Bulk Materials Handling Equipment PDF
Document Details
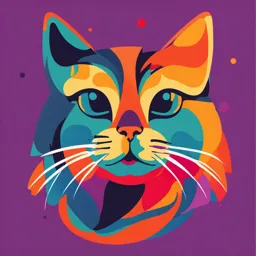
Uploaded by TolerableNobelium9949
Tags
Summary
This document provides an overview of bulk materials handling, focusing on the characteristics of bulk materials and related equipment. It covers types, theories, and principles of bulk material handling systems.
Full Transcript
1 BULK MATERIALS WEEK 10 - Activity No. 8 I. EXPECTED COMPETENCIES The students will be able to: 1. Identify and describe the characteristics of bulk materials according to its classifications. 2. D...
1 BULK MATERIALS WEEK 10 - Activity No. 8 I. EXPECTED COMPETENCIES The students will be able to: 1. Identify and describe the characteristics of bulk materials according to its classifications. 2. Determine the type of equipment in handling bulk materials. II. THEORIES / PRINCIPLES Bulk material handling is an engineering field that is centered on the design of equipment used for the handling of dry materials such as ores, coal, cereals, wood chips, sand, gravel and stone in loose bulk form. It can also relate to the handling of mixed wastes. Bulk material handling systems are typically composed of stationary machinery such as conveyor belts, screw conveyors, stackers, reclaimers, bucket elevators, truck dumpers, railcar dumpers or wagon tipplers, shiploaders, hoppers and diverters and various mobile equipment such as loaders, various shuttles, combined with storage facilities such as stockyards, storage silos or stockpiles. Advanced bulk material handling systems feature integrated bulk storage, conveying, and discharge. CHARACTERISTICS OF BULK MATERIALS The inherent qualities of bulk materials differ so radically from those of solids that a new group of terms is required to describe them. Based on their many years of experience in making practically every type of bulk-handling conveyor, Link-Belt Company has evolved a classification, in the company’s words, to facilitate consideration of all factors which affect their (bulk materials) handling by conveyors. As a matter of fact, the system of classification is so comprehensive that it is not restricted to the characteristics of these products for handling by conveyors, but can be utilized to study these products in all types of handling. CLASSIFICATIONS TABULATED The key to this table, based on sized, flowability, abrasiveness, and other characteristics is as shown in table 8.01 This module is a property of Technological University of the Philippines Visayas and intended for EDUCATIONAL PURPOSES ONLY and is NOT FOR SALE NOR FOR REPRODUCTION. 2 In this key, the term mesh refers in the opening per linear inch of screen through which the material will flow. Thus, 100 mesh is a screen with 100 openings per inch. The angle of repose is the maximum slope, expressed in degrees, at which piled material will stand without sliding. Table 8.01 - Key to Bulk Materials Classes Haynes, D, Oliphant (1962), Materials Handling Applications, page 196 HANDLING BULK MATERIALS AND SCRAP The handling of bulk materials presents two rather distinctive problems: 1. Those concerned with moving these products intermittently in separate lots and 2. The movement of materials in a more or less continuous flow. BULK MATERIALS HANDLED IN LOTS Although a wide variety of machines are utilized to transport, elevate convey and transfer bulk materials in small lot quantities, their applications do not present any very serious technical problems. The primary points to be considered in selecting such equipment are volumetric and weight capacities, construction to meet the physical requirements of the products handled (temperature, abrasiveness, corrosiveness, etc.) and for dumping machines, the angle of declination of the discharging surface to assure product clearance. Transporting devices run the range from wheelbarrows to railroad car dumpers and rolling stock for industrial railroads are available in a wide variety of types and capacities. Machines for moving batches of materials about a plant This module is a property of Technological University of the Philippines Visayas and intended for EDUCATIONAL PURPOSES ONLY and is NOT FOR SALE NOR FOR REPRODUCTION. 3 or a yard are offered to meet any given conditions as to quantities, distances etc. Among these are trailers for use in tractor trains Activities in connection with earth moving are specialized and so is the equipment used for this purpose. Examples of hauling vehicles and scoops are shown in Fig. 8.01. Fig. 8.01 - Haulers and mobile machines Haynes, D, Oliphant (1962), Materials Handling Applications, page 202 Among the devices which can be employed to elevate bulk materials are cranes and derricks (Fig. 8.02) and many types of stackers equipped with special dumping bottles and contraptions for holding drums and barrels to permit their being rotated and emptied into bins, hoppers, furnaces , etc. Skids and pallets made with superstructures such as dumping hoppers, can be moved about and elevated by high lift platform and fork trucks. In addition, scoops, shovels and dumping bins are available as special attachments for fork trucks (Fig. 8.02). This module is a property of Technological University of the Philippines Visayas and intended for EDUCATIONAL PURPOSES ONLY and is NOT FOR SALE NOR FOR REPRODUCTION. 4 Fig. 8.02 - Some lifting devices and fork truck attachments. Haynes, D, Oliphant (1962), Materials Handling Applications, page 203 Transferring equipment such as monorails and overhead-travelling cranes (Fig. 8.03), when equipped with buckets and other devices for building and moving materials that are free-flowing or sluggish, are utilized in many industries- foundries, bakeries, steel mills and many more. Aerial tramways can be included in this group because they are used to move such products as coal, gravel, sand ores, crushed rock, cement, mine waste, sawdust and others when fitted with the right kind of carrier for the product or products handled. This module is a property of Technological University of the Philippines Visayas and intended for EDUCATIONAL PURPOSES ONLY and is NOT FOR SALE NOR FOR REPRODUCTION. 5 Fig. 8.03 - Monorails, overhead travelling cranes and aerial tramways handle bulk materials. Haynes, D, Oliphant (1962), Materials Handling Applications, page 204 This module is a property of Technological University of the Philippines Visayas and intended for EDUCATIONAL PURPOSES ONLY and is NOT FOR SALE NOR FOR REPRODUCTION. 6 Fig. 8.04 - Power cranes and shovels and attachments Haynes, D, Oliphant (1962), Materials Handling Applications, page 205 III. TOOLS, EQUIPMENT & MATERIALS 1. Drawing Tools 1.1 pen or pencil 1.2 triangles (30°x60° and 45°x45°) 2. Drawing Plate (8”x13” bond paper with plate borders) 3. Photograph/Images of machines and devices applicable in handling bulk materials. IV. TASKS (STEPS) & KEY POINTS 1. Make a neat drawing and describe one equipment used in handling a bulk materials according to any of its functions as transporting, elevating, conveying or self-loading equipment. 2. Use a separate sheets of long white bond paper (with plate borders 1 cm.) preferably in a portrait orientation. V. TEST REVIEW EXERCISES Choose the correct answer that corresponds to each question, write the letter on the blank provided. This module is a property of Technological University of the Philippines Visayas and intended for EDUCATIONAL PURPOSES ONLY and is NOT FOR SALE NOR FOR REPRODUCTION. 