Inför Midterm 1 PDF
Document Details
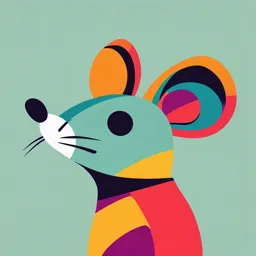
Uploaded by ImmenseMaclaurin
KTH Royal Institute of Technology
Tags
Summary
This document is a table of contents for a midterm on advanced manufacturing technology. It includes summaries of topics such as CNC machining, economics, tooling, and metrology. The document appears to be a study guide for a course.
Full Transcript
AI genererat utifrån alla dokument och gamla midterms Inför midterm 1 Table of contents: 1. CNC Machining Summary for Advanced Manufacturing Technology.......................... 3 1.1 General CNC Machining Concepts............
AI genererat utifrån alla dokument och gamla midterms Inför midterm 1 Table of contents: 1. CNC Machining Summary for Advanced Manufacturing Technology.......................... 3 1.1 General CNC Machining Concepts................................................................................3 1.1.1 Coordinate Systems and Motion Control.............................................................. 3 1.1.2 G-Codes and M-Codes.......................................................................................... 3 1.1.3 Programming Structure......................................................................................... 4 1.1.4. Tool Offsets and Compensation........................................................................... 4 1.1.5 Machining Cycles..................................................................................................4 1.1.6 Advanced Concepts...............................................................................................5 1.2: Lab-Specific CNC Machining Information.................................................................. 5 1.2.1 The "Crazy Cube" Project..................................................................................... 5 1.2.2 Machining Operations........................................................................................... 5 1.2.3 Coordinate Systems and Rotary Axes................................................................... 6 1.2.4 Tools and Cutting Data..........................................................................................6 1.2.5 Key Programming Tips......................................................................................... 7 2. Economics of Machining......................................................................................................8 2.1 PowerPoint Presentation Summary (Expanded)............................................................ 8 2.1.1 Importance of Machining Economics................................................................... 8 2.1.2 Key Factors in Machining Economics.................................................................. 8 2.1.3 Cost Breakdown.................................................................................................... 8 2.1.4 Time Calculations..................................................................................................9 2.1.5 Taylor's Tool Life Equation...................................................................................9 2.1.6 Optimization Strategies......................................................................................... 9 2.1.7 Tool Wear and Failure........................................................................................... 9 2.1.8 Concluding Remarks............................................................................................. 9 2.2 Exercise Steps and Purpose..........................................................................................10 2.2.1 Data Sheet Overview...........................................................................................10 2.3 Mandatory Reading on Tool Wear - Detailed Summary.............................................. 11 2.4 Supporting Reading on Machining Economics............................................................12 2.4.1 Key Cost Components.........................................................................................12 2.4.2 Optimizing Machining Economics......................................................................13 For Minimum Cost:...................................................................................................... 13 For Maximum Production Rate:...................................................................................13 2.4.3 High-Efficiency Machining Range..................................................................... 14 3. Detailed Metrology and Interferometry Summary......................................................... 15 3.1 Fundamentals of Metrology......................................................................................... 