Operations Management Study Guide PDF
Document Details
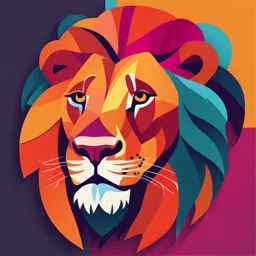
Uploaded by DarlingPlumTree
Milpark Education
Tags
Related
- BOPMAN Chapter 1 - Operations Management PDF
- Group 1 Unit 1_ Introduction to Operations Management PDF
- Introduction to Operations Management & Total Quality Management PDF
- Introduction to Operations Management and Total Quality Management PDF
- Operations Management & TQM PDF
- Operations Management Final Exam Review PDF
Summary
This study guide covers various topics in operations management, including the importance of operational management, design of operations systems and various planning strategies. It also details the module purpose and outcomes of Milpark Education's Operations Management course.
Full Transcript
Operations Management OMAN02-6 Milpark Education Email: [email protected] Address: Deneb House 3rd Floor, 368 Main Road...
Operations Management OMAN02-6 Milpark Education Email: [email protected] Address: Deneb House 3rd Floor, 368 Main Road Observatory Cape Town, 7925 PO Box 44235, Claremont, 7735 © Milpark Education (Pty) Ltd No part of this publication may be reproduced, stored in a retrieval system or transmitted in any form or by any means – electronic, electrostatic, magnetic tape, mechanical, photocopying, recording or otherwise. Information Our commitment to our students is to maintain a friendly, fast and efficient communication service. We aim to respond to queries within 48 hours (Monday to Friday, between 08:00 and 17:00). Please follow our instructions in order to have your queries addressed as soon as possible. Sometimes you may struggle with difficult parts of the module and you may feel that you are at risk of not achieving success in your course – please contact us so that we can provide the necessary assistance and support. We provide a tutor line that we encourage you to use. The promise is to come back to you within two business days. The tutor will explain aspects in the content that you may not understand well. You can use the tutor forums in the online course environment of your module – myCourses: Tutor Forum. If you are in need of any administrative help, please contact us as follows: Any administrative query – Student Support: Email: [email protected] Tutoring: The tutor will explain aspects in the content that you may not understand well. You can use the tutor forums in the online course environments (myCourses) to ask an academic query relating to your studies. Programme/academic assistance: The programme manager will assist with academic queries (please do not forward any administrative queries to programme managers). These queries are related to the programme and the modules on the programme. Help from the Library: Email: [email protected] Contact a student counsellor: Email: [email protected] © Milpark Education (Pty) Ltd Operations Management OMAN02-6 24a iii Queries related to graduations: Email: [email protected] Complaints: If you wish to raise a complaint, these are the steps to follow: 1. First raise your complaint with the specific department where the complaint arose. For example, if it is an academic complaint, first raise it with the relevant staff member in your School, for example your lecturer. 2. If it is not resolved by that person, you can escalate your complaint to the relevant Programme Manager, Head of Department or Head of School. If your complaint is still not resolved at Step 2, you can raise your complaint by sending an email to [email protected]. Do not hesitate to contact us when you are experiencing problems. Note The content in Milpark study guides and teaching documents is not intended to be sold for commercial purposes. Such content is in essence part of tuition and constitutes an integral part of the learning experience in the classroom and at a distance. Note Links to websites and videos were active and functioning at the time of publication. We apologise in advance if there are instances where the owners of the sites or videos have terminated them. Please contact us in such cases. Note A glossary is provided at the end of this study guide to clarify some important terms. © Milpark Education (Pty) Ltd Operations Management OMAN02-6 24a iv Note Any reference to masculine gender may also imply the feminine. Singular may also refer to plural and vice versa. © Milpark Education (Pty) Ltd Operations Management OMAN02-6 24a v Table of contents Heading Page number Module purpose and outcomes ix TOPIC 1 IMPORTANCE OF OPERATIONS MANAGEMENT 10 1.1 Introduction 10 1.2 Operations in the organisation 11 1.3 Scope of operations 13 1.4 Services versus goods 15 1.5 Nature of decision-making 17 1.6 Input, transformation and output process 19 1.7 The four Vs 22 1.8 Role of the operations manager 23 1.9 Performance objectives 24 1.10 Operations strategy 27 Summary 31 Self-Assessment Questions 32 TOPIC 2 DESIGN OF OPERATIONS SYSTEMS 33 2.1 Introduction 33 2.2 Process design objectives 34 2.3 Process types 35 2.4 Process mapping 37 2.5 Process performance measurement 38 2.6 Innovation and design 39 2.7 Stages of design 40 2.8 Business process re-engineering (BPR) 41 Summary 42 Self-Assessment Questions 43 TOPIC 3 SUPPLY CHAIN MANAGEMENT 45 3.1 Introduction 45 3.2 Defining supply chain management 46 3.3 Activities of supply chain management 47 3.4 Supplier selection 47 3.5 Internet and e-procurement 48 3.6 Sourcing strategy 49 © Milpark Education (Pty) Ltd Operations Management OMAN02-6 24a vi 3.7 Logistical and physical distribution management 50 3.8 Relationship between operations and supply chain 51 3.9 Supply chain in practice 52 3.10 Improving the supply chain 53 3.11 E-business in the supply chain 54 3.12 Supply chain network design 54 3.13 Forecasting in supply chain 57 Summary 58 Self-Assessment Questions 59 TOPIC 4 PLANNING AND CONTROL 60 4.1 Introduction 60 4.2 Planning and control in operations management 61 4.3 Sequencing and scheduling 63 4.4 Capacity management 64 4.5 Inventory management 67 4.6 Enterprise resource planning 71 4.7 Materials requirement planning 73 Summary 74 Self-Assessment Questions 75 TOPIC 5 QUALITY MANAGEMENT 76 5.1 Introduction 76 5.2 Characteristics of quality management 77 5.3 Total quality management 78 5.4 ISO 9000 79 5.5 Statistical process control 80 5.6 Lean synchronisation 81 5.7 Continuous improvement 83 5.8 Organising for improvement 85 Summary 87 Self-Assessment Questions 88 TOPIC 6 PLANNING FOR FUTURE CHALLENGES 89 6.1 Introduction 89 6.2 Social and economic challenges 90 6.3 Environmental challenges 92 6.4 Technological challenges 94 Summary 96 Self-Assessment Questions 97 © Milpark Education (Pty) Ltd Operations Management OMAN02-6 24a vii Glossary of terms 99 References 112 Answers to Self-Assessment Questions 115 Topic 1 Self-Assessment Answers 115 Topic 2 Self-Assessment Answers 118 Topic 3 Self-Assessment Answers 120 Topic 4 Self-Assessment Answers 122 Topic 5 Self-Assessment Answers 123 Topic 6 Self-Assessment Answers 125 © Milpark Education (Pty) Ltd Operations Management OMAN02-6 24a viii Module purpose and outcomes Operations management is concerned with designing and controlling the process of production of goods and services. An effective and efficient operations management strategy will require the continuous redesigning of business operations related to the production of goods or services. The purpose of this module is to provide a holistic picture of the field of operations management. Students will be exposed to the basic strategies that can be implemented to ensure the highest level of effectiveness and efficiency. A structured approach to managing a supply chain network will also be presented. Module outcomes are: 1. Demonstrate an understanding of the role of operations management in the overall business strategy of an organisation. 2. Evaluate the processes needed to develop a new product or service, from identifying the customer needs to delivering the final product or service. 3. Evaluate the contribution of key factors in the operations related to the production of goods and services. 4. Apply planning and control methodologies in forecasting aimed at improving operational performance. 5. Apply the basic tools and techniques to manage quality in an organisation. 6. Plan for future challenges in operations management to respond to market needs. Prescribed textbook Slack, N., Brandon-Jones, A. and Burgess, N. 2022. Operations management. 10th ed. South Africa: Pearson. Print ISBN: 9781292408248, 1292408243. eText ISBN: 97812924408217, 1292408219. © Milpark Education (Pty) Ltd Operations Management OMAN02-6 24a ix Topic 1 Importance of operations management 1.1 INTRODUCTION This topic relates to the following module outcomes: 1. Demonstrate an understanding of the role of operations management in the overall business strategy of an organisation. 6. Plan for future challenges in operations management to respond to market needs. Operations management (OM) encompasses all aspects of the running of a business and is flanked by financial management and marketing. It is the engine that transforms inputs into outputs to be sold at a profit. The profit generated through the sale of the products or services is the only source of money into a business, therefore, the faster and more efficient the material can flow through the business, the more products and/or services can be produced and the more capital the business will generate. The aim of operations management is therefore to achieve maximum efficiency, effectiveness, and productivity, at the lowest cost. Sound operations management leads to all areas of the business operating in an integrated fashion, providing a standardised high-quality product or service to the customer while ensuring that all products or services are in line with customer requirements. Operations management incorporates the entire supply chain from the first source of raw materials to the end customer. It incorporates planning, organising, leading and control. Through operations, the robustness and sustainability of the organisation will be enhanced. Operations management informs strategy and provides data upon which strategic plans can be based; it also enables and tactically implements the business strategy through operationalising unique differentiators. Competitive advantage is created and enabled. © Milpark Education (Pty) Ltd Operations Management OMAN02-6 24a 10 In this topic, you will gain knowledge in the following areas: 1. Operations management and its importance in an organisation 2. The scope of operations management and the goals thereof 3. The difference between services and goods, and the implications thereof 4. The nature of strategic, operational and tactical decision-making 5. The input, transformation and output process model 6. The four Vs 7. The role of the operations manager 8. Performance objectives 9. Operations strategy. 