7 1. ____Which of the following refers in the opening per linear inch of screen through which the material will flow? a) Mesh b) Hole c) Square d) None of the above 2. ____Bulk material handling equipment is used to which of the following material? a) Ores b) Wood chips c) Mixed waste d) All of the above 3. ____Which device cannot be employed to elevate bulk materials? a) Crane b) Derrick c) Fork truck d) None of the above 4. ____Which of the following is not a transferring equipment? a) Aerial tramways b) Monorails c) Side dumper d) Overhead-travelling crane 5. ____Which of the following is not a hauling vehicle? a) Wagon type equipment b) Pick-up body type c) Dump truck d) None of the above 6. ____Which machinery is not used in bulk material handling systems? a) Stackers b) Loaders c) Stock piles d) None of the above 7. ____ Aerial tramways can be used to move on which products? a) Crushed rock b) Cement c) Gravel d) All of the above This module is a property of Technological University of the Philippines Visayas and intended for EDUCATIONAL PURPOSES ONLY and is NOT FOR SALE NOR FOR REPRODUCTION. 8 VI. PRODUCTIVITY TEST SHEET/RUBRICS SUBJECT MODULE ACTIVITY / PROJECT: ACTIVITY CODE: TITLE BULK MATERIALS AND HANDLING NO. 8 MT 311 EQUIPMENT IDENTIFICATION MECHANICAL NAME OF STUDENT: HANDLING SYSTEM DIRECTION: This form should afford the Instructor to rate the Productivity/Performance of the student/s for a given Employable Skill/Activity/Project. On the space provided for, write the points which likely coincide with your evaluation for each of the following factors: OUTSTANDING – (9-10); PLUS SATISFACTORY (7-8); SATISFACTORY (5-6); BELOW SATISFACTORY (3-4 / NEED TO REPEAT) SATISFACTORY TASK PERFORMANCE REQUIREMENT Provided with detailed drawing and instructions, available tools and materials, the student should be able to: 1. Identify and describe the different kinds of bulk materials that must be handled. 2. Describe various equipment applicable in handling bulk materials. 3. Finish the task assignment within the deadline set by the instructor. FACTORS RATING A. QUALITY / APPEARANCE (Symmetry, Verticality, Horizontality; Workmanship, Finish) B. ACCURACY/CRITICALITY (Exactness of Dimension/Specification, High, Medium, Low Criticality) FINAL GRADE REMARKS: ________________________________________________________________________ ________________________________________________________________________ ________________________________________________________________________ ________________________________________________________________________ ________________________________________________________________________ ________________________________________________________________________ Assessed by: ______________________________ Instructor This module is a property of Technological University of the Philippines Visayas and intended for EDUCATIONAL PURPOSES ONLY and is NOT FOR SALE NOR FOR REPRODUCTION. 9 ADAPTING TO THE WORK AREA (REMOTE LOCATIONS) WEEK 11 - Activity No. 9 I. EXPECTED COMPETENCIES The students will be able to: 1. Identify and describe the features of distant work locations. 2. Describe the types of handling equipment that can be utilized under remote locations. 3. Discuss the activities in mining, quarrying and construction works. II. THEORIES / PRINCIPLES REMOTE LOCATIONS Somewhat isolated work areas are, in most instances, associated with particular kinds of industrial activities. To mention mining, logging, farming brings to mind the characteristics of the locations where such operations are carried on. In describing the handling equipment best suited for such places, we must, of necessity, use as examples the machines adopted by industries to function well under the conditions imposed by these characteristic locales. THREE CATEGORIES From the standpoint of the broad types of handling equipment which can be utilized, remote locations can be divided into three general categories. 1. First are those placed where the terrain is such that overhead handling equipment and conveyors are the most practical machines for moving materials from one point to another. 2. Next are the situations where it is feasible to lay rails- places like mines where the conditions are not right for trucks on wheels or crawlers. 3. And finally, of course, there are the locations where trucks can operate. The wide-open spaces have extremely diversified terrain characteristics (Fig. 9.01). Materials have to be moved a few hundred feet or over several miles. The ground may be relatively level, hilly, or perhaps mountainous. The landscape may be dotted with fields, woods or marshes or it may present a barren appearance. Sluggish streams may wind their way between gently sloping banks or raging torrents may rush through steep gorges. The climatic conditions may vary from desert dryness to equatorial humidity. Rain, sleet or snow may fall. This module is a property of Technological University of the Philippines Visayas and intended for EDUCATIONAL PURPOSES ONLY and is NOT FOR SALE NOR FOR REPRODUCTION. 10 Moving materials over such country is determined largely by the economics of the situation. Laying rails, especially for temporary operations, tunnelling through mountains and spanning streams requires more investment than equipment that does not ride on rails. It is often impractical or too costly to build highways because of the grades encountered. Fig. 9.01 - Movement but no wheeled vehicles Haynes, D, Oliphant (1962), Materials Handling Applications, page 240 MINING, QUARRYING AND CONSTRUCTIONSWORK The outstanding activities with which we have to deal here are mining, quarrying and construction work. In the first two cases, it is a matter moving materials after they have been extracted from the earth. Construction work includes road building, the erection of dam and similar operations. In erecting dams, tramways and other types of overhead equipment are used to carry materials such as prepared concrete, tools and even personnel in the job location. Narrow gage railroads operate well over relatively level terrain and are employed where conditions are such that roads for wheeled or crawler mounted vehicles are not practical, because the going would be too tough or the work is of a temporary nature. The entrances to mines, the country at and around quarries and logging camps are examples of locations where railroads of this type are used successfully This module is a property of Technological University of the Philippines Visayas and intended for EDUCATIONAL PURPOSES ONLY and is NOT FOR SALE NOR FOR REPRODUCTION. 