Basic Furniture Finishing Test #3 Winter Semester 2024 PDF
Document Details
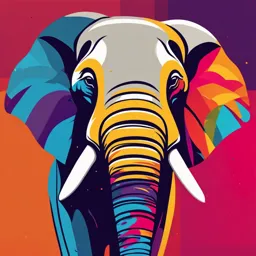
Uploaded by AttractiveJaguar
Algonquin College
2024
Michael Maritan
Tags
Summary
These notes cover various furniture finishing methods, including drying, curing, and different types of finishes. The document describes the characteristics and applications of various finishes like oil, varnish, and wax. The document is aimed at an individual pursuing a professional or advanced level of understanding of furniture finishing techniques.
Full Transcript
Basic Furniture Finishing Test #3 WINTER SEMESTER 2024 INSTRUCTOR: Prof. Michael Maritan [email protected] Definitions Drying – The process of a solvent being removed from a solution by evaporation A physical change Reversible by adding solvent back to the dried material Evaporative Finis...
Basic Furniture Finishing Test #3 WINTER SEMESTER 2024 INSTRUCTOR: Prof. Michael Maritan [email protected] Definitions Drying – The process of a solvent being removed from a solution by evaporation A physical change Reversible by adding solvent back to the dried material Evaporative Finishes A coat of an evaporative finish partially redissolves (“burns into”) the previous coat of the same finish and becomes a single layer once the solvent evaporates The term “Drying Oil” conflicts with this definition. A “Drying Oil” doesn’t dry; it cures. Curing A chemical reaction Typically due to exposure to oxygen or a catalyst Curing processes are generally not reversible by adding the original solvent back to the dried material Reactive Finishes A coat of a reactive finish will sit on top of previous coats of the same finish if the previous coat has fully cured Some finishes “dry” (ie. Shellac). Some finishes “Cure” ie. Pure Tung Oil). Some finishes “Dry” as a first step, then “Cure” as a second step (ie. Varnish). Colour of the Finished Piece 1 Types of Finishes Top Coats Wipe On Brush On Spray On Rag ($) Brush ($$) Spray System ($$$$$$$) Proper PPE Required – Refer to SDS Proper Ventilation Spray Booth Slow Drying Products Slow and Fast Drying Products Easiest Takes Practice Takes Practice Fastest Clean-Up – Rag dried and thrown out (with caution) Slower Clean-Up – Brushes must be cleaned Slowest Clean-Up – All parts must be cleaned Low Throughput Lowest Throughput Highest Throughput Penetrating Finishes Film Finishes Does not cure very hard, Cannot be built up to a significant thickness, Wipe on application Cure/Dry hard, Can be built up in layers to (almost) any thickness, Brush or Spray on application (some can be 2 wiped on) Examples: Tung oil Linseed oil Polymerized oil Oil/Varnish blend Examples: Varnish Shellac Waterborne varnish Brush-on lacquer Penetrating Finishes Oil Finishes Penetrating finish – Soaks in No “Build” – Offers limited protection against scratching and marking Most oils are “drying oils” (curing oils); a few are “non-drying oils” “Drying oils” – “Plasticizes” the surface of the wood at a microscopic level as it cures Darkens the wood Easy repairs – Wipe on another coat Ex. ○ Tung oil ○ Linseed oil Tung Oil A “drying oil” – Reactive finish – Cures Extracted from nuts of the tung tree Wipe-on with a cloth – Wipe off all excess ○ Excess oil will not cure properly – Sticky Cures very slowly – Wait days between coats Cures soft – Limited protection against scratching or marking Fairly water-resistant after five or six coats Yellows over time less than linseed oil – Important on blond woods Read the label – “Pure Tung Oil” vs. “Tung Oil Finish” Linseed Oil 3 A slow “drying oil” – Reactive finish – Cures Extracted from flax seeds An impractical finish in its raw form – Cures even slower than tung oil – Wait weeks between coats Wipe-on with a close – Wipe off all excess to avoid a sticky surface Easily penetrated by water Limited protection against scratching or marking Yellows over time more than Tung oil Boiled Linseed Oil (BLO) A “drying oil” – Reactive finish Addresses the slow cure time associated with pure linseed oil Not actually “boiled” – Metallic driers (salts of cobalt, manganese, or zinc) added to linseed to significantly speed up the curing process Wipe on – Wipe off all excess – Wait approximately 1 day between coats Has the same yellowing and limited protection issues as linseed oil Can spontaneously combust Polymerized Oils “Drying oil” – Reactive finish Oil that has been specially heat treated to