1.2 OPERATIONS IN THE ORGANISATION 1.2.1 Introduction The operations function is considered the engine of the business where inputs are taken and transformed into output through employing core and support processes. It is accompanied by marketing and sales, and research and development. Finance plays a role in recording historical data and providing enough data to operations to enable sound decision-making. In essence, a business consists of eight areas: 1. Research and development 2. Production 3. Supply chain and logistics 4. Quality management 5. Human resource management 6. Information and industrial technology 7. Finance 8. Marketing and sales. Research and development designs the products after collecting information, such as customer specifications, market conditions, macro-environmental analysis and micro-environmental assessments; the correct product can be delivered at the correct price, time and place by the rest of the divisions. Marketing fulfils the role of taking this well-developed product or service to the market to be sold at a profit. © Milpark Education (Pty) Ltd Operations Management OMAN02-6 24a 11 Figure 1.2 on page 8 of the prescribed textbook graphically depicts the various relationships between the different functions. Read Read pages 7 to 13 of the prescribed textbook to understand the importance and scope of operations in business. 1.2.2 Operations in all types of organisations Operational principles remain the same and can be applied in all organisations, whether service, retail, not for profit, or manufacturing. Slack, Brandon-Jones and Burgess (2022:9-11) describe what operations management does in five very different organisations and show the common themes that emerge. They conclude that operations management “uses machines to efficiently assemble products that satisfy customer demands”. In reality, operations does not just use machines, but also materials, plant and equipment, tools and human resources to produce the outputs. In Figure 1.3 on page 9 of the prescribed textbook it is shown how operations use resources to appropriately create outputs that fulfil defined market requirements. Read Read pages 8 to 11 of the prescribed textbook to understand operations management in the smaller organisation and in not-for-profit organisations. 1.2.3 The new operations agenda Operations management is ever evolving and the pressures of operations will vary from industry to industry. As operations management grows as a science, new pressures develop to which it has to respond in the market. Table 1.2 on page 13 of the prescribed textbook lists the business pressures and the relevant operational responses. It shows that operations managers cope with issues such as increased cost-based competition, higher quality expectations, demands for better service, and flexibility and choice in the market, to name but a few. For each of these trends in the market, operations has to develop a response, because it is responsible for achieving the goals and objectives of the business and, as such, deliver on the strategy. © Milpark Education (Pty) Ltd Operations Management OMAN02-6 24a 12 Activity Read the case study on MSF Operations that provide medical help to people in danger on page 10 of the prescribed textbook. What role does operations management play in delivering this type of service to various communities? Activity Watch the video at: https://www.youtube.com/watch?v=leMOReAE2hk and write down the list of elements included in operations management. Compare it to Figure 1.2 on page 8 of the prescribed textbook. 1.3 SCOPE OF OPERATIONS Operations directs and implements the corporate vision and strategy of the business. Operations, research and development, finance and marketing should cooperate in an integrated manner to ensure aligned commitment towards achieving the corporate strategy. Figure 1.1 shows a model of a business format where research and development is at the centre, with the “engine” of operations surrounding it, bound together by marketing, communications and sales. © Milpark Education (Pty) Ltd Operations Management OMAN02-6 24a 13 Figure 1.1 Business model Source: Wright (2012) Kruger, Ramphal and Maritz (2013) postulate that the scope of operations is defined as all activities involved in the creation, operation and improvement of processes and procedures devoted to the production and delivery of the principle products or services of an organisation. A business can be seen as a system with a purpose of generating profit. Operations is responsible for keeping the system working at a pace that will see all demand fulfilled with supply, while adhering to the principles of operations management. The rate of production should equal the rate of demand from the customers. Table 1.1 below explains the subject matter and measures to be undertaken in order to achieve these principles. © Milpark Education (Pty) Ltd Operations Management OMAN02-6 24a 14 Table 1.1 Principles of operations management Principles Subject matter Measures Effectiveness Design of processes Product performance Improving processes Service performance Managing quality Process capability Service quality Customer approval rate Expanding new products and allegiances Voice of the customer Theory of constraints Efficient Set up reduction Lean measures Theory of constraints Learning curves Project management Cycle time and lead time Time-based compensation Mass customisation Low cost Capacity management Inventory counting Supply chain management Forecasting Inventory management Equipment utilisation Design for manufacture Costing Demand management Robust Green supply chain Risk assessment Failure mode and effects Environment analysis Triple bottom line Health and safety Income statement Balanced score card Safety failures Operations strategy Source: Kruger et al. (2013) 1.4 SERVICES VERSUS GOODS The principles of operations management are as applicable in the service industry as in manufacturing or retail. There are very few pure services or pure product companies. If a product is provided there normally is some service that has to accompany the product. When a service is rendered a product is sometimes included, such as in the hotel industry where food and cosmetics are supplied. The objective is to provide a standardised high quality product or service according to customer specifications. Service quality should not vary in relation to the employee rendering the service. Every interaction with the company should be the same and should be in accordance with the company culture and standards and not according to the © Milpark Education (Pty) Ltd Operations Management OMAN02-6 24a 15 employee’s skill or attitude. Employee training and induction therefore becomes of utmost importance. Table 1.2 below provides a summary of the differences between products and services. Table 1.2 Difference between goods and services Services Goods Intangible Tangible Provided by service organisation Produced by manufacturer Impossible to store Can be stored, but this does not necessarily happen, e.g. Boeing does not have a finished goods warehouse since they make to order Cannot be transported Can be transported Consumption and production Delay between production and happen simultaneously consumption Lose value rapidly Maintain value much longer Likely to be unique Less likely to be unique Interaction between customer and Little or no contact between customer provider high and manufacturer Participation of customers in the Little or no participation of customer service Facility of the service near customer Centralised away from customer Labour intensive Processed Difficult to measure quality Easier to measure quality Server determines standard of Does not depend on one person quality Cannot measure output accurately Easier to measure output Source: Kruger et al. (2013) From the table it is clear that the core difference between services and goods is that goods are tangible and services are intangible. Services are dependent on human resources and products are dependent on physical production processes. The emerging model of operations, however, is that every organisation is a service business. Every core service, which is what the organisation provides the market in order to generate profits, is accompanied by value-added services that make the external customer’s life easier or assist employees in carrying out their particular function (Chase, Jacobs and Aquilano, 2004). © Milpark Education (Pty) Ltd Operations Management OMAN02-6 24a 16 According to Chase et al. (2004), service organisations are classified into four categories: 1. Information 2. Problem-solving 3. Sales 4. Field support. In a company providing a product the service excellence will become the unique differentiator for the business. Example McDonald’s was founded in 1940 by Richard and Maurice McDonald. The business grew to being the 8th largest employer in the United States. McDonald’s is a perfect example of a product versus service mixture. The company prides itself on its fast and efficient service. https://www.mcdonalds.com Activity Watch the video at https://www.youtube.com/watch?v=nG5-52a5lRo and compare the differences between a service and a production business. 