11 Fig. 9.02 – Some pit mining equipment Haynes, D, Oliphant (1962), Materials Handling Applications, page 241 Where the operation is sufficiently close to a commercial rail line with standard gage rails, it is frequently feasible to run a spur to the work area. The same rolling stock can then be used on both lines. Strip mines, quarries and logging camps are typical of the kinds of places where rugged cranes and other equipment on wheels and crawlers are used extensively. The various front and attachments- shovels, hoes, draglines, cranes, etc. have been developed to meet operating conditions of this character. In addition to the extractive industries and forestry activities, many farms and orchards are so situated and sufficiently extensive to take advantage of modern methods in moving their produce. Fig. 9.01 serves to show how some of them are applied to moving products over open country. They also illustrate how such machines as aerial tramways and conveyors can operate over terrain where it would be impractical to use rail or automotive equipment. This module is a property of Technological University of the Philippines Visayas and intended for EDUCATIONAL PURPOSES ONLY and is NOT FOR SALE NOR FOR REPRODUCTION. 12 Work below ground in pit mining is typical of conditions where industrial railroads are standard equipment (Fig. 9.02). Mine locomotives have been developed into specialized types such as those for handling metal ores and those for coal. Depending on conditions, there are battery, trolley, diesel electric and diesel-hydraulic locomotives, to mention some of the sources of power available. However, we must not overlook the fact that other means are used to move materials from mines. Conveyors are found underground and of course, in the vicinity of the mines proper where the products are processed, bulk- handling equipment of many types is utilized. In surface or strip mining operations such as a quarrying, the work is done where tractor-mounted machines find their logical locale (Fig. 9.03). Fig. 9.03 – Cranes and shovels in quarrying Haynes, D, Oliphant (1962), Materials Handling Applications, page 242 Cranes and shovels are actively engaged in such operations, but again, we must not forget that other types of bulk-handling machines are used for carrying the products to processing plants such as cement mills. Many ingenious machines have been evolved for handling logs in forest and over rough country (Fig. 9.04). Special attention is called to the mountings- crawler treads for heavy, rough work; wheels where the going is easier. As the logs make their way to lumber mills via truck, rail, water, or other media, they are processed or fabricated by another group of highly specialized machines (Fig. 9.05). Both logging and milling have brought their operations to a high degree of mechanization. This module is a property of Technological University of the Philippines Visayas and intended for EDUCATIONAL PURPOSES ONLY and is NOT FOR SALE NOR FOR REPRODUCTION. 13 Fig. 9.04 – Special handling equipment for logging camps Haynes, D, Oliphant (1962), Materials Handling Applications, page 244 This module is a property of Technological University of the Philippines Visayas and intended for EDUCATIONAL PURPOSES ONLY and is NOT FOR SALE NOR FOR REPRODUCTION. 14 Fig. 9.05 – These are some handling machines used in lumber mills Haynes, D, Oliphant (1962), Materials Handling Applications, page 245 III. TOOLS, EQUIPMENT & MATERIALS 1. Drawing Tools 1.1 pen or pencil 1.2 triangles (30°x60° and 45°x45°) 2. Drawing Plate (8”x13” bond paper with plate borders) 3. Photograph/images of functional handling equipment IV. TASKS (STEPS) & KEY POINTS 1. Applying the knowledge learned from the Materials Handling System, develop a personal design of an equipment or improvement to an existing equipment applicable in handling any materials of your choice. 2. Make a neat and simple sketch of your design, label the parts with approximate dimensions if possible and describe the equipment according to its functions as transporting, elevating, conveying or self-loading equipment. 3. Use a separate sheets of long white bond paper (with plate borders 1 cm.) preferably in a portrait orientation. V. TEST REVIEW EXERCISES QUESTIONS TO ANSWER. 1. What are the three categories of remote locations? Describe the characteristics of each location and the handling equipment best suited for such places. 2. Discuss briefly about the activities in mining, quarrying and construction works This module is a property of Technological University of the Philippines Visayas and intended for EDUCATIONAL PURPOSES ONLY and is NOT FOR SALE NOR FOR REPRODUCTION. 15 VI. PRODUCTIVITY TEST SHEET/RUBRICS SUBJECT MODULE ACTIVITY / PROJECT: ACTIVITY CODE: TITLE REMOTE LOCATIONS AND NO. 9 MT 311 HANDLING EQUIPMENT MECHANICAL NAME OF STUDENT: HANDLING SYSTEM DIRECTION: This form should afford the Instructor to rate the Productivity/Performance of the student/s for a given Employable Skill/Activity/Project. On the space provided for, write the points which likely coincide with your evaluation for each of the following factors: OUTSTANDING – (9-10); PLUS SATISFACTORY (7-8); SATISFACTORY (5-6); BELOW SATISFACTORY (3-4 / NEED TO REPEAT) SATISFACTORY TASK PERFORMANCE REQUIREMENT Provided with detailed drawing and instructions, available tools, machines and materials, the student should be able to: 1. Identify and describe the characteristics of a remote work locations 2. Describe various equipment best suited for such places. 3. Finish the task assignment within the deadline set by the instructor. FACTORS RATING A. QUALITY / APPEARANCE (Symmetry, Verticality, Horizontality; Workmanship, Finish) B. ACCURACY/CRITICALITY (Exactness of Dimension/Specification, High, Medium, Low Criticality) FINAL GRADE REMARKS: ________________________________________________________________________ ________________________________________________________________________ ________________________________________________________________________ ________________________________________________________________________ ________________________________________________________________________ ________________________________________________________________________ Assessed by: ______________________________ Instructor This module is a property of Technological University of the Philippines Visayas and intended for EDUCATIONAL PURPOSES ONLY and is NOT FOR SALE NOR FOR REPRODUCTION. 16 ADAPTING TO THE WORK AREA 2 (YARDS AND PLATFORMS) WEEK 12 - Activity No. 10 I. EXPECTED COMPETENCIES The students will be able to: 1. Identify and describe the features of open work areas referred to as yards. 2. Describe the features of platforms as work areas. 3. Identify and describe the types of handling equipment that can be utilized in the open work areas. II. THEORIES / PRINCIPLES YARDS AND YARD EQUIPMENT The open areas referred to as yards are the scene of many handling activities- storage of various materials, loading and unloading cars and the flow of traffic from one plant to another (Fig.10.01). Bulk materials, lumber, lengths of pipe, reinforcing bars, rolls of wire fencing, structural shapes and other articles, not damaged by exposure, are stored in these locations. Retailers in such industries as coal and lumber operate yards and these are located frequently near a railroad or a marine terminal. RUNNING SURFACES Yards where mobile equipment is operated normally have surfaces suited to vehicular travel. Even so, there is considerable difference in the tractive effort required to move equipment over different running surfaces. Table 10.01 gives the resistance in pounds per ton of gross weight of machine plus load and is given to show the resistances comparatively. Grades encountered must also be taken into account. On upgrades, the resistance is increased by 20 lb. per ton of gross weight for each one percent of grade. On downgrades, the grade resistance is subtracted from the tractive resistance. The figures given here must, of course, be increased if the surface of the roadway is in poor condition. This module is a property of Technological University of the Philippines Visayas and intended for EDUCATIONAL PURPOSES ONLY and is NOT FOR SALE NOR FOR REPRODUCTION. 