Advanced Machining Test #1 Winter Semester 2024 PDF
Document Details
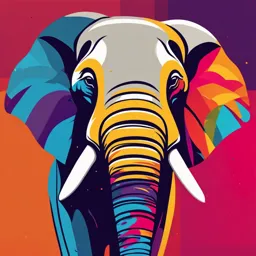
Uploaded by AttractiveJaguar
Algonquin College
2024
Prof. Nick Schafer
Tags
Summary
These are notes for Advanced Machining Test #1, covering various topics in machining. The notes detail different types of machines and their functions, including panel processing machines like rolling table saws and wall panel saws, as well as CNC panel saws/beam saws, and lumber machines.
Full Transcript
Advanced Machining Test #1 WINTER SEMESTER 2024 INSTRUCTOR: Prof. Nick Schafer [email protected] Panel Processing Machines Machines Made to Process Sheet Goods (Plywood, Fiberboard, Melamine Boards, Particle Board) Rolling Table Saw Function: - Designed for the conversion of sheet stock -...
Advanced Machining Test #1 WINTER SEMESTER 2024 INSTRUCTOR: Prof. Nick Schafer [email protected] Panel Processing Machines Machines Made to Process Sheet Goods (Plywood, Fiberboard, Melamine Boards, Particle Board) Rolling Table Saw Function: - Designed for the conversion of sheet stock - Platform moves with the wood - Blades usually 14” diameter - Not used for cutting solid wood stock, saw blade tooth profile designed for composite materials Components: - Rip Fence - Crosscut Fence - Scoring Saw Blades - Function: to “climb-cut” the underside of a melamine board, ensures a chip-free kerf cut 1 - Runs in the opposite direction - Set 2mm above table surface - 2 separate blades - Three types: Matched, Split Sets, and Conical Dangers: - Does not have a break, continues to spin after main blade has stopped - Rolling Table - Console Controls (in decimal inches) - Blade Angle - Blade Height - Rip Fence Position Wall Panel Saws Function: - Same as rolling table saw - Triple Chip Grind tooth profile preferred - Gravity holds panels against wall Advantages: - Requires more than ⅕ of the space required for a rolling table saw Disadvantages: 2 - User fatigue - Gravity closes kerf gap when cutting lengthwise CNC Panel Saw/Beam Saw Function: - Designed to make through cuts Advantages: - High production machine (5 cuts at once) Disadvantages: - Absolutely massive Lumber Machines Ironwood Up-Cut-Saw Function: - Designed to process rough lumber - Saw blade is 18” Advantages: - Kickback is minimal to none due to clamping guard - Boards of equal width can be cut stacked - Saw will not open if blade access is open Disadvantages: - 3 Uses pneumatic pistons, can be incredibly irritating to fix when things go wrong Rip Saw Types: - Gang Rip Saws - Multiple saw blades used to separate stock into predetermined widths - Straight Line Rip Saws - Single blade - Also known as a “Glue Line Rip Saw” Components: - Conveyor belt - Saw location identification lasers on newer machines - Hold-down rollers - Rip fence - Anti-kickback fingers - Control panel Scroll Saw Function: - Designed for very intricate patterns such as on clocks - Associated with hobbyists - “Pierce-work” - Blade must be threaded through every single hole in whatever design is being made - 4 Body position is important to prevent future back problems Components/Additives: - Blade changing mechanism - Sanding attachment - Ability to tilt table Band Saw Function: - Originally designed to cut large logs - Sized by wheel diameter - No chance of kickback due to blade running down Components: - Table insert - Must be removed in order to change blade - Thrust block - - Blade guides - - - Prevents blade from being pushed off wheels Prevents excessive twisting of blade Tooth Shapes: - Regular, 0 degree hook angle - Skip Tooth, also known as “Buttress Tooth” - Hook Tooth, positive hook angle “Three Wheeled Bandsaw” - Provides greater depth between blade and support arm, but flexes the blade more frequently, usually leading to increase blade breakage 5 Drill Press Function: - Designed to drill perfectly perpendicular holes (unless table is tilted) - Fastened to the floor for safety and security - Jig is used to hold stock firmly and increase accuracy when drilling large holes Components: - Step Pulley - Quill - Quill Lock - Jaw Chuck (3 holed, singular holed, or keyless chuck) - - **Must be tightened in all holes** - Do not leave the chuck key in the chuck Attachments: - Mortise