1.5 NATURE OF DECISION-MAKING The ability to make sound business decisions is the main factor contributing to business success. A business or operations manager that can collect the relevant data, collate and analyse the data and then base business decisions upon such information will have the ability to steer the business in the right direction. Operational decisions are taken at various levels: strategic, operational and tactical. The operational decisions taken throughout the organisation are informed by the operational strategy which, in turn, is informed by the corporate strategy. Process decisions have to be in line with the company’s broader strategy, the operations strategy, and the process strategy that will drive company objectives © Milpark Education (Pty) Ltd Operations Management OMAN02-6 24a 17 such as high quality, price leadership, efficient logistics and customer satisfaction. According to Krajewski, Malhorta and Ritzman (2016), the four main process decisions are: 1. process structure 2. customer involvement 3. resource flexibility 4. capital intensity. Decision-making spans all areas of the business, including decisions such as facility location, capacity, forecasting, quality management techniques, inventory, production, such as make-or-buy decisions, and supply chain. According to Burt, Dobler and Starling (2003), supply chain managers and organisations should focus their decision-making process on proactively improving and optimising their supply processes. There are many tools and techniques to enhance decision-making in the business. The first decision strategists and operations managers have to make concerns the competitive advantage. The competitive advantage is what will drive customers to buy from the business rather than from its competition. Activity Watch the video at https://www.youtube.com/watch?v=_-ats2oej5s and reflect on how you would drive buying decisions through competitive advantage. A convenient way to make decisions is through a decision tree. A decision tree is a schematic model of alternatives available to the decision-maker along with the consequences of each choice. A decision tree is composed of decision nodes with branches to and from the nodes. Squares represent decision points and circles represent chance events. Branches from decision points show the choices available to the decision-maker. The probability of each event occurring is entered together with the financial consequence thereof. In order to solve a decision-tree problem, the decision- maker has to work from the end of the tree backwards. The expected values are multiplied by the probability to determine the value of each decision. The branch with the highest value is chosen. © Milpark Education (Pty) Ltd Operations Management OMAN02-6 24a 18 Activity Watch the video at https://www.youtube.com/watch?v=a5yWr1hr6QY for a quick tutorial on how to use decision-tree analysis as a decision-making tool. Example of a decision-tree diagram Source: Sigma zone (2017) It is clear that business management, and especially operations management, involves many decisions to be made at every point of the day. Operations managers must base decisions on correct input data, use the relevant tools and technologies and make decisions that will work towards achieving the business vision and mission 1.6 INPUT, TRANSFORMATION AND OUTPUT PROCESS According to Slack et al. (2022), all operations create and deliver services and products by transforming inputs into outputs. Figure 1.6 on page 12 of the prescribed textbook shows the transformation process model. Each product, business or industry will have its own set of inputs and outputs according to its customers’ demands. Figure 1.2 below is another depiction of the input-transformation-output model: © Milpark Education (Pty) Ltd Operations Management OMAN02-6 24a 19 Figure 1.2 Transformation process Source: Kruger et al. (2013) Essentially the model is about using raw materials as supplied by suppliers and transforming these materials into a service or a product (outputs) which will be sold at a profit. It is important to note that the profit made on each unit is the only source of funding for a business and has to be used to cover fixed costs such as rent, salary, water and lights, insurance and many more. Inputs will be in the form of materials, information, processes and customers. Table 1.3 on page 13 of the prescribed textbook shows the predominant outputs from materials, information or customers. Read Read pages 13 to 15 of the prescribed textbook to understand the nature of inputs. Outputs will be the result of the process. As previously discussed, the outputs for services and product companies will vary. Some operations will produce a service and others will produce a product, but mostly it will be a mix of service and product. Table 1.3 on page 20 of the prescribed textbook shows some of the operations described in terms of their processes. © Milpark Education (Pty) Ltd Operations Management OMAN02-6 24a 20 Activity Read the short case about Marina Bay Sands Hotel on page 14 of the prescribed textbook and reflect on the inputs that the hotel would use in order to provide their outputs. Note the relationship between services and products in the outputs. The process hierarchy Within the input-transformation-output model there is a collection of processes. Such processes must be integrated throughout the organisation, starting with a price-to-payment process; in other words, what happens with the material, information or customer from the point where a quote or price is given to when the customer has been fully serviced to his satisfaction. According to Slack et al. (2022), a process is an arrangement of resources that creates some mixture of service and products. These resources are the building blocks of all operations. Process development is more comprehensively addressed in Topic 2. Read Read pages 19 to 27 of the prescribed textbook to understand the process hierarchy and how it is relevant to all parts of the business. Pay careful attention to Table 1.4 on page 22 to see examples of non-operations functions. Activity Consider the inputs that are required for a retail business such as Pick n Pay. Focus on the peripheral inputs other than the actual products they sell, as these inputs are vital in providing the products to the market. Activity Watch the video at https://www.youtube.com/watch?v=6fYGAOynqfo for more examples of inputs versus outputs. © Milpark Education (Pty) Ltd Operations Management OMAN02-6 24a 21 1.7 THE FOUR VS Operations have different characteristics. These characteristics are classified as volume, variety, variation and visibility. 1. High volume production will require repeatability in the process of production. Standardisation will become a focus as a high volume of products is produced at a pace to match the demand for the product. High volume would normally be in contrast with variety, as it would be nearly impossible to produce high volume and high variety. High volume can be described as lots of products produced in a similar process, providing a standardised product, normally through line or continuous production. 2. The variety dimension relates to the variety of goods to be produced, therefore a range of products which differ in form and format is being produced. This process must be flexible and requires good communication. A production process that has to cope with variety would normally use a job or a batch process, which will be further discussed in Topic 2. 3. The variation dimension speaks to variation in demand. This requires operations managers to vary the capacity of production. Capacity planning becomes a focus of production, as being over or under capacity will have financial consequences for the business. Techniques such as smoothing of capacity will be employed. 4. The visibility dimension is how involved the customer is in the production of the product or delivery of the service. In a medical practice, the service cannot be performed unless the customer is present. The customer experiences the full delivery of the service. In high-visibility operations, the customer will have a relatively shorter waiting tolerance and has to be serviced in a reasonable time frame. Activity Read the short case about two very different hospitality operations on page 24 of the prescribed textbook and reflect on the main differences in the operations management challenges facing the two hotels. © Milpark Education (Pty) Ltd Operations Management OMAN02-6 24a 22 In some cases, such as in an airline, there is a mix between high and low visibility; for instance, customers experience the service of being flown from one city to another, but the preparation of the plane, the fuelling, and the preparation of the food which will be served are invisible to the passengers. Slack et al. (2022) hold that the four dimensions have implications for the cost of creating and delivering a service or a product. Read Read pages 22 to 28 of the prescribed textbook to fully understand the four Vs of operations. Focus on Figure 1.4 on page 21, taking note of the implications of the position on the scale from high to low on operations. Activity Read the worked example on page 21 of the prescribed textbook together with Figure 1.11 on page 25 for a clearer understanding of the four Vs in operations. 1.8 ROLE OF THE OPERATIONS MANAGER The role of the operations manager varies from business to business, but there are similar activities in any business that an operations manager has to do in a skilful manner. According to Slack et al. (2022), the operations manager is responsible for designing and directing the overall nature and strategy of the operation, designing the services, products and processes, planning and controlling process delivery, and developing process performance. The management of operations includes the entire supply chain. The focus of the operations manager includes production, resource allocation (including human resources), quality control, technology, supply chain and logistics. It is up to the operations manager to ensure a smooth flow of material, information and customers, remove duplications and bottlenecks from the system and ensure that a standardised high quality of product is delivered to every customer at the right time and place and at the right price. The operations manager must endeavour to remove as much waste and variance as possible from the business. © Milpark Education (Pty) Ltd Operations Management OMAN02-6 24a 23 The objective of operations management is to increase efficiency, effectiveness and productivity, at minimum cost. Activity Watch the video at https://www.youtube.com/watch?v=AbDUEpFrIy4 for more information about the role of the operations manager. 1.9 PERFORMANCE OBJECTIVES 1.9.1 Introduction As mentioned above, the object of operations is to improve the throughput of material, information and customers at lower cost. The more efficiently the material and work can flow the faster the products can be sold to the market and the more profit will be generated. 1.9.2 Importance of operations performance Operations management can make or break an organisation. The operations function has an effect on every facet of the business. Operations managers have to cope with changes in the market, as well as in the micro and macro environment, to ensure that the business remains stable and the flow is uninterrupted. The operations manager is expected to plan, lead, organise and control the entire operation of the business. This management function is not just to ensure maximum profit, but also to enhance the other two facets of the triple bottom line: people and planet. The sustainability of the business in looking after the environment and communities internally and externally will add to the corporate standing of the business and enhance its ability to interact with stakeholders. Read Read pages 39 to 63 (Chapter 2) of the prescribed textbook to understand the importance of operations in business performance. © Milpark Education (Pty) Ltd Operations Management OMAN02-6 24a 24 Note The market includes competitors, customers and suppliers. The micro environment includes every aspect of internal business management. The macro environment is the external environment within which the business operates and includes the political, environmental, societal, technological, economic and legal conditions. Study Figure 2.3 on page 40 of the prescribed textbook on stakeholder groups with typical operation objectives. Also, take note of Figure 2.4 on page 44 to learn how operations can contribute to financial success through low costs, increasing revenue, lowering risk, making efficient use of capital and building the capabilities for future innovation. 