Advanced Machining Test #2 Winter Semester 2024 PDF
Document Details
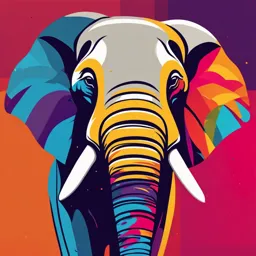
Uploaded by AttractiveJaguar
Algonquin College
Prof. Nick Schafer
Tags
Summary
These notes cover advanced machining topics, focusing on lathes, components, turning techniques, and preparation methods. They also discuss different machine types and their components. The notes are suitable for an undergraduate-level course in advanced machining or a similar field. The instructor is Prof. Nick Schafer from Algonquin College.
Full Transcript
Advanced Machining Test #2 WINTER SEMESTER 2024 INSTRUCTOR: Prof. Nick Schafer [email protected] Standard Machines Lathes Although run by a motor, some still consider it a hand tool. Dates back thousands of years, powered by hand using bows and lathe tools held and guided with hands and f...
Advanced Machining Test #2 WINTER SEMESTER 2024 INSTRUCTOR: Prof. Nick Schafer [email protected] Standard Machines Lathes Although run by a motor, some still consider it a hand tool. Dates back thousands of years, powered by hand using bows and lathe tools held and guided with hands and feet. Pole / Bodger’s Lathe Very common throughout middle ages Employed a ‘springy’ bough of wood (sapling) and a rope that was wound once around the turning ○ Foot pedal would pull the rope, thus spinning the stock, to be cut by chisels Commonly used by ‘Bodgers’ ○ Job: To turn chair rungs and legs ○ Commonly lived in the forest for months at a time while working Components Lathe Headstock ○ Houses the motor, fixed unit ○ Step-pulleys or clutch system ○ In-Board: To the right of the head stock, side of the tool rest ○ Out-Board: To the left of the head stock, side of the locking pin and indexing pin 1 Indexing pin not used to brake the lathe Indexing head allows features to be applied to a turning, a set number of degrees apart ○ Lathe Bed Regular - No gap in bed by headstock Gap-bed - Typically used to carve larger radius pieces close to the head stock ○ ○ Mandrel Never lubricate #2 Morse taper inside Drive Center ○ Banjo ○ Holds the tool rest Tool Rest Fits into the ‘banjo’ Locking mechanism on the underside Lathe Tailstock ○ Fits into mandrel with morse-taper Live ‘Cup’ center Live: Center rotates with the wood Dead: Center is stationary ○ Lock for center ○ Lock for tailstock ○ Hand Wheel to advance center into stock ○ #3 Morse taper inside tailstock mandrel Lathe Main Control Pod ○ Main Power switch underneath headstock, red light indicates power to control pod 2 ○ Emergency stop ○ Stop / Start ○ Variable speed rpm adjust ○ Forward / Reverse rotation ○ Long deceleration switch ○ 12 seconds to stop stock from rotating Short deceleration switch 4 seconds to stop stock from rotating Two Categories of Turning 1) Spindle Turning - Stock is supported on both ends by headstock and tailstock 2) Bowl Turning - Stock is supported by headstock only, may be inboards or outboard Turning Technique Cutting ○ Faster & smoother but requires more skill ○ Tool is held at a lower angle Scraping ○ Slower ○ Sometimes a better option for more difficult woods ○ Tool is held at roughly 90 degrees ‘Dig-in’ - Happens when a part of the tool that is not supported by the tool rest makes contact with the workpiece ○ Wood grabs and rolls the tool 3 Can be unnerving, DO NOT LET GO Tool rest position is important ○ Too high => Causes tool to scrape instead of cut ○ Too low => Can cause the material to want to climb onto the tool ○ Try and maintain a distance of ⅛” ○ Do not fall off the tool rest ALWAYS turn “downhill” ○ From larger diameter to smaller diameter ○ Turning “uphill” => Tool tends to catch and get thrown Prepping Stock Stock should be as close to finished dimensions as possible If gluing blanks, let glue cure overnight (~12 hrs.) If piece is to be turned completely, make blank about ½” longer Stock should be as straight as possible ○ ‘Blocking’ ○ Joints added to entire length or only to required areas Split Turnings ○ **Look for severe checks or weak spots Paper joint Multiple layers of craft paper sandwiched between glue Not waxed Wood - glue - paper - glue - paper - glue - paper - glue - wood Stave Construction ○ For larger turnings (ie. columns, drums) ○ Center is hollow ○ Do not mix different wood cuts, different dimensional changes ○ Rounder blanks Standard Turning Tool Kit 1) Roughing gouge 2) Smaller gouge 3) Parting tool 4) Skew chisel 5) Spear point scraper 6) Round nose scraper Common Lathe Accessories There’s no limit to how much you can accessorize a lathe. Chucks ○ 4 Jawed Chucks 3 or 4 jaws ○ ○ Most self-centering Some have independently moving jaws, usually for machining Part can be mounted on inside or outside Jam Chuck No screw holes Jams into bowl center Doughnut Chuck ○ ○ 4-jawed most common Two pieces of plywood with connecting rods Longworth Chuck Grabs bowls by the rim Mainly used to finish bottoms of bowls Vacuum Chuck No holes Relying on vacuum to hold the part, an additional system, ability to fail Can be dangerous Face Plates Right angle tools Drive centers Etc. Dust Fungal spores from decaying wood (ie. Spalted woods) can be a health hazard Full face respirator required Other Types of Lathes Duplicating Lathe - Original spindle mounted