bit - - Sanding drum - - - Drill press not made to withstand large amounts of vertical pressure Drill press not made to withstand lateral pressure/flexing of spindle Circle Cutter - Designed to cut large diameter circles - Cutting action described as “scrapping” - **Clamps are holding everything down** Safe-T-Planer - Can be used to create raised and fielded panels, requires head of drill press to be angled slightly Drill Bits for Drill Press: - Drill bits with ‘lead’ screws cannot be used in drill press - - Standard Twist Bit - 6 Will ‘self-feed’ and potentially draw themselves too quickly into stock Workhorse of the industry - - - Designed primarily for drilling non-ferrous metals - Tips are sharpened to an angle of 112 to 118 degrees - Ideal angle for wood is between 60 to 82 degrees - Many cabinetmakers regrind their bits to suits wood only Bullet Bits - Developed by Black and Decker - Use the web of bit to increase performance of drill bit - Web usually does no cutting and can inhibit action of bit - By mounting smaller bit to web, increases efficiency of bit Brad Point Bits - Designed for dowel holes - Spurs score outsides of hole before cutting lips remove stock, leaves clean, straight hole - Do not wander in end grain Forstner Bits - Do not require a center point to hold in place - - - - 7 Performed by knife edge of bit - Good for drilling ‘off-center’ holes, enlarging holes, and drill holes at an angle - Provide a clean, smooth hole with a flat bottom - Designed to be used in a drill press, not a hand-held drill Multi-Spur Machine Bits - Similar to Forstner - Cannot be used ‘off-center’ or drill at an angle Spade Bits - Used where a quick, rough hole is required - Long center point allows holes to be drilled at shallow angles - Some come with spurs to create slightly cleaner hole Screw Drills - Commonly used in portable drills, can be used in drill press - Most manufactured to match specific sizes of screws that will inhabit the hole - “Counter-sink” screws - - Vix Bit - Used to center hole in piercings of hinge leaves - Exterior sleeve is spring loaded Plug Cutters - Can only be used in drill press - - No center point to hold in place Once plug is framed, can be released from stock by levering out with screwdriver or ripping stock on band saw - - - Rosette Cutterhead - Used to create details to compliment architectural mouldings - Should only be used in drill press Hole Saws - Designed for portable drill, frequently used in drill press - Must be backed out of hole frequently to clean tooth gullets of sawdust - Carbide tipped ‘saws’ available for melamine and similar material boring Spear Point Glass Drill Bits - Best used in drill press, tendency to wander in portable drill - Drilling action is by abrasion, lubricant required - - Applying too much pressure to bit will crack glass being drilled Drill Bit Shanks - Usually designed to fit a ⅜” or ½” chuck - - If bit is larger is diameter, shank will be reduced in size to fit Advantage of flat faces is reduced tendency to slip in chuck when drilling tough stock Pin Routers Overhead Pin Router 8 ○ Built solid, arm that supports quill/collet subjected to large amounts of stress ○ Commonly used for electric guitar bodies ○ Router is on top, pin (below) follows template attached to underside of stock Inverted Pin Router ○ Pin is mounted above, bit is buries and raised pneumatically ○ Easier to follow template as it is visible ○ Safer since router bit is buried beneath stock Main Takeaway: There are 2 different kinds of pin routers, know them. Everything else is useless. Spindle Shapers Purpose: To impart a shaped edge, or face, to stock => Mouldings Basic Shaper => A motor and spindle for mounting cutterblocks Other forms ○ ‘Spring hold-downs’ => holds stock close to cutterblock ○ Sliding table and hold-down clamp for stock on sliding table ○ CNC Shaper ○ Double Spindle Shapers ○ Tilting Arbor Shaper ○ Power Feeder => Grabs onto stock when ‘climb-cutting’ is done ‘Climb-cutting’ => When stock is cut with the rotation of the cutterblock, incredibly dangerous without power feeding Fence’s can be moved separately for full edge removal Short pieces must be done on a jig Accessories Cutterblocks ○ Solid Profile Cutters Used for