1.9.3 Operations can affect revenue Read Read pages 44 to 45 of the prescribed textbook. 1.9.4 How is operations performance judged at an operational level? According to Slack et al. (2022), assessing performance at a societal level and judging how well an operation contributes to strategic objectives are clearly important, particularly in the longer term, and form the backdrop to all operations decision-making. But running operations at a day-to-day level requires a more tightly defined set of objectives. These are called operations ‘performance objectives’. There are five of them and they apply to all types of operations. Read Read pages 45 and 46 of the prescribed textbook on what kinds of things you are likely to want to do in order to satisfy customers and contribute to competitiveness. © Milpark Education (Pty) Ltd Operations Management OMAN02-6 24a 25 1.9.5 Performance objectives The ultimate objective of operations management is to satisfy the customer to ensure repeat business and the retention of customers. The five operations performance objectives are: 1. doing things right – working towards zero defect. 2. doing things fast – the pace of production must match the pace of demand. 3. doing things on time. 4. changing and improving what needs to be improved. 5. doing things at the lowest possible cost. 1.9.6 Why is quality important? In order to improve productivity it is necessary to measure efficiencies. The output from the operation formula to measure productivity is. It is important to note input to the operation that outputs are everything that the business gets paid for, in other words income, and inputs are everything the business pays for, in other words expenses. Productivity can be measured in financial terms or in units of measure. To improve the productivity ratio, the cost of inputs can be decreased or the amount of outputs can be increased without increasing the inputs. Activity Refer to Figure 2.5 on page 46 of the prescribed textbook and determine how quality means different things in different operations. Activity See the worked example on pages 57 to 58 of the prescribed textbook. Practise these exercises in order to become familiar with the measurement of productivity. All operational improvements and achievements of the objectives will affect costs. In order to improve costs the business has to eliminate all waste, such as wasting of time. A reduction in inventory through faster operations and improvement in dependability and flexibility will allow the organisation to adapt © Milpark Education (Pty) Ltd Operations Management OMAN02-6 24a 26 to changing circumstances as fast as possible. See Figure 2.10 on page 57 of the prescribed textbook in order to understand the effect of performance objectives on the cost structure of the business. 1.10 OPERATIONS STRATEGY 1.10.1 Introduction Slack et al. (2022) describe strategy as setting broad objectives that direct an enterprise towards its overall goal, and then planning the path in order to achieve the objectives. Strategy addresses long-term goals and deals with the organisation as a whole, rather than individual activities. The corporate strategy is based on information as extracted from operations. Once developed, operations will break the corporate strategy into manageable smaller tasks to be executed in line with corporate strategy. Operations strategy will flow from the corporate strategy. It is what operations management does to ensure that the corporate strategy is implemented while remaining customer focused. Operations strategy should ensure that the vision, mission and objectives of the organisation are achieved. Customer needs should drive the operations strategy. The operational environment changes continuously and the sustainability of organisations unaware of and not adapting to these changes will be seriously compromised. Furthermore, organisations should focus on their core competencies in order to grow the business and perform optimally. Note Operations strategy is not the same as corporate strategy, but the two strategies should be in line with each other. Similarly, process strategy is not the same as operations strategy but forms part thereof. Read Read pages 72 to 101 (Chapter 3) of the prescribed textbook to get a full understanding of the concept of operations strategy. © Milpark Education (Pty) Ltd Operations Management OMAN02-6 24a 27 The strategy of operations management should ensure that operations are directly responsible for competitive success. The most basic role of operations is to implement strategy. It should also support the business strategy and drive strategy by giving it a unique and long-term advantage over competitors. Four different theories on operations strategy emerge from literary research. The four strategies are graphically depicted in Figure 3.3 on page 76 of the prescribed textbook. Steps to develop operations strategy include: 1. Ensure that corporate objectives are clearly defined. This forms the basis for the overall strategy and defines the boundaries within which the organisation intends to function. Factors considered for the corporate objectives are issues such as the state of the economy, market conditions and opportunities, levels of competition, capabilities of suppliers and the availability of skills. 2. Develop a market strategy specifying which products and/or services will be sold to which market segments. Issues to be addressed are customers’ buying behaviour in each market segment, volumes, mix, and key competitors. The strategy should also address how each market segment will be reached, from both an awareness as well as a selling point of view. The strategic task of operations is to meet the order qualifiers in a market segment, and to improve on the order winners and be better than any competitor, to win orders. 3. Establish the order qualifiers and order winners; this becomes the common ground between marketing and operations and creates the language for communication between these two functions (and other functions). 4. Translate the identified order winners and order qualifiers into a number of strategic operational decisions, namely the selection of an appropriate process choice, the role of inventory, insourcing/outsourcing decisions (make/buy) as well as where to establish which size capacity. 5. Translate the operations strategy to capacity infrastructure and infrastructure support in terms of decisions regarding number, skill levels and location of people, which facilities and equipment are required, which levels and types of inventory will be kept and where, what the detailed information requirements are, and which utilities would be required in what quantities. In essence, it involves the detail. © Milpark Education (Pty) Ltd Operations Management OMAN02-6 24a 28 1.10.2 Market requirements-based strategies In order to achieve business success, it is necessary to service the market according to its requirements. The market will therefore influence the operations strategy and the performance objectives. Operations managers should continuously seek opportunities to improve the ability of the organisation to create order winners. ‘Order qualifiers’ refers to the basic requirements to be met for doing business with a potential customer. Order winners have created unique differentiators which make their business or market offering desirable and set them apart from competitors. According to Krajewski et al. (2016), an order winner is a unique differentiator, a reason for a customer to choose the product or service over that of a competitor. Such differentiators can come in the form of price leadership, superior quality, a product feature, superior logistics and reliability or after-sales service. Activity Read the worked example about the innovation at Micraytech on page 63 of the prescribed textbook where the firm management has to decide which operational structure will best service the different requirements of customers. Activity Read about the competitive priorities and capabilities of Starbucks at http://om4010team5fa2013.blogspot.co.za/p/competitive-factors-prioities.html 1.10.3 Product/service lifecycle influence Understanding where in the lifecycle the product or service is will enable operations managers to understand the behaviour and requirements of current and potential customers. Study Figure 3.8 on page 83 of the prescribed textbook to fully understand the effect of the product/service lifecycle on operations performance objectives. © Milpark Education (Pty) Ltd Operations Management OMAN02-6 24a 29 The phases of the lifecycle are introduction, growth, maturity and decline. The operations objectives will change depending on the stage of the business services and products. 1.10.4 Operations resource perspective The operations resource perspective holds that the way a firm applies its resources will have a significant impact on the strategic success. It also holds that the impact of the operations resource capabilities will be at least as great as that which the firm gets from its market position. In other words, to achieve operational success, organisational resources have to be developed. Study pages 87 to 91 of the prescribed textbook to determine how resources can be developed. The business has to develop the capabilities in order to service its target market and understand the resource constraints therein. The intangible assets, especially the ability to transform inputs and add value to unlock capital, have to be understood. The business that accumulates better or more appropriate resources will gain sustainable competitive advantage. 