Week 4 Documentations PDF
Document Details
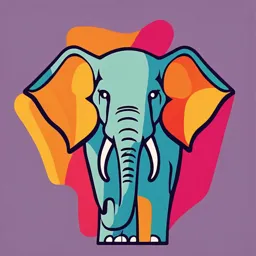
Uploaded by HaleAnecdote
George Mason University
Tags
Related
- Project Management PDF
- TE046 RJ- Disposiciones sobre Proyectos y Dirección de Obras - Libro de Órdenes y Visitas - Certificado Final de Obra - Responsabilidad Profesional del Arquitecto - Colegios - Visado Colegial PDF
- The Role of Engineers in the Construction Project PDF
- Oficina KAHOOT en orden temas PDF
- 5 Construction Projects. Technical Documents PDF
- Stavebnictví II - Zápočet Poznámky PDF
Summary
This document provides an overview of construction documentation. It covers various aspects of documentation, including primary documents, project communications, different types of orders, reports, logs, and more. This information is essential for project managers and construction professionals to ensure accurate and complete documentation.
Full Transcript
Construction Documentations Research shows that poor documentation is the number one cause of costly problems in the construction industry. Documentation is a collection of facts that records the actual history of the project. The primary purpose of documentation is to provi...
Construction Documentations Research shows that poor documentation is the number one cause of costly problems in the construction industry. Documentation is a collection of facts that records the actual history of the project. The primary purpose of documentation is to provide management with information that could be used for future reference and improvement, and/or for dealing with claims that could arise on a project. Construction Documentations The primary documents that a contractor should maintain are: – Contract records – Project communications – Daily logs or reports – Meeting minutes – Photographs – Schedule updates – Time cards – Shop drawings, back-charges, and insurance – Change orders Project Communications Throughout every project, the project manager has to communicate ideas, requests, answers, and orders to communicate with owner, A/E, subcontractors, and/or suppliers on a timely basis and to the appropriate parties. Such correspondences include formal letters, speed messages, emails, memos, and field directives. Examples for field directives include: – Field orders – Emergency field orders – Field clarification orders – Inspection reports Field Order It is an order from the owner or the A/E directing the contractor to do work that supplements the contractual requirements in order to correct unacceptable work or to do additional work. The latter may change the contract price and/or the scheduled time of completion. If so, the owner requests a proposal, initiating the change order process. The work required by a field order should be accomplished without undue delay. Emergency Field Order It demands that certain work be done at once. The owner or the A/E issues such an order usually on the basis of safety or to avoid the consequences of a field accident or an Act of God. Charges for the emergency work are settled after the emergency passes, and an accounting should be kept on a time and materials basis. Field Clarification Order This type of order is issued in response to a question regarding the interpretation of the contract documents. Normally, no change in contract amount is involved. Inspection Report An inspection report is issued as a result of an inspection by someone outside the construction project team such as an OSHA inspector, a city or local government agent, The A/E or the CM. The project manager should review the report and then issue it to the appropriate party to take action. Daily Log (Daily Project Report) The project manager and field supervisors should complete a daily log that contains at minimum the following information: – Verbal instructions – Work progress, including when and where personnel worked during the day, and what areas where started, completed or available – Special requirements or problems – Notice of equipment and material deliveries – Time and date that each change order received – Company and subcontractor manpower on site – Visitors to the site, including the owner, A/E, inspectors, testing agents, and anyone else who is not employed by the construction company Daily Log (Daily Project Report) The PM should insist that each field supervisor complete the log entries daily in order to avoid having to depend on the memory. The PM should review at least weekly the information submitted by each supervisor. The PM should record meetings and conversations with owners, A/E, subcontractors, and suppliers, and include them in the daily log. Photos In order to make each photo a document, the following information should be recorded and attached to it: – Job name and number – Date the photo was taken – Name of the person taking the photo – Subject or purpose of the photo – Any other comments describing the photo, including location, time of day, etc. Photos The PM should require every jobsite to have a camera and require the supervisor to use it at least once a day. The PM or supervisor must be certain that the information in the daily log is the same attached to the photos. Time Reports Time reports should contain information such as hours worked, areas or activities worked on, and amount of work performed. They should reflect additional work done as a result of change orders or directives from the owner or A/E. They should be completed daily by foremen and field supervisors Shop Drawings (Submittals) “Shop drawings” or “Submittals” is a broad term that encompasses drawings, schedules, lists, performance data, manufacturer’s literature, samples, and vendors’ drawings. The A/E requires that shop drawings be submitted prior to delivery of material or equipment to the jobsite. Shop Drawings (Submittals) The following are the basic steps for processing shop drawings: – Log-in shop drawings when received – verify quantities of required copies, samples, etc. – Review shop drawings for accuracy – Submit shop drawings to the A/E If approved, return them to supplier or contractor and distribute approved copies to the project team If rejected, return them to supplier or contractor for corrections and repeat the review process. Shop Drawings (Submittals) The A/E is only responsible for checking the manufacturer, style, and quality of the material or equipment, then approving or rejecting the drawings and returning them to the contractor. It should be noted that the A/E gives only qualified approval. The contractor must verify the quantities and dimensions. The contract documents stipulate that the approval of shop drawings by the A/E does not relieve the contractor of responsibility for furnishing materials and equipment in accordance with the contract documents. Shop Drawings (Submittals) The project manager or the project engineer is responsible for checking shop drawings, but the field supervisors must be involved when dimensions must be verified. If the shop drawings are approved, the contractor returns them to the supplier or subcontractor and distributes them to the field supervisors. Rejected drawings should not be distributed in the field, so as to avoid the error of having wrong information used in construction. Back Charges Back charges occur when a contractor charge another contractor for extra costs incurred. During the course of a project, the PM may be requested to perform work that is outside the terms of the contract documents such as furnishing labor, materials, or equipment in assisting other trade, or repair damaged work by another contractor. They are in the form of change orders. Back Charges The following are examples of back charges commonly occur on construction projects: – Contractors furnishes scaffolding to another contractor – Contractor provides saw cutting and patching for another contractor – Contractor furnishes a pump to another contractor to remove water from a trench – contractor provides labor and equipment to remove other contractors’ trash Close-out Documents Project close-out begins at the point of substantial completion. Its purpose is to ensure that the owner is receiving a finished product that conforms to the contract documents. The PM must provide the documentation that provides this assurance. Close-Out Procedures The PM must formally organize project close-out no later than thirty days prior to substantial completion. This involves sending all subcontractors and suppliers a copy of the project’s close-out procedures. Project Inspection The PM should arrange for all parties to meet with him and conduct an inspection tour (walk-through) of the structure well before the date of substantial completion. Written notification of the walk-through should be sent to all concerned parties well in advance. At the conclusion of the walk-through, the PM must be sure that each party signs a certificate to indicate their acceptance of work Punch List Generally the A/E conducts the inspection. A punch list is then given to the contractors for completion prior to the stated date. Contractors must prepare their own punch list prior to inspection. Owner Acceptance After all inspections are satisfactorily completed, the A/E prepares the certificate of substantial completion for the owner and appends to it a list of any remaining deficiencies (punch List). Usually this document is effective pending on the correction of any deficiencies, and the certification of the local department that it meets the health and safety requirements. As-Built Drawings As-built drawings are developed to show changes to the project as it is being built. Normally, the A/E will furnish a set of drawings for recording any changes. The general contractor is responsible for maintaining a complete set of as-builts and for making sure that each subcontractor keeps the as- builts updated. At the completion of the project, the as-builts are submitted to the A/E as part of the close-out documents. Operation and Maintenance Manuals Operations and maintenance manuals must be furnished to the owner upon completion of the project. They should contain all information necessary for operating, maintaining, repairing, dismantling, and assembling all equipment provided under the project contract. Warranties Warranties are furnished by contractors and suppliers to guarantee workmanship and material integrity for a specified length of time. All warranties must be in writing and on authorized company forms. Consent of Surety and Release of Liens One of the most important close-out documents is the Consent of Surety & Release of Liens. This document releases the bonding company from further liability for the project. In the same manner, the Affidavits of Payment of Debts and Claims release the owner from all claims made by the general contractor, subcontractors, or suppliers. Elements of Good Documentations In order to be useful, documentation must meet five criteria, which represent the elements of good documentation: – Accuracy – Objectivity (Credibility) – Completeness – Uniformity – Timeliness