most common shapes, for shapes run frequently and consistent 9 ○ Circular Blocks ○ Stacked Cutterblocks ○ For complicated profiles Usually have disposable insert knives Slot Spindle or French Head Scrapes instead of cuts, best suited for contrary woods (ie. bird’s eye maple, ribbon strip mahogany and curly woods) ○ Square Block Reserved for use on heavy moulding runs, replaced by stackable circular blocks ○ Stair Trencher (Groover) Can be buried beneath stock Similar in nature to an inverted router bit Designed for the cutting of tread and riser grooves in a stair stringer Guards ○ ○ ○ Cage Guard Surrounds cutter block with steel cage Protects operator from accidental contact with cutter Shaw Guard Guides stock against fence and table Difficult to finish cut due to lack of access Tunnel Guard ○ ○ Used when a large cutter demands a wide opening Sacrificial fence, creates a zero-clearance fence Loses some cutting depth Auxiliary Fence When tall, narrow stock demands an addition to regular fence Other ○ Grinder for profiled knives ○ Guarantees each knife is ground exactly the same as the previous one Ring Fence 10 Similar to shaw guard Break Through Fence Fucking illegal Acts as a ‘lead-in’ for stock in order to ease material onto cutterblock ○ Ball Bearing Rub Collar ‘Donkey’s Ear’ Mortising Machines 5 Main Machines: Hollow Chisel Mortiser Chain(saw) Mortiser Slot Mortiser Maka Mortiser (niche) Alternax Mortiser (niche) Hollow Chisel Mortiser Function Single fluted auger bit runs through hollow chisel Bit cuts circle, chisel cuts corners Problems if chisel and bit not correctly adjusted: ○ Burning of both chisel and bit ○ Fracture of chisel Clearance between chisel and bit must be maintained to avoid damage Combination Mortising Machine => Machines equipped with both Hollow Chisel mortising bits and Chain Mortising capabilities Chain(saw) Mortisers Function 11 Commonly used for through mortising in windows and door construction Mortise size is adjusted by employing chains of varying width and thickness Difficulties with tearout on exit, pressure block used Accessories include wide guide bars Slot Mortisers Function Commonly employed by the chair making industry Create a short ‘stub’ mortise that can be used in small stock frequently found in chair construction Corresponding tenoner that creates rounded tenon to match slot created Maka Mortiser Function Used for small mortise creation, restricted by length and thickness of Maka chisels Alternax Mortiser Function Functions similar to oscillating tools except a chisel is used ○ Chisel movements reverse at end of each swing stroke Common Problems with Mortising Machines 12 Chain slack Poor chip breaker Worn guide-bar roller Chisel set out of square ‘Climb’ in slotting due to overfeed Oversize slot due to overcramping Tenoning Machines - Meant for Production Lines Tablesaw tenoning jigs exist => Designed for single tenons Single-Ended Tenoner Basically a fancy shaper, functions similarly Double-Ended Tenoner Capable of multiple operations Not restricted to creating tenons on end of stock Slot Tenon Machine 13 Companion machine to Slot Mortiser, commonly used for chair construction Portable Machines Circular Saws/Skill Saws Function: - Designed to cut an array of different materials (plastic, metal, wood, etc.) - Light Duty versions are one handed and use a direct-drive, blade runs (**good face is down**) - Heavy Duty versions are two handed and use a worm-drive, blade is backwards and runs down - Blade must project at least ¼” below material to ensure proper cut Advantages: - Portable - Incredibly versatile Disadvantages: - Blade is hidden, incredibly dangerous if not careful - Designed for right-handed use Mitre Saws Not to be confused with a “Chop Saw” that is used for metal Function: - Designed to cut mitres, or angled cuts, in wood 14 - Blade tilts, slides, and pivots - Direct-drive or belt-drive up - Closer to the fence, more accuracy Jig Saws Function: - An incredibly versatile machine, can be used to cut all sorts of materials - Designed specifically to cut curves.. Surprisingly Components - Most important features: Blade Support, Changing Mechanism, and Base Plate - “Puffer”, a jet of air at the sawdust ahead to keep the line