1.10.5 Strategy formulation According to Slack et al. (2022), the formulation of operations strategy is categorised in four steps: 1. Formulation 2. Implementation 3. Monitoring 4. Control. A good strategy will be assessed according to whether it is comprehensive, coherent, includes correspondence and identifies critical issues. Implementation is the way in which the strategy is operationalised in order to ensure that the vision and objectives are being achieved. During the monitoring phase, the ongoing performance is tracked to ensure that required changes are made. In order to control the rollout of the strategy the results need to be evaluated. Study pages 97 to 99 of the prescribed textbook to understand strategy formulation. © Milpark Education (Pty) Ltd Operations Management OMAN02-6 24a 30 Activity Watch the video at https://www.youtube.com/watch?v=EQCo-7SMJ_c to understand the difference between operations and strategy. Summary In this topic, it became clear that sound operations management can create competitive advantage, improve efficiency, effectiveness and productivity and decrease cost in order to enhance profitability. We learnt that operations have to function in an integrated manner with finance, marketing and sales. Furthermore, we found that, according to Slack et al. (2022), operations and the processes that make up both the operations and other business functions are transformation systems. This topic showed us that operations is about taking inputs, transforming it through adding value and producing a product or a service that can be sold for a profit. We also discussed the differences between services and products, and the impact these differences have on operations. We found out that the scope of operations management extends throughout the organisation and covers business areas such as production, supply chain, quality control and human resource management. Operations management is both strategic and tactical in nature and it is the effective running of the entire engine of the business in order to take inputs, add value through transformation and provide a standardised, quality output to be sold at a profit. Operations management concerns increasing volume and variety according to the customers’ requirements, while maintaining quality. We also learnt that the resource-based view holds that the resources need to be managed in terms of how they are directed, how they are designed, how delivery is planned and controlled and how they are developed and improved (Slack et al., 2022). We studied a general model of operations management to examine how operations fit together as a whole and the important decisions that should be of interest to all managers of operations. There are various tools, such as the decision tree, that can assist operations managers in making sound business decisions. We finally came to the conclusion that the nature of operations management is that important business decisions have to be taken on an ongoing basis. Each decision has huge consequences on the profitability and other success factors of the business. © Milpark Education (Pty) Ltd Operations Management OMAN02-6 24a 31 Self-Assessment Questions 1. Each part of the input-transformation-output process should be aligned and contribute towards the achievement of the corporate and operations strategy. Devise an interview schedule with at least five questions you would ask an operations manager on the plan they would use to ensure this alignment. 2. Operations management has to be integrated with all the different departments of an organisation. A lack of integration will lead to misalignment and result in over- or under-stocking. Do you think there are any links between operations and marketing? In your view, how can operations be integrated with marketing and sales? How can this enhance the success of the business? 3. Strategists will decide on the competitive advantage the business will use to gain market share. As an operations manager, you would be responsible for ensuring such a competitive advantage is gained. How would you ensure that the processes contribute towards the competitive advantage of the organisation? 4. The nature of operations will differ according to whether a service or a product is offered to the market. Does the introduction of a new service or product impact on operations management in a company? Use examples of products and/or services to support your view. © Milpark Education (Pty) Ltd Operations Management OMAN02-6 24a 32 Topic 2 Design of operations systems 2.1 INTRODUCTION This topic relates to the following module outcomes: 3. Evaluate the contribution of key factors in the operations related to the manufacturing of products and services. 6. Plan for future challenges in operations management to respond to market needs. Processes have to be designed to enable an organisation to take inputs and transform them into outputs following a certain methodology. Outputs can be sold at a profit, which is the only source of income in any business. Process decisions have to be in line with company strategy and should drive company objectives. According to Slack et al. (2022), any process should be judged on its quality, speed, dependability, flexibility and cost performance. The design should be done in such a way that products and services can be created effectively and efficiently. The four main process decisions are: 1. the process structure 2. customer involvement 3. resource flexibility 4. capital intensity. Processes are designed according to the volume, variety, variation and visibility of the product or service. The process design will determine the look, arrangement and workings of the organisation. It is important to understand that process design and service design are interrelated, that is, by designing the process, the service is inherently designed. It is about the flow of materials, information, work activities and the customer through the organisation. The process design should focus on the reduction of waste and disruptions, such as bottlenecks, duplication of activities, and waiting in the system. © Milpark Education (Pty) Ltd Operations Management OMAN02-6 24a 33 The objective of good process design is therefore for activities to follow each other without any interruption such as waiting for components and without any idle time. The flow should be smooth and only directed towards delivering a high- quality, standardised product or service to the end customer. In this topic, you will gain knowledge in the following areas: 1. Process design objectives 2. Process types 3. Volume–variety effect on process design 4. Product–process matrix 5. Process mapping 6. Process performance measurement 7. Little’s law 8. Innovation and design 9. Stages of design 10. Reducing design complexity 11. Business process re-engineering (BPR). 2.2 PROCESS DESIGN OBJECTIVES The objective of process design is to make sure that the performance of the process is appropriate for the output it wants to produce. The faster a request from customers can be fulfilled, the faster money can be earned by the organisation. The process design should enable the competitive advantage, such as low price or good quality. Table 6.1 on page 181 of the prescribed textbook shows the impact of strategic performance objectives on process design objectives and performance. Such objectives can include quality, speed, dependability, flexibility or cost. Operations managers should also consider micro performance objectives such as throughput rate, cycle time, throughput time, number of items in the process (work in process) and the resource utilisation. It is about ensuring standardised, stable and predictable processes. Process design ensures that all activities in the organisation are performed in a similar way, in other words a “common sequence of activities, methods and use of equipment” (Slack et al., 2022). Environmental protection is becoming more important and has to be taken into account when designing processes. Environmental legislation guides the process. Issues to be taken into account are the source of inputs, quantities and sources © Milpark Education (Pty) Ltd Operations Management OMAN02-6 24a 34 of energy consumed, amounts and types of waste material, the life of the product and the termination of the product. After the overall design has been done, the individual activities must be placed into the optimum sequence and resources allocated to allow for smooth production processes. Read Read pages 179 to 186 (Chapter 6) of the prescribed textbook to fully understand the objectives of process design. Activity Read “Operations in practice: Abantwana Bethu: Helping children in distress” on page 180 of the prescribed textbook and reflect on possible solutions for the flow of funds and assistance and reduction of costs which are spiralling. 2.3 PROCESS TYPES While it is clear that process design should take ethical and environmental elements into consideration, the type of organisation and the products and services it renders will direct the process design. There are various trade-offs between the various factors. 2.3.1 Volume–variety effect on process design Processes range from high-volume production to low-volume production, such as the production of a boat in a job shop production system. Processes can also range from high to low variety. High variety would normally see low volume, while high volume is produced in a low-variety environment. See Figure 6.4 on page 186 of the prescribed textbook to understand the various process types in production and services. Process types are project processes, job processes, batch processes, mass processes (or line production) and continuous processes, whereas services are characterised as professional services, service shops and mass services. © Milpark Education (Pty) Ltd Operations Management OMAN02-6 24a 35 Example In the medical field, high-volume, low-variety services include immunisation programmes, whereas low-volume, high-variety services include operations designed specifically to meet the needs of a patient. Read Read pages 185 to 189 of the prescribed textbook for more information on process types and the volume–variety trade-off. 2.3.2 Product–process matrix To decide upon the structure of process design, various factors are taken into account, such as the need for customisation, volumes of product to be produced and the nature of the product. These factors are typically determined by considering the order qualifiers and order winners as defined by a specific market segment. Figure 6.5 on page 190 of the prescribed textbook depicts the process– product matrix for manufacturing. The underlying idea of the product–process matrix is that many of the more important elements of process design are strongly related to the volume–variety position of the process (Slack et al., 2022). Example See the worked example on page 192 of the prescribed textbook, which shows how the product–process matrix can be used to design appropriate processes. Read Read pages 189 to 192 of the prescribed textbook for more information on the product–process matrix. © Milpark Education (Pty) Ltd Operations Management OMAN02-6 24a 36 Activity View the video at https://www.youtube.com/watch?v=m62whN6CWBM and reflect on the various production processes. 