17 Table 10.01 - Tractive Resistances Haynes, D, Oliphant (1962), Materials Handling Applications, page 249 Large cracks, holes, irregular rail crossings and similar faults should be corrected, not only to reduce power requirements but also to prevent jolts from damaging machines and loads. No such problems are involved where overhead-traveling cranes are installed (Fig. 10.01, center) and such machines frequently serve double duty. However, mobile equipment provides considerably more flexibility in yard operation. Industrial railroads are utilized in some plant yards to move items between buildings and to dispose of refuse. This module is a property of Technological University of the Philippines Visayas and intended for EDUCATIONAL PURPOSES ONLY and is NOT FOR SALE NOR FOR REPRODUCTION. 18 Fig. 10.01 – Yards present many diverse problems Haynes, D, Oliphant (1962), Materials Handling Applications, page 248 On marine wharves, they carry freight between ships and distant storage areas. Trackless trains (Fig. 10.02), because they do not have to follow a fixed path, are more satisfactory for some operations as when the train is made up at separated points or cars are to be dropped off at different spots. Switching is avoided and the tracks are not blocked while the train is being assembled, broken up or just waiting. Mobiles cranes can be mounted on crawlers where yard conditions are not favourable to tire-mounted equipment. Scoop trucks are effective means of loading or moving bulk materials. High-lift fork trucks have introduced new techniques for handling pipe lengths, lumber and similar long articles. Frequently they are teamed up with an end-loader (Fig. 10.01) which does the handling, while the fork truck tier. Side-loaders (Fig. 10.02) tier loads within This module is a property of Technological University of the Philippines Visayas and intended for EDUCATIONAL PURPOSES ONLY and is NOT FOR SALE NOR FOR REPRODUCTION. 19 the reach of their forks or auxiliary cranes. Also they can place long articles on racks, two load lengths in depth by working from two aisles. Fig. 10.02 – Miscellaneous handling jobs in yards Haynes, D, Oliphant (1962), Materials Handling Applications, page 251 PLATFORMS AS WORK AREAS Known variously as shipping platforms, loading docks, receiving areas, and other combinations of these terms, these are the prescribed locations where goods are received or dispatched from plants and warehouses. As a group, they lack common characteristics. Some are low, wooden affairs, rising scarcely above ground level, others are well constructed for handling purposes, some have their front edges at the building line so that the active area is within the building proper, finally there may be no structure at all, or at best a portable platform, as in some western states where the main floor of the plant may be at ground level (Fig.10.03) This module is a property of Technological University of the Philippines Visayas and intended for EDUCATIONAL PURPOSES ONLY and is NOT FOR SALE NOR FOR REPRODUCTION. 20 Many platforms of old buildings are totally inadequate for present day handling equipment and methods. This is scarcely to be wondered at because architects of a few years ago could not foresee the radical changes which have taken place in the last quarter century. SELECTING A PLATFORM The first consideration is the type of carrier to be served. Most plants and warehouses receive and ship by rail, truck or both. Platforms at rail side run parallel with the tracks, while most truck platforms are so arranged that the vehicles back in. Exceptionally, trucks may be loaded and unloaded through side doors. Certain dimensions of rail height platforms are extremely important in their effects on handling (Fig.10.04). The height of edge of the platform above the top of the rails is one such. It should be correlated with the type of car or cars to be served. Unfortunately, no fixed standard exists for the height of a car’s floor above track level. Box, automobile, flat and gondola cars vary in this regard from 43 in. to 47 in. The racks on the floors of refrigerator cars may be as high as 66 in. above the track. A height of 47 ½ in. as recommended by the railroads is not mandatory and can be varied to meet particular requirements. This module is a property of Technological University of the Philippines Visayas and intended for EDUCATIONAL PURPOSES ONLY and is NOT FOR SALE NOR FOR REPRODUCTION. 21 Fig. 10.03 – Many platforms present tough handling problems. Haynes, D, Oliphant (1962), Materials Handling Applications, page 252 Where a compromise must be made, the best arrangement is to have the dock level lower than the floors of the cars to be served. This permits dock boards to slant up into, rather than down into, the car. This saves space within the car, where every square inch counts for the maneuvering of equipment. A second critical dimension is the distance between the center line of the track and the edge of the platform because it determines the amount of open space or gap between the side of the car and the platform. Cars vary in width from 123 to 125 in. The center line dimension recommended by the railroads is 68 in., and this results in the gap at the platform’s edge of between 5 ½ or 6 ½ in. A greater gap occur between refrigerated cars and the platforms because usually the floor racks are set inboard so that the insulated doors can be closed properly, which means that a longer dock board is required to bridge the gap with these cars than with box and other types. WORKING WIDTH The clear working width of the platform, by which is meant the width exclusive of losses due to fixture such as pipes, checker’s booths, etc., has become increasingly important with changes in car loading and unloading equipment. Where necessary, provision must be made for two-way traffic, space taken over by dock boards, possible storage of pallets, etc. Safest procedure is to make a large-scaled drawing of the old or proposed platform and with templates of machines and accessories, test out various widths until the best one for the given situation is found. This module is a property of Technological University of the Philippines Visayas and intended for EDUCATIONAL PURPOSES ONLY and is NOT FOR SALE NOR FOR REPRODUCTION. 22 TRUCK DOCKS In general, the same broad principles apply to the design and the construction of truck docks (Fig. 10.4) as for rail facilities. Again, the problem is complicated by lack of standards for height of trucks above road level. Where trucks of differing bed heights are handled, the practice is to make the platform, if it has an adjustable dock board, 52 in. high- 48 in. without such a device. Truck beds are lower when the vehicle is loaded than when it is empty, but these differences can be compensated for by means of chocks or hydraulic tilts if the situation is too serious (Fig.10.5). Fig. 10.04 – Critical dimensions to check for railroad and truck platforms Haynes, D, Oliphant (1962), Materials Handling Applications, page 254 With the increase in trucking activities, many cities are ruling that truck bays must be within the building line to avoid interference with passing traffic. In Fig. 10.03 are indicated minimum dimensions for such constructions, based on current state limitations as to width and height of vehicles. This module is a property of Technological University of the Philippines Visayas and intended for EDUCATIONAL PURPOSES ONLY and is NOT FOR SALE NOR FOR REPRODUCTION. 