15 3.1.1 Measurement Systems and Traceability..............................................................15 3.1.2 Important Measurement Tools.............................................................................16 3.2 Measurement Errors and Uncertainty...........................................................................16 3.3 Interferometry...............................................................................................................17 3.3.1 Basic Principles................................................................................................... 17 3.3.2 Types of Interferometers..................................................................................... 17 3.3.3 Applications in Engineering................................................................................17 3.3.4 Considerations in Interferometry........................................................................ 18 3.3.5 Advanced Applications....................................................................................... 18 4. Coordinate Measuring Machines (CMM)..................................................................................... 19 4.1. CMM vs. Traditional Measurement Methods....................................................................19 4.2. Principle of Operation........................................................................................................19 4.3 Geometric Elements in Measurement................................................................................. 19 4.4. Example: Tolerance Verification........................................................................................20 4.5. History of CMM Development.......................................................................................... 20 4.6. Types of CMMs................................................................................................................. 20 4.7. Probing Methods................................................................................................................ 21 4.8. CMM Components.............................................................................................................21 4.9. Probing Calibration............................................................................................................ 21 4.10. Key CMM Techniques..................................................................................................... 21 4.11. 5-Axis Probing................................................................................................................. 22 4.12. Measuring Setup Tips...................................................................................................... 22 4.13. Common Errors and Uncertainty..................................................................................... 22 4.14. Environmental Effects......................................................................................................22 4.15. Calibration and Verification............................................................................................. 23 4.16. Reporting and Analysis....................................................................................................23 1.CNC Machining Summary for Advanced Manufacturing Technology 1.1 General CNC Machining Concepts 1.1.1 Coordinate Systems and Motion Control Cartesian Coordinate System: CNC motion is based on a 3D Cartesian coordinate system (X, Y, Z). Machine Coordinate System (MCS): Where the axes reach their global zero position. Workpiece Coordinate System (WCS): A point selected by the programmer on the part, stock, or fixture. 1.1.2 G-Codes and M-Codes Common G-Codes Code Description G00 or G0 Rapid positioning G01 or G1 Linear interpolation G02 Circular interpolation (clockwise) G03 Circular interpolation (counterclockwise) G17 XY plane selection G90 Absolute dimensioning G91 Incremental dimensioning Common M-Codes Code Description M3 Spindle start (clockwise) M5 Spindle stop M6 Tool change M8 Coolant on M9 Coolant off M30 Program end 1.1.3 Programming Structure 1. Program start 2. Load tool 3. Spindle start 4. Coolant on 5. Rapid to position above part 6. Machining operations 7. Coolant off 8. Spindle off 9. Retract to safe position 10. End of program 1.1.4. Tool Offsets and Compensation Tool length compensation Tool radius compensation (G41/G42) Tool offset call (D) 1.1.5 Machining Cycles Drilling cycles (e.g., CYCLE82) Tapping cycles (e.g., CYCLE84) Pocket milling cycles (e.g., POCKET3, POCKET4) Pattern cycles (e.g., HOLES2, CYCLE801) 1.1.6 Advanced Concepts 5-axis machining (using A and C axes) Modal and non-modal commands Subroutine calls (e.g., MCALL for modal cycle calls) 1.2: Lab-Specific CNC Machining Information 1.2.1 The "Crazy