2.4 PROCESS MAPPING There are four steps in documenting processes: 1. Observing 2. Mapping the flowchart 3. Analysing the flowchart for efficiency 4. Continuously improving. The objective of process mapping is to find out exactly how a business executes activities in delivering or manufacturing a service or a product. According to Krajewski et al. (2016), flowcharts trace the flow of information, customers, equipment and materials. There are various types of flowcharts, such as the Swim Lane Flowchart. The service blueprint is used in the service industry and shows which processes are activities that have high customer interaction. The sum of the activities will complete the task. See Figure 6.7 on page 193 of the prescribed textbook to see a process map for an ‘enquiry to delivery’ process at a stage lighting operation. Different levels of process mapping are used, from high-level or ‘price to payment’ to detailed maps of each activity. In some instances, it is necessary for the process to be visible in order to enhance the customer’s understanding of the process. In Figure 6.9 on page 195 of the prescribed textbook, three levels of visibility are shown. Example See Figure 6.8 on page 194 of the prescribed textbook for an example of the ‘supply and install’ operations process mapped at three levels. © Milpark Education (Pty) Ltd Operations Management OMAN02-6 24a 37 Activity Watch the video at https://www.youtube.com/watch?v=RQSh2CyxdiA and reflect on the pitfalls of process mapping and how to avoid them. Read Read pages 193 to 195 of the prescribed textbook to fully understand process mapping and the different levels thereof. 2.5 PROCESS PERFORMANCE MEASUREMENT Processes are measured according to various metrics such as throughput time, cycle time and work in progress. Throughput time is the time between items entering the process and leaving it. Cycle time is the average time between items being processed, and work in progress is the number of items within the process at any given time. Formulas used to determine the process efficiency are: Work content Throughput efficiency = × 100 Throughput time Time adding value Value-added throughput efficiency = Throughput time Items produced Output Productivity = Inputs consumed = Inputs Actual rate Efficiency = Designed production rate × 100 Little’s law Little’s Law is based on the mathematical relationship of: Throughput time = work-in-process × cycle time. This formula can be applied to any stable process. The theory is based on the assumption that the average number of items in the system is the product of the average rate at which items leave the system and the average time each one spends in the system. © Milpark Education (Pty) Ltd Operations Management OMAN02-6 24a 38 Read Read pages 196 to 201 of the prescribed textbook to fully understand process performance measurement and analysis. Activity Calculate the worked examples on pages 198 to 200 of the prescribed textbook in order to fully understand the application of the formulae. Activity Study the case study “Efekto – making seasonal changes” on page 211 of the prescribed textbook and reflect on the Action Response Applications Processing Unit (ARAPU) case study. 2.6 INNOVATION AND DESIGN Design is concerned with putting new ideas into practice and innovation is about introducing new ideas. It is about doing things differently and in a better way. According to Slack et al. (2022), innovation is about doing something new and design is to conceive the looks, arrangement, and workings of the novel idea. When new ideas are introduced, the impact thereof normally follows an S-curve. Introducing a new idea requires time, effort and resources. Performance will increase in relation to the growth in knowledge and experience. With maturity comes limits and it becomes more difficult to improve performance. See Figure 4.3 on page 112 of the prescribed textbook for more information on the innovation S-curve. Due to the critical role innovation plays in the achievement of business success, it is important to understand what makes some companies more successful at innovation than others. The Henderson-Clark model splits innovation into incremental and radical innovation: incremental innovation is built upon existing components and architectural knowledge, and radical innovation changes both components and architectural knowledge. © Milpark Education (Pty) Ltd Operations Management OMAN02-6 24a 39 Read Read pages 111 to 114 of the prescribed textbook for a deeper understanding of the relationship between innovation and design. Activity Read the case study “The slow innovation progress of the zip fastener” on page 112 of the prescribed textbook. Example Watch the video at https://www.youtube.com/watch?v=B4ZSGQW0UMI&t=293s for examples of innovation. 2.7 STAGES OF DESIGN Design itself is a process and there are various steps of design. Figure 4.5 on page 115 of the prescribed textbook shows the product and service design innovation activity as a process. The design activity passes through several key stages. The sequence of these stages is shown on page 119 of the prescribed textbook in Figure 4.7. The first step is concept generation where innovative ideas are born and inspiration for new services or products is found. There are various sources of inspiration such as customers, competitor activity, employees, and research and development. The greater community, especially customers or users of the system, service or product, can also inspire innovation. Crowdsourcing has become easy with the internet and social media, and it is possible to receive input from international sources. The second stage in design is concept screening, during which designs and new innovation will be filtered and tested for feasibility. Feasibility includes determining the availability of skills, organisational capacity, and financial resources. It is decided whether the design is actually desirable, satisfies the © Milpark Education (Pty) Ltd Operations Management OMAN02-6 24a 40 performance criteria and whether the customer will want it. It also has to be determined whether the design is economically viable. The owners of the design must decide on the risk level and their tolerance for the risk. The next stage, the design funnel, applies criteria that will reduce the number of options. The preliminary design can commence after an acceptable, feasible and viable service or product concept has been identified. The service or product is defined and components of the design identified. The design can then be developed, evaluated and improved. The purpose of this stage is to take the preliminary design through a testing process to evaluate and determine whether the design can be improved before launching it to the market. Value engineering and quality function deployment are two methodologies used during this stage. Once the design is deemed acceptable, the final design can be concluded and a prototype can be made. Reducing design complexity Three approaches are used to reduce the complexity in design throughout the organisation: standardisation, commonality and modularisation. During standardisation, variety is reduced by utilising standard, off-the-shelf components as far as possible. This is applicable to line production or continuous production processes where high-volume, low-variety goods are produced. Commonality refers to the use of common elements within a service or a product. This is achieved when the same automobile part is produced to fit all the models of the manufacturer. Modularisation is used when sub-components are standardised, but can be assembled in a customised manner. Read Read pages 114 to 118 of the prescribed textbook for a deeper understanding of the strategic role of product and service innovation. 2.8 BUSINESS PROCESS RE-ENGINEERING (BPR) BPR originated with the idea that, rather than automate work, do away with work. This implies that all non-value-adding activities should be removed from the organisation. All systems and activities are therefore examined for their value in satisfying the end customer and whatever does not add value is seen as a waste. Processes are redesigned with the unnecessary activities removed. © Milpark Education (Pty) Ltd Operations Management OMAN02-6 24a 41 Processes have to be re-engineered to achieve breakthrough improvement and the re-engineering (BPR) process has to be treated as a project. Once the breakthrough improvement has been achieved, there has to be total quality management to ensure continuous improvement. According to Slack et al. (2022), BPR occurs “when a business tries to improve its performance in every area, not just manufacturing, by completely redesigning systems, processes, etc., rather than changing the existing ones.” This definition refers to the use of various methodologies, such as lean manufacturing, process flow-charting, critical examination in method study, operations network management, and customer-focused operations. Slack et al. (2022) summarise BPR as rethinking business processes in a cross-functional manner, striving for dramatic improvements in performance, bringing the production process closer to the customer and putting decision points where the work is performed. Example See the worked example on page 525 of the prescribed textbook as a good example of a process before and after re-engineering. Read Read page 525 of the prescribed textbook for a deeper understanding of business process re-engineering. Summary In this topic, we addressed the fact that every process utilised within an organisation consumes resources, which cost money. Sometimes the resource might be scarce and very expensive. The process must therefore produce something of value. Without processes, the organisation will be unable to produce goods or services that can be sold at a profit. Process decisions are therefore some of the most important business decisions to make. This was followed by a discussion of the various aspects of process design, such as the design objectives and the various process types, which should be chosen in line © Milpark Education (Pty) Ltd Operations Management OMAN02-6 24a 42 with the strategic objectives of the business and the type of product or service it renders. We then looked at the product–process matrix and determined that processes are also chosen according to the volume and variety of products, making use of this matrix. This was followed by a description of process-mapping and the tools we use to do mapping. Once the process strategy and structure have been decided on, processes must be mapped into flow diagrams, each with a work breakdown structure, and implemented throughout the organisation. Moreover, we discussed how continuous improvement ensures that well-designed, mapped and implemented processes are measured and continuously analysed for efficiency. We concluded the chapter by reviewing the methodologies that are used to measure efficiency, including throughput efficiency and value-added throughput efficiency. Little’s law formula, which is also used to determine process efficiency, was also evaluated in the topic. Process and product design has to be innovative and render the company more productive overall, at a lower cost. The various stages of design are concept generation, concept screening, preliminary design, evaluation and improvement, and prototyping and final design. It is important to reduce design complexity, rendering the processes simple enough for all users to successfully use in order to take inputs and transform them into outputs to be sold at a profit. Self-Assessment Questions 1. Map a process in your workplace that you have to follow and identify the bottlenecks. 