partially pre-cure the product – Reduces curing time after application Oil processed in this manner is called “polymerized” Thick/high viscosity – Some products are diluted with mineral spirits for easier application Cannot be applied in thick layers – Oil will not cure properly and stay gummy Wipe on – Wipe off all excess Ex. ○ Polymerized Tung Oil ○ Polymerized Linseed Oil Double-Boiled Linseed Oil (DBLO) 4 Manufacturing process / ingredients vary from manufacturer to manufacturer ○ Multi-step / prolonged polymerization ○ Polymerization plus chemicals to speed curing ○ Wipe on – Wipe off all excess Oil / Varnish Blends Reactive finish Oil and varnish combined to create a thick oil / thin varnish More protective than straight oil but softer / less protective than straight varnish Lower gloss than straight carnish Cures slower than straight varnish – Plenty of time to apply Application directions vary from product to product – Read the TDS Danish Oil A vague marketing term Means different things depending on the manufacturer Wax Finish Evaporative “finish” Used as an early finish before availability of better oil and film finishes Minimal protection against heat, water, solvents, scuff, and scrapes Beeswax, paraffin wax, carnauba wax, etc. Dissolves in a solvent to create a paste or liquid for application Solvents evaporate – Wax becomes solid at room temp Rub on a thin layer – Wait for solvents to evaporate – Buff out Today, wax is seldom used as a furniture finish on raw wood. However, it is used as a decorative finish on carved / turned items and as a polish over other finishes ○ Sometimes used over an oil finish for a traditional ○ Sometimes added to other types of finishes Hardwax-Oil 5 Blend of oils and waxes plus sometimes solvents, driers, and catalysts Reactive finish Popular in Europe – Relatively new in North America Originally developed for wood flooring – Used on furniture Relatively expensive but a little goes a long way Wipe on – Wipe off all excess “Food Safe” Finishes Irrelevant for many items – Chest of drawers Important for others – Cutting boards Some finishes claim to be “food safe” in both liquid and solid form Some finishes claim to be “food safe” once cured Understand the product you select and follow the TDS Using Cooking Oil for Cutting Boards “Non-drying” oils Exposure to air, light, and heat can cause the fat molecules in cooking oils to break down – Rancidification ○ Rancid oils have a bad smell and taste Do not use cooking oils to protect wooden items Mineral Oil “Non-drying” oil Petroleum product Does not go rancid when exposed to oxygen Often used on cutting boards and wooden utensils – Not furniture Will eventually wash off – Wipe-on and wipe-off excess Reapply as needed Darkens the wood Non-yellowing Minimal water protection Often combined with wax to improve water resistance Film Finishes 6 Coats the wood / sits on the surface Must be applied in a uniform layer Cures / Dries harder than oil finishes – Can be built up to a measurable thickness Thicker layer provides better protection from abrasion, scratches, and water Practical limits to film thickness ○ If finish is too thick – May develop cracks as a result of expansion and contraction of wood underneath Can be less “natural” looking than penetrating finishes Chemistry:: ○ Evaporative finish ○ Reactive finish ○ Coalescing finish Varnish (Including Polyurethane – Excluding Waterborne Finishes) Reactive finish – Cures Combination of oils, resins, and solvents ○ Selected ratio of ingredients provides a finish with specific characteristics (hard v. soft) ○ Tree sap was the tradition resin Modern resins are alkyd, phenolic, or polyurethane Typically includes metallic dryers Can be thinned with mineral spirits (check TDS) Apply with high quality natural bristle brush Pros: ○ Very good heat, wear, water, and chemical resistance ○ Brushes easily with long open time Cons: ○ Long open time – Slow drying resulting in dust contamination problems and runs / sags ○ Yellows over time ○ Can be difficult to rub out ○ “Invisible” repairs are difficult Wiping Varnish 7 Reactive finish – Cures Varnish with lots of thinner ○ Commercial wiping varnish ○ Homemade – Add thinner to brushing varnish (start thinning ~25% and adjust until desired consistency is achieved) Levels well due to low viscosity Less build per coat Application options: ○ Wipe on and wipe off all excess ○ Brush on and leave to cure ○ Wipe