A330 RR Trent 700 Technical Training Manual PDF
Document Details
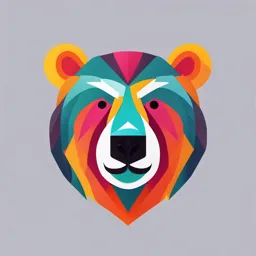
Uploaded by EminentAspen
UAntwerp
2019
Tags
Summary
This document provides detailed component locations and descriptions for a RR Trent 700 engine, covering the thrust reverser system, oil system, engine control systems, and ignition/starting processes. The information is part of a technical training manual.
Full Transcript
POWER PLANT RR TRENT 700 COMPONENT LOCATION (2) THRUST REVERSER SYSTEM The Isolation Control Unit (ICU) is installed at the top of the R/H fan case. The Directional Control Unit (DCU) is on the front face of the R/H c-duct. The pivoting doors actuators and primary locks are attached on the fron...
POWER PLANT RR TRENT 700 COMPONENT LOCATION (2) THRUST REVERSER SYSTEM The Isolation Control Unit (ICU) is installed at the top of the R/H fan case. The Directional Control Unit (DCU) is on the front face of the R/H c-duct. The pivoting doors actuators and primary locks are attached on the front face of each c-duct. Two pivoting door are installed on the side of each c-duct. The tertiary locks are accessible through a dedicated access panel located in-between both pivoting doors. MECHANICAL & AVIONICS COURSE - T1+T2 (LVL 2&3) 70 - POWER PLANT (RR Trent 700) POWER PLANT RR TRENT 700 COMPONENT LOCATION (2) Apr 16, 2013 Page 200 A330 RR Trent 700 TECHNICAL TRAINING MANUAL GCL13151 - GEHT0M0 - FM70C9COMPLOC71 B1/B2\_A330\_DIFF\_FR\_A320 REV. 1 DATE: 01.06.2019 DVIATION TRAINING SERVICES FOR TRAINING PURPOSES ONLY 200 THRUST REVERSER SYSTEM MECHANICAL & AVIONICS COURSE - T1+T2 (LVL 2&3) 70 - POWER PLANT (RR Trent 700) POWER PLANT RR TRENT 700 COMPONENT LOCATION (2) Apr 16, 2013 Page 201 A330 RR Trent 700 TECHNICAL TRAINING MANUAL GCL13151 - GEHT0M0 - FM70C9COMPLOC71 B1/B2\_A330\_DIFF\_FR\_A320 REV. 1 DATE: 01.06.2019 DVIATION TRAINING SERVICES FOR TRAINING PURPOSES ONLY 201 THRUST REVERSER SYSTEM MECHANICAL & AVIONICS COURSE - T1+T2 (LVL 2&3) 70 - POWER PLANT (RR Trent 700) POWER PLANT RR TRENT 700 COMPONENT LOCATION (2) Apr 16, 2013 Page 202 A330 RR Trent 700 TECHNICAL TRAINING MANUAL GCL13151 - GEHT0M0 - FM70C9COMPLOC71 B1/B2\_A330\_DIFF\_FR\_A320 REV. 1 DATE: 01.06.2019 DVIATION TRAINING SERVICES FOR TRAINING PURPOSES ONLY 202 This Page Intentionally Left Blank MECHANICAL & AVIONICS COURSE - T1+T2 (LVL 2&3) 70 - POWER PLANT (RR Trent 700) POWER PLANT RR TRENT 700 COMPONENT LOCATION (2) Apr 16, 2013 Page 203 A330 RR Trent 700 TECHNICAL TRAINING MANUAL GCL13151 - GEHT0M0 - FM70C9COMPLOC71 B1/B2\_A330\_DIFF\_FR\_A320 REV. 1 DATE: 01.06.2019 DVIATION TRAINING SERVICES FOR TRAINING PURPOSES ONLY 203 POWER PLANT RR TRENT 700 COMPONENT LOCATION (2) OIL SYSTEM The following components are fitted on the R/H fan case: \- Oil tank, \- Master chip detector, \- Scavenge filter, \- Air/Oil Heat Exchanger (AOHE), \- Fuel Oil Heat Exchanger (FOHE). The lubrication unit is on the rear face of the gearbox. MECHANICAL & AVIONICS COURSE - T1+T2 (LVL 2&3) 70 - POWER PLANT (RR Trent 700) POWER PLANT RR TRENT 700 COMPONENT LOCATION (2) Apr 16, 2013 Page 204 A330 RR Trent 700 TECHNICAL TRAINING MANUAL GCL13151 - GEHT0M0 - FM70C9COMPLOC71 B1/B2\_A330\_DIFF\_FR\_A320 REV. 1 DATE: 01.06.2019 DVIATION TRAINING SERVICES FOR TRAINING PURPOSES ONLY 204 OIL SYSTEM MECHANICAL & AVIONICS COURSE - T1+T2 (LVL 2&3) 70 - POWER PLANT (RR Trent 700) POWER PLANT RR TRENT 700 COMPONENT LOCATION (2) Apr 16, 2013 Page 205 A330 RR Trent 700 TECHNICAL TRAINING MANUAL GCL13151 - GEHT0M0 - FM70C9COMPLOC71 B1/B2\_A330\_DIFF\_FR\_A320 REV. 1 DATE: 01.06.2019 DVIATION TRAINING SERVICES FOR TRAINING PURPOSES ONLY 205 ENGINE SYSTEM CONTROL & INDICATING (2) LOCATE CONTROL/INDICATING IN COCKPIT FADEC POWERING ENGINE START & MOTORING CONTROLS THRUST CONTROL ANIMATED SCHEMATIC MECHANICAL & AVIONICS COURSE - T1+T2 (LVL 2&3) 70 - POWER PLANT (RR Trent 700) ENGINE SYSTEM CONTROL & INDICATING (2) Apr 16, 2013 Page 206 A330 RR Trent 700 TECHNICAL TRAINING MANUAL GCL13151 - GEHT0M0 - FM70IZLEVEL0201 B1/B2\_A330\_DIFF\_FR\_A320 REV. 1 DATE: 01.06.2019 DVIATION TRAINING SERVICES FOR TRAINING PURPOSES ONLY 206 This Page Intentionally Left Blank MECHANICAL & AVIONICS COURSE - T1+T2 (LVL 2&3) 70 - POWER PLANT (RR Trent 700) ENGINE SYSTEM CONTROL & INDICATING (2) Apr 16, 2013 Page 207 A330 RR Trent 700 TECHNICAL TRAINING MANUAL GCL13151 - GEHT0M0 - FM70IZLEVEL0201 B1/B2\_A330\_DIFF\_FR\_A320 REV. 1 DATE: 01.06.2019 DVIATION TRAINING SERVICES FOR TRAINING PURPOSES ONLY 207 IGNITION AND STARTING D/O (3) GENERAL Engine starting, motoring and ignition sequences are selected by the Engine Electronic Controller (EEC) according to digital command inputs from the Engine Interface and Vibration Monitoring Unit (EIVMU). To achieve these functions, the following sub-systems are combined: \- starting, \- fuel, \- ignition. MECHANICAL & AVIONICS COURSE - T1+T2 (LVL 2&3) 70 - POWER PLANT (RR Trent 700) IGNITION AND STARTING D/O (3) Apr 16, 2013 Page 208 A330 RR Trent 700 TECHNICAL TRAINING MANUAL GCL13151 - GEHT0M0 - FM70DC000000071 B1/B2\_A330\_DIFF\_FR\_A320 REV. 1 DATE: 01.06.2019 DVIATION TRAINING SERVICES FOR TRAINING PURPOSES ONLY 208 GENERAL MECHANICAL & AVIONICS COURSE - T1+T2 (LVL 2&3) 70 - POWER PLANT (RR Trent 700) IGNITION AND STARTING D/O (3) Apr 16, 2013 Page 209 A330 RR Trent 700 TECHNICAL TRAINING MANUAL GCL13151 - GEHT0M0 - FM70DC000000071 B1/B2\_A330\_DIFF\_FR\_A320 REV. 1 DATE: 01.06.2019 DVIATION TRAINING SERVICES FOR TRAINING PURPOSES ONLY 209 IGNITION AND STARTING D/O (3) STARTING SYSTEM DESCRIPTION The primary components of the engine pneumatic starting system are: \- the Starter Control Valve (SCV), \- the pneumatic starter. The starting system uses air from a ground air supply, the APU or the other engine already started. MECHANICAL & AVIONICS COURSE - T1+T2 (LVL 2&3) 70 - POWER PLANT (RR Trent 700) IGNITION AND STARTING D/O (3) Apr 16, 2013 Page 210 A330 RR Trent 700 TECHNICAL TRAINING MANUAL GCL13151 - GEHT0M0 - FM70DC000000071 B1/B2\_A330\_DIFF\_FR\_A320 REV. 1 DATE: 01.06.2019 DVIATION TRAINING SERVICES FOR TRAINING PURPOSES ONLY 210 STARTING SYSTEM DESCRIPTION MECHANICAL & AVIONICS COURSE - T1+T2 (LVL 2&3) 70 - POWER PLANT (RR Trent 700) IGNITION AND STARTING D/O (3) Apr 16, 2013 Page 211 A330 RR Trent 700 TECHNICAL TRAINING MANUAL GCL13151 - GEHT0M0 - FM70DC000000071 B1/B2\_A330\_DIFF\_FR\_A320 REV. 1 DATE: 01.06.2019 DVIATION TRAINING SERVICES FOR TRAINING PURPOSES ONLY 211 IGNITION AND STARTING D/O (3) STARTING SYSTEM DESCRIPTION (continued) PNEUMATIC STARTER The pneumatic starter is a pneumatically operated turbine installed on the gearbox by a Quick Attach Detach (QAD) adapter. The starter rotates the HP rotor (N3) through an external gearbox module input shaft. An oil fill plug and an oil level overflow plug are installed on the starter case. An oil level sight glass is also installed on the starter case for oil level indication. A drain plug with a Magnetic Chip Detector (MCD) is installed on the starter case lower surface. The continuous operation of the pneumatic starter must be limited in accordance with the limits outlined in the AMM. MECHANICAL & AVIONICS COURSE - T1+T2 (LVL 2&3) 70 - POWER PLANT (RR Trent 700) IGNITION AND STARTING D/O (3) Apr 16, 2013 Page 212 A330 RR Trent 700 TECHNICAL TRAINING MANUAL GCL13151 - GEHT0M0 - FM70DC000000071 B1/B2\_A330\_DIFF\_FR\_A320 REV. 1 DATE: 01.06.2019 DVIATION TRAINING SERVICES FOR TRAINING PURPOSES ONLY 212 STARTING SYSTEM DESCRIPTION - PNEUMATIC STARTER MECHANICAL & AVIONICS COURSE - T1+T2 (LVL 2&3) 70 - POWER PLANT (RR Trent 700) IGNITION AND STARTING D/O (3) Apr 16, 2013 Page 213 A330 RR Trent 700 TECHNICAL TRAINING MANUAL GCL13151 - GEHT0M0 - FM70DC000000071 B1/B2\_A330\_DIFF\_FR\_A320 REV. 1 DATE: 01.06.2019 DVIATION TRAINING SERVICES FOR TRAINING PURPOSES ONLY 213 IGNITION AND STARTING D/O (3) STARTING SYSTEM DESCRIPTION (continued) STARTER CONTROL VALVE (SCV) The Starter Control Valve (SCV) controls the airflow delivered to the pneumatic starter. The SCV is located on the lower LH side of the LP compressor case. The SCV is electrically controlled and monitored by the EEC and is pneumatically operated. The primary components of the SCV are: \- a valve assembly which has a butterfly valve, \- an actuator assembly that transmits the movement to open and close the butterfly valve, \- a dual coil solenoid, controlled by electrical signals from the EEC. The SCV has a square socket to get manual operation of the butterfly valve in case of SCV electrical control failure. It is accessible through an access door located on the left fan cowl door (it is not necessary to open the fan cowl doors). The valve position is given to the EEC by two microswitches, one for each EEC channel. MECHANICAL & AVIONICS COURSE - T1+T2 (LVL 2&3) 70 - POWER PLANT (RR Trent 700) IGNITION AND STARTING D/O (3) Apr 16, 2013 Page 214 A330 RR Trent 700 TECHNICAL TRAINING MANUAL GCL13151 - GEHT0M0 - FM70DC000000071 B1/B2\_A330\_DIFF\_FR\_A320 REV. 1 DATE: 01.06.2019 DVIATION TRAINING SERVICES FOR TRAINING PURPOSES ONLY 214 STARTING SYSTEM DESCRIPTION - STARTER CONTROL VALVE (SCV) MECHANICAL & AVIONICS COURSE - T1+T2 (LVL 2&3) 70 - POWER PLANT (RR Trent 700) IGNITION AND STARTING D/O (3) Apr 16, 2013 Page 215 A330 RR Trent 700 TECHNICAL TRAINING MANUAL GCL13151 - GEHT0M0 - FM70DC000000071 B1/B2\_A330\_DIFF\_FR\_A320 REV. 1 DATE: 01.06.2019 DVIATION TRAINING SERVICES FOR TRAINING PURPOSES ONLY 215 IGNITION AND STARTING D/O (3) IGNITION SYSTEM DESCRIPTION Each engine has two ignition systems, A and B. These systems are controlled by the EEC and can be operated independently or simultaneously. Each system has an ignition unit, an ignition lead and an igniter plug. Each ignition system is electrically supplied with a dedicated 115 VAC power line delivered by the aircraft electrical system through the EIVMU and transmitted to the Power Control Unit (PCU). MECHANICAL & AVIONICS COURSE - T1+T2 (LVL 2&3) 70 - POWER PLANT (RR Trent 700) IGNITION AND STARTING D/O (3) Apr 16, 2013 Page 216 A330 RR Trent 700 TECHNICAL TRAINING MANUAL GCL13151 - GEHT0M0 - FM70DC000000071 B1/B2\_A330\_DIFF\_FR\_A320 REV. 1 DATE: 01.06.2019 DVIATION TRAINING SERVICES FOR TRAINING PURPOSES ONLY 216 IGNITION SYSTEM DESCRIPTION MECHANICAL & AVIONICS COURSE - T1+T2 (LVL 2&3) 70 - POWER PLANT (RR Trent 700) IGNITION AND STARTING D/O (3) Apr 16, 2013 Page 217 A330 RR Trent 700 TECHNICAL TRAINING MANUAL GCL13151 - GEHT0M0 - FM70DC000000071 B1/B2\_A330\_DIFF\_FR\_A320 REV. 1 DATE: 01.06.2019 DVIATION TRAINING SERVICES FOR TRAINING PURPOSES ONLY 217 IGNITION AND STARTING D/O (3) IGNITION SYSTEM DESCRIPTION (continued) IGNITION UNITS Two ignition units are installed on bracket assemblies on the lower LH side of the LP compressor case. Each ignition unit changes electrical inputs into high voltage electrical outputs of between 2.7 and 3.0 Kvolts. The ignition systems are of high-voltage and high-energy type. Energy is stored in the ignition unit and is released at a rate of 60 to 135 sparks per minute. IGNITER PLUGS AND LEADS The igniter plugs are installed adjacent to the number 10 and number 16 fuel spray nozzles. Each igniter plug is directly supplied electrically from its associated ignition unit through an ignition lead. MECHANICAL & AVIONICS COURSE - T1+T2 (LVL 2&3) 70 - POWER PLANT (RR Trent 700) IGNITION AND STARTING D/O (3) Apr 16, 2013 Page 218 A330 RR Trent 700 TECHNICAL TRAINING MANUAL GCL13151 - GEHT0M0 - FM70DC000000071 B1/B2\_A330\_DIFF\_FR\_A320 REV. 1 DATE: 01.06.2019 DVIATION TRAINING SERVICES FOR TRAINING PURPOSES ONLY 218 IGNITION SYSTEM DESCRIPTION - IGNITION UNITS & IGNITER PLUGS AND LEADS MECHANICAL & AVIONICS COURSE - T1+T2 (LVL 2&3) 70 - POWER PLANT (RR Trent 700) IGNITION AND STARTING D/O (3) Apr 16, 2013 Page 219 A330 RR Trent 700 TECHNICAL TRAINING MANUAL GCL13151 - GEHT0M0 - FM70DC000000071 B1/B2\_A330\_DIFF\_FR\_A320 REV. 1 DATE: 01.06.2019 DVIATION TRAINING SERVICES FOR TRAINING PURPOSES ONLY 219 IGNITION AND STARTING D/O (3) IGNITION SYSTEM DESCRIPTION (continued) IGNITION SYSTEM POWER SUPPLY Two inputs of 115 Volts 400 Hz AC power are supplied by the aircraft electrical system to the PCU through the EIVMU. The PCU electrical supply remains operational