Aircraft Powerplant Systems PDF
Document Details
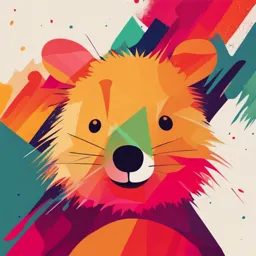
Uploaded by OticArcticTundra2877
PATTS College of Aeronautics
Tags
Related
- AMT-1104 Aircraft Powerplant I (Reciprocating Engine) PDF
- AMT 613 A/C Powerplant I (Reciprocating Engine) PDF
- Powerplant Systems PDF
- ET-PP04 Aircraft Engine Inspection, Maintenance, Operation, and Troubleshooting PDF
- Aircraft General Knowledge (Basic Airplane Powerplant) PDF
- Chapter 8 PowerPlant Installation PDF
Summary
This document provides an overview of aircraft powerplant systems. It covers various engine types, components like fuel, lubrication, and cooling systems, and their functions.
Full Transcript
POWERPLANT SYSTEMS The aircraft powerplant provides mechanical force to power the aircraft and associated accessories necessary for flight. An aircraft's powerplant is the system responsible for generating thrust or power to propel the aircraft. This typicall...
POWERPLANT SYSTEMS The aircraft powerplant provides mechanical force to power the aircraft and associated accessories necessary for flight. An aircraft's powerplant is the system responsible for generating thrust or power to propel the aircraft. This typically consists of an engine and its supporting systems. Engine Types The primary types of engines used in aircraft are: Reciprocating Engines: These engines use pistons that move back and forth to convert chemical energy (from fuel) into mechanical energy. They are commonly used in smaller general aviation aircraft. Turbine Engines: These engines use the force of hot, high-pressure gases to spin turbines. They are more efficient and powerful than reciprocating engines, and are commonly used in larger commercial and military aircraft. FUEL SYSTEM LUBRICATION SYSTEM COOLING SYSTEM INDUCTION SYSTEM IGNITION SYSTEM EXHAUST SYSTEM PROPELLER SYSTEM ENGINE CONTROLS FUEL SYSTEM Delivers fuel to the engine for combustion. It includes fuel tanks, pumps, filters, and lines. Fuel Tanks: These store the fuel that powers the engine. They are typically located in the wings or fuselage. Fuel Pumps: These pumps move fuel from the tanks to the engine. They are essential for ensuring a steady fuel supply. Fuel Filters: These remove impurities from the fuel, preventing them from clogging the engine's fuel injectors or carburetors. Fuel Lines: These pipes and tubes carry fuel from the tanks to the engine. They are designed to withstand high pressure and temperature. LUBRICATION SYSTEM Circulates oil to lubricate engine components, reducing friction and wear. It includes oil tanks, pumps, filters, and lines. Oil Tank: This stores the lubricating oil. It is typically located near the engine. Oil Pump: This circulates the oil throughout the engine. It is essential for preventing wear and tear on engine components. Oil Filter: This removes impurities from the oil, preventing them from damaging engine components. Oil Lines: These pipes and tubes carry oil throughout the engine. They are designed to withstand high pressure and temperature. COOLING SYSTEM Removes heat from the engine to prevent overheating. This can be achieved through air cooling or liquid cooling. Air Cooling: In this system, air is drawn over the engine to cool it. This is common in smaller aircraft. Liquid Cooling: In this system, a liquid (usually coolant) is circulated through the engine to absorb heat. This is common in larger aircraft. The coolant is then cooled by a radiator or heat exchanger. INDUCTION SYSTEM Draws air into the engine for combustion. It includes air filters and carburetors or fuel injectors. Air Filter: This removes dirt and debris from the air before it enters the engine. Carburetor or Fuel Injectors: These devices mix fuel with air and deliver the mixture to the engine's cylinders. Carburetor: A mechanical device that mixes fuel and air using a Venturi effect. Fuel Injectors: Electronic devices that spray fuel directly into the engine's cylinders. IGNITION SYSTEM Provides a spark to ignite the fuel-air mixture in the engine's cylinders. Spark Plugs: These devices create a spark to ignite the fuel-air mixture in the engine's cylinders. Ignition Coil: This supplies the electrical current to the spark plugs. Ignition Control Unit: This controls the timing of the spark. EXHAUST SYSTEM Directs the hot exhaust gases away from the aircraft. Exhaust Manifold: This collects the exhaust gases from the engine's cylinders. Exhaust Pipes: These carry the exhaust gases away from the engine. Silencer or Muffler: This reduces the noise of the exhaust gases. PROPELLER SYSTEM In propeller-driven aircraft, the propeller converts the engine's mechanical energy into thrust. Propeller Blades: These blades convert the engine's rotational energy into thrust. Propeller Hub: This connects the propeller blades to the engine's crankshaft. Propeller Governor: This controls the propeller's pitch, which affects the amount of thrust produced. ENGINE CONTROLS Allows the pilot to control the engine's power output. Throttle: This controls the amount of fuel and air that enters the engine. Mixture Control: This controls the ratio of fuel to air in the mixture. Ignition Timing Control: This controls the timing of the spark. ADDITIONAL SYSTEMS ENGINE MANAGEMENT SYSTEM AUXILIARY POWER UNIT THRUST REVERSERS Engine Management System (EMS) A computer system that monitors and controls various engine parameters, improving efficiency and reducing pilot workload. Function: The EMS is a computerized system that monitors and controls various engine parameters, such as fuel flow, air intake, ignition timing, and exhaust temperature. By constantly analyzing and adjusting these parameters, the EMS can optimize engine performance, improve fuel efficiency, and reduce emissions. Benefits: Enhanced efficiency: The EMS can optimize engine performance to minimize fuel consumption and reduce operating costs. Improved safety: By monitoring engine parameters in real-time, the EMS can detect and prevent potential problems, such as engine failures or overheating. Reduced pilot workload: The EMS can automate many routine engine management tasks, freeing up pilots to focus on other aspects of flight. Auxiliary Power Unit (APU) A small turbine engine that can provide power for various aircraft systems when the main engines are not running. Function: The APU is a small turbine engine that can generate electrical power and hydraulic pressure for the aircraft's systems when the main engines are not running. It is typically located in the tail of the aircraft. Applications: Ground power: The APU can provide power for essential systems on the ground, such as air conditioning, lighting, and avionics. Emergency power: In case of a main engine failure, the APU can provide backup power to essential systems, allowing the aircraft to maintain control and land safely. Start-up assistance: The APU can be used to start the main engines, especially in cold weather conditions. Thrust Reversers Devices that can reverse the direction of thrust, aiding in braking during landing. Function: Thrust reversers are devices that can reverse the direction of thrust, aiding in braking during landing. They are typically located in the rear of the engine. Types: Target-type reversers: These reversers have movable targets that deflect the exhaust gases forward. Cascade-type reversers: These reversers have a series of vanes that can be rotated to reverse the direction of the exhaust gases. Benefits: Shorter landing roll: Thrust reversers can significantly shorten the landing roll, reducing the amount of runway required. Improved braking: Thrust reversers can provide additional braking force, especially on wet or icy runways. Reduced tire wear: By reducing the braking load on the tires, thrust reversers can help to prolong their lifespan.