visible - The narrower the blade, the tighter the radius Portable Sanders Divided into 4 main categories: - - Belt Sanders - Heavy - Light Orbital Sanders - Orbital - Random Orbital - Pad Sanders (Finishing Sanders) - Specialty Sanders Belt Sanders (Heavy) Designed to be heavy, weight of sander would apply appropriate pressure to stock surface for proper sanding Operator guides sander, does not apply pressure Used for the initial sanding of large, horizontal surfaces where stroke sander is unavailable 15 Orientation of unit is usually aligned with grain Common application: Flushing joints Trigger lock => **Make sure it is off before plugging in sander** Belt Sanders (Light) Allows for use on vertical surfaces without operator fatigue Some operator pressure required Common application: Edge sanding of table tops, counters, etc. Replacing Belt: Release tension on belt using side lever Tracking must be adjusted to ensure belt is running true, track knob located by front wheel Common belt sizes: 3” x 21” and 3” x 24” ○ Best sanders commonly referred to by belt capacity Orbital Sanders Leave orbital pattern left by disc, requires hand sanding to obscure it Random Orbital Sanders Can be used for flat and convex surfaces Air powered or electric ○ Air powered => less moving parts, consume large amounts of air, require lubricant ‘Random’ means disc does not follow purely circular path, vibrates as it rotates, obscures sanding lines Avoid lifting sander, wears pad and creates divots in stock Attaching Sanding Discs: 16 2 most common methods ○ Hook and Loop Faster ○ Pressure Sensitive Adhesive (PSA) Primary concern => Ease of sanding disc replacement Must be aligned with holes for sawdust collection bag Pad Sanders (Finishing Sanders) Sized according to fractional size of standard sheet of sanding paper Used with the grain Spring clips commonly used to secure sandpaper Smaller ¼ sheet frequently used for cutting back finishes and/or just before finish is applied Specialty Sanders Designed for specific or obscure applications Not designed for commercial duty Other Info: Crepe Rubber Cleaning Sticks => Used to clean sander belts and pads Down-draft Sanding Tables => Reduces ambient dust from powered sanding operations Do not overlook ‘sanding-by-hand’, removes marks left by powered sanders ○ Must be done using sanding block/pad, minus moulding or curved work, otherwise abrasive will remove earlywood faster than latewood, leaving ridges behind Portable Electric Drills - Corded and Battery Early Drills (‘Pump’ drills or brasen bits) were hand-held, used a counterweight to help with motion Types: 17 Standard, medium duty, corded drill Heavy duty, corded drill Heavy duty hammer, corded drill Portable electric, cordless drill Routers 3 most common routers: Plunge Routers, Regular Routers, & Laminate Trimmers Laminate Trimmers Operational single-handed Required for laminate work ○ Only trims thin (1/16”) thick material, not as large or robust ○ After initial trimming with straight bit, trimmed again with beveled bit or file Trimming Bits: ○ Typically ¼” shank small bits ○ Bevel or flush/straight Different bases for speciality applications Regular Routers Designed for creating a profiled edge ○ Most can be shaped in single pass, more complicated profiles and difficult woods require more ○ Final pass should take bite of 1/16” thick Fence Accessory => Router follows straight edge, cupped chute to direct chip disposal Collars => Attached to base of most routers, used to follow a template ○ Size of lipped opening in collar determines displacement of router bit from edge of template ○ Ie. Dovetail bits for dovetail jigs Router tables allow router to be used as mini-shaper ○ Specialty bases for specialty purposes Ie. Angled routing Plunge Routers Have ability to enter stock cleanly from face ○ 18 Bits used must cut on down-stroke and in conventional manner Adjustable depth stop Suited to handling bits with ½” shank diameter Router Bits ‘Norm’ => High Speed Steel (HSS) router bits with solid pilots Router Bit Anatomy Fluted Bits => Single or Double Shank Diameters: ○ Most common => ½” and ¼”, others available Most profiles can be found in both shank sizes Collet => Piece that bit is held by ○ Sizes and shapes