2. Process development will ensure a standardised output at an acceptable level and according to customer requirements. Processes should be developed throughout the organisation. Do you think organisations can gain a competitive advantage from process development? Justify your view. 3. BPR is a process of improvement and brings about breakthrough implementation. Describe the circumstances under which you would embark on a BPR project. © Milpark Education (Pty) Ltd Operations Management OMAN02-6 24a 43 4. In order to produce standardised high-quality outputs, processes have to be developed. Quality guru W. Edwards Deming once stated, “Workers are responsible for 15 percent of the problems; the processes, for the other 85 percent. The process is the responsibility of management” (Slack et al., 2022). Do you agree with this statement? Justify your view. © Milpark Education (Pty) Ltd Operations Management OMAN02-6 24a 44 Topic 3 Supply chain management 3.1 INTRODUCTION This topic relates to the following module outcome: 2. Evaluate the processes needed to develop a new product or service, from identifying the customer needs to delivering the final product or service. Supply chain management (SCM) is about the management of a chain of suppliers versus customers. It is defined as “an approach which allows for the management of various aspects of the supply operation in a cross-functional way” (Kruger et al., 2013). It is about the movement of raw materials, information and customers and the distribution of finished goods. The supply chain is split into internal and external supply, external being upstream, towards a specific organisation, and downstream, from the organisation up to the end customer where money enters the supply chain. The internal supply chain includes the flow of material throughout the organisation, whereas one workstation becomes the supplier or customer of peer workstations. The art of SCM is to coordinate, manage and improve collaboration among supply chain partners. Processes should be developed across the entire supply chain in order to deliver a standardised product or service. Supply chain activities include purchasing, physical distribution management, logistics, materials management and customer relationship management (CRM). Supply chain managers are responsible for important decisions in the organisation such as location decisions, forecasting, purchasing and choosing suppliers, and distribution networks. Creating an effective supply chain involves the recognition of external competitive pressures and internal organisational pressures from groups such as sales, marketing, and product development (Krajewski et al., 2016). Such pressures could include variation in sales volumes, customer expectations, new markets and emerging markets. According to Krajewski et al. (2016), supply chain management has become increasingly complex in the global economy. To be effective, accurate inventory and demand information is required. In order to achieve supply chain success the integration of the entire supply chain is © Milpark Education (Pty) Ltd Operations Management OMAN02-6 24a 45 required, which is the effective coordination of the processes and visibility into the capacities and inventories of other members of the chain. In this topic, you will gain knowledge in the following areas: 1. Defining supply chain management 2. Activities of supply chain management 3. Supplier selection 4. Internet and e-procurement 5. Global sourcing 6. Logistical and physical distribution management 7. Relationship between operations and supply chain 8. Supply chain in practice 9. Improving the supply chain 10. E-business in supply chain 11. Supply chain network design 12. Forecasting in supply chain. 3.2 DEFINING SUPPLY CHAIN MANAGEMENT Supply chain management is the organisation of the interconnection between organisations that relate to each other through upstream and downstream linkages (Slack et al., 2022). Slack et al. (2022) hold that supply chain management is about the development and maintenance of the processes that produce value to the ultimate or end customer in the form of products or services. It is about the flow of physical goods, services and information. The supply chain is external and internal to the organisation, with each phase of production being a supplier or customer of the other. The supply chain is about the physical movement of tangible materials, but it is also relevant in the service industry and retail. All organisations have suppliers and customers and therefore form part of a supply chain. The supply chain management objective is first and foremost to satisfy the end customer. When the end customer purchases a product or a service, it triggers the flow through the supply chain and enters funds into the chain that will flow back up the supply chain. Each supply chain partner should endeavour to satisfy its direct customer, but should also have the specifications and requirements of the end customer in mind. The various factors of the supply chain should work in sync. These factors would include product design, production planning, © Milpark Education (Pty) Ltd Operations Management OMAN02-6 24a 46 manufacturing, and distribution, in order to deliver the right products to the right place at the right time and at the right price. Secondary objectives of supply chain management are the control and maintenance of quality, speed of delivery, dependability, flexibility and cost. The quality of a product or service is a function of the quality performance of every operation in the chain. Read Read pages 407 to 409 of the prescribed textbook for a deeper understanding of what supply chain management is. 3.3 ACTIVITIES OF SUPPLY CHAIN MANAGEMENT Supply chain management co-ordinates all the operations on the supply side and demand side. Supply chain management includes purchasing, physical distribution, logistics (which is sometimes done through an outsourcing partner), and materials management. It is about building supplier and customer relationships and controlling the interaction and touch points in each of these relationships. Purchasing buys the materials. They must understand the requirements of all the processes within the organisation and the capabilities of the suppliers. Purchasing has a significant impact on the profitability of the organisation. If supply is bought at minimum cost, the gross profit on the product increases, which has a direct impact on the bottom line. Inefficient purchasing will therefore negatively affect profitability or render the product or service more expensive, affecting the price leadership of the business. 3.4 SUPPLIER SELECTION When suppliers are chosen, various aspects have to be taken into account. Supplier scoring techniques should be used to avoid acting on perceptions which could be incorrect. The relative importance of each factor must be determined and suppliers scored on each factor with a weighting. © Milpark Education (Pty) Ltd Operations Management OMAN02-6 24a 47 Example See the worked example on page 420 of the prescribed textbook to understand the concept of rating and scoring suppliers according to factors with different weightings. Procurement managers have to decide whether to purchase from one specific supplier or from multiple suppliers. 3.5 INTERNET AND E-PROCUREMENT The use of the internet in procurement is increasing rapidly. Supplier information is now made available on the internet, making it easier to find suppliers. It also enables buyers to group together with other organisations to benefit from economies of scale, in other words, to create orders of sufficient size to warrant lower prices. E-procurement is the use of electronic methods in every stage of the purchasing process from identification of requirement to payment. It also includes contract management. The advantages of e-procurement include electronic ordering, shorter requisition and fulfilment cycles, centralised spending controls and a standardised global IT catalogue, enabling the buyer to see what is available and making choices from the comfort of the office. Making use of e-procurement will lower the cost of ordering and improve efficiency. Electronic marketplaces can take on different formats such as: a private marketplace where buyers or sellers conduct business only with its supply chain partners. a consortium, where several large businesses combine. a third party e-marketplace where an independent party creates an unbiased, market-driven retail space for buyers and sellers. E-procurement does not only involve transactions; e-procurement can also be an important source of information. It does not take the place of face-to-face negotiations and trade, but is considered a tool towards enhancing the procurement process. © Milpark Education (Pty) Ltd Operations Management OMAN02-6 24a 48 Read Read pages 414 to 415 of the prescribed textbook for more information on how relationships in supply chains should be managed. Example Watch the video at https://www.youtube.com/watch?v=2zsd3vRjfn8 to see an example of an e-procurement system. 