even if the EIVMU fails or is not powered. The AC emergency bus is connected to two relays in PCU channel A and the AC normal bus is connected to two relays in PCU channel B. The four relays of the PCU are controlled by the EEC to supply the ignition system A or system B, or both, with either emergency or normal aircraft 115 VAC power supply. The EEC thus cycles through the possible combinations of ignition systems and aircraft power supplies during successive engine starts. The EEC automatic start logic selects a different ignition system from the previous start in order to identify any potential ignition system failure as soon as possible. A functional test of the ignition system can be done through the EEC MCDU page, to check correct operation of any of the power supply and ignition unit combination. MECHANICAL & AVIONICS COURSE - T1+T2 (LVL 2&3) 70 - POWER PLANT (RR Trent 700) IGNITION AND STARTING D/O (3) Apr 16, 2013 Page 220 A330 RR Trent 700 TECHNICAL TRAINING MANUAL GCL13151 - GEHT0M0 - FM70DC000000071 B1/B2\_A330\_DIFF\_FR\_A320 REV. 1 DATE: 01.06.2019 DVIATION TRAINING SERVICES FOR TRAINING PURPOSES ONLY 220 IGNITION SYSTEM DESCRIPTION - IGNITION SYSTEM POWER SUPPLY MECHANICAL & AVIONICS COURSE - T1+T2 (LVL 2&3) 70 - POWER PLANT (RR Trent 700) IGNITION AND STARTING D/O (3) Apr 16, 2013 Page 221 A330 RR Trent 700 TECHNICAL TRAINING MANUAL GCL13151 - GEHT0M0 - FM70DC000000071 B1/B2\_A330\_DIFF\_FR\_A320 REV. 1 DATE: 01.06.2019 DVIATION TRAINING SERVICES FOR TRAINING PURPOSES ONLY 221 IGNITION AND STARTING D/O (3) STARTING OPERATION The Full Authority Digital Engine Control (FADEC) system gives two modes of engine start: automatic start and manual start. The EEC selects the start mode according to digital inputs from the EIVMU reflecting the cockpit settings. The automatic starting sequence can be selected with valid EIVMU data or using an alternate start discrete if the EIVMU data is invalid. Manual start mode can only be selected with valid EIVMU data. AUTOMATIC START ON GROUND In automatic start mode, the igniters, fuel, and SCV are under full authority of the EEC. The engine start initial configuration is: \- the ENG MASTER switch on the ENG MASTER panel in the OFF position, \- the selector on the ENG START panel in the NORM position, \- air pressure available and above 30 psi, \- electrical power available, \- engine fuel supply available. To initiate the automatic start sequence, first the ENG START selector must be set to IGN/START position. The FADECs are then powered and the ENGINE system page comes up automatically on the ECAM SD. Start valve position and engine bleed pressure are shown on this page in place of nacelle temperature indication. When an ENG MASTER switch is set to ON, the corresponding fuel LP valve opens and the associated EEC controls the SCV to the open position by energizing its solenoid. Air pressure is delivered to the pneumatic starter, which starts to rotate the N3 rotor. The FADEC continuously monitors N3 and Exhaust Gas Temperature (EGT) during the starting sequence. When N3 reaches 25%, and EGT is below 150 degrees Celsius, the EEC commands the fuel supply by opening the fuel metering valve and the Pressure Raising and Shut Off Valve (PRSOV), and selects one ignition system on (A or B). The active ignition system is indicated on ECAM. The fuel flow starts to increase. When N3 reaches 50%, the EEC closes the SCV and de-energizes the active igniter. The ECAM indication of the active igniter disappears. The EEC continues to monitor the starting sequence until minimum idle is reached. At the end of the sequence, the ENG START selector must be set back to NORM. MECHANICAL & AVIONICS COURSE - T1+T2 (LVL 2&3) 70 - POWER PLANT (RR Trent 700) IGNITION AND STARTING D/O (3) Apr 16, 2013 Page 222 A330 RR Trent 700 TECHNICAL TRAINING MANUAL GCL13151 - GEHT0M0 - FM70DC000000071 B1/B2\_A330\_DIFF\_FR\_A320 REV. 1 DATE: 01.06.2019 DVIATION TRAINING SERVICES FOR TRAINING PURPOSES ONLY 222 STARTING OPERATION - AUTOMATIC START ON GROUND MECHANICAL & AVIONICS COURSE - T1+T2 (LVL 2&3) 70 - POWER PLANT (RR Trent 700) IGNITION AND STARTING D/O (3) Apr 16, 2013 Page 223 A330 RR Trent 700 TECHNICAL TRAINING MANUAL GCL13151 - GEHT0M0 - FM70DC000000071 B1/B2\_A330\_DIFF\_FR\_A320 REV. 1 DATE: 01.06.2019 DVIATION TRAINING SERVICES FOR TRAINING PURPOSES ONLY 223 STARTING OPERATION - AUTOMATIC START ON GROUND MECHANICAL & AVIONICS COURSE - T1+T2 (LVL 2&3) 70 - POWER PLANT (RR Trent 700) IGNITION AND STARTING D/O (3) Apr 16, 2013 Page 224 A330 RR Trent 700 TECHNICAL TRAINING MANUAL GCL13151 - GEHT0M0 - FM70DC000000071 B1/B2\_A330\_DIFF\_FR\_A320 REV. 1 DATE: 01.06.2019 DVIATION TRAINING SERVICES FOR TRAINING PURPOSES ONLY 224 STARTING OPERATION - AUTOMATIC START ON GROUND MECHANICAL & AVIONICS COURSE - T1+T2 (LVL 2&3) 70 - POWER PLANT (RR Trent 700) IGNITION AND STARTING D/O (3) Apr 16, 2013 Page 225 A330 RR Trent 700 TECHNICAL TRAINING MANUAL GCL13151 - GEHT0M0 - FM70DC000000071 B1/B2\_A330\_DIFF\_FR\_A320 REV. 1 DATE: 01.06.2019 DVIATION TRAINING SERVICES FOR TRAINING PURPOSES ONLY 225 STARTING OPERATION - AUTOMATIC START ON GROUND MECHANICAL & AVIONICS COURSE - T1+T2 (LVL 2&3) 70 - POWER PLANT (RR Trent 700) IGNITION AND STARTING D/O (3) Apr 16, 2013 Page 226 A330 RR Trent 700 TECHNICAL TRAINING MANUAL GCL13151 - GEHT0M0 - FM70DC000000071 B1/B2\_A330\_DIFF\_FR\_A320 REV. 1 DATE: 01.06.2019 DVIATION TRAINING SERVICES FOR TRAINING PURPOSES ONLY 226 STARTING OPERATION - AUTOMATIC START ON GROUND MECHANICAL & AVIONICS COURSE - T1+T2 (LVL 2&3) 70 - POWER PLANT (RR Trent 700) IGNITION AND STARTING D/O (3) Apr 16, 2013 Page 227 A330 RR Trent 700 TECHNICAL TRAINING MANUAL GCL13151 - GEHT0M0 - FM70DC000000071 B1/B2\_A330\_DIFF\_FR\_A320 REV. 1 DATE: 01.06.2019 DVIATION TRAINING SERVICES FOR TRAINING PURPOSES ONLY 227 STARTING OPERATION - AUTOMATIC START ON GROUND MECHANICAL & AVIONICS COURSE - T1+T2 (LVL 2&3) 70 - POWER PLANT (RR Trent 700) IGNITION AND STARTING D/O (3) Apr 16, 2013 Page 228 A330 RR Trent 700 TECHNICAL TRAINING MANUAL GCL13151 - GEHT0M0 - FM70DC000000071 B1/B2\_A330\_DIFF\_FR\_A320 REV. 1 DATE: 01.06.2019 DVIATION TRAINING SERVICES FOR TRAINING PURPOSES ONLY 228 This Page Intentionally Left Blank MECHANICAL & AVIONICS COURSE - T1+T2 (LVL 2&3) 70 - POWER PLANT (RR Trent 700) IGNITION AND STARTING D/O (3) Apr 16, 2013 Page 229 A330 RR Trent 700 TECHNICAL TRAINING MANUAL GCL13151 - GEHT0M0 - FM70DC000000071 B1/B2\_A330\_DIFF\_FR\_A320 REV. 1 DATE: 01.06.2019 DVIATION TRAINING SERVICES FOR TRAINING PURPOSES ONLY 229 IGNITION AND STARTING D/O (3) STARTING OPERATION (continued) MANUAL START ON GROUND A manual start procedure is recommended at high altitude airports, during hot weather conditions, or any time the pneumatic pressure delivered to SCV is low. In manual start mode, starting control is under limited authority of the EEC. The SCV, fuel supply and igniters are controlled by the crew using a conventional procedure. The initial conditions to start the engine in manual mode are identical to those of the automatic start. To initiate a manual start sequence, the ENG START selector must be set to IGN/START position. Both EECs are then powered and the ENGINE system page comes up automatically on the ECAM SD. The EEC ensures only a passive monitoring of the manual start sequence. The associated ENGine MANual START P/B is set to ON position and the EEC opens the SCV, allowing the pneumatic starter to rotate the N3 rotor. When N3 reaches its maximum motoring speed and at least 25%, the associated ENG MASTER switch has to be selected ON. Then, the EEC commands the fuel supply by opening the metering valve and the PRSOV and selects both ignition systems on. The fuel flow starts to increase. The EEC monitors the N3. When N3 reaches 50%, the EEC closes the SCV and de-energizes both ignition systems. Once the start sequence is completed, the ENG START selector is set back to NORM position and the ENG MAN START P/B is set back to OFF. MECHANICAL & AVIONICS COURSE - T1+T2 (LVL 2&3) 70 - POWER PLANT (RR Trent 700) IGNITION AND STARTING D/O (3) Apr 16, 2013 Page 230 A330 RR Trent 700 TECHNICAL TRAINING MANUAL GCL13151 - GEHT0M0 - FM70DC000000071 B1/B2\_A330\_DIFF\_FR\_A320 REV. 1 DATE: 01.06.2019 DVIATION TRAINING SERVICES FOR TRAINING PURPOSES ONLY 230 STARTING OPERATION - MANUAL START ON GROUND MECHANICAL & AVIONICS COURSE - T1+T2 (LVL 2&3) 70 - POWER PLANT (RR Trent 700) IGNITION AND STARTING D/O (3) Apr 16, 2013 Page 231 A330 RR Trent 700 TECHNICAL TRAINING MANUAL GCL13151 - GEHT0M0 - FM70DC000000071 B1/B2\_A330\_DIFF\_FR\_A320 REV. 1 DATE: 01.06.2019 DVIATION TRAINING SERVICES FOR TRAINING PURPOSES ONLY 231 STARTING OPERATION - MANUAL START ON GROUND MECHANICAL & AVIONICS COURSE - T1+T2 (LVL 2&3) 70 - POWER PLANT (RR Trent 700) IGNITION AND STARTING D/O (3) Apr 16, 2013 Page 232 A330 RR Trent 700 TECHNICAL TRAINING MANUAL GCL13151 - GEHT0M0 - FM70DC000000071 B1/B2\_A330\_DIFF\_FR\_A320 REV. 1 DATE: 01.06.2019 DVIATION TRAINING SERVICES FOR TRAINING PURPOSES ONLY 232 STARTING OPERATION - MANUAL START ON GROUND MECHANICAL & AVIONICS COURSE - T1+T2 (LVL 2&3) 70 - POWER PLANT (RR Trent 700) IGNITION AND STARTING D/O (3) Apr 16, 2013 Page 233 A330 RR Trent 700 TECHNICAL TRAINING MANUAL GCL13151 - GEHT0M0 - FM70DC000000071 B1/B2\_A330\_DIFF\_FR\_A320 REV. 1 DATE: 01.06.2019 DVIATION TRAINING SERVICES FOR TRAINING PURPOSES ONLY 233 STARTING OPERATION - MANUAL START ON GROUND MECHANICAL & AVIONICS COURSE - T1+T2 (LVL 2&3) 70 - POWER PLANT (RR Trent 700) IGNITION AND STARTING D/O (3) Apr 16, 2013 Page 234 A330 RR Trent 700 TECHNICAL TRAINING MANUAL GCL13151 - GEHT0M0 - FM70DC000000071 B1/B2\_A330\_DIFF\_FR\_A320 REV. 1 DATE: 01.06.2019 DVIATION TRAINING SERVICES FOR TRAINING PURPOSES ONLY 234 STARTING OPERATION - MANUAL START ON GROUND MECHANICAL & AVIONICS COURSE - T1+T2 (LVL 2&3) 70 - POWER PLANT (RR Trent 700) IGNITION AND STARTING D/O (3) Apr 16, 2013 Page 235 A330 RR Trent 700 TECHNICAL TRAINING MANUAL GCL13151 - GEHT0M0 - FM70DC000000071 B1/B2\_A330\_DIFF\_FR\_A320 REV. 1 DATE: 01.06.2019 DVIATION TRAINING SERVICES FOR TRAINING PURPOSES ONLY 235 STARTING OPERATION - MANUAL START ON GROUND MECHANICAL & AVIONICS COURSE - T1+T2 (LVL 2&3) 70 - POWER PLANT (RR Trent 700) IGNITION AND STARTING D/O (3) Apr 16, 2013 Page 236 A330 RR Trent 700 TECHNICAL TRAINING MANUAL GCL13151 - GEHT0M0 - FM70DC000000071 B1/B2\_A330\_DIFF\_FR\_A320 REV. 1 DATE: 01.06.2019 DVIATION TRAINING SERVICES FOR TRAINING PURPOSES ONLY 236 This Page Intentionally Left Blank MECHANICAL & AVIONICS COURSE - T1+T2 (LVL 2&3) 70 - POWER PLANT (RR Trent 700) IGNITION AND STARTING D/O (3) Apr 16, 2013 Page 237 A330 RR Trent 700 TECHNICAL TRAINING MANUAL GCL13151 - GEHT0M0 - FM70DC000000071 B1/B2\_A330\_DIFF\_FR\_A320 REV. 1 DATE: 01.06.2019 DVIATION TRAINING SERVICES FOR TRAINING PURPOSES ONLY 237 IGNITION AND STARTING D/O (3) STARTING OPERATION (continued) APU BOOST During an automatic or manual start using APU bleed, when the ENG START selector is set to IGN/START position, the APU Electronic Control Box (ECB) receives a Main Engine Start (MES) input signal via the EIVMU to boost the APU bleed airflow. When N3 reaches 50%, the ECB sets the bleed airflow back to normal. MECHANICAL & AVIONICS COURSE - T1+T2 (LVL 2&3) 70 - POWER PLANT (RR Trent 700) IGNITION AND STARTING D/O (3) Apr 16, 2013 Page 238 A330 RR Trent 700 TECHNICAL TRAINING MANUAL GCL13151 - GEHT0M0 - FM70DC000000071 B1/B2\_A330\_DIFF\_FR\_A320 REV. 1 DATE: 01.06.2019 DVIATION TRAINING SERVICES FOR TRAINING PURPOSES ONLY 238 STARTING OPERATION - APU BOOST MECHANICAL & AVIONICS COURSE - T1+T2 (LVL 2&3) 70 - POWER PLANT (RR Trent 700) IGNITION AND STARTING D/O (3) Apr 16, 2013 Page 239 A330 RR Trent 700 TECHNICAL TRAINING MANUAL GCL13151 - GEHT0M0 - FM70DC000000071 B1/B2\_A330\_DIFF\_FR\_A320 REV. 1 DATE: 01.06.2019 DVIATION TRAINING SERVICES FOR TRAINING PURPOSES ONLY 239 IGNITION AND STARTING D/O (3) STARTING OPERATION (continued) ALTERNATE START DISCRETE LOGIC In normal operation, engine starting/shutdown/ignition control is initiated by the EEC based on the position of switches on the engine control panels. The discrete signals from these switches are sent to the EIVMU, converted into digital