Cube" Project Workpiece: Aluminum block 90 x 90 x 90 mm One side pre-machined with four tapped holes for mounting 1.2.2 Machining Operations Face Milling Machine five remaining sides to 85 mm ± 0.1 mm Use face mill (80 mm diameter) Multiple passes required Flatness requirement: 0.02 mm Surface roughness: Ra 3.2 Bearing Seats Two opposite cylindrical pockets Depth: 8 mm (+0.05/-0.15 mm) Diameter: 35 mm (M7 tolerance) Use POCKET4 cycle Central hole: 21 mm diameter (H11 tolerance) Use CYCLE82 for drilling Third Bearing Seat Base diameter: 28 mm (M7 tolerance) Central hole: 12 mm diameter (H8 tolerance) Options for central hole: 1. Twist drill (11.7 mm) + Reamer (12 mm H8) 2. Carbide twist drill (12 mm) Rectangular Through Pocket Length: 62 mm, Width: 60 mm Corner radius: 10 mm Use POCKET3 cycle Machine from both sides Max axial depth of cut: 5 mm per pass Threaded Hole Patterns Two patterns of four M6 threaded holes each Drill depth: 13 mm, Thread depth: 10 mm Use center drill for spot drilling View A: Use HOLES2, CYCLE82, CYCLE84 View F: Use CYCLE801, CYCLE82, CYCLE84 1.2.3 Coordinate Systems and Rotary Axes G505 - G509 for different cube faces A and C axes for 5-axis positioning Example: ○ G505: A0 C0 ○ G506: A-90 C0 ○ G507: A-90 C90 ○ G508: A-90 C180 ○ G509: A-90 C270 1.2.4 Tools and Cutting Data Tool Type Name Size Speed Feed (mm/min) (mm) (RPM) Face mill FACEMIL 80 3000 1800 L80 Centre drill CENTERD 12, 90° 7500 375 RILL Twist drill (HSS) DRILL5 5 2000 100 Twist drill (HSS) DRILL11 11.7 2000 100 Reamer (H8) REAMER 12 800 240 Delta drill DRILL20 20 3000 150 Tap tool TAP_M6 M6 1000 1000 End mill MILL16 16 7500 1150 (surface) / 750 (depth) Twist drill (Carbide) DRILL12 12 6500 325 1.2.5 Key Programming Tips Use G00 for rapid positioning and G01 for machining movements Program 4th and 5th axes (A and C) using absolute dimensions (G90) Reposition A axis after each tool change Use appropriate cycles for different operations (POCKET3, POCKET4, CYCLE82, CYCLE84, HOLES2, CYCLE801) Implement modal calls (MCALL) for repeated cycle operations Set _ZSD=0 before using POCKET3 for center point dimensioning 2. Economics of Machining 2.1 PowerPoint Presentation Summary (Expanded) 2.1.1 Importance of Machining Economics Machining operations are crucial for many automotive parts Machining typically takes longer than forming or shaping processes There's a constant need to reduce non-cutting time Material waste is inevitable in machining, emphasizing cost considerations 2.1.2 Key Factors in Machining Economics 1. Equipment and Tools: ○ Machine tools ○ Work holding devices and fixtures ○ Cutting tools 2. Labor and Costs: ○ Direct labor costs ○ Overhead associated with indirect costs 3. Time Factors: ○ Setup time for each process ○ Material handling time (loading/unloading) ○ Gauging time for dimensional accuracy and surface finish ○ Cutting and non-cutting times 2.1.3 Cost Breakdown Total machining cost per piece (C_p) is divided into: 1. Machining cost (C_m): ○ C_m = T_m (L_m + B_m) ○ T_m: Machining time per piece ○ L_m: Labor cost per hour ○ B_m: Burden rate (overhead) 2. Setup cost (C_s) 3. Loading/unloading cost (C_l): ○ C_l = T_l (L_m + B_m) ○ T_l: Time for loading/unloading and setting parameters 4. Tooling cost (C_t): ○ C_t = [T_c (L_m + B_m) + D_i] / N_i + [T_i (L_m + B_m)] / N_e ○ T_c: Time to change insert ○ T_i: Time to index insert ○ D_i: Insert depreciation ○ N_i: Number of parts per insert ○ N_e: Number of parts per insert edge 2.1.4 Time Calculations Total time per part: T_p = T_l + T_m + T_c/N_i + T_i/N_e Machining time for turning: T_m = πLD / fV ○ L: Length of cut ○ D: Workpiece diameter ○ f: Feed rate ○ V: Cutting speed 2.1.5 Taylor's Tool Life Equation VT^n = C T = (C/V)^(1/n) Used to relate cutting speed (V) to tool life (T) C and n are constants depending on tool material, work material, and cutting conditions 2.1.6 Optimization Strategies 1. Optimum Cutting Speed and Tool Life for Minimum Cost: ○ Derived by differentiating C_p with respect to V and setting to zero 2. Optimum Cutting Speed and Tool Life for Maximum Production: ○ Derived by differentiating T_p with respect to V and setting to zero 3. High Efficiency Machining Range: ○ Balances cost and production rate 2.1.7 Tool Wear and Failure Types of wear: Flank wear, crater wear, thermal cracking Catastrophic tool failures: Fracture, temperature-related failures Importance of monitoring and predicting tool wear for optimal machining 2.1.8 Concluding Remarks Emphasizes the importance of identifying all relevant parameters Stresses the need to determine various cost factors Highlights the significance of accurate time measurements Notes that small changes in cutting speed can significantly affect cost or production rate 2.2 Exercise Steps and Purpose