vary across manufacturers and quality levels of routers ○ Ideally ½” of router bit should be held by collet ○ Curvature of router bit MUST NOT touch collet NEVER bottom out bit Reduction Sleeves => Common method of reducing capacity of collet to accommodate smaller shank sizes 19 Unlimited profiles, custom ones for specialty bits Slotting/Grooving Bits ○ ○ Used to create grooves in edge of stock for: Joints ‘T’ Mouldings Splines Bearings and cutters come in range of sizes Lock Mitre Bits ○ Single bit used to create both halves of mitre joint ○ Joint is ‘self registering’, can be clamped easily ○ Used in solid woods and composites Glue Joint Bits ○ Single profile creates both halves of joint ○ Matching ‘tongues’ almost double gluing surface Stile and Rail Cutters Panel Piercing Bits ○ ‘V’ point used to pierce laminates ○ Flat section on shank ‘follows’ cut-out in stock ○ Single flute cuts laminate flush to stock edge ○ Commonly used in laminate trimmers, fixed pilot does not burn laminate if kept moving 20 Up-Cut Spiral ○ Upward cutting flutes help pull chips from stock ○ Thrust of bit is upwards ○ Serrated edges break chips into small pieces ○ Commonly used in CNC machines Down-Cut Spiral ○ Provides downward pressure to stock ○ Serrated edges help break chips into small pieces for easier removal ○ Commonly used in CNC machines Compression Bit ○ Compresses chips from both faces toward center ○ Up-Cut and Down-Cut teeth are employed ○ Commonly used in CNC machines Sanding Machines Bobbin Sanders Also known as Oscillating Spindle Sander Function: - Commonly used to sand small curves and holes - Spindle oscillates up and down white rotating - Evens wear on sanding sleeve - Different diameter spindles available - Table can be titled for angled sanding - Available in floor mount and table top models Disc Sanders Function: - Frequently combined with belt sander - Edge of disc spins faster than inside - Designed for end grain - Only side of disc that is rotating down towards table should be used - ‘Pull’ from abrasive holds stock to table - Wrong side => Tendency to lift stock off table Pump Drum Sanders Function: - Drums inflated with air - Pressure can be varied for different tasks, less air => softer, more pliable sanding surface 21 - Designed at sanding compound curves - Can either be floor or bench mount - Dust makes used to avoid inhaling dust due to ineffective dust system Edge Sanders Function: - Designed to sand edges of wide/long stock - - Table must be angled to prevent loading of belt in one location Stock pushed down the table from back to front using gentle pressure, held against belt - - Small narrow stock or end grain => Disc sander Idler spindle not perfectly square Stroke Sanders Function: - Primarily used for sanding large flat surfaces (ie. table tops) - Profile sanders: - Shaped block used to force belt to contour of edge being sanded - Belts require special flexible backing material - Can be equipped with motors to help raise and lower them - Sanding pads can use pneumatics to maintain proper contact - Sanding belts must be spliced together, different splices used for different applications Wide Belt Machines Thickness Sanders - Also known as Abrasive Planers - Designed to reduce thickness of stock, similar to thickness planer - Typically use series of belts of progressively finer grits - Advantage over regular planers => Sanded surface with no tear-out and ability to thickness composite boards 22 Finishing Sanders - Designed for removal of small amount of material and final surface prep - Generally have more sensitive adjustments and settings than abrasive planers - Stock first passes through sanding belt, then fine belt, then denibbing wheel Other Info: - Machine load for belts measured using an Ammeter - Air jets used to help strip sawdust from belts - Arrangement of contact rolls and platens based on demands of product - Drum Sander Specialized Sanding Machines Fladder Sanders - Used for denibbing finishes or finish sanding contoured surfaces (ie. frame and panel doors) Profile Edge Sanders - Used to sand specific profile edges Narrow Belt Sanders 23 - Used for small parts and sharpening tools - Can have leather belts for stropping or polishing sharpened edges