data and transmitted to the EEC. So that an EIVMU failure should not prevent the aircraft dispatch, an alternate start discrete logic has been designed to allow the main starting functions to be maintained. When EIVMU data are not available, the alternate start discrete logic lets the EEC peform an automatic start, dry motoring or selection of continuous ignition. The alternate start discrete logic integrates the position of the following controls: \- the ENG START rotary selector, \- the ENG MASTER switch, \- the ENG MANual START P/B, \- the ENG ANTI ICE P/B and, \- the engine running discrete (N3\>50%). When IGN START is selected and the ENG MASTER switch is set to ON the EEC initiates an automatic start. When CRANK is selected and the MAN START P/B is pressed in the EEC initiates the dry motoring procedure. When IGN START is selected and the engine is running, the EEC selects continuous ignition. When ENG ANTI ICE is selected while the engine is running, the EEC selects continuous ignition. MECHANICAL & AVIONICS COURSE - T1+T2 (LVL 2&3) 70 - POWER PLANT (RR Trent 700) IGNITION AND STARTING D/O (3) Apr 16, 2013 Page 240 A330 RR Trent 700 TECHNICAL TRAINING MANUAL GCL13151 - GEHT0M0 - FM70DC000000071 B1/B2\_A330\_DIFF\_FR\_A320 REV. 1 DATE: 01.06.2019 DVIATION TRAINING SERVICES FOR TRAINING PURPOSES ONLY 240 STARTING OPERATION - ALTERNATE START DISCRETE LOGIC MECHANICAL & AVIONICS COURSE - T1+T2 (LVL 2&3) 70 - POWER PLANT (RR Trent 700) IGNITION AND STARTING D/O (3) Apr 16, 2013 Page 241 A330 RR Trent 700 TECHNICAL TRAINING MANUAL GCL13151 - GEHT0M0 - FM70DC000000071 B1/B2\_A330\_DIFF\_FR\_A320 REV. 1 DATE: 01.06.2019 DVIATION TRAINING SERVICES FOR TRAINING PURPOSES ONLY 241 STARTING OPERATION - ALTERNATE START DISCRETE LOGIC MECHANICAL & AVIONICS COURSE - T1+T2 (LVL 2&3) 70 - POWER PLANT (RR Trent 700) IGNITION AND STARTING D/O (3) Apr 16, 2013 Page 242 A330 RR Trent 700 TECHNICAL TRAINING MANUAL GCL13151 - GEHT0M0 - FM70DC000000071 B1/B2\_A330\_DIFF\_FR\_A320 REV. 1 DATE: 01.06.2019 DVIATION TRAINING SERVICES FOR TRAINING PURPOSES ONLY 242 STARTING OPERATION - ALTERNATE START DISCRETE LOGIC MECHANICAL & AVIONICS COURSE - T1+T2 (LVL 2&3) 70 - POWER PLANT (RR Trent 700) IGNITION AND STARTING D/O (3) Apr 16, 2013 Page 243 A330 RR Trent 700 TECHNICAL TRAINING MANUAL GCL13151 - GEHT0M0 - FM70DC000000071 B1/B2\_A330\_DIFF\_FR\_A320 REV. 1 DATE: 01.06.2019 DVIATION TRAINING SERVICES FOR TRAINING PURPOSES ONLY 243 STARTING OPERATION - ALTERNATE START DISCRETE LOGIC MECHANICAL & AVIONICS COURSE - T1+T2 (LVL 2&3) 70 - POWER PLANT (RR Trent 700) IGNITION AND STARTING D/O (3) Apr 16, 2013 Page 244 A330 RR Trent 700 TECHNICAL TRAINING MANUAL GCL13151 - GEHT0M0 - FM70DC000000071 B1/B2\_A330\_DIFF\_FR\_A320 REV. 1 DATE: 01.06.2019 DVIATION TRAINING SERVICES FOR TRAINING PURPOSES ONLY 244 STARTING OPERATION - ALTERNATE START DISCRETE LOGIC MECHANICAL & AVIONICS COURSE - T1+T2 (LVL 2&3) 70 - POWER PLANT (RR Trent 700) IGNITION AND STARTING D/O (3) Apr 16, 2013 Page 245 A330 RR Trent 700 TECHNICAL TRAINING MANUAL GCL13151 - GEHT0M0 - FM70DC000000071 B1/B2\_A330\_DIFF\_FR\_A320 REV. 1 DATE: 01.06.2019 DVIATION TRAINING SERVICES FOR TRAINING PURPOSES ONLY 245 IGNITION AND STARTING D/O (3) STARTING OPERATION (continued) AUTO START MANUAL ABORT The automatic and manual start sequence can be interrupted by placing the ENG MASTER switch back to the OFF position. This causes: \- closure of the PRSOV directly, \- closure of the SCV, \- de-energization of the igniters. Turning the ENG START selector switch to NORM or CRANK while the automatic start sequence is already initiated has no effect. MECHANICAL & AVIONICS COURSE - T1+T2 (LVL 2&3) 70 - POWER PLANT (RR Trent 700) IGNITION AND STARTING D/O (3) Apr 16, 2013 Page 246 A330 RR Trent 700 TECHNICAL TRAINING MANUAL GCL13151 - GEHT0M0 - FM70DC000000071 B1/B2\_A330\_DIFF\_FR\_A320 REV. 1 DATE: 01.06.2019 DVIATION TRAINING SERVICES FOR TRAINING PURPOSES ONLY 246 STARTING OPERATION - AUTO START MANUAL ABORT MECHANICAL & AVIONICS COURSE - T1+T2 (LVL 2&3) 70 - POWER PLANT (RR Trent 700) IGNITION AND STARTING D/O (3) Apr 16, 2013 Page 247 A330 RR Trent 700 TECHNICAL TRAINING MANUAL GCL13151 - GEHT0M0 - FM70DC000000071 B1/B2\_A330\_DIFF\_FR\_A320 REV. 1 DATE: 01.06.2019 DVIATION TRAINING SERVICES FOR TRAINING PURPOSES ONLY 247 IGNITION AND STARTING D/O (3) STARTING OPERATION (continued) MANUAL START ABORT BEFORE MASTER LEVER ON In manual start mode, if the ENGine MANual START P/B is released out before the ENG MASTER switch is set to ON, the SCV will close and abort the manual starting sequence. MECHANICAL & AVIONICS COURSE - T1+T2 (LVL 2&3) 70 - POWER PLANT (RR Trent 700) IGNITION AND STARTING D/O (3) Apr 16, 2013 Page 248 A330 RR Trent 700 TECHNICAL TRAINING MANUAL GCL13151 - GEHT0M0 - FM70DC000000071 B1/B2\_A330\_DIFF\_FR\_A320 REV. 1 DATE: 01.06.2019 DVIATION TRAINING SERVICES FOR TRAINING PURPOSES ONLY 248 STARTING OPERATION - MANUAL START ABORT BEFORE MASTER LEVER ON MECHANICAL & AVIONICS COURSE - T1+T2 (LVL 2&3) 70 - POWER PLANT (RR Trent 700) IGNITION AND STARTING D/O (3) Apr 16, 2013 Page 249 A330 RR Trent 700 TECHNICAL TRAINING MANUAL GCL13151 - GEHT0M0 - FM70DC000000071 B1/B2\_A330\_DIFF\_FR\_A320 REV. 1 DATE: 01.06.2019 DVIATION TRAINING SERVICES FOR TRAINING PURPOSES ONLY 249 IGNITION AND STARTING D/O (3) STARTING OPERATION (continued) AUTO START ABORT DUE TO EGT OVERLIMIT On ground only, the EEC can abort an automatic start sequence for the following conditions: \- hot start (EGT overlimit), \- hung start (no acceleration), \- no light up (no ignition), \- stall, \- locked N1 rotor. In case of hot start, stall or no light up, the EEC cuts off the fuel supply and ignition, does an automatic dry cranking and initiates a second start attempt when the EGT is below 150 degrees Celsius. If the second start attempt is not successful, the starting sequence is aborted. A warning is displayed on ECAM and the FAULT light illuminates on the ENG MASTER panel. Set the ENGine MASTER lever to ON position to open the starter valve and the LP valve. When N3 reaches 25%, one ignition system is excited. At each start, the EEC selects alternatively one ignition system A or B. The second igniter can be turned on for a delayed or no light operation. The EGT reaches the EGT overlimit. The EEC starts a dry crank until the EGT reaches 150°C. The EEC restarts the engine with the two igniters A and B. When N3 reaches 50%, the SAV closes and the starter valve is closed. The EEC considers that the start sequence is completed when the engine reaches the minimum idle core speed. Then the rotary selector is turned back to the NORM position. MECHANICAL & AVIONICS COURSE - T1+T2 (LVL 2&3) 70 - POWER PLANT (RR Trent 700) IGNITION AND STARTING D/O (3) Apr 16, 2013 Page 250 A330 RR Trent 700 TECHNICAL TRAINING MANUAL GCL13151 - GEHT0M0 - FM70DC000000071 B1/B2\_A330\_DIFF\_FR\_A320 REV. 1 DATE: 01.06.2019 DVIATION TRAINING SERVICES FOR TRAINING PURPOSES ONLY 250 STARTING OPERATION - AUTO START ABORT DUE TO EGT OVERLIMIT MECHANICAL & AVIONICS COURSE - T1+T2 (LVL 2&3) 70 - POWER PLANT (RR Trent 700) IGNITION AND STARTING D/O (3) Apr 16, 2013 Page 251 A330 RR Trent 700 TECHNICAL TRAINING MANUAL GCL13151 - GEHT0M0 - FM70DC000000071 B1/B2\_A330\_DIFF\_FR\_A320 REV. 1 DATE: 01.06.2019 DVIATION TRAINING SERVICES FOR TRAINING PURPOSES ONLY 251 STARTING OPERATION - AUTO START ABORT DUE TO EGT OVERLIMIT MECHANICAL & AVIONICS COURSE - T1+T2 (LVL 2&3) 70 - POWER PLANT (RR Trent 700) IGNITION AND STARTING D/O (3) Apr 16, 2013 Page 252 A330 RR Trent 700 TECHNICAL TRAINING MANUAL GCL13151 - GEHT0M0 - FM70DC000000071 B1/B2\_A330\_DIFF\_FR\_A320 REV. 1 DATE: 01.06.2019 DVIATION TRAINING SERVICES FOR TRAINING PURPOSES ONLY 252 STARTING OPERATION - AUTO START ABORT DUE TO EGT OVERLIMIT MECHANICAL & AVIONICS COURSE - T1+T2 (LVL 2&3) 70 - POWER PLANT (RR Trent 700) IGNITION AND STARTING D/O (3) Apr 16, 2013 Page 253 A330 RR Trent 700 TECHNICAL TRAINING MANUAL GCL13151 - GEHT0M0 - FM70DC000000071 B1/B2\_A330\_DIFF\_FR\_A320 REV. 1 DATE: 01.06.2019 DVIATION TRAINING SERVICES FOR TRAINING PURPOSES ONLY 253 STARTING OPERATION - AUTO START ABORT DUE TO EGT OVERLIMIT MECHANICAL & AVIONICS COURSE - T1+T2 (LVL 2&3) 70 - POWER PLANT (RR Trent 700) IGNITION AND STARTING D/O (3) Apr 16, 2013 Page 254 A330 RR Trent 700 TECHNICAL TRAINING MANUAL GCL13151 - GEHT0M0 - FM70DC000000071 B1/B2\_A330\_DIFF\_FR\_A320 REV. 1 DATE: 01.06.2019 DVIATION TRAINING SERVICES FOR TRAINING PURPOSES ONLY 254 STARTING OPERATION - AUTO START ABORT DUE TO EGT OVERLIMIT MECHANICAL & AVIONICS COURSE - T1+T2 (LVL 2&3) 70 - POWER PLANT (RR Trent 700) IGNITION AND STARTING D/O (3) Apr 16, 2013 Page 255 A330 RR Trent 700 TECHNICAL TRAINING MANUAL GCL13151 - GEHT0M0 - FM70DC000000071 B1/B2\_A330\_DIFF\_FR\_A320 REV. 1 DATE: 01.06.2019 DVIATION TRAINING SERVICES FOR TRAINING PURPOSES ONLY 255 STARTING OPERATION - AUTO START ABORT DUE TO EGT OVERLIMIT MECHANICAL & AVIONICS COURSE - T1+T2 (LVL 2&3) 70 - POWER PLANT (RR Trent 700) IGNITION AND STARTING D/O (3) Apr 16, 2013 Page 256 A330 RR Trent 700 TECHNICAL TRAINING MANUAL GCL13151 - GEHT0M0 - FM70DC000000071 B1/B2\_A330\_DIFF\_FR\_A320 REV. 1 DATE: 01.06.2019 DVIATION TRAINING SERVICES FOR TRAINING PURPOSES ONLY 256 STARTING OPERATION - AUTO START ABORT DUE TO EGT OVERLIMIT MECHANICAL & AVIONICS COURSE - T1+T2 (LVL 2&3) 70 - POWER PLANT (RR Trent 700) IGNITION AND STARTING D/O (3) Apr 16, 2013 Page 257 A330 RR Trent 700 TECHNICAL TRAINING MANUAL GCL13151 - GEHT0M0 - FM70DC000000071 B1/B2\_A330\_DIFF\_FR\_A320 REV. 1 DATE: 01.06.2019 DVIATION TRAINING SERVICES FOR TRAINING PURPOSES ONLY 257 STARTING OPERATION - AUTO START ABORT DUE TO EGT OVERLIMIT MECHANICAL & AVIONICS COURSE - T1+T2 (LVL 2&3) 70 - POWER PLANT (RR Trent 700) IGNITION AND STARTING D/O (3) Apr 16, 2013 Page 258 A330 RR Trent 700 TECHNICAL TRAINING MANUAL GCL13151 - GEHT0M0 - FM70DC000000071 B1/B2\_A330\_DIFF\_FR\_A320 REV. 1 DATE: 01.06.2019 DVIATION TRAINING SERVICES FOR TRAINING PURPOSES ONLY 258 This Page Intentionally Left Blank MECHANICAL & AVIONICS COURSE - T1+T2 (LVL 2&3) 70 - POWER PLANT (RR Trent 700) IGNITION AND STARTING D/O (3) Apr 16, 2013 Page 259 A330 RR Trent 700 TECHNICAL TRAINING MANUAL GCL13151 - GEHT0M0 - FM70DC000000071 B1/B2\_A330\_DIFF\_FR\_A320 REV. 1 DATE: 01.06.2019 DVIATION TRAINING SERVICES FOR TRAINING PURPOSES ONLY 259 IGNITION AND STARTING D/O (3) CONTINUOUS IGNITION OPERATION Besides the normal automatic or manual start modes, the EEC is able to control continuous ignition depending on cockpit selections, or on an abnormal engine condition detection. In each case, the purpose of the continuous ignition selection is to maintain or recover normal engine operation. Both igniter plugs are energized in the continuous ignition mode and \"IGNITION\" indication is shown on the ECAM memo display. MANUAL SELECTION OF CONTINUOUS IGNITION Continuous ignition may be manually selected when the engine is running by moving the ENG START rotary selector to IGN/START position. AUTOMATIC SELECTION OF CONTINUOUS IGNITION Continuous ignition is set by the EEC while the engine is running if the ENG ANTI ICE P/B is selected ON. The EEC AUTOMATIC RELIGHT function energizes both igniters to give protection from an engine flame-out condition at idle. The automatic relight function is armed when the ENG MASTER switch is ON and the engine has started normally. The EEC then monitors the rate of change of N3 rotor speed at idle and compares it to a minimum datum calculated from the burner pressure (P30). If a flame-out condition is detected, both igniters are continuously energized until 10 seconds after normal engine operation is recovered. The flight crew can initiate an engine QUICK RELIGHT in flight in order to quickly re-start the engine without any action on the ENG START rotary selector. This is done when the ENG MASTER switch is moved from OFF to ON within 30 seconds, and with N3 higher than 10%. For the quick relight function, the EEC ignores the usual automatic start checks and the position of the ENG START rotary selector. It immediately opens the fuel metering valve and PRSOV and energizes both igniter plugs. AUTOMATIC PROTECTION IN CASE OF RAIN/HAIL INGESTION During