The exercise involves optimizing cutting parameters for turning a steel bar. Key steps include: 1. Calculating economical tool life (T_e) 2. Determining economical feed and cutting speed without technical constraints 3. Calculating feed and speed with technical constraints (power, surface roughness, max force) 4. Comparing different machining strategies (e.g., single 8mm cut vs. two 4mm cuts) 5. Analyzing costs for different tool grades (P30 vs. P10) Purpose: To apply theoretical concepts to a practical scenario To understand the trade-offs between different machining parameters To learn how to optimize for minimum cost or maximum production rate To appreciate the impact of tool selection on overall machining economics 2.2.1 Data Sheet Overview The data sheet (RO653) provides material-specific information crucial for machining calculations: Key Information: Material properties (e.g., specific cutting force, exponents) Tool characteristics (e.g., costs, max loads, geometries) Machine specifications (e.g., power, costs) Uses: 1. Input for Taylor's tool life equation 2. Calculating maximum allowable feed rates 3. Determining power constraints 4. Estimating tool wear and life 5. Cost calculations for different machining strategies The data sheet allows for personalized problem-solving by providing unique input values based on the student's birth date, ensuring that each student works with a slightly different scenario while applying the same principles. 2.3 Mandatory Reading on Tool Wear - Detailed Summary Tool wear is a critical factor in machining operations, significantly impacting tool life, surface quality, dimensional accuracy, and overall machining economics. The primary causes of wear include high localized stresses at the tool tip, elevated temperatures (especially along the rake face), and friction from chip and workpiece sliding against the tool. Flank wear, occurring on the relief face of the tool, is one of the most common types of wear. It results from the tool rubbing against the machined surface and is exacerbated by high temperatures. Flank wear is often used as a criterion for tool life and is described by Taylor's tool life equation: VT^n = C, where V is cutting speed, T is tool life, n is an exponent dependent on conditions, and C is a constant. This equation highlights the inverse relationship between cutting speed and tool life, a crucial consideration in optimizing machining processes. Crater wear, another significant type, forms on the rake face of the tool. It's primarily attributed to a diffusion mechanism, where atoms move across the tool-chip interface. As temperature increases, crater wear accelerates rapidly, changing the tool-chip interface geometry and affecting cutting performance. Both flank and crater wear can be mitigated to some extent by applying protective coatings like titanium nitride or aluminum oxide to the tool. Other wear types include nose wear (rounding of the tool tip), notch wear (at the depth-of-cut line), and edge chipping. Nose wear affects chip formation and can lead to rubbing instead of cutting, potentially inducing residual stresses on the machined surface. Notch wear can weaken the tool tip, leading to gross chipping, especially in brittle tool materials. Chipping, a sudden loss of tool material, is particularly problematic as it can drastically alter the tool geometry and worsen surface finish. Tool condition monitoring is essential in modern machining, especially with automated systems. Methods include direct optical measurements and indirect techniques like monitoring cutting forces, power consumption, or acoustic emissions. These systems help predict tool failure and optimize tool usage, crucial for maintaining production efficiency and part quality. The following table summarizes key wear types and their implications: Wear Location Primary Causes Implications Type Flank Relief face Rubbing, high Gradual tool deterioration, used for Wear temperatures tool life criteria Crater Rake face Diffusion, high Changes tool geometry, affects chip Wear temperatures flow Nose Tool tip Mechanical and thermal Affects surface finish, can induce Wear effects residual stresses Notch Depth-of-cut Work hardening, Can lead to tool tip fracture Wear line oxidation Chipping Cutting edge Mechanical shock, Sudden geometry change, poor thermal fatigue surface finish Optimizing machining processes involves balancing cutting speed with tool life. While higher speeds increase productivity, they also accelerate wear. The concept of an optimum cutting speed aims to maximize material removal while maintaining acceptable tool life. This balance is crucial for economic machining, especially in high-volume production environments. Understanding these wear mechanisms and implementing effective monitoring and optimization strategies are essential for modern manufacturing. They enable manufacturers to improve productivity, ensure consistent part quality, and manage tooling costs effectively in an increasingly competitive industrial landscape. 