23 Fig. 10.05 – How docks can be improved and some operations from the ground. Haynes, D, Oliphant (1962), Materials Handling Applications, page 255 III. TOOLS, EQUIPMENT & MATERIALS 1. Lay-out Tools 1.1 pen or pencil 1.2 Ruler 2. Drawing of equipment design as model. 3. Indigenous materials available such as: 3.1 stiff paper or plastic 3.2 cardboards 3.3 match sticks 3.4 broom sticks 3.5 coconut leaves 3.6 bamboo 3.7 sugar cane stalks (bilaho), etc. 4. Paste Materials and tools 4.1 Glue gun and stick 4.2 Adhesive tape 4.3 Tie wire 4.4 stapler 4.5 Elmer’s glue, etc. 5. Cutters This module is a property of Technological University of the Philippines Visayas and intended for EDUCATIONAL PURPOSES ONLY and is NOT FOR SALE NOR FOR REPRODUCTION. 24 VII. TASKS (STEPS) & KEY POINTS 1. Build a miniature model of the handling equipment you designed from the previous week using the indigenous materials available in your place. Size is approximately 12”x12” 2. Describe the functions of this handling equipment. 3. Take a picture of the finished miniature equipment model and send it to your instructor for evaluation. VIII. TEST REVIEW EXERCISES TRUE OR FALSE. Write T if the statement is true and F if the statement is false. ______ 1. Scoop trucks are effective means of loading or moving bulk materials. ______ 2. A greater gap occur between refrigerated cars and the platforms. ______ 3. Bulk materials are stored in the open areas referred to as yards. ______ 4. The clear working width of the platform is meant the width inclusive of losses due to fixture such as pipes, checker’s booths, etc. ______ 5. The first consideration is the type of carrier to be served in selecting a platform. ______ 6. Industrial railroads are utilized in some plant yards to move items between buildings and to dispose of refuse. ______ 7. Yards where mobile equipment is operated normally have surfaces not suited to vehicular travel. ______ 8. With the increase in trucking activities, many cities are ruling that truck bays must be within the building line. ______ 9. Platforms are the prescribed locations where goods are received or dispatched from plants and warehouses. ______ 10. The distance between the center line of the track and the edge of the platform determines the amount of open space or gap between the side of the car and the platform. This module is a property of Technological University of the Philippines Visayas and intended for EDUCATIONAL PURPOSES ONLY and is NOT FOR SALE NOR FOR REPRODUCTION. 25 IX. PRODUCTIVITY TEST SHEET/RUBRICS SUBJECT MODULE ACTIVITY / PROJECT: ACTIVITY CODE: TITLE YARDS AND PLATFORMS, NO. 10 MT 311 HANDLING EQUIPMENT MECHANICAL NAME OF STUDENT: HANDLING SYSTEM DIRECTION: This form should afford the Instructor to rate the Productivity/Performance of the student/s for a given Employable Skill/Activity/Project. On the space provided for, write the points which likely coincide with your evaluation for each of the following factors: OUTSTANDING – (9-10); PLUS SATISFACTORY (7-8); SATISFACTORY (5- 6); BELOW SATISFACTORY (3-4 / NEED TO REPEAT) SATISFACTORY TASK PERFORMANCE REQUIREMENT Provided with detailed drawing and instructions, available tools and materials, the student should be able to: 1. Identify and describe the features of open work areas referred to as yards. 2. Describe the features of platforms as work areas. 3. Identify and describe the types of handling equipment that can be utilized in the open work areas. 4. Finish the task assignment within the deadline set by the instructor. FACTORS RATING A. QUALITY / APPEARANCE (Symmetry, Verticality, Horizontality; Workmanship, Finish) B. ACCURACY/CRITICALITY (Exactness of Dimension/Specification, High, Medium, Low Criticality) FINAL GRADE REMARKS: _______________________________________________________________ _______________________________________________________________ _______________________________________________________________ _______________________________________________________________ _______________________________________________________________ _______________________________________________________________ ______________________________________________________ Assessed by: ______________________________ Instructor This module is a property of Technological University of the Philippines Visayas and intended for EDUCATIONAL PURPOSES ONLY and is NOT FOR SALE NOR FOR REPRODUCTION. 26 SAFETY IN MATERIALS HANDLING WEEK 13 - Activity No. 11 I. EXPECTED COMPETENCIES The students will be able to: 1. Describe the safety rules and regulations in materials handling and storing. 2. Apply basic safety procedures to reduce injuries resulting from handling and storing of materials. 3. Appreciate the importance of safety in materials handling II. THEORIES / PRINCIPLES Each kind of material which is classified as dangerous presents its own peculiar problems and these are concerned primarily with the safety aspect of handling. Handling and storing materials involve diverse operations such as hoisting tons of steel with a crane; driving a truck loaded with concrete blocks; carrying bags or materials manually; and stacking palletized bricks or other materials such as drums, barrels, kegs, and lumber. The efficient handling and storing of materials are vital to industry. In addition to raw materials, these operations provide a continuous flow of parts and assemblies through the workplace and ensure that materials are available when needed. Unfortunately, the improper handling and storing of materials often result in costly injuries. SAFETY RULES AND REGULATIONS 1. What should your employees know before moving, handling, and storing materials? In addition to training and education, applying general safety principles—such as proper work practices, equipment, and controls—can help reduce workplace accidents involving the moving, handling, and storing of materials. Whether moving materials manually or mechanically, your employees should know and understand the potential hazards associated with the task at hand and how to control their workplaces to minimize the danger. Because numerous injuries can result from improperly handling and storing materials, workers should also be aware of accidents that may result from the unsafe or improper handling of equipment as well as from improper work practices. In addition, workers should be able to recognize the methods for eliminating—or at least minimizing—the occurrence of such accidents. This module is a property of Technological University of the Philippines Visayas and intended for EDUCATIONAL PURPOSES ONLY and is NOT FOR SALE NOR FOR REPRODUCTION. 27 Employers and employees should examine their workplaces to detect any unsafe or unhealthful conditions, practices, or equipment and take corrective action. 