bad weather conditions, the ingestion of large quantity of water and/or hail in the core engine can cause a sudden decrease of the burner temperature (T30), inducing a risk of engine flame-out. In such conditions, to prevent engine flame-out, the EEC energizes both igniter plugs to get continuous ignition. NOTE: Note: that in addition, the EEC increases the N3 rotor speed in relation to T30 value and opens the core engine bleed valves to send the water into the by-pass casing. Note: the rain/hail ingestion logic is not active on ground to avoid unwanted thrust increase while the aircraft is taxiing. MECHANICAL & AVIONICS COURSE - T1+T2 (LVL 2&3) 70 - POWER PLANT (RR Trent 700) IGNITION AND STARTING D/O (3) Apr 16, 2013 Page 260 A330 RR Trent 700 TECHNICAL TRAINING MANUAL GCL13151 - GEHT0M0 - FM70DC000000071 B1/B2\_A330\_DIFF\_FR\_A320 REV. 1 DATE: 01.06.2019 DVIATION TRAINING SERVICES FOR TRAINING PURPOSES ONLY 260 CONTINUOUS IGNITION OPERATION - MANUAL SELECTION OF CONTINUOUS IGNITION \... AUTOMATIC PROTECTION IN CASE OF RAIN/HAIL INGESTION MECHANICAL & AVIONICS COURSE - T1+T2 (LVL 2&3) 70 - POWER PLANT (RR Trent 700) IGNITION AND STARTING D/O (3) Apr 16, 2013 Page 261 A330 RR Trent 700 TECHNICAL TRAINING MANUAL GCL13151 - GEHT0M0 - FM70DC000000071 B1/B2\_A330\_DIFF\_FR\_A320 REV. 1 DATE: 01.06.2019 DVIATION TRAINING SERVICES FOR TRAINING PURPOSES ONLY 261 IGNITION AND STARTING D/O (3) ENGINE SHUTDOWN Engine shutdown is primarily controlled by closure of the PRSOV. The PRSOV is operated by a solenoid coil directly wired to the ENG/MASTER switch. The EEC also has the capability to shut off the fuel via the FMV when the engine enters the following modes: \- ground autostart, no light, stall, overtemperature, \- ground manual start with an excessive EGT, \- dual FMV position failures. If the ENG/MASTER switch is cycled from the ON to the OFF, then to the ON position, the EEC will control the FMV and the ignition system to ON if the engine speed (N2) is above the flameout protection speed. If the engine is not running, the EEC will obey the pilot requested commands to do the engine starting logic. MECHANICAL & AVIONICS COURSE - T1+T2 (LVL 2&3) 70 - POWER PLANT (RR Trent 700) IGNITION AND STARTING D/O (3) Apr 16, 2013 Page 262 A330 RR Trent 700 TECHNICAL TRAINING MANUAL GCL13151 - GEHT0M0 - FM70DC000000071 B1/B2\_A330\_DIFF\_FR\_A320 REV. 1 DATE: 01.06.2019 DVIATION TRAINING SERVICES FOR TRAINING PURPOSES ONLY 262 ENGINE SHUTDOWN MECHANICAL & AVIONICS COURSE - T1+T2 (LVL 2&3) 70 - POWER PLANT (RR Trent 700) IGNITION AND STARTING D/O (3) Apr 16, 2013 Page 263 A330 RR Trent 700 TECHNICAL TRAINING MANUAL GCL13151 - GEHT0M0 - FM70DC000000071 B1/B2\_A330\_DIFF\_FR\_A320 REV. 1 DATE: 01.06.2019 DVIATION TRAINING SERVICES FOR TRAINING PURPOSES ONLY 263 IGNITION AND STARTING D/O (3) ENGINE MOTORING The FADEC gives two modes of engine motoring: dry and wet. Mode selection is done by the EEC according to the EIVMU digital input which reflects cockpit settings. A dry motoring sequence can be initiated with valid EIVMU data or via the alternate start logic circuit when the EIVMU data is invalid. Wet motoring can only be initiated with valid EIVMU data. DRY MOTORING The engine dry motoring initial configuration is: \- ENG MASTER switch set to OFF position, \- ENG START rotary selector set to NORM position, \- electrical power available, \- air pressure available and above 30 psi. To initiate dry motoring, set the ENG START rotary selector to the CRANK position. The EECs are then powered and the ENGINE system page comes up automatically on the ECAM SD, showing the SCV position and the bleed pressure available to the SCV. When the ENG MAN START P/B is set to the ON position, the associated EEC controls the SCV to open by energizing its solenoid. The pneumatic starter rotates the N3 rotor. Continuous operation of the pneumatic starter is limited; the starter cycle must not exceed 5 minutes. It is possible to interrupt the dry motoring procedure at any time by releasing out the ENG MAN START P/B. MECHANICAL & AVIONICS COURSE - T1+T2 (LVL 2&3) 70 - POWER PLANT (RR Trent 700) IGNITION AND STARTING D/O (3) Apr 16, 2013 Page 264 A330 RR Trent 700 TECHNICAL TRAINING MANUAL GCL13151 - GEHT0M0 - FM70DC000000071 B1/B2\_A330\_DIFF\_FR\_A320 REV. 1 DATE: 01.06.2019 DVIATION TRAINING SERVICES FOR TRAINING PURPOSES ONLY 264 ENGINE MOTORING - DRY MOTORING MECHANICAL & AVIONICS COURSE - T1+T2 (LVL 2&3) 70 - POWER PLANT (RR Trent 700) IGNITION AND STARTING D/O (3) Apr 16, 2013 Page 265 A330 RR Trent 700 TECHNICAL TRAINING MANUAL GCL13151 - GEHT0M0 - FM70DC000000071 B1/B2\_A330\_DIFF\_FR\_A320 REV. 1 DATE: 01.06.2019 DVIATION TRAINING SERVICES FOR TRAINING PURPOSES ONLY 265 ENGINE MOTORING - DRY MOTORING MECHANICAL & AVIONICS COURSE - T1+T2 (LVL 2&3) 70 - POWER PLANT (RR Trent 700) IGNITION AND STARTING D/O (3) Apr 16, 2013 Page 266 A330 RR Trent 700 TECHNICAL TRAINING MANUAL GCL13151 - GEHT0M0 - FM70DC000000071 B1/B2\_A330\_DIFF\_FR\_A320 REV. 1 DATE: 01.06.2019 DVIATION TRAINING SERVICES FOR TRAINING PURPOSES ONLY 266 ENGINE MOTORING - DRY MOTORING MECHANICAL & AVIONICS COURSE - T1+T2 (LVL 2&3) 70 - POWER PLANT (RR Trent 700) IGNITION AND STARTING D/O (3) Apr 16, 2013 Page 267 A330 RR Trent 700 TECHNICAL TRAINING MANUAL GCL13151 - GEHT0M0 - FM70DC000000071 B1/B2\_A330\_DIFF\_FR\_A320 REV. 1 DATE: 01.06.2019 DVIATION TRAINING SERVICES FOR TRAINING PURPOSES ONLY 267 ENGINE MOTORING - DRY MOTORING MECHANICAL & AVIONICS COURSE - T1+T2 (LVL 2&3) 70 - POWER PLANT (RR Trent 700) IGNITION AND STARTING D/O (3) Apr 16, 2013 Page 268 A330 RR Trent 700 TECHNICAL TRAINING MANUAL GCL13151 - GEHT0M0 - FM70DC000000071 B1/B2\_A330\_DIFF\_FR\_A320 REV. 1 DATE: 01.06.2019 DVIATION TRAINING SERVICES FOR TRAINING PURPOSES ONLY 268 This Page Intentionally Left Blank MECHANICAL & AVIONICS COURSE - T1+T2 (LVL 2&3) 70 - POWER PLANT (RR Trent 700) IGNITION AND STARTING D/O (3) Apr 16, 2013 Page 269 A330 RR Trent 700 TECHNICAL TRAINING MANUAL GCL13151 - GEHT0M0 - FM70DC000000071 B1/B2\_A330\_DIFF\_FR\_A320 REV. 1 DATE: 01.06.2019 DVIATION TRAINING SERVICES FOR TRAINING PURPOSES ONLY 269 IGNITION AND STARTING D/O (3) ENGINE MOTORING (continued) WET MOTORING The engine wet motoring initial configuration is the same as for the dry motoring initial configuration, but with engine fuel supply available and the engine ignition C/Bs pulled for safety. To initiate wet motoring, set the ENG START rotary selector to the CRANK position. The EECs are then powered and the ENGINE system page comes up automatically on the ECAM SD, showing the SCV position and the bleed pressure available to the SCV. When the ENG MAN START P/B is set to ON position, the associated EEC controls the SCV to open by energizing its solenoid. The pneumatic starter rotates the N3 rotor. When N3 reaches at least 20%, the associated ENG MASTER switch has to be selected ON. Then, the EEC commands the fuel supply by opening the metering valve and the PRSOV. After fuel flow confirmation, selecting the ENG MASTER switch to OFF stops the fuel flow and initiates a dry motoring procedure. The engine continues to motor without fuel supply to allow the combustion chamber to dry out. The wet motoring sequence can be aborted by placing the ENG MANual START P/B switch in the OFF position or by moving the ENG START rotary selector back to the NORM position. MECHANICAL & AVIONICS COURSE - T1+T2 (LVL 2&3) 70 - POWER PLANT (RR Trent 700) IGNITION AND STARTING D/O (3) Apr 16, 2013 Page 270 A330 RR Trent 700 TECHNICAL TRAINING MANUAL GCL13151 - GEHT0M0 - FM70DC000000071 B1/B2\_A330\_DIFF\_FR\_A320 REV. 1 DATE: 01.06.2019 DVIATION TRAINING SERVICES FOR TRAINING PURPOSES ONLY 270 ENGINE MOTORING - WET MOTORING MECHANICAL & AVIONICS COURSE - T1+T2 (LVL 2&3) 70 - POWER PLANT (RR Trent 700) IGNITION AND STARTING D/O (3) Apr 16, 2013 Page 271 A330 RR Trent 700 TECHNICAL TRAINING MANUAL GCL13151 - GEHT0M0 - FM70DC000000071 B1/B2\_A330\_DIFF\_FR\_A320 REV. 1 DATE: 01.06.2019 DVIATION TRAINING SERVICES FOR TRAINING PURPOSES ONLY 271 ENGINE MOTORING - WET MOTORING MECHANICAL & AVIONICS COURSE - T1+T2 (LVL 2&3) 70 - POWER PLANT (RR Trent 700) IGNITION AND STARTING D/O (3) Apr 16, 2013 Page 272 A330 RR Trent 700 TECHNICAL TRAINING MANUAL GCL13151 - GEHT0M0 - FM70DC000000071 B1/B2\_A330\_DIFF\_FR\_A320 REV. 1 DATE: 01.06.2019 DVIATION TRAINING SERVICES FOR TRAINING PURPOSES ONLY 272 ENGINE MOTORING - WET MOTORING MECHANICAL & AVIONICS COURSE - T1+T2 (LVL 2&3) 70 - POWER PLANT (RR Trent 700) IGNITION AND STARTING D/O (3) Apr 16, 2013 Page 273 A330 RR Trent 700 TECHNICAL TRAINING MANUAL GCL13151 - GEHT0M0 - FM70DC000000071 B1/B2\_A330\_DIFF\_FR\_A320 REV. 1 DATE: 01.06.2019 DVIATION TRAINING SERVICES FOR TRAINING PURPOSES ONLY 273 ENGINE MOTORING - WET MOTORING MECHANICAL & AVIONICS COURSE - T1+T2 (LVL 2&3) 70 - POWER PLANT (RR Trent 700) IGNITION AND STARTING D/O (3) Apr 16, 2013 Page 274 A330 RR Trent 700 TECHNICAL TRAINING MANUAL GCL13151 - GEHT0M0 - FM70DC000000071 B1/B2\_A330\_DIFF\_FR\_A320 REV. 1 DATE: 01.06.2019 DVIATION TRAINING SERVICES FOR TRAINING PURPOSES ONLY 274 ENGINE MOTORING - WET MOTORING MECHANICAL & AVIONICS COURSE - T1+T2 (LVL 2&3) 70 - POWER PLANT (RR Trent 700) IGNITION AND STARTING D/O (3) Apr 16, 2013 Page 275 A330 RR Trent 700 TECHNICAL TRAINING MANUAL GCL13151 - GEHT0M0 - FM70DC000000071 B1/B2\_A330\_DIFF\_FR\_A320 REV. 1 DATE: 01.06.2019 DVIATION TRAINING SERVICES FOR TRAINING PURPOSES ONLY 275 AIRFLOW CONTROL SYSTEM D/O (3) GENERAL The function of the airflow control system is to fulfill a stable airflow through the Intermediate Pressure (IP) and High Pressure (HP) compressors at any thrust ranges to avoid engine stall or surge. It also controls the volume of airflow through the IP and HP compressors. To control the airflow, the system uses: \- Variable Inlet Guide Vanes (VIGVs) and two stages of IP compressor Variable Stator Vanes (VSVs), \- four IP bleed valves in line with stage 8 of the IP compressor, \- three HP bleed valves in line with stage 3 of the HP compressor. The airflow control system is controlled by the Engine Electronic Controller (EEC). MECHANICAL & AVIONICS COURSE - T1+T2 (LVL 2&3) 70 - POWER PLANT (RR Trent 700) AIRFLOW CONTROL SYSTEM D/O (3) Apr 16, 2013 Page 276 A330 RR Trent 700 TECHNICAL TRAINING MANUAL GCL13151 - GEHT0M0 - FM70D4000000071 B1/B2\_A330\_DIFF\_FR\_A320 REV. 1 DATE: 01.06.2019 DVIATION TRAINING SERVICES FOR TRAINING PURPOSES ONLY 276 GENERAL MECHANICAL & AVIONICS COURSE - T1+T2 (LVL 2&3) 70 - POWER PLANT (RR Trent 700) AIRFLOW CONTROL SYSTEM D/O (3) Apr 16, 2013 Page 277 A330 RR Trent 700 TECHNICAL TRAINING MANUAL GCL13151 - GEHT0M0 - FM70D4000000071 B1/B2\_A330\_DIFF\_FR\_A320 REV. 1 DATE: 01.06.2019 DVIATION TRAINING SERVICES FOR TRAINING PURPOSES ONLY 277 AIRFLOW CONTROL SYSTEM D/O (3) VIGV/VSV DESCRIPTION The IP compressor VIGV/VSV system includes: \- one VSV control unit, \- two VSV actuators, \- VIGV/VSV actuating mechanism. VSV CONTROL UNIT The VSV control unit is used to control the VSV actuators position using fuel servo pressure. It is installed on the lower left side of the compressor intermediate case. The VSV control unit mainly has a torque motor and a control servo valve which control the flow of servo fuel to and from the VSV actuators. VSV ACTUATORS Two VSV actuators are installed 180 degrees apart on each side of the engine horizontal center line. Each actuator controls the movement of the VIGVs and VSVs through the VIGV/VSV actuating mechanism. They are actuated by servo fuel pressure from the VSV control unit. When the actuator retracts, the VSVs open and when it extends, the VSVs close. Each actuator has a Linear Variable Differential Transducer (LVDT) for position feedback. The LH actuator sends the LVDT information to EEC channel A and, respectively, the RH actuator sends the LVDT information to EEC channel B. Each actuator also has a fuel drain tube. VIGV/VSV ACTUATING MECHANISM The VIGV/VSV actuating mechanism is installed around the LP/IP bearing support assembly and the IP compressor case. It changes the linear movement of the actuator to the angular movement of the VIGVs and VSVs. This actuating system includes rods, bellcranks and unison rings. VIGV/VSV OPERATION