2.4 Supporting Reading on Machining Economics The economics of machining is crucial for balancing productivity, cost-efficiency, and quality in manufacturing processes. Despite limitations like longer processing times and material waste compared to forming or shaping, machining remains essential for producing complex parts with high dimensional accuracy and surface finish. 2.4.1 Key Cost Components The total machining cost per piece (Cp) is composed of four main elements: Cp = Cm + Cs + Cl + Ct Where: Cm = Machining cost Cs = Setup cost Cl = Loading/unloading cost Ct = Tooling cost These components can be further broken down: 1. Machining cost: Cm = Tm(Lm + Bm) ○ Tm = Machining time per piece ○ Lm = Labor cost per hour ○ Bm = Machine burden rate (overhead) 2. Loading/unloading cost: Cl = Tl(Lm + Bm) ○ Tl = Loading/unloading time 3. Tooling cost: Ct = [Tc(Lm + Bm) + Di]/Ni + [Ti(Lm + Bm)]/Nf ○ Tc = Insert change time ○ Ti = Insert indexing time ○ Di = Insert depreciation cost ○ Ni = Number of parts per insert ○ Nf = Number of parts per insert face 2.4.2 Optimizing Machining Economics The goal is to minimize the cost per piece or maximize the production rate by finding the optimum cutting speed (Vo) and optimum tool life (To). For Minimum Cost: Vo = C^(1/n) * [ ((1-n)/n) * ((Tc(Lm + Bm) + Di)/m + Ti(Lm + Bm)) / (Lm + Bm) ]^(-1/n) To = (n/(1-n)) * ((Tc(Lm + Bm) + Di)/m + Ti(Lm + Bm)) / (Lm + Bm) For Maximum Production Rate: Vo = C^(1/n) * [ ((1-n)/n) * (Tc/m + Ti) ]^(-1/n) To = (n/(1-n)) * (Tc/m + Ti) Where: C and n are constants from the Taylor tool life equation (VT^n = C) m is the number of insert faces actually used 2.4.3 High-Efficiency Machining Range The range between the optimum speed for minimum cost and the optimum speed for maximum production rate is known as the high-efficiency machining range. Operating within this range balances cost and productivity effectively. 3. Detailed Metrology and Interferometry Summary 3.1 Fundamentals of Metrology Metrology, the science of measurement, forms the backbone of modern manufacturing and quality control. At its core is the ISO-GPS (Geometrical Product Specification), an internationally accepted concept that governs all requirements indicated on technical drawings. This system ensures consistency and precision across different manufacturing environments and countries. Key aspects of ISO-GPS include: Standard Reference Temperature (ISO 1): Fixed at 20°C for all geometrical specifications GPS Tolerancing Model: Defines how tolerances should be given on technical drawings Geometric Tolerances: Specified using symbols and frames for various tolerance types The GPS system is crucial because it allows engineers and manufacturers to communicate precise requirements for parts and products. For instance, the position of a hole might have different meanings depending on whether it's specified by dimensional tolerances or positional tolerances. GPS aims to represent requirements in a way that's closer to functional intentions and less ambiguous. 3.1.1 Measurement Systems and Traceability A universal measurement system relies on three key prerequisites: 1. An international coherent system for units (SI) 2. The ability to compare measurements from different places and times (traceability) 3. A unified way of expressing uncertainties (GUM - Guide to the expression of uncertainty in measurement) Traceability is particularly important. It ensures that measurements made in a workshop can be traced back through a chain of increasingly precise references, ultimately to the international standards maintained by the Bureau International des Poids et Mesures (BIPM). This chain typically looks like: Workshop → Certified laboratory → National Measurement Institute → BIPM This system ensures that measurements made anywhere in the world are comparable and reliable. 3.1.2 Important Measurement Tools Several tools are fundamental to metrology: Gauge Blocks: These precision-ground blocks of steel or ceramic play a crucial role in calibration. They can be "wrung" together to create combined lengths, allowing for a wide range of precise measurements. Calipers: Common measuring tools that use either a vernier scale or, more commonly now, a digital readout. While versatile, they are subject to certain errors like parallax. Micrometers: More accurate than calipers, micrometers follow Abbe's Principle, which states that the measuring scale should be in line with the length being measured. This design reduces certain types of measurement errors. 