below the lathe bed, duplicator follows its outline Back Knife Lathe - Knives are mounted behind the spinning stock, introduced slowly to the spinning stock to create the shape 5 CNC Lathe - CNC program is stored on a diskette and called when needed to create a specific profile Portable Machines Biscuit Joiners Created in the 1950s by Swiss cabinetmaker Herman Steiner, later founded Steiner Lamello Company Also known as Lemon Spliners or Plate Joiners Creates a self-leveling joint with some side-to-side play Useful when creating and gluing multiple miter joints Components Height adjustment for fence Alignment guide Anti-friction pins Variable angle fence Blade ○ Have long shoulders to reduce possibility of kickback, necessary for how machine is designed to be used Biscuit recess size adjustment On/Off switch Biscuits Spacing is project specific 3 Standard Sizes: #20, #10, and #0 Specialty Sizes: 6 ○ #6 – Accommodates larger joints ○ #4 - Smaller joints than #6 ○ #9 – Very small joints (ie. miters) ○ #11 – Specifically used with routers Made of pre-compressed Beech, grain at 45 degrees to long axis for strength Must be stored in a cool, dry place until used In Practice Hand position is very important ○ Do not place any hand to the left of the tool when in use Double row of biscuits for thick stock Fence set for biscuiting 45 degree miter Portable Planers Typically used on site Common applications: ○ Counter-tops ○ Built-in’s ○ Scribing strips ○ Mouldings Considerations: Width of cutter and depth of cut Rebating capability Ease of sharpening and knife changing Manufacturers reputation and availability of local servicing Components Belt guard Trigger switch Outfeed table (Back shoe) Infeed table (Front shoe) Cutter blade ○ 7 Readily available Cutter retainer Cutter Head Front handle Nail Guns Dust Collection Shop Air Systems Main Function – To provide the correct volume of clean air to the tool/machine when needed 6 Main Parts 1) Compressor a) Available in many sizes b) Most important aspect – How quickly it can produce the volume of air required i) Need to know how many CFM are required c) Portables i) Should produce about 25% more CFM’s than tool requires ii) Gets incredibly hot when ran for a long time iii) Oil-less or Oil lubed 2) Air Lines a) Materials: i) Galvanized Pipe – Common for long runs ii) Copper Pipe – Common for long runs and low cost iii) Nylon – Usually sold in coil fashion, very light in weight, inexpensive but not repairable iv) PVC – One of the cheapest, gets quite stiff in colder temperatures, can be difficult to work with, fairly light in weight v) Rubber – Heaviest, but stays flexible even in cold temperatures, more expensive than PVC or Nylon vi) Polyurethane – Most expensive, lighter than rubber, quite flexible in cold weather, easy to repair and clean 8 b) Diameter is important: i) Too narrow – Pressure drop due to friction within run, starves tool for air 3) Filter a) Long Runs – Filled with a desiccant ike silica gel 4) Oiler 5) Regulator (and Gauge) a) Can be set to adjust the flow of air to the tool b) Should be located as close to the tool as possible c) Gauge that accompanies a regulator should be glycerin or oil filled to dampen needle 6) Fittings Dust Collection Systems 5 good reasons to have dust collection on each machine: 1) 2) 3) 4) 5) Fire Hazards House Cleaning Air Quality Finishing Problems Noise Reduction on Machines Important Info: In order to move wood dust efficiently through the system, the air flow needs to maintain a velocity of 3500 in main lines and 4000 CFM in branch lines. Farther away from compressor – Duct diameter reduces to maintain velocity As diameter decreases, the speed of air flow must increase in order to move the same volume of air. This principle can be used to maintain the cfm of a system when pressure loss within the ducts tries to reduce it. Machines that produce the heaviest chips – Closest to collector Machines that produce light, occasional, dust (ie. bobbin sander) – Towards the end of the run 9 5 Principle Parts of a Dust Collection System Collector ○ 3 Main functions: Separation Heavy chips drop down to storage bins below Lighter, finer particles carried up to be removed by filter bags above Pulse, air jet, cleans filter bags to help maintain effectiveness – Returned to maintain even air pressure Filtration Best filter bags made from woven felt, gauge of felt determines effectiveness Storage Hoppers – designed to allow discharge into a truck that can be stationed below it Large external units store dust in removable containers, can be switched on a regular basis Collector Hood ○ Design and position incredibly important to be effective Blast Gate ○ Design depends on equipment Allows the closing of piping without the need to turn off the system Ducting/Piping ○ Can run overhead or under the floor ○ Can be straight pipe, spiral, or flexible ○ Spiral most effective Pipe junctions and judicious use of flex hose can affect system efficiency Must gently re-direct flow of air, abrupt changes create dead air zones, allow dust to accumulate – reduced air flow 10 Fan ○ Majority ‘paddle-wheel’ variety with material passing through paddles ○ Efficiency rating should be between 50 to 60 percent 11