. Only a proper evaluation of the adhesion properties, using gluing tests, determines the gluing characteristics of the plywood surfaces. Pressure block Preparing Glues for Use The manufacturer’s directions should be followed for the preparation of any glue or adhesive. Unless otherwise specified by the glue manufacturer, clear, cool water should be used with glues that require mixing with water. The recommended proportions of glue, catalyst, and water or other solvent should be determined by the weight of each component. Mixing can be either by hand or machine. Whatever method is used, the glue should be thoroughly mixed and free of air bubbles, foam, and lumps of insoluble material. Applying the Glue/Adhesive To make a satisfactorily bonded joint, it is generally desirable to apply adhesive to both surfaces and join in a thin even layer. The adhesive can be applied with a brush, glue spreader, or a grooved rubber roller. Follow the adhesive manufacturer’s application instructions for satisfactory results. Be careful to ensure the surfaces make good contact and the joint is positioned correctly before applying the adhesive. Keep the open assembly time as short as possible and do not exceed the recommended times indicated in the product data sheet. Pressure on the Joint To ensure the maximum strength of the bonded surfaces, apply even force to the joint. Non-uniform gluing pressure commonly results in weak areas and strong areas in the same joint. The results of applied pressure are illustrated in Figure 6-11. Use pressure to squeeze the glue out into a thin continuous film between the wood layers, to force air from the joint, to bring the wood surfaces into intimate contact with the glue, and to hold them in this position during the setting of the glue. Pressure may be applied by means of clamps, elastic straps, weight, vacuum bags, or other mechanical devices. Other methods used to apply pressure to joints in aircraft gluing operations range from the use of brads, nails, and screws to the use of electric and hydraulic power presses. The amount of pressure required to produce strong joints in aircraft assembly operations may vary from 10 to 150 psi for softwoods and as high as 200 psi for hardwoods. Insufficient Pressure block Arrows indicate pressure Figure 6-11. Even distribution of gluing pressure creates a strong, gap-free joint. pressure to poorly machined or fitted wood joints usually results in a thick glue line, indicating a weak joint, and should be carefully avoided. High clamping pressure is neither essential nor desirable, provided good contact between the surfaces being joined is obtained. When pressure is applied, a small quantity of glue should be squeezed from the joint. This excess should be removed before it sets. It is important that full pressure be maintained on the joint for the entire cure time of the adhesive because the adhesive does not chemically relink and bond if it is disturbed before it is fully cured. The full curing time of the adhesive is dependent on the ambient temperature; therefore, it is very important to follow the manufacturer’s product data sheets for all phases of the gluing operation from the shelf life to the moisture content of the wood to the proper mixing of the adhesive to the application, and especially to the temperature. The successful assembly and fabrication depends on the workmanship and quality of the joints and following the glue manufacturer’s instructions. All gluing operations should be performed above 70 °F for proper performance of the adhesive. Higher temperatures shorten the assembly times, as does coating the pieces of wood with glue and exposing openly to the air. This open assembly promotes a more rapid thickening of the glue than pieces being mated together as soon as the spreading of the glue is completed. Figure 6-12 provides an example of resorcinol resin glue and the allowable assembly times and gluing pressure when in the open and closed assembly condition. All examples are for an ambient temperature of 75 °F. 6-11 Glue Gluing Pressure Type of Assembly Maximum Assembly Time Resorcinol resins 100–250 psi 100–250 psi Less than 100 psi Less than 100 psi Closed Open Closed Open Up to 50 minutes Up to 12 minutes Up to 40 minutes Up to 10 minutes Figure 6-12. Examples of differences for open and closed assembly times. Figure 6-13 provides examples of strong and weak glue joints resulting from different gluing conditions. A is a well-glued joint with a high percentage of wood failure made under proper conditions; B is a glue-starved joint resulting from the application of excessive pressure with thin glues; C is a dried glue joint resulting from an excessively long assembly time and/or insufficient pressure. Testing Glued Joints Satisfactory glue joints in aircraft should develop the full strength of the wood under all conditions of stress. Tests should be made by the mechanic prior to gluing a joint of a major repair, such as a wing spar. Whenever possible, perform tests using pieces cut from the actual wood used for the repair under the same mechanical and environmental conditions A B C that the repair will undergo. Perform a sample test using two pieces of scrap wood from the intended repair, each cut approximately 1" × 2" × 4". The pieces should be joined by overlapping each approximately 2 inches. The type of glue, pressure, and curing time should be the same as used for the actual repair. After full cure, place the test sample in a bench vise and break the joint by exerting pressure on the overlapping member. The fractured glue faces should show a high percentage of at least 75 percent of the wood fibers evenly distributed over the fractured glue surface. [Figure 6-14] Repair of Wood Aircraft Components Wing Rib Repairs Ribs that have sustained damage may be repaired or replaced, depending upon the type of damage and location in the aircraft. If new parts are available from the aircraft manufacturer or the holder of a PMA for the part, it is advisable to replace the part rather than to repair it. If you make a repair to a rib, do the work in such a manner and using materials of such quality that the completed repair is at least equal to the original part in aerodynamic function, structural strength, deterioration, and other qualities affecting airworthiness, such as fit and finish. When manufacturer’s repair manuals or instructions are not available, acceptable methods of repairing damaged ribs are described in AC 43.13-1 under Wood Structure Repairs. When necessary, a rib can be fabricated and installed using the same materials and dimensions from a manufacturerapproved drawing or by reference to an original rib. However, if you fabricated it from an existing rib, you must provide evidence to verify that the dimensions are accurate and the materials are correct for the replacement part. You can repair a cap strip of a wood rib using a scarf splice. The repair is reinforced on the side opposite the wing covering by a spruce block that extends beyond the scarf joint not less than three times the thickness of the strips being repaired. Reinforce the entire splice, including the spruce reinforcing block, on each side with a plywood side plate. Figure 6-13. Strong and weak glue joints. 6-12