3.2 Measurement Errors and Uncertainty Understanding errors and uncertainty is crucial in metrology. Errors fall into three main categories: 1. Known systematic errors 2. Unknown systematic errors 3. Random errors Two common types of errors that often occur in measurements are: Cosine Error: Occurs when there's a misalignment between the measured and intended distance. This typically results in a measurement that's longer than the true value. Sine Error: Results from misalignment perpendicular to the direction of measurement. This can lead to significant errors, especially in precision measurements. Uncertainty in measurements is different from error. It quantifies the doubt about the measurement result. Uncertainties are typically categorized as: Type A: Evaluated using statistical methods from repeated measurements Type B: Estimated from other information, such as calibration certificates or manufacturer specifications When expressing measurement results, it's important to include: 1. The measurement value 2. The associated uncertainty 3. The coverage factor (k) 4. The confidence level For example: "The length of the part is 20 cm ± 1 cm (k=2, 95% confidence level)" 3.3 Interferometry Interferometry is a powerful measurement technique based on the principle of wave interference. It's particularly useful for high-precision measurements in engineering and scientific applications. 3.3.1 Basic Principles Interference occurs when two or more waves superpose, resulting in a new wave pattern. This can be: Constructive interference: When waves are in phase, amplitudes add Destructive interference: When waves are out of phase, amplitudes subtract 3.3.2 Types of Interferometers 1. Michelson Interferometer: This classic design uses a beam splitter and two mirrors, one of which is movable. It's fundamental to understanding many interferometry applications. The Michelson interferometer can measure very small displacements, down to a fraction of the wavelength of light used. 2. Fabry-Pérot Interferometer: Consists of two parallel reflecting surfaces. It's particularly useful for analyzing the spectrum of light, making it valuable in spectroscopy and telecommunications. 3. Heterodyning Interferometer: This advanced technique mixes two close frequencies to produce a measurable beat frequency. It's less sensitive to light intensity variations and provides higher resolution, making it ideal for precision engineering measurements. 3.3.3 Applications in Engineering Interferometry has numerous applications in engineering, particularly in precision measurement and quality control: 1. Length Measurement: Laser interferometers can measure distances with extremely high accuracy, often used in calibrating machine tools and coordinate measuring machines (CMMs). 2. Angular Measurement: Specialized optical components allow interferometers to measure very small angular displacements. 3. Straightness Measurement: Used to assess the quality of linear motion in machine tools and other precision equipment. 4. Squareness Measurement: Helps in checking the perpendicularity of machine axes, crucial for maintaining accuracy in multi-axis machines. 3.3.4 Considerations in Interferometry Several factors must be considered for accurate interferometric measurements: Environmental Factors: Temperature, pressure, and humidity affect the wavelength of light, requiring careful compensation. Deadpath Error: In relative measurements, there's often an uncompensated distance that can introduce errors. Abbe Error: Occurs when there's an offset between the measurement line and the axis of motion, leading to angular errors being amplified. 3.3.5 Advanced Applications One of the most impressive applications of interferometry is the LIGO (Laser Interferometer Gravitational-Wave Observatory) project, which won the Nobel Prize in Physics in 2017. LIGO uses extremely sensitive laser interferometry to detect gravitational waves, providing new insights into the nature of the universe and confirming predictions of Einstein's general theory of relativity. Understanding these principles and applications of metrology and interferometry is crucial for engineers and scientists working in fields requiring high-precision measurements and quality control. 4. Coordinate Measuring Machines (CMM) A Coordinate Measuring Machine (CMM) is a highly accurate and versatile device used in industrial metrology to measure the physical geometry of an object. It operates by capturing the 3D coordinates of points on the surface of a workpiece using a probing system. The measured points are then used to assess the object’s dimensions and verify tolerances. CMMs are especially valuable in manufacturing environments where precision is critical, such as the automotive, aerospace, and medical industries. Initially used primarily in quality control labs, CMMs are now increasingly integrated directly into production lines to enable real-time quality monitoring. 