3.6 SOURCING STRATEGY Globalisation has had an effect on supply chain management as it has brought about an expansion in the market and supply. The term global sourcing is used for identifying, evaluating, negotiating and configuring supply across multiple geographies. Ultimately, it is about importing. Global sourcing will increase complexity and risk in the supply chain. The cost of transport has to be considered and negotiations are done over long distances; there is often a language barrier to cope with. Procurement managers must consider factors such as purchase price, exchange rates, transport costs, carrying costs, taxes, border tariffs and duty costs, supply performance and operational risks. It is the duty of the procurement manager to ensure that ethical suppliers are found and monitored. Social, cultural and religious differences across borders can often lead to a varying perception of ethics. Read Read pages 416 to 418 of the prescribed textbook for more information on sourcing strategy. © Milpark Education (Pty) Ltd Operations Management OMAN02-6 24a 49 Activity Read the short case ‘Company values reflected in Urbanitas’ global sourcing policy’ and reflect on what drives large companies to draw up policies such as described in the case. 3.7 LOGISTICAL AND PHYSICAL DISTRIBUTION MANAGEMENT Logistics include six interrelated activities: 1. Transportation 2. Storage 3. Warehousing 4. Materials handling 5. Security and order processes 6. Communications. Internet communications in physical distribution management have had two major effects: to make information available, thus readily sharing information throughout the chain, and physical distribution, because consumers can buy goods online. Online buying increases the need for transportation, as all goods sold have to be delivered rather than taken by the customer upon the purchase in a retail environment. Read Read pages 426 to 428 of the prescribed textbook to fully understand logistics services. Example Look at sites such as Takealot and Bidorbuy as examples of business-to- consumer sites. www.takealot.com; www.bidorbuy.co.za © Milpark Education (Pty) Ltd Operations Management OMAN02-6 24a 50 3.8 RELATIONSHIP BETWEEN OPERATIONS AND SUPPLY CHAIN Supply chain management is the management of the immediate relationships with suppliers and customers. According to Slack et al. (2022), the growth in e- commerce has established broad categorised market sectors defined by who is supplying whom. This results in four types of businesses: 1. Business to business (B2B) 2. Business to consumer (B2C) 3. Consumer to business (C2B) 4. Customer to customer (C2C). Two main decisions in supply chain management are who to buy from and what to outsource. It also has to be decided whether one supplier or multiple suppliers will be used. The level of relationships has to be determined. Figure 12.6 on page 414 of the prescribed textbook illustrates the types of supply chain relationships. There are arm’s-length relationships, which are more like contractual relationships, and then there are close relationships or partnerships within the supply chain. The strength of the supply relationships will affect the efficiency of transactions that has a major impact on the operational metrics of the business. Slow supply will affect the cycle time and how dependable the business is to its customers. The quality of supply will affect the ability of the business to supply a standardised high-quality product or service to its customers. Price negotiations will have an impact on the sales prices of the business in the market. Market-based supply relationships are about purchasing goods and services, seeking the best supplier every time it is necessary to buy. Each transaction is a separate decision, with short-term relationships. The benefits of transactional and partnership supply chain relationships are outlined in Table 12.1 on page 415 of the prescribed textbook. While supply relationships can be at various levels, the responsibility of the business is to always build strong relationships with customers. Various software systems have been designed to track customer specifications. According to Slack et al. (2022), it is a process that helps to understand customers’ needs and to develop ways of meeting those needs, while maximising profitability. © Milpark Education (Pty) Ltd Operations Management OMAN02-6 24a 51 Read Read pages 414 to 426 of the prescribed textbook to understand the relationship between operations and supply chain management. Activity Watch the video at https://www.youtube.com/watch?v=J7nR2CC6y5Q and reflect on how supply chain management enables production and the ability of the business to service its customers. 3.9 SUPPLY CHAIN IN PRACTICE In supply chain management there are many variables to contend with, such as trends, fashions, varying demand, and scarcity of material. Supply chain managers are expected to understand the macro environment and be forewarned and prepared to deal with eventualities. The competitive environment, including direct competitors and substitute products, is one of the major disruptions and threats to the business and affects the supply chain. Many supply chain managers deal with products in various stages of the product life cycle. The current product life cycle stage of the product or service will affect the supply chain decisions. Efficient and responsive supply chain policies are required for products at various stages of the supply chain. Efficient supply chain policies will keep inventory low to maintain fast throughput, whereas responsive supply chain policies stress high service levels and responsive supply to the end customer. These are just examples of many supply chain decisions that managers have to face. The bullwhip effect The bullwhip effect refers to how a small disturbance at the downstream end of a supply chain causes increasingly large disturbances or errors, inaccuracies and volatility as it works its way upstream (Slack et al., 2022). Supply chain managers have to be aware of possible disturbances and need to be able to mitigate the effect of such disturbances. Study Table 12.4 on page 430 of the prescribed textbook to see how fluctuations of production levels along the supply chain will vary in response to small changes in end-customer demand. © Milpark Education (Pty) Ltd Operations Management OMAN02-6 24a 52 Along any chain, communications can be misinterpreted and in the supply chain where there are numerous upstream and downstream relationships and various complexities, misunderstandings can cause major losses. For instance, when exporting, a small miscommunication in destination information can cost hundreds of thousands in shipping costs. See Figure 12.11 on page 431 of the prescribed textbook for a depiction of typical supply chain dynamics. Read Read pages 429 to 433 of the prescribed textbook to understand the dynamics of the supply chain. 3.10 IMPROVING THE SUPPLY CHAIN In the past, a supply chain would hedge against interruptions and disturbances by planning for excess resources in the form of large buffer stocks. This had the result of cash tied up in inventory and high holding costs. Concepts such as just- in-time developed to ensure a leaner and more efficient supply chain operation, despite complexities such as global sourcing. New technologies and information systems have been developed to allow supply chain managers to know with higher levels of accuracy which items are required in the raw material warehouse, in progress and in the finished goods warehouse. This inventory knowledge includes material to and from the warehouse in transit. The SCOR Model “The Supply Chain Operations Reference (SCOR) model is a broad, but highly structured and systematic framework to supply chain improvement that has been developed by the Supply Chain Council (SCC), a global non-profit consortium” (Slack et al., 2022). The SCOR model uses three techniques: business process modelling, benchmarking performance, and best practice analysis, in an integrated manner to improve and communicate supply chain practices between different operations within the chain. © Milpark Education (Pty) Ltd Operations Management OMAN02-6 24a 53 3.11 E-BUSINESS IN THE SUPPLY CHAIN According to Slack et al. (2022), new information technology applications combined with the internet-based e-business have transformed the supply chain management practices through providing better and faster information and communication platforms. Some of the benefits of e-business in supply chain management include the real-time information share, channel alignment and operational efficiency, with each operation in the chain making an effort to reduce its own complexity and cost of doing business, and to increase throughput. It is about accuracy, speed of delivery, and efficiency. A supply chain is vulnerable, having to cope with many possible disruptions such as late deliveries, quality problems, incorrect information, shipping disasters and production delays. Lean supply chain practices have left little room for error. Therefore, technology has to be embraced to mitigate some of the complexities. Read Read pages 407 to 415 of the prescribed textbook to understand the effect of supply network on supply chain management. Example Watch the video at https://www.youtube.com/watch?v=YbM_LydRlnM to study the example of the iPhone e-commerce supply chain. 3.12 SUPPLY CHAIN NETWORK DESIGN 3.12.1 Introduction The view of the supply network gives a holistic view of the entire engine working towards satisfying the end customer. Taking a wider view, rather than just looking at the individual business, will provide a better understanding of the competitive environment. It will also assist in identifying the links in the network and focusing on long-term issues. Figure 5.2 on page 146 of the prescribed © Milpark Education (Pty) Ltd Operations Management OMAN02-6 24a 54 textbook shows an operations network for a plastic hardware company and a shopping mall. There are various decisions to be taken in the supply network, such as how the network should be configured, where each part should be located, and what capacity is required at each part of the network. Configuring the network involves the overall pattern, which includes two main sets of decisions: the pattern, shape and arrangement, and how much of the network each specific part should own. A recent trend in network configuration is to minimise suppliers and as such minimise complexity. Another trend would be dis-intermediation whereby an organisation will bypass supply chain partners to make contact with the end customer directly. According to the co-opetition approach, each business is surrounded by four types of players: 1. Suppliers 2. Customers 3. Competition 4. Complementors. 3.12.2 Outsourcing Outsourcing is a good way to increase capacity without capital investment. The trend to outsource is growing; organisations will buy in large amounts of components rather than produce them in-house. Figure 5.11 on page 162 of the prescribed textbook shows three companies operating in the wind-powe