2. What are the potential hazards for workers? Workers frequently cite the weight and bulkiness of objects that they lift as major contributing factors to their injuries. In 1999, for example, more than 420,000 workplace accidents resulted in back injuries. Bending, followed by twisting and turning, were the more commonly cited movements that caused back injuries. Other hazards include falling objects, improperly stacked materials, and various types of equipment. You should make your employees aware of potential injuries that can occur when manually moving materials, including the following: a. Strains and sprains from lifting loads improperly or from carrying loads that are either too large or too heavy, b. Fractures and bruises caused by being struck by materials or by being caught in pinch points, and c. Cuts and bruises caused by falling materials that have been improperly stored or by incorrectly cutting ties or other securing devices. 3. What precautions should workers take when moving materials manually? When moving materials manually, workers should attach handles or holders to loads. In addition, workers should always wear appropriate personal protective equipment and use proper lifting techniques. To prevent injury from oversize loads, workers should seek help in the following: a. When a load is so bulky that employees cannot properly grasp or lift it, b. When employees cannot see around or over a load, or c. When employees cannot safely handle a load. Using the following personal protective equipment prevents needless injuries when manually moving materials: a. Hand and forearm protection, such as gloves, for loads with sharp or rough edges. b. Eye protection. c. Steel-toed safety shoes or boots. d. Metal, fiber, or plastic metatarsal guards to protect the instep area from impact or compression. Employees should use blocking materials to manage loads safely. Workers should also be cautious when placing blocks under a raised load to ensure that the load is not released before removing their hands from under the load. Blocking materials and timbers should be large and strong enough to support the load safely. In addition to materials with cracks, workers should not use materials with rounded corners, splintered pieces, or dry rot for blocking. This module is a property of Technological University of the Philippines Visayas and intended for EDUCATIONAL PURPOSES ONLY and is NOT FOR SALE NOR FOR REPRODUCTION. 28 4. What precautions should workers take when moving materials mechanically? Using mechanical equipment to move and store materials increases the potential for employee injuries. Workers must be aware of both manual handling safety concerns and safe equipment operating techniques. Employees should avoid overloading equipment when moving materials mechanically by letting the weight, size, and shape of the material being moved dictate the type of equipment used. All materials-handling equipment has rated capacities that determine the maximum weight the equipment can safely handle and the conditions under which it can handle that weight. Employers must ensure that the equipment- rated capacity is displayed on each piece of equipment and is not exceeded except for load testing. Although workers may be knowledgeable about powered equipment, they should take precautions when stacking and storing material. When picking up items with a powered industrial truck, workers must do the following: a. Center the load on the forks as close to the mast as possible to minimize the potential for the truck tipping or the load falling, b. Avoid overloading a lift truck because it impairs control and causes tipping over, c. Do not place extra weight on the rear of a counterbalanced forklift to allow an overload, d. Adjust the load to the lowest position when traveling, e. Follow the truck manufacturer's operational requirements, and f. Pile and cross-tier all stacked loads correctly when possible. 5. What precautions must workers take to avoid storage hazards? Stored materials must not create a hazard for employees. Employers should make workers aware of such factors as the materials' height and weight, how accessible the stored materials are to the user, and the condition of the containers where the materials are being stored when stacking and piling materials. To prevent creating hazards when storing materials, employers must do the following: a. Keep storage areas free from accumulated materials that cause tripping, fires, or explosions, or that may contribute to the harboring of rats and other pests; b. Place stored materials inside buildings that are under construction and at least 6 feet from hoist ways, or inside floor openings and at least 10 feet away from exterior walls; c. Separate non compatible material; and d. Equip employees who work on stored grain in silos, hoppers, or tanks, with lifelines and safety belts. This module is a property of Technological University of the Philippines Visayas and intended for EDUCATIONAL PURPOSES ONLY and is NOT FOR SALE NOR FOR REPRODUCTION. 29 In addition, workers should consider placing bound material on racks, and secure it by stacking, blocking, or interlocking to prevent it from sliding, falling, or collapsing. 6. What safeguards must workers follow when stacking materials? Stacking materials can be dangerous if workers do not follow safety guidelines. Falling materials and collapsing loads can crush or pin workers, causing injuries or death. To help prevent injuries when stacking materials, workers must do the following: a. Stack lumber no more than 16 feet high if it is handled manually, and no more than 20 feet if using a forklift; b. Remove all nails from used lumber before stacking; c. Stack and level lumber on solidly supported bracing; d. Ensure that stacks are stable and self-supporting; e. Do not store pipes and bars in racks that face main aisles to avoid creating a hazard to passersby when removing supplies; f. Stack bags and bundles in interlocking rows to keep them secure; and g. Stack bagged material by stepping back the layers and cross-keying the bags at least every ten layers (to remove bags from the stack, start from the top row first). During materials stacking activities, workers must also do the following: a. Store baled paper and rags inside a building no closer than 18 inches to the walls, partitions, or sprinkler heads; b. Band boxed materials or secure them with cross-ties or shrink plastic fiber; c. Stack drums, barrels, and kegs symmetrically; d. Block the bottom tiers of drums, barrels, and kegs to keep them from rolling if stored on their sides; e. Place planks, sheets of plywood dunnage, or pallets between each tier of drums, barrels, and kegs to make a firm, flat, stacking surface when stacking on end; f. Chock the bottom tier of drums, barrels, and kegs on each side to prevent shifting in either direction when stacking two or more tiers high; and g. Stack and block poles as well as structural steel, bar stock, and other cylindrical materials to prevent spreading or tilting unless they are in racks. In addition, workers should do the following: a. Paint walls or posts with stripes to indicate maximum stacking heights for quick reference; b. Observe height limitations when stacking materials; c. Consider the need for availability of the material; and d. Stack loose bricks no more than 7 feet in height. (When these stacks reach a height of 4 feet, taper them back 2 inches for every foot of height above the 4-foot level. When masonry blocks are stacked higher than 6 This module is a property of Technological University of the Philippines Visayas and intended for EDUCATIONAL PURPOSES ONLY and is NOT FOR SALE NOR FOR REPRODUCTION. 