The VIGVs and VSVs are adjusted during starting, acceleration, deceleration and surge conditions to maintain the correct operation of the IP and the HP compressors. The EEC uses IP compressor shaft speed (N2) and the IP compressor inlet temperature (T24) signals to control the angular position of the VIGVs and VSVs. If these signals are not available the EEC uses signals based on a pressure ratio to control the VIGVs and VSVs. Each LVDT sends its actuator position feedback to a different EEC channel. If a failure of the electrical supply occurs, the VIGVs and VSVs are moved to their failsafe position (closed position), corresponding to a low speed position. MECHANICAL & AVIONICS COURSE - T1+T2 (LVL 2&3) 70 - POWER PLANT (RR Trent 700) AIRFLOW CONTROL SYSTEM D/O (3) Apr 16, 2013 Page 278 A330 RR Trent 700 TECHNICAL TRAINING MANUAL GCL13151 - GEHT0M0 - FM70D4000000071 B1/B2\_A330\_DIFF\_FR\_A320 REV. 1 DATE: 01.06.2019 DVIATION TRAINING SERVICES FOR TRAINING PURPOSES ONLY 278 VIGV/VSV DESCRIPTION & VIGV/VSV OPERATION MECHANICAL & AVIONICS COURSE - T1+T2 (LVL 2&3) 70 - POWER PLANT (RR Trent 700) AIRFLOW CONTROL SYSTEM D/O (3) Apr 16, 2013 Page 279 A330 RR Trent 700 TECHNICAL TRAINING MANUAL GCL13151 - GEHT0M0 - FM70D4000000071 B1/B2\_A330\_DIFF\_FR\_A320 REV. 1 DATE: 01.06.2019 DVIATION TRAINING SERVICES FOR TRAINING PURPOSES ONLY 279 AIRFLOW CONTROL SYSTEM D/O (3) IP & HP BLEED VALVES DESCRIPTION Seven bleed valves are installed around the IP and HP compressor. These valves are controlled via a bleed valve solenoid unit. IP & HP BLEED VALVES Four IP bleed valves are installed on and around the compressor intermediate case and aligned with stage 8 of the IP compressor. Three HP bleed valves are installed near the front of the combustion outer case and aligned with stage 3 of the HP compressor. Two HP bleed valves, HP3.3 and HP3.2, are installed at the top right and bottom right of the case. The third one, HP3.1, is located at the bottom left of the case. Each IP/HP bleed valve has a perforated silencer/seal assembly that seals the valve against the flat inner surface of the thrust reverser cowl. The silencer goes through an opening in the thrust reverser cowl to discharge the compressor air in the fan stream. The valves have internal chambers and springs for operation and are supplied with HP3 air muscle pressure from the bleed valve solenoid unit through its solenoid valves. BLEED VALVE SOLENOID UNIT The bleed valve solenoid unit is composed of five solenoid valves attached together to make one unit and it is installed on RH side in front of the compressor intermediate case. Access is gained by opening the thrust reverser cowls and removing the right center gas generator fairing. The four IP bleed valves are operated in pairs by two of the solenoid valves. The three HP bleed valves are operated by the remaining three solenoid valves. The bleed valve solenoid unit has a pneumatic connector for HP3 air supply with two electrical connectors for EEC channel A and B electrical control. Each solenoid valve has two coils: one linked to EEC channel A and the other to channel B. It can supply or stop HP3 servo air to open or close a bleed valve. MECHANICAL & AVIONICS COURSE - T1+T2 (LVL 2&3) 70 - POWER PLANT (RR Trent 700) AIRFLOW CONTROL SYSTEM D/O (3) Apr 16, 2013 Page 280 A330 RR Trent 700 TECHNICAL TRAINING MANUAL GCL13151 - GEHT0M0 - FM70D4000000071 B1/B2\_A330\_DIFF\_FR\_A320 REV. 1 DATE: 01.06.2019 DVIATION TRAINING SERVICES FOR TRAINING PURPOSES ONLY 280 IP & HP BLEED VALVES DESCRIPTION - IP & HP BLEED VALVES & BLEED VALVE SOLENOID UNIT MECHANICAL & AVIONICS COURSE - T1+T2 (LVL 2&3) 70 - POWER PLANT (RR Trent 700) AIRFLOW CONTROL SYSTEM D/O (3) Apr 16, 2013 Page 281 A330 RR Trent 700 TECHNICAL TRAINING MANUAL GCL13151 - GEHT0M0 - FM70D4000000071 B1/B2\_A330\_DIFF\_FR\_A320 REV. 1 DATE: 01.06.2019 DVIATION TRAINING SERVICES FOR TRAINING PURPOSES ONLY 281 AIRFLOW CONTROL SYSTEM D/O (3) IP & HP BLEED VALVES OPERATION IP and HP bleed valves are controlled to open during engine starting, at low engine speed and during specific conditions. They are used to discharge a proportion of IP or HP compressor air into the engine by-pass casing. The scheduling of the bleed valves is computed by the EEC and controlled through the bleed valve solenoid unit. Each solenoid valve is connected to both channels of the EEC. Each valve is independently operated as a function of N2 and IP compressor inlet temperature (T24) for the IP bleed valves, and as a function of N3 and T24 for the HP bleed valves. If these signals are not available the EEC uses signals based on a pressure ratio. The EEC can also use signals from the Throttle Resolver Angle (TRA) to set each bleed valve. When one HP/IP bleed valve solenoid is de-energized, HP3 air muscle pressure forces the corresponding valve to open in addition to the spring load. When the solenoid is energized, HP3 air from the servo chamber is released through the solenoid valve. This lets the compressor air pressure close the bleed valves. With no electrical control signal, the bleed valves are maintained in the open position by spring load. MECHANICAL & AVIONICS COURSE - T1+T2 (LVL 2&3) 70 - POWER PLANT (RR Trent 700) AIRFLOW CONTROL SYSTEM D/O (3) Apr 16, 2013 Page 282 A330 RR Trent 700 TECHNICAL TRAINING MANUAL GCL13151 - GEHT0M0 - FM70D4000000071 B1/B2\_A330\_DIFF\_FR\_A320 REV. 1 DATE: 01.06.2019 DVIATION TRAINING SERVICES FOR TRAINING PURPOSES ONLY 282 IP & HP BLEED VALVES OPERATION MECHANICAL & AVIONICS COURSE - T1+T2 (LVL 2&3) 70 - POWER PLANT (RR Trent 700) AIRFLOW CONTROL SYSTEM D/O (3) Apr 16, 2013 Page 283 A330 RR Trent 700 TECHNICAL TRAINING MANUAL GCL13151 - GEHT0M0 - FM70D4000000071 B1/B2\_A330\_DIFF\_FR\_A320 REV. 1 DATE: 01.06.2019 DVIATION TRAINING SERVICES FOR TRAINING PURPOSES ONLY 283 IP & HP BLEED VALVES OPERATION MECHANICAL & AVIONICS COURSE - T1+T2 (LVL 2&3) 70 - POWER PLANT (RR Trent 700) AIRFLOW CONTROL SYSTEM D/O (3) Apr 16, 2013 Page 284 A330 RR Trent 700 TECHNICAL TRAINING MANUAL GCL13151 - GEHT0M0 - FM70D4000000071 B1/B2\_A330\_DIFF\_FR\_A320 REV. 1 DATE: 01.06.2019 DVIATION TRAINING SERVICES FOR TRAINING PURPOSES ONLY 284 This Page Intentionally Left Blank MECHANICAL & AVIONICS COURSE - T1+T2 (LVL 2&3) 70 - POWER PLANT (RR Trent 700) AIRFLOW CONTROL SYSTEM D/O (3) Apr 16, 2013 Page 285 A330 RR Trent 700 TECHNICAL TRAINING MANUAL GCL13151 - GEHT0M0 - FM70D4000000071 B1/B2\_A330\_DIFF\_FR\_A320 REV. 1 DATE: 01.06.2019 DVIATION TRAINING SERVICES FOR TRAINING PURPOSES ONLY 285 ENGINE COOLING SYSTEM D/O (3) GENERAL Air is supplied from different sources to decrease the engine temperature through internal and external cooling. The air used to cool and pressurize the different engine compartments is supplied through external tubes and through internal passages. Internal compartments that are at different pressures are isolated from each other by labyrinth seals. For cooling, the nacelle is divided into 3 different zones. Cooling airflow is also provided for the Full Authority Digital Engine Control (FADEC) electronic units, located in the electronic unit protection box. MECHANICAL & AVIONICS COURSE - T1+T2 (LVL 2&3) 70 - POWER PLANT (RR Trent 700) ENGINE COOLING SYSTEM D/O (3) Apr 16, 2013 Page 286 A330 RR Trent 700 TECHNICAL TRAINING MANUAL GCL13151 - GEHT0M0 - FM70D5000000071 B1/B2\_A330\_DIFF\_FR\_A320 REV. 1 DATE: 01.06.2019 DVIATION TRAINING SERVICES FOR TRAINING PURPOSES ONLY 286 GENERAL MECHANICAL & AVIONICS COURSE - T1+T2 (LVL 2&3) 70 - POWER PLANT (RR Trent 700) ENGINE COOLING SYSTEM D/O (3) Apr 16, 2013 Page 287 A330 RR Trent 700 TECHNICAL TRAINING MANUAL GCL13151 - GEHT0M0 - FM70D5000000071 B1/B2\_A330\_DIFF\_FR\_A320 REV. 1 DATE: 01.06.2019 DVIATION TRAINING SERVICES FOR TRAINING PURPOSES ONLY 287 ENGINE COOLING SYSTEM D/O (3) NACELLE COOLING D/O The powerplant is divided into three primary fire-resistant zones isolated from each other by fireproof bulkheads and seals. These zones are supplied with cooling airflow in order to: \- keep the temperature in the cowls at a satisfactory level, \- decrease the temperature of the main fuel and oil accessory units, \- prevent the accumulation of hazardous vapours. Zone 1 - Fan Case Compartment: The zone 1 is ventilated by ram air ducted through an opening on top of the air intake cowl, The ventilation air is exhausted through an opening in the lower part of the right hand fan cowl door. Zone 2 - Intermediate Compressor Case Compartment: The zone 2 is ventilated by air from the LP compressor that enters through two holes at the top rear of the zone and then flows around the zone. The ventilation air is exhausted at the bottom of the zone into the by-pass casing through two holes in the front of the engine core fairings. Zone 3 - Core Engine Compartment: The zone 3 is ventilated by air from the LP compressor that enters through ducts in the inner fixed structure of the \'C\' ducts. The ventilation air is exhausted through an exit at the bottom of the \'C\' duct longitudinal beam. At the bottom of the core engine, in the front flange of the combustion outer case, there is a thermocouple probe installed and electrically connected to the EEC for Nacelle temperature indicating function. Nacelle temperature is indicated: \- in green color in normal operation \- in green pulsing color if the temperature exceeds 260 DEG.C (500 DEG.F) (High nacelle temperature advisory). A separate fire-resistant and cooling zone is the electronic unit protection box installed on the left fan case. The following FADEC electronic boxes are installed inside a protection box: \- the Engine Electronic Controller (EEC), \- the Power Control Unit (PCU), \- the Overspeed Protection Unit (OPU). The ventilation and cooling of the protection box is done by using external air from the air intake cowl that is ducted across the LP compressor case to the protection box. The cooling air flows out from the protection box and is ducted to the inlet of the LP compressor. MECHANICAL & AVIONICS COURSE - T1+T2 (LVL 2&3) 70 - POWER PLANT (RR Trent 700) ENGINE COOLING SYSTEM D/O (3) Apr 16, 2013 Page 288 A330 RR Trent 700 TECHNICAL TRAINING MANUAL GCL13151 - GEHT0M0 - FM70D5000000071 B1/B2\_A330\_DIFF\_FR\_A320 REV. 1 DATE: 01.06.2019 DVIATION TRAINING SERVICES FOR TRAINING PURPOSES ONLY 288 NACELLE COOLING D/O MECHANICAL & AVIONICS COURSE - T1+T2 (LVL 2&3) 70 - POWER PLANT (RR Trent 700) ENGINE COOLING SYSTEM D/O (3) Apr 16, 2013 Page 289 A330 RR Trent 700 TECHNICAL TRAINING MANUAL GCL13151 - GEHT0M0 - FM70D5000000071 B1/B2\_A330\_DIFF\_FR\_A320 REV. 1 DATE: 01.06.2019 DVIATION TRAINING SERVICES FOR TRAINING PURPOSES ONLY 289 NACELLE COOLING D/O MECHANICAL & AVIONICS COURSE - T1+T2 (LVL 2&3) 70 - POWER PLANT (RR Trent 700) ENGINE COOLING SYSTEM D/O (3) Apr 16, 2013 Page 290 A330 RR Trent 700 TECHNICAL TRAINING MANUAL GCL13151 - GEHT0M0 - FM70D5000000071 B1/B2\_A330\_DIFF\_FR\_A320 REV. 1 DATE: 01.06.2019 DVIATION TRAINING SERVICES FOR TRAINING PURPOSES ONLY 290 This Page Intentionally Left Blank MECHANICAL & AVIONICS COURSE - T1+T2 (LVL 2&3) 70 - POWER PLANT (RR Trent 700) ENGINE COOLING SYSTEM D/O (3) Apr 16, 2013 Page 291 A330 RR Trent 700 TECHNICAL TRAINING MANUAL GCL13151 - GEHT0M0 - FM70D5000000071 B1/B2\_A330\_DIFF\_FR\_A320 REV. 1 DATE: 01.06.2019 DVIATION TRAINING SERVICES FOR TRAINING PURPOSES ONLY 291 ENGINE COOLING SYSTEM D/O (3) TURBINE IMPINGEMENT COOLING (TIC) D/O The TIC system is designed to maximize the turbine efficiency. During engine operation, the turbine cases heat up and expand at a higher rate than the turbine blades. This expansion increases the blade tip clearance. The TIC system supplies fan air to both the IP and LP turbine cases to control the IP turbine blade tip clearances and cool the LP case. The TIC valve is controlled by the EEC. MECHANICAL & AVIONICS COURSE - T1+T2 (LVL 2&3) 70 - POWER PLANT (RR Trent 700) ENGINE COOLING SYSTEM D/O (3) Apr 16, 2013 Page 292 A330 RR Trent 700 TECHNICAL TRAINING MANUAL GCL13151 - GEHT0M0 - FM70D5000000071 B1/B2\_A330\_DIFF\_FR\_A320 REV. 1 DATE: 01.06.2019 DVIATION TRAINING SERVICES FOR TRAINING PURPOSES ONLY 292 TURBINE IMPINGEMENT COOLING (TIC) D/O MECHANICAL & AVIONICS COURSE - T1+T2 (LVL 2&3) 70 - POWER PLANT (RR Trent 700) ENGINE COOLING SYSTEM D/O (3) Apr 16, 2013 Page 293 A330 RR Trent 700 TECHNICAL TRAINING MANUAL GCL13151 - GEHT0M0 - FM70D5000000071 B1/B2\_A330\_DIFF\_FR\_A320 REV. 1 DATE: 01.06.2019 DVIATION TRAINING SERVICES FOR TRAINING PURPOSES ONLY 293 ENGINE COOLING SYSTEM D/O (3) TURBINE IMPINGEMENT COOLING (TIC) D/O (continued) DESCRIPTION The TIC system is composed of: \- a solenoid valve, \- an actuating ram, \- the TIC valve, \- a coolingmanifold. OPERATION The solenoid valve is attached to the bottom of the intermediate case. It is electrically controlled by the EEC and supplied with HP3 air. When energized, the solenoid valve sends HP3 air pressure to the actuating ram (piston). The TIC is only active during stable cruise mode and the EEC control is based on Engine Pressure Ratio (EPR) and Mach number, or N1 and A/C altitude. The actuating ram is attached to the HP/IP turbine casing and is pneumatically operated by the HP3 air pressure from the solenoid valve. The TIC valve is operated by the actuating ram, and is spring loaded closed. The valve is fully closed when the actuating ram is retracted, and it goes to the fully open position when the actuating ram is extended. The cooling air is directed to the IP turbine casing through an air manifold with two lines of rows drilled at equal distance around its inner surface. A liner assembly is installed around the LP turbine case to let the cooling air from the manifold flow around it. MECHANICAL & AVIONICS COURSE - T1+T2 (LVL 2&3) 70 - POWER PLANT (RR Trent 700) ENGINE COOLING SYSTEM D/O (3) Apr 16, 2013 Page 294 A330 RR Trent 700 TECHNICAL TRAINING MANUAL GCL13151 - GEHT0M0 - FM70D5000000071 B1/B2\_A330\_DIFF\_FR\_A320 REV. 1 DATE: 01.06.2019 DVIATION TRAINING SERVICES FOR TRAINING PURPOSES ONLY 294 TURBINE IMPINGEMENT COOLING (TIC) D/O - DESCRIPTION & OPERATION MECHANICAL & AVIONICS COURSE - T1+T2 (LVL 2&3) 70 - POWER PLANT (RR Trent 700) ENGINE COOLING SYSTEM D/O (3) Apr 16, 2013 Page 295 A330 RR Trent 700 TECHNICAL TRAINING MANUAL GCL13151 - GEHT0M0 - FM70D5000000071 B1/B2\_A330\_DIFF\_FR\_A320 REV. 1 DATE: 01.06.2019 DVIATION TRAINING SERVICES FOR TRAINING PURPOSES ONLY 295 THRUST CONTROL D/O (3) GENERAL The engine thrust is controlled by the Engine Electronic Controller (EEC). The engine thrust can be set: \- Manually by the throttle control lever or, \- Automatically by the Auto Flight System (AFS). The main thrust control parameter is the Engine Pressure Ratio (EPR). The EPR is replaced by N1 (LP rotor) in reverse thrust or in backup mode. The EPR is calculated by the EEC as a function of the total pressure at the engine inlet P20 and the total pressure at the core engine outlet P50. It is expressed as a ratio: EPR = P50/P20. The throttle control lever position is also used by the EEC to define the thrust limit mode and to compute the EPR rating limit. The thrust limit mode and the EPR rating limit are used by the AFS in autothrust mode. The thrust control parameters are displayed on the ECAM E/WD: \- EPR (actual), \- EPR (limit), \- Thrust Limit mode, \- N1. MECHANICAL & AVIONICS COURSE - T1+T2 (LVL 2&3) 70 - POWER PLANT (RR Trent 700) THRUST CONTROL D/O (3) Apr 16, 2013 Page 296 A330 RR Trent 700 TECHNICAL TRAINING MANUAL GCL13151 - GEHT0M0 - FM70DG000000071 B1/B2\_A330\_DIFF\_FR\_A320 REV. 1 DATE: 01.06.2019 DVIATION TRAINING SERVICES FOR TRAINING PURPOSES ONLY 296 GENERAL MECHANICAL & AVIONICS COURSE - T1+T2 (LVL 2&3) 70 - POWER PLANT (RR Trent 700) THRUST CONTROL D/O (3) Apr 16, 2013 Page 297 A330 RR Trent 700 TECHNICAL TRAINING MANUAL GCL13151 - GEHT0M0 - FM70DG000000071 B1/B2\_A330\_DIFF\_FR\_A320 REV. 1 DATE: 01.06.2019 DVIATION TRAINING SERVICES FOR TRAINING PURPOSES ONLY 297 GENERAL MECHANICAL & AVIONICS COURSE - T1+T2 (LVL 2&3) 70 - POWER PLANT (RR Trent 700) THRUST CONTROL D/O (3) Apr 16, 2013 Page 298 A330 RR Trent 700 TECHNICAL TRAINING MANUAL GCL13151 - GEHT0M0 - FM70DG000000071 B1/B2\_A330\_DIFF\_FR\_A320 REV. 1 DATE: 01.06.2019 DVIATION TRAINING SERVICES FOR TRAINING PURPOSES ONLY 298 This Page Intentionally Left Blank MECHANICAL & AVIONICS COURSE - T1+T2 (LVL 2&3) 70 - POWER PLANT (RR Trent 700) THRUST CONTROL D/O (3) Apr 16, 2013 Page 299 A330 RR Trent 700 TECHNICAL TRAINING MANUAL GCL13151 - GEHT0M0 - FM70DG000000071 B1/B2\_A330\_DIFF\_FR\_A320 REV. 1 DATE: 01.06.2019 DVIATION TRAINING SERVICES FOR TRAINING PURPOSES ONLY 299 THRUST CONTROL D/O (3) GENERAL (continued) MANUAL THRUST The engines are in manual mode, provided the Autothrust (A/THR) function is not engaged, or is engaged and not active (throttle levers not in the A/THR operating range). In these conditions, each engine thrust is controlled by the position of its throttle control lever. To control the thrust, the pilot moves the throttle control lever between the IDLE and TOGA (Take Off Go Around) positions. Each position within these limits is related to a predicted (or commanded) EPR shown as a blue circle on the EPR indicator. At the end of the thrust adjustment, the actual EPR (green needle and digital indication) is aligned with the predicted/commanded EPR value. When the throttle control lever is in a detent, the related EPR is equal to the EPR rating limit calculated by the EEC. Between idle and max power, there are 2 detent positions: \- CL (Climb) \- FLX/MCT (Flex/Max Continuous Thrust). If the EEC finds that the EPR is not accurate, the EEC automatically goes back to N1 MODE: the EEC uses the N1 parameter to calculate the thrust. The N1 mode can also be set manually by the operation of the N1 MODE pushbutton on the cockpit overhead panel. In the N1 MODE, the predicted N1 related to the thrust lever position is shown by a blue circle. An amber index shows the N1 limit value of the TOGA or REV mode. During take-off the engine thrust is manually set at FLX/MCT or above (TOGA). The maximum TOGA thrust is calculated by the EEC based on ambient conditions and is displayed on the E/WD as soon as one engine is started. In flight, the FLX/MCT detent is used for a single engine operation. Autothrust is available in this configuration. The pilot has the option to use less than the maximum thrust (40% thrust reduction) for takeoff in specific conditions (altitude, temperature, A/C weight, runway length, etc.). This is known as a FLEX Takeoff. The pilot must consult the Flight Manual (FM) and enter a FLEX TEMP (fictitious temperature between -128 °C and +128 °C) into the Flight Management System (FMS) through the MCDU. The throttle control lever is in the FLX/MCT detent position and a new lower thrust limit will be displayed on the E/WD. MECHANICAL & AVIONICS COURSE - T1+T2 (LVL 2&3) 70 - POWER PLANT (RR Trent 700) THRUST CONTROL D/O (3) Apr 16, 2013 Page 300 A330 RR Trent 700 TECHNICAL TRAINING MANUAL GCL13151 - GEHT0M0 - FM70DG000000071 B1/B2\_A330\_DIFF\_FR\_A320 REV. 1 DATE: 01.06.2019 DVIATION TRAINING SERVICES FOR TRAINING PURPOSES ONLY 300 GENERAL - MANUAL THRUST MECHANICAL & AVIONICS COURSE - T1+T2 (LVL 2&3) 70 - POWER PLANT (RR Trent 700) THRUST CONTROL D/O (3) Apr 16, 2013 Page 301 A330 RR Trent 700 TECHNICAL TRAINING MANUAL GCL13151 - GEHT0M0 - FM70DG000000071 B1/B2\_A330\_DIFF\_FR\_A320 REV. 1 DATE: 01.06.2019 DVIATION TRAINING SERVICES FOR TRAINING PURPOSES ONLY 301 GENERAL - MANUAL THRUST MECHANICAL & AVIONICS COURSE - T1+T2 (LVL 2&3) 70 - POWER PLANT (RR Trent 700) THRUST CONTROL D/O (3) Apr 16, 2013 Page 302 A330 RR Trent 700 TECHNICAL TRAINING MANUAL GCL13151 - GEHT0M0 - FM70DG000000071 B1/B2\_A330\_DIFF\_FR\_A320 REV. 1 DATE: 01.06.2019 DVIATION TRAINING SERVICES FOR TRAINING PURPOSES ONLY 302 This Page Intentionally Left Blank MECHANICAL & AVIONICS COURSE - T1+T2 (LVL 2&3) 70 - POWER PLANT (RR Trent 700) THRUST CONTROL D/O (3) Apr 16, 2013 Page 303 A330 RR Trent 700 TECHNICAL TRAINING MANUAL GCL13151 - GEHT0M0 - FM70DG000000071 B1/B2\_A330\_DIFF\_FR\_A320 REV. 1 DATE: 01.06.2019 DVIATION TRAINING SERVICES FOR TRAINING PURPOSES ONLY 303 THRUST CONTROL D/O (3) AUTOMATIC THRUST A/THR is a function of the FMS. The FMS includes the Flight Management Guidance and Envelope Computers (FMGECs), the Flight Control Unit (FCU) and, the MCDUs. The FCU is installed on the glareshield panel and the MCDUs are installed on the center pedestal. They are the interfaces between the flight crew and the FMGECs. The FCU is equipped with an A/THR pushbutton to engage or to disengage the autothrust. When ENGAGED, the A/THR may be ACTIVE or NOT ACTIVE. The A/THR is ACTIVE when the thrust control levers are in the A/THR range (above IDLE to FLX/MCT detent), The A/THR is NOT ACTIVE when the thrust control levers are not in the A/THR range (at IDLE stop or above the FLX/MCT detent). The A/THR may also be disengaged using the Instinctive Disconnect Switch on the throttle control levers. The MCDU is used to enter the flight plan and FLEX TAKEOFF Temperature. If equipped with the optional capability, derated take off and derated climb are also entered through the MCDU. Alpha Floor (A.FLOOR) protection is used to prevent an aircraft stall. It is automatically activated by the FMGEC if the aircraft reaches an exccessive angle-of-attack. When activated, the maximum engine thrust (TOGA) is automatically commanded regardless of the throttle control lever position, with the autothrust engaged or not. AUTOMATIC THRUST ENGAGEMENT The A/THR pushbutton lets engage, or disconnect the A/THR. It comes on green when the A/THR is engaged. The A/THR is active when it is engaged and the thrust levers are set in the A/THR operating range (between IDLE and CL). Note that during take-off, the A/THR function is engaged but not active. In case of reversion to N1 mode on one engine, the A/THR is deactivated. The A/THR system can operate with or without the AP. If the A/THR is working with the AP, the FMGEC commands the thrust according to the AP logic. The thrust is limited by the position of the throttle lever. (For example, when the throttle levers are set to CL, A/THR can command a thrust between IDLE and CL). If the A/THR is working without the AP, the A/THR always controls the aircraft speed. The thrust is always limited by the position of the throttle lever. In case of A/THR failure, the A.FLOOR protection is lost. A/THR MODE DISCONNECTION Standard disconnection, by pushing one of the instinctive disconnect Pushbuttons (P/Bs) on the throttle levers, the A/THR mode is disconnected and the thrust is set in manual mode, according to the actual throttle control lever position. If instinctive disconnect P/B is pushed and held for more than 15 seconds, all A/THR functions including A.FLOOR protection are lost for the flight in progress. Setting all throttle levers to IDLE detent results in A/THR disconnection. Non-standard disconnection results in activation of the thrust lock function when: \- the A/THR pushbutton is released out while A/THR is engaged or active, or \- the system looses one of the engagement conditions, or \- the throttle lever is set at CL or at MCT when one engine is inoperative. The Thrust lock function is locked or frozen at the level set prior to the non standard disconnection. Moving the throttle levers out of CL (or MCT with one engine inoperative) cancels the thrust lock function, and the thrust reverts to manual control. MECHANICAL & AVIONICS COURSE - T1+T2 (LVL 2&3) 70 - POWER PLANT (RR Trent 700) THRUST CONTROL D/O (3) Apr 16, 2013 Page 304 A330 RR Trent 700 TECHNICAL TRAINING MANUAL GCL13151 - GEHT0M0 - FM70DG000000071 B1/B2\_A330\_DIFF\_FR\_A320 REV. 1 DATE: 01.06.2019 DVIATION TRAINING SERVICES FOR TRAINING PURPOSES ONLY 304 AUTOMATIC THRUST - AUTOMATIC THRUST ENGAGEMENT & A/THR MODE DISCONNECTION MECHANICAL & AVIONICS COURSE - T1+T2 (LVL 2&3) 70 - POWER PLANT (RR Trent 700) THRUST CONTROL D/O (3) Apr 16, 2013 Page 305 A330 RR Trent 700 TECHNICAL TRAINING MANUAL GCL13151 - GEHT0M0 - FM70DG000000071 B1/B2\_A330\_DIFF\_FR\_A320 REV. 1 DATE: 01.06.2019 DVIATION TRAINING SERVICES FOR TRAINING PURPOSES ONLY 305 THRUST CONTROL D/O (3) EPR MODE OPERATION EPR mode is the normal thrust control mode. The EEC computes the EPR command as a function of: \- TRA, \- altitude or static pressure (Ps or P0), \- total air pressure (Pt or P20), \- P50 \- Total Air Temperature (TAT or T20), \- mach