4.1. CMM vs. Traditional Measurement Methods Before CMMs became widely available, manufacturers relied on manual measuring tools like calipers, micrometers, rulers, and height gauges. These instruments, while still useful, have limitations in accuracy and repeatability. The reliability of manual tools is significantly affected by operator skill and consistency, leading to variations in measurement outcomes. For instance, two different technicians using the same caliper may record slightly different results, introducing a level of uncertainty. CMMs eliminate much of this operator-induced variability, as they automate the measuring process, making it more reliable and repeatable. 4.2. Principle of Operation The operation of a CMM follows a systematic process: 1. Measurement Planning: Before any measurements are taken, the features of the object that need to be measured are identified. This involves selecting specific points or surfaces to probe and deciding which type of probe or sensor is most suitable for the task. 2. Measuring Points: Once the plan is in place, the CMM probes the workpiece, recording the coordinates (X, Y, Z) of specific points on the surface. In some cases, additional data, such as the surface normal vector, may also be captured to better define the geometry. 3. Data Processing: After the measurements are completed, the CMM software processes the captured points, fitting them to ideal geometrical shapes like planes, cylinders, or circles. These shapes are then used to verify whether the actual dimensions of the part fall within the specified tolerances. This process allows for the precise assessment of complex geometrical features and ensures that manufactured parts meet strict quality standards. 4.3 Geometric Elements in Measurement In CMM operations, different geometrical elements of a part are measured and evaluated individually. These include: Spheres: Portions of spherical surfaces can be measured, such as ball bearings. Cylinders: Cylindrical surfaces like shafts or bores can be accurately assessed. Planes: Flat surfaces are often measured to verify flatness and orientation. Cones and Tori: Complex surfaces, such as tapered holes or toroidal surfaces, can also be analyzed. A critical aspect of CMM use is understanding how to define and measure geometric elements. For instance, when measuring the diameter of a hole (inside diameter), the CMM calculates the largest inscribed circle. For shafts (outside diameter), it calculates the smallest circumscribed circle. These standard practices help ensure consistent and accurate measurements. 4.4. Example: Tolerance Verification A common application of CMMs is verifying whether a part meets its specified tolerances. For example, a CMM can be used to check if a cylinder’s centerline is perfectly perpendicular to a reference plane. In this scenario, the machine would measure multiple points along both the plane and the cylinder, calculate the ideal geometric elements (a plane and a cylinder), and then determine whether the centerline of the cylinder fits within the tolerance zone defined by the designer. This process is invaluable because even the most advanced manufacturing equipment cannot produce a part exactly to the design specification. CMMs allow manufacturers to assess whether deviations are within acceptable limits, ensuring both functionality and quality. 4.5. History of CMM Development The development of CMMs coincided with advancements in numerically controlled machine tools. Early CMMs from the 1950s and 1960s were manually operated, with operators physically moving the probe over the part and recording measurements. The first computer-controlled CMMs appeared in the 1970s, significantly improving accuracy and usability. Rolls Royce and Renishaw were pioneers in developing the touch-trigger probe during this time, which revolutionized the industry by allowing automated point capturing, reducing human error, and increasing measurement speed. 4.6. Types of CMMs CMMs come in various designs, tailored to different measurement needs and part sizes: Bridge-type: A common design where the probe moves in three axes along a bridge structure, allowing precise movement over the workpiece. Cantilever: A single-arm CMM used for smaller parts. Gantry-type: Large machines used for measuring large objects, such as car bodies, often found in automotive or aerospace industries. Articulated Arm: This type moves through angular joints rather than along straight axes, making it more flexible for measuring parts with complex shapes or awkward orientations. 