30 feet, taper the stacks back one-half block for each tier above the 6-foot level.) IMPORTANT SAFETY MEASURES To reduce the number of accidents associated with workplace equipment, employers must train employees in the proper use and limitations of the equipment they operate. In addition to powered industrial trucks, this includes knowing how to safely and effectively use equipment such as conveyors, cranes, and slings. 7. What safety measures should employer stake regarding conveyors? When using conveyors, workers may get their hands caught in nip points where the conveyor medium runs near the frame or over support members or rollers. Workers also may be struck by material falling off the conveyor, or they may get caught in the conveyor and drawn into the conveyor path as a result. To prevent or reduce the severity of an injury, employers must take the following precautions to protect workers: a. Install an emergency button or pull cord designed to stop the conveyor at the employee's work station. b. Install emergency stop cables that extend the entire length of continuously accessible conveyor belts so that the cables can be accessed from any location along the conveyor. c. Design the emergency stop switch so that it must be reset before the conveyor can be restarted. d. Ensure that appropriate personnel inspect the conveyor and clear the stoppage before restarting a conveyor that has stopped due to an overload. e. Prohibit employees from riding on a materials-handling conveyor. f. Provide guards where conveyors pass over work areas or aisles to keep employees from being struck by falling material. (If the crossover is low enough for workers to run into it, mark the guard with a warning sign or paint it a bright color to protect employees.) g. Cover screw conveyors completely except at loading and discharging points. (At those points, guards must protect employees against contacting the moving screw. The guards are movable, and they must be interlocked to prevent conveyor movement when the guards are not in place.) 8. What safety measures should employer stake regarding cranes? Employers must permit only thoroughly trained and competent workers to operate cranes. Operators should know what they are lifting and what it weighs. For example, the rated capacity of mobile cranes varies with the length of the boom and the boom radius. When a crane has a telescoping boom, a load may be safe to lift at a short boom length or a short boom radius, but may overload the crane when the boom is extended and the radius increases. This module is a property of Technological University of the Philippines Visayas and intended for EDUCATIONAL PURPOSES ONLY and is NOT FOR SALE NOR FOR REPRODUCTION. 31 To reduce the severity of an injury, employers must take the following precautions: a. Equip all cranes that have adjustable booms with boom angle indicators. b. Provide cranes with telescoping booms with some means to determine boom lengths unless the load rating is independent of the boom length. c. Post load rating charts in the cab of cab-operated cranes. (All cranes do not have uniform capacities for the same boom length and radius in all directions around the chassis of the vehicle.) d. Require workers to always check the crane's load chart to ensure that the crane will not be overloaded by operating conditions. e. Instruct workers to plan lifts before starting them to ensure that they are safe. f. Tell workers to take additional precautions and exercise extra care when operating around power lines. g. Teach workers that outriggers on mobile cranes must rest on firm ground, on timbers, or be sufficiently cribbed to spread the weight of the crane and the load over a large enough area. (Some mobile cranes cannot operate with outriggers in the traveling position.) h. Direct workers to always keep hoisting chains and ropes free of kinks or twists and never wrapped around a load. i. Train workers to attach loads to the load hook by slings, fixtures, and other devices that have the capacity to support the load on the hook. j. Instruct workers to pad sharp edges of loads to prevent cutting slings. k. Teach workers to maintain proper sling angles so that slings are not loaded in excess of their capacity. l. Ensure that all cranes are inspected frequently by persons thoroughly familiar with the crane, the methods of inspecting the crane, and what can make the crane unserviceable. Crane activity, the severity of use, and environmental conditions should determine inspection schedules. m. Ensure that the critical parts of a crane—such as crane operating mechanisms, hooks, air, or hydraulic system components and other load- carrying components—are inspected daily for any maladjustment, deterioration, leakage, deformation, or other damage. 9. What must employers do to ensure the safe use of slings? As an employer, you must designate a competent person to conduct inspections of slings before and during use, especially when service conditions warrant. In addition, you must ensure that workers observe the following precautions when working with slings: a. Remove immediately damaged or defective slings from service. b. Do not shorten slings with knots or bolts or other makeshift devices. c. Do not kink sling legs. d. Do not load slings beyond their rated capacity. e. Keep suspended loads clear of all obstructions. f. Remain clear of loads about to be lifted and suspended. g. Do not engage in shock loading. This module is a property of Technological University of the Philippines Visayas and intended for EDUCATIONAL PURPOSES ONLY and is NOT FOR SALE NOR FOR REPRODUCTION. 32 h. Avoid sudden crane acceleration and deceleration when moving suspended loads. 10. What must employers do to protect workers who operate powered industrial trucks? Workers who handle and store materials often use fork trucks, platform lift trucks, motorized hand trucks, and other specialized industrial trucks powered by electrical motors or internal combustion engines. Employers must make these workers aware of the safety requirements pertaining the design, maintenance, and use of these trucks. 11. What are the safety requirements for design? All new powered industrial trucks, except vehicles intended primarily for earth moving or over-the-road hauling, must meet the design and construction requirements for powered industrial trucks established in the American National Standard for Powered Industrial Trucks, Part II, ANSI B56.1-1969. Trucks approved for fire safety also must bear a label, or some other identifying mark, indicating acceptance by a nationally recognized testing laboratory. 