number, \- bleed demand. The EPR rating limit is computed by the EEC, depending on the TRA, and is displayed in green on the upper ECAM. The EPR limit value displayed is the highest EPR limit value of the two engines. N1 MODE OPERATION If the EEC is unable to compute EPR, the engine thrust control automatically reverts to N1 mode. The N1 mode can also be commanded manually by selecting the ENG N1 MODE P/B ON. Upon automatic reversion to N1 mode, a thrust equivalent to that achieved in EPR mode is set and locked by the EEC until the operator changes the throttle control lever position. An ECAM message will be generated, requesting that the operator select BOTH engines to N1 mode keep the throttle control levers matched. There are two N1 modes for thrust control. Depending on the failure conditions leading to EPR mode loss, the EEC will revert to either rated N1 or unrated N1 mode. RATED N1 MODE An automatic reversion to rated N1 mode occurs, when: \- engine P20 and / or P50 are not available, \- engine P20 is lower than Air Data/Inertial Reference Units (ADIRUs) Pt. The EEC computes an EPR command, depending on the TLA, then converts it to an N1 command as a function of Mach number. The displayed N1 rating limit is only computed in the N1 rated mode, according to the TRA. The Max thrust and throttle control lever position indications shift from the EPR indicator to the N1 indicator. UNRATED N1 MODE An automatic reversion to unrated N1 mode occurs, when: \- engine P20 and ADIRUs Pt are not available, or \- engine T20 and ADIRUs TAT are not available, or \- engine P0 and ADIRUs Ps are not available. N1 command is defined as a function of the TLA and altitude. N1 is limited by the EEC to either the smaller of N1 max or N1 redline, depending on T20 availability. The N1 rating limit, predicted N1 (N1 TLA) and N1 MAX ECAM indications are lost. Basically, there is no engine limit protection in this mode. MECHANICAL & AVIONICS COURSE - T1+T2 (LVL 2&3) 70 - POWER PLANT (RR Trent 700) THRUST CONTROL D/O (3) Apr 16, 2013 Page 306 A330 RR Trent 700 TECHNICAL TRAINING MANUAL GCL13151 - GEHT0M0 - FM70DG000000071 B1/B2\_A330\_DIFF\_FR\_A320 REV. 1 DATE: 01.06.2019 DVIATION TRAINING SERVICES FOR TRAINING PURPOSES ONLY 306 EPR MODE OPERATION & N1 MODE OPERATION MECHANICAL & AVIONICS COURSE - T1+T2 (LVL 2&3) 70 - POWER PLANT (RR Trent 700) THRUST CONTROL D/O (3) Apr 16, 2013 Page 307 A330 RR Trent 700 TECHNICAL TRAINING MANUAL GCL13151 - GEHT0M0 - FM70DG000000071 B1/B2\_A330\_DIFF\_FR\_A320 REV. 1 DATE: 01.06.2019 DVIATION TRAINING SERVICES FOR TRAINING PURPOSES ONLY 307 THRUST CONTROL D/O (3) THROTTLE CONTROL LEVER ASSEMBLY Each throttle control lever mechanical assembly includes the throttle control lever connected to the artificial feel unit and a Throttle Control Unit (TCU) by adjustable rods. The throttle control lever incorporates the thrust reverse control lever and the Instinctive Disconnect P/B Switch for the A/THR. THROTTLE CONTROL LEVERS The throttle control lever position input to the TCU is the Throttle Lever Angle (TLA). The throttle control levers range of movement is from the IDLE stop (0° TLA) to the TOGA stop (55° TLA). There are two detents: CL and FLX/MCT. THRUST REVERSER CONTROL LEVERS The thrust reverser control lever position input to the TCU is the Reverser Lever Angle (RLA). The thrust reverser control levers range of movement is from the IDLE stop (0° RLA) to the MAX REVERSE stop (96° RLA). At 51.5° RLA there is a REVERSE IDLE detent point. THROTTLE CONTROL ARTIFICIAL FEEL UNIT The throttle control artificial feel unit is a friction system which supplies an artificial load feedback to the throttle control levers and the reverser control levers. The load may be adjusted on the unit using a specific load measuring tool. THROTTLE CONTROL UNIT The primary component of the TCU is the dual resolver. The resolver is a FADEC component, which receives its excitation current from the EEC and transmits the throttle control lever position signal back to the EEC. This signal is the throttle resolver angle (TRA). The TRA signal is used to set the engine thrust in manual and reverse thrust. In automatic thrust, the TRA is used by the EEC to set the thrust limit. In other words, during normal autothrust operation, the engine thrust will likely be less than the thrust limit based on the throttle control lever position which is indicated by the cyan (blue) circle on the indicator. The TCU also includes three potentiometers and a microswitch. The potentiometers are not part of the FADEC system but send throttle control lever position to the Flight Control Primary Computers (FCPCs) for control of the thrust reverser independent locking system tertiary locks. The microswitch sends a \"thrust reverse selected\" signal to the EIVMU for thrust reverser deployment control. MECHANICAL & AVIONICS COURSE - T1+T2 (LVL 2&3) 70 - POWER PLANT (RR Trent 700) THRUST CONTROL D/O (3) Apr 16, 2013 Page 308 A330 RR Trent 700 TECHNICAL TRAINING MANUAL GCL13151 - GEHT0M0 - FM70DG000000071 B1/B2\_A330\_DIFF\_FR\_A320 REV. 1 DATE: 01.06.2019 DVIATION TRAINING SERVICES FOR TRAINING PURPOSES ONLY 308 THROTTLE CONTROL LEVER ASSEMBLY - THROTTLE CONTROL LEVERS \... THROTTLE CONTROL UNIT MECHANICAL & AVIONICS COURSE - T1+T2 (LVL 2&3) 70 - POWER PLANT (RR Trent 700) THRUST CONTROL D/O (3) Apr 16, 2013 Page 309 A330 RR Trent 700 TECHNICAL TRAINING MANUAL GCL13151 - GEHT0M0 - FM70DG000000071 B1/B2\_A330\_DIFF\_FR\_A320 REV. 1 DATE: 01.06.2019 DVIATION TRAINING SERVICES FOR TRAINING PURPOSES ONLY 309 THROTTLE CONTROL LEVER ASSEMBLY - THROTTLE CONTROL LEVERS \... THROTTLE CONTROL UNIT MECHANICAL & AVIONICS COURSE - T1+T2 (LVL 2&3) 70 - POWER PLANT (RR Trent 700) THRUST CONTROL D/O (3) Apr 16, 2013 Page 310 A330 RR Trent 700 TECHNICAL TRAINING MANUAL GCL13151 - GEHT0M0 - FM70DG000000071 B1/B2\_A330\_DIFF\_FR\_A320 REV. 1 DATE: 01.06.2019 DVIATION TRAINING SERVICES FOR TRAINING PURPOSES ONLY 310 This Page Intentionally Left Blank MECHANICAL & AVIONICS COURSE - T1+T2 (LVL 2&3) 70 - POWER PLANT (RR Trent 700) THRUST CONTROL D/O (3) Apr 16, 2013 Page 311 A330 RR Trent 700 TECHNICAL TRAINING MANUAL GCL13151 - GEHT0M0 - FM70DG000000071 B1/B2\_A330\_DIFF\_FR\_A320 REV. 1 DATE: 01.06.2019 DVIATION TRAINING SERVICES FOR TRAINING PURPOSES ONLY 311 ENGINE MASTER CONTROL D/O (3) GENERAL The ENGine MASTER lever located on the center pedestal, interfaces with the fuel system and the FADEC system. On the fuel system, the ENGine MASTER lever acts on the LP valve and the Pressure Raising and Shut-Off Valve (PRSOV). Note that the ENGine FIRE pushbutton also acts on the LP fuel valve. On the FADEC system, the ENGine MASTER lever is used for selection of the starting mode and for reset of the Engine Electronic Controller (EEC) memory. MECHANICAL & AVIONICS COURSE - T1+T2 (LVL 2&3) 70 - POWER PLANT (RR Trent 700) ENGINE MASTER CONTROL D/O (3) Apr 16, 2013 Page 312 A330 RR Trent 700 TECHNICAL TRAINING MANUAL GCL13151 - GEHT0M0 - FM70DH000000071 B1/B2\_A330\_DIFF\_FR\_A320 REV. 1 DATE: 01.06.2019 DVIATION TRAINING SERVICES FOR TRAINING PURPOSES ONLY 312 GENERAL MECHANICAL & AVIONICS COURSE - T1+T2 (LVL 2&3) 70 - POWER PLANT (RR Trent 700) ENGINE MASTER CONTROL D/O (3) Apr 16, 2013 Page 313 A330 RR Trent 700 TECHNICAL TRAINING MANUAL GCL13151 - GEHT0M0 - FM70DH000000071 B1/B2\_A330\_DIFF\_FR\_A320 REV. 1 DATE: 01.06.2019 DVIATION TRAINING SERVICES FOR TRAINING PURPOSES ONLY 313 ENGINE MASTER CONTROL D/O (3) FUEL LP VALVE AND PRSOV CONTROL The ENGine MASTER lever simultaneously controls the LP fuel line and the High Pressure (HP) fuel line opening and closure. LP VALVE AND SLAVE MASTER SWITCH RELAY The ENGine MASTER lever controls the low pressure fuel supply from the aircraft wing through the engine master switch slave relay. When the ENGine MASTER lever is moved to the \"OFF\" position, the engine master switch slave relay is energized. This supplies 28 VDC power to both LP valve actuator motors and causes the LP valve to close. The MASTER switch slave relay takes its 28 VDC power supply from the PRSOV C/B. One actuator motor of the LP valve is electrically supplied from the DC HOT BUS. Pulling out the PRSOV C/B or switching off the aircraft power supply, leads to the automatic opening of the LP valve. The LP valve fail-safe opening logic is mainly used for the engine dry motoring procedure. Pulling out the PRSOV C/B, while the ENGine MASTER lever is kept \"OFF\", makes the fuel feeding to the engine fuel pumps for their lubrication. Selection of the ENGine FIRE pushbutton leads to LP valve closure, regardless of the ENGine MASTER lever position. PRSOV AND AUTO POWER OFF RELAY The ENGine MASTER lever is directly hardwired to the fuel shut off torque motor. It provides an independent authority to shut down the engine by cutting off the fuel supply, regardless of the EEC command. When the ENGine MASTER switch is set to \"OFF\", an aircraft 28 VDC closes the auto power off time delay relay and supplies the fuel shut off torque motor, resulting in the PRSOV closure. Two minutes later, the auto power off relay cuts off the power supply to the fuel shut off torque motor. The PRSOV is maintained in the closed position by spring load. The PRSOV position indication signals are sent to both EEC channels by two microswitches. ENGINE MASTER PANEL FAULT LIGHT The amber \'\'FAULT\" light located on the ENGine MASTER panel comes on in case of: \- an aborted starting procedure during an autostart sequence, \- a PRSOV position disagree. In case both PRSOV microswitches disagree with the MASTER lever position, the EEC sends a fault signal to the Engine Interface and Vibration Monitoring Unit (EIVMU) for \"FAULT\" light and corresponding ECAM message activation. MECHANICAL & AVIONICS COURSE - T1+T2 (LVL 2&3) 70 - POWER PLANT (RR Trent 700) ENGINE MASTER CONTROL D/O (3) Apr 16, 2013 Page 314 A330 RR Trent 700 TECHNICAL TRAINING MANUAL GCL13151 - GEHT0M0 - FM70DH000000071 B1/B2\_A330\_DIFF\_FR\_A320 REV. 1 DATE: 01.06.2019 DVIATION TRAINING SERVICES FOR TRAINING PURPOSES ONLY 314 FUEL LP VALVE AND PRSOV CONTROL - LP VALVE AND SLAVE MASTER SWITCH RELAY \... ENGINE MASTER PANEL FAULT LIGHT MECHANICAL & AVIONICS COURSE - T1+T2 (LVL 2&3) 70 - POWER PLANT (RR Trent 700) ENGINE MASTER CONTROL D/O (3) Apr 16, 2013 Page 315 A330 RR Trent 700 TECHNICAL TRAINING MANUAL GCL13151 - GEHT0M0 - FM70DH000000071 B1/B2\_A330\_DIFF\_FR\_A320 REV. 1 DATE: 01.06.2019 DVIATION TRAINING SERVICES FOR TRAINING PURPOSES ONLY 315 ENGINE MASTER CONTROL D/O (3) MASTER LEVER STARTING AND RESET FUNCTION The ENGine MASTER switch interfaces with the starting sequence and memory reset function of the EEC. STARTING MODE OPERATION During engine start, the ENGine MASTER switch command signal is sent to the EIVMU, which then transmits the information to the EEC in digital format. In case of EIVMU failure or loss of the EIVMU output data, the EEC uses its reset hardwired discrete signals from the ENGine MASTER switch as command signal. RESET FUNCTION The ENGine MASTER switch is directly hardwired to the EEC to satisfy the reset function. Moving the ENGine MASTER lever from \"ON\" to \"OFF\" position closes both channel reset discrete contacts, thus resetting both EEC channels; all data stored in the EEC RAM memory will be cleared. MECHANICAL & AVIONICS COURSE - T1+T2 (LVL 2&3) 70 - POWER PLANT (RR Trent 700) ENGINE MASTER CONTROL D/O (3) Apr 16, 2013 Page 316 A330 RR Trent 700 TECHNICAL TRAINING MANUAL GCL13151 - GEHT0M0 - FM70DH000000071 B1/B2\_A330\_DIFF\_FR\_A320 REV. 1 DATE: 01.06.2019 DVIATION TRAINING SERVICES FOR TRAINING PURPOSES ONLY 316 MASTER LEVER STARTING AND RESET FUNCTION - STARTING MODE OPERATION & RESET FUNCTION MECHANICAL & AVIONICS COURSE - T1+T2 (LVL 2&3) 70 - POWER PLANT (RR Trent 700) ENGINE MASTER CONTROL D/O (3) Apr 16, 2013 Page 317 A330 RR Trent 700 TECHNICAL TRAINING MANUAL GCL13151 - GEHT0M0 - FM70DH000000071 B1/B2\_A330\_DIFF\_FR\_A320 REV. 1 DATE: 01.06.2019 DVIATION TRAINING SERVICES FOR TRAINING PURPOSES ONLY 317 VIBRATION MONITORING SYSTEM D/O (3) GENERAL The vibration monitoring system supplies continuous indications of the state of balance of the N1, N2 and N3 engine rotors. This indication is available on the SD ENGINE page