4.7. Probing Methods Probes are essential for CMM measurements and come in different types depending on the application: Mechanical Probing: This involves direct contact with the workpiece. ○ Touch-trigger probes capture single points when the probe touches the surface. They are commonly used for inspecting features like holes or edges, where discrete measurements are sufficient. ○ Scanning probes continuously measure surfaces as the probe moves along the object. These are ideal for capturing detailed surface profiles or assessing the form of complex shapes, such as turbine blades. Optical Probing: Used when the workpiece is too soft or delicate to be probed mechanically. Optical systems can measure without contact but generally offer lower accuracy compared to mechanical probes. 4.8. CMM Components A typical CMM consists of several key components: Probe: The part of the CMM that makes contact with the object or scans its surface. Surface Plate: Usually made of granite to provide a stable and precise reference surface. Frame: Supports the probe’s movement along three orthogonal axes (X, Y, Z), allowing it to position the probe accurately over the object. Control Software: The software is responsible for managing the probe’s movements, recording data points, and performing geometric calculations. 4.9. Probing Calibration Each probe or stylus used on a CMM must be carefully calibrated. Calibration involves measuring a reference object, such as a sphere, to determine the exact dimensions and form of the stylus tip. This ensures that the measurements taken during actual use are accurate and consistent. Calibration is essential, especially when using different stylus orientations, as any deviation can lead to incorrect measurements. 4.10. Key CMM Techniques CMMs employ various techniques for different tasks: Touch-trigger Probing: Ideal for simple geometric measurements, where the probe captures individual points on a surface. This method is less expensive and causes minimal wear on the stylus. Scanning Probes: These capture a continuous stream of data, making them better suited for form and profile measurements. While more accurate and faster, scanning probes are more expensive and can cause more wear to the stylus. 4.11. 5-Axis Probing Advanced CMMs with 5-axis probing can significantly increase the speed and accuracy of measurements. In traditional 3-axis systems, the entire machine must decelerate and reaccelerate as it moves along the workpiece, introducing errors due to frame movement. In 5-axis systems, the probe head does most of the work, allowing the machine frame to remain stationary or move at a constant speed, thus improving accuracy and enabling high-speed scanning without compromising precision. 4.12. Measuring Setup Tips Setting up a CMM for measurement requires careful consideration to minimize errors: Minimize Setups: Reducing the number of setups reduces the risk of misalignment and other errors. Datum Features: Choose datum points carefully, as they define the part’s reference coordinate system. Ensuring proper alignment with the datum points on the drawing is essential to achieving accurate measurements. Fixture Use: Ensure that the workpiece is held securely but without excessive force that could distort the part or introduce errors into the measurements. 4.13. Common Errors and Uncertainty Several types of errors can occur during CMM measurement: Cosine Error: Happens when the measurement direction is not perfectly aligned with the object, leading to overestimated distances. Sine Error: Occurs when there is a misalignment perpendicular to the measurement direction, potentially causing significant deviations in the measurement results. CMMs also come with inherent uncertainty, which manufacturers specify as Maximum Permissible Error (MPE). This value includes several factors, such as temperature and vibration, that can affect the machine’s performance. 4.14. Environmental Effects CMMs are sensitive to environmental factors. Variations in temperature, humidity, or vibration levels can distort the measurements. For example, temperature changes can cause slight expansions or contractions in both the machine and the workpiece, which may lead to inaccuracies. Thus, CMMs should be used in controlled environments where these variables are minimized. 4.15. Calibration and Verification Calibration and verification of CMMs are performed using reference objects, such as gauge blocks, which are known to have precise dimensions. For larger machines, laser interferometers are used to measure and verify their accuracy. This process ensures that the CMM is functioning correctly and delivering reliable measurements. 4.16. Reporting and Analysis After the measurements are taken, the CMM software analyzes the data