12. What are the safety requirements for modification? You and your employees must not make modifications and additions affecting capacity and safe operation of the trucks without the manufacturer's prior written approval. In these cases, you must change capacity, operation, and maintenance instruction plates and tags or decals to reflect the new information. If the truck is equipped with front-end attachments that are not factory installed, the user must request that the truck be marked to identify these attachments and show the truck's approximate weight— including the installed attachment— when it is at maximum elevation with its load laterally centered. BASIC SAFETY AND HEALTH PRINCIPLES Employers can reduce injuries resulting from handling and storing materials by using some basic safety procedures such as adopting sound ergonomics practices, taking general fire safety precautions, and keeping aisles and passageways clear. What Is Ergonomics? Ergonomics is defined as the study of work and is based on the principle that the job should be adapted to fit the person rather than forcing the person to fit the job. Ergonomics focuses on the work environment, such as its design and function, as well as items—such as the design and function of work stations, controls, displays, safety devices, tools, and lighting to fit the employees' physical requirements and to ensure their health and well being. This module is a property of Technological University of the Philippines Visayas and intended for EDUCATIONAL PURPOSES ONLY and is NOT FOR SALE NOR FOR REPRODUCTION. 33 Ergonomics includes restructuring or changing workplace conditions, to make the job easier, and reducing stressors that cause musculoskeletal disorders. In the area of materials handling and storing, ergonomic principles may require controls such as reducing the size or weight of the objects lifted, installing a mechanical lifting aid, or changing the height of a pallet or shelf. Although no approach completely eliminates back injuries resulting from lifting materials, you can prevent a substantial number of lifting injuries by implementing an effective ergonomics program and by training your employees in appropriate lifting techniques. What About Fire Safety? In adhering to fire safety precautions, instruct employees that flammable and combustible materials must be stored according to their fire characteristics. Flammable liquids, for example, must be separated from other material by a fire wall. Also, other combustibles must be stored in an area where smoking and using an open flame or a spark-producing device is prohibited. Dissimilar materials that are dangerous when they come into contact with each other must be stored apart. What About Aisles and Passage ways? When using aisles and passageways to move materials mechanically, workers must allow sufficient clearance for aisles at loading docks, through doorways, wherever turns must be made, and in other parts of the workplace. Providing sufficient clearance for mechanically-moved materials will prevent workers from being pinned between the equipment and fixtures in the workplace, such as walls, racks, posts, or other machines. Sufficient clearance also will prevent the load from striking an obstruction and falling on an employee. Employers must ensure that all passageways that workers use remain clear of obstructions and tripping hazards. Workers should not store materials in excess of supplies needed for immediate operations in aisles or passageways, and employers must mark permanent aisles and passageways appropriately. SAFETY POSTERS AND SLOGAN It’s a well-known fact – promotion of safety and health clearly demonstrates the commitment of the business owner to establishing an effective safety management system. Much careful thought and consideration should be given to this. Promotional approaches adopted should have clearly defined objectives. The following are some approaches to be tried, based on almost free safety poster and safety awareness poster that does not cost much: This module is a property of Technological University of the Philippines Visayas and intended for EDUCATIONAL PURPOSES ONLY and is NOT FOR SALE NOR FOR REPRODUCTION. 34 Fig. 11.01 – Safety posters and slogan https://safetyrisk.net/safety-awareness-posters-and-graphics/ This module is a property of Technological University of the Philippines Visayas and intended for EDUCATIONAL PURPOSES ONLY and is NOT FOR SALE NOR FOR REPRODUCTION. 35 III. TOOLS, EQUIPMENT & MATERIALS 1. Drawing Tools 1.1 pen or pencil 1.2 triangles (30°x60° and 45°x45°) 2. Drawing Materials (8”x13” bond paper with plate borders) X. TASKS (STEPS) & KEY POINTS 1. Design a safety poster with slogan for sheetmetal workshop use. 2. Draw and describe the safety poster and slogan. 3. Use a separate sheets of long white bond paper (with borders) for your poster. XI. TEST REVIEW EXERCISES QUESTIONS TO ANSWER: 1. What Is Ergonomics? 2. What should you as employee know before moving, handling, and storing materials? VII. PRODUCTIVITY TEST SHEET/RUBRICS SUBJECT MODULE ACTIVITY / PROJECT: ACTIVITY CODE: TITLE SAFETY IN MATERIALS HANDLING NO. 11 MT 311 MECHANICAL NAME OF STUDENT: HANDLING SYSTEM DIRECTION: This form should afford the Instructor to rate the Productivity/Performance of the student/s for a given Employable Skill/Activity/Project. On the space provided for, write the points which likely coincide with your evaluation for each of the following factors: This module is a property of Technological University of the Philippines Visayas and intended for EDUCATIONAL PURPOSES ONLY and is NOT FOR SALE NOR FOR REPRODUCTION. 36 OUTSTANDING – (9-10); PLUS SATISFACTORY (7-8); SATISFACTORY (5- 6); BELOW SATISFACTORY (3-4 / NEED TO REPEAT) SATISFACTORY TASK PERFORMANCE REQUIREMENT Provided with detailed drawing and instructions, available tools and materials, the student should be able to: 1. Describe the safety rules and regulations in materials handling and storing. 2. Apply basic safety procedures to reduce injuries resulting from handling and storing of materials. 3. Appreciate the importance of safety in materials handling FACTORS RATING A. QUALITY / APPEARANCE (Symmetry, Verticality, Horizontality; Workmanship, Finish) B. ACCURACY/CRITICALITY (Exactness of Dimension/specification, High, Medium, Low Criticality) FINAL GRADE REMARKS: _______________________________________________________________ _______________________________________________________________ _______________________________________________________________ _______________________________________________________________ _______________________________________________________________ _______________________________________________________________ ______________________________________________________ Assessed by: ______________________________ Instructor This module is a property of Technological University of the Philippines Visayas and intended for EDUCATIONAL PURPOSES ONLY and is NOT FOR SALE NOR FOR REPRODUCTION. 37 LIST OF REFERENCES Textbook/s: Haynes, D. Oliphant (1962), Materials Handling Applications Matthew W. Potts (1946), Materials Handling Equipment James M. Apple (1971), Materials Handling William Handby, Industrial Safety Handbook Mechanical Engineers Handbook Design and Production On-line: https://www.osha.gov/Publications/OSHA2236/osha2236.html https://safetyrisk.net/safety-awareness-posters-and-graphics/ Laboratory Manuals: Department of MET, workshop laboratory manual ABOUT THE AUTHOR/S This module is a property of Technological University of the Philippines Visayas and intended for EDUCATIONAL PURPOSES ONLY and is NOT FOR SALE NOR FOR REPRODUCTION.