on and wipe off some excess Easier to work with Same cons as varnish Shellac Evaporative finish Natural resin secreted by lac beetle Dissolved in alcohol Naturally orange-ish in colour – Range of colour intensities available Traditional finish on quality furniture throughout 19th and early 20th century Apply with high quality natural bristle brush Available in button, flake, or predisolved liquid form ○ “Pound Cut” – # of lbs. of Shellac Flakes dissolved in a gallon of denatured alcohol ○ 8 “Split-Coat” – ½ pound cut Natural shellac contains wax – Dewaxed shellac is available Pros: ○ Dries rapidly – Minimal dust problems ○ Good rubbing properties ○ Good repair qualities ○ Does not dark much with age ○ Excellent sealing properties Bonds well over oil, wax, and resins Blocks odours Excellent barrier to silicone Cons: ○ Weak resistance to heat, water, and chemicals ○ Moderate resistance to wear ○ Short shelf life in liquid form Shellac Freshness User mixed liquid shellac has a limited shelf life – Rule of thumb: 6 Months Stale shellac will not dry hard due to “esterification” To check freshness ○ Create a thin layer on a hard surface ○ Wait 15 minutes ○ Preform “Fingerprint Test” Shellac in solid form has a very long shelf life Some premixed commercial shellac products (ie. Zinsser) claim a shelf life of 3 years French Polish 19th Century finishing technique using shellac Alternative to brush on application Many, many, many, many thin coats of shellac are applied with a pad sometimes lubricated with oil Produces a very smooth high gloss surface with deep colour Very time consuming Requires lots of practice and patience to achieve good results Brushing Lacquer 9 Evaporative finish Most lacquer is sprayed – Solvents used evaporate very quickly Brushing lacquer uses slower evaporating solvents Solid material is nitrocellulose based Thinner is lacquer thinner Limited working time Good rubbing properties Good repair qualities Coalescing Finishes (Waterborne Technology) Rapidly evolving category of product, low VOC Composed of microscopic droplets / balls containing a reactive finish Droplets are suspended in water and a very slow evaporating solvent (glycol ether) ○ Water evaporates first ○ Remaining solvent then softens outside of droplets ○ Droplets stick together (coalesce) when solvent evaporates and finish cures Water is “carrier”; not solvent (Distilled) Water typically used for thinning waterborne finishes Waterborne Varnish Coalescing finish Solvent is glycol ether Thinner is water Apply with a high quality synthetic bristle brush Resin is typically acrylic or polyurethane Less working time than traditional varnishes Milky white when in liquid state – Dries clear Pros: 10 ○ Low VOC ○ Non-flammable in liquid state ○ Dries quickly – Less dust contamination, more coats in a day ○ Easy soap and water cleanup ○ Cured finish virtually colourless – Minimal change to blond woods ○ Does not yellow over time Cons: ○ Water content raises the grain ○ Less resistant to heat, chemicals, scratches, and water vapour ○ Dries quickly – Difficult to keep a wet edge and avoid brush marks ○ Limited ability to thin ○ Cured finish is virtually colourless – Can be bland looking on dark woods ○ Potential compatibility issues with oil stans ○ Potential foaming issues Applying Multiple Coats Evaporative Finish Solvent in finish will redissolve previous coat Creates single thicker layer – No adhesion issues between layers Overworking finish can create problems – Work quickly Reactive Finish Solvent in finish will not affect previous coat – Provided it has cured Final finish made up of multiple discrete layers Refer to TDS for time between coats Chemical Reactions 1. Curing is a chemical reaction 2. As finishes cure, they typically generate heat a. Slow curing – Generates less heat b. Fast curing – Generates more heat 3. Temperature can affect curing process a. Lower temperature – Slower curing b. Higher temperature – Faster curing Spontaneous Combustion Crumpled up rags acts as insulation – Heat cannot escape quickly Crumpled up rag soaked with finish 11 ○ Finish start to cure – Generates heat ○ Heat can’t escape – Warm environment finish to cure faster ○ Fasture curing creates even more heat – Finish cures faster till; ○ More heat – Faster curing – More heat – Faster curing… ○ Eventually – Fire “Thermal Runaway” can lead to spontaneous combustion 12 Dispose of finish-soaked materials properly