during all engine operating conditions. The vibration monitoring system also helps the operators to do the maintenance operations such as fan trim balance and to monitor the engine vibration trend. MECHANICAL & AVIONICS COURSE - T1+T2 (LVL 2&3) 70 - POWER PLANT (RR Trent 700) VIBRATION MONITORING SYSTEM D/O (3) Apr 16, 2013 Page 318 A330 RR Trent 700 TECHNICAL TRAINING MANUAL GCL13151 - GEHT0M0 - FM70DD000000071 B1/B2\_A330\_DIFF\_FR\_A320 REV. 1 DATE: 01.06.2019 DVIATION TRAINING SERVICES FOR TRAINING PURPOSES ONLY 318 GENERAL MECHANICAL & AVIONICS COURSE - T1+T2 (LVL 2&3) 70 - POWER PLANT (RR Trent 700) VIBRATION MONITORING SYSTEM D/O (3) Apr 16, 2013 Page 319 A330 RR Trent 700 TECHNICAL TRAINING MANUAL GCL13151 - GEHT0M0 - FM70DD000000071 B1/B2\_A330\_DIFF\_FR\_A320 REV. 1 DATE: 01.06.2019 DVIATION TRAINING SERVICES FOR TRAINING PURPOSES ONLY 319 VIBRATION MONITORING SYSTEM D/O (3) VIBRATION MONITORING SYSTEM DESCRIPTION The vibration monitoring system uses the N1, N2 and N3 speed indications processed by the Engine Electronic Controller (EEC) using signals from the engine N1, and N2 speed probes, and from the dedicated alternator (for N3 speed). The vibration monitoring system comprises: \- the N1 trim balance probe, \- the dual vibration transducer, which is a dual output accelerometer, \- the vibration junction box, \- the Remote Charge Converter (RCC), \- the Engine Interface and Vibration Monitoring Unit (EIVMU). ENGINE SHAFT SPEED AND TRIM BALANCE PROBE N1 and N2 shaft speeds are measured using probes that interact with phonic wheels, which are installed in the front bearing housing. The output from the N1 and N2 speed probes is sent to the EEC via the Overspeed Protection Unit (OPU). One of the phase windings in each three-phase circuit of the dedicated alternator supplies the EEC, via the Power Control Unit (PCU), with the N3 shaft speed. The trim balance probe is installed in the engine front bearing housing. It sends a once-per-revolution signal for the LP compressor shaft to the EIVMU. The trim balance probe is identical to the N1 speed probes. VIBRATION TRANSDUCER AND VIBRATION JUNCTION BOX The vibration transducer is a dual output accelerometer installed on the RH side of the engine intermediate case. It contains two piezo-electric crystal stack elements, with a mechanical load of an electrically insulated seismic mass. Each element is connected to an electrical lead. Both leads are connected to the vibration junction box. The vibration junction box is attached to the right engine intermediate case and is divided into two parts. Each part contains the terminals where a transducer lead and cables which go to the RCC, are connected. REMOTE CHARGE CONVERTER (RCC) The RCC is an electronic unit installed on the LH side of the fan case. It receives the signals from the vibration transducer via the vibration junction box. These signals are filtered, \[ amplified and \[ modulated into voltage signals, \[ to be sent to the EIVMU. ENGINE INTERFACE AND VIBRATION MONITORING UNIT (EIVMU) The EIVMU is installed in the aircraft avionics compartment. The EIVMU uses these data for the N1, N2, and N3 rotor vibration level determination and broadband calculation as Inch Per Second (IPS) data. The N1, N2, and N3 rotor vibration levels are displayed on the ENGINE system page and are also available for maintenance purposes through the MCDU via the Central Maintenance Computer (CMC). VIBRATION MONITORING SYSTEM OPERATION To indicate engine vibration levels in the cockpit or to let operators do a fan trim balance, the EIVMU uses information from the RCC, the EEC, and from the trim balance probe. REMOTE CHARGE CONVERTER (RCC) The engine vibrations cause the seismic mass in the transducer to apply pressure on the piezo-electric crystal stack elements. This causes the elements to generate electrical signals proportional to the engine vibration. The signals are then sent to the RCC which amplifies them to give output signals to the EIVMU. MECHANICAL & AVIONICS COURSE - T1+T2 (LVL 2&3) 70 - POWER PLANT (RR Trent 700) VIBRATION MONITORING SYSTEM D/O (3) Apr 16, 2013 Page 320 A330 RR Trent 700 TECHNICAL TRAINING MANUAL GCL13151 - GEHT0M0 - FM70DD000000071 B1/B2\_A330\_DIFF\_FR\_A320 REV. 1 DATE: 01.06.2019 DVIATION TRAINING SERVICES FOR TRAINING PURPOSES ONLY 320 ENGINE ELECTRONIC CONTROLLER (EEC) The engine speed signals N1, N2 and N3 are sent to the EIVMU through an ARINC data bus connection, and are used for vibration retrieval and display on the MCDU through the EIVMU menu. TRIM BALANCE PROBE Once-per-revolution analog signal is sent by the trim balance probe to the EIVMU. It is used for determination of the N1 unbalance phase angle. This phase angle is accessible through the EIVMU menu and is used, with the vibration amplitude, for the fan trim balance procedure. VIBRATION INDICATING AND MAINTENANCE DATA The EIVMU maintains the interface between the engine systems and the aircraft, and sends ARINC data to the cockpit. VIBRATION INDICATING The vibration indication is displayed on the ECAM ENGINE and CRUISE pages. The vibration data from the EIVMU in IPS are converted in \"cockpit UNITS\" in a range from 0 to 10. An ECAM advisory informs the flight crew when N1, N2 or N3 vibration level exceeds a specific value. In such a case, the vibration over limit value pulses in green. VIBRATION MAINTENANCE DATA The Aircraft Maintenance Manual (AMM) 71-00-00 chapter (adjustment / test) contains the information required to do the LP compressor trim balance test (test number 16) with the engine on wing, and the engine vibration survey test (test number 11). The LP compressor trim balance test, is done through the MCDU menus to identify where the trim balance bolts have to be installed on the LP compressor make-up piece to recover nominal balance. The engine vibration survey test (test number 11) is done to schedule the engine module replacement as a preventive maintenance operation. MECHANICAL & AVIONICS COURSE - T1+T2 (LVL 2&3) 70 - POWER PLANT (RR Trent 700) VIBRATION MONITORING SYSTEM D/O (3) Apr 16, 2013 Page 321 A330 RR Trent 700 TECHNICAL TRAINING MANUAL GCL13151 - GEHT0M0 - FM70DD000000071 B1/B2\_A330\_DIFF\_FR\_A320 REV. 1 DATE: 01.06.2019 DVIATION TRAINING SERVICES FOR TRAINING PURPOSES ONLY 321 VIBRATION MONITORING SYSTEM DESCRIPTION \... VIBRATION INDICATING AND MAINTENANCE DATA MECHANICAL & AVIONICS COURSE - T1+T2 (LVL 2&3) 70 - POWER PLANT (RR Trent 700) VIBRATION MONITORING SYSTEM D/O (3) Apr 16, 2013 Page 322 A330 RR Trent 700 TECHNICAL TRAINING MANUAL GCL13151 - GEHT0M0 - FM70DD000000071 B1/B2\_A330\_DIFF\_FR\_A320 REV. 1 DATE: 01.06.2019 DVIATION TRAINING SERVICES FOR TRAINING PURPOSES ONLY 322 VIBRATION MONITORING SYSTEM DESCRIPTION \... VIBRATION INDICATING AND MAINTENANCE DATA MECHANICAL & AVIONICS COURSE - T1+T2 (LVL 2&3) 70 - POWER PLANT (RR Trent 700) VIBRATION MONITORING SYSTEM D/O (3) Apr 16, 2013 Page 323 A330 RR Trent 700 TECHNICAL TRAINING MANUAL GCL13151 - GEHT0M0 - FM70DD000000071 B1/B2\_A330\_DIFF\_FR\_A320 REV. 1 DATE: 01.06.2019 DVIATION TRAINING SERVICES FOR TRAINING PURPOSES ONLY 323 THRUST REVERSER SYSTEM D/O (3) GENERAL The thrust reverser system helps the wheel brakes by supplying additional deceleration forces to the aircraft. The thrust reversers are used only on the ground to reduce aircraft roll distance for landing or in case of aborted take-off. The thrust reversers are incorporated into the left and right C-ducts. Each C-duct has 2 pivoting doors, each one operated by a hydraulic actuator. When the pivoting doors are deployed, they stop the fan airflow to the Common Nozzle Assembly (CNA) and redirect it forward. Thrust reverse is selected from the throttle control levers and is controlled and monitored by the Engine Electronic Controller (EEC). The pivoting door actuators are operated by the Isolation Control Unit (ICU) and the Direction Control Unit (DCU). The ICU and DCU of each engine are supplied by the engine-driven pump of that engine. MECHANICAL & AVIONICS COURSE - T1+T2 (LVL 2&3) 70 - POWER PLANT (RR Trent 700) THRUST REVERSER SYSTEM D/O (3) Apr 16, 2013 Page 324 A330 RR Trent 700 TECHNICAL TRAINING MANUAL GCL13151 - GEHT0M0 - FM70D6000000071 B1/B2\_A330\_DIFF\_FR\_A320 REV. 1 DATE: 01.06.2019 DVIATION TRAINING SERVICES FOR TRAINING PURPOSES ONLY 324 GENERAL MECHANICAL & AVIONICS COURSE - T1+T2 (LVL 2&3) 70 - POWER PLANT (RR Trent 700) THRUST REVERSER SYSTEM D/O (3) Apr 16, 2013 Page 325 A330 RR Trent 700 TECHNICAL TRAINING MANUAL GCL13151 - GEHT0M0 - FM70D6000000071 B1/B2\_A330\_DIFF\_FR\_A320 REV. 1 DATE: 01.06.2019 DVIATION TRAINING SERVICES FOR TRAINING PURPOSES ONLY 325 GENERAL MECHANICAL & AVIONICS COURSE - T1+T2 (LVL 2&3) 70 - POWER PLANT (RR Trent 700) THRUST REVERSER SYSTEM D/O (3) Apr 16, 2013 Page 326 A330 RR Trent 700 TECHNICAL TRAINING MANUAL GCL13151 - GEHT0M0 - FM70D6000000071 B1/B2\_A330\_DIFF\_FR\_A320 REV. 1 DATE: 01.06.2019 DVIATION TRAINING SERVICES FOR TRAINING PURPOSES ONLY 326 This Page Intentionally Left Blank MECHANICAL & AVIONICS COURSE - T1+T2 (LVL 2&3) 70 - POWER PLANT (RR Trent 700) THRUST REVERSER SYSTEM D/O (3) Apr 16, 2013 Page 327 A330 RR Trent 700 TECHNICAL TRAINING MANUAL GCL13151 - GEHT0M0 - FM70D6000000071 B1/B2\_A330\_DIFF\_FR\_A320 REV. 1 DATE: 01.06.2019 DVIATION TRAINING SERVICES FOR TRAINING PURPOSES ONLY 327 THRUST REVERSER SYSTEM D/O (3) THRUST REVERSER CONTROL - GENERAL The thrust reverser is primarily controlled by the EEC. In addition to the EEC, there is a second and third layer of protection built in to prevent inadvertent or accidental thrust reverser deployment. EEC CONTROL The EEC receives a DEPLOY signal from resolvers in the Thrust Control Unit (TCU) when the throttle control levers are selected to the thrust reverse position. As long as the engine is running, the EEC validates the DEPLOY command and sends a command signal to open the isolation control valve, pressurizing the system. Hydraulic pressure is then directed to the stow side of the door actuators. EIVMU CONTROL The DEPLOY command is also controlled by the Engine Interface and Vibration Monitoring Unit (EIVMU). The EIVMU receives the \"aircraft on ground\" signal from the Landing Gear Control and Interface Unit (LGCIU) and a \"thrust reverse selected\" signal from a dedicated switch in the TCU. The EIVMU then energizes the Permission Switch, which controls the power supply to the thrust reverser direction control unit. The ground for the relay is controlled by the EEC when the DEPLOY command is validated. Hydraulic pressure is then directed to the hydraulic latches to unlock the reversers and then to the deploy side of the actuators to open the thrust reverser pivoting doors after unlocking the internal (secondary) actuator locks. FCPC CONTROL Regulations also require another layer of protection, sometimes referred to as the \"third line of defense\". This additional protection system must be independently-controlled. In other words, it must use signals different from the EEC/EIVMU control. On the A330, this additional protection is provided by the Tertiary Locking System (TLS). The tertiary locks mechanically lock each pivoting door in the stowed position. The locks are released electrically to deploy the reverser. The TLS is independently controlled by the Flight Control Primary Computers (FCPC 1, 2, 3). The FCPC command the tertiary locks to unlock when the following conditions are satisfied: \- \"thrust reverse selected\" signals from dedicated potentiometers in the TCU \- other engine throttle control levers in IDLE position \- \"aircraft on ground\" - Radio Altimeter (RA) signal \< 6 ft. MECHANICAL & AVIONICS COURSE - T1+T2 (LVL 2&3) 70 - POWER PLANT (RR Trent 700) THRUST REVERSER SYSTEM D/O (3) Apr 16, 2013 Page 328 A330 RR Trent 700 TECHNICAL TRAINING MANUAL GCL13151 - GEHT0M0 - FM70D6000000071 B1/B2\_A330\_DIFF\_FR\_A320 REV. 1 DATE: 01.06.2019 DVIATION TRAINING SERVICES FOR TRAINING PURPOSES ONLY 328 THRUST REVERSER CONTROL - GENERAL - EEC CONTROL \... FCPC CONTROL MECHANICAL & AVIONICS COURSE - T1+T2 (LVL 2&3) 70 - POWER PLANT (RR Trent 700) THRUST REVERSER SYSTEM D/O (3) Apr 16, 2013 Page 329 A330 RR Trent 700 TECHNICAL TRAINING MANUAL GCL13151 - GEHT0M0 - FM70D6000000071